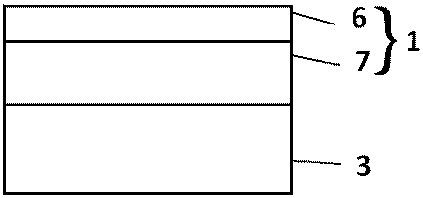
本实用新型涉及具有软包电池热控制装置的用电设备或发电设备,特别涉及具有可浸泡于冷却水中的软包电池热控制装置的车用动力电池领域和储能电池领域。
背景技术:
:热管理技术是软包动力电池的核心技术之一,现有技术中也开始有浸泡式水冷的研究,其冷却效率相比以前的非接触式水冷可显著提高,然而,铝塑膜的长期耐蚀性仍然是需要解决的问题。现有技术中软包电池包装用的铝塑膜通常采用8系铝合金铝箔,这种铝箔退火后为软质铝箔,冲深成型性好。若采用3系铝合金铝箔,其抗面腐蚀性可有一定改善。目前电池包装材料主要考虑的是耐电解质腐蚀性,主要技术方案是在包装材料朝向电解质的一侧通过物理或化学方式改性形成耐腐蚀层,其作用是防止电解质腐蚀铝箔内表面而导致铝塑膜层间剥离。现有铝塑膜最外层基本上都含有聚酰胺等保护用塑料膜。技术实现要素:基于当前大容量电池热管理问题仍然是制约行业发展的瓶颈问题,本实用新型从软包电池冷却的需求出发,为了获得更高的电池冷却性能,本实用新型大胆采用将软包电池直接浸泡于冷却水中的冷却方案。然而,经过深入研究和长期测试后才发现,现有电池包装材料不能适应这种浸泡式水冷要求,现有软包电池包装用铝塑膜中最外侧尼龙保护层抗乙二醇防冻液腐蚀性能差,作为阻水层的铝箔为铝铁合金,其机械强度和抗乙二醇防冻液腐蚀性能(特别是抗点蚀性能)也较差,即使其采用传统的技术手段(如铝箔表面做防腐涂层处理)也容易出现点腐蚀,故现有铝塑膜不能满足长期的浸泡式水冷系统要求。为了克服上述缺陷,本实用新型创造性地提供如下新的电池冷却系统方案和电池包装材料方案,以解决上述系列技术问题并满足新能源车用或储能用等大容量电池系统的热管理需求。在兼顾铝塑膜铝箔成型能力前提下,同时针对现有技术中用于包装电池(battery)的铝塑膜耐车用防冻冷却液(简称防冻液,其主要成分为乙二醇和水)或耐冷却水的抗腐蚀性能不足的缺陷,即容易被腐蚀穿孔的缺陷,本实用新型特提供一种可用于锂离子二次电池包装用铝塑复合膜(以下简称铝塑膜),其具有更高的耐冷却液腐蚀能力。现有铝塑膜中的单层铝合金抗蚀性不足,特别是抗点蚀性能较差。为了改善铝塑膜中铝箔在冷却水中的腐蚀形态、防止点蚀发生,本实用新型优选提供具有牺牲阳极功能的复合层铝箔作为铝塑膜中铝箔。进一步的,在改善腐蚀形态的基础上,本实用新型更优选提供具有较好变形能力的复合层铝箔作为铝塑膜中铝箔。本实用新型第一个方面是提供一种由金属塑料复合薄膜形成的电池、优选为软包电池用包装材料(优选为铝塑膜),包括金属箔层(优选为铝箔层)和复合于金属箔层(优选为铝箔层)内表面的塑料层。本实用新型第二个方面是提供一种软包电池,包含有电极材料和电解质以及外部包裹用的上述的金属塑料复合薄膜(优选为铝塑膜),所述金属箔层(优选为铝箔层)内表面的塑料层将电解质与金属箔层(优选为铝塑膜)隔离。优选地,所述电解质包含有六氟磷酸锂和/或四氟硼酸锂(LiBF4)。本实用新型第三个方面是提供一种电池热控制装置,优选为软包电池热控制装置,包含有上述的软包电池。该软包电池可采用耐冷却液浸泡腐蚀的上述的铝塑膜包装之后,可以将该软包电池浸泡在冷却液(如防冻冷却液)中,优选地,所述由金属塑料复合薄膜形成的电池用包装材料浸泡在所述冷却液中,更优选地,所述金属箔层(优选为铝箔层)浸泡在所述冷却液中,从而金属箔层可以直接与冷却液进行热交换。这样电池的换热效果更好,且电池上下左右各处的温度更均匀。本实用新型第四个方面是提供一种采用热控制装置冷却电池单元的方法。本实用新型第五个方面是提供一种制造所述由金属塑料复合薄膜形成的电池用包装材料、优选为铝塑膜的方法。本实用新型第六个方面是提供一种用电设备和发电设备,该用电设备和发电设备包含有上述任一种电池和/或任一种电池热控制装置。本实用新型还提供一种交通工具和储能装置,该交通工具和储能装置包含有上述软包电池和/或上述软包电池热控制装置。下面具体介绍技术方案。若未特别说明,本实用新型中所谓耐腐蚀均是指耐冷却水或防冻液腐蚀,而不是指耐电解液腐蚀。本实用新型采用的耐冷却水腐蚀的技术手段也不同于传统的耐电解液腐蚀的技术手段。在本实用新型一种铝塑膜的优选实施例中,其铝箔层为复合层,铝箔层包含有芯材和位于芯材外侧的皮材,铝箔层的皮材的腐蚀电位低于芯材的腐蚀电位。更优选地,所述芯材位于铝箔层内侧的塑料层与皮材之间。更优选的,所述电池热控制装置中,包装软包电池的铝塑膜铝箔的皮材直接浸泡在所述冷却液中。需要说明的是,芯材是相对于皮材而言位于内侧,皮材是相对于芯材而言位于外侧。本实用新型的复合层铝箔中,特别是对于具有多层的铝箔或者是对于经过元素扩散处理后的铝箔,其芯材和皮材已经没有绝对的定义或明显的界限,该二者只是相对而言。此外,铝合金皮材也可以称为铝合金牺牲层或铝合金触水层。本实用新型的铝塑膜是一种塑料膜和铝箔膜形成的薄膜复合材料,是作为聚合物锂电池用包装材料。其中,可以是铝箔层的内外两侧均复合有塑料层。但优选地,该铝塑膜由铝箔层和位于铝箔层内侧的塑料层复合形成,或者所述铝塑膜由位于内侧的热塑性树脂薄膜和位于外侧的铝箔层复合形成,即塑料层仅复合于铝箔层的内侧,而该铝塑膜的铝箔层外侧无塑料层。复合的方法既可以是干法复合也可以是热法复合。其中,上述方案中包括如下情况:复合于铝箔层某一侧表面的塑料层,既可以是单层塑料,也可以是多层塑料。进一步的,所述内侧塑料层优选为热塑性树脂薄膜。比如,聚丙烯(PP)薄膜或聚乙烯(PE)薄膜。其中,内侧塑料层的厚度可选为50-300微米,优选为大于60小于100微米,更为优选为70-90微米。该内侧塑料层也可以是热封层或密封层。优选地,所述内侧塑料层为聚烯烃树脂或酸改性聚烯烃树脂。该内侧塑料层中也可以配合各种添加剂,如阻燃剂、润滑剂、防粘连剂、抗氧化剂、光稳定剂、粘着赋予剂中的一种或几种。优选地内侧塑料层具有更好的电绝缘特性,从而耐电压值更高,比如耐电压优选大于1000V,更为优选大于2000V。若含有外侧塑料层,所述外侧塑料层优选为耐热性树脂薄膜。比如聚酰胺(PA)或尼龙(Ny或ON)膜、或聚酯(PET)薄膜、或聚酰亚胺(PI)薄膜。另外,上述复合层铝合金,优选为至少包括芯材和复合于芯材外侧的皮材。复合层铝合金可以是两层组分不同的铝合金、也可以是多层组分不同的铝合金。本实用新型上述铝塑膜,可以是包括A)-C)中的任意一种结构:A)所述铝塑膜具有由内侧塑料热封层、中间金属箔层、和外侧塑料保护层复合形成的叠层体,其中,中间金属箔优选为铝箔,中间铝箔层更优选为具有牺牲阳极保护功能的复合层铝箔形成。比如,该复合层铝箔由芯材和腐蚀电位低于芯材的皮材形成。B)所述铝塑膜具有由内侧塑料热封层、和外侧金属箔层复合形成的叠层体,其中,外侧金属箔优选为铝箔,外侧铝箔层更优选为具有牺牲阳极保护功能的复合层铝箔形成。该铝塑膜不含有外侧塑料保护层。C)所述铝塑膜具有依次由内侧塑料热封层、中间金属箔、中间绝缘树脂层、以及外侧金属箔复合形成的叠层体。其中,中间金属箔和外侧金属箔可分别选择为铝箔或不锈钢箔或铜箔,更优选为铝箔。内侧塑料热封层起热封的作用。中间铝箔可发挥阻隔内侧物质(如电解液或导电离子)向外渗透作用。中间绝缘树脂层可发挥绝缘作用,使得电解液与外侧铝箔之间的绝缘强度满足电气安全需要。外侧铝箔可发挥耐冷却水腐蚀作用,同时可阻隔外部物质(如水汽)向内渗透;该外侧铝箔可选择为耐冷却水腐蚀的单层铝箔,优选为具有牺牲阳极功能的复合层铝箔,进一步优选地复合层铝箔中芯材为纯铝或铝铁铝合金,复合层铝箔的外侧皮材为铝锌铝合金。对于该方案C的铝塑膜来说,若未特别说明,下面关于铝箔的说明或限定均指外侧铝箔,而非中间铝箔。作为上述方案C的可选的变形方案C2,方案C2可在方案C的基础上再在最外侧增加塑料保护层,比如在方案C的外侧金属箔的外侧增加尼龙保护层(该尼龙层可在深冲过程中保护铝箔);即方案C2的所述铝塑膜具有依次由内侧塑料热封层、中间金属箔(优选铝箔)、中间绝缘树脂层、和外侧金属箔(优选铝箔)、以及外侧塑料保护层(例如尼龙层)复合形成的叠层体。