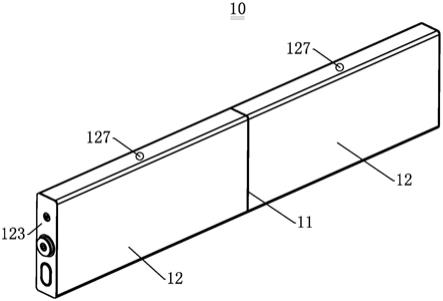
[0001]
本申请涉及电池的技术领域,尤其涉及一种拼接式长动力电池和电池包。
背景技术:[0002]
随着新能源行业的蓬勃发展以及新能源电动汽车的进一步普及,人民群众对新能源乘用车的认可也逐步提升。对于动力电芯制造商来说,如何进一步提升动力电芯模组的体积空间利用率,在有限的乖用车空间内,提升装载电量,满足长续航要求,并可采用低成本高可靠性的体系方案,无疑是最关键的技术难点。
[0003]
有鉴于此,亟需开发一款高能量密度的电池包。
技术实现要素:[0004]
本申请的目的是提供一种拼接式长动力电池和电池包以解决电动汽车的续航问题。
[0005]
为实现上述目的本申请采用以下技术方案实现的:提供一种拼接式长动力电池,该拼接式长动力电池包括:至少两个单体电池和中间电极组件,至少两个单体电池分别与中间电极组件的相对两侧抵接,且电性连接,以串联在一起;单体电池包括电芯、端部电极组件和壳体,中间电极组件的相对两侧分别与电芯电性连接,端部电极组件与电芯的远离中间电极组件的一端连接,壳体从端部电极组件的一端插入包覆电芯并抵接中间电极组件。
[0006]
进一步地,壳体包括周壁和端壁,周壁围设形成双通的容纳腔,端壁与周壁的一端连接,端壁开设有开口,端部电极组件、电芯和中间电极组件整体插入容纳腔中,端部电极组件与端壁连接且穿设开口,中间电极组件与周壁连接且盖封容纳腔。
[0007]
进一步地,端部电极组件包括端部端盖、端部连接片和端部极柱,端部端盖与端壁连接且盖设开口,端部连接片与电芯的一端电性连接,端部极柱与端部连接片电性连接,且穿设端部端盖。
[0008]
进一步地,电芯为全极耳结构,端部连接片包括第一固定部、第二固定部和主体部,主体部的相对两端分别设置有第一固定部和第二固定部以构成u型结构,第一固定部和第二固定部分别与电芯电性连接,端部极柱穿设主体部。
[0009]
进一步地,电芯为模切极耳结构,端部连接片包括第一固定部、第二固定部和主体部,主体部的相对两端分别设置有与主体部层叠设置的第一固定部和第二固定部,第一固定部和第二固定部分别与电芯电性连接,端部极柱穿设主体部。
[0010]
进一步地,端部端盖设置有搭接部,搭接部搭设在端壁的内侧面上。
[0011]
进一步地,中间电极组件包括中间端盖、第一连接片、第二连接片、第一极柱和第二极柱,中间端盖与周壁连接且盖封两侧的容纳腔,第一连接片和第二连接片分别与两侧的电芯的电性连接,第一极柱与第一连接片电性连接,第二极柱与第二连接片电性连接,且第一极柱与第二极柱电性连接。
[0012]
进一步地,中间端盖的两侧设置有台阶部,周壁抵接于台阶部上。
[0013]
进一步地,单体电池还包括胶塞,周壁上开设有用于向容纳腔中注入电解液的注液孔,胶塞过盈配合于注液孔中。
[0014]
为解决上述技术问题,本申请还提供一种电池包,电池包包括外包壳和多个如上述任一项的拼接式长动力电池,多个拼接式长动力电池并排排列于外包壳中,拼接式长动力电池的端部电极组件朝向外包壳的厚度区域。
[0015]
本申请实施例的有益效果为:拼接式长动力电池包括:至少两个单体电池和中间电极组件,至少两个单体电池分别与中间电极组件的相对两侧抵接,且电性连接,以串联在一起,形成一个大电池。根据电池包的实际大小决定单体电池的拼接数量以拼接出合适长度的拼接式长动力电池,可以理解地,每两个单体电池通过一个中间电极组件连接在一起就减少一个电极组件的使用,从而减少电极组件占用电池包的空间,提高电池包的能量密度。
附图说明
[0016]
为了更清楚地说明本申请实施例或前期研发中的技术方案,下面将对实施例或前期研发描述中所需要使用的附图作简单地介绍,显而易见地,下面描述中的附图仅仅是本申请的一些实施例,对于本领域普通技术人员来讲,在不付出创造性劳动的前提下,还可以根据这些附图示出的结构获得其他的附图。
