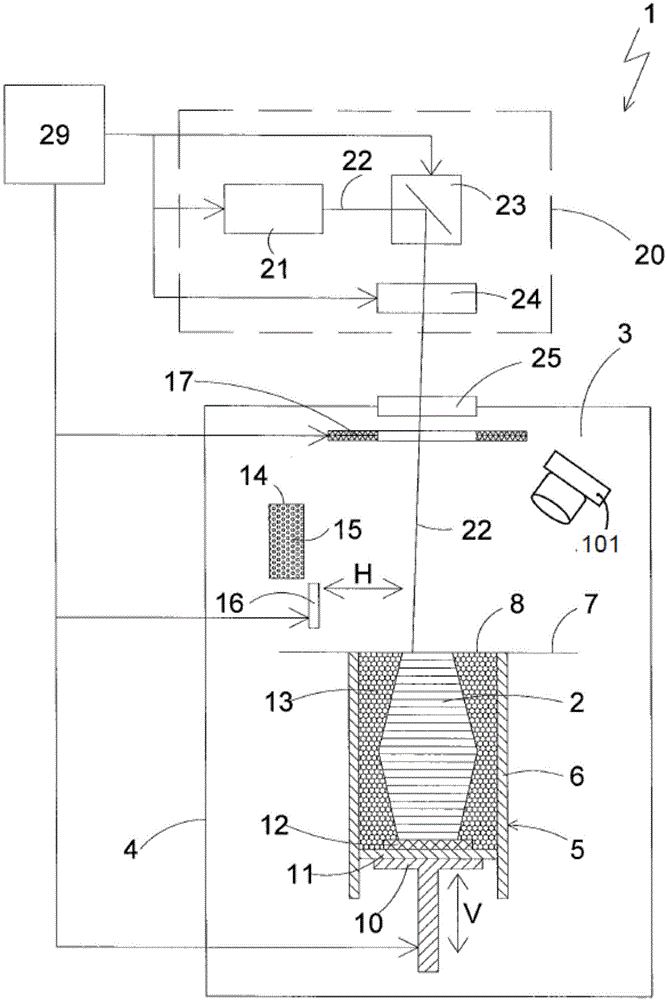
本发明涉及一种检测通过逐层增材制造方法制造的物体的质量的方法和装置,特别是确定所述物体的质量指标的方法和装置。
背景技术:
:r.和t.grünberger的投给“2015年制造业激光会议”的会议论文(文章“通过光学在线监测来识别dmls中的过程现象”)描述了基于金属的逐层增材制造方法(有时也被称为基于金属的增材制造方法)如何被光学地监测。具体地,它是关于一种dmls(直接金属激光烧结)方法,其中金属粉末通过激光逐层熔化,以便由金属粉末制造物体。特别地,从熔融材料(即熔池)发射的过程辐射,被光学地检测,并用作用于该过程的自动质量评估的基础。在该会议论文中,描述了如何从过程辐射获得关于不期望的过程行为的信息以及如何识别过程缺陷,其中过程缺陷导致制造的零件的质量不佳。发明人已经发现该文章中描述的方法有时可能导致物体被错误地归类为有缺陷的情况或者导致分类相对复杂并因此可能变得苛刻的情况。技术实现要素:因此,本发明的一个目的是提供一种自动检测物体质量的改进的方法和相应的装置,该物体是通过逐层增材制造方法制造的,该方法和装置特别优选地以更精确的方式检测此物体的质量。该目的通过根据权利要求1所述的确定质量指标的方法、根据权利要求13所述的确定质量指标的装置、根据权利要求14所述的过程监测装置、根据权利要求16所述的制造至少一个三维物体的装置、和根据权利要求17所述的计算机程序来实现。在从属权利要求中给出了本发明的进一步发展。在此,这些方法还可以通过下面进一步提到的或在相应的从属权利要求中提到的装置的特征来进一步发展,反之亦然。而且,为了进一步发展,可以互换装置的特征。一种确定物体的质量指标的发明方法,所述物体通过逐层增材制造方法制造,其中在所述逐层增材制造方法中,所述物体通过在层中相对应于所述物体的截面的位置处的构造材料的固化来逐层制造,所述发明方法包括至少以下步骤:步骤s1,提供第一数据集,第一数据集被分配给过程监测装置,其中用于在所述制造过程中的彼此跟随的若干层的第一数据集中,特别是彼此紧随的层的第一数据集中,由过程监测装置检测到的过程异常信息被分配给层的预定数量的固化位置中的每一个,步骤s2,对于彼此跟随的若干层,检测层中过程异常的相对发生频率,并且根据检测到的相对频率将等级指标值分配到层中的固化的物体截面,其中,对于所述相对频率的不同范围的值,分配指示不同质量水平的不同等级指标值,和步骤s3,生成第二数据集,其中等级指标值被分配到所述彼此跟随的若干层的每一层中的物体截面,和步骤s4,通过使用第二数据集(或若干其他数据集)确定质量指标,所述质量指标指示制造的物体的质量。根据本发明,被分配到过程监测装置并且包含由这样的过程监测装置检测的过程异常的第一数据集被进一步分析。通过检测彼此跟随的若干层中的每个物体截面的过程异常的相对发生频率,可以考虑在许多过程中的以某种频率发生的过程异常,然而,并不必然导致制造的物体的严重质量缺陷。因此,根据本发明的方法导致比其中例如只检测在物体制造中总共发生了多少过程异常的方法更加精确的结果。根据本发明,可以考虑只有几层中的过程异常的累积发生导致零件质量的显著降低。如果只能考虑物体的过程异常的总数,则这将是不可能的。在这方面,过程异常可以例如是过程光(过程辐射)的时间或空间变化、在层内的温度变化、检测到的外来颗粒、层不均匀等。优选地,所述的逐层增材制造方法是一种其中通过用能量辐射选择性地扫描层,通过向与所述层中的所述物体的截面相对应的位置提供热量来固化粉末形式的构造材料的方法,并且其中由所述过程监测装置检测到的所述过程异常信息指示当所述位置被扫描时,该位置处是否发生过程异常。在构造材料的选择性固化期间监测熔化过程(有时用术语“熔池监测”表示)特别适合于提供关于物体的制造过程的质量的有价值信息。因此,当使用相应的过程监测装置时,尤其实现本发明方法的优点。特别优选地,所述相对频率通过确定发生过程异常的物体的那些位置相对于所述物体截面的总面积的面积比来检测。如果确定过程异常的相对频率是基于确定物体截面内具有过程异常的位置的面积比,则可以考虑,截面内的过程异常是否被非常强烈地限制在局部,或者是否与物体截面中较大的面积相关,后者会使得过程异常更加地严重。在此,应该注意的是,发生过程异常的物体位置相对于物体截面的总面积的面积比,可以被认为等于发生过程异常的物体位置相对于用于制造物体截面的总时间的时间占比(因为它们基本上线性相关)。因此,在下文中,“面积比”被认为是“时间比”的同义词,除非明确说明相反的情况。