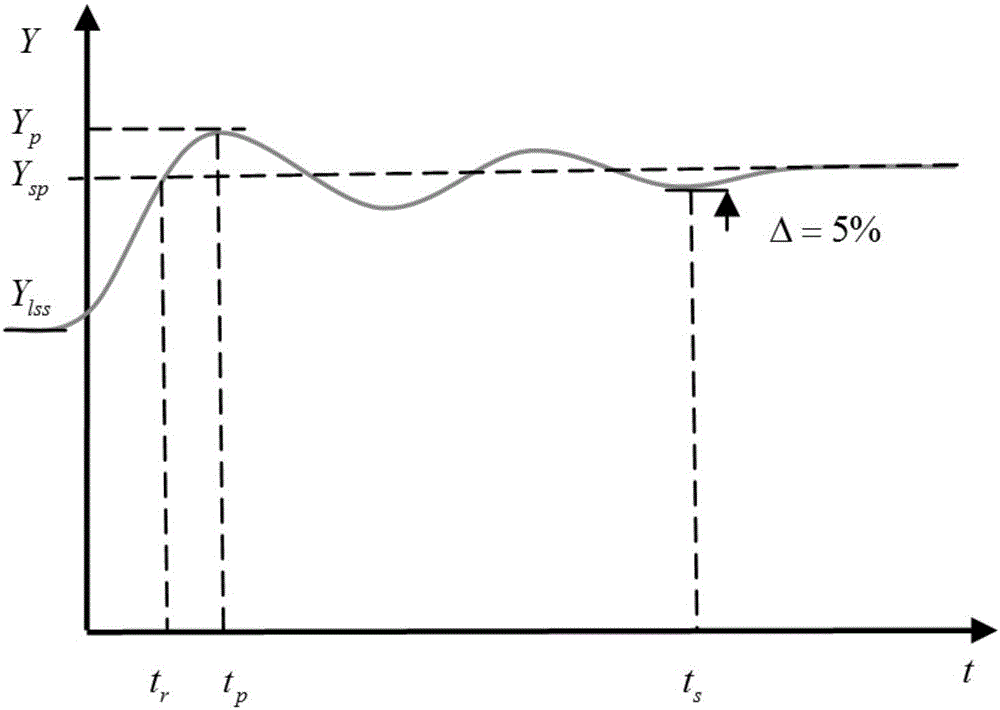
本发明属于自动化控制领域,特别涉及PID性能评估方法。
背景技术:
:据统计90%以上的自动控制回路均采用了PID(proportion-比例、integral-积分、differential-微分)控制策略。随着工业自动化水平的逐步提高,以分布式控制系统(DistributedControlSystem,DCS)为核心的大规模集散控制系统已成为工业生产必备。随着集散控制系统DCS的普及,现代工业中充斥着大量的PID控制回路,这些回路推动者生产的自动运行。这些回路在投运初期一般都具有良好的性能,但如果得不到定期的维护,其性能将随时间的推移而降低。控制回路性能不佳将降低控制回路的有效性,进而可能导致产品产量降低、不合格产品和操作成本增加等问题。但大型过程装置中通常存在大量动态特性经常发生变化的控制回路,及时发现这些性能恶化的回路需要投入大量的人力资源,而工厂中相应的维护工程师却很少,无法达到及时发现,准确维护的理想维护状态,只能任由控制性能的一步步恶化,给装置的安全平稳运行带来安全隐患。技术实现要素:为了解决现有技术中存在的缺点和不足,本发明提供了用于延长设备使用寿命、提高生产过程安全性的PID性能评估方法。为了达到上述技术目的,本发明提供了PID性能评估方法,所述评估方法,包括:获取控制回路的生产数据、以及与生产数据对应的数据质量码,根据数据质量码对生产数据进行坏值处理,得到处理后的生产数据序列;根据处理后的生产数据序列,结合预设的过程模型对控制回路的响应时间进行更新,得到更新后的响应时间;结合更新后的响应时间获取与控制回路对应的性能评价参数,根据性能评价参数确定控制回路的性能等级;其中,生产数据包括控制回路的测量值、设定值以及操作值。可选的,所述获取控制回路的生产数据、以及与生产数据对应的数据质量码,根据数据质量码对生产数据进行坏值处理,得到处理后的生产数据序列,包括:获取控制回路的生产数据中的测量值PV、设定值SV以及操作值MV。提取生产数据中的时刻值t,根据时刻值t将生产数据划分成N个数据点,得到由N个数据点构成的生产数据序列PV(t)、SV(t)以及MV(t);如果数据质量码出现坏值,确定与出现坏值的数据质量码对应的位于生产数据序列内的差错数据,对差错数据进行替换处理,得到处理后的生产数据序列。可选的,所述对差错数据进行替换处理,包括:获取差错数据的前一位数据和后一位数据,确定前一位数据与后一位数据的平均值,将差错数据替换为平均值。可选的,所述根据处理后的生产数据序列,结合预设的过程模型对控制回路的响应时间进行更新,得到更新后的响应时间,包括构建预设的过程模型output=M·input,其中output代表控制回路的实际输出时间序列,input代表控制回路的输入时间序列,M代表控制回路的过程控制函数,M=f(k,T,σ),其中k代表回路增益,T为时间常数,σ表示迟滞;建立目标优化函数对目标优化函数求解,获取令目标优化函数取得最小值的k、T、σ,其中,代表控制回路的理想输入时间序列,y代表控制回路的实际输出时间序列;基于求解后的T、σ,得到更新后的响应时间。可选的,所述性能评价参数,包括动态性能评价参数和静态性能评价参数。