[0017]
图1是本申请提供的电池包100的结构示意图;
[0018]
图2是本申请提供的拼接式长动力电池10的装配结构示意图;
[0019]
图3是本申请提供的拼接式长动力电池10的分解结构示意图;
[0020]
图4是本申请提供的拼接式长动力电池10的截面示意图;
[0021]
图5是本申请提供的图4中b区域的局部放大示意图;
[0022]
图6是本申请提供的端部电极组件123的分解结构示意图;
[0023]
图7是本申请提供的图4中a区域的局部放大示意图;
[0024]
图8是本申请提供的中间电极组件11的分解结构示意图;
[0025]
图9为本申请提供的拼接式长动力电池10的另一实施例的分解结构示意图;
[0026]
图10为本申请提供的拼接式长动力电池10的在冲压前的局部放大截面示意图;
[0027]
图11为本申请提供的拼接式长动力电池10的在冲压后的局部放大截面示意图;
[0028]
图12是本申请提供的拼接式长动力电池10的组装方法的流程示意图。
[0029]
图示标记如下:
[0030]
电池包100
ꢀꢀꢀꢀꢀꢀꢀꢀꢀꢀ
外包壳20
ꢀꢀꢀꢀꢀꢀꢀꢀꢀꢀꢀꢀꢀꢀ
拼接式长动力电池10
[0031]
中间电极组件11
ꢀꢀꢀꢀꢀ
中间端盖111
ꢀꢀꢀꢀꢀꢀꢀꢀꢀꢀꢀ
台阶部1112
[0032]
第一连接片113
ꢀꢀꢀꢀꢀꢀ
第二连接片115
ꢀꢀꢀꢀꢀꢀꢀꢀꢀ
第一极柱117
[0033]
第二极柱119
ꢀꢀꢀꢀꢀꢀꢀꢀ
第一塑胶垫112
ꢀꢀꢀꢀꢀꢀꢀꢀꢀ
第二塑胶垫114
[0034]
第一绝缘圈116
ꢀꢀꢀꢀꢀꢀ
第二绝缘圈118
ꢀꢀꢀꢀꢀꢀꢀꢀꢀ
单体电池12
[0035]
电芯121
ꢀꢀꢀꢀꢀꢀꢀꢀꢀꢀꢀꢀ
全极耳结构124
ꢀꢀꢀꢀꢀꢀꢀꢀꢀ
模切极耳结构126
[0036]
端部电极组件123
ꢀꢀꢀꢀ
端部端盖1231
ꢀꢀꢀꢀꢀꢀꢀꢀꢀꢀ
搭接部1237
[0037]
端部连接片1232
ꢀꢀꢀꢀꢀ
端部极柱1233
ꢀꢀꢀꢀꢀꢀꢀꢀꢀꢀ
端部塑胶垫1238
[0038]
端部绝缘圈1239
ꢀꢀꢀꢀꢀ
第一固定部1234
ꢀꢀꢀꢀꢀꢀꢀꢀ
第二固定部1235
[0039]
主体部1236
ꢀꢀꢀꢀꢀꢀꢀꢀꢀ
壳体125
ꢀꢀꢀꢀꢀꢀꢀꢀꢀꢀꢀꢀꢀꢀꢀ
周壁1251
[0040]
容纳腔1253
ꢀꢀꢀꢀꢀꢀꢀꢀꢀ
注液孔1254
ꢀꢀꢀꢀꢀꢀꢀꢀꢀꢀꢀꢀ
端壁1252
[0041]
开口1255
ꢀꢀꢀꢀꢀꢀꢀꢀꢀꢀꢀ
胶塞127
具体实施方式
[0042]
在本申请中涉及“第一”、“第二”等的描述仅用于描述目的,而不能理解为指示或暗示其相对重要性或者隐含指明所指示的技术特征的数量。
[0043]
在本实用新型中涉及“第一”、“第二”等的描述仅用于描述目的,而不能理解为指示或暗示其相对重要性或者隐含指明所指示的技术特征的数量。
[0044]
请参阅图1,图1是本申请提供的电池包100的结构示意图。
[0045]
本申请的电池包100安装于电动汽车的底盘上,作为蓄能部件。电池包100包括外包壳20和多个拼接式长动力电池10,多个拼接式长动力电池10并排排列于外包壳20中,拼接式长动力电池10的端部电极组件123朝向外包壳20的厚度区域,即拼接式长动力电池10 的端部朝向底盘的高度区域。
[0046]
请参阅图1至图3,图2是本申请提供的拼接式长动力电池10 的装配结构示意图,图3是本申请提供的拼接式长动力电池10的分解结构示意图。
[0047]
