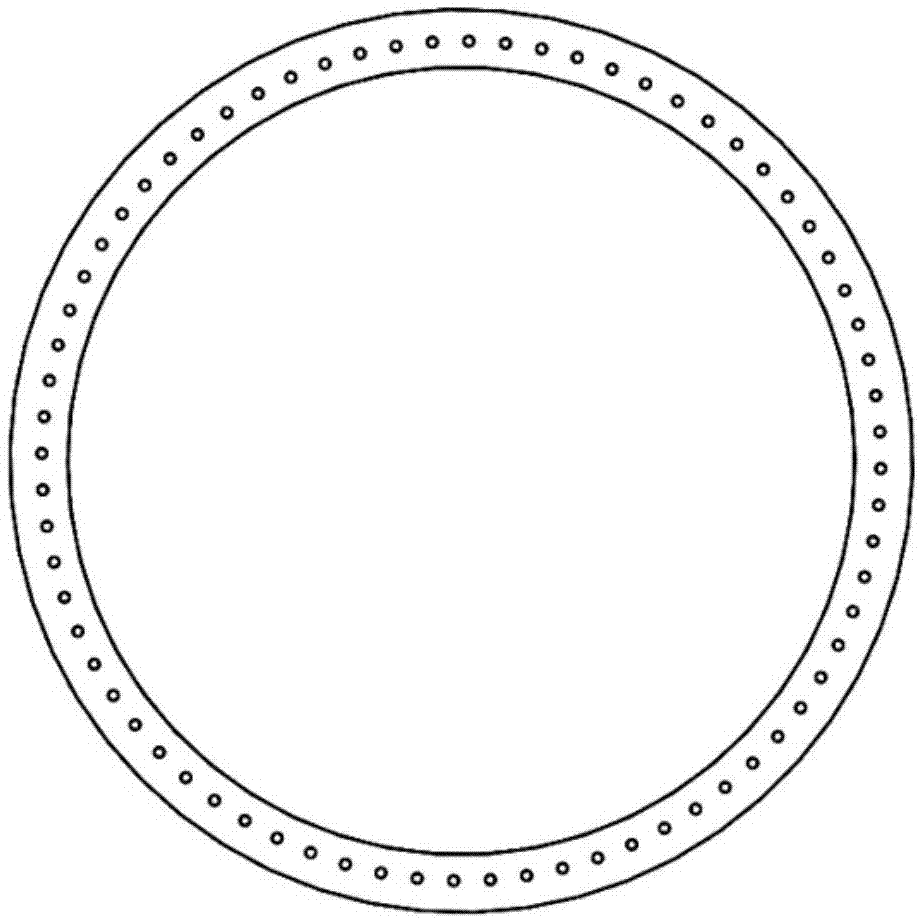
本发明涉及一种全断面硬岩掘进机减振优化结构设计方法,属于全断面硬岩掘进机结构设计优化
技术领域:
。
背景技术:
:随着当今社会经济水平的飞速发展,交通拥堵问题日益加重,地下公路、地下隧道等地下空间的开发成为一种趋势,全断面硬岩掘进机已成为国际上快速开挖隧道的主流,是国内外最先进的隧道施工方法之一。全断面硬岩掘进机主要由刀盘系统、驱动系统、支撑系统、推进系统、润滑系统、液压系统、电器控制系统、定位导向系统、衬砌支护系统等多个系统组成。其中刀盘系统和驱动系统在掘进机中尺寸最大,质量最重,工作环境十分恶劣,是最为关键的核心部件。通过对国内实际隧道工程的调研发现,由于地质环境、施工参数的复杂性及多变性,全断面隧道掘进机的振动问题较为突出,常常诱发刀具异常磨损,刀盘面板、焊缝开裂及主轴承密封失效等各种难以修复的损伤。强振动问题导致的关键部件失效,不仅降低了施工效率,延误了工期,甚至致使整条隧道报废,后果十分严重。因此降低全断面硬岩掘进机主驱动系统整机振动或提高其抗振能力势在必行。当前在刀盘和刀盘驱动系统之间起连接作用的法兰和回转支承是全断面硬岩掘进机的关键部件,其特点是作为传递横向振动的部件,所受振动强度剧烈。强烈的振动将导致出现诸多工程问题,对全断面硬岩掘进机施工的成本、速度和效率有着重要的影响。高分子夹层阻尼减振钢板具有优越的隔吸声及阻尼减振性能,它利用了夹层材料的粘弹性特征来实现对噪声及振动的阻尼作用。在近十几年,高分子夹层阻尼减振钢板研究发展迅速,工程应用日渐广泛,但到目前为止,还没有看到将高分子夹层阻尼减振钢板应用于全断面硬岩掘进机的公开文献,因此为了减小振动对全断面硬岩掘进机主机的影响,提高隧道施工效率,节约经济成本,提出在强度不变的前提下,在法兰与转接环之间,转接环与回转支承之间安装高分子夹层阻尼减振钢板提升了整机的减振功能。技术实现要素:本发明是针对全断面硬岩掘进机主机振动强度大的问题,在保证全断面硬岩掘进机的掘进性能和强度要求下,发明了一种减少全断面硬岩掘进机主机振动强度的优化设计结构,该结构可以减少全断面硬岩掘进机主机振动强度,降低全断面硬岩掘进机主机部件的损害程度,从而降低全断面硬岩掘进机部件更换频率,提高隧道施工效率,极大加快掘进工程的施工进度。本发明的技术方案:一种全断面硬岩掘进机减振优化结构设计方法,步骤如下:步骤1、高分子夹层阻尼减振钢板夹层材料的选择材料的阻尼特性一般用损耗因子β表示,损耗因子越大,材料的减振效果越好。根据调研结果显示:在一定条件下,高分子材料的损耗因子超出钢、铁2~4数量级,由钢板和高分子聚合物复合而成的减振钢板具有良好的阻尼减振特性。综合考虑了材料的适用温度、损耗因子、经济性,结合全断面硬岩掘进机的工况,决定选用人造橡胶作为减振钢板的夹层材料。步骤2、确定高分子夹层阻尼减振钢板的结构及尺寸出于全断面岩石掘进机整体结构合理性和螺栓受力均匀性来考虑,高分子夹层阻尼减振钢板为圆环形。减振钢板与法兰是通过螺栓进行连接,所以减振钢板的尺寸确定方程如下:r=rfr=rfα=αf式中,r为减振钢板内径;r为减振钢板外径;α为减振钢板中螺纹孔间隔角;rf为法兰内径;rf为法兰外径;αf为法兰中螺纹孔间隔角。