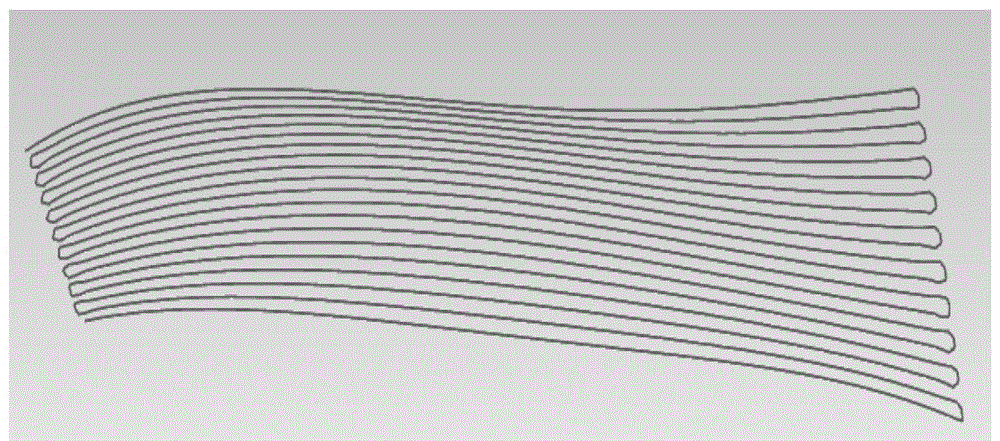
本发明涉及齿轮领域,具体而言,涉及一种齿轮的修形设计方法和用该方法制造的齿轮。
背景技术:螺旋锥齿轮作为传递空间相交轴运动的关键零部件,由于其重合度高、传动平稳、噪音低,广泛应用于航空、航天、轨道交通、海洋工程、能源装备及工程机械。适应现代工业应用的需求,齿轮传动系统正朝着高速、重载、高可靠性的方向发展。螺旋锥齿轮齿面属于空间复杂曲面,其齿制和专用机床的加工调整参数及刀盘规格相关,没有统一的理论齿面。在加工螺旋锥齿轮时,机床和刀具的选择更为复杂。在该领域,主要存在三种不同的齿形齿制:格里森齿制、奥利康齿制和克林根贝格齿制。每一种齿制都必须使用专用于该种齿制的机床和相应的刀盘才能制成。中国专利CN102166673公开了一种螺旋锥齿轮的加工方法,其结合使用格里森608和609机床生产格里森齿制的螺旋锥齿轮。公开号CN1614526的直齿圆柱齿轮修形方法对两齿轮同时进行齿向修形,增加了修形齿轮的设计和加工难度,齿廓修形方面,采用了样条曲线拟合作为齿廓修形曲线。
技术实现要素:本发明的目的是提供一种齿轮的修形设计方法,其特征在于包括:1)获取第一齿轮的齿面离散数据,包括位置矢量和法向矢量;该齿面离散数据点不包括齿根圆角;2)根据啮合原理,直接由第一齿轮齿面的离散数据点的位置矢量和法向矢量反求与其配对的第二齿轮的齿面离散数据点的位置矢量和法向矢量;3)第一齿轮不修形,根据反求第二齿轮的齿面离散数据,进行修形设计;修形设计具体为先得到瞬时接触线,根据测量精度把啮合转角相差不超过1mm的点作为同一条瞬时接触线的点;然后选择瞬时接触线中的一条lc,作为确定初始接触轨迹线平面的定位瞬时接触线,由该瞬时接触线上三个点pmid-1、pmid和pmid+1确定三点所在平面的法矢Vf,以及由点pmid-1、pmid+1所在直线的方向矢量Vt,由Vf和Vt的叉积得到中间矢量矢量VR:VR=Vf×Vt进而得到接触轨迹线平面法向矢量VN,VN=Vf×VR;从而确定了接触轨迹线初始平面;或者通过选择瞬时接触线上的一个点,将接触轨迹线初始平面绕方向为VR且过该点的轴旋转;确定了接触轨迹线平面;或者通过选择瞬时接触线上不同于上述确定接触轨迹线初始平面的三个点确定了第一接触轨迹线平面,然后再通过选择瞬时接触线上的一个点,将第一接触轨迹线平面绕方向为VR且过该点的轴旋转,确定了接触轨迹线平面;上述接触轨迹线平面是由用户需求决定的;通过定义接触轨迹线所在平面的位置确定接触区域的位置,通过控制接触轨迹线平面与瞬时接触线的角度控制齿面接触的重合度,通过控制沿接触轨迹线和瞬时接触线的修形范围,控制接触区域的大小;从瞬时接触线的各点中选择到接触轨迹线平面距离最小的点作为该瞬时接触线的接触中心点;连接各瞬时接触线上的接触中心点连接形成齿面接触轨迹线;沿接触轨迹线或瞬时接触线之一或者两者同时修形;3)根据第二齿轮的齿面修形离散数据点,对齿面离散数据进行拟合,并建立第二齿轮的实体模型;4)使用通用数控机床加工修形第二齿轮。