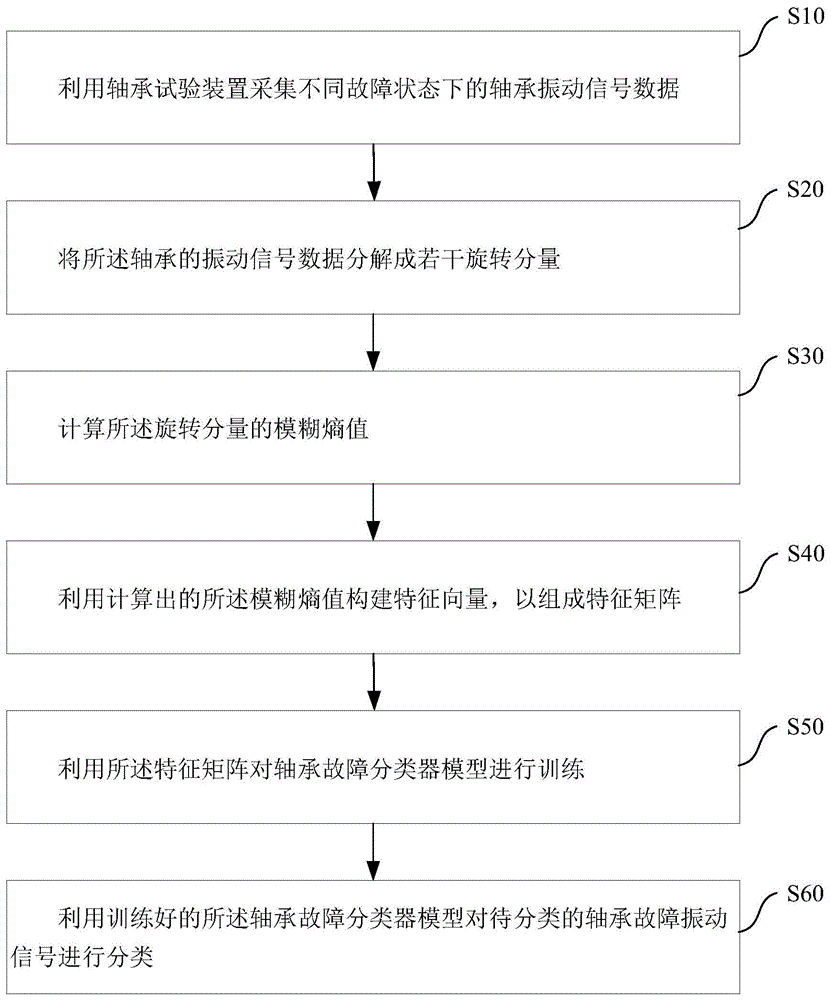
本发明涉及轴承故障诊断
技术领域:
,特别涉及一种轴承故障分类方法及系统。
背景技术:
:滚动轴承是大多数机械和电气设备的重要支承部件,它发生故障将直接影响设备的正常工作,导致重大经济损失。准确有效地轴承故障诊断分类方法既可提高设备运行的可靠性和稳定性,也可避免重大事故的发生。在现有的轴承故障诊断分类方法中存在以下问题:基于固有时间尺度分解(intrinsictime-scaledecomposition,itd)和近似熵结合随机森林(randomforest,rf)的轴承故障诊断方法,itd分解后的信号噪声抑制不明显,高频固有旋转分量(properrotationcomponents,prc,下文称为pr分量)去噪效果差,且近似熵采用硬阈值作为判据指标,影响数据统计结果稳定性;利用itd对轴承故障信号进行分解,利用相关系数计算pr分量得到熵值与时域特征,再通过主成分分析(principalcomponentanalysis,pca)降维后输入到极限学习机识别出轴承故障状态,但itd分解本身不可避免出现端点效应和波形失真问题,且故障诊断模型的建立步骤复杂,过程繁琐;基于iitd样本熵和支持向量机的齿轮故障诊断方法,样本熵易受数据波动影响,支持向量机在处理大样本数据能力不足以及多分类问题精度较低等缺陷。技术实现要素:鉴于以上所述现有技术的缺点,本发明的目的在于提供一种轴承故障分类方法及系统,用于解决现有技术中itd分解的端点效应和波形失真、近似熵、样本熵易受数据波动影响和基线漂移、传统分类器特征选择困难、分类精度低的技术问题。为实现上述目的及其他相关目的,本发明提供一种轴承故障分类方法,所述轴承故障分类方法包括以下步骤:利用轴承试验装置获取不同故障状态下的轴承振动信号数据;将所述轴承的振动信号数据分解成若干固有旋转分量;计算所述固有旋转分量的模糊熵值;利用计算出的所述模糊熵值构建特征向量,以组成特征矩阵;利用所述特征矩阵对轴承故障分类器模型进行训练;利用训练好的所述轴承故障分类器模型对待分类的轴承故障振动信号进行分类。在一可选实施例中,所述不同故障状态包括正常状态、滚动体故障、内圈故障、外圈故障、保持架故障以及复合型故障。在一可选实施例中,在所述利用轴承试验装置获取不同故障状态下的轴承振动信号数据的步骤中,通过激光打标机和线切割完成轴承不同故障类型的加工。在一可选实施例中,在所述利用轴承试验装置获取不同故障状态下的轴承振动信号数据的步骤中,利用设置于主轴轴承试验机的加速度振动传感器来采集轴承试验装置在不同故障状态下的轴承振动信号数据。在一可选实施例中,在所述利用轴承试验装置获取不同故障状态下的轴承振动信号数据的步骤中,利用设置于主轴轴承试验机的三向加速度振动传感器和单向加速度振动传感器来采集轴承试验装置在不同故障状态下的轴承振动信号数据。在一可选实施例中,在所述将所述轴承的振动信号数据分解成若干固有旋转分量的步骤中,利用改进的固有时间尺度分解方法对所述轴承的振动信号数据进行分解,以获取若干固有旋转分量。在一可选实施例中,所述计算所述固有旋转分量的模糊熵值的步骤包括,选取表征故障主要信息的有效固有旋转分量计算其模糊熵值。在一可选实施例中,所述选取表征故障主要信息的有效固有旋转分量并计算其模糊熵值的步骤包括:计算获取所述固有旋转分量的互相关系数;通过互相关系数选取表征故障主要信息的有效固有旋转分量并计算其模糊熵值。