其中,铝塑膜中内侧塑料热封层与铝箔的复合方式可选择现有技术中的干法复合,更优选为热法复合。内侧的塑料热封层也可以是热塑性树脂薄膜层,外侧的塑料保护层也可以是耐热性树脂薄膜层。复合层铝箔中皮材的腐蚀电位比芯材的腐蚀电位低5mV-500mV。进一步的,皮材的腐蚀电位比芯材的腐蚀电位低50mV-500mV。优选地,皮材的腐蚀电位比芯材的腐蚀电位低70mV-200mV。更为优选地,皮材的腐蚀电位比芯材的腐蚀电位低100mV-170mV。上述电位差是指在复合之前或热处理之前的电位差。本实用新型复合层铝箔通过将芯材和皮材堆叠轧制复合得到。优选地,本实用新型中所述复合层铝箔由芯材和皮材复合后,再对芯材和皮材之间进行元素扩散处理。元素扩散处理的手段可以是高温退火处理。通过上述元素扩散处理可使得复合层铝箔中各元素含量在厚度方向上连续逐步变化,这可使得腐蚀更趋于缓慢的层状腐蚀。故优选地,本实用新型中所有复合层铝箔,在与塑料层复合形成铝塑膜之前,均已经经过了上述元素扩散处理。若金属复合层间仅采用电镀或轧制的方式复合、未进行元素扩散处理,其层间元素含量突变、层间电位突变,将导致其在冷却水中腐蚀时复合层整层的快速腐蚀脱离,其腐蚀速度甚至快过单层金属。所以本实用新型优选地对金属复合层间进行元素扩散处理。另外,不同于换热器上采用的复合层,由于换热器需通过高温钎焊,钎焊的过程也即是元素扩散的过程,故换热器用复合层铝箔使用前不需要特别的元素扩散处理工艺,而本实用新型铝塑膜用复合层铝箔没有上述钎焊过程,故优选需要专门的铝箔复合层间元素扩散工艺。本实用新型所述复合层铝箔的一种制造方法A,其包括以下步骤:1)按元素配比分别制造芯材合金和皮材合金;2)通过轧制使芯材合金和皮材合金复合。在本实用新型的一个实施方案中,上述步骤2)包括:任选实施的均匀化、铣面、复合、加热、热轧、冷轧以及中间退火。然后,精轧轧至成品厚度。最后,对复合层铝箔进行元素扩散处理(如退火)得到使用状态的铝箔,以供后续与塑料层复合使用制造铝塑膜。本实用新型复合层铝箔的另一种制造方法B,其包括以下步骤:1)按元素配比分别制造芯材合金和皮材合金;2)使芯材合金和皮材合金轧制复合;3)对上述轧制复合的复合层铝材先进行元素扩散处理(如退火处理),以使得复合层铝材截面上具有适当的元素分布梯度;4)然后对上述具有适当元素分布梯度的复合层铝材进行冷轧,并冷轧至使用厚度。在上述制造方法B的步骤中,可以将热轧工艺安排在步骤2)之后,也可以将热轧工艺安排在步骤3)之后。在上述制造方法B中,通过元素扩散处理(如退火处理)使得复合层铝材截面上具有适当的元素分布梯度,有利于后续铝箔成品的缓慢均匀腐蚀;但退火处理的同时也会导致再结晶晶粒长大,从而导致深冲性能变差。然而冷轧工艺有利于晶粒细化。本实用新型上述复合层铝箔的制造方法B的一个特征即是将元素扩散工艺置于冷轧工艺之前,这样既可以保证适当的元素扩散,又保证成品铝箔的晶粒不至于过大。在本实用新型制造方法B的一个实施方案中,上述步骤2)包括:任选实施的均匀化、铣面、加热以及中间退火。本实用新型中所述复合层铝箔优选是通过采用上述制造方法B得到的。本实用新型中,若未特别说明的,腐蚀电位均指为在水基冷却液环境下的腐蚀电位。复合铝箔中皮材与芯材的合理的电位匹配有利于避免铝箔(特别是芯材)的点腐蚀。可以通过向铝合金中添加不同含量的锌元素来调整铝合金的腐蚀电位,铝合金中锌元素含量越高,腐蚀电位越低。本实用新型中若未特别说明,所述冷却水和所述冷却液均指水基冷却液。所谓水基冷却液,是指以水作为基本成分的冷却液。水基冷却液中还可以是包含有各种防冻剂(比如乙醇、乙二醇、丙二醇等)以形成具有防冻功能的防冻液。所以,本实用新型的冷却液包含有如下种类:纯水、乙二醇与水的混合液等。作为一种优选方案,上述复合铝箔层的芯材由耐腐蚀的铝合金或纯铝形成。所述纯铝包括工业纯铝和高纯铝。所述纯铝中铝的含量优选≥99.0%,更为优选为99.0%-99.99%。本实用新型所述的耐腐蚀的铝合金,是指在与冷却液直接接触的环境下,铝合金和铝塑膜能长期保持正常的功能而不失效,比如铝合金不被冷却液腐蚀穿孔。其中所述“不失效”包括铝塑膜的电绝缘功能不失效且水汽阻隔功能也不失效。其性能虽然有量上的衰减,但仍能满足基本要求。其中所谓的“长期”,是指产品(如汽车或汽车动力蓄电池)正常的寿命周期时长,比如寿命大于5年,优选大于10年,更为优选大于15年。若铝箔层为复合层,由芯材和皮材复合形成,芯材位于内侧,皮材位于外侧,且皮材的腐蚀电位低于(或称负于)芯材的腐蚀电位。在与有腐蚀性介质接触时,形成电化学腐蚀,皮材作为被牺牲的阳极,保护作为阴极的芯材,从而确保铝塑膜中的铝箔层能够长期耐水基冷却液腐蚀,进而确保电池的使用寿命。其中,皮材可以是单层铝材,也可以是多层铝材。若皮材为多层,则优选地多层皮材由内到外腐蚀电位依次降低。皮材厚度优选占整个铝箔层的8~50%,更为优选为10±2%。本实用新型所谓内侧是指应用于软包电池时,靠近电芯内部电解质的那侧;所谓外侧是指应用于软包电池时,远离电芯内部电解质的那侧。其中,芯材也可称为铝基材。塑料层可以是现有技术中各种成熟应用的塑料层,如内层采用流延聚丙烯薄膜(CPP),外层采用尼龙薄膜(ON)或/和聚酯薄膜(PET),且塑料层与铝箔层之间可以采用现有工艺中粘合剂干法复合或热法复合。本实用新型铝合金命名采用美国铝业协会相应标准。作为一种优选方案,该铝塑膜采用复合层铝箔,复合层铝箔中芯材为纯铝或铝铁铝合金,复合层铝箔的外侧皮材为铝锌铝合金。锌元素在该铝锌铝合金中的含量优选为1%-10%,更为优选为2%-5%。作为一种更优选的方案,该铝塑膜采用复合层铝箔,复合层铝箔中芯材为纯铝或铝铁铝合金,复合层铝箔的外侧皮材为铝锌铁铝合金。铁元素在该铝锌铁铝合金中的含量优选为0.8%~3.0%,更优选为1.0%~2.0%。铁元素在该铝铁铝合金中的含量优选为0.8%~3.0%,更优选为1.0%~2.0%。上述方案包括:所述元素的含量可以是轧制态时的含量,或者所述元素的含量也可以是退火后的含量。但上述锌元素和铁元素含量优选是指轧制态(即退火处理前或元素扩散前的状态)时的含量。若未特别说明,本实用新型所述铝合金中的元素含量均优选默认为轧制态时的含量。所谓铝铁铝合金是指在该铝合金中除铝元素之外的其他元素中铁元素的含量最大(即该铝合金中铝元素的含量最多,铁元素含量为第二多);同样,所谓铝锌铝合金是指铝合金中除铝元素之外锌元素为含量最大的添加元素的铝合金(即该铝合金中铝元素的含量最多,锌元素含量为第二多)。所谓铝锌铁铝合金是指该铝合金中铝作为基础元素含量最多,锌元素含量第二多,铁元素含量第三多。除了上述元素外,上述铝合金中还可以添加少量的硅元素、铜元素、稀土元素以改善其变形性能和耐蚀性能。在上述铝合金中,铁元素可以细化晶粒提升变形性能,锌元素可以调节腐蚀电位改善腐蚀形态。以上铝铁铝合金、铝锌铝合金、和铝锌铁铝合金中的上述元素含量只是作为优选或示例,在本实用新型教导下并结合现有知识,本领域技术人员通过合理预测或常规试验即可得到合适的完整的合金元素组分配比,还可以得到其他等同的技术方案甚至稍优的技术方案。作为上述铝塑膜的一种优选方案,其特征在于,该铝塑膜采用复合层铝箔,复合层铝箔中芯材的成分质量百分比配比为:Fe:0.8-1.8wt%、更优选为1.0-1.5wt%,Si:0.1-0.3wt%,Mn:0.1-0.5wt%、更优选为0.2-0.3wt%,Cu:≤0.1wt%,Zn≤0.2wt%,Zr:0.01-0.2wt%,其余为Al;其外侧皮材的成分配比为:Zn:2.0-7.0wt%、更优选为3.0-4.0wt%,Fe:0.8-1.6wt%,Si:0.1-0.3wt%,Mn:0.1-0.3wt%,Cu:≤0.1wt%,Zr:0.01-0.2wt%,其余为Al。