高分子夹层阻尼减振钢板分三层,上下层为钢板,内层为高分子夹层。通过构建全断面硬岩掘进机刀盘动力学模型,对模型结果进行分析对比,确定减振钢板的高分子夹层厚度t1与钢板厚度尺寸t2;步骤3、建立全断面硬岩掘进机刀盘动力学模型考虑到全断面岩石掘进机零部件之间的动力学耦合,本专利针对刀盘驱动系统多点啮合、多结合面等复杂结构特征,基于有限元思想,提出一种适用于复杂传动系统动力学研究的分层次建模方法。根据部件间的装配关系将全断面硬岩掘进机主机系统进行拆分,分成刀盘刀具系统、刀盘驱动系统和其他部分。刀盘刀具系统作为切削岩石的执行部件,由刀盘分体和刀盘中心块组成;刀盘驱动系统作为全断面岩石掘进机的核心功能件,是一个包含多级传动,具有多结合面、多点结合等结构特征的复杂传动系统,由刀盘、法兰、主轴承、齿圈、小齿轮、主减速器与变频电机组成;针对结构复杂的刀盘驱动系统整机进行逐级拆分,分为刀盘—主轴承—齿圈子系统、驱动轴子系统以及支撑架—主梁子系统三个子系统;运用集中质量法,考虑多结合面的接触刚度、阻尼以及螺栓预紧力等,建立全断面硬岩掘进机主驱动系统多自由度耦合振动系统。步骤4、确定全断面硬岩掘进机主驱动系统多自由度耦合振动系统下的各子系统的等效刚度与阻尼刀盘—主轴承—齿圈子系统、驱动轴子系统以及支撑架—主梁子系统等效刚度通过有限元方法确定,在对模型施加约束和单位载荷后,通过位移云图和胡克定律确定三个子系统的等效刚度。等效阻尼按照如下公式计算:式中,ξ为阻尼比,me,ke分别为等效质量和等效刚度。步骤5、通过ansys/ls-dyna计算模型外部激励全断面岩石掘进机在施工过程中,滚刀与岩石之间接触力学行为复杂,ls-dyna程序能够描述岩石力学特征的材料本构模型,并且能准确地模拟滚刀与岩石间的非线性接触行为。围岩的力学性能参数是决定滚刀破岩载荷的关键因素,本专利采用hjc动态损伤本构模型模拟围岩材料,该模型考虑了材料损伤累计、应变率效应以及单轴抗压强度对屈服应力的影响,其中屈服面方程如下:σ=[a(1-d)+bpn](1+clnε)式中,σ,p为标准化的等效应力及静水压力,分别等于实际等效应力和静水压力除以材料的抗压强度,ε为无量纲应变率,等于真实应变率除以参考应变率,d为损伤度,a、b、c、n为材料强度参数。其中损伤演化方程如下:式中,δεp,δup分别为一个计算循环内的等效塑性应变和塑性化积应变;分别为常压下破碎的等效塑性应变和塑性体积应变。步骤6、基于外部激励载荷、护盾与围岩相互作用力和振动响应,计算破岩能量消耗、整机振动能量耗散和破岩体积,计算评价硬岩掘进机掘进性能的动态比能,并以单位时间内的加速度均值表征硬岩掘进机整机振动水平。对比安装不同夹层、钢板厚度的高分子阻尼减振钢板振动烈度,确定夹层厚度t1与钢板厚度尺寸t2。本发明的有益效果:本发明考虑了现有的更改部件连接方式和更替部件材料方法的缺点,提出了一种结构减振的方法,可以在满足安全性和强度要求下,降低全断面硬岩掘进机主机振动强度,从而降低全断面硬岩掘进机主机部件的损害程度,提高了隧道施工效率,极大加快掘进工程的施工进度。附图说明图1为高分子减振钢板示意图(a)俯视图,(b)正视图。图2为全断面硬岩掘进机刀盘、主驱动结构。