在一可选实施例中,所述利用所述特征矩阵对轴承故障分类器模型进行训练的步骤包括:将所述特征矩阵划分为训练集和测试集;利用所述训练集对所述对轴承故障分类器模型进行训练;利用所述测试集来测试训练后的所述轴承故障分类器模型。在一可选实施例中,所述轴承故障分类器模型包括随机森林分类器模型。为实现上述目的及其他相关目的,本发明还提供一种轴承故障分类系统,所述轴承故障分类系统包括:轴承试验装置,用于对不同故障状态的轴承进行试验;信号采集模块,所述信号采集模块的加速度振动传感器设置于所述轴承试验装置上,用于采集不同故障状态下的轴承振动信号数据;故障特征信号处理模块,用于将所述轴承的振动信号数据分解成若干固有旋转分量,计算所述固有旋转分量的模糊熵值,利用计算出的所述模糊熵值构建特征向量,以组成特征矩阵;以及轴承故障分类模块,与所述故障特征信号处理模块连接,用于利用所述特征矩阵对轴承故障分类器模型进行训练,并利用训练好的所述轴承故障分类器模型对待分类的轴承故障振动信号进行分类。本发明的改进的itd结合随机森林的轴承故障分类方法及系统,将改进的itd和模糊熵及随机森林分类器进行融合并发挥各自优势,改进的itd解决了前述的itd分解的端点效应和波形失真问题;本发明的基于改进的itd结合随机森林的轴承故障分类方法及系统,模糊熵作为iitd特征提取后的特征选择依据,解决了近似熵、样本熵易受数据波动影响和基线漂移的问题;本发明的基于改进的itd结合随机森林的滚动轴承故障分类方法及系统,对于多分类问题,随机森林分类器可以克服传统分类器特征选择困难、分类精度低的问题;本发明的基于改进的itd结合随机森林的滚动轴承故障分类方法及系统,不仅能够针对轴承的单种故障进行分类,而且还可以对轴承的复合型故障进行分类;经试验数据验证,本发明提出的将iitd、模糊熵与随机森林相结合的轴承故障分类模型,在小样本数据和微弱故障信号情况下仍然能准确判断出滚动轴承故障类别。附图说明图1显示为本发明的轴承故障分类方法的流程图。图2显示为本发明实施例的信号采集模块的流程图。图3显示为本发明实施例的轴承故障分类系统的结构框图。图4显示为本发明实施例的轴承故障分类系统的轴承试验装置的结构框图。图5显示为本发明实施例的电子设备的结构框图。图6a显示为本发明的具体实施例中随机森林分类结果。图6b显示为本发明的具体实施例中支持向量机分类结果。图6c显示为本发明的具体实施例中bp神经网络分类结果。具体实施方式以下通过特定的具体实例说明本发明的实施方式,本领域技术人员可由本说明书所揭露的内容轻易地了解本发明的其他优点与功效。本发明还可以通过另外不同的具体实施方式加以实施或应用,本说明书中的各项细节也可以基于不同观点与应用,在没有背离本发明的精神下进行各种修饰或改变。请参阅图1-5。需要说明的是,本实施例中所提供的图示仅以示意方式说明本发明的基本构想,遂图式中仅显示与本发明中有关的组件而非按照实际实施时的组件数目、形状及尺寸绘制,其实际实施时各组件的型态、数量及比例可为一种随意的改变,且其组件布局型态也可能更为复杂。本发明的实施例提出一种基于改进的固有时间尺度分解(improvedintrinsictime-scaledecomposition,iitd)融合随机森林(randomforest,rf)的滚动轴承故障分类方法,具体地说是基于改进的固有时间尺度分解(iitd)以得到故障特征,计算模糊熵值(fuzzyentropy,fe)后输入随机森林分类器的轴承故障分类方法,其中,所述轴承例如可以是滚动轴承。其中,图1示出了本发明的实施例的轴承故障分类方法的流程图;图2示出了本发明的实施例的信号采集模块22的流程图;图3示出了本发明的实施例的计轴承故障分类系统2的结构框图;图4示出了本发明的实施例的计轴承故障分类系统2的轴承试验装置21的结构框图。