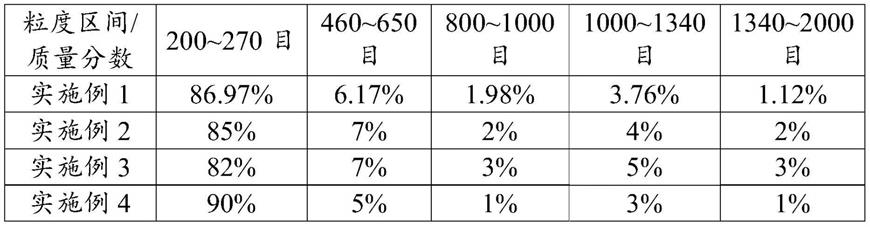
1.本发明属于软磁材料制备技术领域,具体涉及一种混合软磁粉末及其在软磁粉芯制备中的应用。
背景技术:2.磁粉芯是将金属软磁粉末颗粒与绝缘剂混合或使其表层生成一层致密的绝缘膜,再根据实际需要压制成不同形状并通过热处理退火而得到的金属软磁复合材料。通过传统的粉末冶金方法制备,软磁原料粉末的成分、粒度、形貌会影响金属磁粉芯的物理性能和磁性能。作为金属磁粉芯的关键指标之一,磁粉芯的磁导率与磁粉芯的密度息息相关。磁粉芯主要是通过绕制铜线、制成电感应用于电子电力领域,高磁导的磁粉芯可以减少铜线用量以降低生产成本。在保证软磁粉末成分以及形貌固定的条件下,如何通过合理的粒度配比提高磁粉芯的密度进而提升磁导率并保持一定的损耗十分重要。
技术实现要素:3.针对上述现有技术的缺点,本发明提供一种混合软磁粉末及其在软磁粉芯制备中的应用。本发明采用最优粒度配比的混合软磁粉末经过加工,压制,热处理得到密度高、磁导率高、磁损耗低的软磁粉芯。
4.为实现上述目的,本发明采取的技术方案为:一种混合软磁粉末,所述混合软磁粉末为将5个粒径区间的软磁粉末进行混合的混合软磁粉末;其中,相对于混合软磁粉末的总质量,200目≤粒径区间≤270目的软磁粉末的质量比例为82%~90%,460目≤粒径区间≤650目的软磁粉末的质量比例为5%~7%,800目≤粒径区间<1000目的软磁粉末的质量比例为1%~3%,1000目≤粒径区间<1340目的软磁粉末的质量比例为3%~5%,1340目≤粒径区间≤2000目的软磁粉末的质量比例为1%~3%。
5.本发明将五个粒径区间的软磁粉末颗粒按照上述比例配比,以最大粒径区间的颗粒为基准,次粒度区间颗粒填充于最大粒径区间颗粒间隙,按此规则由小粒径区间颗粒填充较大粒径区间颗粒,得到的混合软磁粉末的密度最大,实现单位体积下所填充的混合软磁粉末最密,有利于制备高密度、高磁导率、低磁损耗的软磁粉芯。
6.作为本发明的优选实施方式,所述软磁粉末为雾化或者还原制备的球形铁基软磁粉末,所述球形铁基软磁粉末为纯铁粉、铁硅合金粉末、铁硅铝合金粉末、铁镍合金粉末、铁镍钼合金粉末、铁基非晶合金粉末、铁基纳米晶合金粉末中的至少一种。
7.本发明还要求保护所述混合软磁粉末在软磁粉芯制备中的应用。
8.本发明还要求保护所述一种软磁粉芯,所述软磁粉芯包括混合软磁粉末。
9.本发明将具有最大填充密度的混合软磁粉末应用于软磁粉芯的制备中,有利于优化软磁粉芯的密度、磁导率和磁损耗。
10.作为本发明的优选实施方式,所述软磁粉芯还包括有机硅树脂、溶剂;所述有机硅树脂、混合软磁粉末的质量比为0.004~0.04:1;所述溶剂、混合软磁粉末的体积比为5~
12:1。
11.作为本发明的优选实施方式,所述溶剂为丙酮。
12.本发明所述软磁粉芯的制备方法,包括如下步骤:
13.(1)将混合软磁粉末、有机硅树脂、溶剂混合并超声搅拌均匀至溶剂挥发,得到混合粉末;
14.(2)将混合粉末干燥后,压制成生坯;
15.(3)将生坯在真空或惰性气体下退火热处理得到软磁粉芯。
16.作为本发明的优选实施方式,所述步骤(2)中,干燥为真空干燥,干燥温度为60~100℃,时间为1~3小时。
17.作为本发明的优选实施方式,所述步骤(2)中,压制的压力为1000~2000mpa,保压时间5~15秒。
18.作为本发明的优选实施方式,所述步骤(3)中,退火热处理的温度为200~500℃,时间为1~3小时。
19.所述惰性气体为氮气、氩气、氦气中的至少一种。
20.与现有技术相比,本发明的有益效果为:本发明将五个粒径区间的软磁粉末颗粒按照本发明限定的比例配比,得到的混合软磁粉末的密度最大,实现单位体积下所填充的混合软磁粉末最密,有利于制备高密度、高磁导率、低磁损耗的软磁粉芯。
