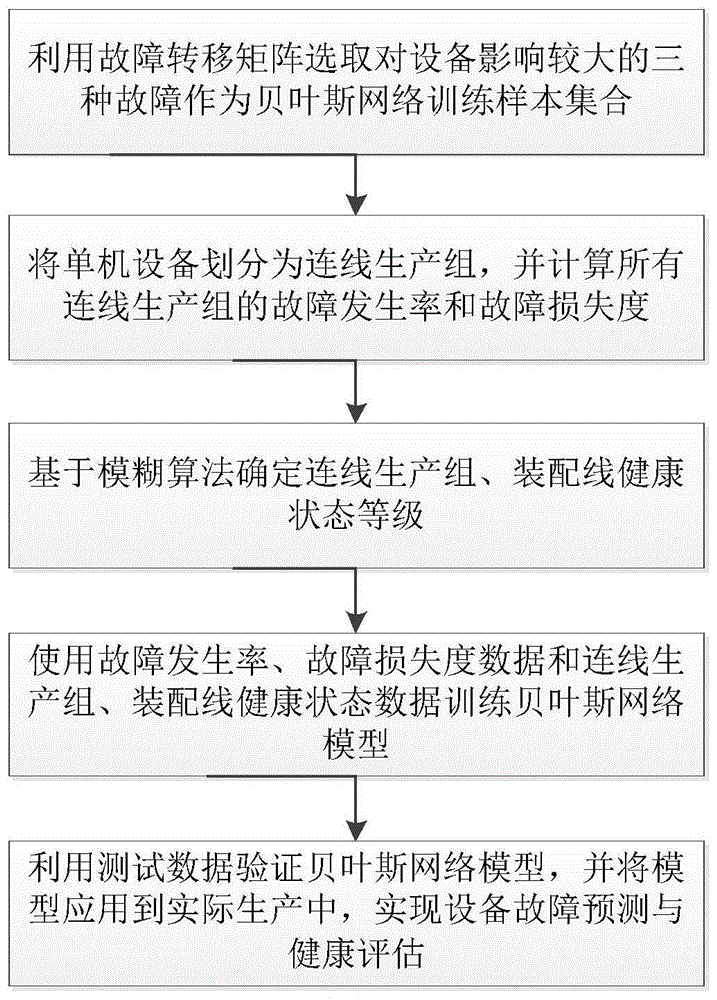
本发明属于智能工厂设备建设
技术领域:
,涉及设备故障预测与健康评估方法,具体涉及一种基于模糊贝叶斯网络的设备故障预测与健康评估方法。
背景技术:
:智能工厂设备故障分析与预测是精益生产的需求,也是建设智能工厂的关键任务之一。随着智能工厂的集成度和复杂度越来越高,系统故障发生概率和功能失效概率也逐渐加大,且故障一旦发生,会造成极大的危害,严重的会导致系统整个失效和瘫痪。如果在故障发生的早期,即在其还未对系统造成任何损害的情况下及时检测出故障并实施可靠的维修策略排除故障,就可以在很大程度上避免产品损坏、系统瘫痪以及灾难性事故的发生。智能工厂的设备故障分析与预测主要包括设备故障类型定义,设备故障数据采集与处理,故障特征提取,故障诊断,故障预测,健康状态评估等环节。故障是设备不能完成规定功能或性能退化到不满足规定要求的状态;故障诊断利用设备状态监测数据,借助于智能诊断算法,对已出现故障的设备进行诊断,为故障隔离和故障检修奠定基础;故障预测依据监测所得历史数据和故障模型,对各种数据和信息资源进行综合分析,通过基于模型的、基于数据驱动的、基于概率统计的故障预测方法,预测设备未来可能发生故障的部位和概率,为维修决策提供支撑;健康评估是用系统的健康状态决定是否启动故障诊断和设备维护。智能工厂采集了海量的生产过程数据,基于数据驱动(data-driven)的故障预测方法逐渐获得重视并取得快速发展。目前已有多种基于监测数据的故障预测方法,例如box等提出用于处理时间序列预测的自回归积分滑动平均模型(autoregressiveintegratedmovingaveragemodel,arima),该模型本质上是把时间序列看成内在关联的全过程来研究,排除时间序列中异常值,计算时间序列数据的自相关性并以此表征时间序列未来的发展趋势,以达到对数据的未来值进行短期预测的目的。奇异谱分析(singularspectrumanalysis,ssa)是一种时域和频域相结合的非参数故障时间序列预测方法,包含嵌入、奇异值分解和重构三个过程,该方法的核心是提取序列中的有效成分实现对时间序列的建模和预测,时间序列可以是非线性、非平稳及包含噪声的。支持向量回归(supportvectormachinesregression,svr)是一种用于时间序列预测的机器学习方法,该方法针对有限样本,其思想是实现结构风险最小化,通过一个非线性核函数将多维输入映射到更高维度的特征空间后执行回归运算,进而得到与输出指标的非线性映射关系,实现对时间序列的预测。上述故障预测方法由于从设备故障信息中挖掘获取的信息较少,不能发现连续生产工序上各单机设备故障之间的相互作用,没有考虑相关联的故障对系统的影响,不能发现主要故障,因此故障预测准确率较低。技术实现要素:为了克服上述现有技术的不足,本发明提供一种基于模糊贝叶斯网络的设备故障预测与健康评估方法,提取设备的主要故障,将连续生产工序上各单机设备故障之间的相互作用对系统的影响量化为故障损失度,构建模糊贝叶斯网络实现设备故障预测与健康评估。本发明方法能够充分利用设备的故障信息、发现有代表性的故障,使设备故障预测结果更加准确,并能够通过故障损失度使健康评估更符合实情,设计合理、操作简便,具有广泛的应用价值。本方法利用故障转移矩阵选取对设备影响较大的三种故障作为贝叶斯网络训练样本集合;将单机设备划分为连线生产组,并计算所有连线生产组的故障发生率和故障损失度;基于模糊算法确定连线生产组、装配线健康状态等级;使用故障发生率、故障损失度数据和连线生产组、装配线健康状态数据训练贝叶斯网络模型;利用测试数据验证贝叶斯网络模型,并将模型应用到实际生产中,实现设备故障预测与健康评估。