现将结合图1来对本实施例的轴承故障分类方法的各步骤作具体说明。首先,执行步骤s10中,利用轴承试验装置21获取不同工况下的不同故障轴承振动信号数据,所述不同工况是指:转速、径向载荷、温度的不同及其组合;故障轴承是指在滚动体、内圈、外圈、保持架接触面上由激光打标机烧蚀缺陷的轴承。具体地,提供轴承试验装置21,信号采集模块22通过利用设置在主轴轴承试验机211上加速度振动传感器采集轴承在各种工况类型下运行的实验数据,其中,该轴承试验装置21用于通过更换主轴轴承试验机211中的多种故障轴承轴承进行试验,该多种故障轴承例如可以包含有轴承正常状态、滚动体故障、内圈故障、外圈故障、保持架故障以及复合型故障多种状态类型,其中复合型故障可以是滚动体故障、内圈故障、外圈故障、保持架故障中的任意两种或三种的复合,例如滚动体内圈复合型故障,滚动体外圈复合型故障,滚动体保持架复合型故障,内圈外圈复合型故障,内圈保持架复合型故障,外圈保持架复合型故障,滚动体内圈外圈复合型故障,滚动体内圈保持架复合型故障,内圈外圈保持架复合型故障,滚动体外圈保持架复合型故障;所述复合型故障也可以是滚动体故障、内圈故障、外圈故障和保持架故障中的四种的复合,也即滚动体内圈外圈保持架复合型故障。例如可以通过激光打标机和线切割加工出内圈、外圈、滚动体、保持架完成轴承不同故障类型的加工,具体地,内圈故障例如可使用激光打标机在内圈的内表面加工形成非贯通型的小尺寸方形点蚀损伤(当然也可以是矩形故障或者圆形的点蚀损伤;滚动体故障例如可使用线切割在所述滚动体上沿轴向分布加工形成一细条形贯通槽;外圈故障例如也可使用线切割在所述外圈的与滚动体接触的表面上沿轴向分布加工形成一细条形贯通槽,保持架故障例如可以使用激光打标机在保持架的与滚动体产生相对转动接触的内部侧壁上加工形成小尺寸矩形点蚀损伤故障(对于nsk的nu1010型号单列圆柱滚子轴承,在一具体示例中,该矩形点蚀损伤的尺寸的长为3mm,宽为1mm,深度为0.1mm)。通过加工形成小尺寸的点蚀损伤和细条形贯通槽可以保证后续步骤s20中采集到的轴承振动信号数据为微弱振动信号,从而可以使利用该微弱振动信号训练后的轴承故障分类器模型能够适用于滚动轴承故障微弱振动信号特征分类。在一具体实施例中,信号采集模块22利用设置在主轴轴承试验机211上的3向加速度振动传感器和单向加速度振动传感器采集轴承在各种工况下运行的实验数据。所述3向加速度振动传感器例如可以设置在轴承试验机211的机罩的侧壁,利用3向加速度振动传感器可以供采集到轴承试验机211表面3个方向(x方向、y方向、z方向)的振动加速度信号;所述单向加速度振动传感器例如可以设置在轴承试验机211的机罩的顶部,利用单向加速度振动传感器可以采集一个方向(例如z方向)的振动加速度信号,单向加速度振动传感器采集的一个方向的振动加速度信号可以和3向加速度振动传感器采集的对应方向的振动加速度信号进行验证。在实际的数据处理过程中,可以经过数据分析采用所有方向中信号受外界干扰小的方向(例如y方向)的振动加速度信号作为后续处理的轴承振动信号数据,该选定方向的振动加速度信号更符合滚动轴承故障的实际数据特点。接着,执行步骤s20,利用故障特征信号处理模块23进行故障特征信号处理,将所述轴承的振动信号数据xt分解成若干固有旋转分量与一个残余项,包括以下步骤:步骤21,获取轴承的振动信号数据xt的基线信号l1(t)。