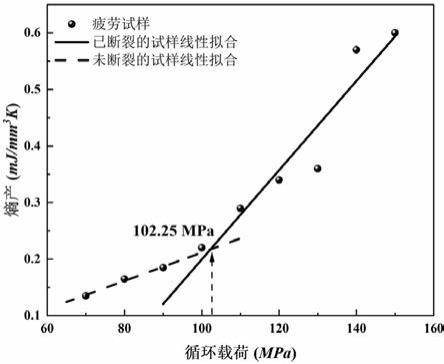
1.本发明属于力学性能检测技术领域,具体涉及一种基于熵产稳定值预测金属材料疲劳极限的方法。
背景技术:2.在结构材料技术领域,服役结构件在服役过程中往往承受疲劳载荷作用,疲劳是机械部件中最常见的失效形式之一,一旦出现疲劳断裂,给人们的生命财产带来灾难性的损失。目前的疲劳极限测定主要依靠试验手段对金属材料的疲劳性能进行分析和检测,然而这些疲劳试验方法存在着试验周期长、试件消耗大、数据离散等不足,这些都为获取金属材料的疲劳极限带来了一定的困难。
3.中国发明专利“基于疲劳损伤熵熵产速率焊接接头疲劳极限快速预测方法”(申请号:202010083782.5),该方法利用累积损伤熵熵产速率与应力之间的关系,进而预测焊接接头疲劳极限的方法。与目前的疲劳试验方法相比,该方法可以得到实时的材料内部损伤情况,具有相对方便、快捷、准确等优点。然而,该方法虽能快速测得临界值,但是需要先计算出累计损伤熵产并求出熵产率(即斜率),此过程中可能较大的人为误差以及计算的繁杂,并且试验还是要做到106以上,试验过程不够简便。
技术实现要素:4.为了克服现有技术的不足,解决金属材料疲劳极限快速、准确预测的技术问题,本发明提供一种基于熵产稳定值预测金属材料疲劳极限的方法。
5.为实现上述目的,本发明是根据以下技术方案实现的:
6.基于熵产稳定值预测金属材料疲劳极限的方法,包括以下步骤:
7.s1、制备疲劳试验试件:
8.s1-1、根据gb/t6398-2000标准并采用线切割方法加工而成金属材料标准疲劳试样;
9.s1-2、用砂纸打磨标准疲劳试样,使标准疲劳试样的表面及线切割加工面光滑;
10.s1-3、用乙醇擦拭标准疲劳试样,使标准疲劳试样的表面洁净;
11.s1-4、在标准疲劳试样的待测温表面一侧均匀涂覆一层黑色哑光漆,增加热反射率,制得疲劳试验试件,留待后步使用;
12.s2、疲劳试验试件加载及测温准备:
13.首先,调整疲劳试验参数:循环特征系数为0.1,谐振频率为10hz;然后,将疲劳试验试件装卡在疲劳试验机上,同时将红外热像仪放置于距离疲劳试验试件的测温表面800mm的位置处,红外热像仪记录温度的灵敏度为0.08k,调节红外热像仪的焦距,保证疲劳试验过程中录制的温度图像清晰;
14.s3、疲劳试验:
15.对疲劳试验试件在不同应力水平下进行循环加载,控制系统采集疲劳应变试验数
据,同时使用红外热像仪对疲劳试验试件内部释放至表面的温度进行监测,并储存疲劳试验试件表面特征数据和疲劳热像图;
16.s4、数据处理及分析:
17.s4-1、分析红外热像仪测得的试验结果,提取疲劳试验试件在疲劳载荷作用下的温度-时间关系数据和温度图像;
18.s4-2、分析疲劳试验控制系统测得的应变数据,在origin软件中转化为塑性能密度;
19.s4-3、进行热力学熵产计算,确定不同循环载荷水平下稳定阶段塑性能密度和温度,热力学熵产计算公式为:
[0020][0021]
式中,sg为熵产,f为频率,w
p
为塑性能密度,t为温度;
[0022]
s4-4、确定疲劳试验试件的熵产稳定值与循环载荷关系曲线的形状,熵产稳定值与循环载荷关系包括以下两个阶段:
[0023]
a.熵产稳定值在低循环载荷作用下呈稳定线性增加,此时试件内部混乱度增加率较低,外部表现为熵产稳定值的稳定增加;
[0024]
b.在高循环载荷下曲线出现剧烈的快速升高阶段,此时试件内部发生大量塑性变形,试件内部混乱度增加率快速升高,即熵产迅速增大;
[0025]
a阶段线性线段与b阶段线性线段的交点即为该金属材料的疲劳极限。
[0026]
进一步地,在所述步骤s1-2中,标准疲劳试样正反面及线切割加工面打磨后的粗糙度ra为0.32-0.63μm。
