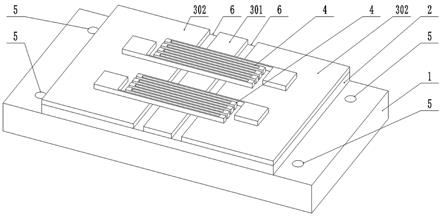
1.本发明涉及薄膜应变传感器,具体是一种双应变缝隙双电阻栅式薄膜应变传感器及其制备方法。
背景技术:2.目前,在众多类型的应变传感器中,薄膜应变传感器因其具有体积小、读取电路简单、价格低廉等优点,而被广泛应用于切削加工中的切削力测量。然而在现有技术条件下,薄膜应变传感器由于自身敏感结构的限制,在应用于低应变或微应变测量环境时存在应变偏小、灵敏度和线性度偏低的问题,由此影响切削力测量的精度和可靠性。基于此,有必要发明一种双应变缝隙双电阻栅式薄膜应变传感器及其制备方法,以解决现有薄膜应变传感器在应用于低应变或微应变测量环境时应变偏小、灵敏度和线性度偏低的问题。
技术实现要素:3.本发明为了解决现有薄膜应变传感器在应用于低应变或微应变测量环境时应变偏小、灵敏度和线性度偏低的问题,提供了一种双应变缝隙双电阻栅式薄膜应变传感器及其制备方法。
4.本发明是采用如下技术方案实现的:一种双应变缝隙双电阻栅式薄膜应变传感器,包括矩形不锈钢基底、矩形氮化钛过渡膜层、条形氮化硅绝缘膜层、两个矩形氮化硅绝缘膜层、两个镍铬薄膜电阻栅;其中,矩形不锈钢基底的表面四角各贯通开设有一个安装圆孔;矩形氮化钛过渡膜层沉积于矩形不锈钢基底的上表面中部;条形氮化硅绝缘膜层和两个矩形氮化硅绝缘膜层均沉积于矩形氮化钛过渡膜层的上表面,且两个矩形氮化硅绝缘膜层对称分布于条形氮化硅绝缘膜层的左右两侧;条形氮化硅绝缘膜层与两个矩形氮化硅绝缘膜层之间留设有两道沿纵向设置且呈左右对称分布的应变缝隙;每个镍铬薄膜电阻栅均同时沉积于条形氮化硅绝缘膜层的上表面和两个矩形氮化硅绝缘膜层的上表面,且两个镍铬薄膜电阻栅呈前后平行分布。
5.一种双应变缝隙双电阻栅式薄膜应变传感器的制备方法(该方法用于制备本发明所述的一种双应变缝隙双电阻栅式薄膜应变传感器),该方法是采用如下步骤实现的:步骤一:分别制作金属掩膜版a、金属掩膜版b、四根h形双端定位销;所述金属掩膜版a包括矩形版体a;矩形版体a的表面四角各贯通开设有一个定位圆孔a;矩形版体a的下表面边缘延伸设置有两个呈左右对称分布的l形定位凸台a;矩形版体a的下表面中部开设有矩形定位凹槽a,且矩形定位凹槽a的前、后端分别贯通矩形版体a的前、后端面;矩形定位凹槽a的槽底与矩形版体a的上表面之间贯通开设有沿纵向设置的条形窗口a和对称分布于条形窗口a左右两侧的两个矩形窗口;条形窗口a与两个矩形窗口之间形成有两根沿纵向设置且呈左右对称分布的悬臂梁;所述金属掩膜版b包括矩形版体b;矩形版体b的表面四角各贯通开设有一个定位圆孔b;矩形版体b的下表面边缘延伸设置有两个呈左右对称分布的l形定位凸台b;矩形版
体b的下表面中部开设有矩形定位凹槽b,且矩形定位凹槽b的前、后端分别贯通矩形版体b的前、后端面;矩形定位凹槽b的槽底与矩形版体b的上表面之间贯通开设有两个沿纵向设置且呈左右对称分布的条形窗口b;所述h形双端定位销包括中间细两端粗的腰鼓形销体;腰鼓形销体的上端面延伸设置有两根呈左右对称分布的弹性臂a;两根弹性臂a的上端面各延伸设置有一个按压凸块a,且两个按压凸块a呈左右对称分布;两根弹性臂a的外侧面上端各延伸设置有一个弧形定位凸台a,且两个弧形定位凸台a呈左右对称分布;腰鼓形销体的下端面延伸设置有两根呈左右对称分布的弹性臂b;两根弹性臂b的下端面各延伸设置有一个按压凸块b,且两个按压凸块b呈左右对称分布;两根弹性臂b的外侧面下端各延伸设置有一个弧形定位凸台b,且两个弧形定位凸台b呈左右对称分布;步骤二:选取矩形不锈钢基底,并在矩形不锈钢基底的表面四角各贯通开设一个安装