在一个优选的修改中,确定层中已经分配有过程异常的位置是否位于部分物体截面内,优选地位于与物体截面的其他部分相分离的部分物体截面内。如果是这种情况,过程异常的相对发生频率另外地基于部分物体截面来确定,并且将部分等级指标值分配到部分物体截面上。通过刚刚描述的过程的修改,可以考虑的是,在物体截面的一部分中的过程异常的累积是制造的物体在这个位置上存在缺陷的强烈指示,尽管相对于总截面,异常相对频率不显著。具体地,在通过确定出现过程异常的物体的那些位置相对于物体截面的总面积的面积比来检测相对频率之后,还可以额外地确定层中分配有过程异常信息的位置是否位于部分截面内,如果是这种情况,则过程异常的相对发生频率可以根据部分物体截面确定,并且可以将部分等级指标值ri分配到所述部分物体截面。在这种情况下,如果分配到所述部分物体截面的所述部分等级指标值比分配到整个物体截面的等级指标值指示了更低的质量,则分配到层中的物体截面的等级指标值由指示较低质量的等级指标值所代替。由此,在物体制造中的特别关键的位置处,还可以监测物体质量。特别是如果物体的所有层经历根据本发明的方法,则可能获得关于物体的质量的更精确的表述。优选地,对于相对应的多个物体确定多个质量指标,该多个物体通过逐层增材制造方法共同制造。因为在逐层增材制造方法中,若干物体可以在一个共同的构造过程中一起制造,优选地对于多个制造的物体中的每一个,特别是对于它们的全部,确定(用于每个制造的物体的至少一个)质量指标。在根据本发明的方法的变体中,在检测过程异常的相对发生频率的步骤中,将层等级指标值作为等级指标值分配到层中的所有物体截面。特别地,如果存在若干过程监测装置和多个被分配给它们数据集,则根据该方法,可以逐层地确定指标值。该指标值考虑了由所有过程监测装置提供的异常信息。特别地,由此可以检测零件质量的劣化是否是由累积在某些层中的过程误差引起的。特别地,可以根据分配给各个过程监测装置的等级指示值来确定层等级指标值。可替代地,只需检测每层的过程异常的相对频率,并且将层等级指标值分配给该相对频率。在一个优选的方法的变体中,在步骤s1中,提供多个第一数据集,每个所述第一数据集被分配到过程监测装置,其中在步骤s2中,对于每个数据集,等级指标值ri被分配到所述彼此跟随的若干层中的每个物体截面,其中在步骤s3中,基于步骤s2中的分配而生成多个第二数据集,并且其中在步骤s4中,为了确定物体的质量指标q,首先确定对于每个第二数据集的单个质量指标值eq并且根据所述单个质量指标值eq,优选地通过将加权因子添加到所述单个质量指标值,来确定质量指标值q。通过为分配给各个过程监测装置的等级指标值引入加权因子,当评估零件质量时,不同的重要性可以归因于不同的过程监测装置。原则上,具有相同值的加权因子可被分配给至少两个或所有过程监测装置。在该方法的另一种优选修改中,在提供第一数据集的步骤s1中,提供多个第一数据集,其中每个第一数据集被分配到过程监测装置,其中在确定对于每个数据集的过程异常的相对发生频率的步骤s2中,等级指标值被分配到所述彼此跟随的若干层的每个物体截面,其中在生成第二数据集的步骤s3中,基于上个步骤中的分配而生成多个第二数据集,其中在步骤s4中,为了确定物体的质量指标,首先根据多个所述第二数据集确定层中的物体截面的总质量指标值,优选地通过将加权因子添加到分配给物体截面的各个单独等级指标值来确定,并且之后根据确定的所述总质量指标值来确定物体的质量指标。通过这种方式,各个过程监测装置提供的每层的信息可以被加权。在优选的方法中,如果分别地指示了更高质量的等级指标值和总等级指标值被分配到了属于所述物体在至少n个随后的层(优选地在至少n个紧随的层)中的所述物体截面,其中n为预定的自然数(例如用户定义的数字和/或根据预测试确定的数字),则用等级指标值和总等级指标值所分别代替分配到层中的物体截面的等级指标值和总等级指标值。通过刚刚描述的方法,可以考虑的是,一些过程异常不会导致过程或零件缺陷,而是受到退火机制的影响。特别地,如果在随后的层中没有出现过程异常,则这是层中过程异常的累积将不会对零件质量产生不利影响的良好证据。这可以通过刚刚描述的方法来考虑。在此,n可以是例如小于10的数字,如2、4、6或8。在一个优选的方法的变体中,物体是否具有可接受的质量的推导如下:设置等级指标极限值,并且将物体在各个单独层中的物体截面的等级指标值和总等级指标值分别与所述等级指标极限值进行比较。仅当所述等级指标值和总等级指标值都没有分别地被分配到比所述等级指标极限值更低的质量水平时,才确定所述物体的质量是可接受的。