[0027]
进一步地,在所述步骤s2中,所述疲劳试验机为型号为sds-100的电液伺服低周疲劳试验机。
[0028]
与现有技术相比本发明的有益效果为:
[0029]
本发明借助于sds-100电液伺服低周疲劳试验机和红外热像仪,提供一种通过采集金属材料内部变形时所产生的应变情况和释放热量的表面温度并计算出热力学熵产,并建立熵产稳定值和循环载荷的关系准确预测金属材料试样疲劳极限的方法,预测过程仅需1-2小时,预测结果准确。
附图说明
[0030]
图1本发明实施例所用的镁合金标准疲劳试样及其尺寸;其中,a)为标准疲劳试样俯视图;b)为标准疲劳试样主视图;
[0031]
图2为本发明为疲劳红外热像分析试验系统,图中,1为电液伺服低周疲劳试验机,2为卡具,3为疲劳试验试件,4为控制装置(内置控制系统),5为红外热像仪,6为分析装置(内置分析系统);
[0032]
图3本发明实施例所用的镁合金疲劳试验试件表面温度红外热像图;
[0033]
图4本发明实施例所用的镁合金疲劳试验试件塑性能密度图;
[0034]
图5本发明实施例所用的镁合金疲劳试验试件传统s-n图;
[0035]
图6为本发明实施例所用的镁合金基于熵产稳定值测得疲劳极限图;
具体实施方式
[0036]
以下实施例用于说明本发明,但不用来限制本发明的范围。若未特别指明,实施例均按照常规实验条件。另外,对于本领域技术人员而言,在不偏离本发明的实质和范围的前提下,对这些实施方案中的物料成分和用量进行的各种修改或改进,均属于本发明要求保护的范围。
[0037]
本实例使用的化学物质材料为:镁合金板、黑色哑光漆、乙醇和砂纸,其准备用量(以毫米、毫升为计量单位)如下:
[0038]
镁合金板:az31b,300mm
×
300mm
×
10mm,10块;
[0039]
黑色哑光漆:500ml
±
10ml;
[0040]
乙醇:c2h5oh500ml
±
10ml;
[0041]
砂纸:sic800目,276mm
×
0.5mm
×
230mm,5张;
[0042]
砂纸:sic1000目,276mm
×
0.5mm
×
230mm,5张;
[0043]
砂纸:sic1500目,276mm
×
0.5mm
×
230mm,5张。
[0044]
基于熵产稳定值预测金属材料疲劳极限的方法,包括以下步骤:
[0045]
s1、制备疲劳试验试件:
[0046]
s1-1、根据gb/t6398-2000标准并采用线切割方法加工而成金属材料标准疲劳试样,标准疲劳试样的形状及尺寸如图1所示;
[0047]
s1-2、依次采用800目、1000目和1500目的金相砂纸对标准疲劳试样表面进行打磨,使标准疲劳试样的表面及线切割加工面光滑,粗糙度ra达到0.32-0.63μm;
[0048]
s1-3、用乙醇擦拭标准疲劳试样,使标准疲劳试样的表面洁净;
[0049]
s1-4、在标准疲劳试样的待测温表面一侧均匀涂覆一层黑色哑光漆,增加热反射率,制得疲劳试验试件,留待后步使用;
[0050]
s2、疲劳试验试件加载及测温准备:
[0051]
首先,调整疲劳试验参数:循环特征系数为0.1,谐振频率为10hz;然后,将疲劳试验试件装卡在疲劳试验机上,同时将红外热像仪放置于距离疲劳试验试件的测温表面800mm的位置处,红外热像仪记录温度的灵敏度为0.08k,调节红外热像仪的焦距,保证疲劳试验过程中录制的温度图像清晰;
[0052]
s3、疲劳试验:
[0053]
对疲劳试验试件在不同应力水平下进行循环加载,控制系统采集疲劳应变试验数据,同时使用红外热像仪对疲劳试验试件内部释放至表面的温度进行监测,并储存疲劳试验试件表面特征数据和疲劳热像图;
[0054]
s4、数据处理及分析:
[0055]
