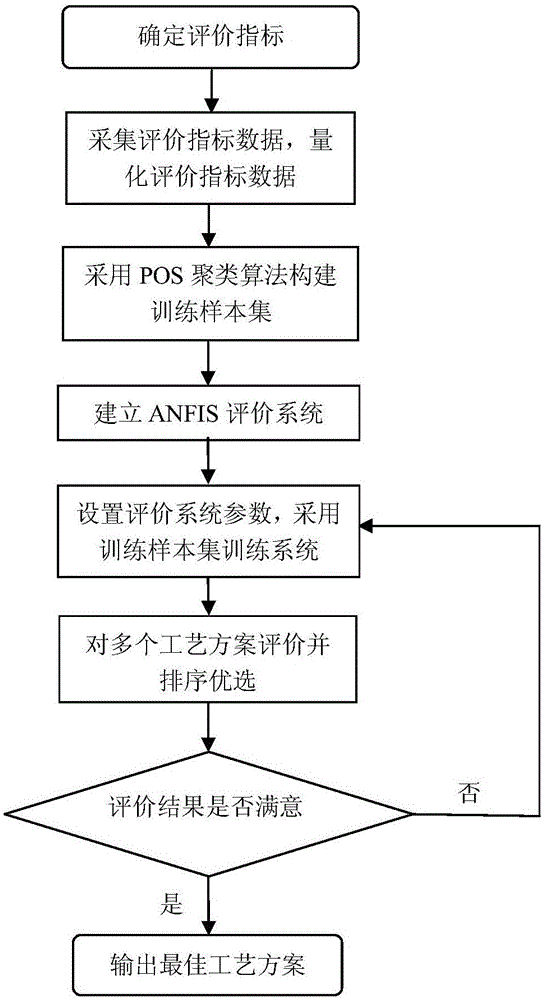
本发明涉及切削工艺
技术领域:
,尤其涉及一种切削加工工艺优选系统及方法。
背景技术:
:当今世界,各国都在积极追求制造业的绿色、智能、可持续发展。特别是进入新世纪以来,绿色制造已成为我国制造业发展的重要趋势。目前,我国企业中绿色制造工艺技术的应用率很低,主要原因是一方面企业对绿色制造工艺的技术储备不足,制造工艺水平较低;另一方面,企业对绿色制造认识不足,缺少实用的绿色工艺分析评价方法和优选工具。因此,迫切需要开发一种切削工艺评价方法和优选工具,以实现绿色切削工艺的优化与开发,促进企业绿色制造的升级与开展。金属切削加工是制造业的重要组成部分,是机械加工领域中应用最广泛的制造工艺技术之一。切削加工采用刀具从工件上切除多余材料,从而获得形状、尺寸精度及表面质量等合乎要求的零件的加工技术手段。但切削加工往往也是机械制造业中对资源和环境影响最大的一种加工工艺。生产工艺的优劣直接关系到资源的消耗量和废物排放的种类及数量,对环境的影响至关重要。随着我国环保法规的健全,切削废液及排放废物的回收处理成本将进一步增加,加工的高能耗、高成本将加重制造企业的经济负担,也制约对资源和能源的合理利用。因此,对切削工艺过程进行绿色特性评价和优选,开发高效科学的切削工艺评价方法及优选工具,实现在保证产品质量的同时、提高劳动生产率、降低加工成本、缩短生产周期并优化利用资源、减少对环境的影响,最终实现经济效益、环境效益和社会效益的最优化。切削工艺的评价优选是一个包括工艺特性分析、评价指标体系构建、评价方法建模的开放式复杂巨系统,具有高度非线性和复杂不确定性,系统中各种耦合问题复杂并呈现高维化评价特征。毫无疑问,针对这一复杂系统的分析与管理,无论是采用经典的控制理论,还是采用传统的数学手段,都将遇到诸如信息不确定性、模型合理可靠性、数据资料不完备性等方面的困难,亟待研究和发展新的评价优选方法体系。目前,广泛应用的绿色制造评价方法主要分为两大类:一类是基于生命周期评价方法;另一类是层次分析评价法。两类评价方法的特征与比较如表1所示。近几年,我国在绿色制造方面的评价也主要集中于以上两种方法或其改进方法,尚未有创新和突破。表1基于生命周期和层次分析两种评价方法的比较技术实现要素:针对现有技术的缺陷,本发明提供一种切削加工工艺优选系统及方法,能实现智能评价和事前评价,且评价过程简洁明了,通过该系统及方法,可以将同一零件不同切削加工工艺方案进行比较,确定最优工艺路线,在保证减小排放、保护环境的提前下,更好的实现切削加工工艺。一方面,本发明提供一种切削加工工艺优选系统,该系统包括评价指标选择器、数据量化处理器、样本分类器、工艺方案评价器和工艺方案选择器;评价指标选择器用于在对传统工艺评价指标研究的基础上,充分考虑切削工艺的绿色特性及影响因素,选择评价指标,并按照选择的评价指标收集切削加工工艺数据;数据量化处理器用于对于收集的切削加工工艺数据进行量化处理,将评价指标分为定性指标和定量指标,分别进行量化,使工艺数据以数值形式表示;再对量化好的数值进行归一化处理,即将有量纲的数值经过变换,化为无量纲的数值,生成数值值域为[0,1]的纯小数;样本分类器用于将数据量化处理器处理好的样本采用粒子群优化算法进行聚类分析,生成被自适应神经模糊推理系统(AdaptiveNeuro-FuzzyInferenceSystem,简称ANFIS)学习的训练样本集;工艺方案评价器包括模型建立模块、模型训练模块和方案评价模块;模型建立模块用于建立ANFIS模型;模型训练模块用于采用训练样本集训练建立的ANFIS模型,使该模型收敛,自动生成模糊推理规则;方案评价模块用于将数据量化处理器生成的待检测样本输入训练过的ANFIS,根据ANFIS学习获得的推理规则,智能决策计算输出结果;工艺方案选择器用于对制造同一机械零件的多个检测工艺方案的评价结果进行比较,选取最优工艺方案。