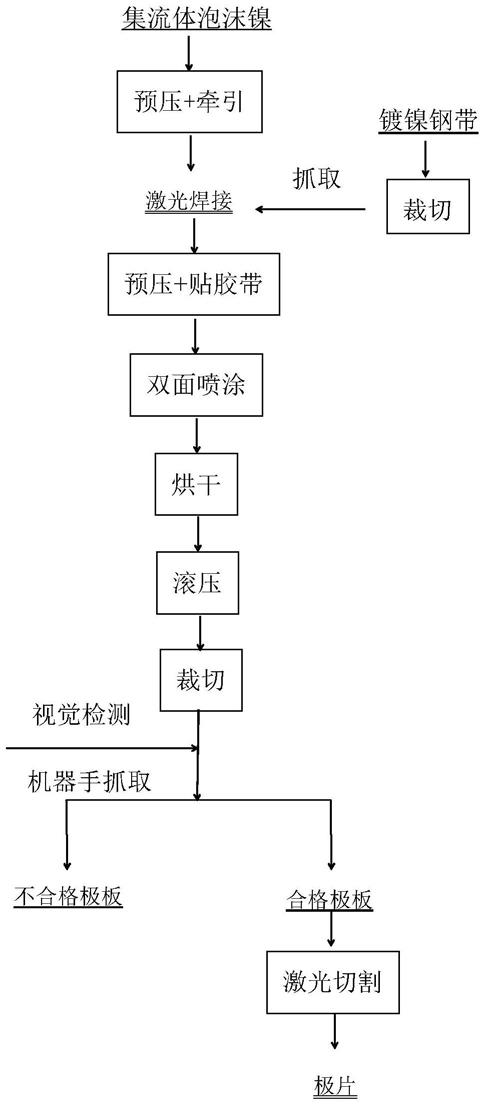
1.本发明属于二次电池制造技术领域,具体涉及一种稀土新电源极片、其制备方法及由其制备的电池。
背景技术:2.大容量水系二次电池具有高安全、长寿命、环境温度范围宽(-55℃~60℃)等优点,一直获得大量应用,但大容量水系二次电池的电芯由正负极片交替组合,高效生产高品质极片一直是生产流程的关键工序。
3.现有技术通常是在极板生产出来后,专门焊接导电极耳成极片,极板生产过程中需要使用胶带保证预留的白边不受污染,极板生产前需要把胶带去除,去除胶带过程中存在撕裂白边的风险和需要一名操作人员看守,而焊接极耳后需要再贴上新胶带,因此,这种焊接存在周转工序多,人工效率较低和胶带利用率低于50%等问题。也有一种端面焊工艺,将整卷镀镍钢带预先焊接在泡沫镍白边,但具有只能应用在负极极片生产、极片厚度不能太厚等缺陷,若能开发一种极板与极耳在线直接成型的极片制备方法,正极和负极均可应用,还能适应不同厚度,很有工业和商业价值。
技术实现要素:4.现有技术通过先生产制造极板、再专门单独焊接极耳制备极片,存在工序多、生产效率低等问题,针对现有技术的不足,本发明的目的是提供一种稀土新电源极片的制备方法,能够实现极板与极耳在线直接成型制备极片,实现极片在线连续生产和一体化制备,具有生产效率高和生产更智能的优势,胶带利用率高,且正极和负极均可应用,还能适应不同厚度;本发明还提供一种由该制备方法制备得到的稀土新电源极片;本发明还提供一种由该极片制备得到的电池。
5.本发明提供一种稀土新电源极片的制备方法,包括以下步骤:
6.(1)将集流体泡沫镍预压滚,所述集流体泡沫镍其中一个边预留白边,经牵引进入焊接平台;
7.(2)将镀镍钢带裁切成若干段,分别采用激光焊接在步骤(1)得到的集流体泡沫镍的白边上,预压后进行双面贴胶带;其中每一段镀镍钢带的长度是极板宽度的整数倍;
8.(3)经牵引进入喷涂浆料工位喷涂浆料;
9.(4)经牵引进入烘干室进行烘干,出来后滚压;
10.(5)进行横向裁切,再经极耳成型切割后,得到极片。
11.泡沫镍作为集流体具有电池活性材料附着力强的优势,但也存在滚压后延伸的劣势,这也是现有技术一直想实现一体化极片成型,却始终无法实现的技术瓶颈。本发明中镀镍钢带不能整个焊接在集流体泡沫镍的白边上,因为泡沫镍在后续滚压后存在延伸,但镀镍钢带不延伸,整体基带(基带是指焊接了镀镍钢带的泡沫镍)就会变形甚至卷曲,导致极板报废。本发明通过将镀镍钢带裁切成若干段,以分段焊接的方式分别焊接在集流体泡沫
镍的白边上,解决了镀镍钢带和泡沫镍延伸不同步的问题,采用喷涂浆料的上料方式减少浆料对胶带的污染,后续激光切割成型极耳,实现了极板与极耳在线直接成型制备极片,实现极片在线连续生产,实现一体化极片成型。其中,每一段镀镍钢带的长度是极板宽度的整数倍,也就是每次裁切并不一定是沿两段镀镍钢带的交接处裁切,但镀镍钢带采用此长度能保证裁切时最后一刀在两段镀镍钢带的交接处裁切。比如如果极板宽度为100mm,镀镍钢带的长度采用100mm的整数倍,以300mm为例,那么基带递送过去,后续裁切时裁切刀会快速裁切三次,最后一刀在两段镀镍钢带的交接处裁切。为防止纠偏困难,泡沫镍只有其中一个边预留白边,成品率高,不能两边都有,也不能在中间。采用喷涂浆料的方式可以有效解决浆料污染胶带表面问题。
