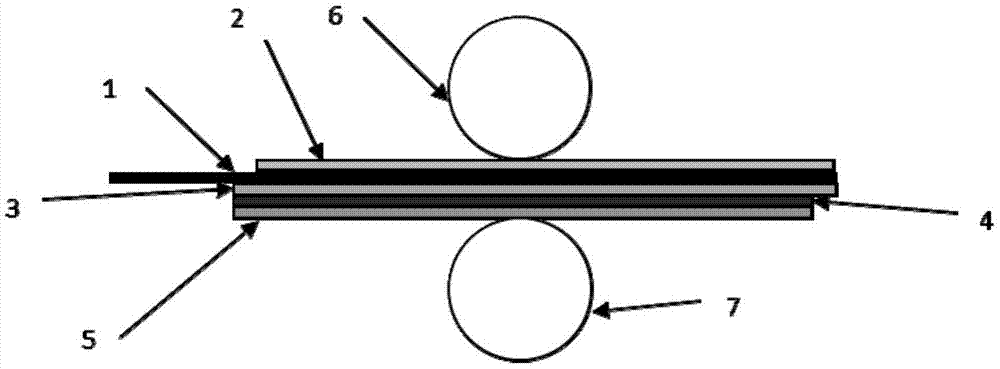
本发明属于磁性材料
技术领域:
,具体涉及一种软磁片及其制备方法和用途。
背景技术:
便携式智能终端、手机、数码相机、智能手表等电子设备中的锂离子电池的充电都是一个逆变器把交流电变换为直流电进行充电。而无线充电技术是把交流电变换成100khz及以上,然后利用电磁感应原理或磁共振原理通过供电线圈耦合到受电线圈,然后经过交流变换到直流给电池二次充电。无线充电线圈背面多使用软磁铁氧体材料作为软磁片,软磁片的主要功能有两个:一方面是为电磁感应或磁共振的线圈耦合提供高磁导率的通道,增大其磁通量,提高充电效率;另一方面是保证电磁感应线圈的交变磁场对其他电子部件不产生电磁干扰,起到屏蔽的作用。软磁铁氧体材料如果加工成薄片,非常容易断裂,成品率非常低,同时,铁氧体材料的饱和磁感应强度很低,大电流充电时需要很大的厚度才能防止其饱和,极大增加了设备的重量和体积,完全不能满足电子设备轻量化、薄型化、小型化、集成化等对软磁材料越来越高的要求。在快速充电或大电流充电的场合会带来充电线圈和软磁材料的发热现象,甚至会带给其他周边部件感应加热,造成致命的后果。为了解决上述问题,需要用高性能软磁材料对发射端线圈和接收端线圈之间进行导磁,对接收端线圈周围电子部件进行电磁屏蔽。对于无线电能传输(wpt)用软磁材料,要求本征磁导率高,饱和磁感应强度高,涡流损耗低、厚度薄以及方便加工成各种形状以满足不同线圈要求。一般情况下,便携式智能终端产品预留的空间很小,因此,需要研发一种柔性、超薄、高磁导率和低损耗的软磁材料来实现最佳导磁与屏蔽效果。传统的无线充电用软磁材料如铁氧体、金属粉末与聚合物的复合材料等由于它们的磁导率低和饱和磁感应强度低,作为导磁和屏蔽材料的它们很难做到很薄型化,不能满足智能终端产品日趋向超薄型、小型化方向发展的要求。而非晶纳米晶材料是一种优良的超薄软磁材料可以制备到20μm甚至更薄的厚度,并且具有高的有效磁导率和高的饱和磁感应强度的优势,最适合作为wpt用导磁和屏蔽材料。作为wpt用的非晶纳米晶软磁材料在薄带状态下的磁导率和饱和磁感都满足要求。但是,在中、高频条件下使用时因涡流损耗过大会导致充电线圈的品质因数q值降低,发热比较严重,不宜在wpt系统中直接使用。但是,作为屏蔽功能使用时可以满足要求。因此,如果实现非晶纳米晶材料既能起到良好导磁的作用,又能发挥其优异的屏蔽效果,需要采用适当处理技术来降低软磁材料的涡流损耗。在实现工艺上可以通过减小软磁材料的面积、降低材料的厚度、提高材料的电阻率或者对碎片进行绝缘包覆处理等方法来降低涡流损耗,目前比较常用的方法是减小软磁材料的面积,即:把非晶纳米晶软磁薄带材料进行小单元分割,单体小单元下的面积小,涡流小,断开了整个导磁片面积内的大循环涡流,从而使软磁材料的损耗降低,发热减少。cn104011814a提到了一种将整体非晶纳米晶带材分割成小单元的方法,其中提到了采用层压的方法使薄带片间绝缘,通过单层非晶纳米晶薄带上、下两面施加保护膜或胶带的方式,然后进行压碎制备无线充电用软磁片。该技术生产效率低,工序繁琐且表面质量的一致性不宜控制。cn104900383a公开了一种无线充电用单/多层导磁片及其制备方法,采用了浸漆固化的方法对压碎的裂片进行绝缘处理,但是该工艺比较复杂,难以进行产业化生产。因此,开发一种工序简单,磁导率(实部磁导率)高,涡流损耗(虚部磁导率)低的软磁片对于本领域有重要的意义。技术实现要素:针对现有技术中存在的上述不足,本发明的目的在于提供一种软磁片及其制备方法和用途。本发明提供的软磁片可实现高磁导率(实部磁导率)和低涡流损耗(虚部磁导率),在提高充电效率的同时降低了充电过程中造成的发热损失。本发明提供的制备方法适于产业化生产此种软磁片。为达此目的,本发明采用以下技术方案:第一方面,本发明提供一种软磁片,所述软磁片包括:软磁合金层,位于软磁合金层一面的保护膜,和位于软磁合金层另一面的离型膜,所述离型膜和软磁合金层之间设有粘结层,所述软磁合金层包括至少一层软磁合金片,软磁合金片之间设有粘结层,所述软磁合金片中含有裂纹,裂纹将软磁合金片分割为裂片单元,裂纹中填充有绝缘物质。