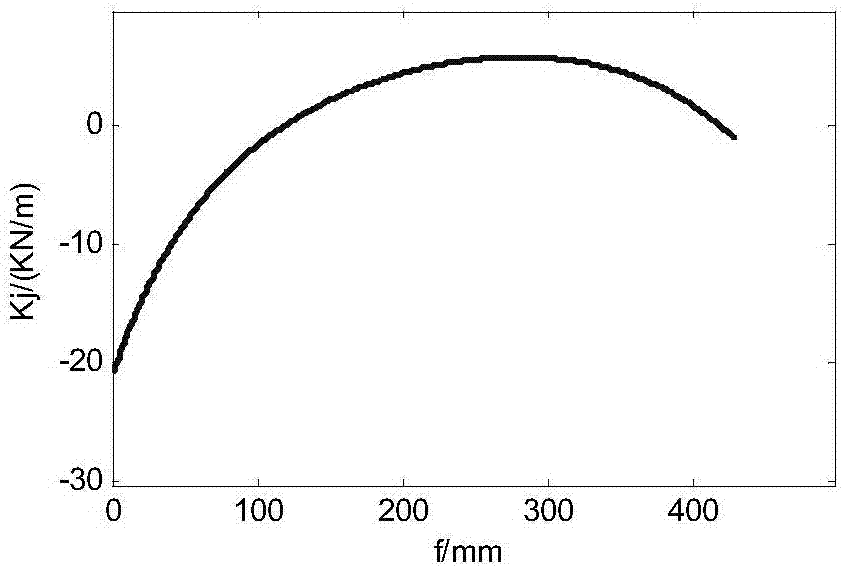
本发明涉及一种车辆悬挂系统的优化特性评价方法,尤其是一种车辆电控空气悬挂优化特性评价方法,适用于摆动缸与固定缸式油气悬挂的结构优化设计。
背景技术:
相关研究与试验表明,安装机电悬挂系统(ecass)的轮式车辆或履带车辆,其越野速度可提高2~3倍,使部队作战节奏明显加快;平台的稳定性、越野行驶时的操控性能显著提高,从而使武器发射地点更为灵活,并能显著提高武器系统的射击精度;安装ecass系统能够显著吸收冲击和震动能量,大幅减小车辆的相对运动和振动,从而显著提高可靠性,提高乘员的工作效率;车辆的装载能力、燃油经济性等均有显著提高。鉴于ecass系统的优越性能,国内也展开了相关研究。但前期研究表明,按照原有的电控空气悬挂结构参数进行分析,发现悬挂刚度曲线不理想(如图1所示),这将导致车辆姿态不一,调节困难,并易导致悬挂击穿与脱带现象,难以满足相关车辆的行动系统设计要求,因此必须对悬挂结构及参数进行优化。显然,优化设计的前提是有一个明确的优化目标模型与相应的评价方法或评价模型。对于车辆悬挂系统的优化,国内外研究较多,但多数优化表现在对悬挂的刚度与阻尼系数的优化,优化目标为行驶平顺性;而提高操稳性对悬挂结构参数优化多限于轮式车辆。对于车辆平顺性的评价方法,国内外学者也进行了大量研究,提出了很多的平顺性评价方法与评价标准,最为典型的是iso标准、美国陆军试验规程、中国对应的野外振动试验规程等。但是绝大多数评价方法主要是针对轮式车辆,且均是在试验数据的基础上进行的。到目前为止,在设计阶段还没有一个公认、统一、系统的与履带车辆行驶平顺性相关的悬挂设计标准或规则,国内外相关的评价指标体系与评价方法仍处于空白。技术实现要素:针对电控空气悬挂结构设计过程中遇到的问题,本发明在分析机电悬挂特性指标、影响因素、约束条件的基础上,建立了机电悬挂的结构及其参数优化的目标模型,并对其结构及其参数进行了优化设计研究,提出了系统的电控空气悬挂结构优化规则与悬挂特性评价方法。为实现上述目的,本发明采用的技术方案是:车辆电控空气悬挂优化特性评价方法,首先设置优化参数的搜索范围,然后依次分析弹簧与平衡肘大头干涉约束、弹簧上行程约束、弹簧下形成约束、弹簧内部压强约束,然后进行约束检查和加权求和后,输出最大结果。具体步骤为:(1)设置机电悬挂的优化参数范围(2)确定机电悬挂特性及评价指标具体的评价指标为:(2.1)总缓冲势量及总比位能(2.2)垂直振动周期(2.3)纵向角振动周期(2.4)空气弹簧作用于平衡肘的传动角(3)确定单个悬挂特性的结构影响因素综合分析发现,下述参数对机电悬挂特性的影响较大:(3.1)平衡肘长度(3.2)弹簧上、下支点位置参数(3.3)空气弹簧气缸内径与活塞杆中空内腔直径及深度(4)分析约束条件在优化过程中发现,如果改变上支点位置,会使弹簧行程减小,并会导致内部干涉;其次,平衡肘受力效果、悬挂特性也不会达到最优。