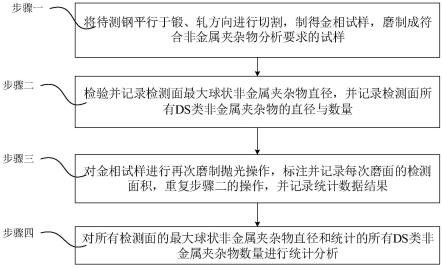
1.本发明涉及金相组织检测技术领域,尤其涉及一种用于大尺寸非金属夹杂物检测方法。
背景技术:2.非金属夹杂物是钢中必然存在的产物,由于大型夹杂物对钢材性能的有害影响,人们主要将注意力集中在大型夹杂物上,但由于大型夹杂物的低发生率和无损检测的局限性,它们通常很难检测,尤其是在特别是一些大体积钢结构件(如大锻件)中。
3.目前的测量方法为采用小样品进行夹杂物观察,所以存在很大的偶然性;另外,金相小样品夹杂物检测评级只能反应取样样品的夹杂物水平,而不能反应大体积钢中夹杂物水平,并且主流的最恶劣视场检验非金属夹杂物级别的方法(如gb/t 10561-2005/iso 4967:1998中a法)只能表征在检验过程中观察到的非金属夹杂物最高级别,难以同时兼顾夹杂物分布密集程度和夹杂物尺寸大小,因此,通过基于一些统计分析的预测来获得大尺寸夹杂物数量、尺寸分布的结果,能够客观反映大尺寸夹杂物在钢中的分布规律与纯净度。
技术实现要素:4.针对现有算法的不足,本发明能够客观的反映大尺寸夹杂物在钢中的分布规律与纯净度。
5.本发明所采用的技术方案是:一种用于大尺寸非金属夹杂物检测方法包括以下步骤:
6.步骤一、将待测钢平行于锻、轧方向进行切割,制得金相试样,磨制成符合非金属夹杂物分析要求的试样;
7.进一步的,每个横向的金相试样应检测面积在160mm2以上;
8.进一步的,磨制的方法为:先依次使用320目、600目和1000目砂纸研磨金相试样的待检测面,之后再用3.5μm粒度的金相抛光剂对金相试样的待检测面进行抛光。
9.步骤二、检验并记录检测面最大球状非金属夹杂物直径,并记录检测面所有ds类非金属夹杂物的直径与数量;
10.进一步的,非金属夹杂物的直径为费雷特直径;
11.步骤三、对金相试样进行再次磨制抛光操作,标注并记录每次磨面的检测面积,重复步骤二的操作,并记录统计数据结果;
12.进一步的,再次磨制时至少去除0.3mm的材料,形成一个新的检验面;
13.进一步的,最少检验24个检测面积;
14.步骤四、对所有检测面的最大球状非金属夹杂物直径和统计的所有ds类非金属夹杂物数量进行统计分析;
15.进一步的,详细包括:
16.首先,依据检测的夹杂物个数与夹杂物尺寸,计算得到累计概率密度;
17.其次,对最大极值法的累计密度函数进行简化,推导出累计密度函数的反函数,并计算简约变量y;
18.最后,根据尺度参数δ与位置参数λ,利用最大极值法得到最大夹杂物尺寸x。
19.进一步的,最大极值法的一般方程式为:
20.x=δ*y+λ(8)
21.其中,δ为尺度参数,λ为位置参数,y为简约变量。
22.本发明的有益效果:
23.1、可在观测区域内获取足够数量的视场,保证检测结果的代表性;
24.2、可根据统计学原理,客观表征钢中整体夹杂物的信息,给出大尺寸夹杂物的分布规律、纯净度等综合评价结果,为钢材的生产、研发、加工以及使用等提供精确的夹杂物数据支撑;
25.3、传统极值分析法,仅能依据试样中最大的夹杂物尺寸推断钢中最大的夹杂物尺寸分布情况,不能反映出某一炉钢ds夹杂物的数量密度分布情况;传统ds夹杂物评级,由于取样数量少且仅根据最大的ds夹杂物进行评级,不能反映出某一炉钢的真是ds夹杂物水平;本方法在极值统计分析的同时,不仅记录最大的点状夹杂物尺寸,同时记录所有≥13μm的夹杂物数量及尺寸,确保预测极值尺寸的同时能够评判ds夹杂物的数量密度,保证检测的有效性及准确性。
附图说明
26.图1是本发明的用于大尺寸非金属夹杂物检测方法流程图;
27.图2是本发明实施例中取样的结构示意图;
28.图3为本发明实施例中的基于最大极值分布分析方法,预测a炉钢中夹杂物尺寸sev曲线;
29.图4为本发明实施例中的基于最大极值分布分析方法,预测b炉钢中夹杂物尺寸sev曲线。
具体实施方式
30.下面结合附图和实施例对本发明作进一步说明,此图为简化的示意图,仅以示意方式说明本发明的基本结构,因此其仅显示与本发明有关的构成。
31.以a、b两炉scr420钢为例对本发明进行详细的说明。
32.如图1所示,一种用于大尺寸非金属夹杂物检测方法包括以下步骤:
33.步骤一、将待测钢平行于锻、轧方向进行切割,制得金相试样,磨制成符合非金属夹杂物分析要求的试样;
34.试样制备:将待测钢分别垂直于锻、轧方向进行切割,制得6个160mm2以上的检测面积的横向金相试样,之后依次用粒度为320目、600目、1000目的金相砂纸,在金相磨抛机上对试样的检验面进行依次研磨,每换下一道砂纸磨制时都应保证前一道砂纸磨制的划痕被磨掉,最后获得仅剩最细砂纸磨制的划痕的待检面;研磨结束后,使用3.5μm粒度的金相抛光剂对试样的待检面进行抛光,最后获得待检面光滑如镜面的金相试样备用;
35.步骤二、检验并记录检测面最大球状非金属夹杂物直径,并记录检测面所有ds类
(单颗粒球状类)非金属夹杂物的直径与数量;
36.检验并记录所述步骤一中的金相试样里所有点状夹杂物得最大夹杂物直径,并记录检测面所有超过13μm非金属夹杂物(ds类夹杂物)的直径与数量;
37.表1 a炉试样检测结果
[0038][0039][0040]
表2 b炉试样检测结果
[0041]
编号1-12-12-23-13-24-15-15-25-3夹杂物尺寸13.8314.6821.0314.4613.5512.47618.4923.7315.26编号6-17-18-18-28-39-110-110-211-1夹杂物尺寸15.4616.6520.5514.3232.7814.1316.1923.2427.31编号11-212-112-213-114-114-215-116-116-2夹杂物尺寸14.1221.7913.2412.5613.0120.0224.5117.4223.10编号16-317-118-118-219-119-219-320-121-1夹杂物尺寸13.4710.6731.4416.2217.2716.0113.9614.3915.16编号21-222-122-223-123-224-1
ꢀꢀꢀ
夹杂物尺寸13.0625.7813.5214.513.1912.517
ꢀꢀꢀ
[0042]
步骤三、对金相试样进行再次磨制抛光操作,标注并记录每次磨面的检测面积,重复步骤2的操作,最少检验24个检测面,并记录统计数据结果。
[0043]
对所述步骤一中的12个横向金相试样进行再次磨制抛光操作,磨制时应至少去除0.3mm的材料,以形成一个新的检验面,标注并记录每次磨面的检测面积,重复步骤二的操作,a、b试样分别最少检验24个检测面,并记录统计数据结果。
[0044]
步骤四、对所有检测面的最大球状非金属夹杂物直径和统计的所有ds类非金属夹杂物数量进行统计分析;
[0045]
对a、b试样的24个检测面的最大夹杂物直径进行统计记录,预测钢种最大夹杂物尺寸;
[0046]
为了找出钢中球状非金属夹杂物的最大值,采取极值分布模型的理论,钢中球状非金属夹杂物尺寸的数据集合服从正态分布,检测的非金属夹杂物尺寸为数据集中的一个随机变量,因此可以认为该数据集合的概率分布符合二元gumbel分布,其累计密度函数(cdf)为:
[0047][0048]
其中,δ是位置系数,λ是尺度系数。
[0049]
依据累计密度函数推导出其反函数为:
[0050]
f-1
(p;δ,λ)=δ-λln(-ln(p))(2)
[0051]
其中,p为依据检测的夹杂物个数与夹杂物尺寸计算得到累计概率密度,因此可以将公式简化,其中设定简约变量y与累计概率函数有关y=-ln(-ln(p));
[0052]
首先,依据检测的夹杂物个数与夹杂物尺寸,计算得到累计概率密度pi;
[0053]
累计概率密度公式pi:
[0054][0055]
其中,n是检测的夹杂物个数,夹杂物表示的是每一个检验面的最大夹杂物;i代表的是任意数据点1≤i≤n;
[0056]
使用公式(4)计算重复周期t,即找到等于或大于指定夹杂物长度的夹杂物所应观察到的区域的数量;其中,a
ref
为任意选择的进行预测的面积,本实例中为75000mm2,a0为检验测量面积,本实例中为500mm2,重复周期t为150;通过(3)公式计算出在本实例的检测面积与预测面积条件下(也就是t在150这个条件下)的最大夹杂物尺寸对应累计概率p为99.3%:
[0057]
t=1/(1-p)(4)
[0058]
t=a
ref
/a0(5)
[0059]