本发明中,所述裂片单元相比于碎片,其区别在于裂纹宽度更小,这有助于在不改变软磁片的磁导率的基础上,减小其涡流损耗。本发明提供的软磁片可通过控制裂片单元的尺寸和裂片单元间的间距(即裂纹宽度)以及裂纹中绝缘物质填充得是否充分和均匀来控制材料的涡流损耗,进而实现减小充电过程中的发热损失,提高充电效率。本发明中,所述软磁合金层包括至少一层软磁合金片,例如1层、2层、3层、4层、5层或6层等。本发明中,所述离型膜可使用现有技术中常见的离型膜。以下作为本发明优选的技术方案,但不作为本发明提供的技术方案的限制,通过以下技术方案,可以更好的达到和实现本发明的技术目的和有益效果。作为本发明优选的技术方案,所述软磁合金层为非晶软磁合金层和/或纳米晶软磁合金层。优选地,所述软磁合金片为非晶软磁合金片和/或纳米晶软磁合金片。优选地,所述软磁合金片的厚度为14-35μm,例如14μm、18μm、20μm、25μm、30μm、32μm、33μm、34μm或35μm等,但并不仅限于所列举的数值,该数值范围内其他未列举的数值同样适用。优选地,所述保护膜为聚对苯二甲酸乙二醇酯膜和/或聚酰亚胺膜。优选地,所述保护膜的厚度为3-20μm,例如3μm、5μm、10μm、15μm或20μm等,但并不仅限于所列举的数值,该数值范围内其他未列举的数值同样适用。优选地,所述离型膜的厚度为20-120μm,例如20μm、40μm、60μm、80μm、100μm或120μm等,但并不仅限于所列举的数值,该数值范围内其他未列举的数值同样适用。优选地,离型膜和软磁合金层之间的粘结层为双面胶和/或无机胶。所述双面胶包括为3m双面胶、3m强力双面胶、德莎双面胶、pet双面胶、泡棉双面胶或黑色3m双面胶中的任意一种或至少两种的组合。优选地,离型膜和软磁合金层之间的粘结层厚度为3-20μm,例如3μm、5μm、10μm、15μm或20μm等,但并不仅限于所列举的数值,该数值范围内其他未列举的数值同样适用。优选地,软磁合金片之间的粘结层为至少一层,且粘结层独立地为双面胶和/或无机胶。所述双面胶包括为3m双面胶、3m强力双面胶、德莎双面胶、pet双面胶、泡棉双面胶或黑色3m双面胶中的任意一种或至少两种的组合。优选地,软磁合金片之间的粘结层为至少一层,且粘结层的厚度独立地优选为3-20μm,例如3μm、5μm、10μm、15μm或20μm等,但并不仅限于所列举的数值,该数值范围内其他未列举的数值同样适用。优选地,所述裂片单元的形状包括三角形、五边形或六边形中的任意一种或至少两种的组合,上述形状可以使软磁片的涡流损耗更低。优选地,所述裂片单元的边长为0.1-2mm,例如0.1mm、0.5mm、1mm、1.4mm、1.8mm或2mm等,但并不仅限于所列举的数值,该数值范围内其他未列举的数值同样适用。该边长范围使得所述软磁片的涡流损耗更小,提升产品应用价值。优选地,所述裂片单元大小均相同。优选地,所述裂纹的宽度为0.05-0.5μm,例如0.05μm、0.1μm、0.2μm、0.3μm、0.4μm或0.5μm等,但并不仅限于所列举的数值,该数值范围内其他未列举的数值同样适用。上述较窄的裂纹宽度更有利于提升软磁片的磁导率,减小其涡流损耗。优选地,所述绝缘物质为绝缘树脂。优选地,所述绝缘物质包括有机硅树脂、改性有机硅树脂、有机硅酮树脂、环氧树脂或酚醛树脂中的任意一种或至少两种的组合;优选地,所述软磁片为柔性软磁片。第二方面,本发明提供一种如第一方面所述软磁片的制备方法,所述方法包括以下步骤:(1)将软磁合金带材卷绕,进行热处理,热处理后在所述带材的一面上贴第一保护膜,将卷绕的带材打开,得到打开的带材;(2)在步骤(1)所述打开的带材的另一面上设置第一粘结层,在第一粘结层上贴第一离型膜,并在第一离型膜上贴第二粘结层,得到覆粘结层的带材,所述第二粘结层为双面胶且所述双面胶未去除隔离膜;(3)用带图案的模具将步骤(2)所述覆粘结层的带材辊压裂片,辊压裂片过程中控制压力,得到含有裂纹的带材;(4)将步骤(3)所述含有裂纹的带材与绝缘物质混合,在真空条件下进行浸渍处理,得到渗入绝缘物质的带材;(5)当所述软磁