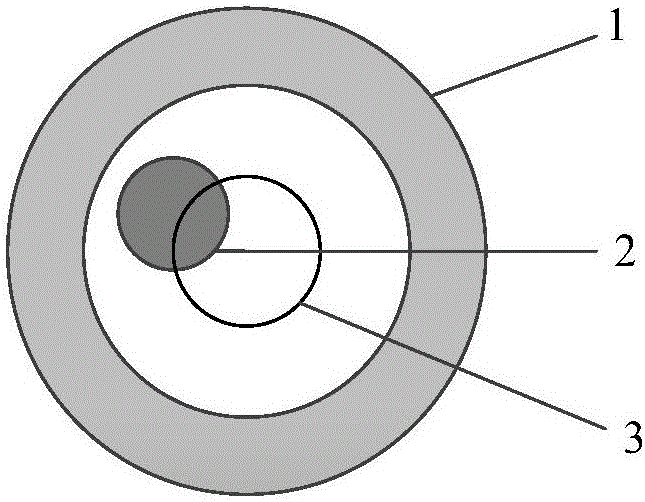
本发明属于机构精度设计
技术领域:
,具体涉及一种考虑磨损的机构运动精度可靠性分配方法,所述方法考虑到机构的可靠性与误差有关,把可靠性分配转化成误差分配,用于确定机构各构件的尺寸公差和铰链间隙。
背景技术:
:运动机构是一类工程中广泛应用的典型运动装置,这就要求机构有较高的精度和可靠性。运动精度可靠性是衡量机构质量的重要指标,因此,对机构进行可靠性设计和分配是很有必要的。传统的可靠性分配方法并不能把可靠性指标分配到构件层次,达到指导机构精度设计的目的。但机构的运动精度可靠性和机构中的误差有关,机构的运动精度主要受原始误差和运行误差的影响。原始误差主要是在机构运行初期就存在,主要由机械制造和装配引起的,主要包括尺寸误差和运动副间隙等;运行误差是指机构运行过程中不断产生的误差,如磨损等引起的,并且这些误差都是随机的。因此可以将机构的可靠性分配转化成机构的误差分配使尺寸误差、运动副间隙满足规定的要求,以保证机构最终的输出满足一定的精度。在国内研究中赵竹青等人在机构运动误差分析的基础上提出了等精度影响法和相依影响法,等精度影响法是将机构所有原始误差对输出偏差的影响按参数大小的比例进行分配,显然该方法有一定的局限性,各原始误差对机构输出偏差的影响不会完全相同,相依影响法的思想是将一些比较难控制和不易改变其允差的机构参数的允差先定下来,将比较容易控制的机构参数的允差作为试凑对象,这往往依靠设计者的经验。这两种方法都不能保证分配结果满足机构精度可靠度(文献[1]赵竹青,周毓明.机构可靠性分析与设计中机构误差的分配方法[J].西安联合大学学报,2002,04:84-87.);随后赵竹青在机构精度可靠性分析的基础上考虑满足机构精度可靠性的要求下对机构进行设计或误差分配,但其并未考虑机构间隙误差以及磨损对机构精度的影响(文献[2]赵竹青.机构运动精度可靠性设计方法及步骤[J].西安联合大学学报,2001,04:52-55.);陈建军等在机构运动精度可靠性分析的基础上,考虑到精度和费用的关系以费用最小为目标,可靠度为约束,开展平面四连杆机构的优化设计,但其忽略了运行误差如磨损对机构可靠性的影响(文献[3]陈建军,陈勇,崔明涛,高伟,赵竹青.基于运动精度可靠性的平面四杆机构优化设计[J].机械科学与技术,2002,06:940-9433.);王晓东等在机构误差传递规律分析的基础上,综合考虑精度与加工成本的关系,以加工成本最小和机构输出误差最小为目标函数,对机构进行误差分配,但忽略了机构精度可靠性以及磨损对机构精度的影响(文献[4]王晓东,王磊,贾方,王兴松.含间隙高速压力机机构的精度优化设计[J].机械工程与自动化,2009,01:187-188+191.);杨世平等在分析各零部件误差对机构运动精度影响的基础上,考虑到精度与成本的关系对机构进行误差分配,但忽略了机构各构件的间隙以及机构的可靠性(文献[5]杨世平,文智慧,李立民,谭援强,陈小告.基于改进最佳极限偏差法的弧面凸轮机构公差分配研究[J].中国机械工程,2014,06:731-736.);颜珍等只考虑到运动副间隙,建立精度与成本的目标函数,进行优化设计(文献[6]颜珍,郭润兰.含间隙平面机构的精度优化设计[J].机械制造,2013,10:42-44.)。国外研究主要集中在考虑机构零件装配过程中的容差分配。