因此在对整个悬挂结构综合优化之前,有必要分析下列约束条件:(4.1)弹簧与平衡肘大头不干涉约束(4.2)弹簧动、静行程约束(4.3)弹簧内部压力约束(4.4)悬挂刚度(5)对悬挂结构进行综合优化具体步骤是:(5.1)建立电控空气悬挂结构优化目标模型(5.2)对电控空气悬挂结构进行优化分析。本发明针对悬挂结构及参数设计不合理导致的刚度曲线不理想,车辆姿态不一,调节困难等问题。在分析机电悬挂特性指标、影响因素、约束条件的基础上,提出了多目标的电控空气悬挂结构优化目标模型,并对其结构及参数进行了优化设计,系统地提出了满足设计要求的机电悬挂特性优化设计规则与评价方法。本发明体现了前期悬挂设计与后期实车行驶的多方面要求;结构优化规则与评价方法科学、可行,适用于摆动缸与固定缸式油气悬挂的结构优化设计与评价。附图说明图1悬挂等效刚度跟悬挂行程的关系曲线图2是机电悬挂机构简图。图3是压缩气体体积(v)跟悬挂行程(f)关系曲线。图4是平衡肘受力(fp)跟悬挂行程(f)关系曲线图。图5是悬挂等效刚度(kj)跟悬挂行程(f)关系曲线图。图6是悬挂等效刚度(kj)跟悬挂行程(f)关系曲线图。图7是悬挂下限位状态下活塞与气缸轴向尺寸示意图。图8是电控空气悬挂结构优化流程图。图9是弹簧内部压力跟悬挂行程关系曲线图。图10是平衡肘受力跟悬挂行程关系曲线图。图11是弹簧支撑力跟悬挂行程关系曲线图。图12是弹簧内部空气体积跟悬挂行程关系曲线图。图13是平衡肘传动角跟悬挂行程关系曲线图。图14是悬挂等效刚度跟悬挂行程关系曲线图。图15是弹簧内部压力p与悬挂行程f关系曲线图。图16是悬挂下限位状态下悬挂结构示意图。图中:1-车体;2-空气弹簧;3-底甲板下平面;4-负重轮;5-地面水平线;6-平衡肘;7-履带;8-上安装轴;9-下安装轴。具体实施方式下面将结合本发明实施例中的附图,对本发明实施例中的技术方案进行清晰、完整地描述,显然,所描述的实施例仅仅是本发明一部分实施例,而不是全部的实施例。基于本发明中的实施例,本领域普通技术人员在没有做出创造性劳动前提下所获得的所有其他实施例,都属于本发明保护的范围。车辆电控空气悬挂优化特性评价方法,首先设置优化参数的搜索范围,然后依次进行弹簧与平衡肘大头干涉约束、弹簧上行程约束、弹簧下形成约束、弹簧内部压强约束,然后进行约束检查和加权求和后,输出最大结果。具体步骤为:(1)设置机电悬挂的优化参数范围机电悬挂机构简图如图2所示,图中机电悬挂相关尺寸几何意义和参数见表1,其中活塞杆中空内腔直径d1、长度h、活塞杆外径d2、气缸内径d3、气缸外径d4等需要优化的机电悬挂相关参数尺寸范围见表2。表1表2(2)确定机电悬挂特性及评价指标单个悬挂特性要求是要在保证满足总体结构参数与设计要求的情况下,使悬挂刚度曲线形状合理,悬挂的缓冲能力、减振设计要求与平衡肘受力效果均达到近似理想状态,具体的评价指标为:(2.1)总缓冲势量及总比位能总缓冲势量e可由(1)式表达:式中:pi为空气弹簧初始充气压力;vi为空气弹簧初始充气时的气体体积;v为任意位置时空气弹簧内的压缩气体体积;av为空气弹簧活塞杆有效面积;s,sd,ss分别为空气弹簧活塞行程、静行程、动行程;τ为压缩气体的多变指数,τ=1.25。