其次,依据最大极值法(最大极值概率分布统计模型),使用公式(6)计算简约变量y:
[0060][0061]
其中,pi为累计概率;
[0062]
最后,设定δ(尺度参数,表示分布的分散程度)与λ(位置参数,表示概率密度最大处的夹杂物尺寸),δ和λ的最大似然法分析结果用于表征数据的最佳拟合线,最后用公式(5)得出最大极值法预测的最大夹杂物尺寸x:
[0063]
x=-δ*ln(-ln(t-1)/t)+λ(7)
[0064]
一般方程式为:
[0065]
x=δ*y+λ(8)
[0066]
绘制图3、4的a、b炉的sev曲线,即最大极值法预测scr420钢中夹杂物尺寸sev曲线,通过拟合曲线得到最大极值法回归方程式分别为:
[0067]
a炉:x=4.414y+17.23;b炉:x=4.725y+16.26;
[0068]
在累计频率p=99.3%条件下,预测的最大夹杂物尺寸分别为:
[0069]
a炉:x=39.12μm;b炉:x=39.69μm;
[0070]
对步骤三中的24个检测面中所有ds类非金属夹杂物数量进行统计,本实例中同样检测面积下,a炉检测出ds类非金属夹杂物数量共61个,b炉中检测出ds类非金属夹杂物数量为38个,ds类非金属夹杂物的数量密度m分别为:(m=ds夹杂物检测的总数*1000/总检测面积)
[0071]
a炉:m=5.08(个/1000mm2);b炉:m=3.17(个/1000mm2)。
[0072]
效果对比:
[0073]
目前普遍采取依据gb/t10561-2005的非金属夹杂物的具体检验操作方法:
[0074]
试样制备:将待测钢分别沿于锻、轧方向进行切割,制得6个纵向金相试样,之后依次用粒度为320目、600目、1000目的金相砂纸,在金相磨抛机上对试样的检验面进行依次研磨,每换下一道砂纸磨制时都应保证前一道砂纸磨制的划痕被磨掉,最后获得仅剩最细砂纸磨制的划痕的待检面。研磨结束后,使用3.5μm粒度的金相抛光剂对试样的待检面进行抛光,最后获得待检面光滑如镜面的金相试样备用;
[0075]
检验整个抛光面,对于点状夹杂物按细系和粗系记下所检验面上最恶劣市场相符合的gb/t10561-2005中标准图片的级别数;两炉点状夹杂物的评级结果为:
[0076]
a炉:d(1.0级)de(0.5级)ds(1.5级);
[0077]
b炉:d(1.0级)de(0.5级)ds(1.5级);
[0078]
采取依据gb/t40281—2021的钢中非金属夹杂物含量的测定极值分析法的具体检验操作方法:
[0079]
试样制备:将待测钢分别沿于锻、轧方向进行切割,制得6个纵向金相试样,之后依次用粒度为320目、600目、1000目的金相砂纸,在金相磨抛机上对试样的检验面进行依次研磨,每换下一道砂纸磨制时都应保证前一道砂纸磨制的划痕被磨掉,最后获得仅剩最细砂纸磨制的划痕的待检面。研磨结束后,使用3.5μm粒度的金相抛光剂对试样的待检面进行抛光,最后获得待检面光滑如镜面的金相试样备用;
[0080]
对24个抛光面进行检验,筛选出每个检验面上最大非金属夹杂物尺寸,判断数据有效性,分析出δ值和λ值,计算所预测的夹杂物最大值l
max
,依据本实例t≥100,p=99.3%,适用于公式(9),其预测的夹杂物最大值l
max
的95%置信区间适用于公式(9):
[0081][0082][0083]
通过最大似然法计算出δ
ml
值和λ
ml
值,其中y=-ln(-lnp)带入公式(9)可计算出l
max
分别为a炉:l
max
=39.12
±
7.78μm;b炉:l
max
=39.69
±
8.32μm。
[0084]
对比a、b两炉无明显区别,且只能代表所取的小尺寸试样的非金属水平,通过对比,本发明方法通过对数据的统计分析,不仅能够准确的获取大体积钢中最大非金属夹杂物尺寸信息,还能获得大体积钢中大尺寸非金属纯净度的信息,更加可靠有代表性,可以广泛推广使用。
[0085]
评价方法对比结果:
[0086][0087]
以上述依据本发明的理想实施例为启示,通过上述的说明内容,相关工作人员完全可以在不偏离本项发明技术思想的范围内,进行多样的变更以及修改。本项发明的技术性范围并不局限于说明书上的内容,必须要根据权利要求范围来确定其技术性范围。