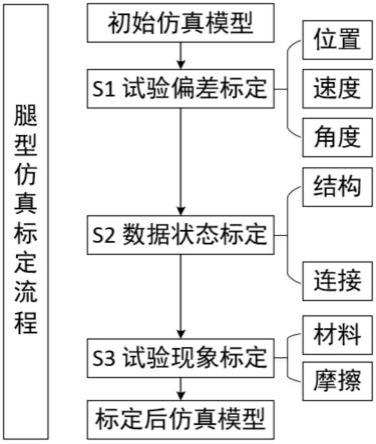
一种行人apli腿型碰撞模型的仿真标定方法
技术领域
1.本发明涉及汽车技术领域,具体的说是一种行人apli腿型碰撞模型的仿真标定方法。
背景技术:2.中国新车评价规程(c-ncap)确定在2021年实施新的测试腿型冲击器(apli),与flex-pli旧腿型相比,新腿型在形状,材质和结构等方面有较大改变,质量分布更符合人体特征。apli腿型相较于flex-pli腿型的变化主要体现在三个方面,腿型重量的变化、上腿型参考指标的变化以及膝关节剪切位移考核指标的变化。apli比flex-pli增重88.6%,且集中在上部,大腿伤害指标考核加入评分,使腿型开发难度增加。同时腿型在行人保护整体评分中的比重也大幅度提升,2018年c-ncap行人保护总分15分,腿型占3分,20%;2021年c-ncap行人保护总分15分,腿型占5分,33.33%。由于缺少针对apli腿型的开发经验,使得apli腿型碰撞仿真精度较低,大多车辆主机厂依靠试验对腿型伤害做出评价,行人保护腿型试验涉及的零部件较多(发罩、外饰、大灯等),腿型伤害不达标导致的零部件设计变更,模具更改在开发周期及试验成本上均会造成较大的浪费。
技术实现要素:3.本发明提供了一种行人apli腿型碰撞模型的仿真标定方法,能提升仿真精度,正向指导车辆设计,降低对行人腿部伤害,提高试验一次性通过率,降低试验成本,解决了现有依靠试验对腿型伤害做出评价,腿型伤害不达标导致的零部件设计变更,模具更改在开发周期及试验成本上均会造成较大的浪费的问题。
4.本发明技术方案结合附图说明如下:
5.一种行人apli腿型碰撞模型的仿真标定方法,包括以下步骤:
6.步骤一、对试验偏差进行标定;
7.步骤二、对数据状态进行标定;
8.步骤三、对试验现象进行标定。
9.进一步地,所述步骤一的具体方法如下:
10.11)根据行人apli腿型碰撞试验的记录,调整行人apli腿型的初始位置设置;
11.12)根据行人apli腿型碰撞试验的记录,调整行人apli腿型的初始速度设置;
12.13)根据行人apli腿型碰撞试验的记录,调整行人apli腿型的初始角度设置。
13.进一步地,所述步骤11)的具体方法如下:
14.将行人apli腿型的仿真的初始设置调整至与行人apli腿型的碰撞试验的位置完全一致,即将仿真中的初始位置调整到第一位置16。
15.进一步地,所述步骤12)的具体方法如下:
16.仿真的行人apli腿型碰撞的初始速度调整至与行人apli腿型的碰撞试验的初始速度完全一致。
17.进一步地,所述步骤13)的具体方法如下:
18.仿真的行人apli腿型的初始角度调整到第一贴纸12与第二贴纸13的连线;所述第一贴纸12与第二贴纸13贴在腿型碰撞器11侧面的中垂线上,第一贴纸12与第二贴纸13的中心连线垂直于地面。
19.进一步地,所述步骤二的具体方法如下:
20.21)对车辆的结构完整性进行标定;
21.22)对车辆中部件之间连接的合理性进行标定。
22.进一步地,所述步骤21)的具体方法如下:
23.在设计变更及时更新、变厚度零件需要拆分成不同厚度定义的多个零件,以及电气件仿真模型的补充。
24.进一步地,所述步骤22)的具体方法如下:
25.螺栓连接采用node-rigid-body进行刚性连接,卡接连接依靠物理结构复现进行柔性连接。
26.进一步地,所述步骤三的具体方法如下:
27.31)根据试验现象-仿真及试验腿型的弯折程度对比,调整泡沫的应力应变曲线缩放系数;
28.32)根据试验现象-结构的失效位置,调整材料失效塑性应变参数epfail,同时局部细化网格,整体网格基本尺寸为5mm,易产生应力集中及断裂失效位置网格基本尺寸为2mm;
29.33)根据试验现象-腿型与车辆接触相对滑动情况,调整静摩擦系数fs及动摩擦系数fd。
30.进一步地,所述步骤31)中,调整泡沫的应力应变曲线缩放系数sfo,调整范围1.0-2.0,直至仿真动画中行人apli腿型的弯折程度与试验录像中腿的弯折程度一致;
31.所述步骤32)中,调整材料失效塑性应变参数epfail,调整范围0-1;
32.所述步骤33)中,调整静摩擦系数fs和动摩擦系数fd,调整范围0-0.5,直至仿真动画中行人apli腿型与车辆之间的相对滑行量与试验录像中腿与车辆之间的相对滑行量一致。