具体来说,本发明提供的技术方案是:一种基于模糊贝叶斯网络的设备故障检测方法,包括下列步骤:a.选取n个设备的主要故障作为贝叶斯网络的训练样本集合w,其中每种设备选取三种主要故障,具体步骤如下:a1.构造n个设备的故障转移概率矩阵,具体步骤如下:a11.构造n个设备的故障转移次数表,表中元素为每种设备在一段时间内一种故障转移到其他类型故障的次数cij(i,j=1,2,…,n),i为故障码i,j为故障码j,n表示某单机设备在研究时间段内出现了n种故障码;所述故障转移,是一种故障发生并修复好后又发生故障的现象,两次故障可能相同也可能不同;a12.计算n个设备的故障转移概率矩阵,矩阵元素为每种设备在一段时间内由一种故障转移到其他类型故障的概率pij(i,j=1,2,…,n),i为故障码i,j为故障码j,n表示某单机设备在研究时间段内出现了n种故障码,如p23表示某设备当前为故障码2,下次转移到故障码3的概率;其中,n表示所检测装配线line上单机设备的个数;a2.构造所有设备的故障码比重矩阵gi(i=1,2,…,n),i为第i个设备,具体步骤如下:a21.计算第i个设备的每种故障码出现的次数占该设备所有故障码出现次数的比例,构成第i个设备的故障码概率矩阵ri(i=1,2,…,n),i为第i个设备;a22.取第i个设备故障转移概率矩阵对角线上的概率{p11,,p22,…,pnn},构成第i个设备的故障码持续概率矩阵wi(i=1,2,…,n),i为第i个设备;a23.根据专家经验确定故障码概率矩阵ri的权重γ1和故障码持续概率矩阵wi的权重γ2;a24.计算第i个设备的故障码比重矩阵gi(i=1,2,…,n),gi=γ1×ri+γ2×wi,i为第i个设备,γ1为故障码概率矩阵ri的权重,γ2为故障码持续概率矩阵wi的权重;a3.选取故障码比重矩阵gi中比重最大的三种故障码作为第i个设备的主要故障码;a4.由n个设备的主要故障码(即3*n个故障码)构成贝叶斯网络的训练样本集合w;b.将装配线line上的n个单机设备划分为m个连线生产组(简称单元组),并计算所有单元组的故障发生率和故障损失度,具体步骤如下:b1.根据装配线line的工序及设备连接情况,将n个设备划分为一个设备或多个相连设备的m个组合,记为m个单元组;b2.计算m个单元组的故障发生率,具体步骤如下:b21.确定第i个单元组内所有设备的主要故障码出现的次数ci,以及装配线line上所有设备的主要故障码出现的总次数nn;b22.计算第i个单元组的故障发生率pi,i为第i个单元组,m为单元组个数,ci为第i个单元组内所有设备的主要故障码出现的次数,nn为装配线line上所有设备的主要故障码出现的总次数;b3.计算m个单元组的故障损失度,故障损失度为第i个单元组故障所带来的产量损失比率,具体步骤如下:b31.确定第i个单元组每次故障发生的时间tj和故障发生的次数k,计算第i个单元组的平均故障时间δti,i为第i个单元组,m为单元组个数,tj为每次故障发生的时间,k为故障发生的次数;b32.计算m个单元组的零件积累量li(i=1,2,…,m)和零件空闲量hi(i=1,2,…,m),i为第i个单元组,m为单元组个数,具体步骤如下:b321第i个单元组发生故障时,确定堆积在第i-1个单元组与第i个单元组间的零部件数量h1和发生故障时第i单元组与第i+1个单元组间的零部件数量h2;b322确定第i个单元组生产零件的速度ψti(i=1,2,…,m),i为第i个单元组,m为单元组个数;b323计算第i个单元组的零件积累量li:i为第i个单元组,δti为第i个单元组的平均故障时间,ψtj为第