需要说明的是,所述“余量为铝”或“其余为Al”并不排除铝合金中存在不可避免的杂质。其中,通过在皮材中添加适当的锌元素,可以降低皮材的腐蚀电位,使得皮材优先腐蚀,且控制锌元素层间含量分布梯度从而实现腐蚀形态为层状腐蚀;通过在铝合金中添加锰元素,可提高铝合金的耐蚀性和强度;通过在铝合金中添加铁元素,可细化铝合金的晶体粒径,提高其延展性和深冲性能。本实用新型所述的铝箔泛指为薄膜状(或薄片状)的纯铝或铝合金,故本实用新型铝箔也可以说是铝膜,厚度可选为200微米以内的铝膜,也可选为200-300微米或300-500微米厚的铝膜。或者,进一步的,铝塑膜中铝箔层的厚度优选为40-300微米,更优选为100-300微米,再更优选为100-200微米。或者,铝塑膜中铝箔层的厚度可选择为80-100微米,或者100-150微米,或者150-200微米,或者200-300微米。铝箔层的热处理状态优选为退火状态(O态)。铝箔层的外部可通过离型剂粘合塑料保护层。这样铝箔层外部的塑料保护层便于被分离。以上技术方案中,铝塑膜的铝箔层为复合层铝箔,则该铝箔层的芯材可以是3系铝合金、或者1系铝合金、或者8系铝合金;其铝箔层的皮材可以是7系铝合金。其中,芯材更优选为1系铝合金或8系铝合金,具有这样芯材的复合层铝箔具有更好的耐蚀性和变形能力。本实用新型以上提供的铝塑膜的铝箔层抗蚀性良好,铝箔层和含有该铝箔层的铝塑膜具有长期耐冷却液腐蚀性能。本实用新型上述的铝塑膜,为电池包装用铝塑膜,所述铝箔层具有阻水层的作用。作为可选方案,上述铝箔层内侧还可以具有防腐蚀处理层,该防腐蚀处理层为铬酸盐处理形成、或者由稀土氧化物处理形成,但并不是必需的。本实用新型中仅包含内侧塑料层的铝塑膜浸泡在导电冷却液中,铝箔层与导电冷却液电连通。在极少数情况下,当电池电解质穿过内侧塑料层达到铝箔层时,电解质与铝箔层、导电冷却液以及外部接地线形成电连通,进而可触发绝缘电阻报警,及时探测到氢氟酸对铝箔的腐蚀,并防止电解液泄漏等危险发生。所以,本实用新型热管理系统中铝塑膜铝箔内侧若不做传统的防腐蚀涂层处理,电池及整个系统的安全性能仍能得到保障。本实用新型提供还如下铝塑膜,所述铝塑膜或其铝箔层具有如下耐冷却液腐蚀性能:耐腐蚀测试方法为OY水溶液(OyamaWaterSolution)腐蚀试验;该铝塑膜或其铝箔层的在上述试验中的耐腐蚀寿命大于500小时。进一步的,所述铝塑膜或其铝箔层的耐腐蚀寿命大于1000小时。更进一步的,所述铝塑膜或其铝箔层的耐腐蚀寿命大于2000小时。本实用新型中上述满足OY水溶液耐腐蚀性能要求的铝塑膜的铝箔厚度优选为大于80微米,进一步优选大于100微米,更进一步优选为120微米-300微米。现有技术中厚度为40微米的8系(如8021或8079)铝箔在OY水溶液腐蚀试验中的寿命约为98小时,根本不能满足车辆设计寿命要求,故不能满足防冻液浸泡式冷却方式的要求。因此,若需具有上述耐腐蚀性能,铝塑膜中铝箔需要具有合适的铝合金材料组成和/或合适的厚度。满足上述耐冷却液腐蚀性能要求的铝箔材料可从如下材料中选取:单层的1系铝合金(纯铝)、单层的3系铝合金、或具有牺牲阳极保护功能的复合层铝合金。满足上述耐冷却液腐蚀性能要求的铝箔厚度可从如下厚度中选取:80-120微米、或120-150微米、或150-200微米、或200-300微米。比如厚度大于150微米的纯铝AA1050,或者厚度为100微米的AA1050与20微米的AA7072复合形成的复合层铝合金(即复合层铝合金总厚度120微米),选用以上两种铝箔用于制造铝塑膜可满足上述耐防冻液腐蚀寿命要求,从而可满足汽车寿命要求。除了从铝箔角度解决上述耐腐蚀寿命问题之外,还可以从外侧塑料层改善铝塑膜的耐水腐蚀寿命问题。比如,该外侧塑料层为耐水解的塑料层。进一步的,该外侧塑料层为特氟龙层、或者PE层、或者PE层与PA层的复合材料、或者PA的耐水改进层。或者,若外侧无塑料层,即铝箔为外层材料,则可在铝箔层外表面做防腐涂层,如铬化处理、或稀土氧化物处理。这些方案虽可采用,但不是本实用新型优选方案。或者,从整车应用角度进行描述,优选铝塑膜或其铝箔耐冷却液(如主要由乙二醇和水组成的防冻液)腐蚀的寿命为大于5年,优选大于10年,更为优选大于15年。本实用新型若未特别说明,所谓寿命,是指铝塑膜和其铝箔在寿命期限内不能出现腐蚀穿孔的缺陷。本实用新型为了得到上述耐冷却液腐蚀性能,铝塑膜中铝箔需要选用上述合适的铝合金材料和足够的厚度。比如优选地,该铝塑膜由铝箔层和复合于铝箔上的热塑性树脂薄膜构成,其中铝箔为具有牺牲阳极功能复合层铝箔,厚度优选为100至300微米。现有的铝塑膜产品没有考虑到浸泡于防冻液中的应用,也不具备长期浸泡于防冻液中而不失效的功能;而本实用新型的铝塑膜产品具备上述特殊特征。进一步的,该铝塑膜或其铝箔还同时具有深冲性或成型性。或者说,该铝塑膜或其铝箔还同时具有良好的深冲性或成型性。或者说该铝塑膜还同时具有良好的深冲成型性。或者该铝塑膜或其铝箔还同时具有良好的杯突值。因其深冲性可以以杯突值来衡量。比如,以GB/T4156-2007《金属材料薄板和薄带埃里克森杯突试验》标准测试,该铝塑膜或铝塑膜中的铝箔的冲压深度值或杯突值大于5毫米,优选大于10毫米,更优选为大于12毫米。其中所谓冲压深度值或杯突值,是指铝塑膜或其铝箔在该值以内的冲压后或杯突测试后不能出现穿孔现象。进一步的,本实用新型还提供一种铝塑膜,所述铝塑膜包括铝箔层和复合于铝箔层表面的塑料层;铝箔层为复合层铝箔,铝箔层包含有芯材和位于芯材外侧的皮材,铝箔层的皮材的腐蚀电位低于芯材的腐蚀电位;其中,位于芯材外侧的皮材由两层皮材或多于两层的多层皮材复合形成,腐蚀电位由内向外依次降低。由此形成面腐蚀梯度,更有利于防止点状腐蚀。或者说优选地,所述铝箔层的横截面上,外侧的电位逐步低于或等于内侧的电位(或Zn含量由内向外逐步增加)。为了形成电位梯度,还可以对复合层铝箔进行高温加热处理,让皮材中锌元素向芯材逐步扩散,从而铝箔层由外到内的过程中,锌元素的含量连续逐步的变化(如图8所示),腐蚀电位也连续逐步变化,避免了如图7所示的锌元素含量和腐蚀电位断崖式变化或突变,从而更有利于腐蚀形态转化为均匀的层状腐蚀。优选地,在已经退火等热处理扩散后的情况下,整个复合层铝箔的横截面内的腐蚀电位的最大值与最小值之差小于250mV(毫伏),更优选小于200mV。或者优选地,整个复合层铝箔的横截面内任一部位的腐蚀电位梯度小于3毫伏/微米,更优选地小于2毫伏/微米。复合层铝箔的防腐机理不同于铝箔表面铬化等传统的防腐涂层处理方式,复合层铝箔本身都是铝材,其通过调整铝箔内部不同层的腐蚀电位改善腐蚀形态,即由点腐蚀引导为层状腐蚀,防止铝箔穿孔和电池失效。若采用铝箔外表面铬化处理后浸泡在冷却水中,虽然可以降低铝箔的腐蚀速率,但不能改善铝箔的腐蚀形态,对点腐蚀的抑制作用不大。值得说明的是,通过退火处理或高温扩散处理后,上述复合层各层之间的界限已不是十分明确,各层之间成分及电位不是阶梯式的突变,而是一个渐变的过程。所以本实用新型所述的复合层铝箔,既包括未高温处理前的多层不同铝合金之间的复合;也包括高温处理后,在垂直于铝箔表面的方向上,铝箔中元素含量渐变或腐蚀电位渐变的复合层。比如,高温退火工艺条件可以选择为:退火温度260~400摄氏度,退火时间1.5~3.5小时;也可经过多次退火以达到理想状态。本实用新型提供如下软包电池热控制装置,包含有由上述任一种电池包装材料包装的软包电池,还可进一步包括冷却液,所述软包电池的外包装与冷却液直接接触。其中,所述软包电池优选为扁平形状,所述扁平形状优选为长度/厚度和宽度/厚度的值分别独立地至少为5,更优选为至少为10,更优选为至少为15,更优选为至少为50,更优选为至少为100。