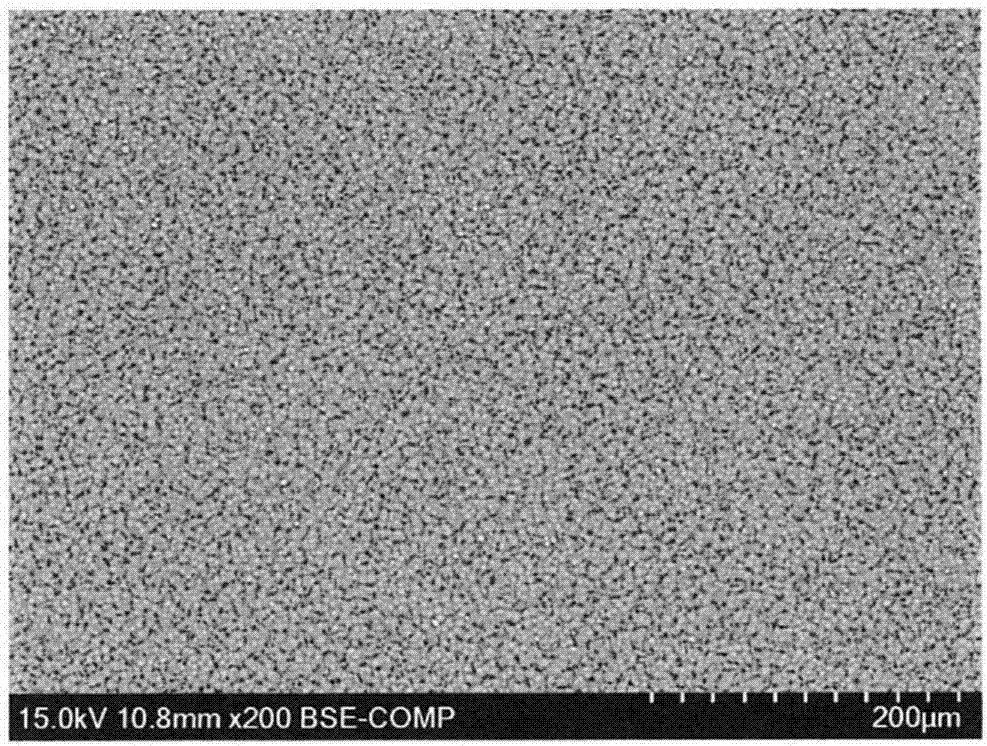
本发明涉及电缆和医疗用中空管。
背景技术:
:在使用硅橡胶作为医疗用探测器电缆等电缆的最外层材料的情况下,硅橡胶摩擦阻力大,其表面发黏,因此在装入包装袋或取出等时,操作性变差。此外,导管等医疗用具中也常常使用对生物体组织影响小的硅橡胶,因此存在同样的问题,需要滑动性的改善(例如参照专利文献1)。现有技术文献专利文献专利文献1:日本特开2008-287号公报技术实现要素:发明所要解决的课题例如,即使对硅胶护套最外层的表面实施凹凸加工以能够实现优异的滑动性,但在反复使用的用途中,也存在将粘在电缆等表面的污垢等擦掉的必要。这就存在如下的问题:随着擦拭次数的增加,表面的凹凸被磨掉,从而滑动性降低,即摩擦阻力变大,其表面发黏。因此,本发明的目的在于,提供具有即使擦拭次数增加也能够维持优异的滑动性的耐擦拭性的电缆和医疗用中空管。用于解决课题的方法为了实现上述目的,本发明提供下述电缆和医疗用中空管。[1]一种电缆,具有包含微粒和空孔的硅橡胶被膜作为最外被膜。[2]上述[1]中记载的电缆,上述微粒为选自硅树脂微粒、硅橡胶微粒和二氧化硅微粒的1种以上。[3]上述[1]或上述[2]中记载的电缆,上述微粒为具有比构成上述硅橡胶被膜的硅橡胶高的硬度的微粒。[4]上述[1]~[3]中任一项所述的电缆,上述微粒的平均粒径为3μm以上且20μm以下。[5]上述[1]~[4]中任一项所述的电缆,上述微粒在上述硅橡胶被膜中含有10质量%以上且50质量%以下。[6]上述[1]~[5]中任一项所述的电缆,上述空孔的最长部的长度为1μm以上且15μm以下。[7]上述[1]~[6]中任一项所述的电缆,上述硅橡胶被膜的厚度为3μm以上且50μm以下。[8]上述[1]~[7]中任一项所述的电缆,上述硅橡胶被膜的表面具有凹凸。[9]上述[1]~[8]中任一项所述的电缆,其涂覆有上述硅橡胶被膜,且具备由含有硅橡胶或氯丁橡胶的组合物形成的护套。[10]一种医疗用中空管,具有包含微粒和空孔的硅橡胶被膜作为最外被膜或最内被膜。发明效果根据本发明,能够提供具有即使擦拭次数增加也能够维持优异的滑动性的耐擦拭性的电缆和医疗用中空管。附图说明图1是显示本发明实施方式涉及的电缆的一例的横截面图。图2是对本发明实施方式涉及的电缆的被膜表面进行拍照而得的照片((a)为200倍,(b)为500倍,(c)为1000倍)。图3是示意性显示本发明实施方式涉及电缆的被膜的构成的截面图。图4是示意性显示比较例涉及电缆的被膜的构成的截面图((a)为比较例1,(b)为比较例2)。图5是对实施例涉及的电缆(耐擦拭性试验前后)的被膜表面和截面进行拍照而得的照片。图6是对比较例涉及的电缆(耐擦拭性试验前后)的被膜表面进行拍照而得照片。图7是显示耐擦拭性试验中实施例和比较例的静摩擦系数的图表。符号说明10:电缆;1:导体;2:绝缘体;3:电线;4:护套;5:绞合芯;6、26:硅橡胶被膜;16:硅树脂被膜;61:硅橡胶;62:微粒;63:空孔。具体实施方式1.电缆本发明实施方式涉及的电缆具有包含微粒和空孔的硅橡胶被膜作为最外被膜。参照附图,详细地对本发明实施方式涉及的电缆进行说明。