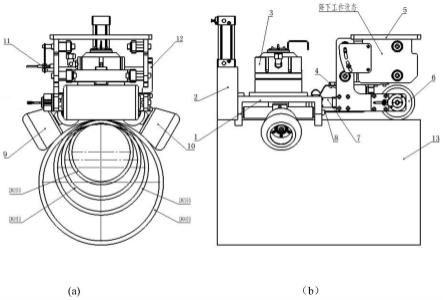
1.本发明涉及管道检测技术领域,具体地,涉及一种用于球墨铸管壁厚检测的三轮自适应小车。
背景技术:2.球墨铸管因其优越的抗腐蚀性、强度和韧性,可承受较高的输水压力、土壤压力和地面载荷,使用安全可靠,广泛应用于输水、输油、输气管道中。球墨铸管在运输和地下敷设时,往往要承受冲击碰撞,埋土后又受到土壤压力,另外,用于排除污水的管道,还经常受到含酸废水的腐蚀。因此,球墨铸管的关键技术参数的检测非常重要。
3.关键技术参数中壁厚的检测尤为重要,壁厚不均匀或局部过薄极易引起局部的承载能力下降,很容易出现管道爆裂事故。另外,由于球墨铸管在生产过程中不能保证它的形状是规则的圆柱面,实际上是无规则变化的复杂空间曲面,工艺要求产生的凸凹不平整的管道表面使得检测仪在检测过程中出现剧烈振动,测量信号受到干扰和损失,因此,行走测量机构如何保证在线实时检测时,能够实时的适应被检测管道复杂的空间曲面,确保检测仪与检测管道表面保持垂直且距离恒定是实现精确检测的关键。
技术实现要素:4.鉴于此,本发明提出的一种用于球墨铸管壁厚检测的三轮自适应小车,既能够保证管道实时检测时检测仪始终与检测表面垂直,距离恒定,又能满足同一个生产线上不同规格的管道检测。
5.为实现上述技术目的,本发明采用如下技术方案:一种用于球墨铸管壁厚检测的三轮自适应小车,包括:底盘、耐磨滚轮对称开合机构、测厚仪、阻尼簧片、四连杆调整机构、前轮、底盘连接轴、耦合剂开合机构、第一滚轮、第二滚轮、光电定位机构、机械限位机构、测量机架,所述底盘上设有呈对称开合的第一滚轮和第二滚轮,所述第一滚轮、第二滚轮均与耐磨滚轮对称开合机构连接;所述前轮通过底盘连接轴与底盘连接,所述测厚仪固定于底盘上,所述耦合剂开合机构通过四连杆调整机构设置于底盘上,所述四连杆调整机构与测量机架连接,所述阻尼簧片设置于底盘和四连杆调整机构之间,并与四连杆调整机构固定连接;所述机械限位机构分别与四连杆调整机构、前轮固定连接,所述光电定位机构设置于四连杆调整机构上。
6.进一步地,所述耐磨滚轮对称开合机构包括:气缸、气缸伸缩杆、气缸安装座、销轴、右轮伸缩轴、右轮伸缩套、左轮滚轴、右轮滚轴、左轮伸缩套、左轮伸缩轴、升降杆、锁紧螺母,所述气缸安装座固定安装于底盘上,所述气缸设置于气缸安装座上,所述气缸伸缩杆与气缸配合,所述气缸伸缩杆与升降杆连接,且所述气缸伸缩杆与升降杆通过锁紧螺母锁紧固定;所述左轮伸缩轴的一端、右轮伸缩轴一端上均设有销孔,销孔通过销轴与升降杆铰链;所述左轮伸缩轴的另一端的外圆柱面与左轮伸缩套的内圆柱面配合,所述左轮伸缩套与左轮滚轴通过螺栓和压板固定连接,所述左轮滚轴与第一滚轮通过螺栓固定连接;所述
右轮伸缩轴的另一端的外圆柱面与右轮伸缩套的内圆柱面配合,所述右轮伸缩套与右轮滚轴通过螺栓和压板固定连接,所述右滚轮轴与第二滚轮通过螺栓固定连接。
7.进一步地,所述底盘连接轴包括:旋转螺栓转轴、连接轴、第二轴承、第五轴承挡圈、第三轴承压板,所述连接轴的一端上设有转轴孔,转轴孔通过旋转螺栓转轴与底盘连接,所述连接轴的另一端设有轴承安装圆柱面,轴承安装圆柱面与第二轴承的内圈连接,所述第三轴承压板设置于轴承安装圆柱面的端面上,并通过第三轴承压板固定螺栓紧固连接;所述第二轴承的外圈设置于前轮支撑横梁的轴承安装孔内,所述第五轴承挡圈设置于前轮支撑横梁的轴承挡圈安装槽内,所述连接轴上设有弧形摆动限位结构,与前轮支撑横梁上的弧形限位槽配合。
8.进一步地,所述阻尼簧片包括:弹性簧片、柔性连接板,所述弹性簧片的一端与柔性连接板的一端通过连接螺栓连接,所述弹性簧片的另一端设置于底盘上平面上的限位槽接触,所述柔性连接板通过第一固定螺栓与四连杆调整机构固定连接。
