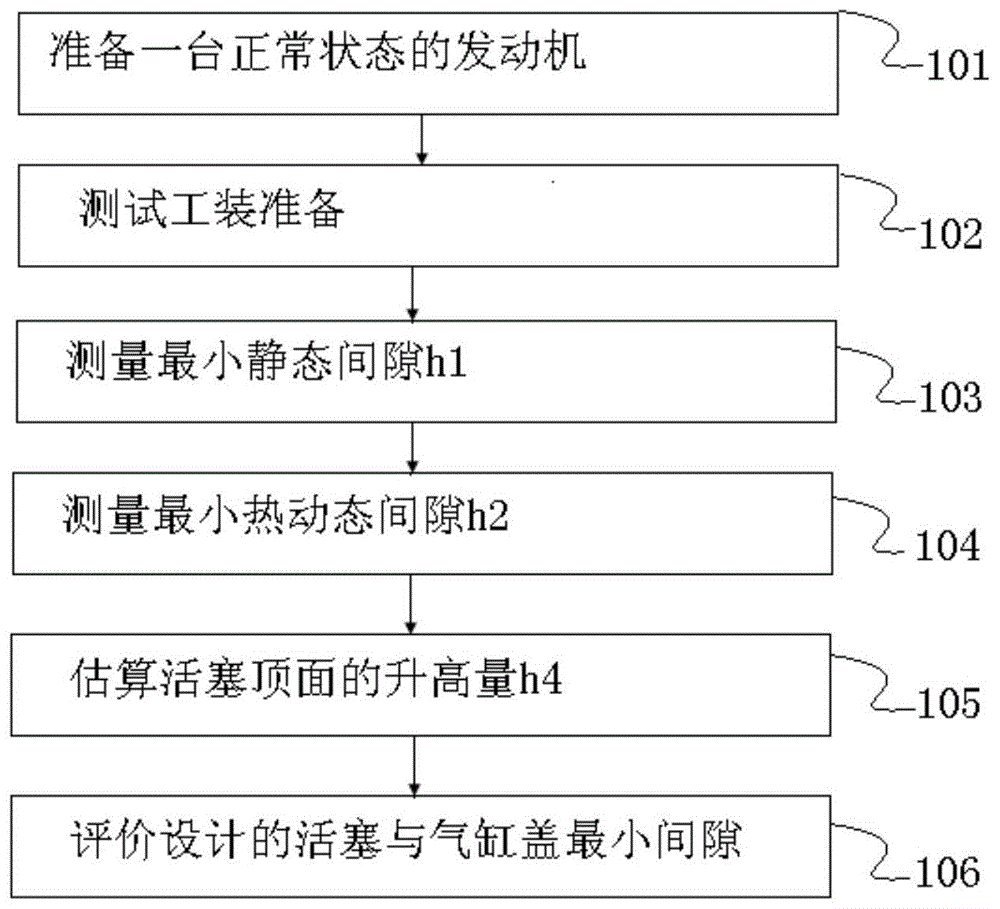
本发明涉及发动机开发试验领域,特别涉及一种发动机活塞与气缸盖最小间隙的评价方法。
背景技术:
:发动机内部活塞与气门、活塞与气缸盖之间存在相对运动,设计上以尺寸链来控制最小间隙,辅助以CAE核算,防止出现活塞与气门、气缸盖发生碰撞。而实际上因缺少与试验的结合,无法准确给定边界值和确定零部件的热膨胀量,市场运行的发动机仍有活塞打顶故障的发生。在发动机试验开发阶段,活塞与气门、活塞与气缸盖之间一直只能进行最小静态间隙的测试,即使用铅丝等较软的材料,放置在活塞顶部的相应位置,装配好缸盖和气门等零部件后,手动盘动发动机两圈以上,再拆开气缸盖和气门等零部件后,取出活塞顶部的铅丝测量最小的间隙,作为活塞与气门、活塞与气缸盖的最小间隙。目前,使用的活塞与气门及气缸盖最小静态间隙的测试方法未考虑到发动机实际运行工况,忽略了惯性力和零部件实际的配合间隙、热伸长量影响,所以测试结果与实际间隙差异较大,也无法正确评价设计指标。公开于该
背景技术:
部分的信息仅仅旨在增加对本发明的总体背景的理解,而不应当被视为承认或以任何形式暗示该信息构成已为本领域一般技术人员所公知的现有技术。技术实现要素:本发明的目的在于提供一种发动机活塞与气缸盖最小间隙的评价方法,充分考虑了发动机的实际运行的极限工况,考虑了极限惯性力和零部件实际的配合间隙、热伸长量的影响,可正确评价设计的最小间隙,评估发动机市场运行发生活塞打顶的风险。为实现上述目的,本发明提供了一种发动机活塞与气缸盖最小间隙的评价方法,包括如下步骤:准备一台正常状态的发动机,在其活塞顶部加工布置螺孔;使用耐高温的软材料加工成螺塞,并将该螺塞安装在活塞顶部的螺孔位置,螺塞凸出活塞顶部高度大于活塞与气缸盖设计计算的最大间隙;人工盘动发动机,测量活塞表面的螺塞凸出活塞顶部的高度为活塞与气缸盖的最小静态间隙h1;将发动机安装在试机台架,起动发动机运行至超速工况后返回怠速并停机,发动机停机冷却后,测量活塞表面的螺塞凸出活塞顶部的高度为活塞与气缸盖的最小热动态间隙h2;利用最小静态间隙h1和最小热动态间隙h2的差值根据温度来分配计算热膨胀和受力伸长量,进而得到活塞顶面的升高量h4;在根据尺寸链计算活塞与气缸盖的间隙的极小值h3大于升高量h4的情况下,将最小热动态间隙h2≥(0.2%×活塞行程)作为评价活塞与气缸盖最小间隙的设计标准。优选地,在起动发动机运行至超速工况的过程中,起动发动机逐步提升转速和扭矩,在100%标定转速和100%标定功率下运行至少15min,再提高功率至110%标定功率状态下运行至少15min,然后在10s内返回怠速并停机。优选地,停机后,在10s内倒拖发动机达到125%标定转速并稳定运行10s,然后返回怠速并停机。优选地,在125%标定转速并稳定运行10s后,再倒拖发动机到140%标定转速运行10s,然后返回怠速并停机。优选地,在活塞顶部均匀加工布置4-6个螺孔。