进一步地,在量化处理中,对于定性指标,由专家采用十分制打分方法进行量化;对于定量指标,则直接采用相应测量值进行量化。另一方面,本发明还提供一种切削加工工艺优选方法,基于粒子群分类和自适应神经模糊推理系统,采用上述的切削加工工艺优选系统实现,该方法包括如下步骤:步骤1:依据切削工艺的绿色特性,确定切削加工工艺的评价指标,选择与切削工艺绿色特性密切相关的10个指标作为评价指标,包括:切削液毒性、切屑回收、原材料消耗、切削液消耗、夹具、刀具消耗、耗电量、加工费、设备折旧费和舒适性;步骤2:采用定性与定量相结合的量化方法对步骤1中的切削加工工艺的评价指标进行量化处理,并进行归一化处理,生成待检测的工艺评价指标数据样本;步骤2.1:量化指标数据;将评价指标分为定性指标和定量指标,对于无法用数值计量的定性指标,参考有关机械加工的法规、标准,由专家采用十分制打分方法进行量化;对于定量指标则直接采用加工统计测量值或仿真测量值;步骤2.2:对量化的指标数据进行归一化处理;采用小数定标标准化方法(Decimalscaling)对量化好的数值进行归一化处理,按式(6)将指标A的原始值w归一化为w',生成数值值域为[0,1]的纯小数;w'=w/(10*a)(6)其中,a表示小数点移动位数,等于指标A的取值中的最大绝对值整位数;步骤3:采用粒子群优化算法对归一化的工艺评价指标数据样本进行聚类分析,建立训练样本集,具体方法为:步骤3.1:随机选择簇的中心(即均值)并赋值给各个粒子,随机产生粒子的速度,并设定最大速度Vmax;步骤3.2:对每个粒子按照最小距离原则对数据进行划分,按照式(7)所示的目标函数Je计算各个粒子的适应值,更新个体极值;其中,Cr是表示第r个聚簇;Nc为聚簇的个数;zp表示样本的数据向量;mr表示簇Cr中样本的中心,nr表示簇Cr中样本的个数;其中,Nb为数据向量的维数;zpk表示第k维样本的数据向量;mrk表示簇Cr中第k维样本的中心;步骤3.3:根据各个粒子的个体极值,找出全局极值和全局极值位置;步骤3.4:按粒子群优化算法的速度公式更新粒子的速度,并把它限制在最大速度Vmax内;步骤3.5:按粒子群优化算法的位置公式更新粒子的位置;步骤3.6:计算种群中的个体适应值,若满足终止条件,则算法结束,输出最优粒子的位置即最优的Nc个聚类中心,否则,返回步骤3.4继续进行速度更新;步骤4:建立自适应神经模糊推理系统模型;采用Takagi-Sugeno型模糊推理系统作为ANFIS的核心结构,构建由前件网络和后件网络两部分组成的多输入、单输出的评价模型,前件网络用于产生每条模糊规则对输入样本的隶属度,后件网络用于生成每条模糊规则的加权和;前件网络包括四层结构:第一层为前件网络输入层,其每个节点直接与输入向量的各分量连接,节点数为N1=p,p为输入样本的维数,用于将输入样本x=[x1,x2,…,xp]T传送到下一层;第二层表示经计算得到的各输入分量属于模糊集合的隶属度,节点数N2=C×p,其中C为模糊规则总数;第三层每个节点代表一条模糊规则,用于确定每条规则的隶属度ui,节点数N3=CP;第四层为前件网络输出层,节点数与第三层相同,输出为(i=1,…,C),表示归一化计算后前件网络的输出值,即输入样本对每条模糊规则的隶属度,如式(8)所示;后件网络包括C个结构相同的子网络,每个子网络产生一个输出量,即每条模糊规则的权值;C个子网络均包括三层结构:第一层为子网络输入层