由于引入了等级指标极限值,可以以简单的方式指定可接受的零件质量的下限。具体地,可以为每个层特定地提供等级指标极限值。具体地,质量指标可以是质量程度指示集之中的元素,其中集的基数大于1,并且在集的成员之间存在顺序关系。由于引入了用于质量指标的有序集(例如某个数字范围或某个自然数子集,例如,数字1至10),可以以特别简单的方式进行质量评估。取决于所制造的物体的应用领域,可以根据质量指标来得出其质量是否足够。例如,获得物体的相对的低质量指标(意味着指示相对低的质量的质量指标)在快速原型制造领域中可能仍然是足够的,而对于用于长期使用的零件的成批生产,与第一个示例相比,可能需要达到更高的质量指标。一种确定物体的质量指标的发明装置,所述物体通过逐层增材制造方法制造,其中在所述逐层增材制造方法中,物体通过在层中对应于所述物体的截面的位置处的构造材料的固化来逐层制造,所述发明装置包括至少以下项:提供第一数据集的提供单元,第一数据集被分配给过程监测装置,其中在用于彼此跟随的若干层的第一数据集中,特别是彼此紧随的层的第一数据集中,由分配到数据集的过程监测装置检测到的过程异常信息被分配给层的预定数量的固化位置中的每一个,检测单元,当操作时,对于所述彼此跟随的若干层,检测层中过程异常的相对发生频率,并且根据检测到的相对频率将等级指标值分配到层中的固化的物体截面,其中,将指示不同质量水平的不同等级指标值分配给所述相对频率的值的不同范围,和生成单元,当操作时,其生成第二数据集,其中等级指标值被分配到所述彼此跟随的若干层的每一层中的物体截面,和确定单元,通过使用第二数据集来确定质量指标,所述质量指标指示制造的物体的质量。用于确定质量指标的装置例如可以通过专用于该目的的计算机来实现,或者其可以仅仅是计算机程序。该计算机程序可以例如在与该逐层增材制造装置在空间上分离的计算装置上运行。一种优选的发明的过程监测装置,用于检测在逐层增材制造方法中过程异常的发生,其中在所述逐层增材制造方法中,通过在层中对应于物体的截面的位置处的构造材料的固化来逐层制造物体,所述发明的过程监测装置包括确定质量指标的发明装置,并且还包括:异常检测单元,其对于已经用能量辐射扫描的层的预定数量的位置中的每一个,进行关于制造中的至少一个过程参数的发生过程异常的异常检测,和过程异常记载单元,其生成第一数据集,其中,对于彼此跟随的若干层,特别是所有层,过程异常信息被分配给已经用能量辐射扫描的层的预定数量的固化位置中的每一个,所述过程异常信息指示在构造材料的固化期间是否在该位置处发生过程异常。因此,用于确定质量指标的装置可以被特别地集成在过程监测装置中。具体地,对于存在若干过程监测装置的情况,每个过程监测装置可以已经提供每层和/或物体截面的等级指标值。优选地,所述异常检测单元是(例如基于照相机或成像的)层监测单元和/或基于光电二极管的熔池监测单元和/或光学断层摄影单元。由于这样的单元,特别是用于熔池监测的装置,能够提供关于零件质量的重要信息,因此本发明具有与用于熔池监测或光学断层摄影单元的这种过程监测装置有关的特别的优点。一种通过逐层增材制造方法制造至少一个三维物体的发明装置,其中在所述逐层增材制造方法中,通过在层中对应于所述物体的截面的位置上的构造材料的固化来逐层制造所述物体,所述发明装置包括:扫描单元,用于通过能量辐射的方式扫描与物体的截面相对应的施涂的构造材料的层的位置,以选择性地固化构造材料,确定质量指标的发明装置和/或发明过程监测装置。可加载到可编程控制单元和/或装置中的发明的计算机程序,所述计算机程序具有程序代码手段,当执行计算机程序时,该程序代码手段实施确定质量指标的发明方法的所有步骤。附图说明本发明的其它特征和优点将从基于所附附图的实施例的描述中得出。图1为根据本发明的一个实施例的用于三维物体的增材制造的装置的示意性局部剖视图。图2为显示可以与本发明结合使用的过程监测装置的设置的示意图。图3为示出确定质量指标的发明装置的设置的示意图。图4为示出确定质量指标的发明方法的步骤的示意图。图5为显示用于实现发明方法的示例性算法的过程流程图。具体实施方式在下文中,为了描述根据本发明的方法,首先,将参考图1使用激光烧结或熔化装置作为示例来描述根据本发明的逐层增材制造装置。在这一点上应该注意的是,在本申请中,术语“多个”总是应理解为“一个或多个”。为了构建物体2,激光烧结或熔化装置1包括具有室壁4的处理室或构建室3。具有容器壁6的顶部开口的容器5布置在处理室3中。工作平面7由容器5的上开口限定,其中工作平面7的位于开口内并可用于物体2的构建的区域被指定为构造区域8。可在垂直方向v上移动的支撑件10布置在容器5中。