片的软磁合金层包括一层软磁合金片时,将步骤(4)所述渗入绝缘物质的带材的第一保护膜去掉,在该面贴第二保护膜,将步骤(4)所述渗入绝缘物质的带材的第一粘结层、第一离型膜和第二粘结层去掉,在该面设置第三粘结层,并在第三粘结层上贴第二离型膜,得到所述软磁片;当所述软磁片的软磁合金层包括多层软磁合金片时,将所需片数的步骤(4)所述渗入绝缘物质的带材的第一保护膜、第一粘结层、第一离型膜和第二粘结层都去掉,将得到的软磁合金片叠置,片与片之间设置片层粘结层,得到软磁合金层,在所述软磁合金层的一面贴第二保护膜,在所述软磁合金层的另一面设置第三粘结层,并在第三粘结层上贴第二离型膜,得到所述软磁片。本发明提供的制备方法中,通过在步骤(2)中在第一离型膜上贴第二粘结层(双面胶且所述双面胶未去除隔离膜),利用未去除隔离膜的双面胶以及第一离型膜的协同作用,在后续的辊压步骤中获得了软磁合金带材“裂而不碎”的形貌,这种“裂而不碎”的形貌使得软磁合金片中的裂纹很窄,最终得到的软磁片具有高磁导率(实部磁导率)和低涡流损耗(虚部磁导率),在提高充电效率的同时降低了充电过程中造成的发热损失。本发明提供的制备方法中,步骤(1)在打开卷绕的带材之前先贴第一保护膜,可以防止在卷材打开的时候发生带材断裂现象,减少原料损耗,降低生产成本。本发明提供的制备方法中,步骤(2)所述打开的带材的另一面是指没有贴第一保护膜的一面。本发明提供的制备方法中,步骤(3)中通过带图案的模具,对带材进行辊压裂片,将模具上的图案转移到所述覆粘结层的带材上,带材上的裂纹分割出的裂片单元与模具上的图案形状相同。步骤(3)中通过控制压力,可以对裂纹的宽度进行控制。本发明提供的制备方法中,步骤(4)在真空条件下进行浸渍处理,能够使绝缘物质更加均匀地进入带材的裂纹中,更好地将裂纹分割出的每个单元进行绝缘隔离,使得涡流损耗(虚部磁导率)更低,提升所述软磁片的应用价值。作为本发明优选的技术方案,步骤(1)中,所述软磁合金带材为非晶软磁合金带材和/或纳米晶软磁合金带材。优选地,步骤(1)中,所述软磁合金带材的宽度为30-150mm,例如30mm、40mm、50mm、60mm、70mm、80mm、90mm、100mm、110mm、120mm、130mm、140mm或150mm等,但并不仅限于所列举的数值,该数值范围内其他未列举的数值同样适用。优选地,步骤(1)中,所述软磁合金带材的厚度为14-35μm,例如14μm、18μm、20μm、25μm、30μm、32μm、33μm、34μm或35μm等,但并不仅限于所列举的数值,该数值范围内其他未列举的数值同样适用。优选地,步骤(1)中,所述软磁合金带材的长度为10-1000m,例如10m、50m、100m、200m、300m、400m、500m、600m、700m、800m、900m或1000m等,但并不仅限于所列举的数值,该数值范围内其他未列举的数值同样适用。步骤(1)中,卷绕软磁合金带材常用卷芯内径为30-152.4mm。优选地,步骤(1)中,所述热处理的温度为300-600℃,例如300℃、350℃、400℃、450℃、500℃、550℃或600℃等,但并不仅限于所列举的数值,该数值范围内其他未列举的数值同样适用。优选地,步骤(1)中,所述热处理的时间为30-120min,例如30min、40min、50min、60min、70min、80min、90min、100min、110min或120min等,但并不仅限于所列举的数值,该数值范围内其他未列举的数值同样适用。优选地,步骤(1)中,所述热处理在真空下进行或在保护气氛下进行。优选地,所述保护气氛包括氮气气氛、氩气气氛、氢气气氛或由氮气和氢气组成的混合气氛中的任意一种。优选地,步骤(1)中,所述第一保护膜包括聚丙烯保护膜、双面胶带或单面胶带中任意一种或至少两种的组合。作为本发明优选的技术方案,步骤(2)中,所述第一粘结层为双面胶和/或无机胶。优选地,当第一粘结层为双面胶时,所述双面胶的厚度为3-20μm,例如3μm、5μm、10μm、15μm或20μm等,但并不仅限于所列举的数值,该数值范围内其他未列举的数值同样适用。