与现有技术相比,本发明具有如下有益效果:发动机活塞与气缸盖最小间隙的评价方法,用于测试和评价活塞与气缸盖之间的最小热动态间隙,实现了从原来只能测试最小静态间隙变为测试最小热动态间隙,解决了活塞与气缸盖之间的最小热动态间隙无法测试和准确评价的问题,按照该评价方法能避免出现活塞与气缸盖发生碰撞的严重故障,大幅度降低因为该严重故障导致的三包索赔服务费用。另外,该评价标准可对配气机构、曲柄连杆机构的设计起到重要的指导作用,从设计源头上降低发动机运行故障风险。附图说明图1是根据本发明的发动机活塞与气缸盖最小间隙的评价方法的流程图。图2是根据本发明的发动机活塞与气缸盖最小间隙的评价方法中发动机活塞与气缸盖的尺寸链示意图。具体实施方式下面结合附图,对本发明的具体实施方式进行详细描述,但应当理解本发明的保护范围并不受具体实施方式的限制。除非另有其它明确表示,否则在整个说明书和权利要求书中,术语“包括”或其变换如“包含”或“包括有”等等将被理解为包括所陈述的元件或组成部分,而并未排除其它元件或其它组成部分。如图1所示,根据本发明具体实施方式的一种发动机活塞与气缸盖最小间隙的评价方法,包括如下步骤:步骤101,准备一台正常状态的发动机,在其活塞顶部加工布置螺孔;步骤102,使用耐高温的软材料加工成螺塞,并将该螺塞安装在活塞顶部的螺孔位置,螺塞凸出活塞顶部高度大于活塞与气缸盖设计计算的最大间隙;步骤103,人工盘动发动机,测量活塞表面的螺塞凸出活塞顶部的高度为活塞与气缸盖的最小静态间隙h1;步骤104,将发动机安装在试机台架,起动发动机运行至超速工况后返回怠速并停机,发动机停机冷却后,测量活塞表面的螺塞凸出活塞顶部的高度为活塞与气缸盖的最小热动态间隙h2;步骤105,利用最小静态间隙h1和最小热动态间隙h2的差值根据温度来分配计算热膨胀和受力伸长量,进而得到活塞顶面的升高量h4;步骤106,在根据尺寸链计算活塞与气缸盖的间隙的极小值h3大于升高量h4的情况下,将最小热动态间隙h2≥(0.2%×活塞行程)作为评价活塞与气缸盖最小间隙的设计标准。作为一种优选实施例,在起动发动机运行至超速工况的过程中,起动发动机逐步提升转速和扭矩,在100%标定转速和100%标定功率下运行至少15min,再提高功率至110%标定功率状态下运行至少15min,然后在10s内返回怠速并停机。作为一种优选实施例,停机后,在10s内倒拖发动机达到125%标定转速并稳定运行10s,然后返回怠速并停机。作为一种优选实施例,在125%标定转速并稳定运行10s后,再倒拖发动机到140%标定转速运行10s,然后返回怠速并停机。作为一种优选实施例,在活塞顶部均匀加工布置4-6个螺孔。上述方案中,在发动机准备中,选择一台正常状态的发动机,在活塞顶部加工布置几个M2或M3的螺孔,螺孔的位置必须包含活塞的气门让位坑位置。在测试工装准备中,使用较软材料并能耐一定高温的材料,比如黄铜,加工成M2或M3的螺塞,并安装在活塞顶部的相应螺孔位置。螺塞凸出活塞顶部高度必须高于设计计算最大间隙。