进一步的,所述的电池热控制装置所包括的冷却液为水、或者包含乙醇与水的混合液、或者包含乙二醇与水的混合液、或者包含丙二醇与水的混合液、或者其他防冻冷却液。这些冷却液为目前汽车上和工业上常用的冷却液,它们不是绝缘型冷却介质,而是具有导电性能(包括微弱的导电性能)的导电冷却液;但是,相比于硅油或变压器油之类的绝缘型冷却介质,上述导电冷却液具有导热系数高、流动性好、导热效率高以及成本相对廉价等优点。在以上基础上,本实用新型提供如下软包电池热控制装置,该软包电池热控制装置包含有软包电池和冷却液,所述软包电池的外包装与冷却液直接接触,软包电池采用以上所述的包装材料包装的软包电池中的一种或几种。其中,冷却液为导电冷却液。本实用新型软包电池优选采用电解质包含六氟磷酸锂的软包电池。进一步的,该热控制装置还包括隔板;所述隔板的至少部分表面与所述软包电池至少部分外表面直接接触,并且隔板内设有流体通道;若干个软包电池组成一个电池单元,电池单元与隔板间隔设置。所述若干个软包电池可以是1个、或2个、或多个组成一个电池单元。当该软包电池热控制装置有水基冷却液时,水基冷却液在流体通道中流动,水基冷却液与软包电池直接接触换热。在一种更优选实施例中,所述隔板包括两个平板,两个平板分别与一个电池单元接触,两个平板之间设有连接在至少一个平板上的连接板,从而在两个平板之间形成流体通道。在另一种更优选实施例中,所述隔板为翅片结构,优选地,翅片之间依次连接,所述连接方式可以是“V”形、“U”形、梯形、弧形、锯齿形等连接,并且相邻翅片之间可以是平行或形成一角度,从而在相邻翅片之间形成所述流体通道。相邻电池单元之间的间隙(D)优选为小于10毫米,进一步优选为小于2毫米。其中,更优选地,所述翅片结构包括竖板以及竖板两端的平板,所述平板与电池直接接触。更优选地,所述翅片结构包括两组所述的平板,所述两组分别与相邻的两个电池单元中的一个电池单元接触,各组中包括多个平板。更优选地,各个平板只连接两个竖板。所述竖板并不必然与所述平板垂直,也可以是倾斜连接在平板上。在一种更优选实施例中,所述翅片上还可以设有孔。在另一种更优选实施例中,所述翅片可以是直板翅片、波浪形翅片中的任意一种或几种,其中,所述波浪形翅片在弯曲处可以是弧形、也可以是形成尖角(如锐角、直角或钝角),更优选为弧形。其中,相邻两个电池单元之间的隔板可以是一个隔板或者是多个子隔板组成的子隔板组,例如,多个子隔板在两个电池单元之间间隔排布;所述子隔板结构选自上述隔板结构中的任意一种或几种。所述隔板优选采用金属材料(如铝合金、不锈钢等);隔板的腐蚀电位等于或负于铝塑膜中铝箔腐蚀电位。进一步的,所述隔板采用金属材料;隔板的腐蚀电位负于铝塑膜中铝箔腐蚀电位,或者隔板的腐蚀电位等于或负于铝塑膜中铝箔的皮材的腐蚀电位。所述隔板起支撑软包电池作用和组织流场作用,隔板可以是挤压扁管,也可以是平直翅片、错列锯齿翅片等各种形式的翅片。本实用新型中上述翅片是隔板的一种,或者说是具有流体通道的翅片式隔板。这些翅片隔板发挥分隔相邻的电池单元并形成流道的作用,并对电池单元进行支撑和固定,这样,该软包电池热控制装置就具有可靠的抗振动强度,从而可以用于汽车等振动环境中。本实用新型所述翅片隔板不包括不能支撑电池单元的针形翅片之类的翅片。另外本实用新型翅片隔板内部具有流体通道(或流道),且流体通道与软包电池直接接触。电池单元与翅片隔板紧密地间隔设置组成一个整体,并可以采用绑带或贯穿螺栓将该整体紧固在一起。相比于扁管或现有技术中其他形式的隔板,本实用新型翅片隔板不仅结构更简单,而且由于没有隔板壁面所以传热效率更高。上述翅片没有耐高温作用或要求,所以翅片隔板不拘泥于采用金属材料,也可采用ABS、PP等塑料材料。进一步的,所述铝塑膜将所述电池芯体四周密封,仅电池电极、或电极连接端口从所述铝塑膜中伸出;电池热控制装置还包括主板,所述主板上设有插口,所述电池从铝塑膜内伸出的部分通过所述插口插入到主板上。进一步的,所述电池热控制装置还包括外壳体,所述外壳体内部设有容纳腔室,所述电池单元与隔板均置于所述外壳体的容纳腔室内,所述外壳体还包括流体入口和流体出口。或者,进一步的,该热控制装置还包括主板和外壳体,主板和外壳体形成密封腔,软包电池的电极伸出于主板之上,软包电池的本体置于密封腔中。除上述形式的装置外,热控制装置还可以具有多个主板形成多个密封腔。进一步的,所述主板位于所述外壳体的容纳腔室内,并将所述容纳腔室隔开成为两个部分,第一部分容纳电池单元主体以及隔板,第二部分容纳从所述铝塑膜伸出的电极和/或电极连接端口部分,所述第一部分和第二部分之间物理隔绝。本实用新型所述电池热控制装置,还可以包括冷却泵、冷却液换热器和相应的水管;或者本实用新型提供一种电池冷却系统,其采用上述电池热控制装置,还包括冷却泵(优选为低于24伏特的低电压水泵,进一步优选为12伏电动水泵)、冷却液换热器(优选为微通道形式的冷却液换热器)和相应的水管(水管内径优选为20毫米以内)。其中,冷却液换热器为冷却液与环境空气进行直接热交换的气液热交换器。本实用新型还提供使用上述任一种软包电池热控制装置冷却电池单元的方法,该热控制装置的流体通道中容纳有水基冷却液。该方法包括将热能从所述电池单元传导至所述铝塑膜中。该方法还包括将热能从所述铝塑膜直接传导至水基冷却液(和/或所述翅片)中以冷却所述电池单元。可以发现,相比于现有技术中的电池水冷方式,本实用新型中电池所产生的热能从电池单元传导至冷却水的中间环节非常少,且没有固体之间的接触热阻,所以传热效率非常高。由于采用上述电池热控制装置,电池的换热效率非常高,电池本体与冷却液之间的传热热阻非常低、换热温差非常小;所以,在保证电池本体内物质(如电解液、隔膜和固体电解质界面膜SEI)不超温的前提下,可以允许冷却液有更高的温度,即降低了电池冷却对外界的要求,降低了冷却成本,从而可以使用上述气液热交换器。进一步的,上述冷却系统还可以包括电加热器,以用于给电池加热。本实用新型以上耐冷却液腐蚀的铝塑膜和由此铝塑膜包裹的软包电池中,铝箔层或者一开始便作为触水层与冷却液接触,或者待外侧保护层(如尼龙膜)剥离后作为触水层与冷却液接触。本实用新型提供另一种电池用包装材料,其由金属箔和位于金属箔内侧的热塑性树脂薄膜复合形成;或者其由热塑性树脂薄膜和金属箔以及耐热性树脂薄膜复合形成,金属箔位于热塑性树脂薄膜和耐热性树脂薄膜之间;其中,金属箔为具有抗蚀性的单层金属,或者金属箔优选为包含有芯材和位于芯材外侧的皮材的复合层金属箔,金属箔的皮材的腐蚀电位低于芯材的腐蚀电位。所述金属箔优选为铝箔和/或铜箔和/或不锈钢箔。金属箔的厚度优选为20到50微米、或50到80微米、或80到150微米、或150到200微米、或200到300微米。优选地,金属箔外侧不含有塑料膜,即塑料膜仅复合于金属箔的内侧。作为可选方案,上述金属箔层内侧还可以具有防腐蚀处理层,该防腐蚀处理层为铬酸盐处理形成、或者由稀土氧化物处理形成。从另一个角度,本实用新型还提供如下软包电池解决方案,即一种软包电池,其采用铝塑膜包装,该软包电池本体具有如下耐冷却液腐蚀性能:耐腐蚀测试方法为:OY水溶液腐蚀试验;将该软包电池的本体浸泡于冷却液中,该软包电池的在上述试验中的耐腐蚀寿命大于500小时。进一步的,所述软包电池本体的耐腐蚀寿命大于1000小时。更进一步的,所述软包电池本体的耐腐蚀寿命大于2000小时。或者,上述耐腐蚀试验方法为ASTMD2570标准中内部耐腐蚀性能试验,或者采用类似QC/T468-2010标准中的5.14节“内部腐蚀性能试验”方法对其外包装铝箔进行评估。本实用新型中所指的OY水溶液(OyamaWaterSolution)腐蚀试验为热交换器铝热传输行业通用的OY水溶液腐蚀试验。