优选地,所述第二粘结层的厚度为10-200μm,例如10μm、20μm、40μm、60μm、80μm、100μm、125μm、150μm、175μm或200μm等,但并不仅限于所列举的数值,该数值范围内其他未列举的数值同样适用。作为本发明优选的技术方案,步骤(3)中,所述模具的图案包括三角形、五边形或六边形中的任意一种或至少两种的组合。优选地,步骤(3)中,所述模具的图案边长为0.1-0.2mm,例如0.1mm、0.5mm、1mm、1.4mm、1.8mm或2mm等,但并不仅限于所列举的数值,该数值范围内其他未列举的数值同样适用。优选地,步骤(3)中,所述模具的材质为金属和/或非金属。优选地,步骤(3)中,通过调节辊压力臂扭矩控制压力。优选地,所述辊压力臂扭矩为9-24n·m,例如9n·m、10n·m、15n·m、20n·m或24n·m等,但并不仅限于所列举的数值,该数值范围内其他未列举的数值同样适用。优选地,步骤(4)中,所述绝缘物质为绝缘树脂。优选地,步骤(4)中,所述绝缘物质包括有机硅树脂、改性有机硅树脂、有机硅酮树脂、环氧树脂或酚醛树脂中的任意一种或至少两种的组合。优选地,步骤(4)中,所述真空的真空度≤10-3pa,例如10-3pa、0.9×10-3pa、0.7×10-3pa、0.5×10-3pa、0.3×10-3pa或0.1×10-3pa等。优选地,步骤(4)中,所述浸渍处理的温度为20-30℃,例如20℃、22℃、24℃、26℃、28℃或30℃等,但并不仅限于所列举的数值,该数值范围内其他未列举的数值同样适用。优选地,步骤(4)中,所述浸渍处理的时间为5-60min,例如5min、10min、20min、30min、40min、50min或60min等,但并不仅限于所列举的数值,该数值范围内其他未列举的数值同样适用。优选地,步骤(4)中,所述浸渍处理在真空炉中进行。优选地,步骤(4)还包括:将所述渗入绝缘物质的带材进行烘干处理。优选地,所述烘干在空气中或者在烘箱中进行。优选地,步骤(4)还包括:对所述渗入绝缘物质的带材进行表面清理。通过清理可以将绝缘物质清理干净。作为本发明优选的技术方案,步骤(5)中,所述第二保护膜为聚对苯二甲酸乙二醇酯膜和/或聚酰亚胺膜。优选地,步骤(5)中,所述第二保护膜的厚度为3-20μm,例如3μm、5μm、10μm、15μm或20μm等,但并不仅限于所列举的数值,该数值范围内其他未列举的数值同样适用。优选地,步骤(5)中,所述第三粘结层为双面胶和/或无机胶。优选地,步骤(5)中,所述第二离型膜的厚度为20-120μm,例如20μm、30μm、40μm、50μm、60μm、70μm、80μm、90μm、100μm、110μm或120μm等,但并不仅限于所列举的数值,该数值范围内其他未列举的数值同样适用。优选地,步骤(5)中,所述片层粘结层独立地为双面胶和/或无机胶。作为本发明优选的技术方案,所述方法还包括步骤(6):将步骤(5)得到的软磁片的边缘处理整齐。优选地,步骤(6)中,处理软磁片边缘的方法为剪切或包边.优选地,步骤(6)中,所述剪切使用的剪切工具包括分条刀。作为本发明所述制备方法的进一步优选技术方案,所述方法包括以下步骤:(1)将软磁合金带材卷绕,进行热处理,热处理后在所述带材的一面上贴第一保护膜,将卷绕的带材打开,得到打开的卷材;其中,所述软磁合金带材为非晶软磁合金带材和/或纳米晶软磁合金带材,所述软磁合金带材的宽度为30-150mm,厚度为32-35μm,长度为50-300m,所述热处理的温度为300-600℃,所述热处理的时间为30-120min,所述热处理在真空下进行或在保护气氛下进行,所述第一保护膜包括聚丙烯保护膜、双面胶带或单面胶带中任意一种或至少两种的组合;(2)在步骤(1)所述打开的卷材的另一面上设置第一粘结层,所述第一粘结层为3-20μm厚的双面胶,在第一粘结层上贴第一离型膜,并在第一离型膜上贴第二粘结层,得到覆粘结层的带材,所述第二粘结层为10-200μm厚的双面胶且所述双面胶未去除隔离膜;(3)用带图案的模具将步骤(2)所述覆粘结层的带材辊压裂片,通过调节辊压力臂扭矩控制辊压裂片的压力,得到含