总比位能概念是针对整车的缓冲能力提出的,一般认为,其值越大,悬挂缓冲能力越强,悬挂发生悬挂击穿的概率越小。对于装备空气弹簧的单个悬挂系统,总比位能λt为动比位能λd与静比位能λs之和,λd、λs可分别通过(2)式、(3)式计算如下:式中:gk为分配于第k个悬挂簧上重量;fas为空气弹簧弹性力。(2.2)垂直振动周期相关书籍与实车试验实践均表明,坦克装甲车辆的振动频率越低,振幅越小,振动的加速度和速度越小,则坦克装甲车辆行驶的平稳性就越好。为此要求悬挂平均刚度要适当小一些(即悬挂稍软一些),z向垂直线振动周期tz和绕横轴y的纵向角振动周期ty要适当大一些。垂直振动周期可由(4)式估计:式中:m为整车簧上质量;kk为第k个悬挂的垂直刚度;n为轮对数;在行动总体参数没有确定的情况下,对于单个悬挂的设计,垂直振动周期可采用(5)式来估计:式中:mk为需要优化计算的第k个悬挂所承担的负荷质量。由负重轮作用于平衡肘的支撑力fr,b、空气弹簧弹性支撑力fas、平衡肘与车体之间的作用力fb,b关系,可推导电控空气悬挂单个悬挂装置的刚度k为[6]式中:pi,vi分别为初始安装状态下空气弹簧内的压力与容积;ps,vs分别为静平衡状态下空气弹簧内的压力与容积;f为悬挂行程;α,β,γ意义见表1。(2.3)纵向角振动周期的纵向角振动周期ty可由(11)式估计:式中:其中ζ为质量分配系数,lv,wv分别为车体长度与车体宽度[17];lk为第k对轮轴中心至车体质心的水平距离,质心前为正,质心后为负。对于特定的装甲车辆,在车体质量与尺寸确定的情况下,轮系布置变化不大,因此纵向角振动周期ty变化不大,可优化的空间较小,在单个悬挂设计阶段可不予考虑。(2.4)空气弹簧作用于平衡肘的传动角除悬挂缓冲性能外,平衡肘受力效果对平衡肘自身及轴承寿命有较大的影响。空气弹簧作用于平衡肘的传动角δ[6]越大,平衡肘受力效果越好。为考察弹簧弹性力作用效果与平衡肘的受力效果,需要考察空气弹簧弹性力fas作用于平衡肘的传动角。由图2所示几何关系可知fas作用于平衡肘的传动角为δ=β-ε,(12)式中:ε为ob力作用线与水平面的夹角,ε=αtan(yb/xb).(13)上式中,xb,yb为b点坐标。由于平衡肘工作在静平衡状态的工作概率最高,且在动行程末端其受力最恶劣,在这两种状态下静传动角δs与动传动角δd均要考虑。(3)确定单个悬挂特性的结构影响因素综合分析发现,下述参数对机电悬挂特性的影响较大:(3.1)平衡肘长度平衡肘长度lb影响到悬挂的动、静行程、悬挂空气弹簧的内部压强及悬挂刚度特性。增加平衡肘长度有利于避免悬挂零件之间的干涉,并改变空气弹簧的工作传动角δ.如图3所示,当xc=210mm,yc=330mm,da_s,i=56mm,,l=85mm,r=50mm,h=0mm,lb=400mm时,在动行程的末端f=430mm附近出现压缩空气体积v<0的情况,这种情况表明活塞已抵达缸筒底部且发生了严重的干涉。如图4和图5所示,当xc=210mm,yc=330mm,da_s,i=56mm,l=85mm,r=50mm,h=0mm,lb=420mm时,在动行程的末端,虽然没有发生干涉,但是由于悬挂在较小动行程内的空气弹簧压缩量较大,导致悬挂支撑力(实际为负重轮作用于平衡肘的力fr,b)及悬挂等效刚度ke发生较大的变化。