,节点数为p+1个,其中第0个结点的输入值为1,用于提供模糊规则后件的常数项;第二层节点数为C个,每个节点代表一条模糊规则,用于计算每个规则的后件;第三层为子网络输出层,输出为yi(i=1,…,C),表示模糊规则后件的加权和,加权系数为前件网络的输出;后件网络的最终输出为Y,即模型的输出如式(9)所示:步骤5:设定初始化参数,采用步骤3生成的训练样本集训练步骤4建立的模型,经迭代计算,使该模型收敛,自动生成模糊推理规则,对待检测样本进行智能评价,具体方法为:步骤5.1:采用模糊C-均值(FCM)算法对前件网络进行训练,通过迭代计算优化第二层节点的隶属度中心,输出结果为输入样本对每条模糊规则的隶属度,包括以下步骤:步骤5.1.1:设置加权指数λ,λ∈[1,∞),模糊规则数C,输入样本个数n,输入样本维数p,终止误差ε,最大迭代次数LOOP1;迭代计数变量赋初值IT1=0;步骤5.1.2:用值域为(0,1)的随机数初始化隶属度矩阵U(IT1),隶属度矩阵uij为隶属度矩阵内元素,并满足i为正整数,且i=1,2,…,C;j为正整数,且j=1,2,…,n;步骤5.1.3:根据计算第i条模糊规则聚类中心向量zi=[z1i,z2i,L,zpi],公式为:其中,xj表示第j个输入样本向量;步骤5.1.4:更新隶属度矩阵U(IT1+1),如式(11)所示;其中,dij表示第j个样本向量到聚类中心向量的欧式距离,dkj表示第j个样本向量到聚类中心向量的欧式距离;步骤5.1.5:若满足或IT1>LOOP1,其中,‖·‖为欧式距离算式,则终止迭代计算,否则更新迭代计数变量,IT1=IT1+1,返回步骤5.1.3;步骤5.2:对后件网络进行训练,后件网络包括C个结构相同的子网络,每个子网络均采用最小均方(LMS)算法调整后件网络的连接权值,包括以下步骤:步骤5.2.1:设置学习率β,终止误差ε1,最大迭代次数LOOP2,迭代计数变量赋初值IT2=0;步骤5.2.2:用值域为(0,1)的随机数初始化权值矩阵bi=[b0i,b1i,L,bpi],i=1,2,…,C;步骤5.2.3:计算后件子网络输出值yi,表示第IT2次迭代产生的第j个输入样本向量对应的后件子网络输出,如式(12)所示;其中,表示归一化计算的前件网络输出值;步骤5.2.4:更新权值矩阵如式(13)所示;其中,表示后件子网络期望输出值;步骤5.2.5:若满足或IT2>LOOP2,则终止迭代计算;否则更新迭代计数变量,IT2=IT2+1,返回步骤5.2.3;步骤6:使用训练后的模型对步骤2生成的待检测工艺评价指标数据样本进行评价,并根据评价结果输出最优切削加工工艺:步骤6.1:将步骤2生成的待检测样本,输入步骤5训练好的模型中,该模型根据模糊推理规则自主计算输出评价值;步骤6.2:对经步骤6.1生成的同一零件的多个工艺方案评价值进行比较,确定最优切削工艺方案。进一步地,步骤2.1中指标数据量化的具体方法为:(1)切削液毒性量化:采用定性分析,根据《污水综合排放标准》(GB8978-1996)、《机械工业含油废水排放规定》(JS7740-95),按10分制评分,如表2所示;表2毒性评分表毒性状况毒性严重毒性一般毒性很小无毒性评分值8631其中,毒性严重指毒性严重影响身体健康,可致生病率死亡率显著增加;毒性一般指毒性影响身体健康,可致病;毒性很小指毒性微小,一般不影响身体健康;(2)切屑回收量化:采用定性分析,根据回收处理方式打分,按10分制评分,如表3所示;表3磨削液回收处理评分表(3)原材料消耗量化:采用定量分析,根据工艺过程中工件废弃物质量W(kg)来确定量化值,量化公式如下:W=RI-RO(1)其中,RI表示进入磨削加工工