拼接式长动力电池包100括:至少两个单体电池12和中间电极组件11,至少两个单体电池12分别与中间电极组件11的相对两侧抵接,且电性连接,以串联在一起,形成一个大电池。根据电池包 100的实际大小决定单体电池12的拼接数量以拼接出合适长度的拼接式长动力电池10,可以理解地,每两个单体电池12通过一个中间电极组件11连接在一起就减少一个电极组件的使用,从而减少电极组件占用电池包100的空间,提高电池包100的能量密度。在本实施例中,单体电池12的数量为两个,两个单体电池12通过中间电极组件11拼接串联在一起。
[0048]
本申请的单体电池包100括电芯121、端部电极组件123和壳体 125,中间电极组件11的相对两侧分别与电芯121电性连接,端部电极组件123与电芯121的远离中间电极组件11的一端连接,壳体125 从端部电极组件123的一端插入包覆电芯121并抵接中间电极组件11,从而完成对拼接式长动力电池10的组装,首尾两个端部电极组件123为正负极用于将电芯121中的电量导出中间电极组件11分别,中间电极组件11作为电性连接件,将中间电极组件11相对两侧的电芯121串联在一起。
[0049]
壳体125包括周壁1251和端壁1252,周壁1251围设形成双通的容纳腔1253,端壁1252与周壁1251的一端连接,端壁1252开设有开口1255,周壁1251和端壁1252可以一体成型连接,也可以焊接连接。中间电极组件11、中间电极组件11两侧的电芯121和端部电极组件123在壳体125的外部装配好,然后整体插入至容纳腔1253 中,电芯121收容于容纳腔1253中,端部电极组件123与端壁1252 连接且进一步穿设开口1255,以封堵开口1255,中间电极组件11 与周壁1251连接且盖封容纳腔1253。
[0050]
在本实施例中,首先端部电极组件123、中间电极组件11两侧的电芯121和中间电极组件11在壳体125的外部装配好,然后端部电极组件123、中间电极组件11两侧的电芯121和中间电极组件11 整体插入中间电极组件11两侧的容纳腔1253中,端部电极组件123 封
盖壳体125的一端,中间电极组件11封盖壳体125的相对一端以形成拼接式长动力电池10。因为端部电极组件123和中间电极组件 11在壳体125外分别与电芯121两端的极耳连接在一起,所以可以在没有壳体125遮挡的前提下利用较短的极耳将端部电极组件123和中间电极组件11分别与电芯121连接在一起,避免过多的极耳占用空间,提高了壳体125空间利用率。而且每两个单体电池12之间通过中间电极组件11连接在一起,从而省去一个电极组件,以将该空间给电芯121,提高电池包100的能量密度。
[0051]
如果先把电芯121装配于容纳腔1253中,再在每个壳体125的两端将端部电极组件123和中间电极组件11与电芯121连接在一起,这会导致如下几个缺点:1、操作难度大、空间不足,难以焊接、除尘;2、壳体125高度空间的利用率降低,体积能量密度降低;3、制造成本高昂。
[0052]
另外,中间电极组件11将多个单体电池12串联在一起,每个拼接式长动力电池10的正负电极分布在收尾两端,因此拼接式长动力电池10可以根据实际需要做的又窄又长,从而拼接式长动力电池10 便于以卧倒的方式排布于电动汽车的底盘中,即端部电极组件123和中间电极组件11朝向底盘的高度部分,拼接式长动力电池10完全占用底盘的高度空间,从而提高了底盘高度部分的空间利用率。另外,拼接式长动力电池10的体积做大后,可以减少单体电池12的数量,进而减少辅助材料例如壳体125对底盘空间的占用。
[0053]
在此需要解释的是,在电动汽车领域,单体电池12一般为单通电池,即单体电池12的正负极分布在电池的一端,为了同时容下正负极,单体电池12的端部会做的比较长以隔开放置正负极,这样会导致正负极朝向底盘的上端面摆放(如果正负极朝向底盘的高度部分,单体电池12无法摆放),为了排布分别与正负极电性连接的导线,导致底盘的高度空间被过多占用。事实上,因为电动汽车制造标准的原因,底盘高度空间是固定的,因此底盘高度空间的利用率的提高也同样提高了电池包100的能量密度。