G.Prabhaharan等以容差成本函数最小为目标函数,利用遗传算法求解,但其只考虑了构件的尺寸误差(文献[7]PrabhaharanG,AsokanP,RameshP,etal.Genetic-algorithm-basedoptimaltoleranceallocationusingaleast-costmodel[J].TheInternationalJournalofAdvancedManufacturingTechnology,2004,24(9-10):647-660.);S.S.Rao通过区间分析法,考虑尺寸和间隙误差,以装配成本最小为目标函数进行容差分配(文献[8]RaoSS,WuW.Optimumtoleranceallocationinmechanicalassembliesusinganintervalmethod[J].EngineeringOptimization,2005,37(3):237-257.);KumarA等提出了模糊综合评判的容差分配方法,但为考虑间隙以及是否满足规定的可靠性要求(文献[9]KumarA,GokselL,ChoiSK.Toleranceallocationofassembliesusingfuzzycomprehensiveevaluationanddecisionsupportprocesses[C]//ASME2010internationaldesignengineeringtechnicalconferencesandcomputersandinformationinengineeringconference.AmericanSocietyofMechanicalEngineers,2010:1121-1131.)。到目前为止,虽然有很多种关于误差分配的方法,但在对机构进行误差分配时还没有同时将原始误差以及运行误差同时考虑进去并且以满足规定的可靠度为前提的研究。技术实现要素:传统的可靠性分配方法不能将可靠性指标分配到构件层次,本发明提出了一种机构运动精度可靠性的分配方法,该分配方法基于机构运动精度可靠性分析,将机构各构件尺寸误差的均值和方差以及间隙误差的均值和方差作为设计变量对机构进行参数设计;确定设计变量与机构运动精度可靠性的关系,同时构建关于设计变量的成本函数;以机构可靠度为约束条件,成本最小为目标进行优化求解,根据各级尺寸下不同加工等级公差表选择合理的加工等级来确定最后各构件的尺寸公差。本发明提出的考虑磨损的机构运动精度可靠性分配方法,具体步骤为:步骤一、在机构运动分析的基础上进行机构运动精度可靠性分析;步骤二、确定设计变量,并验证所选材料的磨损率在机构理想状态下(不存在间隙和误差)是否满足可靠度指标;步骤三、建立关于设计变量的成本函数;步骤四、建立以可靠度为约束,成本最小为目标的优化模型并求解;步骤五、根据加工等级公差表,利用步骤四的结果选择加工等级,确定构件的尺寸公差,并验证是否满足机构的可靠度指标。本发明的优点和积极效果在于:(1)本发明首次将可靠度指标分配到了构件层次并且最终体现在了构件的尺寸公差和间隙上,达到了指导构件的加工和设计的目的,避免了专业设计独立于传统的可靠性分配,不能参考传统的可靠性分配结果这一缺点。(2)根据相关标准在各加工等级下,不同尺寸对应着不同的公差,在优化模型中求得的公差可能不符合有关标准,本发明可在既保证机构可靠性,又保证成本最小的情况下,能选择一个合理的加工等级。(3)实现自上而下的分配和自下而上的迭代螺旋式上升设计,实现可靠性设计和可靠性预计的相互融合,同时又将专业设计与可靠性相结合,保证最终结果满足可靠度指标要求。附图说明图1为本发明的考虑磨损的机构运动精度可靠性分配方法流程图;图2为实施例中给出的铰链连接示意图;图3为实施例中给出的有效连接模型示意图;图4为实施例中给出的曲柄滑块机构示意图。图中:1.套孔;2.轴销;3.误差圆。具体实施方式下面将结合附图和实施例对本发明的技术方案作进一步的详细说明。本发明提出了一种考虑磨损的机构运动精度可靠性分配方法,该方法先根据设计变量与机构运动精度可靠性的关系验证所选材料的磨损率特征值在机构理想状态下(不存在间隙和误差)是否满足可靠度要求;若满足要求构建关于设计变量的成本函数;以机构可靠度为约束条件,成本最小为目标进行优化求解,根据各级尺寸下不同加工等级公差表选择合理的加工等级,来确定最后各构件的公差和机构最终的可靠度。