9.进一步地,所述四连杆调整机构包括:四连杆固定座、左上连杆、四连杆、旋转轴压板固定螺栓、旋转轴压板、右上连杆、旋转轴、第一轴承,所述四连杆固定座与测量机架通过螺栓固定连接,所述左上连杆通过第一转轴一端与四连杆固定座连接,第一转轴的另一端与前轮左支撑架连接;所述右上连杆通过第二转轴一端与四连杆固定座连接,第二转轴的另一端与前轮右支撑架连接;所述四连杆通过第三转轴一端与四连杆固定座连接,第三转轴的另一端与前轮左支撑架连接;所述四连杆固定座上设有轴承安装孔,所述第一轴承的外圈与轴承安装孔配合,所述第一轴承的内圈与旋转轴连接,所述旋转轴与右上连杆上的转轴安装孔配合,通过旋转轴压板和旋转轴压板固定螺栓紧固锁死;所述四连杆与柔性连接板通过第一固定螺栓固定连接。
10.进一步地,所述前轮包括:前轮右支撑架、支撑架固定横梁、前轮左支撑架、前滚轮、编码器、前轮滚轮右安装板、右连接板、左连接板、左连接板固定螺栓、右连接板固定螺栓、前滚轮左安装板,所述前轮右支撑架固定连接于支撑架固定横梁的右端面,所述前轮右支撑架通过右连接板与前滚轮右安装板连接,并通过右连接板固定螺栓固定;所述前轮左支撑架固定连接于支撑架固定横梁的左端面,所述前轮左支撑架通过左连接板与前轮滚轮左安装板连接,并通过左连接板固定螺栓固定,所述前滚轮设置于前滚轮右安装板和前滚轮左安装板上;所述编码器设置于前轮滚轮右安装板上,所述编码器的输入轴与前滚轮连接。
11.进一步地,所述耦合剂开合机构包括:安装座、线缆调整螺栓、柔性拖拽线缆、导向滚轮安装座、导向滚轮、第三固定螺栓、开合挡片限位挡块、复位弹簧、开合挡片、耦合剂开合机构安装槽、复位挡块、复位挡块固定螺栓,所述安装座设置于四连杆上,所述线缆调整螺栓设置于安装座的螺纹孔上,所述柔性拖拽线缆的一端与线缆调整螺栓连接,另一端绕过导向滚轮的线缆导向槽,穿过开合挡片限位挡块、复位弹簧与开合挡片连接;所述导向滚轮设置于导向滚轮安装座上,所述导向滚轮安装座设置于底盘上;所述开合挡片限位挡块通过第三固定螺栓设置于耦合剂开合机构安装槽的右端面上,所述耦合剂开合机构安装槽设置于测厚仪的下方,所述复位挡块通过复位挡块固定螺栓设置于耦合剂开合机构安装槽的左端面上;所述开合挡片限位挡块通过第三固定螺栓安装在耦合剂开合机构安装槽的右端面上;所述开合挡片设置于耦合剂开合机构安装槽的导向槽里。
12.进一步地,所述第一滚轮包括:第一耐磨滚轮、第一耐磨滚轮固定螺栓、第一滚轮旋转套、第一轴承压板固定螺栓、第一轴承压板、第一轴承挡圈、第一滚动轴承、第二滚动轴承、第二轴承挡圈、第一滚轮转轴、第一滚轮转轴锁紧螺钉,所述第一耐磨滚轮为圆锥形结构,所述第一耐磨滚轮与第一滚轮旋转套通过第一耐磨滚轮固定螺栓固定连接,所述滚轮旋转套的上端轴承孔与第二滚动轴承的外圈配合,并通过第二轴承挡圈挡住,所述第二滚动轴承的内圈与第一滚轮转轴的下端配合,并通过第一轴承压板和第一轴承压板固定螺栓紧固锁死;所述第一滚轮旋转套的下端轴承孔与第一滚动轴承的外圈配合,并通过第一轴承挡圈挡住,所述第一滚动轴承的内圈与第一滚轮转轴的下端配合,所述第一滚轮转轴与左轮滚轴配合,并通过第一滚轮转轴锁紧螺栓紧定锁死;
13.所述第二滚轮包括:第二耐磨滚轮、第二耐磨滚轮固定螺栓、第二滚轮旋转套、第二轴承压板固定螺栓、第二轴承压板、第三轴承挡圈、第三滚动轴承、第四滚动轴承、第四轴承挡圈、第二滚轮转轴、第二滚轮转轴锁紧螺钉,所述第二耐磨滚轮为圆锥形结构,所述第二耐磨滚轮与第二滚轮旋转套通过第二耐磨滚轮固定螺栓固定连接,所述第二滚轮旋转套的上端轴承孔与第四滚动轴承的外圈配合,并通过第四轴承挡圈挡住,所述第四滚动轴承的内圈与第二滚轮转轴的下端配合,并通过第二轴承压板、第二轴承压板固定螺栓紧固锁死;所述第二滚轮旋转套的下端轴承孔与第三滚动轴承的外圈配合,并通过第三轴承挡圈挡住,所述第三滚动轴承的内圈与第二滚轮转轴的下端配合,所述第二滚轮转轴与右轮滚轴配合,并通过第二滚轮转轴锁紧螺钉紧定锁死。
14.进一步地,所述光电定位机构包括:光电传感器、传感器安装板、安装板调整垫块、磁铁、磁铁安装块,所述安装板调整垫块设置于传感器安装板与四连杆固定座之间,所述光电传感器设置于传感器安装板的弧形腰槽内,所述磁铁安装块设置于前轮右支撑架上,所述磁铁镶嵌于磁铁安装块上。