有裂纹的带材;其中,所述模具上的图案包括三角形、五边形或六边形中的任意一种或至少两种的组合,图案边长为0.1-2mm,所述模具的材质为金属和/或非金属,所述辊压力臂扭矩为9-24n·m;(4)将步骤(3)所述含有裂纹的带材与绝缘树脂混合,放入真空炉中,在≤10-3pa的真空条件下进行浸渍处理,浸渍温度为20-30℃,浸渍时间为5-60min,浸渍后进行烘干处理,得到渗入绝缘物质的带材,对所述渗入绝缘物质的带材进行表面清理;(5)当所述软磁片的软磁合金层包括一层软磁合金片时,将步骤(4)所述渗入绝缘物质的带材的第一保护膜去掉,在该面贴第二保护膜,将步骤(4)所述渗入绝缘物质的带材的第一粘结层、第一离型膜和第二粘结层去掉,在该面设置第三粘结层,并在第三粘结层上贴第二离型膜,得到所述软磁片;当所述软磁片的软磁合金层包括多层软磁合金片时,将所需片数的步骤(3)所述渗入绝缘物质的带材的第一保护膜、第一粘结层、第一离型膜和第二粘结层都去掉,将得到的软磁合金片叠置,片与片之间设置片层粘结层,得到软磁合金层,所述片层粘结层独立地为双面胶和/或无机胶,在所述软磁合金层的一面贴第二保护膜,在所述软磁合金层的另一面设置第三粘结层,并在第三粘结层上贴第二离型膜,得到所述软磁片;其中,所述第二保护膜为聚对苯二甲酸乙二醇酯膜和/或聚酰亚胺膜,厚度为3-20μm,所述第三粘结层为双面胶和/或无机胶,所述第二离型膜的厚度为20-120μm;(6)用分条刀将步骤(5)得到的软磁片的边缘切整齐。第三方面,本发明提供一种如第一方面所述软磁片的用途,所述软磁片用于无线电能传输系统。与现有技术相比,本发明具有以下有益效果:(1)本发明提供的软磁片在128khz的频率下,实部磁导率可达2021,虚部磁导率低于50,在提高充电效率的同时降低了充电过程中造成的发热损失,非常适合用于无线电能传输系统。(2)本发明提供的制备方法通过在第一离型膜上贴第二粘结层(双面胶且所述双面胶未去除隔离膜),利用未去除隔离膜的双面胶以及第一离型膜的协同作用,在后续的辊压步骤中获得了软磁合金带材“裂而不碎”的形貌,使得软磁合金片中的裂纹很窄,解决了软磁合金带材容易断裂,不容易连续制备,不利于规模化生产的问题,提升了软磁片产品的性能。本发明提供的制备方法在真空条件下浸渍绝缘物质,使得绝缘物质更好地渗透到带材的裂纹中,降低了涡流损耗。本发明提供的制备方法可以保证制备工艺的连续性与高效性,操作简单且易于产业化生产。附图说明图1为本发明实施例1提供的软磁片的制备方法中,步骤(3)辊压裂片的示意图,其中1-软磁合金带材,2-第一保护膜,3-第一粘结层,4-第一离型膜,5-第二粘结层,6-模具,7-钢辊。具体实施方式为更好地说明本发明,便于理解本发明的技术方案,下面对本发明进一步详细说明。但下述的实施例仅仅是本发明的简易例子,并不代表或限制本发明的权利保护范围,本发明保护范围以权利要求书为准。以下为本发明典型但非限制性实施例:实施例1本实施例按照如下方法制备软磁片:(1)将宽为60mm,厚度为20μm的非晶软磁合金带材卷绕成内径为78mm,总长度为100m且卷绕紧密的铁芯,将其放在热处理炉内真空条件下进行热处理,热处理温度为540℃,保温60min后打开风机随炉降温至200℃时打开炉门,将热处理后的卷材取出放置在空气中进一步冷却至室温,热处理后在所述带材的一面上贴第一保护膜(opp保护膜),将卷绕的带材打开,得到打开的带材;其中,所述非晶软磁合金带材中的非晶成分为fesib;(2)在步骤(1)所述打开的带材未贴第一保护膜的一面上设置第一粘结层,所述第一粘结层为5μm厚的双面胶,在第一粘结层上贴第一离型膜,并在第一离型膜上贴第二粘结层,得到覆粘结层的带材,所述第二粘结层为100μm厚的双面胶且所述双面胶未去除隔离膜;(3)用带图案的模具将步骤(2)所述覆粘结层的带材辊压裂片,调节辊压力臂扭矩为15n·m以控制压力,得到含有裂纹的带材;其中,所述模具的图案为三角形,三角形边长为0.5mm,所述模具的材质为金属;该步骤的示意图如图1所示,步骤(2)所述覆粘结层的带材从上到下依次包括第一保护膜2、软磁合金带材1、第一粘结层3、第一离型膜4和第二粘结层5,步骤(2)所述覆粘结层的带材被上方的模具6和下方的钢辊7夹持,进行辊压裂片。