图1是显示本发明实施方式涉及的电缆的一例的横截面图。图1所示的本实施方式涉及的电缆10具备:绞合了3根电线3而成的绞合芯5、挤出被覆于绞合芯5外周的护套4以及在护套4外周成膜的硅橡胶被膜6。电线3可以为单芯,也可以为除了三芯以外的多芯绞线。电线3具备由通用的材料,例如纯铜、镀锡铜等形成的导体1以及被覆于导体1外周的绝缘体2。绝缘体2只要是能够作为电线的绝缘体材料使用就没有特别限定,例如由聚乙烯、聚氯乙烯、卡普顿(聚酰亚胺)、硅橡胶、乙烯丙烯(epr)等橡胶材料、etfe、fep、pfa、ptfe等氟系树脂等构成。导体1不限于1根,也可以绞合有多根裸线。此外,电线3可以是同轴线、光纤等。护套4只要是能够作为护套材料使用就没有特别限定,可列举例如硅橡胶、聚氯乙烯、聚乙烯、氯化聚乙烯、氯丁橡胶作为合适的材料。尤其在护套4由滑动性低的材料,即摩擦力高的材料或粘合性高的材料构成的情况下,本发明的应用价值高。可列举例如制成片状基材时伴随静摩擦系数μ为0.7以上的粘合(发黏)的硅橡胶、氯丁橡胶等橡胶组合物作为代表。上述材料不仅可以单独使用,也可以作为含有2种以上的组合物来使用。作为护套材料的组合物中可以添加各种交联剂、交联催化剂、抗老化剂、增塑剂、润滑剂、填充剂、阻燃剂、稳定剂、着色剂等一般的配合剂。护套4可以通过挤出被覆而设置,根据需要实施交联处理。护套4也可以制成多层结构。这种情况下,如果多层结构中的最外层由上述材料构成则本发明的应用价值高。硅橡胶被膜6涂覆于作为最外被覆层的护套4的表面。图2是对本发明实施方式涉及的电缆的被膜表面进行拍照而得的照片((a)为200倍,(b)为500倍,(c)为1000倍)。此外,图3是示意性显示本发明实施方式涉及的电缆的被膜的构成的截面图。硅橡胶被膜6中,硅橡胶61中包含多个微粒62和多个空孔63,如图2所示,遍及硅橡胶被膜6整体而分散。图2中,白色球状部分是微粒62存在的部分,观察到黑点状的部分是存在空孔63的部分。它们遍及硅橡胶被膜6且整体均匀分散是优选的。此外,优选微粒62在硅橡胶被膜6中沿厚度方向点状存在(参照图3)。微粒62即使在擦拭中被擦掉(或即使周围的硅橡胶61被磨掉而露出微粒62),硅橡胶61也会被磨掉而露出新的微粒62,从而能够维持与擦拭用无纺布等的接触面积小的状态,因而容易保持小的摩擦系数。作为微粒62,可以使用硅树脂微粒、硅橡胶微粒、二氧化硅微粒、银微粒等各种微粒,优选为具有比构成硅橡胶被膜6的硅橡胶61高的硬度(例如以肖氏(durometera)硬度计为1.1倍左右以上的硬度)的微粒。微粒62优选为选自硅树脂微粒、硅橡胶微粒和二氧化硅微粒的1种以上,更优选为硅树脂微粒。硅橡胶微粒可以是将球状硅橡胶粉末的表面用硅树脂被覆而得的球状粉末(所谓硅胶复合粉末)。微粒62优选为球状,平均粒径优选为3μm以上且20μm以下,更优选为3.5μm以上且15μm以下,进一步优选为4μm以上且10μm以下。此外,微粒62优选在硅橡胶被膜6中含有10质量%以上且50质量%以下,更优选含有15质量%以上且47质量%以下,进一步优选含有20质量%以上且45质量%以下。