基板11附接到承载件10,该基板11在底部封闭容器5,并从而形成容器5的底部。基板11可以是与承载件10分开地形成并且固定到承载件10的板,或者基板11可以与承载件10一体地形成。取决于所使用的粉末和过程,作为构建基底的构建平台12可以附接到基板11,物体2将在基板11上构建在该构建平台12上。然而,物体2也可以建在基板11本身上,该基板11之后作用为构建基底。在图1中,有待在构建平台12上的容器5中形成的物体2被显示为处于工作平面7下方的中间状态,其中若干固化的层被保持未固化的构造材料13包围。激光烧结装置1还包括用于粉末形式的、可以通过电磁辐射的方式固化的构造材料15的存储容器14和可以在水平方向h上移动以用于在构造区域8内施涂构造材料15的重涂器16。可选地,辐射加热器17布置在处理室3中,其用于加热所施涂的构造材料15。例如,可以提供红外辐射器作为辐射加热器17。激光烧结装置1还包括具有激光器21的曝光装置20,该曝光装置20产生激光束22,激光束22借助于偏转装置23偏转并且借助于聚焦装置24,通过布置在室壁4中的处理室3的顶侧处的耦合窗25聚焦到工作平面7上。此外,激光烧结装置1包括控制单元29,通过该控制单元29可以协调地控制装置1的各个部件,以实施构建过程。可替代地,控制单元也可以部分地或完全地布置在装置的外部。控制单元可以包括cpu,其操作通过计算机程序(软件)控制。计算机程序可以与装置分开地存储在存储介质上,计算机程序可以从该存储介质加载到装置中,特别是加载到控制单元中。控制单元29通过控制命令集来控制,该控制命令集例如包括数据,该数据包括有待制造的多个物体的结构,特别是物体的三维cad层模型,该三维cad层模型具有关于有待固化的构造材料的每个层中的物体的相应截面的信息,以及指定构造材料的固化中的具体参数的数据。具体地,该数据包含关于在制造该数量的物体时每个有待被固化的层的具体信息。在现有技术中充分地描述了控制命令集的详细内容,因此这里不再进一步解释,因为这不是本发明的组成部分。在操作中,通过控制装置29逐层地降低承载件10,控制重涂器16,使得施涂新的粉末层,并且控制偏转装置23,并且如果必要还控制激光器21和/或聚焦装置24,使得通过用激光扫描对应于相应物体的位置的方式,用激光使得相应的层在对应于相应物体的位置处固化。图1还显示了过程监测装置101,其显示在处理室3的内部,并且因此作为激光烧结装置1的一部分,然而,也可以布置在处理室3的外部。过程监测装置101是在通过逐层增材制造装置构建物体期间,检测过程行为的装置。例如,过程监测装置101可以用于监测在使用激光束固化构造材料期间的状况。在这种情况下,它包括传感器,其适用于检测从激光束的入射点发射到构造材料上的过程辐射。例如,该传感器可以被实施为光学摄像头或光电二极管。基于所记录的过程光(过程辐射)的强度或者基于对信号的时间行为的分析(该行为由过程辐射在传感器中引起),可以得出关于固化过程的异常的结论。当使用摄像头而不是光电二极管时,可以额外地获取二维信息。除了作为示例的上述熔池监测装置之外,还已知可以替代地或除了熔池监测装置之外使用的其它过程监测装置,例如,基于摄像头的层监测装置,其能够检测层施涂中的异常,或者能够分析固化过程之后的层表面的装置。可以借助过程监测装置检测到的过程异常的例子具体地有如下:·飞溅、烟雾、蒸汽等颗粒的分别发生和增加(增强)发生;·来自辐射作用于构造材料的位置的辐射的发射的时间或空间变化,该变化允许例如关于构造材料的过热的结论,特别是如果过程辐射的光谱分析(例如还通过诸如多色传感器之类的若干个波长的传感器的间接光谱分析)被额外地执行;·层内已经固化的区域的大的表面粗糙度;·进一步的测量和预测结果,分别表明制造的物体的材料的微结构中增加的缺陷概率。以这种方式,可以得出基于传感器信息的过程异常是领域技术人员已知的、并且不是本发明的目的结论。图2示出了与本发明结合使用的过程监测装置101的示例性设置。特别地,过程监测装置101包括异常检测单元110,通过该异常检测单元110确定在层中的多个位置,在过程流程中是否存在异常。例如,在熔池监测装置的情况下,异常检测单元110会包括例如传感器以及用于传感器信息的后续处理硬件和软件,以便得出是否发生异常的信息。此外,过程监测装置包括产生第一数据集1010的过程异常记载单元111,在第一数据集1010中,对于彼此跟随的若干层,存储每个层的多个位置的过程异常信息,该过程异常信息指示例如在构造材料固化期间,是否在相应位置处发生过程异常。