(4)将步骤(3)所述含有裂纹的带材放入预先准备好的改性有机硅树脂中后放置于真空炉中,在10-3pa的真空条件下进行浸渍处理,浸渍温度为25℃,浸渍时间为10min,浸渍后进行烘干处理,得到渗入绝缘物质的带材,对所述渗入绝缘物质的带材采用无尘布将其表面清理干净后放置在空气中进行晾干处理;(5)将步骤(4)所述渗入绝缘物质的带材的第一保护膜去掉,在该面贴第二保护膜,所述第二保护膜为聚对苯二甲酸乙二醇酯膜保护膜,厚度为10μm,将步骤(4)所述渗入绝缘物质的带材的第一粘结层、第一离型膜和第二粘结层去掉,在该面设置第三粘结层,所述第三粘结层为双面胶,并在第三粘结层上贴第二离型膜,所述第二离型膜为80μm厚的聚对苯二甲酸乙二醇酯膜,最终得到所述软磁片;(6)用分条刀将步骤(5)得到的软磁片的边缘切整齐,以便获得较好的外观。本实施例得到的软磁片为柔性软磁片,包括非晶软磁合金层,位于软磁合金层一面的聚对苯二甲酸乙二醇酯膜保护膜(厚度33μm),和位于软磁合金层另一面的离型膜(厚度80μm),所述离型膜和软磁合金层之间设有粘结层,所述软磁合金层包括1层软磁合金片,所述软磁合金片的厚度为20μm,所述软磁合金片中含有裂纹,裂纹将软磁合金片分割为裂片单元,裂片单元为边长0.5mm的三角形,裂纹宽度为0.25μm,裂片单元大小相同,分布均匀,裂纹被绝缘物质改性有机硅树脂充分填充,粘结层均为双面胶。本实施例得到的软磁片的性能测试结果见表1。实施例2本实施例按照如下方法制备软磁片:(1)将宽为30mm,厚度为14μm的非晶软磁合金带材卷绕成内径为78mm,总长度为50m且卷绕紧密的铁芯,将其放在热处理炉内在氮气气氛下进行热处理,热处理温度为300℃,保温30min后打开风机随炉降温至200℃时打开炉门,将热处理后的卷材取出放置在空气中进一步冷却至室温,热处理后在所述带材的一面上贴第一保护膜(opp保护膜),将卷绕的带材打开,得到打开的带材;其中,所述非晶软磁合金带材中的非晶材料种类与性质参数与实施例1相同。(2)在步骤(1)所述打开的带材未贴第一保护膜的一面上设置第一粘结层,所述第一粘结层为3μm厚的双面胶,在第一粘结层上贴第一离型膜,并在第一离型膜上贴第二粘结层,得到覆粘结层的带材,所述第二粘结层为10μm厚的双面胶且所述双面胶未去除隔离膜;(3)用带图案的模具将步骤(2)所述覆粘结层的带材辊压裂片,调节辊压力臂扭矩为9n·m以控制压力,得到含有裂纹的带材;其中,所述模具的图案为五边形,五边形边长为2mm,所述模具的材质为非金属;(4)将步骤(3)所述含有裂纹的带材放入预先准备好的有机硅树脂中后放置于真空炉中,在0.2×10-3pa的真空条件下进行浸渍处理,浸渍温度为20℃,浸渍时间为5min,浸渍后进行烘干处理,得到渗入绝缘物质的带材,对所述渗入绝缘物质的带材采用无尘布将其表面清理干净后放置在空气中进行晾干处理;(5)将4片的步骤(4)所述渗入绝缘物质的带材的第一保护膜、第一粘结层、第一离型膜和第二粘结层都去掉,将得到的软磁合金片叠置,片与片之间设置片层粘结层,得到软磁合金层,所述片层粘结层为双面胶,在所述软磁合金层的一面贴第二保护膜,所述第二保护膜为聚对苯二甲酸乙二醇酯膜,厚度为3μm,在所述软磁合金层的另一面设置第三粘结层,所述第三粘结层为双面胶,并在第三粘结层上贴第二离型膜,所述第二离型膜的厚度为20μm,得到所述软磁片;(6)用分条刀将步骤(5)得到的软磁片的边缘切整齐,以便获得较好的外观。本实施例得到的软磁片为柔性软磁片,包括非晶软磁合金层,位于软磁合金层一面的聚对苯二甲酸乙二醇酯膜保护膜(厚度3μm),和位于软磁合金层另一面的离型膜(厚度20μm),所述离型膜和软磁合金层之间设有粘结层,所述软磁合金层包括4层软磁合金片,软磁合金片之间设有粘结层,所述软磁合金片的厚度为14μm,所述软磁合金片中含有裂纹,裂纹将软磁合金片分割为裂片单元,裂片单元为边长2mm的五边形,裂纹宽度为0.5μm,裂片单元大小相同,分布均匀,裂纹被绝缘物质有机硅树脂充分填充,粘结层均为双面胶。