15.进一步地,所述机械限位机构包括:机械限位支撑挡块、第一螺栓、机械限位挡块、第二螺栓,所述机械限位挡块通过第二螺栓安装在前轮左支撑架上,所述机械限位支撑挡块通过第一螺栓设置于四连杆固定座左侧安装平面上,当测量机架停止测量升起时,机械限位支撑挡块与机械限位挡块接触;所述机械限位支撑挡块为l型结构,l型结构底面与与前轮左支撑架的上平面之间设计有底盘浮动最大距离。
16.与现有技术相比,本发明具有如下有益效果:本发明用于球墨铸管壁厚检测的三轮自适应小车在底盘上设有耦合剂开合机构,通过四连杆调整机构的升降实现耦合剂开合机构的开合,四连杆调整机构安装在测量机架上,可以保证三轮小车沿球墨铸管轴向运动时,在自身重力的作用下始终贴合球墨铸管管道的表面,保证了安装在底盘上的测厚仪始终保持与被检测管道表面的垂直,距离恒定。另外,三轮自适应小车在检测过程中要能够适应球墨铸管管道的空间变化的表面,需要偏摆、旋转、上下浮动等运动,底盘的偏摆通过底盘连接轴与前轮支撑横梁之间的相对旋转以及限位结构将偏摆角度范围限制在正负5
°
以内,底盘的旋转则通过底盘连接轴与底盘之间的相对旋转以及限位结构将旋转角度范围限位槽限制在正负5
°
以内。为了缓冲底盘的偏摆和旋转动作浮动,设有阻尼簧片,保证测量时底盘运行的平稳性。底盘的上下浮动通过四连杆调整机构实现,利用自身重力的作用下始终贴合球墨铸管管道的表面,保证了安装在底盘上的测厚仪始终保持与被检测管道表面的垂直,距离恒定。滚轮对称开合机构采用倒“y”布局的气动传动结构设计,通过气动装置实
现耐磨滚轮对称开合,通过调整滚轮开合角度,适应同一个生产线上不同球墨铸管管道规格,保证底盘基座在检测不同规格的管道时检测仪对球墨铸管检测技术指标的一致性。本发明用于球墨铸管壁厚检测的三轮自适应小车具有结构紧凑、设计简单、易于装配、维护成本低、适应能力强、抗震能力强的特点。
附图说明
17.图1为本发明用于球墨铸管壁厚检测的三轮自适应小车的结构示意图,其中,图1中的(a)为主视图,图1中的(b)为侧视图;
18.图2为本发明中滚轮开合机构的结构示意图;
19.图3为本发明用于球墨铸管壁厚检测的三轮自适应小车的剖视图;
20.图4为本发明中簧片结构示意图;
21.图5为本发明中四连杆调整机构的示意图;
22.图6为本发明中四连杆调整机构的俯视图;
23.图7为本发明中光电传感器的示意图,其中,图7中的(a)为侧视图,图7中的(b)为主视图;
24.图8为本发明中第一滚轮、第二滚轮的结构示意图;
25.图9为本发明停止工作时机械限位结构位置示意图;
26.图10为本发明工作时机械限位结构位置示意图;
27.其中,1.底盘,2.耐磨滚轮对称开合机构,3.测厚仪,4.阻尼簧片,5.四连杆调整机构,6.前轮,7.底盘连接轴,8.耦合剂开合机构,9.第一滚轮,10.第二滚轮,11.光电定位机构,12.机械限位机构,13-球墨铸管,2-1.气缸,2-2.气缸伸缩杆,2-3.气缸安装座,2-4.销轴,2-5.右轮伸缩轴,2-6.右轮伸缩套,2-7.左轮滚轴,2-8.右轮滚轴,2-9.左轮伸缩套,2-10.左轮伸缩轴,2-11.升降杆,2-12.锁紧螺母,4-1.弹性簧片,4-2.连接螺栓,4-3.柔性连接板,4-4.第一固定螺栓,5-1.四连杆固定座,5-2.左上连杆,5-3.四连杆,5-4.旋转轴压板固定螺栓,5-5.旋转轴压板,5-6.右上连杆,5-7.旋转轴,5-8.第一轴承,6-1.前轮右支撑架,6-2.支撑架固定横梁连接螺栓,6-3.支撑架固定横梁,6-4.前轮左支撑架,6-5.前滚轮,6-6.编码器,6-7.前轮滚轮右安装板,6-8.右连接板,6-9.左连接板,6-10.左连接板固定螺栓,6-11.右连接板固定螺栓,6-12.前滚轮左安装板,7-1.旋转螺栓转轴,7-2.连接轴,7-3.第二轴承,7-4.第五轴承挡圈,7-5.第三轴承压板,7-6.第三轴承压板固定螺栓,8-1.安装座,8-2.