进一步,根据齿面方程求解得到第一齿轮的齿面离散数据或者对第一齿轮的实物进行测量,获得已有第一齿轮齿面的离散数据。进一步,接触轨迹线所在平面由瞬时接触线上的相邻三点确定。进一步,选择一条瞬时接触线lc作为接触轨迹线平面的定位瞬时接触线;由定位瞬时接触线lc和接触轨迹线确定的点PC称为齿面修形中心点,该点不修形,接触轨迹线与其它瞬时接触线lk,k≠C的交点Pk称为瞬时接触线lk的修形中心点,其修形量为hk,点Pk离PC越远,修形量hk越大。进一步:在对瞬时接触线lk进行修形计算时,先假定接触线修形中心点Pk的修形量为零,按法则确定好瞬时接触线lk上所有的点Pk,j的修形量hk,j后,再把该瞬时接触线的基准修形量hk加到每点的修形量上,即Pk,j的实际修形量为hk,j+hk;上述法则为沿接触轨迹线或瞬时接触线的修形量的大小采用函数:h=axn,即线上任一点Pi,其修形量为其中xi为点Pi到修形中心点P0的弧长,其中,xs为设定的接触区域的半轴,hs为接触区域半轴处的修形量。n=2,3,4...,轻载时,沿接触轨迹线或瞬时接触线的修形遵照接触区域边界的修形量为0.00625。进一步,修形策略如下:接触区域内定传动比的点接触齿面的设计方法为沿接触轨迹线,有一段不修形;全齿面定传动比的点触齿面齿面的设计方法为沿接触轨迹线上的点全不修形;接触区域内定传动比的局部线接触齿面的设计方法为沿着接触轨迹线部分区域不修形;全齿面定传动比局部线接触齿面的设计方法为沿着接触轨迹线的整个区域不修形。齿轮,其使用上述任一项所述的方法制造。本发明提出主动修形设计的理论与方法。该方法摆脱了机床加工参数的限制,直接面向齿面几何形状,可以基于功能需求,设计接触区域的范围,方向,控制传动误差及根据工况对修形量的灵活设计。通过分别对接触轨迹线和瞬时接触线进行独立预控,实现齿轮齿面的三维灵活修形效果,从而提高齿轮的传动性能。附图说明图1为按照本发明第1实施例中已有齿轮A的示意图;图2为测量路径;图3为螺旋锥齿轮修形后齿面形式如图4所示为螺旋锥齿轮主动修形设计类型。图5为对接触轨迹线的控制(a)接触轨迹线近似垂直于齿根(b)增大接触轨迹线倾斜角图6为接触轨迹线平面;图7为按照本发明对瞬时接触线3进行修形的原理图;图8为按照本发明同时对瞬时接触线3和接触轨迹线5修形的原理图;图9为接触轨迹线分段修形原理;图10为瞬时接触线修形原理图11为齿面修形交互式对话框(a)沿着瞬时接触线修形(b)沿着接触迹线修形图12为对接触区域范围的控制(a)接触区域范围为10mm(b)接触区域范围为20mm(c)接触区域范围为30mm;图13为大轮螺旋锥齿轮齿面离散测量点云图;图14为基于离散点云拟合出大轮齿面图;图15为小轮共轭离散齿面求解点云图;图16为基于离散点云拟合出小轮齿面;图17为通过Imageware拟合曲面的精度分析图图18为加工示意图;具体实施方式实施例1:如图1所示,对已有齿轮A,进行数据测量得到表1和表2。测量路径如图2所示。