[0054]
拼接式长动力电池10还包括胶塞127,周壁1251上开设有用于向容纳腔1253中注入电解液的注液孔1254,胶塞127过盈配合于注液孔1254中。在注液时,拼接式长动力电池10卧倒,以降低重心,从周壁1251上的注液孔1254向壳体125的内部注射电解液。另外,注液孔1254设置在周壁1251上远离端部电极组件123和中间电极组件11,从而避免向注液孔1254注液过程中外溢的电解液污染并腐蚀端部电极组件123和中间电极组件11。
[0055]
请参阅图4至图6,图4是本申请提供的拼接式长动力电池10 的截面示意图,图5是本申请提供的图4中b区域的局部放大示意图,图6是本申请提供的端部电极组件123的分解结构示意图。
[0056]
端部电极组件123包括端部端盖1231、端部连接片1232和端部极柱1233,端部端盖1231与端壁1252连接且盖设开口1255,端部连接片1232与电芯121的一端电性连接,端部极柱1233与端部连接片1232电性连接,且穿设端部端盖1231至壳体125的外部。电芯 121与端部连接片1232电性导通,端部连接片1232与端部极柱1233 电性导通。
[0057]
需要解释的是,正如上述实施例所介绍的,端部连接片1232与电芯121在壳体125外连接,从而可以在没有壳体125遮挡的前提下利用较短的极耳将端部连接片1232和与电芯121连接在一起,避免过多的极耳占用空间,提高了壳体125空间利用率。连接方式可以是超声波焊接、摩擦焊接。
[0058]
可选地,开口1255为圆形,对应地,端部端盖1231的外轮廓也为圆形。圆形的端部
端盖1231和圆形的开口1255配合,以提高容错能力。
[0059]
端部端盖1231设置有搭接部1237,搭接部1237搭设在端壁1252 的内侧面上,以对端部端盖1231形成限位的作用,防止端部端盖1231 在从容纳腔1253中运动至开口1255处时从开口1255穿出,起到对端部端盖1231在后续与壳体125的焊接工程中的定位作用。进一步地,端壁1252开设有限位槽,搭接部1237限位于容置于限位槽中。
[0060]
端部电极组件123还包括端部塑胶垫1238和端部绝缘圈1239。端部塑胶垫1238设置在端部端盖1231和端部连接片1232之间,以使端部端盖1231和端部连接片1232之间绝缘。端部绝缘圈1239套设在端部极柱1233上,以使端部极柱1233与端部端盖1231绝缘。
[0061]
端部塑胶垫1238的长度大于电芯121的长度,这样在电芯121 放置于壳体125的过程中端部塑胶垫1238可以防止电芯121剐蹭到壳体125上而使电芯121碰伤。
[0062]
请参阅图4、图7至图8,图7是本申请提供的图4中a区域的局部放大示意图,图8是本申请提供的中间电极组件11的分解结构示意图。
[0063]
中间电极组件11包括中间端盖111、第一连接片113、第二连接片115、第一极柱117和第二极柱119,中间端盖111与周壁1251 连接且盖封两侧的容纳腔1253,中间端盖111隔断相邻的两个壳体 125,第一连接片113和第二连接片115分别与两侧的电芯121的电性连接,第一极柱117与第一连接片113电性连接,第二极柱119 与第二连接片115电性连接,且第一极柱117与第二极柱119电性连接。可以第一极柱117穿过中间端盖111与第二极柱119电性连接,可以第二极柱119穿过中间端盖111与第一极柱117电性连接。
[0064]
需要解释的是,正如上述实施例所介绍的,第一连接片113和第二连接片115分别与电芯121在壳体125外连接,从而可以在没有壳体125遮挡的前提下利用较短的极耳将第一连接片113、第二连接片 115与电芯121连接在一起,避免过多的极耳占用空间,提高了壳体 125空间利用率。连接方式可以是超声波焊接、摩擦焊接。