寻找轴承的振动信号数据xt的全部极值点及对应时刻τk(k=1,2,…n),n为极值点的个数,在连续极值点[τk,τk+1]上,定义信号线性提取因子l为:其中其中α为线性缩放因子,α的取值例如可以为0.5(当然也可以是其他合适的值);步骤22,通过上述公式(1)提取到基线控制点lk,利用时间序列采用镜像对称延拓方法处理时间序列信号端点,得到左右两端极值点(τ0,x0)、(τm+1,xm+1);令k分别为0和m-1,进而利用公式(1)求出l1与lm的值,采用akima插值函数(三次样条插值函数)对所有的lk拟合得到基线信号l1(t);步骤23,对轴承的振动信号数据xt进行分解获取pr1。定义h1(t)为原信号xt与基线信号l1(t)差值,也即h1(t)=xt-l1(t),进行基准控制点lk+1判定,当基线控制点lk+1≠0,则h1(t)是一个固有旋转分量,输出h1(t),并令pr1=h1(t);如果lk+1=0,则将h1(t)作为原始数据(将h1(t)赋值给xt),重复上述步骤s21-s23,直至h1k(t)为一个固有旋转分量,并令h1k(t)=pr1;步骤24,将pr1从原信号xt分离出来得到r1(t),也即r1(t)=xt-pr1。步骤25,将r1(t)作为新的给定信号(也即将r1(t)赋值给xt),重复步骤s21-s24,循环n-1次之后,直到rn(t)为一单调函数或常函数,最终,原始信号xt被分解为公式(2)所示的n个pr分量和一个残余项r1(t)之和。需要说明的是,在步骤s20中,需要利用改进的固有时间尺度分解方法分别对每种故障状态下的轴承的振动信号数据xt进行分解,以获取得到若干固有旋转分量,其中,每个轴承的振动信号数据xt都可以被分解成多个固有旋转分量。具体地,在步骤s20中,在对每种故障状态下的轴承的振动信号数据xt进行分解时,可以先将xt进一步划分为至少一个区间长度为特定点数的子数据,分别对每个子数据进行分解,得到多个固有旋转分量,并根据公式(3)计算所述固有旋转分量的互相关系数:其中,e为数学期望,a和b表示原信号的横坐标和纵坐标值,μa和μb表示a、b的均值,σa和σb表示a、b的标准差,相关系数ρab越大,pr分量与原信号越相关;通过互相关系数选取表征故障主要信息的有效固有旋转分量并计算其模糊熵值(也即步骤s30)。再接着,执行步骤s30,利用故障特征信号处理模块23计算所述旋转分量的模糊熵值,包括以下步骤:步骤s31、将iitd分解得到的能够表征故障主要信息的有效pr分量(下面公式中以u来表示)作为模糊熵计算的时间序列,并处理为公式(4)所示的m维向量换句话说,对于给定的n点时间序列{u(i):1≤i≤n},处理后得到公式(4)所示的m维向量其中,表示从第i个点开始连续m个u的值减去均值u0(i)。步骤s32、根据公式(4)计算矢量和两者对应元素间差值的最大值:其中:i,j=1,2…n-m;i≠j;步骤s33、根据模糊函数定义和的相似度其中为指数函数,n和r为边界梯度和宽度;步骤s34、定义模糊熵为:其中,当n为有限数时,模糊熵表达式可以定义下式:其中,式(10)中,模糊熵的值不仅与数据长度n有关,还与参数m、r和n有关,嵌入维数m一般选择1或2,模糊函数的梯度n,相似容限r取0.1~0.5sd(sd是原数据xt的标准差)。作为示例,n可以取2048,n可以取2,m可以取2,r可以取0.2sd。需要说明的是,在步骤s30中,可以获取每种故障状态下对应的有效固有旋转分量的模糊熵。再接着,执行步骤s40,故障特征信号处理模块23利用计算出的所述模糊熵值构建特征向量,以组成特征矩阵,可以将其划分为训练集和测试集,作为轴承故障分类器模型的训练数据和测试数据。