j个单元组生产零件的速度,h1为第i个单元组发生故障时堆积在第i-1个单元组与第i个单元组间的零部件数量;所述零件积累量为第i个单元组发生故障时,该单元组不工作导致的产量损失;b324计算第i个单元组的零件空闲量hi:i为第i个单元组,n表示某单机设备在研究时间段内出现了n种故障码,δti为第i个单元组的平均故障时间,ψtj为第j个单元组生产零件的速度,h2为第i个单元组发生故障时第i单元组与第i+1个单元组间的零部件数量;所述零件空闲量为第i个单元组发生故障时,第i+1个单元组不工作导致的产量损失;b33.计算未发生故障时m个单元组的正常产量qi,i为第i个单元组,m为单元组个数,n表示某单机设备在研究时间段内出现了n种故障码,δti为第i个单元组的平均故障时间,ψtj为第j个单元组生产零件的速度;b34.通过回归分析法求解故障损失度式中的系数λ1、λ2,具体步骤如下:b341建立因变量为故障损失度δi,自变量为零件积累量/正常量(m1)和零件空闲量/正常量(m2)的回归模型:δi=λ1m1+λ2m2+ξ,λ1为故障损失度式中系数,λ2为故障损失度式中系数,m1为零件积累量/正常量,m2为零件空闲量/正常量,ξ为误差项;b342将实际测得的装配线line中某单元组的故障损失度、零件积累量、零件空闲量数据代入步骤b341中所建立的回归模型进行线性拟合,确定回归模型的系数λ1、λ2的值,使模型的拟合度最高,并将所得λ1、λ2的值应用于所有单元组的故障损失度计算中;b35.计算第i个单元组的故障损失度δi,其中,li为第i个单元组的零件积累量,hi为第i个单元组的零件空闲量,qi为第i个单元组未发生故障时的正常产量,λ1、λ2为b3.4所确定的系数;c.基于模糊算法确定单元组、装配线line健康状态等级,具体步骤如下:c1.将单元组的故障发生率和故障损失度映射为故障发生率等级和故障损失度等级,具体步骤如下:c11.利用指派方法确定模糊算法的隶属函数;c12.根据b2步骤中所得故障发生率的值将故障发生率分为小(si)[0-0.2)、中(mi)[0.2-0.4)、大(li)[0.4-1]三个等级;c13.根据b3步骤中所得故障损失度的值将故障损失度分为小(si)[0-0.22)、中(mi)[0.22-0.24)、大(li)[0.24-1]三个等级;c2.根据第i个单元组的故障发生率和故障损失度等级,将该单元组的健康状态分为四个等级:优(si∨si)、良(si∨mi、si∨li、mi∨si)、中(mi∨mi、mi∨li、li∨si)、差(li∨mi、li∨li);c3.将整条装配线line的等级分为优(a)、良(b)、中(c)、差(d)四个等级,划分依据为整条装配线line包含的单元组的优状态的个数,即若整条装配线line包含的单元组中,状态为优的单元组个数占该装配线总单元组个数的百分比为u,当u≥75%时,装配线line的健康等级为优(a),当u≥50%且u<75%时,装配线line的健康等级为良(b),当u≥25%且u<50%时,装配线line的健康等级为中(c),当u<25%时,装配线line的健康等级为差(d);d.使用故障发生率、故障损失度数据和单元组、装配线line健康状态数据训练贝叶斯网络模型,得到训练好的设备故障检测贝叶斯网络模型,具体步骤如下:d1.训练数据取自于所预测装配线line较长一段时间(>=365天)内所有设备的所有故障数据形成的原始数据集,将原始数据划分为70%的训练数据和30%的测试数据,故障发生率、故障损失度数据和单元组、装配线line健康状态数据由原始训练数据通过所述a、b、c方法获得;d2.构建贝叶斯网络有向无环图,具体步骤如下:d21.