艺系统的毛坯质量(kg);RO表示经磨削加工后的工件质量(kg);(4)切削液消耗量化:采用定量分析,根据工艺加工过程切削液的使用量Lz(L/min)确定量化值;(5)夹具量化:采用定性分析,根据夹具的种类、使用效率由专家采用十分制打分量化,如表4所示;表4工装使用评分表使用工装情况使用复杂专用夹具使用简单专用夹具使用通用夹具不使用评分值8631(6)刀具消耗量化:采用定量分析,根据工艺过程中加工一个零件消耗的刀具的消耗量,用刀具修整次数nx确定量化值,量化公式如下:其中,tw表示切削加工一个工件的时间(h);Tc表示刀具的使用寿命(h);(7)耗电量量化:采用定量分析,根据工艺过程中磨削单件产品的耗电量Ei(kW·h)确定量化值,量化公式如下:Ei=(Pu+αPc)Ti(3)其中,Pu表示机床空载功率(kW);Pc表示机床磨削功率(kW);α表示功率平衡损耗系数;Ti表示每件加工时间(h);(8)加工费量化:采用定量分析,加工费用指标Czz:根据生产单件产品的制造过程费用总和确定量化值,量化公式如下:Czz=Cyd+Cgz+Ccl(4)其中,Cyd表示单件产品的耗电费(¥);Cgz表示单件产品机床工人工资(¥);Ccl表示单件产品材料费(¥);(9)设备折旧费量化:采用定量分析,根据工艺过程中设备的折旧费用Csb确定量化值,量化公式如下:其中,Cs表示设备价格(¥);ps表示设备折旧率;Td表示工艺加工时间(min);F表示每年工作总时数(h);ηs表示设备利用率;(10)舒适性量化:采用定性分析,根据工艺方案,对工人操作、工作空间舒适程度按10分制评分,如表5所示。表5工人操作舒适度评分表操作舒适度非常合理舒适合理舒适部分需改进不合理不舒适评分值1-23-56-89-10由上述技术方案可知,本发明的有益效果在于:本发明提供的一种切削加工工艺优选系统及方法,可以将同一零件不同切削加工工艺方案进行比较,确定最优工艺路线,在保证减小排放、保护环境的提前下,更好的实现切削加工工艺。评价过程简洁明了,能实现智能评价和事前评价。通过对训练样本集的学习,自主生成模糊推理规则,能够清晰地解析评估指标体系与评价结果映射规律,克服了评估结果易受专家主观倾向影响的技术瓶颈,可有效消除评价指标的模糊性和随机性对评价结果的影响;可以在工艺设计之初进行评价,给出评估结果;该方法由于未进行实际加工生产,可以大量节省时间、人力和成本,避免“先开发后变更的”。附图说明图1为本发明实施例提供的切削加工工艺优选系统工作示意图;图2为本发明实施例提供的切削加工工艺优选方法流程图;图3为本发明实施例提供的PSO聚类算法流程图;图4为本发明实施例提供的ANFIS模型结构示意图;图5为本发明实施例提供的ANFIS算法流程图。图中:1、前件网络第一层;2、前件网络第二层;3、前件网络第三层;4、前件网络第四层;5、后件子网络第一层;6、后件子网络第二层;7、后件子网络第三层。具体实施方式下面结合附图和实施例,对本发明的具体实施方式作进一步详细描述。以下实施例用于说明本发明,但不用来限制本发明的范围。自适应神经模糊推理系统(AdaptiveNeuro-FuzzyInferenceSystem,ANFIS)是人工智能学科的主要研究分支,具有模糊推理易于表达人类知识,以及分布式数据处理和自主学习的优点,可以有效消除评价指标的模糊性和随机性对评价结果的影响,以及避免评价专家的主观性和倾向性产生的偏差,特别对推理规则还不被人们所完全了解或者结构非常复杂的评价系统是十分有效的。但采用人工智能的机器学习方法进行评价首先需要有高质量的训练样本集。而工艺样本数据具有不确定性、多维性以及量纲差异大的特点,使得训练样本的分类成为一项极其复杂的工作。