线缆调整螺栓,8-3.柔性拖拽线缆,8-4.导向滚轮安装座,8-5.导向滚轮,8-6.第三固定螺栓,8-7.开合挡片限位挡块,8-8.复位弹簧,8-9.开合挡片,8-10.耦合剂开合机构安装槽,8-11.复位挡块,8-12.复位挡块固定螺栓,9-1.第一耐磨滚轮,9-2.第一耐磨滚轮固定螺栓,9-3.第一滚轮旋转套,9-4.第一轴承压板固定螺栓,9-5.第一轴承压板,9-6.第一轴承挡圈,9-7.第一滚动轴承,9-8.第二滚动轴承,9-9.第二轴承挡圈,9-10.第一滚轮转轴,9-11.第一滚轮转轴锁紧螺钉,10-1.第二耐磨滚轮,10-2.第二耐磨滚轮固定螺栓,10-3.第二滚轮旋转套、10-4.第二轴承压板固定螺栓,10-5.第二轴承压板,10-6.第三轴承挡圈,10-7.第三滚动轴承,10-8.第四滚动轴承,10-9.第四轴承挡圈,10-10.第二滚轮转轴,10-11.第二滚轮转轴锁紧螺钉,11-1.光电传感器,11-2.传感器安装板,11-3.安装螺钉,11-4.安装板调整垫块,11-5.磁铁,11-6.磁铁安装块,12-1.机械限位支撑挡块,12-2.第一
螺栓,12-3.机械限位挡块,12-4.第二螺栓。
具体实施方式
28.下面结合附图对本发明的技术方案作进一地解释说明。
29.如图1、3为本发明用于球墨铸管壁厚检测的三轮自适应小车的结构示意图,其中,图1中的(a)为主视图,图1中的(b)为侧视图,该三轮自适应小车包括:底盘1、耐磨滚轮对称开合机构2、测厚仪3、阻尼簧片4、四连杆调整机构5、前轮6、底盘连接轴7、耦合剂开合机构8、第一滚轮9、第二滚轮10、光电定位机构11、机械限位机构12、测量机架,底盘1上设有呈对称开合的第一滚轮9和第二滚轮10,第一滚轮9、第二滚轮10均与耐磨滚轮对称开合机构2连接,第一滚轮9和第二滚轮10通过对称开合机构2根据被检测工件直径确定开合角度,确保安装在底盘1上的侧厚仪3与待检测的球墨铸管13表面垂直,距离恒定;前轮6通过底盘连接轴7与底盘1连接,底盘1可实现偏摆、旋转,使得在重力的作用下第一滚轮9和第二滚轮10始终与待检测的球墨铸管13表面贴合;测厚仪3固定于底盘1上,耦合剂开合机构8通过四连杆调整机构5设置于底盘1上,耦合剂开合机构8通过四连杆调整机构5的升降实现耦合剂开合机构8的开合,四连杆调整机构5与测量机架连接,底盘1的上下浮动通过四连杆调整机构5实现,保证三轮小车沿球墨铸管13轴向运动时,在自身重力的作用下始终贴合球墨铸管13管道的表面;为了缓冲底盘1的偏摆和旋转动作浮动,设置阻尼簧片4,阻尼簧片4设置于底盘1和四连杆调整机构5之间,并与四连杆调整机构5固定连接,保证测量时底盘1运行的平稳性;机械限位机构12分别与四连杆调整机构5、前轮6固定连接,光电定位机构11设置于四连杆调整机构5上。将三轮自适应小车固定到测量机架上,进行球墨铸管13的壁厚检测。
30.如图2,本发明中耐磨滚轮对称开合机构2包括:气缸2-1、气缸伸缩杆2-2、气缸安装座2-3、销轴2-4、右轮伸缩轴2-5、右轮伸缩套2-6、左轮滚轴2-7、右轮滚轴2-8、左轮伸缩套2-9、左轮伸缩轴2-10、升降杆2-11、锁紧螺母2-12,气缸安装座2-3固定安装于底盘1上,气缸2-1设置于气缸安装座2-3上,气缸伸缩杆2-2与气缸2-1配合,气缸伸缩杆2-2与升降杆2-11连接,且气缸伸缩杆2-2与升降杆2-11通过锁紧螺母2-12锁紧固定,防止松动;左轮伸缩轴2-10的一端、右轮伸缩轴2-5一端上均设有销孔,销孔通过销轴2-4与升降杆2-11铰连;左轮伸缩轴2-10的另一端的外圆柱面与左轮伸缩套2-9的内圆柱面配合,左轮伸缩轴2-10与左轮伸缩套2-9组合成直线运动副,左轮伸缩套2-9与左轮滚轴2-8通过螺栓和压板固定连接,左轮滚轴2-8与第一滚轮9通过螺栓固定连接;右轮伸缩轴2-5的另一端的外圆柱面与右轮伸缩套2-6的内圆柱面配合,右轮伸缩轴2-5与右轮伸缩套2-6组成直线运动副,右轮伸缩套2-6与右轮滚轴2-7通过螺栓和压板固定连接,右滚轮轴2-7与第二滚轮10通过螺栓固定连接。