本实用新型所述的铝塑膜制造方法,包括:首先通过如下耐水溶液腐蚀试验选择相应的铝箔:耐腐蚀测试采用OY水溶液腐蚀试验方法,该铝箔的在该腐蚀试验方法下的耐腐蚀寿命大于500小时;然后再将该铝箔和塑料薄膜进行复合形成铝塑膜。其中耐腐蚀寿命优选为大于1000小时。更优选为大于2000小时。所述铝箔可从上述纯铝或铝合金中选取。本实用新型还提供如上所述任一电池热控制装置在用电设备或发电设备上的应用。本实用新型还提供一种用电设备,所述用电设备设有本实用新型所述的任一电池热控制装置、以及用电部件,所述电池单元的电极与所述用电部件之间电连接。其中,所述用电设备可以是运输设备、电器、照明设备、电动工具、电子计算机中的任意一种或几种,如电动汽车、电动自行车、电动摩托车、大型电子计算机、电力机车、飞行器、邮电通讯等。本实用新型还提供一种发电设备,所述发电设备包括发电机以及本实用新型所述的任一电池热控制装置,所述电池热控制装置的电极与所述发电机之间电连接。其中,所述发电机可以是风力发电机、太阳能发电机、水力发电机、核能发电机、火力发电机中的任意一种或几种,并且所述发电机可以是单个发电机也可以是多个发电机组成的发电机组。本实用新型还提供如上所述任一电池热控制装置在交通工具或储能装置上的应用。上述电池热控制装置可以应用于新能源汽车、飞机、船舶等各种交通工具,以及可以应用于家用储能装置或太阳能、风能等商用储能装置。本实用新型还提供一种交通工具(该交通工具可以是新能源汽车,也可以是飞机或船舶),该交通工具包含有上述任一种软包电池、或/和包含有上述任一种软包电池热控制装置、或/和采用上述冷却电池单元的方法。其中优选地,软包电池采用具有上述任一种复合层铝合金的铝塑膜包装。进一步的,该交通工具的动力电池的母线电压高于100V(伏特),更优选地高于200V。进一步的,该交通工具具有驱动电压低于36V的电动水泵,优选为低于24V、更优选为12V的电动水泵。进一步的,该交通工具的软包电池的正极材料为磷酸铁锂或锰酸锂或三元材料。本实用新型提供一种储能装置,该储能装置包含有上述任一种软包电池、或/和包含有上述任一种软包电池热控制装置、或/和采用上述冷却电池单元的方法。进一步的,上述设备或装置的电池的母线电压高于100V(伏特),更优选地高于200V。进一步的,上述设备或装置具有驱动电压低于36V的电动水泵,优选为低于24V、更优选为12V的电动水泵。进一步的,上述设备或装置的软包电池的正极材料为磷酸铁锂或锰酸锂或三元材料。上述任一电池热控制装置为冷却水直接浸泡式电池热控制装置。其换热效率非常高。传统铝塑膜基本上没有长期耐水解的需求和特性,或者为了改善铝塑膜外层耐空气中水汽水解能力,通常是改善外层塑料膜的耐水解能力,比如采用含氟的外层塑料保护膜,但其成本、工艺和热效率方面均较差。本实用新型提供的多个技术方案中更优选的方案之一是,热控制装置中电池的铝塑膜的铝箔仅内侧复合有热塑性塑料薄膜,即铝箔外侧不含有耐热性塑料膜或保护膜,铝箔直接与冷却水接触换热。本实用新型铝塑膜中的铝箔不仅具有阻隔水汽等作用,并具有长期耐水解耐腐蚀的作用,还具有成型和包装作用。相比于现有铝塑膜,本实用新型的主要实用新型点之一在于铝塑膜中铝箔的改进并省略外侧塑料层,该铝箔通过采用了不同的结构和/或组分,改善了其抗腐蚀性和机械强度及硬度,故省略了外侧塑料膜之后的铝塑膜外侧仍然具有较好的耐化学介质腐蚀能力、抗针孔能力和耐擦伤能力,而且工艺更简便和成本更低,当该铝塑膜与冷却水接触换热时,其换热效率更高;更重要的是,本实用新型上述铝塑膜还具有新的功能,即具有能够长期耐冷却水腐蚀功能,故可以长期浸泡在冷却水中而不失效,从而更好地满足浸泡式水冷的软包电池冷却系统的热管理需求,为电池系统的性能提升提供了可靠的保障。本实用新型的铝塑膜省略了外侧尼龙层之后,由于铝箔中含有大量的合金元素,特别是皮材中含有大量的合金元素(如锌元素),起到了合金强化的作用(比如其抗拉强度大于80MPa,甚至大于100MPa),使得本实用新型铝塑膜中铝箔的抗拉强度大于传统铝塑膜中8系铝合金的抗拉强度,故即使没有外侧尼龙层的保护,其依然具有较高的机械强度和抗蚀性。而且,皮材的强度大于芯层,铝箔复合率越大,抗拉强度越高。本实用新型提供的多个技术方案中另一更优选的方案是,铝塑膜中铝箔通过采用内部层间不同腐蚀电位匹配的复合层铝箔,使得铝箔腐蚀形态更趋于层状腐蚀。相比于单层铝箔,上述复合层铝箔更好地避免铝塑膜中铝箔点蚀穿孔失效。在上述多个有关铝塑膜的复合层铝箔的技术方案中,其中更优选方案之一是采用纯铝或铝铁铝合金作为复合层铝箔的芯材,采用铝锌铝合金作为复合层铝箔外侧的皮材。不同于其他复合层铝箔,本实用新型中铝塑膜用于软包电池的外包装,需要同时兼顾变形性能和耐冷却水腐蚀性能,所以该铝塑膜中复合层铝箔不仅发挥了抗冷却水点蚀作用,同时还起到了良好的成型作用和包装作用。本实用新型提供的铝塑膜还可以是上述技术特征的组合形成的技术方案,相比于传统的铝塑膜,其具有新的功能,即可用于与冷却水长期直接接触的软包电池的包装,具有耐冷却水腐蚀、使用寿命长的优点。本实用新型还提供一种电池系统绝缘监测装置。所述绝缘监测装置具有上述任一种电池热控制装置,并具有绝缘电阻监测设备,其中绝缘电阻监测设备的一电极与上述软包电池的一极耳电连接,绝缘电阻监测设备的另一电极与接地端电连接(或与冷却水电连接),监测该绝缘电阻。当该绝缘电阻值下降到低于某一阈值时,即向车辆控制器发送报警信号;并可采取相应保护措施(比如可立即切断电池系统母线电源,并提醒驾驶员尽快逃逸或维修),从而防止热失控、或起火、或爆炸等恶性失效后果。由于电池铝塑膜浸泡在冷却水中,铝塑膜中铝箔与冷却水或接地端电连接,当软包电池的铝塑膜出现腐蚀穿孔、或电解液泄漏、或软包电池电极与铝塑膜中铝箔短路的时候,该绝缘电阻值将下降,从而触发报警;所以,该绝缘监测装置可有效地监控铝塑膜是否失效,从而保障电池系统的安全。本实用新型还提供一种电池系统绝缘监测方法。所述方法具有:在上述任一种冷却水浸泡式电池热控制装置的基础上,将绝缘电阻监测设备的一电极与上述软包电池的一极耳电连接,绝缘电阻监测设备的另一电极与接地端电连接(或与冷却水电连接),监测该绝缘电阻;当该绝缘电阻值下降到低于某一阈值时,即向车辆控制器发送报警信号,并可采取相应保护措施(比如可立即切断电池系统母线电源,并提醒驾驶员尽快逃逸或维修),从而防止热失控、起火、或爆炸等恶性失效后果发生。其中,导致绝缘电阻值下降的触发因素有:软包电池的铝塑膜出现腐蚀穿孔、或电解液泄漏、或软包电池电极与铝塑膜中铝箔短路。本实用新型还提供下列复合层铝箔的技术方案,其可用作为铝塑膜的铝箔:复合层铝箔方案1:一种可以应用于铝塑膜的铝箔,该铝箔为复合层铝箔,其采用铝铁铝合金作为芯材,芯材铁含量为0.9%~1.8%,硅含量为0.1%~0.3%,锰含量为0.1%~0.3%;采用铝锌铝合金作为外侧皮材,皮材锌含量为2.0%~5.0%,硅含量0.1%~0.3%。上述芯材和皮材的其余成分或者是由Al和不可避免的杂质构成,或者还可以含有其他元素。复合层铝箔方案2:一种可以应用于铝塑膜的铝箔,该铝箔为由芯材和皮材复合形成的复合层铝箔,所述芯材为含有如下组分的铝合金:Si≤0.25wt%;Cu≤0.05wt%;Mg≤0.05wt%;Zn≤0.05wt%;Mn≤0.05wt%;Ti≤0.03wt%;V≤0.05wt%;Fe≤0.4wt%;其余为铝;所述皮材为包括含有如下组分的铝锌铝合金:Zn4-7wt%;Si0.5-1.0wt%;Ti0.1-0.2wt%;Fe0.5-1.5wt%;或者;所述芯材为含有如下组分的铝合金:Si≤0.25wt%;Cu≤0.05wt%;Mg≤0.05wt%;Zn≤0.05wt%;Mn≤0.05wt%;Ti≤0.03wt%;V≤0.05wt%;Fe≤0.4wt%;Sm0.1-0.3wt%;其余为铝;所述皮材为含有如下组分的铝锌铝合金:Zn4-7wt%;Si0.5-1.0wt%;Ti0.1-0.2wt%;Fe0.5-1.5wt%;Sm0.1-0.3wt%。