33.本发明的有益效果为:
34.1)本发明系统地提出了影响apli腿型仿真精度的因素,解耦多影响因子标定的优先级;
35.2)本发明详细描述了各仿真精度影响因子对仿真精度提升的敏感度以及标定方法;
36.3)本发明提升了仿真精度,正向指导车辆设计,降低对行人腿部伤害,提高试验一次性通过率,降低试验成本。
附图说明
37.为了更清楚地说明本发明实施例的技术方案,下面将对实施例中所需要使用的附图作简单地介绍,应当理解,以下附图仅示出了本发明的某些实施例,因此不应被看作是对范围的限定,对于本领域普通技术人员来讲,在不付出创造性劳动的前提下,还可以根据这
些附图获得其他相关的附图。
38.图1为本发明所述一种行人apli腿型碰撞模型的仿真标定方法的流程图;
39.图2为一种贴纸法监测腿型碰撞器试验偏差示意图;
40.图3为一种结构完整性标定流程图;
41.图4为一种连接仿真方法示意图。
42.图中:
43.10、试验车辆;11、apli腿型冲击器;12、第一贴纸;13、第二贴纸;14、车辆与腿型碰撞的理论第一接触点;15、第三贴纸;16、车辆与腿型碰撞的实际第一接触点。
具体实施方式
44.下面将结合本发明实施例中的附图,对本发明实施例中的技术方案进行清楚、完整地描述,显然,所描述的实施例仅是本发明一部分实施例,而不是全部的实施例。基于本发明中的实施例,本领域普通技术人员在没有做出创造性劳动前提下所获得的所有其他实施例,都属于本发明保护的范围。
45.实施例一
46.参阅图1,一种行人apli腿型碰撞模型的仿真标定方法,包括以下步骤:
47.步骤一、对试验偏差进行标定;
48.试验偏差主要体现在试验时腿型碰撞器的打击位置、打击速度和打击角度的偏差,其中打击位置偏差对腿型评价指标的影响较大。在apli腿型试验时,车处于静止状态,腿型安装在距离车辆有一定距离的发射器上,设定位置、速度和角度,因腿型冲击器在发射后,接触车辆之前会在空中无约束运动一段时间,因此在接触车辆的一刻,位置、速度和角度都会出现一定偏差;而仿真模型中腿型的初始位置为紧贴车辆,无自由运动阶段,因此无偏差。
49.为标定仿真模型,排除因试验偏差对仿真精度带来的影响,在仿真标定时需考虑试验偏差。应用贴纸法监测试验时腿型的打击偏差,见图2,试验前在腿型碰撞器11上设置第一贴纸12、第二贴纸13和第三贴纸15;其中,所述第一贴纸12和第二贴纸13贴在腿侧面的中垂线上,两点中心连线垂直于地面;第一贴纸12和第二贴纸13用以通过高速摄像机监测腿型冲击器在试验过程中的角度偏差;在试验完成后的高速摄像上,在刚接触车辆的那一刻,截图,连接第一贴纸12,第二贴纸13的中心做一条直线,再做一条垂直于地面的线,就可以测量出角度偏差;腿型冲击器的正面设置第三贴纸15,车辆上涂染料,在碰撞过程中染料可标记到贴纸15上,用以记录车辆与腿型碰撞的实际第一接触点16的位置,通过测量车辆与腿型碰撞的实际第一接触点16与车辆与腿型碰撞的理论第一接触点14的距离确定位置偏差。
50.综上,仿真的初始位置:腿型碰撞的理论第一接触点14;初始速度:40km/h;初始角度:腿接触到车的那一刻与地面垂直
51.试验的初始位置:车辆与腿型碰撞的实际第一接触点16;初始速度:传感器检测值;初始角度:腿接触到车的那一刻第一贴纸12和第二贴纸13的连线。
52.仿真标定具体步骤如下:
53.11)根据行人apli腿型碰撞试验的记录,将行人apli腿型的仿真的初始设置调整
至与行人apli腿型的碰撞试验的位置完全一致,即将仿真中的初始位置调整到第一位置16。
54.12)根据行人apli腿型碰撞试验的记录,将仿真的行人apli腿型碰撞的初始速度调整至行人apli腿型的碰撞试验的初始速度完全一致。
55.13)根据行人apli腿型碰撞试验的记录,将仿真的行人apli腿型的初始角度调整到第一贴纸12与第二贴纸13的连线;所述第一贴纸12与第二贴纸13贴在腿型碰撞器11侧面的中垂线上,第一贴纸12与第二贴纸13的中心连线垂直于地面;
56.通过上述方法可以排除试验打击偏差对仿真精度带来的影响。
57.步骤二、对数据状态进行标定;
58.具体如下:
59.数据状态偏差主要体现在结构完整性和连接合理性;