再接着,执行步骤s50、轴承故障分类模块24利用所述特征矩阵对轴承故障分类器模型进行训练。具体地,将计算得到的轴承故障模糊熵数据构建成特征矩阵,划分为训练集和测试集,输入到随机森林分类器中进行轴承故障预测分类。利用bootstrap法重采样生成子样本集,通过随机抽取特征向量f(f≤f)作为当前数非叶子节点的分类特征,构建成决策树,不做剪枝处理并按照不纯度最小原则充分生长,直到决策树的属性生长到叶子节点或完全被使用,综合决策树预测结果,最后随机森林使用公式(11)进行投票得到分类结果。其中,随机森林算法包括以下步骤:步骤s51:生成子样本集。随机森林利用bootstrap法重采样有放回无权重地从原始训练集中抽取大约t个(例如训练集的63.2%),每一个子样本集对应一个决策树。未被抽中的数据称为袋外数据(out-of-bag,oob),oob数据用来评估分类器的正确率,且对异常数据具有抗干扰能力,这样可以避免随机森林中的决策树产生局部最优解,使分类更准确。步骤s52:生成每颗决策树。利用步骤s51中子样本集生成的决策树。在树的每个非叶子节点处,从f个特征向量中随机抽取f(f≤f)个特征向量作为当前节点的分类特征集,其中f代表训练集特征向量个数。根据经验[12]f取的向下整数,即根据节点不纯度最小原则,从f个特征向量中选出一个特征β作为当前节点的分类属性。步骤s53:决策树生长。特征β把节点分成2个分支,然后从剩下的特征中寻找分类效果最好的特征,最终决策树按照不纯度最小原则充分生长,且不剪枝处理,直到决策树的属性生长到叶子节点或完全被使用。步骤s54:随机森林分类。通过构建的决策树对测试样本预测后分类,分类的标签来自于所有决策树的综合。随机森林使用投票原则,即:其中,t表示森林中决策树的数目,i(*)表示示性函数,表示决策树hi对类别c的分类结果,表示树的叶子节点数。最后,可以利用训练好的所述轴承故障分类器模型对待分类的轴承故障振动信号进行分类(也即步骤s50),以判定轴承的故障状态。请参阅图3,本发明的实施例还提供一种图3示出了实现轴承故障分类方法的分类系统,所述计轴承故障分类系统2包括轴承试验装置21,用于对不同故障状态的轴承进行试验;信号采集模块22(其中图2示出了信号采集模块22的一种示例流程图),所述信号采集模块22的振动加速度传感器设置于所述轴承试验装置21的机罩上,用于采集不同故障状态下的轴承振动信号数据;故障特征信号处理模块23,用于将所述轴承的振动信号数据分解成若干旋转分量,计算所述旋转分量的模糊熵值,利用计算出的所述模糊熵值构建特征向量,以组成特征矩阵;以及轴承故障分类模块24,与所述故障特征信号处理模块23连接,用于利用所述特征矩阵对轴承故障分类器模型进行训练,并利用训练好的所述轴承故障分类器模型对待分类的轴承故障振动信号进行分类。需要说明的是,在本实施例中,上述轴承试验装置21,信号采集模块22,故障特征信号处理模块23及轴承故障分类模块24的功能详见上文的方法部分中的各步骤,在此不做赘述。请参阅图4,在本实施例中,所述轴承试验装置21主要包括轴承试验机211以及分别与轴承试验机211连接的加载站212,润滑站213和冷却站214等配套设备。需要说明的是,上述所述计轴承故障分类系统2中的故障特征信号处理模块23及轴承故障分类模块24,实际实现时可以全部或部分集成到一个物理实体上,也可以物理上分开。且这些单元可以全部以软件通过处理元件调用的形式实现;也可以全部以硬件的形式实现;还可以部分单元通过处理元件调用软件的形式实现,部分单元通过硬件的形式实现。此外这些单元全部或部分可以集成在一起,也可以独立实现。