本实施例得到的软磁片的性能测试结果见表1。实施例3本实施例按照如下方法制备软磁片:(1)将宽为150mm,厚度为35μm的非晶软磁合金带材卷绕成内径为78mm,总长度为300m且卷绕紧密的铁芯,将其放在热处理炉内在氮气气氛下进行热处理,热处理温度为600℃,保温120min后打开风机随炉降温至200℃时打开炉门,将热处理后的卷材取出放置在空气中进一步冷却至室温,热处理后在所述带材的一面上贴第一保护膜(opp保护膜),将卷绕的带材打开,得到打开的带材;其中,所述非晶软磁合金带材中的非晶材料种类与性质参数与实施例1相同;(2)在步骤(1)所述打开的带材未贴第一保护膜的一面上设置第一粘结层,所述第一粘结层为20μm厚的双面胶,在第一粘结层上贴第一离型膜,并在第一离型膜上贴第二粘结层,得到覆粘结层的带材,所述第二粘结层为200μm厚的双面胶且所述双面胶未去除隔离膜;(3)用带图案的模具将步骤(2)所述覆粘结层的带材辊压裂片,调节辊压力臂扭矩为24n·m以控制压力,得到含有裂纹的带材;其中,所述模具的图案为六边形,六边形边长为0.1mm,所述模具的材质为金属;(4)将步骤(3)所述含有裂纹的带材放入预先准备好的环氧树脂中后放置于真空炉中,在0.6×10-3pa的真空条件下进行浸渍处理,浸渍温度为30℃,浸渍时间为60min,浸渍后进行烘干处理,得到渗入绝缘物质的带材,对所述渗入绝缘物质的带材采用无尘布将其表面清理干净后放置在空气中进行晾干处理;(5)将2片的步骤(4)所述渗入绝缘物质的带材的第一保护膜、第一粘结层、第一离型膜和第二粘结层都去掉,将得到的软磁合金片叠置,片与片之间设置片层粘结层,得到软磁合金层,所述片层粘结层为双面胶,在所述软磁合金层的一面贴第二保护膜,所述第二保护膜为聚酰亚胺膜,厚度为20μm,在所述软磁合金层的另一面设置第三粘结层,所述第三粘结层为双面胶,并在第三粘结层上贴第二离型膜,所述第二离型膜的厚度为120μm,得到所述软磁片;(6)用分条刀将步骤(5)得到的软磁片的边缘切整齐,以便获得较好的外观。本实施例得到的软磁片为柔性软磁片,包括非晶软磁合金层,位于软磁合金层一面的聚酰亚胺膜保护膜(厚度20μm),和位于软磁合金层另一面的离型膜(厚度120μm),所述离型膜和软磁合金层之间设有粘结层,所述软磁合金层包括2层软磁合金片,所述软磁合金片的厚度为35μm,所述软磁合金片中含有裂纹,裂纹将软磁合金片分割为裂片单元,裂片单元为边长0.1mm的六边形,裂纹宽度为0.05μm,裂片单元大小相同,分布均匀,裂纹被绝缘物质环氧树脂充分填充,粘结层均为双面胶。本实施例得到的软磁片的性能测试结果见表1。实施例4本实施例按照如下方法制备软磁片:(1)将宽为60mm,厚度为50μm的非晶软磁合金带材卷绕成内径为78mm,总长度为100m且卷绕紧密的铁芯,将其放在热处理炉内真空条件下进行热处理,热处理温度为520℃,保温60min后打开风机随炉降温至200℃时打开炉门,将热处理后的卷材取出放置在空气中进一步冷却至室温,热处理后在所述带材的一面上贴第一保护膜(opp保护膜),将卷绕的带材打开,得到打开的带材;其中,所述非晶软磁合金带材中的非晶材料种类与性质参数与实施例1相同;(2)在步骤(1)所述打开的带材未贴第一保护膜的一面上设置第一粘结层,所述第一粘结层为5μm厚的双面胶,在第一粘结层上贴第一离型膜,并在第一离型膜上贴第二粘结层,得到覆粘结层的带材,所述第二粘结层为100μm厚的双面胶且所述双面胶未去除隔离膜;(3)用带图案的模具将步骤(2)所述覆粘结层的带材辊压裂片,调节辊压力臂扭矩为15n·m以控制压力,得到含有裂纹的带材;其中,所述模具的图案为三角形,三角形边长为0.5mm,所述模具的材质为金属;(4)将步骤(3)所述含有裂纹的带材放入预先准备好的改性有机硅树脂中后放置于真空炉中,在10-3pa的真空条件下进行浸渍处理,浸渍温度为25℃,浸渍时间为30min,浸渍后进行烘干处理,得到渗入绝缘物质的带材,对所述渗入绝缘物质的带材采用无尘布将其表面清理干净后放置在空气中进行晾干处理;(5)将步骤(4)所述渗入绝缘物质的带材的第一保护膜去掉,在该面贴第二保护膜,所述第二保护膜为聚对苯二甲酸乙二醇酯膜保护膜,厚度为10μm,将步骤(4)所述渗入绝缘物质的带材的第一粘结层、第一离型膜和第二粘结层去掉,在该面设置第三粘结层,所述第三粘结层为双面胶,并在第三粘结层上贴第二离型膜,所述第二离型膜为80μm厚的聚对苯二甲酸乙二醇酯膜,最终得到所述软磁片;(6)用分条刀将步骤(5)得到的软磁片的边缘切整齐,以便获得较好的外观。