群智能算法中的粒子群优化算法(particleswarmoptimization,PSO)算法概念简单、实现容易,具有很强的适应性和鲁棒性,在分类和模式识别领域获得了很大发展。因此,本发明采用粒子群优化算法对工艺数据进行聚类分析并生成样本训练集,为实现采用ANFIS评价模型提供决策支持;将自适应神经模糊推理系统用于切削加工工艺优选,实现准确合理的评价结果输出。该方法具有事前评价能力,智能推理的特点,可广泛应用到绿色制造领域的评价优选分析中。本实施例提供一种采用基于粒子群分类和自适应神经模糊推理系统的切削加工工艺优选系统,如图1所示,包括:评价指标选择器、数据量化处理器、样本分类器、工艺方案评价器和工艺方案选择器。评价指标选择器:用于在对传统工艺评价指标研究的基础上,充分考虑切削工艺的绿色特性及影响因素,选择具有代表性的10个评价指标,对工艺数据进行采集和整理。评价指标包括:切削液毒性、切屑回收、原材料消耗、切削液消耗、夹具、刀具消耗、耗电量、加工费、设备折旧费和舒适性。数据量化处理器:用于对于收集的切削加工工艺数据进行量化处理,将评价指标分为定性指标和定量指标,分别进行量化,对于无法用数值计量的定性指标,由专家采用十分制打分方法进行量化;对于定量指标则直接采用测量值。使工艺数据以数值形式表示,为避免具有不同物理意义和量纲的输入变量不能平等使用,再对量化好的数值进行归一化处理,即将有量纲的数值经过变换,化为无量纲的数值,生成数值值域为[0,1]的纯小数。样本分类器:用于将数据量化处理器处理好的样本采用粒子群优化算法进行聚类,生成可被自适应神经模糊推理系统学习的训练样本集,用于ANFIS训练学习并建立评价推理规则,为实现对待检测工艺样本的评价优选提供支持。工艺方案评价器包括模型建立模块、模型训练模块和方案评价模块;模型建立模块用于建立ANFIS模型;模型训练模块用于采用训练样本集训练建立的ANFIS模型,使该模型收敛,自动生成模糊推理规则;方案评价模块用于将检测工艺数据首先通过数据量化处理器生成检测样本,再输入训练过的ANFIS,ANFIS将根据学习获得的推理规则,智能决策计算输出工艺评价结果。工艺方案选择器:用于对制造同一机械零件的多个检测工艺方案的计算结果进行比较,获得最优工艺方案。本实施例以EA111发动机凸轮轴工件作为研究对象,以凸轮轮廓磨削加工为例,分别采用MBA1632磨床(工艺方案1)和Quickpoint5002/N磨床(工艺方案2)设计磨削加工工艺,并对上述两种加工工艺进行优选,方法流程如图2所示,包括以下步骤:步骤1:通过对切削工艺绿色特性及影响因素的充分考虑,选择具有一定代表性的10个评价指标,包括:切削液毒性、切屑回收、原材料消耗、切削液消耗、夹具、刀具消耗、耗电量、加工费、设备折旧费、舒适性。步骤2:采用定性与定量相结合的量化方法对步骤1中的切削加工工艺的评价指标数据进行量化处理,并进行归一化处理,生成训练工艺评价指标数据样本,具体方法为:步骤2.1:量化指标数据;定量量化方法是依据加工统计数据或仿真计算数据,赋值给定量指标数值;定性量化方法则是依据有关机械加工的法规、标准,由专家采用十分制打分方法,赋值给无法用数值计量的定性指标。