图3为结构改进后的全断面硬岩掘进机刀盘、主驱动结构。图4为全断面硬岩掘进机主机沿隧道开挖方向的轴向动力学模型,其中fl沿隧道开挖方向的轴向力,mi、keqiz、ceqiz与zi(i=1,2,3)分别为刀盘—主轴承—齿圈子系统、驱动轴子系统、支撑架—主梁子系统轴向等效刚度、轴向等效阻尼与轴向振动位移。图5为全断面硬岩掘进机主机沿刀盘盘面的横向动力学模型,其中fx沿刀盘盘面的横向不平衡力,mi、keqix、ceqix与xi(i=1,2,3)分别为刀盘—主轴承—齿圈子系统、驱动轴子系统、支撑架—主梁子系统的质量、横向等效刚度、横向等效阻尼与横向振动位移,keqx、ceqx分别为支撑系统的横向等效刚度与等效阻尼。图中:1-1刀盘右边块连接法兰、1-2刀盘中心块连接法兰、1-3螺栓连接、2刀盘法兰、3外端盖、4刀盘转接环、5-1回转支承内圈、5-2回转支承外圈、5-3回转支承滚动体、6螺柱连接、7刀盘转接环、8减振钢板1、9减振钢板2。具体实施方式以下结合附图和技术方案,进一步说明本发明的具体实施方式。本发明以某隧道工程为例,其中:岩石主要物理参数为:全断面掘进机掘进岩石主要为花岗片麻岩,其岩石密度2750kg·m-3,岩石饱和抗压强度95mpa,内摩擦角33.4°,内聚力0.9mpa,弹性模量20×103mpa,泊松比0.2,围压8~30mpa,埋深330~780m。全断面掘进机主要参数为:刀盘半径r=5.015m,刀盘转速为8.5r/min,刀盘子系统质量为155t,法兰螺栓连接子系统质量为20t,支撑驱动子系统300t。本例将上述全断面掘进机主要参数与围岩参数带入到一种全断面硬岩掘进机减振优化结构设计方法,具体步骤如下:步骤1高分子夹层阻尼减振钢板夹层材料的选择材料的阻尼特性一般用损耗因子β表示,损耗因子越大,材料的减振效果越好。根据调研结果显示:在一定条件下,高分子材料的损耗因子超出钢、铁2~4数量级,由钢板和高分子聚合物复合而成的减振钢板具有良好的阻尼减振特性。表1部分材料的损耗因子β材料损耗因子ββ对应的频率/hz丁级树脂1.8010000硫化橡胶5.001000人造橡胶2.593000综合考虑了材料的适用温度、损耗因子、经济性,结合全断面岩石掘进机的工况,决定选用人造橡胶作为减振钢板的夹层材料。步骤2确定高分子夹层阻尼减振钢板的结构及尺寸出于全断面岩石掘进机整体结构合理性和螺栓受力均匀性来考虑,高分子夹层阻尼减振钢板为圆环形状。减振钢板与法兰是通过螺栓进行连接,所以减振钢板的尺寸确定方程如下:r=rfr=rfα=αf式中,r为减振钢板内径;r为减振钢板外径;α为减振钢板中螺纹孔间隔角;rf为法兰内径;rf为法兰外径;αf为法兰中螺纹孔间隔角。高分子夹层阻尼减振钢板分三层,外层为钢板,内层为高分子夹层。通过构建全断面硬岩掘进机刀盘动力学模型,对模型结果进行分析对比,确定减振钢板的夹层厚度t1与钢板厚度尺寸t2。高分子夹层阻尼减振钢板如图1所示。步骤3建立全断面硬岩掘进机刀盘动力学模型考虑到全断面岩石掘进机零部件之间的动力学耦合,本专利针对刀盘驱动系统多点啮合、多结合面等复杂结构特征,基于有限元思想,提出一种适用于复杂传动系统动力学研究的分层次建模方法。根据部件间的装配关系将全断面硬岩掘进机主机系统进行拆分,分成刀盘刀具系统、刀盘驱动系统、主梁、推进系统及支撑系统。