在物体的制造过程期间指代层i的这种第一数据集1010中的条目可以例如具有以下内容:(xj,yj,ok,i,…,i)在上面的条目中,指标ok表示条目指代物体k的事实,因为在逐层增材制造方法中,可以同时制造若干个物体,并且因此在有待固化的层内还可以存在若干个物体截面。坐标xj和yj指定存储异常信息的层的位置。最后,参数i表示过程异常信息。参数i可以是表示过程异常的严重性的指示数(例如在1和10之间的自然数),或者它也可以仅仅是二进制信息(0和1)。例如,1将会指示在与层i中的物体k相关的物体截面中的位置xj,yj处发生过程异常。没有检测到过程异常的每个位置,异常指标i的值可以为0。第一数据集1010可以存储在过程监测装置101中的存储器中,如图2所示,其中存储器也可以在过程异常记载单元111自身中,或者可以将其输出到过程监测装置101外部的存储装置,过程监测装置101根据信令与存储设备连接。图3示意性地示出了确定通过逐层增材制造方法制造的物体的质量指标q的发明装置1000的设置。图4示出了确定质量指标q的发明方法的顺序,该方法可以例如通过图3中的装置1000实施。装置1000包括提供单元1001,用于提供(步骤s1)多个第一数据集1010,每个第一数据集1010被分配到相应数量的过程监测装置101中的一个。换句话说,提供单元1001从多个过程监测装置101接收由其过程异常记载单元111生成的第一数据集1010。过程监测装置101的数量可以仅是单个过程监测装置,或者可以是优选地彼此不同的多个过程监测装置,然而,并不必须彼此之间不同。对于接收多个第一数据集1010,装置1000不是必须连接到相应的过程监测装置101。相反,第一数据集也可以存储在与过程监测装置101和/或设备1000分离的存储器中。然而,在每种情况下,提供单元1001使得第一数据集的内容对于装置1000的其他部件是可访问的。另外,装置1000包括检测单元1002,通过该检测单元1002,在图4中示出的本发明方法的处理步骤s2可以得以实施。具体地,检测单元1002检测在彼此跟随的多个层中的每个层中物体的物体截面(优选地,对于这些层中的若干、特别是所有物体的截面)内的过程异常的相对发生频率。随后,检测单元1002根据针对其检测到的相对频率,将等级指标值ri分配给层中的物体截面。例如,可以通过确定在第一数据集1010中指示过程异常的位置相对于物体截面的总面积的面积比来检测相对频率。可替代地,可将发生过程异常的物体截面内的位置的数量与第一数据集1010中的存在于物体截面内的位置的总数量进行比较。有利地,等级指标值ri是自然数(例如在1和10之间的数字)。例如,可以将等级指标值ri如下分配给每层和物体截面的相对频率值:异常的相对频率等级指标值ri0-2%12-5%25-10%310-15%415-25%5等等可以看出,在上表中,对于等级指标值ri存在相对频率范围的非线性分配。换句话说,当相对频率的值上升时,与相对频率的较低值相比,将更大范围的百分比分配给特定等级指标值ri。然而,这不是必须的,这种非线性分配具有的优点特别是感兴趣的质量范围可以被解析为精细的细节。如果过程质量差,例如,质量是“非常差”还是“特别差”并不重要。最后,生成单元1003针对多个第一数据集1010中的每一个生成对应的第二数据集1020,其中在每个层中,将等级指标值ri分配给物体截面(图4中的步骤s3)。在物体的制造过程期间引用层i的这种第二数据集1020中的条目可以例如具有以下内容:(ok,ri,mi)在上面的条目中,指标ok表示条目指代物体k的事实,因为在逐层增材制造方法中,可以同时制造若干物体,并且因此在有待固化的层内还可以存在若干物体截面。指标mi表征该条目(类似于整个第二数据集)与过程监测装置m的从属关系。因此,对于每个过程监测装置101,存在第二数据集1020,其中将等级指标值ri分配给每个层中的物体截面。这样的等级指标值ri表示由用于这一层中的物体截面的过程监测装置提供的过程异常的频率。出于简洁的原因,图3中仅显示了一个第二数据集1020。最后,用于确定质量指标q的装置还包括质量指标确定单元1004,质量指标确定单元1004基于第二数据集1020中的数据来确定制造的物体(优选地若干物体,特别是在一个制造过程中并行制造的物体中的每一个)的质量指标值,意味着将质量指标值ri分配给这些数据库中的各个单独层和物体截面(图4中的步骤s4)。在下文中,作为示例描述了如何基于第二数据集1020获得物体的质量指标值的不同可能方法。这里,以下描述首先限于这样的情况,其中由于得到的更简单的解释,仅存在一个第二数据集1020:在下面的示例中,还假设等级指标值ri是在1和上限(例如10)之间的自然数。