复合层铝箔方案3:一种可以应用于铝塑膜的铝箔,该铝箔为由芯材和皮材复合形成的复合层铝箔,其采用铝铁铝合金作为芯材,芯材铁含量为0.9%~1.8%,硅含量为0.1%~0.3%,锰含量为0.1%~0.3%;采用铝锌铝合金作为外侧皮材,皮材锌含量为2.0%~5.0%,硅含量0.1%~0.3%。复合层铝箔方案4:一种复合层铝箔,复合层铝箔中芯材的成分质量百分比配比为:Fe:0.8-1.8wt%、更优选为1.0-1.5wt%,Si:0.1-0.3wt%,Mn:0.1-0.5wt%、更优选为0.2-0.3wt%,Cu:≤0.1wt%,Zn≤0.2wt%,Zr:0.01-0.2wt%,其余为Al;其外侧皮材的成分配比为:Zn:2.0-7.0wt%、更优选为3.0-4.0wt%,Fe:0.8-1.6wt%,Si:0.1-0.3wt%,Mn:0.1-0.3wt%,Cu:≤0.1wt%,Zr:0.01-0.2wt%,其余为Al;所述“其余为Al”并不排除铝合金中存在不可避免的杂质。复合层铝箔方案5:一种复合层铝箔,所述复合层铝箔由下列芯材和皮材复合形成,所述芯材由具有以下质量百分比组成的铝合金制得:Si≤0.9wt%;Fe≤1.7wt%;Cu≤0.1wt%;Mn≤0.2wt%;Mg≤0.05wt%;Zn≤0.1wt%;Ti≤0.08wt%;Cr≤0.05wt%;其它杂质元素单个≤0.05%;其它杂质元素总计≤0.15%;其余为铝;所述皮材由具有以下质量百分比组成的铝锌铝合金制得:Zn4-7wt%;Fe0.5-1.5wt%。复合层铝箔方案6:一种复合层铝箔,所述复合层铝箔由下列芯材和皮材复合形成,其中芯材为8079或8021,外侧皮材由8系铝合金基础上添加质量百分比为1%-10%的Zn,更优选为2%-6%的Zn。复合层铝箔方案7:一种复合层铝箔,所述复合层铝箔由下列芯材和皮材复合形成,其中芯材为AA8079或AA8021或AA8011铝合金,外侧皮材由具有以下质量百分比组成的铝合金制得:硅元素质量含量为≤0.25%,铁元素质量含量为≤0.40%,铜元素质量含量为≤0.05%,锰元素质量含量为≤0.05%,镁元素质量含量为≤0.05%,锌元素质量含量为2.0~6.0%,钒元素质量含量为≤0.05%,钛元素质量含量为≤0.03%,其他元素质量含量为≤0.03%,余量为铝。复合层铝箔方案8:一种复合层铝箔,所述复合层铝箔由下列芯材和皮材复合形成,其中:芯材为AA8079或AA8021或AA8011,外侧皮材由具有以下质量百分比组成的铝合金制得:硅元素质量含量为0.20%,铁元素质量含量为0.30%,铜元素质量含量为0.03%,锰元素质量含量为0.03%,镁元素质量含量为0.03%,锌元素质量含量为4.0%,钒元素质量含量为0.03%,钛元素质量含量为0.01%,其他元素质量含量为≤0.03%,余量为铝。复合层铝箔方案9:一种复合层铝箔,所述复合层铝箔由下列芯材和皮材复合形成,其中:芯材为AA8079或AA8021或AA8011,外侧皮材由具有以下质量百分比组成的铝合金制得:硅元素质量含量为0.20%,铁元素质量含量为1.10%,铜元素质量含量为0.03%,锌元素质量含量为5.0%,其他元素质量含量为≤0.15%,余量为铝;或者,外侧皮材由具有以下质量百分比组成的铝合金制得:硅元素质量含量为0.1%,铁元素质量含量为1.2%,铜元素质量含量为0.03%,锌元素质量含量为4.50%,其他元素质量含量为≤0.15%,余量为铝。复合层铝箔方案10:一种复合层铝箔,所述复合层铝箔由下列芯材和皮材复合形成,其中芯材为AA8079或AA8021或AA8011铝合金,外侧皮材由具有以下质量百分比组成的铝合金制得:硅元素质量含量为0.05-0.30%,铁元素质量含量为0.70-1.3%,铜元素质量含量为≤0.05%,锌元素质量含量为1.0~10.0%,其他元素质量含量为≤0.15%,余量为铝;或者,外侧皮材由具有以下质量百分比组成的铝合金制得:硅元素质量含量为≤0.15%,铁元素质量含量为1.2~1.7%,铜元素质量含量为≤0.05%,锌元素质量含量为1.0~10.0%,其他元素质量含量为≤0.15%,余量为铝。本实用新型还提供如下包装材料方案:一种电池包装用铝塑膜,其具备上述复合层铝箔方案1到10中任一种复合层铝箔。本实用新型还提供如下铝塑膜方案:一种铝塑膜,其由内侧的塑料热封层和外侧的复合层铝箔复合形成,复合层铝箔为上述复合层铝箔方案1到10中任一种复合层铝箔。优选地,该铝塑膜的复合层铝箔外侧无塑料树脂层。热封层与铝箔层之间的所述复合方式可以为采用粘合剂的干法复合,或者可以为热法复合;更优选为热法复合。需要说明的是,本实用新型记载的各种技术方案中还包括上述技术特征和子方案的组合。为了表述简洁起见,本实用新型未对由上述各种技术特征和子方案的组合而形成的技术方案一一进行描述,但这些组合方案也应该属于本实用新型记载的范围,也都应涵盖在本实用新型的保护范围内。附图说明:图1为本实用新型优选的铝塑膜结构示意图。图2为软包电池热控制装置示意图。图3为单层铝合金(左图)与复合层铝合金(右图)抗点蚀性能对比测试效果图。图4所示为新能源汽车电池冷却系统示意图。图5本实用新型另一种多层结构的铝塑膜示意图。图6本实用新型所示的防止铝塑膜绝缘失效的电池系统绝缘监测装置。图7所示为复合层铝箔复合后轧制态(未退火)时,铝箔厚度方向上锌元素的含量分布;其中横坐标为厚度方向,纵坐标为锌元素质量含量;锌元素由皮材到芯材,其质量含量出现断崖式下降,表明轧制态时锌元素尚未扩散。图8所示为复合层铝箔复合后并经过2小时退火后,铝箔厚度方向上锌元素的含量分布;其中横坐标为厚度方向,纵坐标为锌元素质量含量;锌元素由皮材到芯材,其质量含量连续逐步降低,表明退火后锌元素由皮材向芯材逐渐扩散。具体实施方式下面结合具体实例对本实用新型进行进一步描述,本实用新型的保护范围包括但不限于此。实施例一本实施例所介绍的铝塑膜为由热塑性树脂薄膜(即热封层,如聚丙烯)和复合层铝合金铝箔复合形成。铝箔层的芯材层7采用牌号为1050的纯铝,皮材6由在纯铝1050基础上添加4%-7%锌元素的铝合金形成(简化表示为AA1050+4-7%Zn),皮材的腐蚀电位负于芯材,皮材作为牺牲阳极保护芯材,皮材复合率优选为20±2%。复合铝合金铝箔层的热处理状态为退火状态(O态),厚度优选为100-300微米,更为优选为100-200微米。相比传统的复合层铝合金,本实施例上述以纯铝为芯材的复合铝箔层既具有优良的耐冷却液腐蚀性能,又具有很好的延展性和深冲性能。所谓复合率是指皮材厚度占整个复合层(芯材+皮材)厚度的比率。该铝塑膜或其铝箔要求具有较好的延展性和深冲性能,比如以GB/T4156-2007《金属材料薄板和薄带埃里克森杯突试验》标准测试,该铝塑膜的铝箔的杯突值大于8毫米。该铝塑膜或其铝箔要求具有较好的耐冷却液腐蚀性能。耐腐蚀性能试验方法采用OY水溶液(OyamaWaterSolution)腐蚀试验。该OY水溶液腐蚀试验如下:OY水溶液组分:氯离子(Cl-):195±1毫克/升,硫酸根离子(SO42-):60±0.2毫克/升,铁离子(Fe3+):30±0.1毫克/升,铜离子(Cu2+):1±0.01毫克/升。OY水溶液的pH约为3(在未特别说明的情况下,本实用新型所述的OY试验中水溶液pH取值均约为3)。OY水溶液温度:88°C,以0.6-0.9m/s(200rpm)的速度搅拌8小时,然后静置16小时;重复上述循环。在上述OY水溶液腐蚀试验中,忽略接近铝箔边缘5mm的任何穿孔。当铝箔中除边缘5mm之外的任一点发生腐蚀穿孔时,所累积的腐蚀试验时间即为该铝塑膜铝箔在该OY水溶液中的耐腐蚀寿命。