可选的,所述结合更新后的响应时间获取与控制回路对应的性能评价参数,根据性能评价参数确定控制回路的性能等级,包括:根据更新后的响应时间,获取包括控制回路的上升时间tr、调节时间ts以及超调量σ%在内的动态性能评价参数;将动态性能评价参数与预设动态性能参数阈值进行对比,根据对比结果,判定控制回路在动态性能方面的性能等级;可选的,所述结合更新后的响应时间获取与控制回路对应的性能评价参数,根据性能评价参数确定控制回路的性能等级,包括:根据更新后的响应时间,对处理后的生产数据序列进行频率分割,对分割后的生产数据序列进行滤波分解,获取分解后的低频段生产数据序列以及高频段生产数据序列;确定低频段生产数据序列和高频段生产数据序列在各频段的方差值,基于方差值获取高频段生产数据与包含低频段生产数据、高频段生产数据的总体数据的能量比值;将能量比值与预设稳态性能参数阈值进行对比,根据对比结果,判定控制回路在稳态性能方面的性能等级。可选的,所述评估方法,还包括:获取经验响应时间。可选的,所述评估方法,还包括:根据处理后的生产数据序列对经验响应时间进行验证;如果验证结果表明经验响应时间产生的误差低于预设阈值,则根据经验响应时间扩区与控制回路对应的性能评价参数,根据性能评价参数确定控制回路的性能等级。可选的,所述评估方法,还包括:在首次运行PID性能评估方法时,在得到处理后的生产数据序列后,结合初始设定的响应时间,获取与控制回路对应的性能评价参数,根据性能评价参数确定控制回路的性能等级;基于性能评价参数对控制回路进行调节,结合预设的过程模型对控制回路的响应时间进行更新,得到更新后的响应时间。本发明提供的技术方案带来的有益效果是:通过获取包括控制回路的测量值、设定值、操作值在内的多种数据,并且构建了用于对控制回路内的响应时间进行更新的过程模型,基于获取到的数据对控制回路的性能进行评估,同时能够基于过程模型结合获取到的多种数据对评估标准进行迭代更新,令控制回路的性能维持在合理的标准,相对于现有技术能够降低因未能及时进行人工维护导致控制性能恶化的可能性,减少控制回路出现安全隐患的概率。附图说明为了更清楚地说明本发明的技术方案,下面将对实施例描述中所需要使用的附图作简单地介绍,显而易见地,下面描述中的附图仅仅是本发明的一些实施例,对于本领域普通技术人员来讲,在不付出创造性劳动的前提下,还可以根据这些附图获得其他的附图。图1是本发明提供的PID性能评估方法的流程示意图;图2是本发明提供的动态性能指标示意图。具体实施方式为使本发明实施例的目的、技术方案和优点更为清楚,下面将结合本发明实施例中的附图,对本发明实施例中的技术方案进行清楚、完整的描述,显然,所描述的实施例是本发明一部分实施例,而不是全部的实施例。基于本发明中的实施例,本领域普通技术人员在没有做出创造性劳动前提下所获得的所有其他实施例,都属于本发明保护的范围。实施例一本发明提供了PID性能评估方法,该方法用于工业自动化过程中DCS内部动态调整,主要在包括温度、液位、流量在内的控制回路内预设相应时间模型。在调整过程中引入了包含控制回路测量值、设定值、操作值在内的生产数据,并且构建了过程模型,用于根据生产数据对DCS的响应时间进行更新,从而根据更新后的响应时间对过程进行控制,以便达到维持较佳工作状态的目的。