步骤1中所述的10个评价指标的量化方法具体为:(1)切削液毒性量化:采用定性分析,根据《污水综合排放标准》(GB8978-1996)、《机械工业含油废水排放规定》(JS7740-95),按10分制评分,如表2所示;表2毒性评分表毒性状况毒性严重毒性一般毒性很小无毒性评分值8631其中,毒性严重指毒性严重影响身体健康,可致生病率死亡率显著增加;毒性一般指毒性影响身体健康,可致病;毒性很小指毒性微小,一般不影响身体健康;(2)切屑回收量化:采用定性分析,根据回收处理方式打分,按10分制评分,如表3所示;表3磨削液回收处理评分表回收处理状况回收集中处理回收随意处理回收不处理不回收评分值1368(3)原材料消耗量化:采用定量分析,根据工艺过程中工件废弃物质量W(kg)来确定量化值,量化公式如下:W=RI-RO(1)其中,RI表示进入磨削加工工艺系统的毛坯质量(kg);RO表示经磨削加工后的工件质量(kg);(4)切削液消耗量化:采用定量分析,根据工艺加工过程切削液的使用量Lz(L/min)确定量化值;(5)夹具量化:采用定性分析,根据夹具的种类、使用效率由专家采用十分制打分量化,如表4所示;表4工装使用评分表使用工装情况使用复杂专用夹具使用简单专用夹具使用通用夹具不使用评分值8631(6)刀具消耗量化:采用定量分析,根据工艺过程中加工一个零件消耗的刀具的消耗量,用刀具修整次数nx确定量化值,量化公式如下:其中,tw表示切削加工一个工件的时间(h);Tc表示刀具的使用寿命(h);(7)耗电量量化:采用定量分析,根据工艺过程中磨削单件产品的耗电量Ei(kW·h)确定量化值,量化公式如下:Ei=(Pu+αPc)Ti(3)其中,Pu表示机床空载功率(kW);Pc表示机床磨削功率(kW);α表示功率平衡损耗系数;Ti表示每件加工时间(h);(8)加工费量化:采用定量分析,加工费用指标Czz:根据生产单件产品的制造过程费用总和确定量化值,量化公式如下:Czz=Cyd+Cgz+Ccl(4)其中,Cyd表示单件产品的耗电费(¥);Cgz表示单件产品机床工人工资(¥);Ccl表示单件产品材料费(¥);(9)设备折旧费量化:采用定量分析,根据工艺过程中设备的折旧费用Csb确定量化值,量化公式如下:其中,Cs表示设备价格(¥);ps表示设备折旧率(一般取值为20%-25%);Td表示工艺加工时间(min);F表示每年工作总时数(h);ηs表示设备利用率(一般取值为0.8-0.95);(10)舒适性量化:采用定性分析,根据工艺方案,对工人操作、工作空间舒适程度按10分制评分,如表5所示。表5工人操作舒适度评分表操作舒适度非常合理舒适合理舒适部分需改进不合理不舒适评分值1-23-56-89-10步骤2.2:对上述量化的指标数据进行归一化处理;采用小数定标标准化方法(Decimalscaling)对量化好的数值进行归一化处理,按式(6)将指标A的原始值w归一化为w',生成数值值域为[0,1]的纯小数,保证各指标数据对工艺方案评价的趋同化作用;w'=w/(10*a)(6)其中,a表示小数点移动位数,等于指标A的取值中的最大绝对值整位数。步骤3:采用粒子群优化算法(PSO算法)对归一化的工艺评价指标数据样本进行聚类分析,建立训练样本集,用于自适应神经模糊推理系统学习和建立评价推理规则,粒子群优化聚类算法流程如图3所示,具体方法为:步骤3.1:随机选择簇的中心(即均值)并赋值给各个粒子,随机产生粒子的速度,并设定最大速度Vmax;步骤3.2:对每个粒子按照最小距离原则对数据进行划分,按照式(7)所示的目标函数Je计算各个粒子的适应值,更新个体极值;其中,Cr是表示第r个聚簇;Nc为聚簇的个数;zp表示样本的数据向量;mr表示簇Cr中样本的中心,nr表示簇Cr中样本的个数;其中,Nb为数据向量的维数;zpk表示第k维样本的数据向量;mrk表示簇Cr中第k维样本的中心;步骤3.3:根据各个粒子的个体极值,找出全局极值和全局极值位置;步骤3.4:按粒子群优化算法的速度公式更新粒子的速度,并把它限制在最大速度Vmax内;步骤3.5:按粒子群优化算法的位置公式更新粒子的位置;步骤3.6:计算种群中的个体适应值,若满足终止条件,则算法结束,输出最优粒子的位置即最优的Nc个聚类中心,否则,返回步骤3.4继续进行速度更新。