这里所述的处理元件可以是一种集成电路,具有信号的处理能力。在实现过程中,上述方法的部分或全部步骤,或以上故障特征信号处理模块23及轴承故障分类模块24可以通过处理器元件中的硬件的集成逻辑电路或者软件形式的指令完成。需要说明的是,如图5所示,本实施例的轴承故障分类方法及处理系统还可以通过一电子设备3来实现上述的故障特征信号处理模块23及轴承故障分类模块24的功能,所述电子设备3包括相互连接的存储器33、处理器31及通信器32,所述存储器33存储有计算机程序,该程序被所述处理器31执行时实现所述轴承故障分类方法。上述的处理器31可以是通用处理器,包括中央处理器(centralprocessingunit,简称cpu)、网络处理器(networkprocessor,简称np)等;还可以是数字信号处理器(digitalsignalprocessing,简称dsp)、专用集成电路(applicationspecificintegratedcircuit,简称asic)、现场可编程门阵列(field-programmablegatearray,简称fpga)或者其他可编程逻辑器件、分立门或者晶体管逻辑器件、分立硬件组件;上述的存储器33可能包含随机存取存储器(randomaccessmemory,简称ram),也可能还包括非易失性存储器(non-volatilememory),例如至少一个磁盘存储器。需要说明的是,上述存储器33中的计算机程序可以通过软件功能单元的形式实现并作为独立的产品销售或使用时,可以存储在一个计算机可读存储介质中。基于这样的理解,本发明的技术方案本质上或者说对现有技术做出贡献的部分或者该技术方案的部分可以软件产品的形式体现出来,该计算机软件产品存储在一个存储介质中,包括若干指令用以使得一台计算机设备(可以是个人计算机,电子设备,或者网络设备等)执行本发明各个实施例方法的全部或部分步骤。下面将结合一个具体实施例来说明本发明的实施例的所述轴承故障分类方法。为了体现本发明提出方法的有效性和可行性,采用试验台现场采集的数据进行验证。数据采集来自本单位的航空发动机轴承试验台(也即轴承试验装置21),如图4所示。实验轴承采用nsk的nu1010型号单列圆柱滚子轴承,该试验轴承的基本参数见表1。表1试验轴承基本参数因轴承结构和加工方式的限制,采用不同的加工方式完成轴承不同故障类型的加工。为满足实验需求,利用激光打标机和线切割加工出内圈、外圈、滚动体三种轴承故障。内圈故障例如可使用大族激光生产的型号ylp-f10的激光打标机在内圈的内表面加工形成非贯通型的小尺寸方形点蚀损伤故障(当然也可以是矩形故障或者圆形故障);滚动体故障例如可使用北京阿奇夏米尔生产的型号fw1u中走丝线切割机床在所述滚动体上沿轴向分布加工形成一细条形贯通槽;外圈故障例如也可使用北京阿奇夏米尔生产的型号fw1u中走丝线切割机床在所述外圈的与滚动体接触的表面上沿轴向分布加工形成一细条形贯通槽,表2示出了该具体实施例采用的三种轴承故障的故障尺寸表,可以理解的是,所述加工故障尺寸可以根据实际需要进行调整。表2加工故障尺寸表序号部件故障类型长、宽、深故障分布1外圈贯通型9mm×0.2mm×0.1mm1处2内圈非贯通型1mm×1mm×0.1mm1处3圆柱滚子贯通型9mm×0.2mm×0.1mm1处如图2所示,利用lmstest.lab软件在电脑上采集额定轴向载荷四种故障状态三种转速振动信号,3向和单向振动加速度传感器分别布置在轴承试验机211的机罩的侧壁和上表面。试验工况设定:采样频率为20480hz。转速为3000rpm,轴向载荷为2kn,定转速每类故障状态采集长度为634880。