圆孔;然后,先将矩形不锈钢基底置于丙酮中超声清洗300s,再将矩形不锈钢基底置于乙醇中超声清洗300s,随后将矩形不锈钢基底用去离子水冲洗60s,而后用氮气枪将矩形不锈钢基底吹干;步骤三:将矩形不锈钢基底置于超高真空磁控溅射系统中,用纯度为99.999%、直径为60mm、厚度为3mm的钛靶材,在矩形不锈钢基底的上表面中部沉积矩形氮化钛过渡膜层,由此得到双层复合结构;步骤四:将金属掩膜版a置于双层复合结构的上方,一方面使得四个定位圆孔a与四个安装圆孔一一正对,另一方面使得矩形氮化钛过渡膜层通过条形窗口a和两个矩形窗口暴露出来,由此形成条形暴露区域和两个矩形暴露区域;然后,将四根h形双端定位销一一对应地插入四个定位圆孔a和四个安装圆孔内,一方面使得八个弧形定位凸台a均与矩形版体a的上表面接触,另一方面使得八个弧形定位凸台b均与矩形不锈钢基底的下表面接触,由此将金属掩膜版a和双层复合结构连接在一起;步骤五:采用等离子体增强化学气相沉积系统在矩形氮化钛过渡膜层的条形暴露区域和两个矩形暴露区域分别沉积条形氮化硅绝缘膜层和两个矩形氮化硅绝缘膜层,由此得到三层复合结构;在沉积过程中,由于两根悬臂梁的遮挡,使得条形氮化硅绝缘膜层与两个矩形氮化硅绝缘膜层之间形成两道沿纵向设置且呈左右对称分布的应变缝隙;步骤六:将四根h形双端定位销一一对应地从四个定位圆孔a和四个安装圆孔内拔出,并将金属掩膜版a从三层复合结构的上方移走,使得两道应变缝隙暴露出来;步骤七:将金属掩膜版b置于三层复合结构的上方,一方面使得四个定位圆孔b与四个安装圆孔一一正对,另一方面使得两道应变缝隙分别通过两个条形窗口b暴露出来;然后,将四根h形双端定位销一一对应地插入四个定位圆孔b和四个安装圆孔内,一方面使得八个弧形定位凸台a均与矩形版体b的上表面接触,另一方面使得八个弧形定位凸台b均与矩形不锈钢基底的下表面接触,由此将金属掩膜版b和三层复合结构连接在一起;步骤八:将金属掩膜版b和三层复合结构一起置于超高真空磁控溅射系统中,用纯度为99.99%、直径为60mm、厚度为3mm的铝靶材,在两道应变缝隙内分别沉积两个条形铝牺牲膜层,由此得到带有牺牲膜层的三层复合结构;
步骤九:将四根h形双端定位销一一对应地从四个定位圆孔b和四个安装圆孔内拔出,并将金属掩膜版b从带有牺牲膜层的三层复合结构的上方移走,使得两个条形铝牺牲膜层暴露出来;步骤十:将带有牺牲膜层的三层复合结构置于超高真空磁控溅射系统中,用纯度为99.99%、直径为60mm、厚度为3mm的ni
80
cr
20
靶材,在条形氮化硅绝缘膜层的上表面、两个矩形氮化硅绝缘膜层的上表面、两个条形铝牺牲膜层的上表面沉积镍铬敏感膜层;步骤十一:采用光刻工艺和离子束刻蚀工艺将镍铬敏感膜层刻蚀成为两个镍铬薄膜电阻栅;步骤十二:采用湿法刻蚀工艺去除两个条形铝牺牲膜层,由此制得一种双应变缝隙双电阻栅式薄膜应变传感器。
6.工作时,两个镍铬薄膜电阻栅依次通过测量电路、信号处理模块与pc机连接。具体工作过程如下:在进行切削加工时,切削力传递至矩形不锈钢基底,使得矩形不锈钢基底发生变形,由此使得矩形氮化钛过渡膜层、条形氮化硅绝缘膜层、两个矩形氮化硅绝缘膜层、两道应变缝隙、两个镍铬薄膜电阻栅均发生变形,从而使得两个镍铬薄膜电阻栅的电阻值均发生改变。此时,由于两个镍铬薄膜电阻栅的电阻值均发生改变,使得测量电路输出电压信号。测量电路输出的电压信号经信号处理模块进行处理后传输至pc机,pc机根据接收到的电压信号即可实时获取切削加工中的切削力信息。