s4-1、分析红外热像仪测得的试验结果,提取疲劳试验试件在疲劳载荷作用下的温度-时间关系数据和温度图像;如图3所示,由于疲劳试验试件形状具有对称性,所以试件始终受到两边对称的拉力。其中在载荷逐渐增大的情况下,塑性变形幅度增大散出的热量越多,温度的幅度也发生相应的变化;
[0056]
镁合金在受到疲劳载荷时,外部施加的机械功会转化为其内部的内能,从而导致试件温度升高;当温度高于环境温度时,其内部的热量会向周围散失,温度差越大热量散失的速度就越快,所以镁合金的温度在疲劳载荷下不会一直升高。当单位时间内试件内部产
生的热量与散失到周围环境的热量相等时,镁合金的温度就会达到产热和散热的动态平衡。平稳阶段占据了整个寿命的70%-90%,选取图3中稳定阶段的温度进行后续计算;
[0057]
s4-2、分析疲劳试验控制系统测得的应变数据,在origin中转化为塑性能密度;
[0058]
镁合金在不同循环载荷下的塑性应变能在疲劳过程中具有相同的演化规律,其中在载荷逐渐增大的情况下,塑性变形幅度增大,塑性能密度的幅度也发生相应的变化;
[0059]
镁合金在受到疲劳载荷时,外部施加的机械功做功导致试样产生应变,塑形能密度公式如下:
[0060][0061]
其中,σa为应力幅,δε
p
塑形应变,n
′
加工硬化指数;
[0062]
镁合金试件在承受循环载荷时初始阶段由于静态试样在循环应力突然加载时发生大量塑性变形,导致塑性应变能迅速积累。随着循环次数的增加试件受加工硬化影响,使塑性应变缓慢增加。根据应变能计算公式,应力保持不变,应变略有增加,加工硬化指数增加,整体应变能密度曲线呈下降趋势。当位错积累到一定程度时,就会发生位错堆积,并且加工硬化程度稳定,因此塑性应变能密度几乎保持不变。平稳阶段占据了整个寿命的70%-90%,选取图4稳定阶段的塑性能密度进行后续计算;
[0063]
s4-3、进行热力学熵产计算,确定不同循环载荷水平下稳定阶段塑性能密度和温度,热力学熵产计算公式为:
[0064][0065]
式中,sg为熵产,f为频率,w
p
为塑性能密度,t为温度;
[0066]
s4-4、确定疲劳试验试件的熵产稳定值与循环载荷关系曲线的形状,熵产稳定值与循环载荷关系包括以下两个阶段:
[0067]
a.熵产稳定值在低循环载荷作用下呈稳定线性增加,此时试件内部混乱度增加率较低,外部表现为熵产稳定值的稳定增加;
[0068]
b.在高循环载荷下曲线出现剧烈的快速升高阶段,此时试件内部发生大量塑性变形,试件内部混乱度增加率快速升高,即熵产迅速增大;
[0069]
a阶段线性线段与b阶段线性线段的交点即为该金属材料的疲劳极限,具体参数如下表一所示。
[0070]
表一试验图形参数表
[0071][0072]
如图5所示,在传统试验下获得的s-n曲线,分别选取了150mpa、140mpa、130mpa、120mpa、110mpa、100mpa、90mpa、80mpa疲劳试验,最后得到疲劳极限为95.66mpa。如图6所示,本实施例中镁合金的疲劳极限预测值为102.25mpa,与传统试验下获得的疲劳极限误差为6.8%。
[0073]
由上述分析可见,通过本发明中提出的方法得到的镁合金表面温度、塑性能密度与载荷循环次数关系,最终得到熵产稳定值和不同循环载荷下的关系曲线,通过分析曲线形状特征,便可以准确的判断镁合金疲劳试验试件的疲劳极限。采用本发明提出的镁合金疲劳极限测定方法仅需1-2个小时,因此很大程度上节省了试验时间和试验材料,具有明显的先进性。
[0074]
以上所述,仅为本发明的具体实施方式,但本发明的保护范围并不局限于此,任何熟悉技术领域的技术人员在本发明揭露的技术范围内,可轻易想到的变化或替换,都应涵盖在本发明的保护范围之内。因此,本发明的保护范围应以所述权利要求的保护范围为准。