12.如果泡沫镍孔数太多,孔径偏小,电池浆料不易喷涂,且喷涂压力增大,导致基带走动过程中容易断带;如果孔数太少,孔径偏大,电池浆料填充太多,后续最终滚压后容易开裂。泡沫镍厚度选择因素与孔数成直接关系,如果太厚,造成每卷泡沫镍直径过大,生产上不好操作;如果太薄,泡沫镍进货质量不好把控;泡沫镍宽度基于极板尺寸和延伸率考虑,如果宽度太小,泡沫镍强度会大大降低,很难适应连续生产;如果宽度太大,横向延伸率产生的绝对值增加,滚压后极板的横向变形超过上限报警值,造成极板报废几率增加。本发明基于后续镀镍钢带焊接和预压等因素考虑,优选地,步骤(1)中集流体泡沫镍的孔数为90~120ppi,厚度为0.7~2.4mm,宽度为60~300mm。
13.泡沫镍一边预留宽度8~10mm,作为与镀镍钢带焊接的叠压处,也叫白边。为防止纠偏困难,泡沫镍只有其中一个边预留白边,成品率高,不能两边都有,也不能在中间;电池材料附着的地方(也就是步骤(4)喷涂浆料的地方),叫非白边。白边需要焊接镀镍钢带,多孔的泡沫镍经过预压滚后,密度增大,增加与镀镍钢带的接触面,利于后续激光焊接。但白边不能压的太薄,如果太薄,导致白边机械强度下降,容易撕裂;非白边的预压主要是控制单位面积上浆料量,从而控制最终的单位面积比重,需要根据后续极板要求定预压厚度,不能太厚,太厚了,浆料量太多,后续滚压容易开裂,也不能太薄,太薄导致上浆料量少,电池容量太低。优选地,步骤(1)中预压滚为:将集流体泡沫镍进行预压滚,将集流体泡沫镍其中一个边预压宽度至8~10mm作为白边,白边预压厚度至0.2~0.5mm,非白边预压厚度至0.5~0.9mm。
14.如果镀镍钢带太薄,镀镍钢带生产困难,采购成本急剧增加,且本身刚度较低,生产工序抓取每一段镀镍钢带,容易弯曲,导致左右偏差大;如果太厚,一方面要大幅度提高激光焊接功率才能熔透,增加设备投入,另一方面是重量增加太多,降低电池质量比能量。镀镍钢带的宽度是根据极片要求定。作为一种优选方案,镀镍钢带不能太窄,如果太窄,成型后的极耳突出端太少,不能满足与极柱焊接要求,也不能太宽,太宽会造成电池内部无效空间增加,间接降低电池体积比能量。优选地,步骤(2)中镀镍钢带的厚度为0.05~1.5mm,宽度为15~35mm。
15.步骤(2)将镀镍钢带裁切成若干段,每一段镀镍钢带不能太长,一方面机器手抓取有一定的尺寸上限限制,另一方面,需要控制在延伸率上限范围内,第三还需要考虑后续裁切的频率和极板宽度,通常裁切是连续裁切2片或3片或多片才牵引基带往前移动,也就是间歇式连续移动,因此,每一段镀镍钢带长度是极板宽度的2n或3n的倍数。优选地,步骤(2)中每一段镀镍钢带的长度为300~1000mm,是极板宽度的2n倍或3n倍,n为阿拉伯数字1~9
的整数。
16.优选地,步骤(2)中,激光焊接采用连续点焊成焊缝的方式,也就是点状连续焊接,外观呈直线;为了增加导电性,所述焊缝为两条;焊缝与镀镍钢带的长边相平行,为避免热量集中,两条焊缝距离一定间隙;白边的最大宽度只有10mm,焊缝宽度本身2~3mm,所以两条焊缝之间的距离不能太远,优选为2~3mm。焊接往后,表面会有一定的毛刺,进行预压可以消除毛刺,然后贴上胶带,彻底消除毛刺隐患,杜绝毛刺微短路。
17.优选地,步骤(3)中喷涂浆料为双面喷涂。镀镍钢带焊接后贴上了胶带,由于胶带在后续是需要保持继续使用,尽可能减少浆料附着,采用双面喷涂可以有效解决浆料污染胶带表面问题。目前水系浆料通常是单面喷涂,另一面为负压吸料,此种容易造成基带向前移动过程中,基带向一边偏移,存在断带风险;采用双面喷涂,两侧受力均匀。
18.优选地,步骤(4)中烘干室为双向垂直烘干室,所述双向垂直烘干室是由上升段烘干区和下降段烘干区组成,上升段烘干区和下降段烘干区相互平行且均与地面垂直,共分为4-6段温度烘干区,上升段有2-3段烘干区,下降段有2-3段烘干区。喷涂后的浆料需要快速烘干,为避免出现浆料流挂现象所导致的基带表面不均匀,烘干区域分成多段,有利于温度控制均匀,采用垂直上下方便烘干,一方面减少设备整体长度,另一方面也是因为水系浆料特征,垂直方式烘干快速均匀,还有利于干燥产生的水蒸气快速排出,提高烘干效率和浆料干燥质量。