7.基于上述过程,与现有薄膜应变传感器相比,本发明所述的一种双应变缝隙双电阻栅式薄膜应变传感器通过采用全新的双应变缝隙双电阻栅式敏感结构,实现了在小面积内产生应力集中区域,由此能够有效阻止应变能量耗散,从而能够在应用于低应变或微应变测量环境时有效增大应变、有效提高灵敏度和线性度,进而有效保证了切削力测量的精度和可靠性。
8.本发明有效解决了现有薄膜应变传感器在应用于低应变或微应变测量环境时应变偏小、灵敏度和线性度偏低的问题,适用于切削加工中的切削力测量。
附图说明
9.图1是本发明的结构示意图。
10.图2是本发明中金属掩膜版a的结构示意图。
11.图3是本发明中金属掩膜版b的结构示意图。
12.图4是本发明中h形双端定位销的结构示意图。
13.图5是本发明中步骤三的示意图。
14.图6是本发明中步骤四的示意图一。
15.图7是本发明中步骤四的示意图二。
16.图8是本发明中步骤五的示意图。
17.图9是本发明中步骤六的示意图。
18.图10是本发明中步骤七的示意图一。
19.图11是本发明中步骤七的示意图二。
20.图12是本发明中步骤八的示意图。
21.图13是本发明中步骤九的示意图。
22.图14是本发明中步骤十的示意图。
23.图15是本发明中步骤十一的示意图。
24.图16是本发明中步骤十二的示意图。
25.图中:1-矩形不锈钢基底,2-矩形氮化钛过渡膜层,301-条形氮化硅绝缘膜层,302-矩形氮化硅绝缘膜层,4-镍铬薄膜电阻栅,5-安装圆孔,6-应变缝隙,701-矩形版体a,702-定位圆孔a,703-l形定位凸台a,704-条形窗口a,705-矩形窗口,706-悬臂梁,801-矩形版体b,802-定位圆孔b,803-l形定位凸台b,804-条形窗口b,901-腰鼓形销体,902-弹性臂a,903-按压凸块a,904-弧形定位凸台a,905-弹性臂b,906-按压凸块b,907-弧形定位凸台b,10-条形铝牺牲膜层,11-镍铬敏感膜层。
具体实施方式
26.一种双应变缝隙双电阻栅式薄膜应变传感器,包括矩形不锈钢基底1、矩形氮化钛过渡膜层2、条形氮化硅绝缘膜层301、两个矩形氮化硅绝缘膜层302、两个镍铬薄膜电阻栅4;其中,矩形不锈钢基底1的表面四角各贯通开设有一个安装圆孔5;矩形氮化钛过渡膜层2沉积于矩形不锈钢基底1的上表面中部;条形氮化硅绝缘膜层301和两个矩形氮化硅绝缘膜层302均沉积于矩形氮化钛过渡膜层2的上表面,且两个矩形氮化硅绝缘膜层302对称分布于条形氮化硅绝缘膜层301的左右两侧;条形氮化硅绝缘膜层301与两个矩形氮化硅绝缘膜层302之间留设有两道沿纵向设置且呈左右对称分布的应变缝隙6;每个镍铬薄膜电阻栅4均同时沉积于条形氮化硅绝缘膜层301的上表面和两个矩形氮化硅绝缘膜层302的上表面,且两个镍铬薄膜电阻栅4呈前后平行分布。
27.矩形不锈钢基底1采用304不锈钢制成;矩形氮化钛过渡膜层2的厚度为500nm~800nm;条形氮化硅绝缘膜层301的厚度、两个矩形氮化硅绝缘膜层302的厚度均为200nm~800nm;两个镍铬薄膜电阻栅4的厚度均为800nm~1000nm。
28.一种双应变缝隙双电阻栅式薄膜应变传感器的制备方法(该方法用于制备本发明所述的一种双应变缝隙双电阻栅式薄膜应变传感器),该方法是采用如下步骤实现的:步骤一:分别制作金属掩膜版a、金属掩膜版b、四根h形双端定位销;所述金属掩膜版a包括矩形版体a701;矩形版体a701的表面四角各贯通开设有一个定位圆孔a702;矩形版体a701的下表面边缘延伸设置有两个呈左右对称分布的l形定位凸台a703;矩形版体a701的下表面中部开设有矩形定位凹槽a,且矩形定位凹槽a的前、后端分别贯通矩形版体a701的前、后端面;矩形定位凹槽a的槽底与