本发明提出的考虑磨损的机构运动精度可靠性分配方法,流程图如图1所示,包括以下几个步骤:步骤一、在机构运动分析的基础上进行机构运动精度可靠性分析。要进行机构可靠性分析,首先要知道机构运动精度可靠性的定义,机构运动精度可靠性是在给定机构主动件运动规律的条件下,研究机构中指定构件上某一点的位移、速度和加速度,在各种影响因素等随机变量作用下,达到规定值和落在规定值范围内的概率(文献[10]梁清华,何成铭.机构可靠性研究现状及发展趋势[A].中国机械工程学会可靠性工程分会、吉林大学机械科学与工程学院.2012年全国机械行业可靠性技术学术交流会暨第四届可靠性工程分会第四次全体委员大会论文集[C].中国机械工程学会可靠性工程分会、吉林大学机械科学与工程学院:,2012:4.)。机构运动精度可靠度R的数学表达式为:R=φ(μ0-μσ02+σ2)---(1)]]>其中,φ()为标准正态分布累积概率分布函数,μ0和分别是机构输出位移允许误差的均值和方差,μ和σ2分别是机构实际输出位移误差的均值和方差。如果求得机构实际输出位移误差的均值和方差后,就可求得机构的运动精度可靠度R。在明确了机构运动精度可靠性之后,要对机构进行误差分析,对于一个机构而言,如果其由n个构件通过铰链连接而成,通常从动件的位置函数是主动件及中间构件参数的函数,设理想状态下机构输出位移可由下式表示:Y0=f(X1,X2,…,Xn)(2)其中,Y0表示理想状态下机构输出位移,Xi(i=1,2,3……,n)表示理想状态下第i个构件的参数。在实际中由于机构构件在制造加工过程中会存在误差,因此机构实际输出位移可以由下式表示:Y=f(X1+ΔX1,X2+ΔX2,…,Xn+ΔXn)(3)其中,Y表示机构实际输出位移,ΔXi表示第i个构件的参数误差。将式(3)在理想状态下的参数Xi处按泰勒级数展开,鉴于参数误差ΔXi远远小于参数Xi,所以可略去高阶无穷小,只取零阶项和一阶项可得:Y=f(X1,X2,...,Xi)+Σi=1n(∂Y∂Xi)ΔXi---(4)]]>则机构实际输出位移误差为:ΔY=Y-Y0=Σi=1n(∂Y∂Xi)ΔXi---(5)]]>假设不同构件的各参数误差ΔXi彼此是相对独立变量,在这里参数误差只考虑构件尺寸误差,根据最小位移线性叠加原理,则机构由机构构件尺寸误差引起的机构输出位移误差的均值和方差分别为:μ=E(ΔY)=Σi=1n∂Y∂XiE(ΔXi)=Σi=1n∂Y∂Xiμi---(6)]]>σ2=D(ΔY)=Σi=1n(∂Y∂Xi)2D(ΔXi)=Σi=1n(∂Y∂Xi)22σi2---(7)]]>其中,μi和分别为第i个构件尺寸误差的均值和方差。上述的误差分析只考虑了机构原始误差中的构件尺寸误差,在本发明中所有构件都是通过铰链连接,因此铰链中的间隙会影响机构的运动精度,“有效长度模型”理论(文献[11]LEESJ.&GILMOREBJ.1991TheDeterminationoftheprobabilisticpropertiesofvelocitiesandaccelerationsinkinematicchainswithuncertainty[J].JournalofMechanicalDesign,1991,113(1):84-90.)针对铰链式运动副中径向间隙和轴销位置的不确定性因素对连杆有效长度的影响,对机构运动误差做了详尽的分析。如图2所示为一对铰链连接示意图,轴销2在套孔1中运动,轴销2中心随机分布在误差圆3内,误差圆3的半径由套孔1与轴销2的直径差决定,误差圆3的半径rc为:rc=12(d1-d2)---(8)]]>其中,d1和d2分别为套孔1和轴销2的直径。