显然,这些情况对悬挂工作是不允许的。从图3~图5所示的情况来看,平衡肘对悬挂干涉及刚度特性影响确实较大。(3.2)弹簧上、下支点位置参数如图1所示,增加xc,yc或减小l,r,可减小空气弹簧倾斜角度,有利于改善悬挂的受力效果。由于上支点离平衡肘在车体上的安装点竖直距离yc受整个履带环高度限制,不能增加太多。(3.3)空气弹簧气缸内径与活塞杆中空内腔直径及深度如图6所示,当空气弹簧气缸内径da_s,i=56mm时,其他参数在表2中的范围内进行优化时,都会在动行程末端压力超过密封压力限值(40pma)的情况(见图15)。因此,为避免弹簧在悬挂动行程末端内部压力太大,根本的解决方法就是增大弹簧的体积(内径或深度)。由于增大直径受车体侧向布置空间限制,空气弹簧气缸内径(da_s,i)不能增加太多。为此,ecass采取了中空活塞杆的增加压缩空气体积的方案,其相应的参数有活塞杆中空内腔直径及长度(dp_r,i,h)。(4)分析约束条件在优化过程中发现,如果改变上支点的位置,会使弹簧行程减小,并会导致内部干涉;其次,平衡肘受力效果、悬挂特性也不会达到最优。因此在对整个悬挂结构综合优化之前,有必要分析下列约束条件。(4.1)弹簧与平衡肘大头不干涉约束如图16所示,在下限位或初始安装位置,空气弹簧缸筒外表面与电磁致动器相切,过电磁致动器中心作空气弹簧中心线的垂线,其垂足为q,则与垂直线的夹角θ为θ=αtan(xc/yc),(14)与垂直线的夹角为式中:da,o为(电磁)致动器的外径。则弹簧与平衡肘大头不干涉约束为ψ-θ>0.(16)(4.2)弹簧动、静行程约束如图2所示的空气弹簧内部结构所示,在悬挂处于最大动行程(对应上限位)状态下,活塞端面几乎抵至气缸底部,设上安装轴距离气缸底部距离为lb,u_a,气缸口端部密封宽度为we,s,上安装轴距离气缸口距离为lu_a,e,活塞杆有效长度为lp_r,气缸活塞宽度为wp,此时空气弹簧长度(上、下安装轴之间距离)为la_s。为避免活塞与气缸底部发生硬性碰撞(活塞端面至气缸底部距离不小于δs=10mm),其对应的悬挂行程约束条件为la_s,u+lb,u_a-lp_r≥δs.(17)上式中,la_s,u为空气弹簧在上限位置时,上下安装轴之间的距离。在平衡肘处于下限位状态下,活塞相对气缸的位置如图8所示,为使活塞保持一定的导向长度,活塞右端面与气缸口的距离必须大于活塞的长度,设此长度为lu_a,e,显然,为了避免活塞拉出气缸并保持一定的导向长度,其对应的悬挂行程约束条件为(lp_r-wp)-(la_s,d-lu_a,e+we,s)≥δs.(18)上式中,la_s,d为空气弹簧在下限位置时,上下安装轴之间的距离。(4.3)弹簧内部压力约束当悬挂达到最大动行程时,平衡肘处于上限位状态下,弹簧内部对应的压力pd达到最大,由于国内液压动密封当前能达到40mpa,因此弹簧内部压力约束为pd≤40mpa.