当然,数字“0”也可以是一个可能的等级指标值。质量指标确定单元1004的动作可以例如为如下的样子:在第二数据集1020中,将物体的每个等级指标值ri(因此将该物体在第二数据集的层中的物体截面的所有等级指标值)与等级指标极限值z进行比较。该等级指标极限值z例如是等级指标值,对于该等级指标值,当被超过或底切时,对应的物体截面的质量被认为不再是可接受的。质量指标q的值的选择(其例如也是有限集合中的自然数,例如数字1至6)现在可以分别取决于物体的等级指标极限值z是否被超过和底切以及超过和底切发生得多频繁而决定。例如,当等级指标极限值z分别被等级指标值ri超过和底切时,可以分别将最大和最小等级指标值ri确定为质量指标值q。如果没有超过或(特别是)底切等级指标极限值z,例如所有等级指标值的平均值<ri>可以简单地被选择为质量指标值q。为了更简单地解释,从现在开始假设较高等级指标值指示着更频繁的过程异常(因此质量更差)。通过本发明检测层中每个物体截面的等级指标,可以以特别简单的方式检测由具有特别差的质量的一个或若干物体截面引起的不足够的零件质量。即,在仅基于过程异常的总数来推断零件质量的方法中,无法充分地考虑一个(单个)特别地“差”的层。特别地,也可以仅允许质量指标q的值为0和1,并且仅当物体的等级指标值中都没有超过等级指标极限值z时,才可以将值1分配给质量指标。这里,在不脱离本发明的思想的情况下,存在许多变化的可能性。可选地,如果仅允许质量指标的值为0和1,则可以另外引入接受指标a,该接受指标a可以仅采用值1(可接受的物体质量)和值0(不可接受的物体质量)。之后,可以根据质量指标的值来确定接收指标a的值。尽管上述方法已经导致对缺陷物体的更精确的检测,但是有可能对其进行修改,使得可以对制造的物体的质量作出更精确的陈述。发明人已经发现,在制造过程中存在退火机制。例如,在物体截面的面积的较大百分比中出现异常的情况下,这首先是有问题的,因为可由此推断出材料缺陷(结合缺陷、熔结的飞溅或孔)。然而,这样的材料缺陷可以通过暴露随后的层来退火。原因是,已固化的层在位于其上面的层的暴露中被再次(部分地)熔化。然而,退火的先决条件是在位于其上面的层中过程异常不会过度地发生。因此,即使在层中在很大程度上出现过程异常的累积,由于退火机制,该零件仍可具有良好的质量。因此,为了确定质量指标q,如果在该层之后的至少n个层中存在指示较高质量的等级指标值,第二数据集1020中的物体的层的等级指标值可以由指示较高质量的等级指标值替换。这里,n可以是1和例如10之间的任何自然数如3、5、8等。具体地,等级指标值的升级(在以上示例中,这将对应于等级指标值ri的降低)可以仅针对其中在第二数据集1020中存在超过预定的等级指标极限值z的等级指标值的那些层来进行。通过这种方法,可以减少被错误地分类为“劣等”的制造物体的数量。下面将参考图5来描述刚刚描述的方法的示例性算法的顺序:在下文中,ri应指定存在于第二数据集1020中的每层和物体截面的等级指标值,并且q将指定质量指标的值。此外,“y”应指示存在检查条件,并且“n”应指示不存在检查条件。现在,根据示例性算法,该过程如下:首先,对于存在于第二数据集1020中的每个等级指标值ri,测试这样的等级指标值ri是否满足条件ri>z+3。如果这是针对一个或多个等级指标值的情况,则将满足该条件的等级指标值ri的最大值分配给质量指标q,将值0分配给接受指标(指示不可接受的质量),并且算法停止。因此,在本示例中,以超过等级指标极限值z三个评估水平的等级指标值ri作为对应层中的过程异常严重到以至于导致的零件缺陷不可退火并且该零件整体具有低质量的指示,该质量指标值由具有与最差等级指标值ri相同的值的质量指标值表示。应该注意的是,上述的表述“z+3”仅仅是作为示例。当然,也可以将术语选择为“z+2”、“z+4”等。或者也可以选择由于缺乏质量而导致的另一个立即停止标准。继续该示例,如果等级指标值都不满足条件ri>z+3,则测试第二数据集1020中是否存在超过等级指标极限值z的一个或多个等级指标值ri。如果不是这种情况,则将第二数据集中存在的所有等级指标值ri的平均值作为值(q=<ri>)分配给质量指标q。此外,将值1分配给接受指标a(指示可接受的质量),并且算法停止。如果只有整数值应该被允许用于质量指标q,则平均值在被分配给质量指标q之前被四舍五入(5图中未示出)。如果存在超过等级指标极限值z的等级指标值ri,则针对这些等级指标值中的每一个检查是否可能在随后的层中发生退火过程。