有效长度模型如图3所示,点P和点C分别是套孔1和轴销2的中心,由于间隙的存在,点P和点C不会总是重合,以O点为坐标原点,OP方向为横轴x正方向,纵轴y的正方向垂直于横轴向上,因此有效长度L(OC段)为:L=(l+x)2+y2---(9)]]>其中,l是构件的实际长度,x和y为轴销中心的局部坐标,局部坐标以点P为原点,x和y的正方向与原坐标系相同。轴销中心C随机分布在误差圆3内,因此x和y也具有随机性,假设其服从标准正态分布,则有:μx=μy=0σx2=σy2=(σR2+μR2)/9---(10)]]>其中,μx和μy分别是局部坐标x和y的均值,和分别是局部坐标x和y的方差,μR和是运动副原始间隙的均值和方差。当构件的实际长度l被有效长度L代替后机构输出位移误差均值不变,则同时考虑构件尺寸误差和间隙误差后,机构输出位移误差的均值和方差为:μ=Σi=1n∂Y∂Xiμiσ2=Σi=1n(∂Y∂Xi)2(σi2+σRi2+μRi29)---(11)]]>其中,μRi和为第i个运动副原始间隙的均值和方差。上述误差分析只考虑了存在于构件尺寸和运动副间隙中的误差,由于轴销2在套孔1中频繁运动势必会产生磨损,使运动副间隙增大,故而影响到机构的运动精度。运动副间隙的磨损表现在轴销2直径的减小和套孔1直径的增加,即考虑磨损的实际间隙等于不考虑磨损时的原始间隙与磨损量的总和。Δ'R=ΔR+ΔQ(12)其中,Δ′R为实际间隙,ΔR为原始间隙,ΔQ为磨损量。由于磨损是与载荷、运动速度、温度等许多随机因素有关,是随机变量,而实际间隙又是这些随机变量的线性叠加,因此实际间隙是随机数,其均值和方差分别为:μR′=E(ΔR′)=E(ΔR)+E(ΔQ)=μR+μQσR′2=D(ΔR′)=D(ΔR)+D(ΔQ)=σR2+σQ2---(13)]]>其中,μR和分别是运动副原始间隙的均值和方差,μQ和分别是磨损量的均值和方差。当原始间隙被考虑磨损时的实际间隙代替后,将式(13)代入到式(11)可以得到同时考虑构件尺寸误差、运动副间隙误差和磨损时机构输出位移误差的均值和方差:μ=Σi=1n∂Y∂Xiμiσ2=Σi=1n(∂Y∂Xi)2(σi2+σRi2+σQ2+(μRi+μQ)29)---(14)]]>研究表明磨损主要分为三个阶段:跑合阶段、稳定阶段和加速磨损阶段,我们以稳定阶段为例,稳定阶段的磨损速度基本为一个恒定值,稳定阶段的磨损量与磨损速度可用如下公式表示:q=vt(15)其中,q为稳定阶段的磨损量,v为磨损速度,t为工作时间。磨损速度是一个随机变量,因此稳定阶段的磨损量q的均值μq和方差分别为:μq=μvtσq2=σv2t2---(16)]]>其中,μv和分别是磨损速度的均值和方差,可根据机构的运动规律和构件的材料来确定其取值。将式(16)代入到式(14)中可得磨损稳定阶段机构输出位移误差的均值和方差的表达式:μ=Σi=1n∂Y∂Xiμiσ2=Σi=1n(∂Y∂Xi)2(σi2+σRi2+σv2t2+(μRi+μvt)29)---(17)]]>将式(17)代入到式(1)就可以得到机构运动精度可靠度。步骤二、确定设计变量,并验证所选材料的磨损率在机构理想状态下(不存在间隙和误差)是否满足可靠度指标。机构工作时间t后其可靠度为R0,机构输出位移允许误差的特征值(μ0,σ0)是我们的设计指标,在进行机构设计的时候已经明确,当构件的材料一旦选定,根据机构的运动规律、载荷等条件,磨损速度的特征值(μv,σv)也会随之确定。假设构件尺寸偏差呈对称性,因此构件长度误差均值为0,构件尺寸误差特征值(0,σi)和间隙特征值(μRi,σRi)作为设计变量。