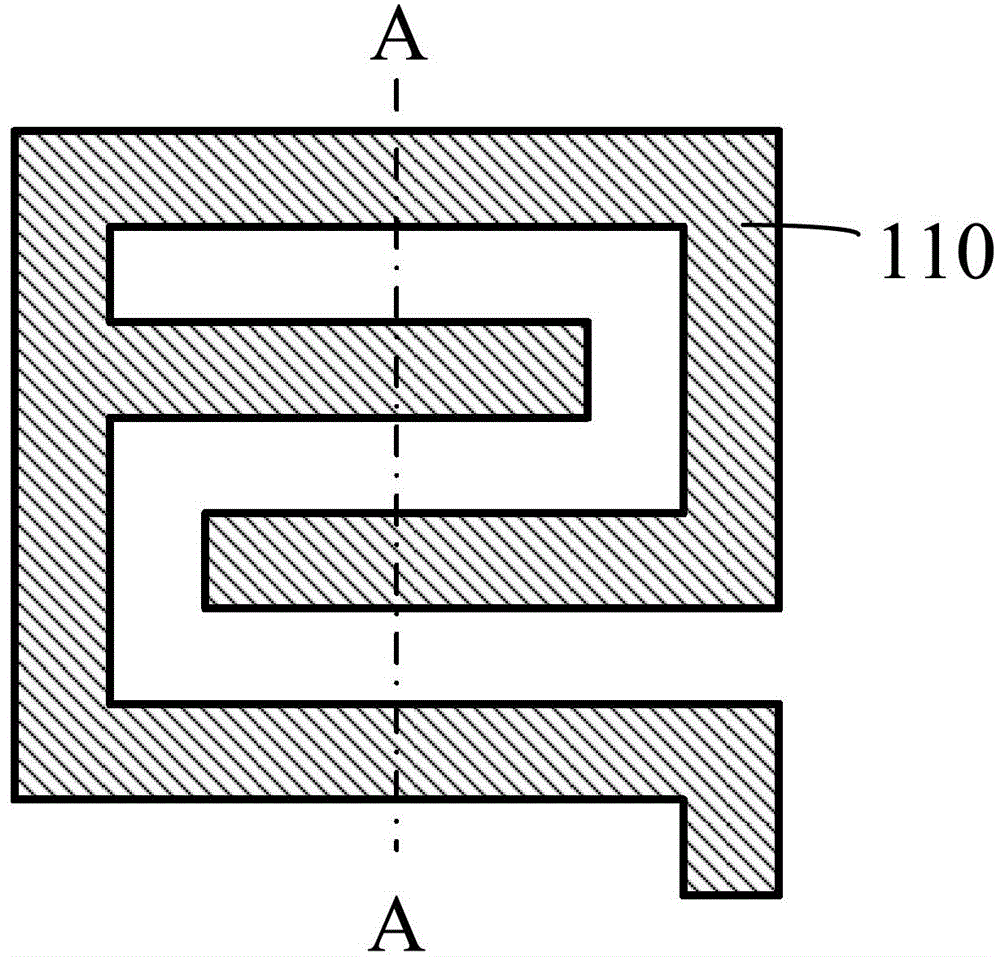
本发明涉及半导体工艺领域,特别涉及一种测试线的形成方法。
背景技术:在半导体后段工艺中,通常会在晶圆表面一定空白区域中制作一定长度的测试线。该测试线的制作材料与半导体器件功能区中金属线(例如金属互连线)的制作材料相同,其作用是代替功能区中的金属线接受电阻值的检测,根据检测出的电阻值计算出测试线的电阻率,从而得到功能区金属线的电阻率。如果该测试线的长度较小,检测到该测试线的电阻值不稳定,得到该测试线的电阻率准确度较低。为此,通常需要将测试线的长度设置得较大。但是,随着半导体集成化程度的提高,半导体设计对晶圆表面的利用率越来越高,导致能够用来制作测试线的空白区域面积越来越小。现有测试线的制作方法通常是利用光刻工艺来实现,如公开号为CN101894756A的中国发明专利申请提供了一种“形成沟槽的方法、形成金属连线的方法、光刻方法及设备”,但是受限于光刻工艺分辨率的限制,利用光刻工艺无法在面积较小的区域中制作出长度较大的测试线。为此,需要一种新的测试线的制作方法,以便能够在面积较小的区域中制作长度较大的测试线。
技术实现要素:本发明解决的问题是提供一种测试线的形成方法,以便在面积较小的区域上制作出长度较大的测试线。为解决上述问题,本发明提供一种测试线的形成方法,包括:提供具有测试材料层的衬底;在所述测试材料层上形成第一测试图案;在所述第一测试图案的侧壁形成第一侧墙;去除所述第一测试图案,形成第一闭合图案;在所述第一闭合图案上形成第一缺口,形成第二测试图案;在所述第二测试图案的侧壁形成第二侧墙;去除所述第二测试图案,形成第二闭合图案;在所述第二闭合图案上形成第二缺口,形成待转移测试图案;将所述待转移测试图案转移到所述测试材料层,形成测试线。可选的,所述测试材料层的制作材料包括以下一种或多种的任意组合:铝、铜、钼、钽、钛和钨。可选的,所述第一侧墙或者所述第二侧墙的制作材料包括多晶硅、氧化硅和氮化硅中的至少一种。可选的,所述第一侧墙或者所述第二侧墙的厚度大于或者等于100埃且小于或者等于300埃。可选的,采用干法蚀刻或者选择性湿法蚀刻去除所述第一测试图案或者所述第二测试图案。可选的,所述第一缺口和第二缺口位于所述测试材料层上相同位置。与现有技术相比,本发明的技术方案具有以下优点:本发明所提供的测试线的形成方法通过先形成第一测试图案,从而完成测试线轮廓的设置,再在第一测试图案的侧壁形成第一侧墙,然后去除第一测试图案,并在第一侧墙上形成第一缺口,使得第一侧墙变成第二测试图案,再经过一次侧墙形成和缺口形成,最终形成具有较大长度的待转移测试图案绕线图形,而通过将该待转移测试图案转移到测试材料层形成测试线,所形成的测试线在所处区域的面积上,具有较大长度,而长度较大的测试线有利用后续准确地测试出该测试线制作材料的电阻率,从而有利于得到功能区金属线准确的电阻率。进一步,本发明可选方案中,将第一缺口和第二缺口设置在位于所述测试材料层上相同位置,使得在形成第二缺口的位置比较容易找准,从而使得工艺更简单,并且最终形成的测试图案也比较规则整齐。附图说明图1至图14为本发明实施例示意图。具体实施方式现有测试线的制作方法通常是以光刻工艺,通过曝光显影等步骤形成相应的测试线。受限于光刻工艺分辨率的影响,用光刻工艺形成的测试线的线宽通常在400埃以上,并且两段平行测试线之间的间距在800埃以上。