19.水系浆料烘干温度如果太高,容易导致烘干速度过快,浆料表面发硬,易开裂;烘干温度如果太低,浆料内的水分不容易挥发,本发明优选所有烘干区的烘干温度在90~145℃内,起点烘干区温度高,起点烘干区温度优选在120~145℃,中间烘干区的温度高低交替,前后烘干区温差在5~15℃,可形成温度气氛波动,有利于水蒸汽排出,末端烘干区的温度低,末端烘干区的温度优选90~110℃,避免浆料干燥后冷却速度快导致的开裂。
20.优选地,步骤(4)中滚压压力80~400t。烘干出来的基带,经过校正偏移后,温度一般在40~50℃,进入辊压机,经过一定的压力滚压成一定厚度的基带,根据电池材料活性物质、极片厚度、压实密度要求,设置不同压力,通常正极极片压力较低,最低可80t,如果过低,极板的活性物质材料之间结合度不够,影响极片寿命;负极压力较高,最高达到400t,如果过高,设备投资过高,负极活性材料颗粒也容易压的过碎,影响电池倍率性能。
21.优选地,步骤(5)为:按照设置参数进行横向裁切,裁切出来的极板通过视觉装置扫描,合格极板经机器手进入激光切割工位,再经极耳成型切割后,制备出极片。横向裁切出来的极板为长方形或正方形,在裁切过程中,比如起步的首片,一般是作为废片,后续间歇连续裁切中,有些极板裁切为斜片,通过视觉装置进行在线监测,将不符合要求的抓取放置一边,由人工处理;裁切合格的极板,机器手直接抓取放置在激光裁切工位,由激光切割机进行极耳成型切割,切割完毕,制备得到极片。优选地,步骤(5)中裁切出来的极板:宽度50~120mm,长度65~330mm,厚度0.16~0.4mm,极板长度=泡沫镍的宽度+镀镍钢带的宽度-重叠部分,重叠部分也就是白边宽度;所对应制备出来的极片:宽度50~120mm,长度65~330mm,厚度0.16~0.4mm。
22.本发明还提供一种上述任一制备方法制备得到的稀土新电源极片。
23.采用上述方法能够适用于制备正极和负极,也适用于制备不同厚度,均具有较高的成品率。
24.本发明还提供一种上述稀土新电源极片制备的电池,制备工艺采用现有工艺,将所述的稀土新电源极片进入后续清粉工序,正负极极片与隔膜交替叠片成电芯,经入壳、注液、封口、化成,制造出成品电池。
25.综上所述,本发明具有以下优点:
26.(1)泡沫镍作为集流体具有电池活性材料附着力强的优势,但也存在滚压后延伸的劣势,这也是现有技术一直想实现一体化极片成型,却始终无法实现的技术瓶颈。本发明中镀镍钢带不能整个焊接在集流体泡沫镍的白边上,因为泡沫镍在后续滚压后存在延伸,但镀镍钢带不延伸,整体基带就会变形甚至卷曲,导致极板报废。本发明通过将镀镍钢带裁切成若干段,以分段焊接的方式分别焊接在集流体泡沫镍的白边上,也就是将镀镍钢带分段预先与集流体泡沫镍焊接,解决了镀镍钢带和泡沫镍延伸不同步的问题,采用喷涂浆料的上料方式减少浆料对胶带的污染,后续激光切割成型极耳,实现了极板与极耳在线直接成型制备极片,实现极片在线连续生产,实现一体化极片成型。
27.(2)本发明相对于现有技术通过先生产制造极板,再专门单独焊接极耳制备极片,还具有生产效率高和生产更智能的优势。
28.(3)为防止纠偏困难,泡沫镍只有其中一个边预留白边,成品率高。
29.(4)采用喷涂浆料的方式可以有效解决浆料污染胶带表面问题。
30.(5)本发明正极和负极均可应用,还能适应不同厚度,应用范围广。
31.(6)本发明对胶带利用率几乎100%,经济环保。
附图说明
32.图1是本发明所述的稀土新电源极片的制备方法的工艺流程图。