刀盘刀具系统作为切削岩石的执行部件,由刀盘分体和刀盘中心块组成;刀盘驱动系统作为全断面岩石掘进机的核心功能件,是一个包含多级传动,具有多结合面、多点结合等结构特征的复杂传动系统。由刀盘、法兰、主轴承、齿圈、小齿轮、主减速器与变频电机组成;针对结构复杂的刀盘驱动系统整机进行逐级拆分,分为刀盘—主轴承—齿圈子系统、驱动轴子系统以及支撑架—主梁子系统三个子系统。运用集中质量法,考虑多结合面的接触刚度、阻尼以及螺栓预紧力等,建立全断面硬岩掘进机主驱动系统多自由度耦合振动系统。全断面硬岩掘进机主机沿隧道开挖方向的轴向动力学模型如图4所示,全断面硬岩掘进机主机沿刀盘盘面的横向动力学模型如图5所示。步骤4确定全断面硬岩掘进机主驱动系统多自由度耦合振动系统下的各子系统的等效刚度与阻尼。刀盘—主轴承—齿圈子系统、驱动轴子系统以及支撑架—主梁子系统等效刚度通过有限元方法确定,在对模型施加约束和单位载荷后,通过位移云图和胡克定律确定三个子系统的等效刚度。等效阻尼按照如下公式计算:式中,ξ为阻尼比,me,ke分别为等效质量和等效刚度。表2等效刚度和等效阻尼步骤5通过ansys/ls-dyna计算模型外部激励全断面岩石掘进机在施工过程中,滚刀与岩石之间接触力学行为复杂,ls-dyna程序能够描述岩石力学特征的材料本构模型,并且能准确地模拟滚刀与岩石间的非线性接触行为。围岩的力学性能参数是决定滚刀破岩载荷的关键因素,本专利采用hjc动态损伤本构模型模拟围岩材料表3围岩主要物理力学参数密度/(kg·m-3)弹性模量/gpa泊松比抗压强度/mpa内摩擦角内聚力/mpa2750200.29533.4°0.9表4hjc本构模型参数强度参数a强度参数b硬化系数c剪切模量g/gpa抗压强度σ/mpa0.791.60.0078.393.6压碎应力/mpa压力常数k压力硬化指数n损伤常数d1失效类型fs322080.610.041取刀盘转速为9r/min,掘进速度为5.5mm/s,并施加在滚刀刀体上;在岩石侧面和底面分别设为15mpa和30mpa的围压。刀盘与刀体静摩擦系数0.15,动摩擦系数0.15,刀盘与岩石静摩擦系数0.4,动摩擦系数0.35,得到单个滚刀侧向力、垂直力与滚动力。滚刀载荷统计如表5所示、表5滚刀载荷统计表步骤6求解动力学模型,确定高分子阻尼减振钢板夹层和钢板的厚度,并对比增加高分子阻尼减振钢板前后的全断面硬岩掘进机的振动强度。基于外部激励载荷、护盾与围岩相互作用力和振动响应,计算破岩能量消耗、整机振动能量耗散和破岩体积,计算评价硬岩掘进机掘进性能的动态比能,并以单位时间内的加速度均值表征硬岩掘进机整机振动水平。利用matlab软件,求解动力学模型,确定高分子阻尼减振钢板夹层和钢板的厚度,并计算各系统单位时间轴向加速度均值如表6所示表6各系统单位时间轴向加速度均值如表所示,刀盘—主轴承—齿圈子系统、驱动轴子系统以及支撑架—主梁子系统轴向加速度在增加减振钢板后,都有相应的减少,其中刀盘—主轴承—齿圈子系统轴向加速度减少5%,驱动轴子系统轴向加速度减少10%,支撑架—主梁子系统轴向加速度减少8%。可证明本专利一种全断面硬岩掘进机减振优化结构设计方法是合理可行的。当前第1页12