2、根据啮合原理:求解得到:表-3共轭齿面点云数据求解部分结果(mm)确定瞬时接触线瞬时接触线就是当两齿面在某个位置接触时,由齿面上各个接触点按顺序连接构造出来的曲线,两齿面在不同的接触位置,形成不同的瞬时接触线,齿面实质上可以认为是由无数条的瞬时接触线所组成的表面。在啮合过程中,两齿面Σ2和Σ1共轭线接触。对大轮齿面Σ1而言,每转动一个角,齿面上都会有一条啮合线(大轮齿面上所有相同的点);此时,小轮辅助齿面Σ1会相应转动角,齿面也会有一条对应的啮合线(小轮齿面上所有相同的点)。1)齿面瞬时接触线确定的原理与方法设计算出的小齿面上点集Γ由N个点构成,即Γ={Ci|i=1,2,…,N},每一个点Ci可以表示为三元组其中pi、ni和分别表示点Ci的矢径、法矢和成为啮合点时的转角,为叙述方便,以下称为点Ci的啮合转角。当齿面由初始位置旋转一个角度与另一齿面接触时,齿面瞬时接触线上的点的转角相同,因此在齿面点集Γ中,能构成瞬时接触线的点的条件是这些点的啮合转角相同,所以从齿面点集Γ确定瞬时接触线的准则是找到啮合转角相同的点。首先对点集Γ的点Ci按啮合转角的大小从小到大排序,然后把啮合转角相同的点作为一条瞬时接触线的点,考虑到测点间距和测量误差的影响,把啮合转角相差不超过阈值ε的点作为同一条瞬时接触线的点。修形策略:根据上述修形原理和方法,通过对接触区域及传动误差的控制,可形成点接触及局部线接触的螺旋锥齿轮齿面,如图3-10所示。图3为螺旋锥齿轮修形后齿面形式。接触轨迹线的确定原理与方法在齿面上的一条瞬时接触线lj上,选择一个点作为该瞬时接触区域的接触中心点lj:mj,该点不修形,依次连接各瞬时接触线上的接触中心点就形成一条接触轨迹线。反过来说,瞬时接触线上的接触中心点是接触轨迹线与瞬时接触线的交点。因此,要确定瞬时接触线上的接触中心点,需预先确定接触轨迹线。直接指定一条在齿面上的三维空间曲线作为接触轨迹线是困难的。本文通过指定一个平面(以下称为接触轨迹线平面),由该平面与齿面的交线得到接触轨迹线。通过改变接触轨迹线平面的位置和方向,就可得到不同的接触轨迹线。先确定初始的接触轨迹线平面,其方法是:从识别出的瞬时接触线集L中选择一条位于齿面中部的瞬时接触线lc(也可交互选择)作为接触轨迹线平面的定位接触线(称为定位瞬时接触线),设点pmid-1、pmid和pmid+1是接触线lc上相邻的三个点,且点pmid是lc的中点。取点pmid作为接触轨迹线平面的初始定位点,点pmid-1、pmid和pmid+1所确定的平面的法矢Vf为Vf=(pmid+1-pmid)×(pmid-1-pmid)(3-5)点pmid-1和pmid+1所在直线的方向矢量Vt为:Vt=pmid+1-pmid-1(3-6)矢量VR为:VR=Vf×Vt(3-7)则初始的接触轨迹线平面法矢量VN为VN=Vf×VR(3-8)图6接触轨迹线平面根据初始定位点pmid和法矢VN即可确定接触轨迹线平面的方程。初步确定了接触轨迹线平面后,可以通过交互手段改变接触轨迹线平面的位置和方向,从而可以得到所需要的接触轨迹线。