如果低于10质量%则有可能摩耗耐性降低,如果超过50质量%则存在微粒62难以固着于硅橡胶61的倾向。图2中,使用硅橡胶表面改性用涂覆材料(商品名:x-93-1755-1,信越化学公司制)作为硅橡胶61用涂料,在该涂覆材料中,添加平均粒径4.6μm的硅树脂微粒(商品名:x-52-1621,信越化学公司制)作为微粒62并分散,制作最终的涂覆液,将其涂布、干燥,从而形成硅橡胶被膜6。该硅橡胶被膜6中含有45质量%硅树脂微粒。另一方面,空孔63的最长部的长度为0.5μm以上且20μm以下,优选为1μm以上且15μm以下,更优选为2μm以上且10μm以下。空孔63即便是少量的,也有利于作为本发明效果的耐擦拭性的提高,优选以微粒62的数量±30%以内程度的数量存在。可以是多个空孔63相连接。图2中,在硅橡胶被膜6中形成最长部的长度为3~10μm的空孔63,存在数量为微粒62的数量±20%左右的空孔63。此外,如图3、图5的截面图所示,优选硅橡胶被膜6的表面具有凹凸。由此,能够使电缆运动时与接触物体的接触面积小,因此摩擦力进一步减小,滑动性提高。具体而言,表面粗糙度例如以算数平均粗糙度(ra)计优选为0.2μm以上,更优选为0.4μm以上,进一步优选为0.6μm以上。算数平均粗糙度(ra)的上限没有特别限定,优选为5μm以下。图2中,硅橡胶被膜6的表面粗糙度以算数平均粗糙度(ra)计为0.5μm。算数平均粗糙度(ra)测定通过利用了基恩士制的激光的超深度形状测定显微镜(型号:vk-8500)来实施。将观察倍率设为500倍、测定距离设为298μm,调整高度方向的测定范围,以测定间距0.01μm进行测量。硅橡胶被膜6的厚度没有特别限定,优选为3μm以上且50μm以下,更优选为6μm以上且30μm以下,进一步优选为7μm以上且25μm以下。图2中,硅橡胶被膜6的厚度为15μm。硅橡胶被膜6可通过一般的方法成膜,例如,可通过浸涂、喷涂来成膜。作为被膜用溶液,可以使用硅橡胶涂覆材中含有微粒62而得的涂覆溶液,其中,硅橡胶涂覆材包含用于形成空孔63的挥发性溶剂。作为挥发性稀释溶剂,可以使用例如甲苯、正庚烷、苯、乙苯、邻二甲苯、间二甲苯、对二甲苯等。通过选择适当的挥发性稀释溶剂并调节微粒62和溶剂的含量,能够调节空孔63的数量和大小。其中,图2中,使用的是含有平均粒径4.6μm的硅树脂微粒(商品名:x-52-1621,信越化学公司制)作为微粒62并含有乙烯基肟硅烷和甲苯、正庚烷作为具有空孔的硅橡胶61用涂覆材料的材料(商品名:x-93-1755-1,信越化学公司制)。使用相对于100质量份该硅橡胶涂覆材含有10质量份硅树脂微粒的溶液,通过浸涂法(提升速度:2m/s)使硅橡胶被膜6成膜。然后,以120℃的温度进行60分钟的干燥。干燥后,皮膜6中微粒62的比例为45%。该比例是以信越化学工业(株)硅胶新闻(siliconenews)vol.130,硅橡胶表面改性用涂覆材料(x-93-1710,x-93-1755-1)中记载的涂覆液中不挥发分12%为基准计算的。具体而言,由“皮膜6中的微粒62的比例=10重量份(微粒62的质量)/[10重量份(微粒62的质量)+100重量份(硅橡胶涂覆材)×0.12]”算出。