[0065]
中间端盖111的两侧设置有台阶部1112,中间端盖111两侧的周壁1251抵接于台阶部1112上,以起到对中间端盖111两侧的壳体 125的隔离作用,防止相邻壳体125中的电解液相对对流。另外,台阶部1112对壳体125起到一定的限位作用,防止。
[0066]
中间电极组件11还包括第一塑胶垫112、第二塑胶垫114、第一绝缘圈116和第二绝缘圈118。第一塑胶垫112设置在中间端盖111 和第一连接片113之间,以使中间端盖111和第一连接片113之间绝缘;第二塑胶垫114设置在中间端盖111和第二连接片115之间,以使中间端盖111和第二连接片115之间绝缘。第一绝缘圈116套设在第一极柱117上,以使第一极柱117与中间端盖111绝缘;第二绝缘圈118套设在第二极柱119上,以使第二极柱119与中间端盖111 绝缘。
[0067]
第一塑胶垫112、第二塑胶垫114的长度分别大于电芯121的长度,这样在电芯121放置于壳体125的过程中可以防止电芯121剐蹭到壳体125上而使电芯121碰伤。
[0068]
请继续参阅图5,在一实施例中,电芯121为全极耳结构124,首先将多层铜箔卷绕,然后将卷芯的端部整体压设形成作为极耳的全极耳结构124,全极耳结构124的优势在于导电面积大,从而电阻小,发热小。端部连接片1232包括第一固定部1234、第二固定部1235 和主体部1236,主体部1236的相对两端分别设置有第一固定部1234 和第二固定部1235以构成u型结构,第一固定部1234和第二固定部1235分别与电芯121电性连接,端部极柱1233穿设主体部1236。同理,第二连接片115也可以有与端部连接片1232相同的结构以与全极耳结
构124连接。
[0069]
在另一实施例中,电芯121为模切极耳结构126。具体地,请参阅图9至图11,图9为本申请提供的拼接式长动力电池10的另一实施例的分解结构示意图,图10为本申请提供的拼接式长动力电池10 的在冲压前的局部放大截面示意图,图11为本申请提供的拼接式长动力电池10的在冲压后的局部放大截面示意图。
[0070]
电芯121为模切极耳结构126,首先将铜箔的边缘冲切形成极耳片,然后多层铜箔卷绕后,多个极耳片叠加在一起形成作为极耳的模切极耳结构126,模切极耳结构126的优势在于面积小,易变形方便折弯。端部连接片1232包括第一固定部1234、第二固定部1235和主体部1236,主体部1236的相对两端分别设置有与主体部1236层叠设置的第一固定部1234和第二固定部1235,第一固定部1234和第二固定部1235分别与电芯121电性连接,端部极柱1233穿设主体部1236。
[0071]
具体的装配过程为:第一固定部1234和第二固定部1235分别与主体部1236呈度,将极耳分别与第一固定部1234和第二固定部1235 连接在一起,然后侧向推压第一固定部1234和第二固定部1235,直至第一固定部1234和第二固定部1235分别与主体部1236层叠设置,从而减少极耳在空间上的占用率。同理,第二连接片115也可以有与端部连接片1232相同的结构以与全极耳结构124连接。
[0072]
请参阅图3和图12,图12是本申请提供的拼接式长动力电池10 的组装方法的流程示意图。
[0073]
拼接式长动力电池包100括至少两个单体电池12和中间电极组件11。单体电池包100括电芯121、端部电极组件123、中间电极组件11和壳体125。
[0074]
s101:将中间电极组件11分别与相邻的电芯121电性连接在一起。
[0075]
将中间电极组件11分别与相邻的电芯121电性连接在一起,中间电极组件11作为电性连接件,将中间电极组件11相对两侧的电芯 121串联在一起。
[0076]