因而用现有方法来制作测试线,对晶圆表面积的面积利用率低,无法在面积较小的区域中制作出长度较大的测试线。本发明提供一种测试线的制作方法,通过在测试材料层上形成第一测试图案,然后在所述测试图案侧壁形成第一侧墙,之后去除所述测试图案,并在第一侧墙上形成一个缺口,形成第二测试图案,再以相类似的步骤重复一次,最终形成,形成待转移测试图案,再将所述待转移测试图案转移到所述测试材料层,形成测试线。这样,就能够在较小的面积中制作出长度较大的测试线。为使本发明的上述目的、特征和优点能够更为明显易懂,下面结合附图对本发明的具体实施例做详细的说明。应当理解,当一结构或层被称为在另一层“上”时,它可以直接在另一层或结构“上”,或可以存在插入结构。应当理解,尽管实施例中使用术语第一、第二、第三等来描述各个结构、层或部分,但是这些结构、层或部分不应该受这些术语限制。同时,附图描述了本发明的某些实施例,这些附图是本发明的理想化实施例的示意图。照此,将预想由于图例形状的变化例如制造工艺或容差的变化。因此,本发明的实施例不应该认为限于在此所示的区域的特定形状,而是包括所得的形状例如由制造的偏差。另外,除非另外限定,在此使用的所有术语(包括技术和科学术语)具有与属于本发明的技术领域的普通技术人员通常理解的相同意思。还应当理解,如在通常使用的词典中定义的那些术语应该解释为具有符合相关技术的环境中的意思,且不被解释理想化或过度地形式感知。本实施例提供一种测试线的形成方法,包括步骤S11至步骤S19。需要说明的是,本实施例以S11至步骤S19命名各步骤是为了区分和便于说明各步骤,但并不限定各步骤的先后顺序,在不同实施例中,某些步骤顺序可调整。以下将对各步骤加以说明,请参考图1至图13。步骤S11,请参考图1,本实施例提供具有测试材料层120的衬底。图1中未显示出衬底而仅显示出位于衬底上的测试材料层120。该未显示出的衬底可以是半导体衬底,例如是单晶硅衬底、多晶硅衬底或者绝缘体上硅衬底(SOI)。另外,该衬底也可以是绝缘衬底等其它衬底。本实施例中该测试材料层120形成在该衬底用于制作测试线的区域上。测试材料层120的制作材料为导电材料,例如可以是掺杂多晶硅或者是掺杂多晶硅和金属硅化物的叠层,也可以是导电金属材料,例如包括铝、铜、钼、钽、钛、钨或者它们的合金的至少其中一种。本实施例中该测试材料层的材料为铜。本实施例中,该测试材料层120可以通过多种沉积工艺形成在衬底上。例如,可以通过化学气相沉积(ChemicalVapordeposition,CVD)工艺、物理气相沉积(PhysicalVaporDeposition,PVD)工艺或者原子层沉积(atomiclayerdeposition,ALD)工艺在衬底上形成该测试材料层120。步骤S12,请参考图1和图2,在测试材料层120上形成第一测试图案110。图2中包括有A-A点划线,图1可以看成是图2所示结构沿A-A点划线切开得到的截面示意图。图2省略了对图1中测试材料层120的显示,仅显示了第一测试图案110,但应当理解,该第一测试图案110形成在该测试材料层120上,如图1所示。该第一测试图案110的制作材料可以是氧化硅、氮化硅、无定形碳或者光刻胶。在本实施例中,该第一测试图案110由光刻胶材料制作而成。可以通过涂覆光刻胶,再对光刻胶曝光显影,形成如图2所示的第一测试图案110。需要说明的是,第一测试图案110除了图2中所显示的形状之外,还可以是其它形状,例如曲线图案形状,或者直线弯折图案与曲线图案两者结合形成的形状,例如笛卡尔曲线,“之”字型弯折图案以及它们的组合等。