为了验证所选材料是否满足规定的可靠度,将磨损速度特征值(μv,σv)在设计变量为0(误差和间隙特征值为0)的情况下代入到式(17)和式(1),若R>R0,说明在实际情况中,由于机构存在误差和间隙时,在该磨损速度下机构的可靠度势必要减小但仍有大于R0的可能性,满足该要求的误差和间隙不只有一组解,本发明的工作就是在其满足机构规定的可靠度的前提下,找出其中的最优解。若R<R0,说明理想状态下都不能满足规定的可靠度要求,当机构存在误差和间隙时更不会满足,后面的分配也是没有意义的,这时应重新选择一种耐磨性更好的材料再继续验证其是够满足规定的可靠度。步骤三、建立关于设计变量的成本函数。设计变量即尺寸误差和间隙特征值反映了各构件和构件配合的精度和公差。从机械加工的常识可知,尺寸和配合的均方差越小,则加工的精度越高,相应的加工成本也将随之增加。加工精度成本函数(文献[3])如下:G(Zi)=Ci(Zi-σ'i)2+Di(18)其中,Ci为加工等级费用修正系数,Di为加工基本费用,Zi为加工精度,σ′i为最低加工精度。在实际中可以通过对有关构件加工费用的统计与分析来调整式(18)中的参数,使得各构件中的费用曲线尽可能与实际情况吻合。加工的精度Zi可以用尺寸误差和间隙的均方差σi和σRi来表示,因此分别建立构件尺寸加工精度的费用函数G(σi)和铰链间隙加工精度费用函数G(σRi):G(σi)=CLi(σi-σ'Li)2+DLi(19)其中,CLi为构件i的尺寸加工等级费用修正系数,DLi为加工构件i的基本费用,σ′Li为构件i的最低加工精度。G(σRi)=CRi(σRi-σ'Ri)2+DRi(20)其中,CRi为间隙i的加工等级费用修正系数,DRi为加工间隙i的基本费用,σ′Ri为间隙i的最低加工精度。因此总的加工精度费用函数如下所示:G(σ)=Σi=1m1G(σi)+Σi=1m2G(σRi)---(21)]]>其中,m1为构件的数量,m2为间隙的数量。同时成本也和构件的公差有关,但是精确建立公差和成本之间的关系是相当复杂的,根据一些实验数据统计,制造成本随着公差的增大呈负指数形式衰减。Dieter曲线是目前研究成本—公差关系的经典曲线(文献[12]王家金,孟宪举.基于成本的连杆机构的稳健性设计[J].机械设计,2006,12:36-38.),该曲线表示为:C(Ti)=aie-biTi---(22)]]>其中,Ti为第i个构件或第i个间隙的公差,C(Ti)为关于公差的成本函数,ai和bi为大于0的曲线拟合参数。根据机械设计中的“3σ”准则,构件的尺寸公差与其均方差有如下关系:Tci=6σi(23)其中,Tci为构件i的尺寸公差。假设间隙偏差呈对称性,所以第i个间隙的公差与其间隙均值有如下关系:TRi=2μRi(24)其中,TRi为第i个间隙的公差。所以总的公差成本函数为:C(T)=Σi=1m3C(Ti)---(25)]]>其中,m3为所考虑的公差的数量。因此,机构总成本为:W=G(σ)+C(T)(26)步骤四、建立以可靠度为约束,成本最小为目标的优化模型并求解。机构的构件尺寸误差和运动副间隙会导致机构输出运动产生机械误差,进而影响机构的运动精度。为了提高运动精度,希望在设计时严格规定构件尺寸误差和运动副间隙,但严格的误差和运动副间隙将大大增加制造成本。为了解决运动精度和制造成本这一矛盾,本发明以可靠度为约束,成本最小为目标函数,建立优化模型如下所示:minWs.t.μ0-μσ02+σ2≥φ-1(R0)0<σi≤Li′0<σRi≤Ri′μRi>0---(27)]]>其中,R0为设计时所要求的工作t时间后的可靠度,φ-1()为标准正态分布累积概率分布函数的逆函数。许多智能优化算法都可以用来求解上述优化模型,本发明拟采用遗传算法。当求解出构件尺寸误差方差后,根据式(23)可得到构件的尺寸公差。步骤五、根据加工等级公差表,选择合理的加工等级,确定合理的构件尺寸公差,并验证是否满足机构的可靠度指标。