本实施例中,实例样本数据采自某汽车制造企业凸轮轴加工工艺。首先按照步骤2.1进行量化,再按公式(6)进行归一化处理,聚类分析后将样本分为三类:优、良、差,并分别给出相应的期望值,最终的训练样本如表6所示。表6训练样本集在表5中,y为期望值,根据聚类分组个数将评价结果分级,期望值y确定方法如下:评价结果为“优”时,系统输出期望值设置为0.3;评价结果为“良”时,系统输出期望值设置为0.5;评价结果为“差”时,系统输出期望值设置为0.8。步骤4:建立自适应神经模糊推理系统模型;采用Takagi-Sugeno型模糊推理系统作为ANFIS的核心结构,构建由前件网络和后件网络两部分组成的多输入、单输出的评价模型,模型结构如图4所示。前件网络用于产生每条模糊规则对输入样本的隶属度,后件网络用于生成每条模糊规则的加权和。采用VisalC++软件开发平台及SQL2005数据库编写软件实现模型。前件网络包括四层结构:第一层1为前件网络输入层,其每个节点直接与输入向量的各分量连接,节点数为N1=p,p为输入样本的维数,用于将输入样本x=[x1,x2,…,xp]T传送到下一层;第二层2表示经计算得到的各输入分量属于模糊集合的隶属度,节点数N2=C×p,其中C为模糊规则总数;第三层3每个节点代表一条模糊规则,用于确定每条规则的隶属度ui,节点数N3=CP;第四层4为前件网络输出层,节点数与第三层3相同,输出为(i=1,…,C),表示归一化计算后前件网络的输出值,即输入样本对每条模糊规则的隶属度,如式(8)所示;后件网络包括C个结构相同的子网络,每个子网络产生一个输出量,即每条模糊规则的权值;C个子网络均包括三层结构:第一层5为子网络输入层,节点数为p+1个,其中第0个结点的输入值为1,用于提供模糊规则后件的常数项;第二层6节点数为C个,每个节点代表一条模糊规则,用于计算每个规则的后件;第三层7为子网络输出层,输出为yi(i=1,…,C),表示模糊规则后件的加权和,加权系数为前件网络的输出;后件网络的最终输出为Y,即模型的输出如式(9)所示:步骤5:设定初始化参数,采用步骤3生成的训练样本集训练步骤4建立的模型,如图5所示,经81次迭代计算,满足算法终止条件,网络收敛停止迭代计算,对待检测样本进行智能评价,具体方法为:步骤5.1:采用模糊C-均值(FCM)算法对前件网络进行训练,通过迭代计算优化第二层节点的隶属度中心,输出结果为输入样本对每条模糊规则的隶属度,包括以下步骤:步骤5.1.1:设置加权指数λ,λ∈[1,∞),模糊规则数C,输入样本个数n,输入样本维数p,终止误差ε,最大迭代次数LOOP1;迭代计数变量赋初值IT1=0;步骤5.1.2:用值域为(0,1)的随机数初始化隶属度矩阵U(IT1),隶属度矩阵uij为隶属度矩阵内元素,并满足i为正整数,且i=1,2,…,C;j为正整数,且j=1,2,…,n;步骤5.1.3:根据计算第i条模糊规则聚类中心向量zi=[z1i,z2i,L,zpi],公式为:其中,xj表示第j个输入样本向量;步骤5.1.4:更新隶属度矩阵U(IT1+1),如式(11)所示;其中,dij表示第j个样本向量到聚类中心向量的欧式距离,dkj表示第j个样本向量到聚类中心向量的欧式距离;步骤5.1.5:若满足或IT1>LOOP1,则终止迭代计算,否则更新迭代计数变量,IT1=IT1+1,返回步骤5.1.3,‖·‖为欧式距离算式;步骤5.2:对后件网络进行训练,后件网络包括C个结构相同的子网络,每个子网络均采用最小均方(LMS)算法调整后件网络的连接权