可以根据用于上述衬底中,用于制作测试线的区域的形状来对应设计该第一测试图案110的形状。步骤S13,请参考图3、图4和图5,在第一测试图案110侧壁形成第一侧墙132’。请参考图3,本实施例在图1所示的结构中沉积一层材料层,该材料层可以是多晶硅、氧化硅和氮化硅中的至少一种。该材料层沉积在第一测试图案110之后分成三部分,分别如图3中所示的:位于第一测试图案110顶部表面的第一部分131;位于第一测试图案110侧壁的第二部分132,位于第一测试图案110间隙之间的测试材料层120上的第三部分133。可以通过ALD工艺形成该材料层,ALD工艺能够容易地控制材料层的形成厚度,并且由于该工艺的沉积过程中,在各个方向和位置上的沉积速度基本相同,因而利用ALD工艺能够沉积出具有良好的台阶形状的材料层。请参考图4,本实施例接着对图3所示结构进行一次各向异性蚀刻,将图3中位于第一测试图案110顶部表面的材料层第一部分131和位于第一测试图案110间隙之间的材料层第三部分133去除,只保留着位于第一测试图案110侧壁的材料层第二部分132,该部分保留的材料层第二部分132形成第一侧墙132’,如图4所示。该各向异性蚀刻可以是干法蚀刻,可以根据上述材料层的具体材料来选择不同的蚀刻参数。本实施例中,该第一侧墙132’的厚度可以设置在100埃~300埃之间。该第一侧墙132’的厚度可以通过上述ALD工艺控制。第一侧墙132’的厚度可以制作到100埃~300埃之间,小于用光刻工艺能够达到的最小间距(光刻工艺达到的最小间距在800埃以上),因而本实施例后续能够制作出密集程度高的测试线。请参考图5,图5可以看成是图4所示结构的俯视示意图。上述过程最终形成的结构俯视示意图如图5所示。在第一测试图案110的侧壁形成有第一侧墙132’,该第一侧墙132’由上述蚀刻过程中得到。步骤S14,请参考图6,去除第一测试图案110,形成第一闭合图案140。本实施例在形成图5所示结构之后,可以采用干法蚀刻或者选择性湿法蚀刻去除第一测试图案110,形成第一闭合图案140,如图6所示。事实上,该第一闭合图案140即为上述第一侧墙132’,但是在第一测试图案110被去除之后,以第一闭合图案140来表示,以显示出其作为一种独立的结构。步骤S15,请结合参考图6、图7和图8,在第一闭合图案140上形成第一缺口,形成第二测试图案150。在图6所示的结构中,右下角存在着B-B虚线,沿该B-B虚线切开第一闭合图案140,形成第一缺口(未标号),形成如图7所示的第二测试图案150。该步骤可以通过光刻工艺实现,具体过程本说明书不详细展开。需要说明的是,本实施例中,第一缺口的位置可以是图7中所示位置,也可以是其它位置。由于第一闭合图案140上形成了第一缺口,该第一闭合图案140转化成的第二测试图案150呈一根连续的线条(即非封闭的绕线结构),如图7所示,这样,就保证了后续形成的第二闭合图案170(请参考图12)为首尾连接的闭合结构。图8可以看成是图7所示结构沿图7中C-C点划线切开得到的截面示意图。从图8中可以看到,第二测试图案150位于测试材料层120上,并且第二测试图案150自身的宽度(未标注)小,在图8所示截面中,相邻两段第二测试图案150之间的间距(未标注)也小,这就进一步保证能够在较小的区域中制作出长度较大的测试线。