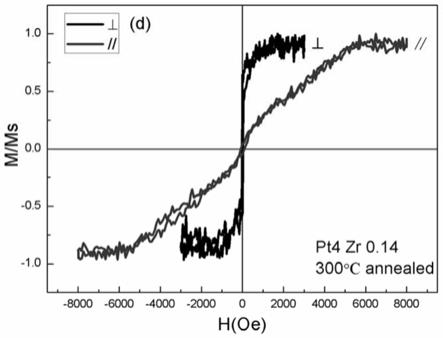
可调控co2fex合金垂直磁各向异性的磁性薄膜材料及方法
技术领域
1.本发明属于磁性薄膜领域,涉及一种可调控co2fex合金垂直磁各向异性的磁性薄膜材料及方法。
背景技术:2.赫斯勒合金具有高自旋极化率、低阻尼常数、高的居里温度,满足磁性随机存储器(mram)中低磁化翻转电流的需求,有望成为下一代高密度垂直磁记录器件mram的电极材料而广泛受到关注。但该合金由于磁晶各项异性能很低,使得在赫斯勒合金/氧化物多层膜中获得pma变得很困难,所以提高赫斯勒合金体系的磁各向异性成了其应用的关键。具有较高垂直磁各向异性和好的热稳定性的磁性材料是mram、磁传感器应用的基础,目前国际上还在不断地挖掘磁性薄膜的潜力,提高其磁性能和热稳定性等,以扩大其应用领域。
技术实现要素:3.本发明公开了一种可调控co2fex合金垂直磁各向异性的磁性薄膜材料及方法,以解决现有技术的上述技术问题以及其他潜在问题中的任意问题。
4.为了解决上述问题,本发明的技术方案是:可调控co2fex合金垂直磁各向异性的磁性薄膜材料,
5.本发明的技术方案是:一种可调控co2fex合金垂直磁各向异性的磁性薄膜材料,该磁性薄膜材料包括基底、缓冲层、co2fex(x为al、si、mn的一种或者多种)/zr/co2fex(x为al、si、mn的一种或者多种)/mo(mo为金属氧化物如mgo、alox等)多层膜、保护层;
6.其中,所述缓冲层和保护层均由金属ta或其它金属或者不同金属元素的复合层构成,其它金属可以为pt、pd、mo、cr等。
7.进一步,所述基底为硅片、玻璃片、mgo基底。本发明的另一目的是提供上述磁性薄膜材料的制备方法,该方法具体包括以下步骤:
8.步骤1:选取基底材料,进行清洗;
9.步骤2:采用共溅射方法将ta或其它金属沉积在经步骤1处理后的基底材料上作为缓冲层,
10.步骤3:在所述缓冲层上沉积co2fex(x为al、si、mn的一种或者多种)/zr/co2fex(x为al、si、mn的一种或者多种)/mo(mo为金属氧化物如mgo、alox)多层膜;
11.步骤4:采用磁控溅射方法将ta或其它金属沉积在上述多层膜上作为保护层;
12.步骤5:将上述制备的(0.1~100.0m)ta或其它金属/co2fex(x为al、si、mn的一种或者多种)/zr/co2fex(x为al、si、mn的一种或者多种)/mo(mo为金属氧化物如mgo、alox)/(0.1~100.0nm)ta或其它金属薄膜材料放入真空退火炉进行退火处理。
13.进一步,所述共溅射方法的具体工艺为:溅射室本底真空度为1.0
×
10
‑4~9.9
×
10
‑4pa或者1.0
×
10
‑5~9.9
×
10
‑5pa,溅射前通入镀膜室99.99%纯度氩气0.5~1小时,维持在气压0.1~1.5pa;溅射时99.99%纯度的高纯氩气气压为0.2~2.7pa;基片用循环去离子
水冷却,平行于基片平面方向加有5~60ka/m的磁场。
14.进一步,所述步骤5的退火工艺为:退火炉本底真空为1.0
×
10
‑4~9.9
×
10
‑4pa或者1.0
×
10
‑5~9.9
×
10
‑5pa、退火温度为100
‑
500℃,退火时间为1分钟
‑
120分钟,退火时沿薄膜的易轴方向加5
‑
100ka/m的磁场,并在磁场中随炉冷却。
15.进一步,所述缓冲层和保护层的沉积厚度为:0.1~100.0nm。
16.进一步,所述ta或其它金属/co2fex(x为al、si、mn的一种或者多种)/zr/co2fex(x为al、si、mn的一种或者多种)/mo(mo为金属氧化物如mgo、alo