其中,在形成的膜的空孔直径过小,例如为0.1μm以下的情况下,通过向涂覆液加入作为挥发性稀释溶剂的甲苯、正庚烷、苯、乙苯、邻二甲苯、间二甲苯、对二甲苯等,能够调整由于挥发而产生的空孔直径、数量。此外,也可以利用提升速度快则膜的厚度增加来适当实施增加空孔直径的调整。本实施方式涉及的电缆10中,可以根据需要加入由隔膜、编织、金属箔形成的遮蔽胶带等。本发明实施方式涉及的电缆能够适用于各种用途的电缆,尤其是对于医疗用电缆(内窥镜电缆、探测器电缆、导管用连接电缆等)和橡皮绝缘电缆等作为电缆彼此或与接触物的摩擦成为问题的用途的、且将污垢等擦掉而反复使用的用途的电缆是合适的。2.医疗用中空管本发明不仅能够适用于电缆,而且能够适用于作为与接触物的摩擦成为问题的用途的、且将污垢等擦掉而反复使用的用途中使用的其他物品,尤其适合于导管等医疗用中空管。即,本发明实施方式涉及的医疗用中空管具有包含微粒和空孔的硅橡胶被膜作为最外被膜。除了具有上述包含微粒和空孔的硅橡胶被膜的作为最外被膜一点以外,可以采用与公知的医疗用中空管同样的构成。此外,在将器具插入导管等医疗用中空管的管内而使用的情况下,作为医疗用中空管的最内被膜(内壁面),可以适用上述包含微粒和空孔的硅橡胶被膜。实施例以下,基于实施例,进一步详细地对本发明进行说明,但本发明不限于此。电缆的耐擦拭性的评价:通过如下方法制造图1结构的电缆,进行耐擦拭性的评价。电缆(电线:3根×22mm2)的各部位的尺寸如下。·导体构成(导体外径/裸线根数/裸线直径):7mm/20根/0.45mm·绝缘体厚度:1.2mm·护套厚度:2.7mm·成品外径:26mm电线3如下获得:作为绝缘体2,将各种颜色(红、白、黑)的硫交联epr(乙丙橡胶)分别在导体1上挤出被覆规定的厚度后,利用加压水蒸气进行交联。将该3根(各色)电线3绞合,得到绞合芯5。利用挤出机在该绞合芯5外周以5m/分钟的速度挤出被覆护套材料。使用硅橡胶作为护套材料。被覆护套后,对护套表面进行清洁,然后,使硅橡胶被膜在护套表面成膜,得到实施例1的电缆。具体而言,使用相对于含有挥发性溶剂(正庚烷、甲苯)的硅橡胶涂覆材(商品名:x-93-1755-1,信越化学公司制)100质量份含有10质量份平均粒径4.6μm的硅树脂微粒(商品名:x-52-1621,信越化学公司制)的溶液,通过浸涂法(提升速度:2m/s)使膜厚15μm的硅橡胶被膜6成膜。该硅橡胶被膜6中硅树脂微粒62的含量为45质量%。此外,硅橡胶被膜6中形成最长部的长度3~10μm的空孔63,空孔63以微粒62的数量±20%程度的数量存在。接下来,改变被膜的材料,得到比较例1~2的电缆。使被膜在护套表面成膜之前的工序与上述实施例1是同样的。比较例1中,使用硅树脂(商品名:x-93-1710,信越化学公司制)溶液,通过浸涂法(提升速度:1.5m/s)使膜厚7μm的硅树脂被膜16成膜(参照图4(a))。比较例2中,使用硅橡胶(商品名:x-93-1755-1,信越化学公司制)溶液,通过浸涂法(提升速度:2m/s)使膜厚7μm的硅橡胶被膜26成膜(参照图4(b))。将实施例和比较例的电缆各切下15cm,分别对其进行以下的耐擦拭性试验。