这意味着针对这些等级指标值ri中的每一个,检查了等级指标值ri+1,ri+2,ri+3是否也超过了等级指标极限值z。(在本示例中,对后续的三个层中的每一个进行检查。然而,也可以针对不同数量的后续的层进行检查,例如2或4层等层数。)如果在这些随后的层中都没有相应的等级指标值超过等级指标极限值z,则假定层i中的有缺陷的过程质量已经被退火。然后,将等级指标极限值z的值分配给质量指标q,值1被分配给接受指标a(指示可接受的质量),并且算法停止。虽然假定退火,但仍假定零件不具有特别好的零件质量,其中在这种情况下,质量指标q通常来说可能不比等级指标极限值z更“好”。如果存在超过等级指标极限值z的等级指标值ri(其中在随后的层中不能检测到退火),则将这些等级指标值ri的最大值作为值分配给质量指标q,将值0分配给接受指标(指示不可接受的质量),并且算法停止。应注意的是,在图5中在图中的对应位置处的表达式“max(ri)”不是所有等级指示值ri中的最大值,而仅是不能检测到退火的那些值中的最大值。当然,也可以有上述示例的不同修改。然而,可以认识到,本方法超出了对等级指标值的平均值的简单确定,并且使得质量指标对零件的更可靠的分配成为可能。首先,上述方法仅确定物体的质量指标值。然后,从物体上的哪个点被视为具有可接受质量的物体,只需取决于质量指标的值范围内物体的接受限制值。特别地,本发明的优点在于,为了确定指示零件质量的质量指标值,考虑了所有第二数据集1020,将每个第二数据集1020分配给过程监测装置。基于不同的过程监测系统,获得物体的制造中的过程质量的总体评估。特别地,可以首先分别为每个第二数据集1020确定单个质量指标值eq,并然后基于这些单独确定的单个质量指标值来确定质量指标值q(用于总质量)。这里,对于质量指标值q的确定,加权因子可以归因于单个质量指标值eq,由此对于质量指标值q的确定,这种单个质量指标值eq在不同程度上被考虑。可替代地,当然也可以考虑所有存在的第二数据集1020来首先确定每个物体和层的总等级指标值。在后者情况下,将根据每个层和物体检测到的总等级指标值来确定质量指标值q。此外,根据本发明的方法的特别的优点在于,可以通过适当选择加权因子来自动解决由各个过程监测系统提供的过程异常信息中的冲突。可替代地,还可以检查其他条件,例如,两个不同的过程监测装置是否指示物体的层中的相同位置的过程异常等。利用本发明的方法,可以从零件制造中的有缺陷的过程质量推断不良的零件质量。这里,在制造过程期间还可能发生存在过程质量不足的某些层。这将对在构建过程中制造的在这些层中具有物体截面的所有物体具有影响。因此,在本发明的修改中,在确定质量指标值之前,首先基于第二数据集1020来确定每层的层等级指标值si(因此独立于层中的特定物体截面),例如,通过确定所有物体截面上的过程异常的相对频率的平均值,或者通过对分配给一个层中的各个物体截面的等级指标值ri求平均,或者通过选择最差等级指标值ri作为层的等级指示值si来确定。在参考图3和4描述的方法的进一步修改中,代替或除了确定每个物体截面的等级指标值ri之外,可以为层中的物体截面的部分区域(部分物体截面)确定过程异常的相对频率。然后,根据层中的物体截面的部分区域的加工异常的相对频率,可以确定该部分区域的等级指标值rj。通过这种方法,可以仅考虑提前预先确定的用于评估零件质量的物体截面的部分区域。可替代地,在物体截面内,对于该物体截面的几个部分区域检测加工异常的相对频率,并且将部分区域等级指标值rj对应地分配给每个部分区域。以这种方式,可以更系统地识别在物体制造中在非常特定位置处的过程缺陷,或者仅考虑用于评估物体质量的特别关键的位置。如果对于部分区域存在较差的等级指标值rj,则还可以降级物体截面的等级指标值ri。如果物体截面逐条形或逐正方形地曝光,则物体截面的上述部分区域特别地可以是曝光的条形或曝光的正方形。为了避免任何误解,应指出条形不是线形曝光,因为它发生在例如所谓的“孵化”中。在确定质量指标q的本发明方法和本发明装置的以上描述中,涉及第一数据集和第二数据集的存在。这里,应当指出,本发明当然不限于首先在某处存储上述定义的第一数据集1010并且在另一位置明确地存储上述定义的第二数据集1020的情况。第一数据集1010和第二数据集1020的数据也可以是存在于数据处理设备的易失性存储器中的信息,该信息仅作为短期计算结果存在并且被立即进一步处理。特别地,在存储器中的某处不需要存在数据集包括关于所有层和物体的信息的完整的第一数据集和第二数据集。