60.21)对车辆的结构完整性进行标定;
61.研发阶段为提升计算效率,仿真模型中往往会忽略一些电气件如雷达、线束等结构的建模,且存在试验车有一些发生设计变更的部件,仿真模型中未及时更新的现象,这些部件的缺失和结构变化都会对仿真精度产生较大影响。结构完整性标定主要体现在设计变更及时更新、变厚度零件需要拆分成不同厚度定义的多个零件,以及雷达、摄像头、线束等电气件仿真模型的补充,如图3。其中,变厚度零件需要拆分成不同厚度定义的多个零件按照不同厚度进行拆分,比如一个零件一端是2.0mm,中间是2.1mm,另一端是2.2mm,按照厚度拆分成3个部分,部分与部分之间共节点。
62.22)对车辆中部件之间连接的合理性进行标定。
63.螺栓连接采用node-rigid-body进行刚性连接,卡口即卡爪等卡接连接依靠物理结构复现进行柔性连接而不建立多余的刚性连接,见图4。
64.步骤三、对试验现象进行标定。
65.试验现象标定主要是指材料软硬程度、材料失效和摩擦滑动的复现;
66.具体如下:
67.31)材料硬化:腿型试验涉及的大部分为塑料件,塑料件结构复杂,稳定性较差,受工艺影响较大,存在加工硬化等现象,利用样件标定出来的仿真应力应变曲线与实际结构表现出来的材料特性存在一定差异,该差异对仿真精度影响很大,主要体现在泡沫的材料特性上;
68.根据试验现象-仿真及试验腿型的弯折程度对比,调整泡沫的应力应变曲线缩放系数sfo,调整范围1.0-2.0,直至仿真动画中行人apli腿型的弯折程度与试验录像中腿的弯折程度一致;
69.32)材料失效:apli腿型冲击能量较大,在碰撞过程中会导致一些塑料材料的失效,而仿真模型中材料的失效往往与实际试验存在出入,主要受失效应变参数及网格质量的影响,材料的失效与否对仿真精度影响很大,主要体现在前保格栅的失效特性上;
70.根据试验现象-结构的失效位置,调整材料失效塑性应变参数epfail(187号材料卡),调整范围0-1;同时局部细化网格,整体网格基本尺寸为5mm,易产生应力集中及断裂失效位置网格基本尺寸为2mm;直至仿真动画中车辆产生材料失效的位置和程度与试验录像中车辆的损伤程度一致;
71.33)摩擦系数:腿型与车辆表面存在滑动摩擦,摩擦系数的设定对仿真精度存在一定的影响;
72.根据试验现象-腿型与车辆接触相对滑动情况,调整静摩擦系数fs(static friction)及动摩擦系数fd(dynamic friction);调整范围0-0.5,直至仿真动画中行人apli腿型与车辆之间的相对滑行量与试验录像中腿与车辆之间的相对滑行量一致。
73.综上,通过步骤一、步骤二、步骤三完成对apli腿型仿真分析模型的标定,使仿真精度达到85%以上,用于正向指导设计,更好的开发行人保护-apli腿型安全性能,降低试验成本。
74.实施例二
75.以某车型的y0位置apli腿型打击试验数据为例,对仿真模型标定过程及影响因子进行说明。初始仿真精度见表1,s1试验偏差标定后仿真精度见表2,s21结构完整性标定后仿真精度见表3,s22连接正确性标定后仿真精度见表4,材料特性标定后仿真精度见表5,s32摩擦系数标定后仿真精度见表6。
76.表1 apli初始仿真精度
[0077][0078]
表2 apli试验偏差标定后仿真精度
[0079][0080]
表3 apli结构完整性标定后仿真精度
[0081][0082]
表4 apli连接正确性标定后仿真精度
[0083][0084]
表5 apli材料特性标定后仿真精度
[0085][0086]
表6 apli摩擦标定后仿真精度
[0087][0088]
通过该发明的标定流程及方法,使apli腿型碰撞仿真模型的数值精度提升至90%以上,曲线拟合精度提升至85%以上,可用于车辆的行人保护性能正向开发设计。
[0089]
注意,上述仅为本发明的较佳实施例及所运用技术原理。本领域技术人员会理解,本发明不限于这里所述的特定实施例,对本领域技术人员来说能够进行各种明显的变化、重新调整和替代而不会脱离本发明的保护范围。因此,虽然通过以上实施例对本发明进行了较为详细的说明,但是本发明不仅仅限于以上实施例,在不脱离本发明构思的情况下,还可以包括更多其他等效实施例,而本发明的范围由所附的权利要求范围决定。