接触轨迹线平面位置的变化是通过改变该平面经过瞬时接触线lc上不同的点得到,而方向的改变则是通过绕方向为VR且过定位点的轴旋转给定的角度来实现。接触轨迹线由各瞬时接触线上的接触中心点构成,因此接触线上的接触中心点是该瞬时接触线与接触轨迹线平面的交点。由于瞬时接触线由离散的点构成,所以从瞬时接触线的各点中选择到接触轨迹线平面距离最小的点作为该瞬时接触线的接触中心点。修形总体方案整个齿面的修形可分为两步进行,首先对接触轨迹线修形,然后对瞬时接触线进行修形。如图8所示,粗实线和粗虚线分别表示修形前和修形后的接触轨迹线,细实线和细虚线分别表示修形前和修形后的瞬时接触线,接触轨迹线上的点同时也是瞬时接触线的点,由定位瞬时接触线lc和接触轨迹线确定的点PC称为齿面修形中心点,该点不修形,接触轨迹线与其它瞬时接触线lk(k≠C)的交点Pk称为瞬时接触线lk的修形中心点,其修形量为hk,点Pk离PC越远,修形量hk越大。在确定好接触轨迹线上所有点Pk的修形量hk并把hk作为瞬时接触线lk的基准修形量予以保存后,再对各条瞬时接触线修形。在对瞬时接触线lk进行修形计算时,先假定接触线修形中心点Pk的修形量为零,按某种法则确定好瞬时接触线lk上所有的点Pk,j的修形量hk,j后,再把该瞬时接触线的基准修形量hk加到每点的修形量上,即Pk,j的实际修形量为hk,j+hk。齿面修形量确定原理与方法1)沿接触轨迹线方向的修形原理与方法如图9示,点P0是齿面修形中心点,该点修形量为零,其余各点离P0的弧长越大,其修形量越大。为了增加修形的灵活性,把整条接触轨迹线以齿面修形中心点为中心分成内外两部分,这两部分可采用不同的修形方式。设整条接触轨迹线的弧长为L,定义内部区域的弧长占整个弧长L的比例为η,令则当接触轨迹线上的点到修形中心点P0的弧长小于LC时,该点位于内部区域;否则,位于外部区域。并令内部区域和外部区域的分界点处(即该点到P0的弧长为LC)的修形量为hC。接触轨迹线的弧长参数L由计算得到,参数η和hC采用交互方式给出。接触轨迹线的点的修形量,可采用下式计算:h=axnn=2,3,4,,,(3-10)沿接触轨迹线方向的修形实质是预先计算每条瞬时接触线lk的基准修形量hk,其值通过计算接触轨迹线和瞬时接触线lk的交点处的修形量得到,适用于接触轨迹线与瞬时接触线lk存在交点的情况。若接触轨迹线与瞬时接触线lk没有交点,则可以构造一个瞬时接触线lk和接触轨迹线的虚拟交点Pk,方法是计算瞬时接触线lk中离接触轨迹线平面最近的点在接触轨迹线平面的投影点,其投影点就是虚拟交点Pk。2)瞬时接触线方向的修形(1)沿瞬时接触线的修形原理如图10所示,对瞬时接触线修形时,先假定每条瞬时接触线的修形中心点修形量为零,其余点离修形中心点越远,其修形量越大,可以采用抛物线等曲线计算每点的修形量。应用所提出的修形理论和方法,进一步可以得如图3-11所示的齿面优化形式。包括无传动比误差的点接触螺旋锥齿轮齿面与无传动比误差的线接触螺旋锥齿轮齿面。