耐擦拭性试验方法:在实施了涂覆的电缆的护套部分,沿长度方向切出切口,将除了护套以外的内容物除去,将护套打开,以成为长度约15cm、宽度约8cm的平面片状的方式粘贴在平板上,从而制作试验用片材。握住试验用片材的一个端部,用浸有消毒用乙醇的5cm见方的无纺布,以擦拭涂覆表面的方式进行擦拭。以无纺布不会干燥的方式,在擦拭了10次时用消毒用乙醇浸泡无纺布。在擦拭了300次时,更换为新的无纺布。擦拭是沿1个方向反复实施,实施例1和比较例2擦拭1万次,比较例1擦拭5千次。擦拭的力量是,将试验用片材固定在秤上,用无纺布对涂覆表面进行按压擦拭,从该测量的量来测量水平。通过在每次擦拭试验前实施该测量,使水平对齐。具体的擦拭负荷设为约0.3kg。擦拭是,擦拭距离约15cm/次,以约75次/分钟的速度进行。耐擦拭性试验前后进行被膜表面的拍照(1000倍)。关于实施例1,还拍摄了截面的照片(1000倍)。图5是对实施例涉及的电缆(耐擦拭性试验前后)的被膜表面和截面进行拍照而得的照片,图6是对比较例涉及的电缆(耐擦拭性试验前后)的被膜表面进行拍照而得的照片。此外,耐擦拭性试验前后和试验中(比较例1~2为500次,实施例1和比较例2为5千次),进行被膜表面静摩擦系数的测定。静摩擦系数的测定是,对与耐擦拭性试验同样实施了涂覆的电缆进行加工,或者对擦拭试验后的试验用片材进行加工,以成为长度约10cm、宽度约2.5cm的平面片状的方式粘贴在平板上(片材1)。此外,对同样实施了涂覆的电缆或者擦拭试验后的试验用片材进行加工,切下1.5cm×1.5cm见方的片材,粘贴在平板上(片材2)。对于片材1的实施了涂覆的表面或者擦拭后的表面,以面向片材2的实施了涂覆的表面或者擦拭后的表面的方式,从上部接触,从片材2平板上施加2n的负荷w,同时利用推拉力计水平拉动粘贴片材2的平板,测定该拉力(摩擦力)f。静摩擦系数μ通过f=μw算出。图7是显示耐擦拭性试验中实施例和比较例的静摩擦系数的图表。如由图7可见,对于使包含微粒和空孔的硅橡胶被膜6成膜而作为最外被膜的实施例1的电缆表面,在耐擦拭性试验前后静摩擦系数均较小(试验前:0.16,1万次擦拭试验后:0.18),得到具有即使擦拭次数增加也能够维持优异的滑动性的耐擦拭性的(即发黏少的)电缆。而比较例1~2的电缆中,静摩擦系数比实施例1大,而且,耐擦拭性试验后静摩擦系数大幅上升(试验前的比较例1:0.7,5千次擦拭试验后的比较例1:0.82;试验前的比较例2:0.3,1万次擦拭试验后的比较例2:0.43)。硅橡胶被膜6具有空孔63,呈海绵状。因此认为,硅橡胶被膜6以容易由于擦拭试验时施加的应力而变形,从而作用为逃避该应力,因而实施例1的电缆表面的耐擦拭性提高。以这种方式,使包含微粒和空孔的硅橡胶被膜6成膜而得的实施例1的电缆在初始的5千次擦拭后、进而在1万次擦拭后,均未感觉到表面的发黏,静摩擦系数为0.3以下、优选为0.25以下、更优选为0.20以下。此外,耐擦拭性试验前后测定的算数平均粗糙度(ra)如下述表1所示。算数平均粗糙度(ra)使用基恩士公司制激光显微镜系统(vk-8500)测定。表1如由表1可见,使包含微粒和空孔的硅橡胶被膜6成膜而得的实施例1的电缆表面与比较例1~2的电缆表面相比,算数平均粗糙度(ra)大,试验后也只有20%左右的减少。