如图1所示,该PID性能评估方法,具体包括:101、获取控制回路的生产数据、以及与生产数据对应的数据质量码,根据数据质量码对生产数据进行坏值处理,得到处理后的生产数据序列;102、根据处理后的生产数据序列,结合预设的过程模型对控制回路的响应时间进行更新,得到更新后的响应时间;103、结合更新后的响应时间获取与控制回路对应的性能评价参数,根据性能评价参数确定控制回路的性能等级;其中,生产数据包括控制回路的测量值、设定值以及操作值。在本实施例中,首先获取控制回路的生产数据,根据与生产数据对应的数据质量码对生产数据中的某些值进行替换处理,得到能够完整表征控制回路状态的处理后的生产数据序列。接着结合预设的过程模型以及处理后的生产数据序列对控制回路的响应时间进行更新,获取到更新后的响应时间,继而根据更新后的响应时间获取到控制回路的性能评价参数,最终确定控制回路的性能等级。在确定控制回路性能等级的过程中,通过获取包括控制回路的测量值、设定值、操作值在内的多种数据,并且构建了用于对控制回路内的响应时间进行更新的过程模型,基于获取到的数据对控制回路的性能进行评估,同时能够基于过程模型结合获取到的多种数据对评估标准进行迭代更新,令控制回路的性能维持在合理的标准,相对于现有技术能够降低因未能及时进行人工维护导致控制性能恶化的可能性,减少控制回路出现安全隐患的概率。具体的,在步骤101中提出了获取处理后的生产数据序列的方法,包括:获取控制回路的生产数据中的测量值PV、设定值SV以及操作值MV。提取生产数据中的时刻值t,根据时刻值t将生产数据划分成N个数据点,得到由N个数据点构成的生产数据序列PV(t)、SV(t)以及MV(t);如果数据质量码出现坏值,确定与出现坏值的数据质量码对应的位于生产数据序列内的差错数据,对差错数据进行替换处理,得到处理后的生产数据序列。在实施中,从控制回路的控制器处获取生产回路中的测量值PV、设定值SV、操作值MV,以及与三种数值分别对应的数据质量码。由于在数据获取过程中能够获取到每个数据对应的时间值t,因此根据时间值t的不同,将测量值PV、设定值SV、操作值MV划分为N个数据点,从而得到生产数据序列PV(t)、SV(t)以及MV(t)。其中,{PV(t),t=1,2,3,...N},{MV(t),t=1,2,3,...N},{SV(t),t=1,2,3,...N}。N为正整数。在获取到生产数据序列后,根据与每个生产数据序列对应的数据质量码。如果数据质量码出现了坏值,表明该数据质量验证码对应的数据为存在缺陷的差值数据。对于该类型的数据,需要使用其他方式进行替换处理,得到处理后的生产数据序列,从而去除插座数据对后续步骤中更新响应时间的影响。所述对差错数据进行替换处理,包括:获取差错数据的前一位数据和后一位数据,确定前一位数据与后一位数据的平均值,将差错数据替换为平均值。在实施中,较为常见的替换方式为获取差错数据前后一位数据的平均值,使用平均值对差错数据进行替换。当然,这里还有其他替换方式,由于不是本申请的主要内容就不再进行一一列举。可选的,步骤102中提出了基于前一步得到的处理后的生产数据序列得到更新后的响应时间的具体内容,包括在获取到处理后的生产数据序列后,需要结合预设的过程模型对控制回路的响应时间进行更新。这里预设的过程模型output=M·input,其中output代表控制回路的实际输出时间序列,input代表控制回路的输入时间序列,M代表控制回路的过程控制函数。