实验显示,本实施例铝箔耐腐蚀寿命大于1000小时。以上,铝塑膜或其铝箔的耐腐蚀寿命也可以以它在实车上浸泡于防冻液中的耐腐蚀使用寿命进行评估,如选用在实车上的使用寿命大于10年的铝塑膜。实施例五如图2所示,本实施例介绍的电池热控制装置采用以上可长期直接浸泡于冷却液(如主要由乙二醇与水组成的冷却液)中的软包电池。该软包电池热控制装置,包含有软包电池11和水基冷却液,所述软包电池11的外包装与冷却液直接接触,所述软包电池11为由上述任一种抗冷却液腐蚀的包装材料(如抗水基冷却液腐蚀的铝塑膜)形成。该热控制装置还包括隔板12,该隔板12优选为图7所示的错列锯齿翅片隔板或如图8所示的平直翅片隔板;隔板12的至少部分表面与所述软包电池11至少部分外表面直接接触,并且隔板12内设有流体通道121,流体通道121与电池11直接接触,同时流体通道121内的冷却水与电池11直接接触换热;一个软包电池11组成一个电池单元(当然也可以采用两个软包电池组成一个电池单元),电池单元与隔板12间隔设置。隔板一方面起支撑软包电池的作用,另一方面起组织冷却液流场的作用。相邻电池单元之间的间隙D优选为小于10毫米。所述铝塑膜将所述电池芯体四周密封,仅电池电极、或电极连接端口从所述铝塑膜中伸出;电池热控制装置还包括主板13,所述主板13上设有插口,所述电池从铝塑膜内伸出的部分(即正负电极极耳111)通过所述插口插入到主板13上。优选地,电池的部分顶边也通过所述插口插入到主板13上。所述电池热控制装置还包括外壳体14,所述外壳体14内部设有容纳腔室,多个所述电池单元与隔板12组成的紧密整体嵌入外壳体14的容纳腔室内,所述外壳体14还包括流体入口和流体出口(图中未示出)。所述主板13位于所述外壳体14的容纳腔室内,并将所述容纳腔室隔开成为两个部分,第一部分容纳电池单元主体以及隔板12,第二部分容纳从所述铝塑膜伸出的电极和/或电极连接端口部分,所述第一部分和第二部分之间物理隔绝。所述的电池热控制装置还包括冷却液,所述冷却液为水、或者包含乙二醇与水的混合液、或者包含丙二醇与水的混合液、或者防冻冷却液。优选地,所述隔板12采用金属材料;更优选地,隔板12的腐蚀电位负于铝塑膜中铝箔腐蚀电位,比如包装材料金属箔选用AA1050铝合金,隔板12选用AA1050+5%Zn。或者,隔板12的腐蚀电位负于铝塑膜的铝箔的皮材的腐蚀电位,比如包装材料金属箔选用复合材料AA1050/AA1050+3%Zn铝合金,隔板12选用AA1050+5%Zn。这样隔板还可以起阳极保护作用,进一步防止电池腐蚀失效。实施例九本实施例采用附图1所示结构的铝塑膜,其中铝箔由芯材和外侧皮材复合形成,其中芯材为100微米-300微米的8系铝合金(如8079或8021)形成,外侧皮材由8系铝合金基础上添加1%-10%(更优选为2%-6%)质量百分比的锌元素形成(如下表1所述方案1或方案2),复合率优选取10%-50%。含有这种复合铝合金的铝塑膜,其耐蚀性和深冲性都较良好,根据实施例一方法测试,其耐腐蚀寿命大于1300小时。表1元素硅铁铜锌铝其他总计方案1质量百分比%0.05-0.300.70-1.3≤0.051.0~10.0余量≤0.15方案2质量百分比%≤0.151.2~1.7≤0.051.0~10.0余量≤0.15实施例十本实施例采用附图1所示结构的铝塑膜,其中铝箔由芯材和外侧皮材复合形成,其中芯材为100微米-300微米的1系铝合金(如1050)形成,外侧皮材由1系铝合金基础上添加2%-6%质量百分比的锌元素形成(如表4所述),复合率取10%-20%。实施例十一本实施例采用附图1所示结构的铝塑膜,其中芯材为100微米-300微米的1系铝合金(如1050)形成,外侧皮材由1系铝合金基础上添加2%-6%质量百分比的锌元素形成(如表2所示铝合金)。含有这种复合铝合金的铝塑膜,其具有良好的耐电解液腐蚀功能和良好的耐冷却水腐蚀功能;根据实施例一方法测试,其耐腐蚀寿命大于1800小时。表2合金元素硅Si铁Fe铜Cu锰Mn镁Mg锌Zn钒V钛Ti铝Al其它质量百分比%≤0.25≤0.40≤0.05≤0.05≤0.052.0-6.0≤0.05≤0.03余量≤0.03实施例十二本实施例采用附图1所示结构的铝塑膜,其中铝箔由芯材和外侧皮材复合形成,其中芯材为150微米-300微米的8系铝合金(如8079或8021)形成,外侧皮材为7系铝合金(如7072)或铝锌铝合金,复合率取2%-20%或者20%-50%。进一步的,8系与7系复合后再进行加热或退火处理,以便Zn元素的适当扩散形成梯次电位变化。含有这种复合铝合金的铝塑膜,其耐蚀性和深冲性都较良好,根据实施例一方法测试,其耐腐蚀寿命大于1500小时。实施例十三本实施例对单层1050铝合金和复合层铝合金(芯材为1050铝合金、皮材为电位较负的牺牲层)在OY实验中进行耐蚀性对比试验。选择防冻液体系进行OY实验,实验时间为4周,实验后对材料表面进行硝酸浸泡去除腐蚀产物,具体情况如下:如图3中所示,防冻液体系OY试验4周后,左图所示为AA1050单层铝合金发生了较为明显的点蚀,点蚀较为严重;而右图所示为复合牺牲层的铝合金表面未发生明显的点蚀。由此可知,通过在铝合金芯材表面复合腐蚀电位较负的皮材,可以有效地抑制点腐蚀的发生。实施例十四本实施例提供一种软包电池热控制装置,其包括软包电池、金属材料的翅片(如锯齿翅片)和水基冷却液。所述翅片的至少部分表面与所述软包电池至少部分外表面直接接触。若干个软包电池组成一个电池单元,电池单元与翅片间隔设置,所述翅片支撑软包电池和组织流场并形成流体通道;水基冷却液在流体通道中流动,水基冷却液与软包电池直接接触换热。所述软包电池采用铝塑膜包装,所述铝塑膜由位于内侧的热塑性树脂薄膜和位于外侧的铝箔层复合形成,复合方式可以是热法复合也可以通过粘合剂干法复合,所述铝箔层与水基冷却液直接接触换热。其中,所述铝箔层包含有芯材和位于芯材外侧的皮材,铝箔层的芯材为1系铝合金(比如AA1050或AA1060)或8系铝合金(比如AA8021或AA8079),铝箔层的皮材为含锌2%-5%的铝锌铝合金,或者铝箔层的皮材由1系铝合金或3系铝合金或8系铝合金基础上添加2%-5%质量百分比的锌元素形成,或者铝箔层的皮材为含有2%-5%质量百分比的锌元素的铝合金。上述铝塑膜中的铝箔不仅具有阻隔水汽作用,并具有长期耐水解耐腐蚀的作用,且具有更高的机械强度和硬度而不需要外侧尼龙层的保护,还具有良好的成型性和包装作用。实施例十五本实施提供如附图1所示的铝塑膜,所述铝塑膜由铝箔层1和铝箔层内侧的热塑性树脂薄膜层3复合形成,其中,铝箔层1为复合层铝箔1,铝箔层1包含有芯材7和位于芯材外侧的皮材6,铝箔层的皮材的腐蚀电位低于芯材的腐蚀电位。芯材采用铝铁铝合金作为,外侧皮材采用铝锌铝合金。铝箔层1上仅内侧复合了热塑性树脂薄膜层3(也可称热封层3,比如采用PP),而无需外部尼龙防护层。相比于现有技术中具有外层塑料保护膜的铝塑膜,本实施例铝塑膜大胆省略了外侧塑料保护膜之后,同样具有较好的机械强度和硬度、水汽阻隔性和耐电解液性等特性,而且还具有长期耐外界水解功能,并且还简化了铝塑膜的复合工艺并节省了生产工艺成本和原材料成本。热封层3厚度优选为60-150微米,整个复合铝箔层1厚度优选为60~150微米。其中,皮材6复合于外侧,作为牺牲阳极;皮材6的厚度优选占整个铝箔层1的30%。当用作软包电池包装且电池浸泡在冷却水中时,该皮材作为触水层。内侧热塑性树脂薄膜层3与铝箔层1之间可通过粘合剂层(图中未示出)干法复合或者通过热法复合。由以上提供的铝塑膜制成的软包电池可长期浸泡在冷却液中,具备长期耐冷却液腐蚀功能。本实施例中铝塑膜的复合层铝箔,其采用铝铁铝合金作为芯材,采用铝锌铝合金作为外侧皮材。