矩形版体a701的上表面之间贯通开设有沿纵向设置的条形窗口a704和对称分布于条形窗口a704左右两侧的两个矩形窗口705;条形窗口a704与两个矩形窗口705之间形成有两根沿纵向设置且呈左右对称分布的悬臂梁706;所述金属掩膜版b包括矩形版体b801;矩形版体b801的表面四角各贯通开设有一个定位圆孔b802;矩形版体b801的下表面边缘延伸设置有两个呈左右对称分布的l形定位凸台b803;矩形版体b801的下表面中部开设有矩形定位凹槽b,且矩形定位凹槽b的前、后端分别贯通矩形版体b801的前、后端面;矩形定位凹槽b的槽底与矩形版体b801的上表面之间贯通开设有两个沿纵向设置且呈左右对称分布的条形窗口b804;所述h形双端定位销包括中间细两端粗的腰鼓形销体901;腰鼓形销体901的上端
面延伸设置有两根呈左右对称分布的弹性臂a902;两根弹性臂a902的上端面各延伸设置有一个按压凸块a903,且两个按压凸块a903呈左右对称分布;两根弹性臂a902的外侧面上端各延伸设置有一个弧形定位凸台a904,且两个弧形定位凸台a904呈左右对称分布;腰鼓形销体901的下端面延伸设置有两根呈左右对称分布的弹性臂b905;两根弹性臂b905的下端面各延伸设置有一个按压凸块b906,且两个按压凸块b906呈左右对称分布;两根弹性臂b905的外侧面下端各延伸设置有一个弧形定位凸台b907,且两个弧形定位凸台b907呈左右对称分布;步骤二:选取矩形不锈钢基底1,并在矩形不锈钢基底1的表面四角各贯通开设一个安装圆孔5;然后,先将矩形不锈钢基底1置于丙酮中超声清洗300s,再将矩形不锈钢基底1置于乙醇中超声清洗300s,随后将矩形不锈钢基底1用去离子水冲洗60s,而后用氮气枪将矩形不锈钢基底1吹干;步骤三:将矩形不锈钢基底1置于超高真空磁控溅射系统中,用纯度为99.999%、直径为60mm、厚度为3mm的钛靶材,在矩形不锈钢基底1的上表面中部沉积矩形氮化钛过渡膜层2,由此得到双层复合结构;步骤四:将金属掩膜版a置于双层复合结构的上方,一方面使得四个定位圆孔a702与四个安装圆孔5一一正对,另一方面使得矩形氮化钛过渡膜层2通过条形窗口a704和两个矩形窗口705暴露出来,由此形成条形暴露区域和两个矩形暴露区域;然后,将四根h形双端定位销一一对应地插入四个定位圆孔a702和四个安装圆孔5内,一方面使得八个弧形定位凸台a904均与矩形版体a701的上表面接触,另一方面使得八个弧形定位凸台b907均与矩形不锈钢基底1的下表面接触,由此将金属掩膜版a和双层复合结构连接在一起;步骤五:采用等离子体增强化学气相沉积系统在矩形氮化钛过渡膜层2的条形暴露区域和两个矩形暴露区域分别沉积条形氮化硅绝缘膜层301和两个矩形氮化硅绝缘膜层302,由此得到三层复合结构;在沉积过程中,由于两根悬臂梁706的遮挡,使得条形氮化硅绝缘膜层301与两个矩形氮化硅绝缘膜层302之间形成两道沿纵向设置且呈左右对称分布的应变缝隙6;步骤六:将四根h形双端定位销一一对应地从四个定位圆孔a702和四个安装圆孔5内拔出,并将金属掩膜版a从三层复合结构的上方移走,使得两道应变缝隙6暴露出来;步骤七:将金属掩膜版b置于三层复合结构的上方,一方面使得四个定位圆孔b802与四个安装圆孔5一一正对,另一方面使得两道应变缝隙6分别通过两个条形窗口b804暴露出来;然后,将四根h形双端定位销一一对应地插入四个定位圆孔b802和四个安装圆孔5内,一方面使得八个弧形定位凸台a904均与矩形版体b801的上表面接触,另一方面使得八个弧形定位凸台b907均与矩形不锈钢基底1的下表面接触,由此将金属掩膜版b和三层复合结构连接在一起;步骤八:将金属掩膜版b和三层复合结构一起置于超高真空磁控溅射系统中,用纯度为99.99%、直径为60mm、厚度为3mm的铝靶材,在两道应变缝隙6内分别沉积两个条形铝牺牲膜层10,由此得到带有牺牲膜层的三层复合结构;步骤九:将四根h形双端定位销一一对应地从四个定位圆孔b802和四个安装圆孔5