步骤S16,请参考图9、图10和图11,在第二测试图案150的侧壁形成第二侧墙162’。请参考图9,类似于步骤S13,本实施例在图8所示结构中沉积一层材料层,形成如图9所示结构。该材料层沉积之后分成三部分,分别如图9中所示的:位于第二测试图案150顶部表面的第一部分161;位于第二测试图案150侧壁的第二部分162,位于第二测试图案150间隙之间的测试材料层120上的第三部分163。同样的,该材料层可以是多晶硅、氧化硅和氮化硅中的至少一种。可以通过ALD工艺形成该材料层。其原理可以参考步骤S13的相应内容。请参考图10,本实施例接着对图9所示结构进行一次各向异性蚀刻,将图9中位于第二测试图案150顶部表面的材料层第一部分161和位于第二测试图案150间隙之间的材料层第三部分163去除,只保留位于第二测试图案150侧壁的材料层第二部分162,该部分保留的材料层第二部分162形成第二侧墙162’,如图10所示。该各向异性蚀刻可以是干法蚀刻,可以根据上述材料层的具体材料来选择不同的蚀刻参数。本实施例中,该第一侧墙162’的厚度可以设置在100埃~300埃之间,该厚度范围的选取可以参考步骤S13相应内容。由于第二侧墙162’的厚度可以制作到100埃~300埃之间,小于用光刻工艺能够达到的最小间距,因而本实施例后续能够制作出密集程度高的测试线。第二侧墙162’的厚度可以制作成小于第一侧墙132’的厚度,例如,将第一侧墙132’设置成300埃,而将第二侧墙162’的厚度设置成100埃。这样,有助于后续形成线条较细的测试线。但是,如果希望得到线条较粗的测试线,而可以对应将第二侧墙162’的厚度设置成大于或等于第一侧墙132’的厚度。而如果要得到最终间距较小的测试线,则需要将第一侧墙132’的厚度设置成较小,因为第二侧墙162’各段之间的间距与第一侧墙132’的厚度大致相等。请参考图11,图11可以看成是图10所示结构的俯视示意图。上述过程最终形成的结构俯视示意图如图11所示。在第二测试图案150的侧壁形成有第二侧墙162’,该第二侧墙162’由上述蚀刻过程中得到。步骤S17,请参考图12,去除第二测试图案150,形成第二闭合图案170。本实施例在形成图11所示结构之后,可以采用干法蚀刻或者选择性湿法蚀刻去除第二测试图案150,形成第二闭合图案170,如图12所示。事实上,该第二闭合图案170即为上述第二侧墙162’,但是在第二测试图案150被去除之后,以第二闭合图案170来表示。步骤S18,请结合参考图12、图13和图14,在第二闭合图案170上形成一个缺口,形成第三测试图案180。在图12所示的结构中,右下角存在着D-D虚线,沿该D-D虚线切开第二闭合图案170,形成第二缺口(未标号),形成如图13所示的第三测试图案180。该步骤可以通过光刻工艺实现,具体过程本说明书不详细展开。图13中显示,该第三测试图案180为非封闭结构,而是一根连续的线条,并且,对比图2可知,该第三测试图案180从图2所示的单绕线结构第一测试图案110变成图13所示的四重绕线结构,即对比图2和图13可知,图2中可看出有四条横线段,而图13中对应有十六条横线段(图13中第三测试图案180的长度为图2中第一测试图案110长度的四倍)。可见该第三测试图案180在其所在区域具有较大的长度,面积利用率高。图14可以看成是图13所示结构沿图13中E-E点划线切开得到的截面示意图。