构建贝叶斯网络前期拓扑图:由原始数据—影响因素—健康状态的层次结构以及专家经验确定贝叶斯网络前期拓扑图,变量关系为:主要故障码—>设备,设备—>故障发生率,设备—>故障损失度,故障发生率—>健康状态,故障损失度—>健康状态;d22.构建贝叶斯网络后期拓扑图:由装配线健康状态—单元组状态—故障发生率和故障损失度的层次结构构建贝叶斯网络后期拓扑图,变量关系为:装配线健康状态—>单元组健康状态,单元组健康状态—>单元组故障发生率,单元组健康状态—>单元组故障损失度;所述“—>”表示所连接的两个变量间的因果关系,“—>”前的变量为原因(也称“—>”后变量的父节点),“—>”后的变量为结果(也称“—>”前变量的子节点);d3.分两层求贝叶斯网络条件概率表,具体步骤如下:d31.利用装配线line健康状态,求解m个单元组健康状态的条件概率,由步骤c所得装配线line的健康状态及单元组的健康状态等级数据,分别计算单元组的健康状态为a、b、c、d等级的概率,分别计算装配线line的健康状态为a、b、c、d等级的同时单元组健康状态为a、b、c、d等级的概率,由条件概率公式分别求取在装配线line的健康状态为a、b、c、d等级的条件下m个单元组的健康状态为a、b、c、d等级的条件概率;d32.利用m个单元组的健康状态,求解m个单元组故障发生率和故障损失度的条件概率,由步骤c所得单元组的健康状态等级数据及故障发生率和故障损失度等级数据,分别计算故障发生率为s、m、l等级的概率,分别计算故障损失度为s、m、l等级的概率,分别计算m个单元组健康状态为a、b、c、d等级的同时故障发生率为s、m、l等级的概率,分别计算m个单元组健康状态为a、b、c、d等级的同时故障损失度为s、m、l等级的概率,由条件概率公式分别求取在m个单元组健康状态为a、b、c、d等级的条件下故障发生率为s、m、l等级的条件概率,分别求取在m个单元组健康状态为a、b、c、d等级的条件下故障损失度为s、m、l等级的条件概率;e.将测试数据应用于训练后的贝叶斯网络模型,对日期d当日的m个单元组和装配线line健康状态作出评估,并将模型应用到实际生产中,具体步骤如下:e1.利用日期d前的一段时间(>=30天)的历史数据,通过a、b、c步骤所述方法获得m个单元组的故障发生率和故障损失度等级数据;e2.将m个单元组的故障发生率和故障损失度等级数据输入所构建的模糊贝叶斯网络模型,模型输出单元组的健康状态;e3.将e2所得单元组健康状态数据输入到所构建的模糊贝叶斯网络模型,模型输出装配线line的健康状态;e4.根据e3预测所得的装配线line健康状态信息判断这一天的设备故障情况。与现有技术相比,本发明的有益效果是:本发明的技术优点是考虑了连续生产工序上各单机设备故障之间的关系,可以及时的了解产线和连线生产组的健康状态,对故障进行有效的预测,便于有针对性地采取维修措施及时解决系统问题,对维修人员及时高效的排除故障、防止危害性事故发生、提高维修保障能力具有重要意义。附图说明图1是本发明提供的基于模糊贝叶斯网络的设备故障与健康评估方法的流程框图。图2是本发明实施例中装配线xa贝叶斯网络前期拓扑图。图3是本发明实施例中装配线xa贝叶斯网络后期拓扑图。具体实施方式下面结合附图,通过实施例进一步描述本发明,但不以任何方式限制本发明的范围。以下实施例采用某家电企业2017年9月到2018年7月装配线xa数据(该装配线上共有9台单机设备),详细叙述本发明提供的预测方法的实施过程。方法流程图如图1所示。