x
等)/ta或其它金属,多层膜的沉积厚度为:1.0~200.0nm。
17.本发明的原理是:制备mram和磁传感器的传统材料是在基片上沉积ta或其它金属/co2fex(x为al、si、mn的一种或者多种)/zr/co2fex(x为al、si、mn的一种或者多种)/mo(mo为金属氧化物如mgo、alo
x
)/ta或其它金属的多层膜。多层膜的pma取决于co
‑
o、fe
‑
o的轨道杂化,但co、fe的欠氧化和过氧化都不利于薄膜的pma。在制备多层膜材料过程中,co2fex上沉积氧化物,在制备态co、fe有一定程度的氧化。在一定温度热处理下,co、fe、x等元素会发生扩散,co、fe的氧化状态也会发生变化,影响样品的磁各向异性。因此在磁性层中沉积一定的zr,zr易于和氧发生反应,利用金属zr对o的亲和力调控co
‑
o、fe
‑
o的比例,提高样品的pma及热稳定性。可以单独溅射zr也可以采用共溅射的方法制备zr和上层co2fex磁性层,进而达到提高上述薄膜的垂直磁各向异性的目的。
18.为了解决上述问题,本发明的目的是提供工艺简单,具有较高的垂直磁各向异性的磁性薄膜材料及其制备方法。
附图说明
19.图1为pt(4nm)/co2feal(0.7nm)/mgo(1nm)/ta(2nm)薄膜制备态的磁化曲线示意图。
20.图2为pt(4nm)/co2feal(0.7nm)/mgo(1nm)/ta(2nm)薄膜300℃、30分钟退火的磁化曲线示意图。
21.图3采用本发明方法制备得到的pt(4nm)/co2feal(0.35nm)/zr(0nm)/co2feal(0.35nm)/mgo(1.0nm)/ta(2nm)薄膜300℃、30分钟退火的磁化曲线示意图。
22.图4为采用本发明方法制备得到的pt(4nm)/co2feal(0.35nm)/zr(0.02nm)/co2feal(0.35nm)/mgo(1.0nm)/ta(2nm)薄膜300℃、30分钟退火的磁化曲线示意图。
23.图5为采用本发明方法制备得到的pt(4nm)/co2feal(0.35nm)/zr(0.08nm)/co2feal(0.35nm)/mgo(1.0nm)/ta(2nm)300℃、30分钟退火的磁化曲线示意图。
24.图6为pt(4nm)/co2feal(0.35nm)/zr(0.14nm)/co2feal(0.35nm)/mgo(1.0nm)/ta(2nm)薄膜300℃、30分钟退火的磁化曲线示意图。
25.图7为pt(4nm)/co2feal(0.35nm)/zr(0.20nm)/co2feal(0.35nm)/mgo(1.0nm)/ta(2nm)薄膜300℃、30分钟退火的磁化曲线示意图。
26.图8为pt(4nm)/co2fealsi(0.40nm)/zr(0.12nm)/co2fealsi(0.40nm)/mgo(1.0nm)/ta(2nm)薄膜300℃、30分钟退火的磁化曲线示意图。
具体实施方式
27.下面结合附图和具体实施例对本发明的技术方案做进一步说明。
28.本发明一种可调控co2fex合金垂直磁各向异性的磁性薄膜材料,该可调控co2fex合金垂直磁各向异性的磁性薄膜材料包括:基底、缓冲层、磁性层、氧化物层和保护层,所述磁性层的磁性材料为断裂式的co2fex/zr/co2fex,其中,x为al、si、mn的一种或者多种,zr占磁性层的质量比为0.001
‑
50%。
29.所述氧化物层为金属氧化物,所述缓冲层和保护层为单层或复合层。