从图14中可以看到,第三测试图案180位于测试材料层120上,并且第三测试图案180自身的宽度(未标注)小,在图14所示截面示意图中,相邻两段第三测试图案180之间的间距(未标注)也小,因而在较小的区域中其长度仍然较大。本步骤形成的第二缺口与步骤S15形成的第一缺口位于测试材料层120上相同位置,可对比图6和图12和两条虚线(分别为B-B虚线和D-D虚线)的位置看出,这种将第二缺口与第一缺口设置在测试材料层120上相同位置能够使得在形成第二缺口的位置比较容易找准,从而使得工艺更简单,并且最终形成的测试图案也比较规则整齐。需要说明的是,在其它实施例中第二缺口也可以与第一缺口位于测试材料层上的不同位置,第二缺口只需要保证使首尾相连的第二闭合图案170形成具有唯一一个缺口的形状即可,亦即只需要保证第二闭合图案170变成一根连线的线条(第三测试图案180)即可。步骤S19,将第三测试图案180作为所述待转移测试图案,转移到测试材料层120,形成测试线。本实施例最后将图13中所示的第三测试图案180作为所述待转移测试图案,转移到测试材料层120,亦可以参考图14,将第三测试图案180作为所述待转移测试图案,转移到测试材料层120。该转移过程可以使用平版印刷工艺、纳米压印工艺、定向自组装工艺、干法蚀刻工艺和湿法蚀刻工艺的至少其中一种工艺。最终得到与第三测试图案180相同形状的测试线(未图示)。通过本实施制作得到的测试线在制作区域面积上的密集程度高。在一定面积内制作测试线时,假设所制作的测试线具有最大的面积利用率时,从一条线段方向切开,该线段的长度为L,该线段所经过的绕线的条数最大值为N,此时各绕线之间具有最小间距为Δ。再假设通过本实施制作得到测试线时,按同一条线段方向切开,该线段的长度为L,此时绕线(如图13所示为四重绕线)的关键尺寸(CD)为x,各绕线不同弯折段之间的最小间距为l,该切开线段所经过的绕线的条数为n,此时有:n=N-[(x-2l)/Δ]×(L/2x)其中:Δ=L/N此时,n越接近N,说明本实施制作得到的测试线面积利用率越高,因而,再假设R为n与N的比值,当R的值为1(事实上不可能达到)时,说明制作的测试线达到了极限面积利用率,即有:R=n/N={N-[(x-2l)/Δ]×(L/2x)}/N代入Δ=L/N,最终得到:R=0.5+l/x由此可知,本实施例中,当关键尺寸x为400埃(此关键尺寸通过光刻工艺即可达到),而绕线不同弯折段之间的最小间距为l为100埃(本实施例中将第二侧墙162’的厚度制作为100埃时,l即为100埃)时,R的值为0.75,即本实施例能够达到极限面积利用率的75%,而现有仅用光刻工艺来制作的测试线(其计算公式未推导),其面积利用率通常小于极限面积利用率的50%。除了上述实施例外,在本发明的其它实施例中,还可以在形成第三测试图案之后,在第三测试图案的侧壁形成第三侧墙,然后去除第三测试图案,形成第三闭合图案,再在第三闭合图案形成第三缺口,形成第四测试图案,最后以第四测试图案为待转移测试图案形成测试线。通过增加一次侧墙的形成,最终得到的测试线具有八重绕线结构,其长度更大,面积利用率更高。需要说明的是,还可以重复一次或多次上述侧墙形成、测试图案去除和缺口形成的步骤(只需要工艺和分辨率允许),从而进一步在较小的面积区域中形成较大长度的测试线。虽然本发明披露如上,但本发明并非限定于此。任何本领域技术人员,在不脱离本发明的精神和范围内,均可作各种更动与修改,因此本发明的保护范围应当以权利要求所限定的范围为准。