本发明方法包括:1)利用故障转移矩阵选取对设备影响较大的三种故障作为贝叶斯网络训练样本集合;2)将单机设备划分为连线生产组,并计算所有连线生产组的故障发生率和故障损失度;3)基于模糊算法确定连线生产组、装配线健康状态等级;4)使用故障发生率、故障损失度数据和连线生产组、装配线健康状态数据训练贝叶斯网络模型;5)利用测试数据验证贝叶斯网络模型,并将模型应用到实际生产中,实现设备故障预测与健康评估。具体实施步骤如下:1.选取9个设备的27种主要故障码作为贝叶斯网络的训练样本集合w,具体步骤如下:1.1.确定9个设备的故障转移概率矩阵;1.2.确定所有设备的故障码比重矩阵gi(i=1,2,…,9),具体步骤如下:1.2.1.计算第i个设备的每种故障码出现的次数占第i个设备所有故障码出现次数的比例,构成第i个设备的故障码概率矩阵ri(i=1,2,…,9);1.2.2.取第i个设备故障转移概率矩阵对角线上的概率{p11,,p22,…,pnn},构成第i个设备的故障码持续概率矩阵wi(i=1,2,…,9);1.2.3.确定故障码概率矩阵ri的权重γ1和故障码持续概率矩阵wi的权重γ2;1.2.4.计算第i个设备的故障码比重矩阵gi(i=1,2,…,9);1.3.选取故障码比重矩阵gi中比重最大的三种故障码作为第i个设备的主要故障码,实例提取结果如表1所示;表1实施例中九种设备的主要故障码1.4.由9个设备的主要故障码(即27个故障码)构成贝叶斯网络的训练样本集合w;2.将装配线上的9个单机设备划分为4个连线生产组(简称单元组),并计算所有单元组的故障发生率和故障损失度,具体步骤如下:2.1.将9个设备划分为4个单元组,具体如表2:表2实施例中的单元组划分表2.2.计算4个单元组的故障发生率,具体步骤如下:2.2.1.确定第i个单元组内所有设备的主要故障码出现的次数ci和所研究装配线上所有设备的主要故障码出现的总次数nn;2.2.2.计算第i个单元组的故障发生率pi,2.3.计算4个单元组的故障损失度,具体步骤如下:2.3.1.确定第i个单元组每次故障发生的时间tj和故障发生的次数k,计算所有单元组的平均故障时间δti,2.3.2.计算4个单元组的零件积累量li(i=1,2,…,4)和零件空闲量hi(i=1,2,…,4),具体步骤如下:2.3.2.1第i个单元组发生故障时,确定堆积在第i-1个单元组与第i个单元组间的零部件数量h1和发生故障时第i单元组与第i+1个单元组间的零部件数量h2;2.3.2.2确定第i个单元组生产零件的速度;2.3.2.3计算第i个单元组的零件积累量和零件空闲量:2.3.3.计算未发生故障时4个单元组的正常产量,2.3.4.通过回归分析法求解故障损失度式中的系数λ1、λ2,具体步骤如下:2.3.4.1建立因变量为故障损失度δi,自变量为零件积累量/正常量(m1)和零件空闲量/正常量(m2)的回归模型:δi=λ1m1+λ2m2+ξ;2.3.4.2根据实际测得的装配线xa中某单元组的故障损失度、零件积累量、零件空闲量数据,确定参数λ1、λ2,使模型的拟合度最高,并将所得λ1、λ2应用于所有单元组的故障损失度计算中;2.3.5.计算第i个单元组的故障损失度δi,3.基于模糊算法确定单元组、装配线健康状态等级,具体步骤如下:3.1.将单元组的故障发生率和故障损失度映射为故障发生率等级和故障损失度等级,具体步骤如下:3.1.1.利用指派方法确定模糊算法的隶属函数;3.1.2.根据故障发生率的值将故障发生率分为小(si)[0-0.2)、中(mi)[0.2-0.4)、大(li)[0.4-1]三个等级,根据故障损失度的值将故障损失度分为小(si)[0-0.22)、中(mi)[0.22-0.24)、大(li)[0.24-1]三个等级;3.2.