本发明中气缸伸缩杆2-2在气缸2-1的控制下实现伸缩时,将气缸2-1的直线运动转化为第一滚轮9和第二滚轮10的旋转运动。本发明中的耐磨滚轮对称开合机构2采用倒“y”布局的气动传动结构设计,通过气缸实现对第一滚轮9、第二滚轮10的对称开合,结构设计简单;另外,由于生产线检测球墨铸管13管道规格较多,直径变化较大,倒“y”形耐磨滚轮对称开合机构2为该三轮自适应小车使用不同管道规格的检测时,提供了底盘1升降空间,同时,保证底盘1在检测不同规格的球墨铸管13管道时测厚仪3对球墨铸管检测技术指标的一致性。
31.为了缓冲底盘1的偏摆和旋转动作浮动,设计了各向异性的阻尼簧片4,保证测量
时底盘1运行的平稳性。如图4,本发明中阻尼簧片4包括:弹性簧片4-1、柔性连接板4-3,弹性簧片4-1的一端与柔性连接板4-3的一端通过连接螺栓4-2连接,弹性簧片4-1的另一端设置于底盘1上平面上的限位槽接触,柔性连接板4-3通过第一固定螺栓4-4与四连杆调整机构5固定连接。通过各向异性的阻尼簧片4,既保证了底盘1在测量时放置上下跳动,又保证球墨铸管13检测时,底盘1偏摆、旋转等运动时的缓冲阻尼的作用,偏摆、旋转角度越大,缓冲阻尼作用越明显,从而使运动平稳可靠。
32.底盘的上下浮动通过四连杆调整机构5实现,利用自身重力的作用下始终贴合球墨铸管13管道的表面,保证了安装在底盘1上的测厚仪3始终保持与被检测管道表面的垂直,距离恒定。如图5-6,本发明中四连杆调整机构5包括:四连杆固定座5-1、左上连杆5-2、四连杆5-3、旋转轴压板固定螺栓5-4、旋转轴压板5-5、右上连杆5-6、旋转轴5-7、第一轴承5-8,四连杆固定座5-1与测量机架通过螺栓固定连接,左上连杆5-2通过第一转轴一端与四连杆固定座5-1连接,实现左上连杆5-2与四连杆固定座5-1的相对转动,第一转轴的另一端与前轮左支撑架6-4连接,实现第一转轴与前轮左支撑架6-4的相对转动;右上连杆5-6通过第二转轴一端与四连杆固定座5-1连接,实现右上连杆5-6与四连杆固定座5-1的相对转动,第二转轴的另一端与前轮右支撑架6-1连接,实现第二转轴与前轮右支撑架6-1的相对转动,从而使得前轮6在四连杆5-3的作用下,实现上下浮动;四连杆5-3通过第三转轴一端与四连杆固定座5-1连接,实现四连杆5-3与四连杆固定座5-1的相对转动,第三转轴的另一端与前轮左支撑架6-4连接,实现第三转轴与前轮左支撑架6-4的相对转动;四连杆固定座5-1上设有轴承安装孔,第一轴承5-8的外圈与轴承安装孔配合,第一轴承5-8的内圈与旋转轴5-7连接,旋转轴5-7与右上连杆5-6上的转轴安装孔配合,为了防止二者之间的相对旋转和轴向窜动,通过旋转轴压板5-5和旋转轴压板固定螺栓5-4紧固锁死,右上连杆5-6绕第一轴承5-8转动。右上连杆5-6的另一端才利用同样的结构,同时,四连杆5-3的其他转轴采用同样的结构,可实现底盘1随球墨铸管13的管道上下波动的随动补偿。四连杆5-3与柔性连接板4-3通过第一固定螺栓4-4固定连接。
33.如图7,本发明中前轮6包括:前轮右支撑架6-1、支撑架固定横梁6-3、前轮左支撑架6-4、前滚轮6-5、编码器6-6、前轮滚轮右安装板6-7、右连接板6-8、左连接板6-9、左连接板固定螺栓6-10、右连接板固定螺栓6-11、前滚轮左安装板6-12,前轮右支撑架6-1通过支撑架固定横梁连接螺栓6-2固定连接于支撑架固定横梁6-3的右端面,前轮右支撑架6-1通过右连接板6-8与前滚轮右安装板6-7连接,并通过右连接板固定螺栓6-11固定;前轮左支撑架6-4固定连接于支撑架固定横梁6-3的左端面,前轮左支撑架6-4通过左连接板6-9与前轮滚轮左安装板6-12连接,并通过左连接板固定螺栓6-10固定,前滚轮6-5设置于前滚轮右安装板6-7和前滚轮左安装板6-12上,方便更换;编码器6-6设置于前轮滚轮右安装板6-7上,编码器6-6的输入轴与前滚轮6-5连接。测量时,利用前滚轮6-5的转动,可以获得三轮自适应小车的行走距离;同时,前滚轮6-5始终与检测的球墨铸管13管道的表面相切,无论检测的球墨铸管13管道的表面在空间如何变化时,都可以保证安装在底盘1上的测厚仪3始终保持与被检测管道表面的垂直,距离恒定。