(19)(4.4)悬挂刚度结构如果设计得不好,会出现图1中刚度特性曲线所示的下凹现象,导致姿态不一,为此必须对刚度曲线形状加以限制。避免这种现象出现的约束条件为对于如图1所示的摆动缸式空气弹簧悬挂刚度特性曲线,其只能有一个上凹处。此时,式(20)所示的条件可简化为mink>0.(21)综合上述各约束条件,总约束条件为(5)对悬挂结构进行综合优化具体步骤是:(5.1)建立电控空气悬挂结构优化目标模型由上分析的悬挂特性评价指标与约束条件,可建立电控空气悬挂结构优化目标函数为式中:ks,kd,kz,kδ分别为与各项评价指标对应的评价权数;[λs],[λd],[tz]分别表示相应指标对应的阈值。根据表1所示的行动总体设计参数,可取[λs]=fs=130mm;[λd]=fd=300mm;根据文献[17],其垂直振动周期与角振动周期分别要求不低1.0s与1.6s,可取[tz]=1.0s;[ty]=1.6s,对于单个悬挂的评价,可忽略ty对应的评价项。因此,(23)式与(22)式一起构成了电控空气悬挂结构优化的目标数学模型。采用反复试凑法进行验算,发现当ks=0.5,kd=3,kz=1,kδ=1时,其对应的悬挂特性曲线基本达到上述要求。(5.2)对电控空气悬挂结构优化分析按照上述目标模型、优化方法与图8所示的步骤,进行结构优化,优化结果见表3及图9-图14。表3优化后电控空气悬挂结构参数表参数数值参数数值参数数值参数数值da_s,i/mm630la_s,u/mm773.3vi/l1.20pi/mpa10.15xc/mm210la_s,s/mm662.0vs/l0.91ps/mpa13.68yc/mm330la_s,d/mm424.1vd/l0.39pd/mpa39.99lb/mm490et/kj14739λt/mm607.1δi/(°)29.34l/mm85es/kj2861.6λs/mm117.9δs/(°)35.98r/mm50ed/kj11877λd/mm489.2δd/(°)42.67h/mm0lu_a,e/mm374.1lp_r/mm476.1tz/s1.10从表3及图9-图14中可见,经过结构优化后的电控空气悬挂避免了结构干涉,且总比位能λt=607mm与动比位能λd=489mm均超过设计要求,悬挂具有较强的缓冲能力,在承担对应的静态质量载荷下,其静态振动周期tz=1.1s,刚度特性曲线非常理想。无论缓冲可靠性还是减振性能均较好,满足了前期悬挂设计与后期实车行驶的多方面要求。结论:(1)优化后的结构参数能满足多重约束与多目标的行动系统设计要求,并使悬挂缓冲性能与平衡肘受力效果达到比较理想的状态。(2)电控空气悬挂结构优化目标模型合理、科学,体现了前期悬挂设计与后期实车行驶的多方面要求,解决了工程设计中的结构设计问题。(3)基于多重约束、最大缓冲势能、振动周期与平衡肘传动效果的加权值最大化的多目标结构优化设计方法是有效、科学的,能指导基于ecass悬挂的结构设计与摆动缸式油气悬挂的设计。(4)由于电控空气悬挂结构与一般履带车辆悬挂结构类似,本文所述的悬挂结构优化目标模型适用带平衡肘的履带式装甲车辆悬挂结构的结构优化,具有较强的通用性。当前第1页12