需要说明的是,在信号采集时,可以针对单种故障状态下轴承进行测试,也可以针对复合型故障状态下轴承进行测试,在该具体实施例中,分别是针对正常、内圈故障、外圈故障、滚动体故障、内圈滚动体复合型故障及外圈滚动体复合型故障等故障状态下轴承进行测试,具体地,当采集内圈故障状态下的轴承振动信号时,内圈的大圆表面加工有表2所示的方形点蚀损伤,而轴承的外圈和滚动体保持正常状态;当采集外圈故障状态下的轴承振动信号时,外圈的小圆表面加工有表2所示的细条形贯通槽故障,而轴承的内圈和滚动体保持正常状态;当采集滚动体故障状态下的轴承振动信号时,滚动体的表面加工有表2所示的沿轴向分布的细条形贯通槽故障,而轴承的外圈和内圈保持正常状态;当采集内圈滚动体复合型故障状态下的轴承振动信号时,内圈的大圆表面加工有表2所示的方形点蚀损伤,滚动体的表面加工有表2所示的沿轴向分布的细条形贯通槽,而轴承的外圈保持正常状态;当采集外圈滚动体复合型故障状态下的轴承振动信号时,外圈的小圆表面加工有表2所示的细条形贯通槽,滚动体的表面加工有表2所示的沿轴向分布的细条形贯通槽,而轴承的内圈保持正常状态。共采集到轴承试验机211表面3个方向(x、y、z)的振动加速度信号,经过数据分析发现采集到的y方向的振动加速度信号受到的干扰小,更符合滚动轴承故障的实际数据特点,选取y方向采集到的信号作为处理数据。将采集的数据划分为45个区间,每个区间长度为1000的点,对信号进行iitd分解;得到若干pr分量,根据互相关系数计算公式(3)所述固有旋转分量的互相关系数,通过相关系数选取有效的pr分量,计算其模糊熵值,即式(10)。经计算,信号分解得到前5个pr分量满足互相关性设定阈值,取前5个pr分量构建特征矩阵,6种故障状态经过计算,每种工况下随机选择其中30组作为训练集,另外15组作为测试集。最终形成(6×45)×5即维数为270×5的数据集,将数据集输入到构建好的随机森林分类器模型中用来验证本发明中的轴承故障诊断分类方法,为了体现随机森林分类方法的准确性,使用同一模糊熵数据集训练支持向量机(supportvectormachine,svm)、反向传播神经网络(backpropagationneuralnetwork,bpnn)进行对比,三者分类输出结果如图6a-6c所示,三者分类的比对结果如表3所示,其中,在图6a-6c中,纵坐标(类别标签)中类别1-6分别代表滚动体故障、内圈故障、外圈故障、正常、内圈滚动体复合型故障,外圈滚动体复合型故障。表3不同分类器的分类输出结果表从图6a-6c,以及表3的数据可以看出,本发明中的轴承故障诊断分类方法相比于svm,bpnn具有更好的准确性。虽然本具体实施例只示出了内圈滚动体复合型故障,外圈滚动体复合型故障两种复合型故障,但可以理解的是,本实施例的技术方案同样可以适用于轴承的其他复合型故障类型的分类。综上所述,本发明的轴承故障分类方法及系统,是基于改进的itd结合随机森林的轴承故障分类方法及系统,可将改进的itd和模糊熵及随机森林分类器进行融合并发挥各自优势,改进的itd解决了前述的itd分解的端点效应和波形失真问题;本发明的轴承故障分类方法及系统,将模糊熵作为iitd特征提取后的特征选择依据,解决了近似熵、样本熵易受数据波动影响和基线漂移的问题;利用本发明的轴承故障分类方法及系统,对于多分类问题,随机森林分类器可以克服传统分类器特征选择困难、分类精度低的问题;本发明的轴承故障分类方法及系统不仅能够针对轴承的单种故障进行分类,而且还可以对轴承的复合型故障进行分类;经试验数据验证,本发明提出的将iitd、模糊熵与随机森林相结合的轴承故障分类模型,在小样本数据和微弱故障信号情况下仍然能准确判断出滚动轴承故障类别。