本实施例得到的软磁片为柔性软磁片,包括非晶软磁合金层,位于软磁合金层一面的聚对苯二甲酸乙二醇酯膜保护膜(厚度10μm),和位于软磁合金层另一面的离型膜(厚度80μm),所述离型膜和软磁合金层之间设有粘结层,所述软磁合金层包括1层软磁合金片,所述软磁合金片的厚度为50μm,所述软磁合金片中含有裂纹,裂纹将软磁合金片分割为裂片单元,裂片单元为边长0.5mm的三角形,裂纹宽度为0.2μm,裂片单元大小相同,分布均匀,裂纹被绝缘物质改性有机硅树脂充分填充,粘结层均为双面胶。本实施例得到的软磁片的性能测试结果见表1。实施例5本实施例的具体方法参照实施1,区别在于,步骤(3)中,模具的图案为三角形,三角形边长为1mm。本实施例得到的软磁片的性能测试结果见表1。实施例6本实施例的具体方法参照实施1,区别在于,步骤(1)中,使用的是纳米晶软磁合金带材,所述纳米晶包含fe、si、b、nb和cu元素。本实施例得到的软磁片的性能测试结果见表1。对比例1本对比例的具体方法参照实施例1,区别在于,步骤(2)中,不贴第二粘结层。其结果为,最终得到的软磁片产品中软磁合金片形成的裂纹很宽,不是“裂而不碎”。本对比例得到的软磁片的性能测试结果见表1。对比例2本对比例的具体方法参照实施例2,区别在于,步骤(2)中,不贴第二粘结层。其结果为,最终得到的软磁片产品中软磁合金片形成的裂纹很宽,不是“裂而不碎”。本对比例得到的软磁片的性能测试结果见表1。对比例3本对比例的具体方法参照实施例3,区别在于,步骤(2)中,不贴第二粘结层。其结果为,最终得到的软磁片产品中软磁合金片形成的裂纹很宽,不是“裂而不碎”。本对比例得到的软磁片的性能测试结果见表1。对比例4本对比例的具体方法参照实施例1,区别在于,步骤(4)中,浸渍处理在常压下进行。其结果为,最终得到的软磁片中绝缘物质对裂纹的填充不充分不均匀,不同位置磁导率波动较大。本对比例得到的软磁片的性能测试结果见表1。对比例5本对比例的具体方法参照实施例2,区别在于,步骤(4)中,浸渍处理在常压下进行。其结果为,最终得到的软磁片中绝缘物质对裂纹的填充不充分不均匀,不同位置磁导率波动较大。本对比例得到的软磁片的性能测试结果见表1。对比例6本对比例的具体方法参照实施例3,区别在于,步骤(4)中,浸渍处理在常压下进行。其结果为,最终得到的软磁片中绝缘物质对裂纹的填充不充分不均匀,不同位置磁导率波动较大。本对比例得到的软磁片的性能测试结果见表1。以对以上实施例和对比例得到的软磁片在128khz的频率下进行磁导率测试,其结果见下表。表1磁导率实部磁导率虚部实施例1202145实施例2200734实施例3198930实施例4201339实施例5169141实施例6160832对比例1153785对比例2148273对比例3132469对比例4158558对比例5154856对比例6151652综合上述实施例和对比例可知,本发明提供的制备方法通过在第一离型膜上贴第二粘结层(双面胶,且所述双面胶未去除隔离膜),利用未去除隔离膜的双面胶以及第一离型膜的协同作用,在后续的辊压步骤中获得了软磁合金带材“裂而不碎”的形貌,解决了软磁合金带材容易断裂,不容易连续制备,不利于规模化生产的问题,提升了软磁片产品的性能。本发明提供的制备方法在真空条件下浸渍绝缘物质,使得绝缘物质更好地渗透到带材的裂纹中,降低了涡流损耗。对比例没有采用本发明的方案,因而无法取得本发明的优良效果。申请人声明,以上所述仅为本发明的具体实施方式,但本发明的保护范围并不局限于此,所属
技术领域:
的技术人员应该明了,任何属于本
技术领域:
的技术人员在本发明揭露的技术范围内,可轻易想到的变化或替换,均落在本发明的保护范围和公开范围之内。当前第1页12