34.为了限制底盘1的上下浮动幅度,设有机械限位机构12,本发明中机械限位机构12包括:机械限位支撑挡块12-1、第一螺栓12-2、机械限位挡块12-3、第二螺栓12-4,机械限位挡块12-3通过第二螺栓12-4安装在前轮左支撑架6-4上,机械限位支撑挡块12-1通过第一
螺栓12-2设置于四连杆固定座5-1左侧安装平面上,如图9,四连杆固定座5-1升起时,机械限位支撑挡块12-1与机械限位挡块12-3接触在一起,限制底盘1的同时将耦合剂开合机构8切换至关闭状态;如图10,机械限位支撑挡块12-1为l型结构,l型结构底面与前轮左支撑架6-4的上平面之间设计有底盘浮动最大距离,检测时,四连杆固定座5-1安装在检测机架上,上下固定不动,底盘1随检测铸管表面上下浮动,机械限位支撑挡块12-1下底面与前轮左支撑架6-4的上平面的间隔距离,限定了底盘1检测时的上下浮动的幅度,使得三轮自适应小车工作时,防止底盘1脱离球墨铸管13管道表面。
35.本发明三轮自适应小车在检测过程中能够适应球墨铸管13管道的空间变化的表面,需要实现偏摆、旋转、上下浮动等运动,底盘1通过底盘连接轴7实现底盘1的偏摆和旋转动作,如图3,本发明中底盘连接轴7包括:旋转螺栓转轴7-1、连接轴7-2、第二轴承7-3、第五轴承挡圈7-4、第三轴承压板7-5,连接轴7-2的一端上设有转轴孔,转轴孔通过旋转螺栓转轴7-1与底盘1连接,连接轴7-2的另一端设有轴承安装圆柱面,轴承安装圆柱面与第二轴承7-3的内圈连接,第三轴承压板7-5设置于轴承安装圆柱面的端面上,并通过第三轴承压板固定螺栓7-6紧固连接;第二轴承7-3的外圈设置于前轮支撑横梁6-3的轴承安装孔内,第五轴承挡圈7-4设置于前轮支撑横梁6-3的轴承挡圈安装槽内,连接轴7-2上设有弧形摆动限位结构,与前轮支撑横梁6-3上的弧形限位槽配合,使得连接轴7-2与支撑架固定横梁6-3之间的相对旋转以及限位结构将偏摆角度范围限制在正负5
°
以内,底盘1的旋转则通过连接轴7-2与底盘1之间的相对旋转以及限位结构将旋转角度范围限位槽限制在正负5
°
以内。
36.为了实现测厚仪3中耦合剂的通断,快速排出耦合剂室内的空气,节约测量时耦合剂的消耗,提高检测响应时间,设有耦合剂开合机构8。如图3,本发明中耦合剂开合机构8包括:安装座8-1、线缆调整螺栓8-2、柔性拖拽线缆8-3、导向滚轮安装座8-4、导向滚轮8-5、第三固定螺栓8-6、开合挡片限位挡块8-7、复位弹簧8-8、开合挡片8-9、耦合剂开合机构安装槽8-10、复位挡块8-11、复位挡块固定螺栓8-12,安装座8-1设置于四连杆5-3上,线缆调整螺栓8-2设置于安装座8-1的螺纹孔上,柔性拖拽线缆8-3的一端与线缆调整螺栓8-2连接,另一端绕过导向滚轮8-5的线缆导向槽,穿过开合挡片限位挡块8-7、复位弹簧8-8与开合挡片8-9连接;导向滚轮8-5设置于导向滚轮安装座8-4上,导向滚轮安装座8-4设置于底盘1上;开合挡片限位挡块8-7通过第三固定螺栓8-6设置于耦合剂开合机构安装槽8-10的右端面上,耦合剂开合机构安装槽8-10设置于测厚仪3的下方,复位挡块8-11通过复位挡块固定螺栓8-12设置于耦合剂开合机构安装槽8-10的左端面上;开合挡片限位挡块8-7通过第三固定螺栓8-6安装在耦合剂开合机构安装槽8-10的右端面上;开合挡片8-9设置于耦合剂开合机构安装槽8-10的导向槽里。通过调整线缆调整螺栓8-2可以室使耦合剂开合机构8调整至工作状态或停止状态;耦合剂开合结构8通过螺栓安装在测厚仪3的下方,工作前,测厚仪3需要先充满耦合剂,排出空气,这时,在四连杆5-3的作用下,开合挡片8-9处于关闭位置,将耦合剂注入测厚仪3内,在耦合剂的作用下,空气快速排出;测量时,四连杆机构5降至工作位置,开合挡片8-9在复位弹簧8-8的作用下切换至打开位置,大大提高了测量的稳定性。