对于过程控制函数M,具体表示为M=f(k,T,σ),其中k代表回路增益,T为时间常数,σ表示迟滞;对控制过程的优化,实质上就是选取适当的控制函数M,为了获取合适的M,这里建立了目标优化函数以对目标优化函数求解的方式,获取令目标优化函数取得最小值的k、T、σ,其中,代表控制回路的理想输入时间序列,y代表控制回路的实际输出时间序列。在得到目标优化函数取最小值时的参数后,基于求解后的T、σ,通过T+σ(即时间常数+时间迟滞)的方式,得到更新后的响应时间。在步骤103中提出的性能评价参数,包括动态性能评价参数和静态性能评价参数。具体的步骤103的内容,也是分别基于动态性能评价参数和静态性能评价参数来对控制回路的性能进行判定。当性能评价参数为动态性能评价参数时,步骤103具体包括:根据更新后的响应时间,获取包括控制回路的上升时间tr、调节时间ts以及超调量σ%在内的动态性能评价参数;将动态性能评价参数与预设动态性能参数阈值进行对比,根据对比结果,判定控制回路在动态性能方面的性能等级。在实施中,结合图2所示的动态性能指标示意图,上升时间tr:指响应从终值10%上升到终值90%所需的时间;对于有振荡的系统,亦可定义为响应从0第一次上升到终值所需的时间。上升时间越短,响应速度越快。调节时间ts:指响应到达并保持在终值±5%内所需的最短时间。超调量σ%:指响应的最大偏离量h(tp)与终值h之差的百分比,即当性能评价参数为动态性能评价参数时,每个回路自身对于过程扰动抑制能力的强弱是由回路响应时间(时滞+时间常数)的快慢所决定的,即回路的响应时间决定了回路被控能力。可以根据每个回路的响应时间,针对稳态数据中的扰动进行特征分类:分为低频扰动、中高频扰动。并通过对稳态数据中各个频段能量占比的分析,计算能量分布指标,从而对控制器的性能进行分析。基于上述理论,步骤103具体包括:根据更新后的响应时间,对处理后的生产数据序列进行频率分割,对分割后的生产数据序列进行滤波分解,获取分解后的低频段生产数据序列以及高频段生产数据序列;确定低频段生产数据序列和高频段生产数据序列在各频段的方差值,基于方差值获取高频段生产数据与包含低频段生产数据、高频段生产数据的总体数据的能量比值;将能量比值与预设稳态性能参数阈值进行对比,根据对比结果,判定控制回路在稳态性能方面的性能等级。在实施中,除了基于方差值获取高频段生产数据与总体数据的能量比值之外,还可以获取低频段生产数据与总体数据的能量比值、亦或是低频段生产数据与高频段生产数据的能量比值。将上述多种能量比值根据预设稳态性能参数阈值进行对比得到的对比结果,均可以用于判定控制回路在稳态性能方面的性能等级。除了上述列出的动态性能评价参数和静态性能评价参数外,还可以跟平稳率评价参数来判定控制回路的性能等级。平稳率指标用于判断PID控制回路的波动程度。波动程度越小,则该回路越平稳。平稳率指标计算方式如下:index_steady=(abs(mean(e))+2*std(e))/range_SV其中,e=pv-sp,e为控制偏差序列。mean(e)指控制偏差序列的平均值,代表了PV偏离SV的距离。而std(e)为控制偏差序列的标准差,通常用2倍的标准差来代表数据的波动幅度。range_SV表示的基于设定值SV的最大值与最小值差值获取到的范围。因此平稳率指标用于反应PID控制回路的波动状况,代表了当前控制回路的控制精度水平。根据性能标准,划分各项指标级别在这一步骤中,用户可以根据实际状况,设定各项指标的基准;若用户没有设定指标基准,则采用默认的基准,将各项指标划分为好、一般、坏三个级别。