内拔出,并将金属掩膜版b从带有牺牲膜层的三层复合结构的上方移走,使得两个条形铝牺牲膜层10暴露出来;步骤十:将带有牺牲膜层的三层复合结构置于超高真空磁控溅射系统中,用纯度为99.99%、直径为60mm、厚度为3mm的ni
80
cr
20
靶材,在条形氮化硅绝缘膜层301的上表面、两个矩形氮化硅绝缘膜层302的上表面、两个条形铝牺牲膜层10的上表面沉积镍铬敏感膜层11;步骤十一:采用光刻工艺和离子束刻蚀工艺将镍铬敏感膜层11刻蚀成为两个镍铬薄膜电阻栅4;步骤十二:采用湿法刻蚀工艺去除两个条形铝牺牲膜层10,由此制得一种双应变缝隙双电阻栅式薄膜应变传感器。
29.四根h形双端定位销均采用弹簧钢制成,八个弧形定位凸台a904的外侧面均为朝向斜上方的倒角面,八个弧形定位凸台b907的外侧面均为朝向斜下方的倒角面;两个条形铝牺牲膜层10的厚度均为200nm~800nm;镍铬敏感膜层11的厚度为800nm~1000nm。
30.所述步骤三中,沉积时的工艺参数如下:功率为100w,偏压为-60v,压强为1pa,氩气和氮气的比例为60:3;所述步骤五中,沉积时的工艺参数如下:功率为350w、气氛压强为4pa、氩气流量为140sccm、氨气流量为8sccm、硅烷流量为145sccm、基底温度为300℃、射频频率为13.56mhz;所述步骤八中,沉积时的工艺参数如下:氩气流量为50sccm,功率为100w,压强为1pa;所述步骤十中,沉积时的工艺参数如下:功率为200w,压力为1.6pa,偏压为-100v,衬底温度为400℃。
31.所述步骤十一中,光刻工艺的步骤依次为:涂胶、前烘、曝光、显影、坚膜;涂胶时,光刻胶采用az6130光刻胶,匀胶机采用cee匀胶机,转速为3000r/min;曝光时,光刻机采用evg光刻机,掩膜版采用菲林纸掩膜版;显影时,显影液采用hg-200-238正胶显影液;坚膜时,电热板采用eh20b电热板,坚膜温度为120℃,坚膜时间为900s;离子束刻蚀工艺的步骤依次为:刻蚀、去胶;刻蚀时的工艺参数如下:阴极电流为5.8a、弧极电压为45v、加速电压为300v、中和电流为6.10a、耦合系数为1.25;去胶时,去胶方式采用干法去胶,去胶时间为30min。
32.所述步骤十二中,采用湿法刻蚀工艺去除两个条形铝牺牲膜层10的具体步骤如下:将带有牺牲膜层的三层复合结构和两个镍铬薄膜电阻栅4一起置于浓度为0.5mol/l~1mol/l的氢氧化钠或氢氧化钾溶液中,水浴加热至60℃,使得两个条形铝牺牲膜层10与氢氧化钠或氢氧化钾完全反应直至消失。
33.所述步骤十二完成后,先将一种双应变缝隙双电阻栅式薄膜应变传感器置于去离子水中去除多余的杂质离子,再将一种双应变缝隙双电阻栅式薄膜应变传感器置于真空下干燥数小时,随后采用精密激光焊接机将导线焊接到两个镍铬薄膜电阻栅4的电极区,而后采用封装机将一种双应变缝隙双电阻栅式薄膜应变传感器封装好,以备后续测量使用。
34.虽然以上描述了本发明的具体实施方式,但是本领域的技术人员应当理解,这些仅是举例说明,本发明的保护范围是由所附权利要求书限定的。本领域的技术人员在不背离本发明的原理和实质的前提下,可以对这些实施方式作出多种变更或修改,但这些变更和修改均落入本发明的保护范围。