37.如图8,本发明中第一滚轮9包括:第一耐磨滚轮9-1、第一耐磨滚轮固定螺栓9-2、第一滚轮旋转套9-3、第一轴承压板固定螺栓9-4、第一轴承压板9-5、第一轴承挡圈9-6、第一滚动轴承9-7、第二滚动轴承9-8、第二轴承挡圈9-9、第一滚轮转轴9-10、第一滚轮转轴锁紧螺钉9-11,第一耐磨滚轮9-1与第一滚轮旋转套9-3通过第一耐磨滚轮固定螺栓9-2固定
连接,可以快速便捷的更换第一耐磨滚轮9-1;滚轮旋转套9-3的上端轴承孔与第二滚动轴承9-8的外圈配合,并通过第二轴承挡圈9-9挡住,限制轴向窜动,第二滚动轴承9-8的内圈与第一滚轮转轴9-10的下端配合,并通过第一轴承压板9-5和第一轴承压板固定螺栓9-4紧固锁死;第一滚轮旋转套9-3的下端轴承孔与第一滚动轴承9-7的外圈配合,并通过第一轴承挡圈9-6挡住,限制轴向窜动,第一滚动轴承9-7的内圈与第一滚轮转轴9-10的下端配合,第一滚轮转轴9-10与左轮滚轴2-7配合,并通过第一滚轮转轴锁紧螺栓9-11紧定锁死,在耐磨滚轮对称开合机构2的动作下完成第一滚轮9-1的角度的改变,以适应同一生产线上不同规格管道的检测。本发明中第二滚轮10包括:第二耐磨滚轮10-1、第二耐磨滚轮固定螺栓10-2、第二滚轮旋转套10-3、第二轴承压板固定螺栓10-4、第二轴承压板10-5、第三轴承挡圈10-6、第三滚动轴承10-7、第四滚动轴承10-8、第四轴承挡圈10-9、第二滚轮转轴10-10、第二滚轮转轴锁紧螺钉10-11,第二耐磨滚轮10-1与第二滚轮旋转套10-3通过第二耐磨滚轮固定螺栓10-2固定连接,可以快速便捷的更换第二耐磨滚轮10-1;第二滚轮旋转套10-3的上端轴承孔与第四滚动轴承10-8的外圈配合,并通过第四轴承挡圈10-9挡住,限制轴向窜动,第四滚动轴承10-8的内圈与第二滚轮转轴10-10的下端配合,并通过第二轴承压板10-5、第二轴承压板固定螺栓10-4紧固锁死;第二滚轮旋转套10-3的下端轴承孔与第三滚动轴承10-7的外圈配合,并通过第三轴承挡圈10-6挡住,限制轴向窜动,第三滚动轴承10-7的内圈与第二滚轮转轴10-10的下端配合,第二滚轮转轴10-10与右轮滚轴2-8配合,并通过第二滚轮转轴锁紧螺钉10-11紧定锁死,在耐磨滚轮对称开合机构2的动作下完成第二耐磨滚轮10-1的角度的改变,以适应同一生产线上不同规格管道的检测。本发明中第一耐磨滚轮9-1、第二耐磨滚轮10-1均为圆锥形结构,使得第一耐磨滚轮9-1、第二耐磨滚轮10-1与不同规格不同直径的球墨铸管13管道表面相切滚动运行时,底盘1相对于球墨铸管13管道表面升降高度变化较小,大大提高了运行的稳定性,可以适应多种规格的球墨铸管13管道的厚度检测。另外,耐磨滚轮通过螺栓固定在车轮旋转套上的机构设计,可以快速便捷的更换耐磨滚轮。车轮转轴通过紧定螺钉与滚轮转轴实现固定连接,在滚轮开合机构的动作下完成滚轮角度的改变,以适应同一生产线上不同规格管道的检测。
38.为了实现对三轮自适应小车在测量时的状态检测,设计有光电定位机构11,如图7,本发明中光电定位机构11包括:光电传感器11-1、传感器安装板11-2、安装螺钉11-3、安装板调整垫块11-4、磁铁11-5、磁铁安装块11-6,安装板调整垫块11-4设置于传感器安装板11-2与四连杆固定座5-1之间,并用安装螺钉11-3实现相互之间的固定连接,四连杆固定座5-1的上下位置通过光电传感器11-1的信号确定,当光电传感器11-1输出信号时,测量机架工作在检测位置,测量时,四轮杆固定座5-1上下位置固定;光电传感器11-1设置于传感器安装板11-2的弧形腰槽内,磁铁安装块11-6设置于前轮右支撑架6-1上,磁铁11-5镶嵌于磁铁安装块11-6上。测量时,三轮自适应行走小车的状态通过光电传感器11-1进行监测,第一滚轮9和第二滚轮10根据待测量球墨铸管13管道规格确定开合角度,三轮自适应小车由机架降落至球墨铸管13管道上。