各项指标内部标准说明如下:平稳率评价指标index_steady:以2%作为基准线,即好:index_steady<2%;一般:2%<index_steady≤5%;坏:index_steady>5%动态性能指标的划分标准如下:超调量:好:index_os≤5%;一般:5%≤index_os≤15%;坏:index_os>15%。调节时间:好:一般:坏:index_settle>Tss。上升时间:好:一般:坏:稳态性能指标:由于稳态性能指标为归一化指标,即指标取值范围为[0,1]其划分标准如下,即好:index≥0.7;一般:0.4≤index_steady<0.7;坏:index<0.4基于上述标准制定的性能等级如表1所示:性能级别平稳率级别稳态性能级别动态性能级别优好好好良一般好>=一般良一般>=一般好中<=一般<=一般好中<=一般好<=一般中差好好差<=一般<=一般<=一般表1控制回路的性能等级在划分过程中使用的诸多阈值的取值,均可以在实际使用过程中根据需求进行针对性调整,本实施例中并不进行限定。可选的,所述评估方法,除了根据步骤102结合预设的过程模型对控制回路的响应时间进行更新外,还包括:获取经验响应时间,进而根据处理后的生产数据序列对经验响应时间进行验证;如果验证结果表明经验响应时间产生的误差低于预设阈值,则根据经验响应时间扩区与控制回路对应的性能评价参数,根据性能评价参数确定控制回路的性能等级。即操作人员也可人工设定响应快慢参数,在本步骤中,会利用生产过程数据进行检验,若设置合理则会采用用户设定的参数。可选的,所述评估方法,还包括:在首次运行PID性能评估方法时,在得到处理后的生产数据序列后,结合初始设定的响应时间,获取与控制回路对应的性能评价参数,根据性能评价参数确定控制回路的性能等级;基于性能评价参数对控制回路进行调节,结合预设的过程模型对控制回路的响应时间进行更新,得到更新后的响应时间。在实施中,如果本实施例提出的PID性能评估方法为首次运行,在步骤102中需要更新的控制回路的响应时间为初始设定的,在初始设定的响应时间下执行步骤103对控制回路的性能等级进行确定,当再次执行本PID性能评估方法时,可以通过步骤102对控制回路的响应时间进行迭代更新,从而令DCS在一定范围内自主的进行调节。本发明提出了PID性能评估方法,包括获取控制回路的生产数据和数据质量码,根据数据质量码对生产数据进行处理得到处理后的生产数据序列,结合预设的过程模型得到更新后的响应时间,进而获取与控制回路对应的性能评价参数,根据性能评价参数确定控制回路的性能等级。通过获取包括控制回路的测量值、设定值、操作值在内的多种数据,并且构建了用于对控制回路内的响应时间进行更新的过程模型,基于获取到的数据对控制回路的性能进行评估,同时能够基于过程模型结合获取到的多种数据对评估标准进行迭代更新,令控制回路的性能维持在合理的标准,相对于现有技术能够降低因未能及时进行人工维护导致控制性能恶化的可能性,减少控制回路出现安全隐患的概率。上述实施例中的各个序号仅仅为了描述,不代表各部件的组装或使用过程中的先后顺序。以上所述仅为本发明的实施例,并不用以限制本发明,凡在本发明的精神和原则之内,所作的任何修改、等同替换、改进等,均应包含在本发明的保护范围之内。当前第1页1 2 3