30.所述单金属层为金属ta、贵金属或稀有金属元素,复合金属层为金属ta与贵金属和稀有金属元素,所述贵金属为pt或pd,所述稀有金属为mo或cr。所述基底为硅片或玻璃片、mgo基底材料。
31.本发明还提供一种制备上述可调控co2fex合金垂直磁各向异性的磁性薄膜材料的方法,该方法具体包括以下步骤:
32.s1)选取基底材料,进行清洗;
33.s2)采用磁控溅射方法将ta或者其它金属沉积在经s1)处理后的基底材料上作为缓冲层,
34.s3)再在s2)得到缓冲层上沉积一定厚度的断裂式磁性层,再沉积氧化物层,
35.s4)再采用磁控溅射方法将ta或者其它金属沉积在氧化物层上作为保护层,
36.s5)将经过s4)制备的薄膜在真空退火炉中进行退火处理,最终得到可调控co2fex合金垂直磁各向异性的磁性薄膜材料。
37.所述s1)和s4)中的磁控溅射方法的具体工艺为:溅射室本底真空度为1.0
×
10
‑4~9.9
×
10
‑4pa或者1.0
×
10
‑5~9.9
×
10
‑5pa,溅射前通入镀膜室99.99%纯度氩气0.5~1小时,维持在气压0.1~1.5pa;溅射时99.99%纯度的高纯氩气气压为0.2~2.7pa;基片用循环去离子水冷却,平行于基片平面方向加有5~60ka/m的磁场。
38.所述s5)中的退火工艺为:退火炉本底真空为1.0
×
10
‑4~9.9
×
10
‑4pa或者1.0
×
10
‑5~9.9
×
10
‑5pa、退火温度为100
‑
500℃,退火时间为1分钟
‑
120分钟,退火时沿薄膜的易轴方向加5
‑
100ka/m的磁场,并在磁场中随炉冷却。
39.所述缓冲层、氧化物层和保护层的沉积厚度均为:0.1~100.0nm。
40.所述磁性层的厚度为:1.0~200.0nm,所述磁性层结构为co2fex/zr/co2fex,其中,zr和co2fex之间分别沉积或与上层co2fex共溅射,zr占磁性层的质量比为0.001
‑
50%。
41.所述可调控co2fex合金垂直磁各向异性的磁性薄膜材料的热稳定性达到400℃。
42.对比实施例:
43.在磁控溅射仪中制备pt/co2feal/zr/co2feal/mgo/ta薄膜。首先将si基片用有机化学溶剂和去离子水超声清洗,然后装入真空室样品基座上。基片用循环去离子水冷却,平行于基片方向加有16ka/m的磁场,并且基片始终以18转/分钟的速率旋转,溅射沉积速率为0.15nm/分钟。溅射室本底真空4.0
×
10
‑5pa,溅射前通入镀膜室99.99%纯度氩气0.5小时,维持在气压0.5pa。在溅射时99.99%纯度的高纯氩气气压为0.3pa的条件下依次沉积pt/co2feal/zr/co2feal/mgo/ta薄膜,图1a为pt(4nm)/co2feal(0.7nm)/mgo(1.0nm)/ta(2nm)薄膜制备态的磁化曲线,该薄膜显示了面内磁各向异性(ima)。
44.实施例1:
45.溅射室本底真空度为6.0
×
10
‑5pa,溅射前通入镀膜室99.99%纯度氩气0.5小时,维持在气压0.7pa;溅射时99.99%纯度的高纯氩气气压为0.3pa;基片用循环去离子水冷却,平行于基片平面方向加有16ka/m的磁场,以诱发一个易磁化方向。制备pt为缓冲层的薄膜。样品结构pt(4nm)/co2feal(t nm)/mgo(1.0nm)/ta(2nm)(t为co2feal厚度)。
46.在真空退火炉中对薄膜进行退火处理,退火温度为300℃,退火时间为30分钟,并在磁场中随炉冷却。退火炉本底真空为3.0
×
10