39.球墨铸管壁厚检测三轮自适应小车通过四连杆固定座5-1安装在检测机架y轴的安装架上。在线实时检测过程中,三轮自适应小车根据检测生产线上待检测的管道规格,通过耐磨滚轮对称开合机构2对称打开第一滚轮9和第二滚轮10,保证测厚仪3始终与待测量球墨铸管13管道表面垂直,距离恒定。具体工作过程如下:
40.(1)三轮自适应小车上电、通气后,耐磨滚轮对称开合机构2根据待测量球墨铸管13管道的规格型号,通过控制气缸伸缩杆2-2将动力输出给升降杆2-11,升降杆2-11通过销轴2-4分别与右轮伸缩轴2-5和左轮伸缩轴2-10铰链,进而通过分别与之配合的右轮伸缩套2-6和左轮伸缩套2-9将升降杆2-11的上下移动转换成第一滚轮9和第二滚轮10的对称旋转开合运动,其开合角度由管道规格确定;底盘1在重力的作用下,机械限位支撑挡块12-1与机械限位挡块12-3贴合在一起,限制了底盘向下运动;同时,耦合剂开合挡片8-9处于关闭状态;
41.(2)三轮自适应小车在检测机架测控制下,移动到待检测管道上方的检测位置后,慢慢落下y轴检测机架,当前轮6与待测量球墨铸管13管道接触后,继续下降y轴检测机架,在四连杆5-3的作用下,光电传感器11-1慢慢向磁铁11-5移动,当光电传感器11-1有输出信号后,y轴检测机架停止下降,此时,底盘1正好处于水平检测位置;弹性簧片4-1的另一端与底盘1上平面上的限位槽接触;耦合剂开合挡片8-9在复位弹簧8-8的作用下切换至打开状态;充分利用四连杆机构运动特点和底盘自身的重力以及复位弹簧的弹力,实现了柔性拖拽线缆8-3的伸缩,巧妙的实现了工作时打开开合挡片8-9,停止时,关闭开合挡片8-9。待测厚仪3的检测信号正常后,即可开始在线检测。
42.(3)开始测量时,三轮自适应小车则保证了测量球墨铸管管道13壁厚时,能够根据球墨铸管管道13的表面空间随机变化,自适应调整。前轮6始终与待测量球墨铸管13最上表面相切,保证了安装在底盘1上的测厚仪3始终保持与被检测球墨铸管管道13表面的垂直,且距离恒定。第一滚轮9和第二滚轮10与检测管道表面相切,沿管表面滚动,保证在线检测时运行的平稳性。与前轮6转轴相连的编码器6-6测量的位置信号与测厚仪3测量的厚度信号一一对应,传送至检测装置控制系统。自适应调整的实现方式如下:三轮自适应小车在检测过程中能够适应球墨铸管13管道的空间变化的表面,需要实现偏摆、旋转、上下浮动等运动。管道上下浮动时,四连杆固定座5-1安装在检测机架y轴的安装架上,上下固定不动,底盘1在自身重力的作用下利用,四连杆机构的结构特点,可以根据管道表面的上下起伏,被动适应上下浮动。另外,机械限位支撑挡块12-1为l型结构,l型结构底面与与前轮左支撑架6-4的上平面之间设计有底盘浮动最大距离,限定了底盘1检测时的上下浮动的幅度,使得三轮自适应小车工作时,防止底盘1剧烈振动,脱离球墨铸管13管道表面。另外,由于前后轮之间存在一定的距离,当前后轮左右偏摆时和相对旋转时,连接轴7-2与支撑架固定横梁6-3之间的相对旋转以及限位结构将偏摆角度范围限制在正负5
°
以内,底盘1的旋转则通过连接轴7-2与底盘1之间的相对旋转以及限位结构将旋转角度范围限位槽限制在正负5
°
以内。
43.(4)测量完成后,升起y轴测量机架,利用自身结构的特点,机械限位支撑挡块12-1与机械限位挡块12-3贴合在一起后,底盘处于锁定稳定状态,此时,耦合剂开合挡片8-9切换至关闭状态,控制测量机架,运动至初始位置,重复下一球墨铸管管道的检测。
44.以上仅是本发明的优选实施方式,本发明的保护范围并不仅局限于上述实施方式,凡属于本发明思路下的技术方案均属于本发明的保护范围。应当指出,对于本技术领域的普通技术人员来说,在不脱离本发明原理前提下的若干改进和润饰,应视为本发明的保护范围。