根据第i个单元组的故障发生率和故障损失度等级,将该单元组的健康状态分为四个等级:优(si∨si)、良(si∨mi、si∨li、mi∨si)、中(mi∨mi、mi∨li、li∨si)、差(li∨mi、li∨li),具体如表3:表3实施例中连线生成单元组的健康状态分类3.3.根据整条装配线包含的单元组的优状态个数将整条装配线的等级分为优(a)、良(b)、中(c)、差(d)四个等级,具体如表4:表4实施例装配线xa健康状态等级表4.使用故障发生率、故障损失度数据和单元组、装配线xa健康状态数据训练贝叶斯网络模型,具体步骤如下:4.1.构建贝叶斯网络有向无环图,具体步骤如下:4.1.1.构建贝叶斯网络前期拓扑图:由原始数据—影响因素—健康状态的层次结构以及专家经验确定贝叶斯网络前期拓扑图,变量关系为:主要故障码—>设备,设备—>故障发生率,设备—>故障损失度,故障发生率—>健康状态,故障损失度—>健康状态,实例构建如附图2,图中设备1—9为实例中的9个单机设备,指向每个设备的3位数的数字为该设备3种主要故障的故障码,故障发生率代表单元组的故障发生率,损失度代表单元组的故障损失度,健康状态代表单元组和装配线的健康状态;4.1.2.构建贝叶斯网络后期拓扑图:由装配线健康状态—单元组(unit)状态—故障发生率和故障损失度的层次结构构建贝叶斯网络后期拓扑图,变量关系为:装配线健康状态—>单元组健康状态,单元组健康状态—>单元组故障发生率,单元组健康状态—>单元组故障损失度,实例构建如附图3;4.2.分两层求条件概率表,具体步骤如下:4.2.1.求解4个单元组健康状态的条件概率,在装配线xa的健康状态分别为a、b、c、d等级下4个单元组的健康状态分别为a、b、c、d等级的条件概率,实例结果如表5:表5实施例中得到的训练数据装配线xa健康状态等级概率表6实施例中4个单元组的条件概率4.2.2.求解4个单元组故障发生率和故障损失度的条件概率,在4个单元组健康状态为a、b、c、d等级下故障发生率分别为s、m、l等级的条件概率,在4个单元组健康状态为a、b、c、d等级下故障损失度分别为s、m、l等级的条件概率,实例计算结果如表7~10:表7unit1故障发生率、故障损失度条件概率表8unit2故障发生率、故障损失度条件概率表9unit3故障发生率、故障损失度条件概率表10unit4故障发生率、故障损失度条件概率5.用测试数据验证训练后的贝叶斯网络模型,对2018年7月14日当日的4个单元组和装配线xa健康状态作出评估,并将模型应用到实际生产中,具体步骤如下:5.1.利用2018年4月14日至2018年7月13日的数据,通过a、b、c步骤所述方法获得故障发生率和故障损失度等级数据,结果如表11:表11单元组故障发生率、故障损失度等级5.2.将单元组的故障发生率和故障损失度等级数据输入所构建的模糊贝叶斯网络模型模型输出单元组的健康状态,实例输出结果如表12:表12单元组健康状态unit1unit2unit3unit4dbcb5.3.将e2所得单元组健康状态数据输入到所构建的模糊贝叶斯网络模型,模型输出装配线2018年7月14日的健康状态,实例结果如表13:表13单元组健康状态及装配线xa的健康状态5.4.根据5.3预测所得的装配线健康状态信息判断这一天设备故障情况。本发明的方法实现了基于模糊贝叶斯网络的故障预测和健康评估,通过5个步骤能够实现对故障的有效预测和对健康状态的评估,便于有针对性地采取维修措施及时解决系统问题,具有很高的经济效益。最后需要注意的是,公布实施例的目的在于帮助进一步理解本发明,但是本领域的技术人员可以理解:在不脱离本发明及所附的权利要求的精神和范围内,各种替换和修改都是可能的。因此,本发明不应局限于实施例所公开的内容,本发明要求保护的范围以权利要求书界定的范围为准。当前第1页12