无传动比误差是为了提高传动的平稳性,降低振动和噪音;点接触齿面和局部线接触齿面是为了避免安装误差的影响,当安装位置发生误差,接触区只会在中点附近移动而不会使载荷集中到齿轮边缘上去,局部线接触螺旋锥齿轮的修形可增大齿面接触强度。如图4所示为螺旋锥齿轮主动修形设计类型。1)传统点接触齿面;保留接触轨迹线一点不修形,形成传统点接触齿面;2)局部定传动比点接触齿面沿接触轨迹线局部不修形,形成局部定传动比点接触齿面3)定传动比点接触齿面沿着接触轨迹线都不修形,则形成定传动比点接触齿面4)区域线接触定传动比齿面沿着接触轨迹线的局部区域不修形,形成区域线接触定传动比齿面5)局部线接触定传动比齿面沿着接触轨迹线的整个区域不修形,形成局部线接触定传动比齿面4、修形实例:设计者可以功能需求,灵活选择其中的任意一种修形方式,进行预定啮合特性的螺旋锥齿轮齿面的设计。1)接触区域位置及倾斜角度控制接触区域中心所在的位置由用户通过可视化的图形环境选择齿面上的一条瞬时接触线,并以其中点作为接触区域中心所在初始位置。通过对接触轨迹线平面及角度控制,确定接触区域的位置及倾斜方向。接触区域的倾斜角度和重合度相关,重合度大,运转更平稳。图5对接触轨迹线的控制,图中水平平面为离散点云数据,水平线为其中的一条瞬时接触线,竖直线为接触轨迹线。竖直平面的接触轨迹线平面。(a)接触轨迹线近似垂直于齿根(b)增大接触轨迹线倾斜角2)接触区域范围控制对于修形区域的范围的设计,设计者可以根据需要,直接设定修形区域的范围:如直接给定接触区域长轴的范围。参数化交互式修形设计系统主要功能如图11所示,对接触区域范围控制如图所示。接触区域范围大,承载能力强。其中(a)沿着瞬时接触线修形(b)沿着接触迹线修形图12为对接触区域范围的控制,其中(a)接触区域范围为10mm(b)接触区域范围为20mm(c)接触区域范围为30mm4)传动误差控制传动误差的大小关系着齿轮传动过程中的振动和噪声。当沿着接触轨迹线不修形时,会得到定传动比齿面形式。当沿着接触轨迹线修形时,传动比将发生变化。5)修形量控制修形量的大小和修形曲线相关。修形时可采用2阶或高阶曲线。当采用2次抛物线修形式,接触区域内修形量的变化相对于其他高阶曲线变化大。当采用四次曲线修形时,接触区域内的修形量变化比较平稳。接触区域外的修形量相对比较大。大轮螺旋锥齿轮齿面离散测量点云如图13所示在Imageware中采用直接点云拟合方式生成的一侧曲面。基于离散点云拟合出大轮齿面如图14所示2)小轮离散齿面数据拟合首先在Imageware中直接导入凹面和凸面的点云数据。小轮共轭离散齿面求解点云如图15所示在Imageware中采用直接点云拟合方式生成曲面。基于离散点云拟合出小轮齿面如图16所示.通过Imageware拟合曲面的精度分析如图17所示,采用针刺图和颜色编码云图方式,得到误差分布图。本齿面的平均拟合精度凹面为0.0019mm,凸面为0.0017mm。完全满足后续修形需要。加工如图18所示。需要说明的是,按照本发明的制造齿轮的方法和由其制造的齿轮的技术方案的范畴包括上述各部分之间的任意组合。