此外,实施例1和比较例2的电缆的挠性优异,但比较例1的电缆在弯曲(r5mm)时产生裂纹,挠性不足。其中,本发明不限于上述实施方式和实施例,可以进行各种变形。例如,可以在护套表面设置用于提高护套与硅橡胶被膜的密合性的、由底漆、硅烷偶联剂等形成的密合增强层。此外,也可以通过对护套表面进行短时间暴露于火焰的火焰处理、或者进行使气体离子化、自由基化而与表面撞击的等离子处理、或者进行在大气中放电而使空气中的成分离子化并暴露于该成分的电晕处理等方法,在护套表面形成表面改性层,提高护套与硅橡胶被膜的密合性。进而,还可以在该表面改性层上设置上述密合增强层后再形成硅橡胶被膜。此外,在电缆的一端安装带有电缆衬套的探测器主体而制造探测器电缆时,可以在位于端部的硅橡胶被膜上涂布粘接剂,介由该粘接层将电缆衬套粘接固定。进而,也可以并用密合增强层和粘接层或者并用表面改性层和粘接层,将电缆衬套粘接固定。其中,密合增强层、表面改性层可以仅在固定电缆衬套的位置形成,也可以贯穿护套全长形成。作为其他方法,可以在安装电缆衬套的位置进行预先遮掩或者除去等,不设置硅橡胶被膜,利用粘接剂直接将护套与电缆衬套粘接固定。此外,还可以在未设置硅橡胶被膜的位置形成表面改性层后,在该表面改性层上涂布粘接剂而将护套与电缆衬套粘接固定。拉伸剪切强度试验方法:准备2片宽度25mm×长度15mm的硅橡胶片。在一片硅橡胶片上,在宽度25mm×长度10mm的区域涂布液状硅橡胶系粘接剂。介由该粘接剂层将2片硅橡胶片粘接固定,制作实验例1的拉伸剪切强度试验样品。实验例2的拉伸剪切强度试验样品是在实施例1的拉伸剪切强度试验样品的制作工序中追加硅橡胶被膜的形成工序而制作的,其他工序是相同的。具体而言,在一片硅橡胶片上全面形成硅橡胶被膜。介由该形成于硅橡胶被膜上的液状硅橡胶系粘接剂层将2片硅橡胶片粘接固定。实验例3的拉伸剪切强度试验样品是在实施例1的拉伸剪切强度试验样品的制作工序中追加表面改性层和硅橡胶被膜的形成工序而制作的,其他工序是相同的。具体而言,对一片硅橡胶片进行火焰处理形成表面改性层,在该表面改性层上全面形成硅橡胶被膜。介由该形成于硅橡胶被膜上的液状硅橡胶系粘接剂层将2片硅橡胶片粘接固定。其中,实验例2和实验例3的硅橡胶被膜在与实施例1同样的条件下形成。将该拉伸剪切强度试验样品1~3在与粘接面平行的方向上以500mm/min的拉伸速度拉伸,评价拉伸剪切强度(样品破坏时的最大负荷)。表2实验例1实验例2实验例3硅橡胶被膜无有有表面改性层无无有拉伸剪切强度(n)1095083如由实验例1、2可见,在将硅橡胶片彼此粘贴的情况下,得到100n以上的拉伸剪切强度,但如果中间存在硅橡胶被膜,则变为50n。这是由于硅橡胶被膜与硅橡胶片之间、或高拉伸剪切强度被膜本身、或硅橡胶被膜与粘接剂层之间的强度弱。与此相对,如由实验例2、3可见,通过在硅橡胶被膜与硅橡胶片之间形成表面改性层,能够提高硅橡胶被膜与硅橡胶片的密合性,能够使拉伸剪切强度为80n以上。通过在高强度的被膜、硅橡胶被膜与粘接剂层之间形成密合增强层、表面改性层,能够获得更高的拉伸剪切强度。当前第1页12