附图说明
21.图1为实施例1-2和对比例1制备的软磁粉芯的磁导率图;
22.图2为实施例1-2和对比例1制备的软磁粉芯的磁损耗图。
具体实施方式
23.为更好地说明本发明的目的、技术方案和优点,下面将结合具体实施例对本发明作进一步说明。
24.本发明实施例和对比例中所述软磁粉末为铁硅合金粉末,即为fe-6.5wt%si合金粉末。
25.实施例1-6和对比例1-5所述混合软磁粉末的粒度配比如表1所述。
26.表1所述混合软磁粉末的粒度配比
27.[0028][0029]
表1中200~270目为200目≤粒径区间≤270目;460~650目为460目≤粒径区间≤650目;800~1000目为800目≤粒径区间<1000目;1000~1340目为1000目≤粒径区间<1340目;1340~2000目为1340目≤粒径区间≤2000目。
[0030]
实施例1-4和对比例1-5所述软磁粉芯的制备方法,包括如下步骤:
[0031]
(1)将混合软磁粉末、有机硅树脂、丙酮混合并超声搅拌均匀至丙酮挥发,得到混合粉末;所述有机硅树脂、混合软磁粉末的质量比为0.02:1;所述丙酮、混合软磁粉末的体积比为8:1;
[0032]
(2)将混合粉末在80℃下真空干燥2小时后,在压制的压力为1500mpa下保压10秒,压制成生坯;
[0033]
(3)将生坯在真空、400℃下退火热处理2小时得到软磁粉芯。
[0034]
实施例5所述软磁粉芯的制备方法,包括如下步骤:
[0035]
(1)将混合软磁粉末、有机硅树脂、丙酮混合并超声搅拌均匀至丙酮挥发,得到混合粉末;所述有机硅树脂、混合软磁粉末的质量比为0.04:1;所述丙酮、混合软磁粉末的体积比为5:1;
[0036]
(2)将混合粉末在100℃下真空干燥1小时后,在压制的压力为1000mpa下保压15秒,压制成生坯;
[0037]
(3)将生坯在氮气氛围下、200℃下退火热处理3小时得到软磁粉芯。
[0038]
实施例6所述软磁粉芯的制备方法,包括如下步骤:
[0039]
(1)将混合软磁粉末、有机硅树脂、丙酮混合并超声搅拌均匀至丙酮挥发,得到混合粉末;所述有机硅树脂、混合软磁粉末的质量比为0.004:1;所述丙酮、混合软磁粉末的体积比为12:1;
[0040]
(2)将混合粉末在60℃下真空干燥3小时后,在压制的压力为2000mpa下保压5秒,压制成生坯;
[0041]
(3)将生坯在真空、500℃下退火热处理1小时得到软磁粉芯。
[0042]
对比例6
[0043]
表2对比例6所述混合软磁粉末的粒度配比
[0044][0045]
表2中200~286目为200目≤粒径区间≤286目;483~690目为483目≤粒径区间≤690目;889~1270目为889目≤粒径区间<1270目;1270~1633目为1270目≤粒径区间≤
1633目;1709~2442目为1709目≤粒径区间≤2442目。
[0046]
对比例6所述软磁粉芯的制备方法与实施例1相同。
[0047]
效果例
[0048]
本效果例是为了测试实施例1-6和对比例1-6所述软磁粉芯的粉芯密度、粉芯磁性能以及粉末松装密度。
[0049]
表3实施例1-6和对比例1-6所述软磁粉芯的性能
[0050][0051]
根据表3的结果可知,与对比例1-6对比,实施例1-6所制备的软磁粉芯具有较高的粉芯密度、粉芯磁导率和较低的粉芯损耗,说明将本发明所述具有最大填充密度的混合软磁粉末用于软磁粉芯的制备中,有利于优化软磁粉芯的密度、磁导率和磁损耗。
[0052]
最后所应当说明的是,以上实施例仅用以说明本发明的技术方案而非对本发明保护范围的限制,尽管参照较佳实施例对本发明作了详细说明,本领域的普通技术人员应当理解,可以对本发明的技术方案进行修改或者等同替换,而不脱离本发明技术方案的实质和范围。