值,包括以下步骤:步骤5.2.1:设置学习率β,终止误差ε1,最大迭代次数LOOP2,迭代计数变量赋初值IT2=0;步骤5.2.2:用值域为(0,1)的随机数初始化权值矩阵bi=[b0i,b1i,L,bpi],i=1,2,…,C;步骤5.2.3:计算后件子网络输出值yi,表示第IT2次迭代产生的第j个输入样本向量对应的后件子网络输出,如式(12)所示;其中,表示归一化计算的前件网络输出值;步骤5.2.4:更新权值矩阵如式(13)所示;其中,表示后件子网络期望输出值;步骤5.2.5:若满足或IT2>LOOP2,则终止迭代计算;否则更新迭代计数变量,IT2=IT2+1,返回步骤5.2.3;此时,训练好的模型已生成模糊推理规则,保存训练好的系统参数,接下来可对待检测样本进行评价。步骤6:使用训练后的模型对生成的待检测工艺评价指标数据样本进行评价,并根据评价结果输出最优切削加工工艺:对磨削凸轮轴加工的两个工艺方案进行优选,按照步骤2量化并归一化生成待检测样本:工艺方案1:X1=[0.40,0.30,0.48,0.72,0.30,0.80,0.56,0.38,0.12,0.20];工艺方案2:X2=[0.60,0.20,0.36,0.60,0.50,0.12,0.50,0.42,0.16,0.20]。步骤6.1:将步骤2生成的待检测样本,输入步骤5训练好的模型中,该模型根据模糊推理规则自主计算输出评价值。本实施例中,分别将检测工艺样本输入步骤5训练好的评价模型中,经计算得到工艺方案1样本的评价数值为0.61,工艺方案2参评样本的评价数值为0.34。步骤6.2:对经步骤6.1生成的同一零件的多个工艺方案评价值进行比较,确定最优切削工艺方案。本实施例中,依据步骤3对评价结果分级的结果,即期望值y按极小型指标确定数值,所以评价结果值越小,表明工艺绿色度越好。对经步骤6.1计算得到的两个工艺方案评价值进行比较,由于工艺方案1样本的评价数值为0.61,大于工艺方案2参评样本的评价数值0.34,所以最优切削工艺为工艺方案2。本实施例提供的优选系统经验证可对切削加工工艺方案进行有效评价并能排序输出最优工艺方案。具有评价过程简洁明了,智能评价和事前评价的特点。1)智能评价由于绿色工艺评价是一个具有高度非线性和复杂不确定性的系统,传统的评价方法难以构建评价指标与评价结果间的函数关系,评价过程通常需要专家参与评判获得评价结果,受评价专家的主观性和倾向性影响较大,且评价规则难以理解。研究的评价优选方法通过对训练样本集的学习,自主生成模糊推理规则,能够清晰地解析评估指标体系与评价结果映射规律,克服了评估结果易受专家主观倾向影响的技术瓶颈,可有效消除评价指标的模糊性和随机性对评价结果的影响。2)事前评价发明的评价优选方法是一种事前评价方法,可以在工艺设计之初进行评价,给出评估结果。与目前普遍采用的事后评价方法——LCA方法相比,可有效克服只能对已开发设计好的工艺或者生产出的产品进行事后辅助验证,不能在设计初始阶段提供评估的局限。该方法由于未进行实际加工生产,可以大量节省时间、人力和成本,避免了以往工艺设计中“先开发后变更的”弊端。用户通过该方法,可以同一零件不同切削加工工艺方案进行比较,确定最优工艺路线,使制造业企业在保证减小排放、保护环境的提前下,更好的实现切削加工工艺。最后应说明的是:以上实施例仅用以说明本发明的技术方案,而非对其限制;尽管参照前述实施例对本发明进行了详细的说明,本领域的普通技术人员应当理解:其依然可以对前述实施例所记载的技术方案进行修改,或者对其中部分或者全部技术特征进行等同替换;而这些修改或者替换,并不使相应技术方案的本质脱离本发明权利要求所限定的范围。当前第1页1 2 3