其中:芯材铁含量为0.9%~1.8%、优选为1.2%,硅含量0.1%~0.3%、优选为0.2%,锰含量为0.1%~0.3%、优选为0.2%;皮材锌含量为2.0%~5.0%、优选为4.5%,硅含量0.1%~0.3%、优选为0.2%。铁元素对降低芯材在回复再结晶过程中的晶粒长大速度、晶粒细化有显著的提高作用,同样厚度等情况下可使铝箔的延伸率相对于不含铁的铝合金(如相对于纯铝)提高约20%甚至更高(如相对于3系铝合金),由其制成的铝塑膜的杯突值达到9.6mm。复合层铝箔材料可通过如下制备方法,其包括以下步骤:(1)将各层按照配比,分别进行熔炼,并分别浇铸成铸锭,将所述铸锭进行切割铣面,在470-510℃均匀化处理,热轧;(2)将步骤(1)的产物,将芯材、皮材进行堆叠,经470-510℃均匀化处理后将铸锭在470-500℃条件下热轧,再然后冷轧至使用厚度。为了使得复合层铝箔横切面上的电位梯度分布更加合理,可进一步对复合层铝箔进行退火处理以让皮材中的锌元素向芯材方向适度扩散,如退火的工艺条件可以选择为:退火温度250~400摄氏度,退火时间1.5~3.5小时得到复合铝箔的使用状态;也可经过多次退火以达到理想状态。实施例十六本实施例在实施例十五的基础上进一步改进皮材的延展性,在上述皮材中添加0.9%~1.6%的铁元素、优选为1.0%,即得到铝锌铁铝合金:皮材锌含量为4.5%,铁元素为1.0%,硅含量为0.2%。这样可使同样厚度等情况下的复合层铝箔的延伸率进一步提高约5%,由其制成的铝塑膜的杯突值达到约10mm。实施例十七本实施例提供一种新能源汽车,其采用锂离子电池系统作为动力系统,其包含有如图4所示的电池冷却系统,该冷却系统包含有如实施例五所示的电池热控制装置A、冷却液换热器B、驱动电压为12V的电动水泵C和相应的水管。并且,电池热控制装置A中的软包电池采用如实施例九或实施例十一所述的铝塑膜包装。实施例十八本实施例提供一种储能装置,其包含有如图4所示的电池冷却系统,该冷却系统包含有如实施例五所示的电池热控制装置A、冷却液换热器B、驱动电压为24伏特的电动水泵C和相应的水管。并且,电池热控制装置A中的软包电池采用如实施例九或实施例十一所述的铝塑膜包装。实施例十九如图5所示,本实施例提供一种多层结构的铝塑膜,其特征在于依次由内侧塑料热封层11、中间铝箔层12、中间绝缘树脂层13、以及外侧铝箔层14复合形成的叠层体。其中,内侧塑料热封层起热封的作用,优选为聚烯烃树脂层或酸改性聚烯烃树脂层。中间铝箔(例如选择AA8079铝箔)可发挥阻隔内侧的电解液或导电离子向外渗透作用。中间绝缘树脂层可发挥绝缘作用,使得电解液与外侧铝箔之间的绝缘强度满足电气安全需要,该中间绝缘树脂层也可为中间绝缘薄膜,可选择绝缘强度高的、熔点比内侧塑料热封层熔点高的树脂层,例如,可选择聚酯膜、聚酰胺膜、聚丙烯膜等的拉伸或未拉伸膜、或者熔点较高的聚烯烃膜。外侧铝箔可发挥耐冷却水腐蚀作用,同时可阻隔外部水汽向内渗透,该外侧铝箔优选为上述任一种具有牺牲阳极功能的复合层铝箔,比如选择实施例十五或实施例十六所述的复合层铝箔;该铝塑膜各层的复合方式可选择现有技术中的采用粘合剂(图5中未示出该粘合剂层)的干法复合,更优选为热法复合。为了便于深冲,还可在外侧铝箔的外侧再复合一层保护树脂薄膜;例如采用离型粘合剂在外侧复合一层PA膜,在深冲后再将该PA层剥离。本实施例中的多层铝塑膜可更好地使得软包电池的电极与外侧铝箔之间的电气绝缘强度得到保障,提高安全性。由本实施例铝塑膜包装的软包电池浸泡在冷却水中时,冷却水与该铝塑膜的外侧铝箔14电导通,但冷却水与软包电池极耳之间仍保持足够的电气绝缘强度(如大于2000伏特)。实施例二十本实施例提供一种如图6所示的防止铝塑膜绝缘失效的电池系统绝缘监测装置和方法。在上述任一种冷却水浸泡式电池热控制装置的基础上,将绝缘电阻仪的一电极与上述软包电池的一极耳电连接,绝缘电阻仪的另一电极与接地端电连接(或与冷却水电连接),监测该绝缘电阻。当软包电池的铝塑膜出现腐蚀穿孔、或电解液泄漏、或软包电池电极与铝塑膜中铝箔短路的时候,该绝缘电阻值将下降,当低于某一阈值(依照国家标准GB/T18384.1-2001规定:绝缘电阻值除以电池系统标称电压,其结果应大于100欧/伏,最好大于500欧/伏;所以该电阻电压比阈值为100欧/伏,最好为500欧/伏;比如对于母线电压为350V的电池系统来说,该电阻阈值为35千欧,最好为175千欧)时,即向车辆控制器发送报警信号,并采取相应保护措施(比如可立即切断电池系统母线电源,并提醒驾驶员尽快逃逸或维修),从而防止触电、或起火、或爆炸等恶性失效后果。实施例二十一本实施例提供如下复合层铝箔,其可以应用于本实用新型如附图1所示的耐水浸泡腐蚀的铝塑膜,得到的铝塑膜可以应用于车辆上的软包电池的包装。一种复合层铝箔,复合层铝箔中芯材的成分质量百分比配比为:Fe:0.8-1.8wt%、更优选为1.2wt%,Si:0.1-0.3wt%,Mn:0.1-0.5wt%、更优选为0.2-0.3wt%,Cu:≤0.1wt%,Zn≤0.2wt%,Zr:0.01-0.2wt%,其余为Al;其外侧皮材的成分配比为:Zn:2.0-7.0wt%、更优选为3.0-4.0wt%,Fe:0.8-1.6wt%,Si:0.1-0.3wt%,Mn:0.1-0.3wt%,Cu:≤0.1wt%,Zr:0.01-0.2wt%,其余为Al;所述“其余为Al”并不排除铝合金中存在不可避免的杂质。更优选地,复合层铝箔中芯材的成分质量百分比配比为:Fe:1.2wt%,Si:0.2wt%,Mn:0.2wt%,Cu:0.05wt%,Zn:0.1wt%,Zr:0.05wt%,其余为Al;其外侧皮材的成分配比为:Zn:4.0wt%,Fe:1.2wt%,Si:0.2wt%,Mn:0.2wt%,Cu:0.05wt%,Zr:0.05wt%,其余为Al。本实施例采用该优选的复合层铝箔进行如实施例一所述的OY水溶液腐蚀试验。厚度为100微米~200微米,优选取150微米。皮材复合率取10%~50%,优选取30%。退火工艺可选为:退火温度为500℃,退火时间选择2.0h。样品数量取3个进行如实施例一所述的OY水溶液腐蚀试验,实验显示其腐蚀寿命>1000小时。腐蚀过程形态为缓慢的均匀的层状腐蚀。实施例二十二本实施例提供如下复合层铝箔,其可以应用于本实用新型如附图1所示的耐水浸泡腐蚀的铝塑膜,得到的铝塑膜可以应用于车辆上的软包电池的包装。一种复合层铝箔,所述复合层铝箔由下列芯材和皮材复合形成,其中:芯材为AA8079;外侧皮材中硅元素质量含量为0.1%、铁元素质量含量为1.2%、铜元素质量含量为0.03%、锌元素质量含量为4.50%、其他元素质量含量为≤0.15%、余量为铝。本实施例采用该复合层铝箔进行如实施例一所述的OY水溶液腐蚀试验。厚度为120微米、160微米,优选取160微米。皮材复合率可取10%~50%,本实施例取20%。退火工艺可选为:退火温度为500℃,退火时间选择2.0h。样品数量取3个进行如实施例一所述的OY水溶液腐蚀试验,实验显示其腐蚀寿命>1000小时。实施例二十三本实施例提供一种车辆,其包含有软包电池,其软包电池采用如实施例十九或实施例二十一或实施例二十二所述的铝塑膜包装。以上对本实用新型的具体实施例进行了详细描述,但其只是作为范例,本实用新型并不限制于以上描述的具体实施例。对于本领域技术人员而言,任何对本实用新型进行的等同修改和替代也都在本实用新型的范畴之中。因此,在不脱离本实用新型的精神和范围下所作的均等变换和修改,都应涵盖在本实用新型的范围内。需要说明的是,本实用新型记载的各种技术方案中还包括上述技术特征、子方案或具体实施例的组合或结合。为了表述简洁起见,本实用新型未对由上述各种技术特征、子方案或具体实施例的组合或结合而形成的技术方案一一进行描述,但这些组合方案也应该属于本实用新型记载的范围,也都应涵盖在本实用新型的保护范围内。当前第1页1 2 3