原则上,如果仅暂时存在关于至少一层和一个物体截面的过程异常和等级指标值的信息(作为中间结果的一种,基于该中间结果,如果必要,可以(例如自动地)停止相应物体或所有物体的制造过程),则这是足够的。然而,如果参考存在于存储器中的第一数据集1010和存在于存储器中的第二数据集1020,则本发明方法当然更容易管理。在本发明的第二实施例中,图3中所示的检测单元1002不被布置在确定质量指标q的装置1000中,而是被布置在图1中和图2中所示的每一个过程监测装置101中。此外,生成单元1003布置在每一个过程监测装置101中,而不是在装置1000中。然而,参照图4中描述的方法并不一定会随之改变。相反,每个过程监测装置101分别检测每个物体截面和层的等级指标值ri,并且自身生成包含该信息的第二数据集1020。之后,装置1000中的提供单元1001将来自过程监测装置101的对应的第二数据集提供给质量指标确定单元1004。然后质量指标确定单元1004通过使用如上进一步描述的多个第二数据集1020来确定质量指标值q。可选地,质量指标确定单元1004也可以在过程监测装置101中形成,例如也可以在每个过程监测装置中形成。在这种情况下,每个过程监测装置101确定其自身的单个质量指标eq。结果,可以或者使用分离的装置1000来确定质量指标q(在这种情况下,过程监测装置101本身是确定质量指标的装置),或者使用专用的装置1000基于首先由单独的过程监测装置101确定的单个质量指标值eq来确定一个或多个制造的物体(优选地每个制造的物体)的质量指标值q。此外,当质量指标值q被确定时,首先为各个单独的过程监测装置确定的单个质量指标值eq可被赋予加权因子。在一个修改中,还可以想到的是,确定置信度指标,该置信度指标指示各个过程监测装置101的单个质量指标eq是彼此不一致还是彼此非常相似。如基于第二实施例可以得出,对于确定质量指标q的装置1000的实施方式存在不同的可能性。人们认识到,组件1001、1002、1003、1004还可以分布在若干物理装置上,并且交互部件1001、1002、1003、1004仍然可以被视为确定质量指标的装置1000。在上述实施例及其修改中,可以使用户指定该方法的一个或多个参数(例如,经由输入单元)。例如,可以由用户指定用于分别考虑由各个过程监测装置提供的异常信息和等级指标值的加权因子。另外,也可以指定等级指标极限值z(可能对于每个过程监测装置分别指定)。此外,可选地,还可以实现分配给各个层的异常信息的图形表示,或者可替代地,分配给各个层和物体截面的等级指标值ri的图形表示。取决于层内的位置的异常信息的可视化可以使得本领域技术人员(特别是对于颜色表示)更容易快速地识别制造过程的质量和物体的质量,并且以简单的方式立即识别例如问题是否出现在层的特定区域中,该问题可能视情况而定归因于构造室中的该区域中的问题。即使对于等级指标或质量指标,到目前为止仅提到了作为自然数的子集的值的范围(包括零,视情况而定),例如数字1至6、5至10等,只要在对应的集的成员之间存在顺序关系,相应的值范围也可以是其它集,例如字母等。即使在图1中描述了激光烧结或激光熔化装置作为逐层增材制造装置的示例,本发明并不限制于激光烧结或激光熔化。它可以结合通过逐层施涂和选择性地固化构造材料来增材制造三维物体的任何方法来应用。这里仅通过示例的方式提及激光熔化、llm(从叠片切割并组装)、flm(从喷嘴施加热塑性材料)、3d印刷、掩模烧结方法和立体光刻方法。曝光装置可包括例如一个或多个气体或固态激光器或任何其它类型的激光器,例如激光二极管,特别是vcsel(垂直腔表面发射激光器)或vecsel(垂直外腔表面发射激光器)或这些激光器的线。通常,可以使用能够将能量作为波或粒子辐射选择性地施加到构造材料的层上的任何装置来代替激光器。例如,可以使用适合于固化构造材料的其他光源、电子束或任何其它能量或辐射源来代替激光器。最后,应提及的是,图1中所示的激光烧结或熔化装置的设置仅仅是示例性的,并且当然可以修改。各种材料可用作构造材料,优选粉末,特别是金属粉末、塑料粉末、陶瓷粉末、砂、填充或混合粉末或光聚合物。最后,应当提到的是,确定质量指标的装置1000可以单独由软件部件来实现,或者由硬件和软件的混合来实现。特别地,本申请中提到的接口不一定需要被实现为硬件部件,而是也可以被实现为软件模块,例如,如果经由它们馈送或输出的数据可以从已经在同一装置上实现的其他部件接管或者必须仅借助于软件被传送到另一部件。另外,还可以在如输入-输出接口的公共接口中组合若干接口。另外,装置1000也可以集成到逐层增材制造装置的控制单元29内。当前第1页12