按装配技术条件要求装配好发动机(气缸盖部件装气门,并调整好气门间隙)后先人工盘动发动机至少两圈,然后拆下气缸盖部件,测量活塞表面的螺塞凸出活塞顶部的高度,该高度为活塞与气缸盖的最小静态间隙h1、活塞与气门的最小静态间隙H1。在测试过程中,发动机安装在具备倒拖功能台架。起动发动机,逐步提升转速和扭矩,待油温、水温达到合适值后,运行在100%标定转速和100%标定功率下至少15min,再提高功率至110%标定功率状态下运行至少15min。目的是让发动机内部各零部件充分受热膨胀,达到发动机使用的极限热负荷。下一步,发动机在10s内迅速返回怠速并停机,然后在10s内倒拖发动机达到125%标定转速(轻型及轻型以下车发动机),并稳定运行10s,再倒拖发动机到140%标定转速(中重型车用发动机)运行10s,是否运行到140%标定转速由发动机配气机构情况和市场定位决定。在发动机超速工况下,发动机运行到用户可能会用到的最大极限转速,此时活塞连杆组受力伸长量达到极限,加上活塞连杆组热膨胀还处于最大极限,这种状态下出现活塞与气门碰撞、活塞与气缸盖碰撞的风险最大。运行的工况见表1。表1:测试结束后,发动机停机冷却后下台架并进行拆检。拆出气缸盖部件,测量活塞表面的螺塞凸出活塞顶部的高度,该高度为活塞与气缸盖的最小热动态间隙h2、活塞与气门的最小动态间隙H2。最后,评价标准。对试验结果进行分析。首先从尺寸链计算活塞与气缸盖的间隙(即压缩余隙),可得到活塞与气缸盖间隙的极大值和极小值h3。因按尺寸链计算的结果未考虑热膨胀和受力伸长,实测间隙会在尺寸链计算下限或低于下限值。需要从试验结果统计分析活塞与气缸盖最小静态间隙h1和最小动态间隙h2的差值,来分析热膨胀量和伸长量,并理论上估算热膨胀和受力伸长量,得到活塞顶面升高量h4。计算见表2。表2:以下以某具体试验为例进行说明:1、试验结果活塞与缸盖最小静态间隙h1①缸②缸③缸④缸⑤缸⑥缸前端1.171.071.381.181.311.14后端1.141.271.361.181.11.22进侧1.351.3211.271.331.33排侧0.840.870.91.060.880.92静态间隙h1平均为1.15mm活塞与缸盖最小热动态间隙h2①缸②缸③缸④缸⑤缸⑥缸前端0.370.500.480.520.540.50后端0.560.470.550.530.50.67进侧0.420.550.540.520.540.55排侧0.520.420.590.420.590.50热动态间隙h2平均为0.51mm活塞与缸盖静态和热动态差值h1-h2①缸②缸③缸④缸⑤缸⑥缸前端0.80.570.90.660.770.64后端0.580.80.810.650.60.55进侧0.930.770.460.750.790.78排侧0.320.450.310.640.290.42h1-h2平均为0.642、设计计算与试验结合活塞与缸盖间隙的极大值和极小值h3(按尺寸链计算)活塞凸高检测值(实测值)活塞凸高的实测值全部在计算值范围内,且实测值的均值与计算值的均值基本相当。