不同的构件尺寸在不同的加工等级下其公差是有相应的标准的,在步骤四中所求得的构件的尺寸公差不一定能满足规定的标准,因此要根据表1且结合步骤四中的公差选择一个合理的加工等级来确定构件的尺寸公差。表1各级尺寸下加工等级IT5至IT8的公差值用h来表示k前面的系数(7,10,16,25,……,1000,1600,2500),构件的尺寸公差可表示为(文献[13]吴波.机械可靠性设计中的零件尺寸公差[J].机械设计,1990,04:30-34+2-3.):T=hk(28)由(文献[13])可知:k=0.45l3+0.001l(μm);l≤500mm0.004l+2.1(μm);500<l≤3150mm---(29)]]>其中,l是构件的实际长度。根据式(28)由构件尺寸和步骤四中求得的构件尺寸公差,在未考虑加工标准时,可以得出理论上的h值,并用ha表示:ha=Tci/k(30)因为上述所求的ha不一定满足相关的加工标准,这样的加工在实际生产中是没有意义的,为了满足有关标准要求h取值应该在表1中选取,考虑到要满足规定的机构运动精度可靠度的要求,加工等级应该越高越好,即h≤ha,但出于对成本的考虑,加工等级不能无限的高,即h不能无限的减小,因此,h应该在表1中取不大于ha的最大值。则经过综合考虑后最终构件实际尺寸公差为:T'ci=hk(31)如果步骤四中求得的构件公差比最高加工等级规定的公差还要小,即步骤五中ha<7,需要重新选择一种耐磨性好的材料,如果比最低加工等级规定的公差还要大,即步骤五中ha>2500,为了节约成本可以按最低加工等级进行加工,即h=2500。实施例基于上述理论对图4的曲柄滑块机构进行可靠性分配或精度设计。如图4所示,所述的曲柄滑块机构包括曲柄OA和连杆AB,以及滑块,O点与滑块上的B点同高,曲柄OA的长度r=20cm,连杆AB的长度g=40cm,α为曲柄OA旋转过的角度。如果在工作了20kh后转角α=90°时,所要求的机构精度可靠度R0=0.942,允许的输出位移误差特征值(μ0,σ0)=(0.95,0.01)(cm),现以磨损的稳定阶段为例,假设所选构件材料在O点和A点处的磨损速度特征值(μv,σv)=(0.06,0.0033)(cm/kh),B处的间隙可忽略。试确定O点和A点处的间隙特征值和构件的尺寸公差。步骤一、在机构运动分析的基础上进行机构运动精度可靠性分析。由图4可知曲柄滑块机构的运动方程为:Y=rcosα+g2-r2sin2α---(32)]]>其中,Y为曲柄滑块的输出位移。根据式(5)可知曲柄滑块机构输出位移误差为:ΔY=∂Y∂rΔr+∂Y∂gΔg+∂Y∂αΔα---(33)]]>假设输入转角为理想值,即Δα=0,则有:ΔY=∂Y∂rΔr+∂Y∂gΔg---(34)]]>当α=90°,r=20cm,g=40cm时有:∂Y∂r=cosα-rsin2αg2-r2sin2α=13---(35)]]>∂Y∂g=gg2-r2sin2α=23---(36)]]>由于曲柄OA和连杆AB的尺寸误差均值为0,因此机构位移输出误差均值为0,将式(35)和式(36)代入式(17)最后可得机构输出位移误差均值和方差:μ=0σ2=13(σr2+σR2+σv2t2+(μR+μvt)29)+43(σg2+σR2+σv2t2+(μR+μvt)29)---(37)]]>将式(37)代入式(1)后可得到曲柄滑块机构运动精度可靠度。步骤二、确定设计变量,并验证所选材料的磨损率在机构理想状态下(不存在间隙和误差)是否满足可靠度指标。假设O点和A点处的间隙特征值相同,其特征值为(μR,σR),OA长度误差特征值(0,σr)和AB长度误差特征值(0,σg)作为设计变量。