‑5pa,退火时沿薄膜的易轴方向加60ka/m的磁场。
47.在制备态,不同厚度的co2feal都显示ima。图1是pt(4nm)/co2feal(0.7nm)/mgo(1.0nm)/ta(2nm)薄膜制备态的磁化曲线,图2是pt(4nm)/co2feal(0.7nm)/mgo(1.0nm)/ta(2nm)薄膜300℃、30分钟退火的磁化曲线。从图上可以看出,0.7nm的co2feal在制备态显示ima,在300℃、30分钟退火后显示较弱的pma。
48.实施例2:
49.溅射室本底真空度为6.0
×
10
‑5pa,溅射前通入镀膜室99.99%纯度氩气0.5小时,维持在气压0.7pa;溅射时99.99%纯度的高纯氩气气压为0.3pa;基片用循环去离子水冷却,平行于基片平面方向加有16ka/m的磁场,以诱发一个易磁化方向。样品结构pt(4nm)/co2feal(0.35nm)/zr(t nm)/co2feal(0.35nm)/mgo(1.0nm)/ta(2nm)(t为zr厚度)。
50.实施例3:
51.溅射室本底真空度为6.0
×
10
‑5pa,溅射前通入镀膜室99.99%纯度氩气0.5小时,维持在气压0.7pa;溅射时99.99%纯度的高纯氩气气压为0.3pa;基片用循环去离子水冷却,平行于基片平面方向加有16ka/m的磁场,以诱发一个易磁化方向。样品结构pt(4nm)/co2fealsi(0.40nm)/zr(t nm)/co2fealsi(0.40nm)/mgo(1.0nm)/ta(2nm)(t为zr厚度)。
52.在真空退火炉中对薄膜进行退火处理,退火温度为300℃,退火时间为30分钟,并在磁场中随炉冷却。退火炉本底真空为3.0
×
10
‑5pa,退火时沿薄膜的易轴方向加60ka/m的磁场。
53.图3为pt(4nm)/co2feal(0.35nm)/zr(0nm)/co2feal(0.35nm)/mgo(1.0nm)/ta(2nm)薄膜300℃、30分钟退火的磁化曲线,图4为pt(4nm)/co2feal(0.35nm)/zr(0.02nm)/co2feal(0.35nm)/mgo(1.0nm)/ta(2nm)薄膜300℃、30分钟退火的磁化曲线,图5为pt(4nm)/co2feal(0.35nm)/zr(0.08nm)/co2feal(0.35nm)/mgo(1.0nm)/ta(2nm)300℃、30分钟退火的磁化曲线,图6为pt(4nm)/co2feal(0.35nm)/zr(0.14nm)/co2feal(0.35nm)/mgo(1.0nm)/ta(2nm)薄膜300℃、30分钟退火的磁化曲线,图7为pt(4nm)/co2feal(0.35nm)/zr(0.20nm)/co2feal(0.35nm)/mgo(1.0nm)/ta(2nm)薄膜300℃、30分钟退火的磁化曲线。图8为(4nm)/co2fealsi(0.40nm)/zr(0.12nm)/co2fealsi(0.40nm)/mgo(1.0nm)/ta(2nm)薄膜300℃、30分钟退火的磁化曲线。从图上可以看出,样品插入zr后都显示pma,且有效磁各向异性常数随着zr厚度增加逐渐增大,当zr为0.14nm时达到最大,之后随着zr厚度增加逐渐减小。可见,这种分裂式的co2feal/zr/co2feal薄膜,可以有效地提高薄膜的pma。
54.上面仅对本发明的较佳实施例作了详细说明,但是本发明并不限于上述实施例,在本领域普通技术人员所具备的知识范围内,还可以在不脱离本发明宗旨的前提下做出各种变化,各种变化均应包含在本发明的保护范围之内。