在壳体125外,首先将中间电极组件11一侧的电芯121与中间电极组件11连接在一起,然后将中间电极组件11另一侧的电芯121 与中间电极组件11连接在一起,使电芯121、端部电极组件123和中间电极组件11连接在一起形成一个整体。
[0077]
根据电池包100的实际大小决定单体电池12的拼接数量以拼接出合适长度的拼接式长动力电池10,从而减少电极组件占用电池包 100的空间,可以理解地,每两个单体电池12通过一个中间电极组件11连接在一起就减少一个电极组件的使用,从而提高电池包100 的能量密度。在本实施例中,单体电池12的数量为两个,两个单体电池12通过中间电极组件11拼接串联在一起。
[0078]
s102:将端部电极组件123与电芯121的远离中间电极组件11 的一端电性连接在一起。
[0079]
将端部电极组件123与电芯121的远离中间电极组件11的一端电性连接在一起,首尾两端的端部电极组件123为正负极。
[0080]
s103:将端部电极组件123、电芯121和中间电极组件11整体插入壳体125中,端部电极组件123穿过壳体125与壳体125连接,中间电极组件11与壳体125的远离端部电极组件123的一端抵接。
[0081]
将端部电极组件123、电芯121和中间电极组件11整体插入壳体125中,当然,也可
以端部电极组件123、电芯121和中间电极组件11不动,将壳体125依次穿过端部电极组件123和电芯121并抵接中间电极组件11。
[0082]
壳体125包括周壁1251和端壁1252,周壁1251围设形成双通的容纳腔1253,端壁1252与周壁1251的一端连接,端壁1252开设有开口1255,周壁1251和端壁1252可以一体成型连接,也可以焊接连接。中间电极组件11、中间电极组件11两侧的电芯121和端部电极组件123在壳体125的外部装配好,然后整体插入至容纳腔1253 中,电芯121收容于容纳腔1253中,端部电极组件123与端壁1252 连接且进一步穿设开口1255,以封堵开口1255,中间电极组件11 与周壁1251连接且盖封容纳腔1253。壳体125的材质可以是铝、铜、不锈钢等。
[0083]
端部电极组件123朝向端壁1252,将端部电极组件123、电芯 121和中间电极组件11整体插入容纳腔1253中,端部电极组件123 依次穿过容纳腔1253和开口1255与端壁1252连接,连接方式可以是焊接,中间电极组件11与周壁1251连接且盖封容纳腔1253。
[0084]
在本实施例中,首先端部电极组件123、中间电极组件11两侧的电芯121和中间电极组件11在壳体125的外部装配好,然后端部电极组件123、中间电极组件11两侧的电芯121和中间电极组件11 整体插入中间电极组件11两侧的容纳腔1253中,端部电极组件123 封盖壳体125的一端,中间电极组件11封盖壳体125的相对一端以形成拼接式长动力电池10。因为端部电极组件123和中间电极组件 11在壳体125外分别与电芯121两端的极耳连接在一起,所以可以在没有壳体125遮挡的前提下利用较短的极耳将端部电极组件123和中间电极组件11分别与电芯121连接在一起,避免过多的极耳占用空间,提高了壳体125空间利用率。而且每两个单体电池12之间通过中间电极组件11连接在一起,从而省去一个电极组件,以将该空间给电芯121,提高电池包100的能量密度。
[0085]
本申请的拼接式长动力电池10的组装方法还可以在上述任一实施例的拼接式长动力电池10的基础上进行实施,在此不一一赘述。
[0086]
以上仅为本实用新型的优选实施例,并非因此限制本实用新型的专利范围,凡是在本实用新型的发明构思下,利用本实用新型说明书及附图内容所作的等效结构变换,或直接/间接运用在其他相关的技术领域均包括在本实用新型的专利保护范围内。