将磨损速度特征值(μv,σv)=(0.06,0.0033)(cm/kh)和工作时间t=20kh代入式(37),其中设计变量取0,可得到只考虑磨损因素状态下机构输出位移误差均值和方差为:μ=0σ2=0.2675---(38)]]>将式(38)结果及机构允许的输出位移误差特征值(μ0,σ0)=(0.95,0.01)(cm)代入到式(1)可得到机构的运动精度可靠度:R=φ(0.95-00.012+0.2675)=0.97---(39)]]>显然R>R0,可以进行步骤三。步骤三、建立关于设计变量的成本函数。如果式(19)、(20)中各加工等级费用修正系数CLr=CRO=CRA=9000,CLg=105,σ′Li=DLi=σ′Ri=DRi=1,根据式(19)、(20)、(21)可以得到机构的精度成本函数:G(σ)=9×103×(σr-1)2+105×(σg-1)2+2×9×103×(σR-1)2+4(40)如果式(22)中ar=9000,ag=105,aO=aA=1.5×105,bi=1,根据式(22)、(23)、(24)和(25)可得到机构的公差成本函数:C(T)=9×103×e-6σr+105×e-6σg+2×1.5×105×e-2μR---(41)]]>因此,总的成本函数为:W=9×103×(σr-1)2+105×(σg-1)2+2×9×103×(σR-1)2+4+9×103×e-6σr+105×e-6σg+2×1.5×105×e-2μR---(42)]]>步骤四、建立以可靠度为约束,成本最小为目标的优化模型并求解。优化分配模型如下:minWs.t.0.950.012+σ2≥1.570<σr≤1,0<σg≤1,0<σR≤1μR>0---(43)]]>式中W如式(42)所示,σ2如式(37)所示。利用遗传算法对该优化模型进行求解,其结果如表2所示:表2优化结果(cm)设计变量优化结果/cmσr0.071σg0.139μR0.149σR0.081根据式(23)可以得到OA和AB的尺寸公差:Tr=6σr=0.426cmTg=6σg=0.834cm---(44)]]>Tr和Tg分别为曲柄OA和连杆AB理论上的尺寸公差。步骤五、根据加工等级公差表,选择合理的加工等级,确定合理的构件尺寸公差,并验证是否满足机构的可靠度指标。由式(29)可知:kr=0.452003+0.001×200=2.83(μm)kg=0.454003+0.001×400=3.71(μm)---(45)]]>将(44)和(45)带入(30)可得:har=Tr/kr=1504.441,hag=Tg/kg=2247.978(46)根据加工等级公差相关标准可知,上述参数har和hag需要满足表1所示的取值。考虑满足可靠度的要求同时满足成本最小,因此,h应该在表1中取不大于ha的最大值,hr=1000,hg=1600,并将该结果和(45)式计算结果带入式(31),可得到曲柄和连杆最终的实际优化公差:Tr′=hrkr=1000×2.83μm=0.283cmTg′=hgkg=1600×3.71μm=0.5936cm---(47)]]>根据式(23)由式(47)的结果可以得出最终构件实际尺寸误差的方差,最终优化结果如表3所示:表3最终优化结果(cm)设计变量优化结果/cmσ′r0.047σ′g0.099μR0.149σR0.081此时将表3结果和磨损特征值以及工作时间代入到式(37)得到曲柄滑块机构实际输出位移误差的均值和方差(μ,σ)=(0,0.594),将其代入式(1),则最终曲柄滑块机构的运动精度可靠度为0.954,显然0.954>0.942,满足规定的可靠度要求。因为构件偏差呈对称性,因此偏差为公差的一半:Δr=12Tr′=0.1415,Δg=12Tg′=0.2968---(48)]]>因此,在对曲柄滑块机构进行可靠性分配或精度设计时,为了达到机构的可靠性指标,同时加工成本最低,对构件进行生产或加工时,其参数应满足如下要求:曲柄OA的长度连杆AB的长度铰链连接处的间隙特征值为(0.149,0.081)cm。当前第1页1 2 3