在本文的描述中,提供了许多特定细节,诸如部件和/或方法的实例,以提供对本发明实施例的完全理解。然而,本领域技术人员将认识到可以在没有一项或多项具体细节的情况下或通过其他设备、系统、组件、方法、部件、材料、零件等等来实践本发明的实施例。在其他情况下,未具体示出或详细描述公知的结构、材料或操作,以避免使本发明实施例的方面变模糊。在整篇说明书中提到“一个实施例(oneembodiment)”、“实施例(anembodiment)”或“具体实施例(aspecificembodiment)”意指与结合实施例描述的特定特征、结构或特性包括在本发明的至少一个实施例中,并且不一定在所有实施例中。因而,在整篇说明书中不同地方的短语“在一个实施例中(inoneembodiment)”、“在实施例中(inanembodiment)”或“在具体实施例中(inaspecificembodiment)”的各个表象不一定是指相同的实施例。此外,本发明的任何具体实施例的特定特征、结构或特性可以按任何合适的方式与一个或多个其他实施例结合。应当理解本文所述和所示的发明实施例的其他变型和修改可能是根据本文教导的,并将被视作本发明精神和范围的一部分。还应当理解还可以以更分离或更整合的方式实施附图所示元件中的一个或多个,或者甚至因为在某些情况下不能操作而被移除或因为可以根据特定应用是有用的而被提供。另外,除非另外明确指明,附图中的任何标志箭头应当仅被视为示例性的,而并非限制。此外,除非另外指明,本文所用的术语“或”一般意在表示“和/或”。在术语因提供分离或组合能力是不清楚的而被预见的情况下,部件或步骤的组合也将视为已被指明。如在本文的描述和在下面整篇权利要求书中所用,除非另外指明,“一个(a)”、“一个(an)”和“该(the)”包括复数参考物。同样,如在本文的描述和在下面整篇权利要求书中所用,除非另外指明,“在…中(in)”的意思包括“在…中(in)”和“在…上(on)”。本发明所示实施例的上述描述(包括在说明书摘要中所述的内容)并非意在详尽列举或将本发明限制到本文所公开的精确形式。尽管在本文仅为说明的目的而描述了本发明的具体实施例和本发明的实例,但是正如本领域技术人员将认识和理解的,各种等效修改是可以在本发明的精神和范围内的。如所指出的,可以按照本发明所述实施例的上述描述来对本发明进行这些修改,并且这些修改将在本发明的精神和范围内。本文已经在总体上将系统和方法描述为有助于理解本发明的细节。此外,已经给出了各种具体细节以提供本发明实施例的总体理解。然而,相关领域的技术人员将会认识到,本发明的实施例可以在没有一个或多个具体细节的情况下进行实践,或者利用其它装置、系统、配件、方法、组件、材料、部分等进行实践。在其它情况下,并未特别示出或详细描述公知结构、材料和/或操作以避免对本发明实施例的各方面造成混淆。因而,尽管本发明在本文已参照其具体实施例进行描述,但是修改自由、各种改变和替换意在上述公开内,并且应当理解,在某些情况下,在未背离所提出发明的范围和精神的前提下,在没有对应使用其他特征的情况下将采用本发明的一些特征。因此,可以进行许多修改,以使特定环境或材料适应本发明的实质范围和精神。本发明并非意在限制到在下面权利要求书中使用的特定术语和/或作为设想用以执行本发明的最佳方式公开的具体实施例,但是本发明将包括落入所附权利要求书范围内的任何和所有实施例及等同物。因而,本发明的范围将只由所附的权利要求书进行确定。当前第1页12