可以推断轴承间隙大致会在均值附近,通过计算得到总的半径轴承间隙大约为0.09mm。轴承间隙minmax均值主轴承半径间隙0.0250.0620.0435连杆瓦轴承半径间隙0.0150.0470.031连杆衬套轴承半径间隙0.0050.0130.009活塞销孔与销半径间隙0.0030.010.0065总半径间隙0.0480.1320.09活塞连杆组升长量=活塞与缸盖静态和热动态差值(h1-h2)-直径轴承间隙=0.64-0.18=0.46mm。按照热膨胀和受力等使活塞顶面上升的0.46mm分配活塞、连杆、机体的平均温升,其中活塞温升250℃、连杆温升150℃、机体温升80℃,得到活塞顶面升高量h4。在上表中,h4=活塞膨胀量+连杆膨胀量-机体膨胀量+连杆升长量,具体是膨胀量=线膨胀系数*温升*长度,受力升长量=往复惯性力*连杆长度÷弹性模量÷连杆截面积,其中往复惯性力=活塞组质量*曲柄半径*最大角速度^2*(1+曲柄半径/连杆长度),其中角速度=π*最高转速/30。从分配计算结果可见,h4=0.4540mm与实际测试结果0.46mm基本相当。再将活塞、连杆、机体平均温升的分配方法运用到其他机型上,发现按活塞温升250℃、连杆温升150℃、机体温升80℃分配具有一定的代表性,与试验结果基本符合。3、评价标准设计计算上,需要满足尺寸链计算的极小值>活塞顶面升长量,才能保证不会出现活塞与缸盖碰撞的问题,即使h3(极小值)=0.548mm>h4=0.454mm,满足设计要求。统计分析多个试验结果,我们提出试验通过标准h2≥(0.2%×活塞行程),即h2=0.51mm≥(0.2%×活塞行程)=0.2%×115mm=0.23mm满足试验要求。通过上述理论和试验结果的结合,计算上需要满足h3(极小值)-h4>0。统计分析实际试验结果,将h2≥(0.2%×活塞行程)作为评价设计的活塞与气缸盖最小间隙的标准,试验通过该标准后,在各种极限使用条件下,均不会出现活塞与气缸盖碰撞的问题。综上,本实施例的发动机活塞与气缸盖最小间隙的评价方法,用于测试和评价活塞与气缸盖之间的最小热动态间隙,实现了从原来只能测试最小静态间隙变为测试最小热动态间隙,解决了活塞与气缸盖之间的最小热动态间隙无法测试和准确评价的问题,按照该评价方法能避免出现活塞与气缸盖发生碰撞的严重故障,大幅度降低因为该严重故障导致的三包索赔服务费用。另外,该评价标准可对配气机构、曲柄连杆机构的设计起到重要的指导作用,从设计源头上降低发动机运行故障风险。前述对本发明的具体示例性实施方案的描述是为了说明和例证的目的。这些描述并非想将本发明限定为所公开的精确形式,并且很显然,根据上述教导,可以进行很多改变和变化。对示例性实施例进行选择和描述的目的在于解释本发明的特定原理及其实际应用,从而使得本领域的技术人员能够实现并利用本发明的各种不同的示例性实施方案以及各种不同的选择和改变。本发明的范围意在由权利要求书及其等同形式所限定。当前第1页1 2 3