具体实施方式
33.下面结合实施例对本发明做进一步说明。
34.实施例1
35.一种稀土新电源极片的制备方法,包括以下步骤:
36.(1)选取孔数为100ppi、厚度为2.0mm、宽度为200mm的泡沫镍作为集流体,将集流体泡沫镍进行预压滚,将集流体泡沫镍其中一个边预压宽度至9mm作为白边,白边预压厚度至0.4mm,非白边预压厚度至0.7mm,经牵引进入焊接平台;
37.(2)选取厚度为1.0mm、宽度为22mm的镀镍钢带,将此镀镍钢带裁切成若干段,每一段镀镍钢带的长度为300mm,长度是极板宽度的3倍,分别采用点焊成焊缝的方式激光焊接在步骤(1)得到的集流体泡沫镍的白边上,焊接两条焊缝,焊缝与镀镍钢带的长边相平行,两条焊缝之间的距离为3mm,预压后进行双面贴胶带;
38.(3)经牵引进入喷涂浆料工位双面喷涂浆料;
39.(4)经牵引进入烘干室进行烘干,烘干室为双向垂直烘干室,所述双向垂直烘干室是由上升段烘干区和下降段烘干区组成,上升段烘干区和下降段烘干区相互平行且均与地面垂直,共分为6段温度烘干区,上升段有3段烘干区,下降段有3段烘干区,起点烘干区温度高,中间烘干区的温度高低交替,从上升至下降每个温区的温度是:140
±
2℃、125
±
2℃、130
±
2℃、115
±
2℃、120
±
2℃、105
±
2℃,出来后滚压,滚压压力为200t;
40.(5)按照设置参数进行横向裁切,裁切出来的极板:宽度100mm,长度213mm,厚度0.3mm;所对应制备出来的极片:宽度100mm,长度213mm,厚度0.3mm;裁切出来的极板通过视觉装置扫描,合格极板经机器手进入激光切割工位,再经极耳成型切割后,制备出极片。
41.通过此实施例制造的极片,胶带利用率由现有技术46%提升到98.5%,直接取消了现有工艺中的极耳单独焊接工序——原先一条极片生产线含极耳单独焊接工序需要16台焊接设备对应两台基板涂布生产线,每一台焊接设备需要两个人工,1个负责操作焊接设备和周转,1个负责极耳整理、基板清粉和极片配重,加上基板涂布生产线6个人(含两台基板涂布生产线的两名撕胶带人员),共需要38个人。
42.本实施例取消撕胶带工位,相应人工数为0,不需要单独的极耳焊接机,基板生产出来经检测合格后直接通过机器手进入激光切割极耳成型极片工位,整体自动化联通,自动化监控人员增加1人,也省略基板到极耳焊接的人工周转,一条极片生产线的工人用数减少至6人,极片人工周转次数减少50%,本实施例成品率达到98.5%。
43.将制备得到的极片进入后续清粉工序,正负极极片与隔膜交替叠片成电芯,经入壳、注液、封口、化成,制造出成品电池。
44.实施例2
45.一种稀土新电源极片的制备方法,包括以下步骤:
46.(1)选取孔数为90ppi、厚度为1.0mm、宽度为100mm的泡沫镍作为集流体,将集流体泡沫镍进行预压滚,将集流体泡沫镍其中一个预压宽度至8mm作为白边,白边预压厚度至0.2mm,非白边预压厚度至0.5mm,经牵引进入焊接平台;
47.(2)选取厚度为0.1mm、宽度为15mm的镀镍钢带,将此镀镍钢带裁切成若干段,每一段镀镍钢带的长度为500mm,长度是极板宽度的10倍,分别采用点焊成焊缝的方式激光焊接在步骤(1)得到的集流体泡沫镍的白边上,焊接两条焊缝,焊缝与镀镍钢带的长边相平行,两条焊缝之间的距离为2mm,预压后进行双面贴胶带;
48.(3)经牵引进入喷涂浆料工位双面喷涂浆料;
49.(4)经牵引进入烘干室进行烘干,烘干室为双向垂直烘干室,所述双向垂直烘干室是由上升段烘干区和下降段烘干区组成,上升段烘干区和下降段烘干区相互平行且均与地面垂直,共分为6段温度烘干区,上升段有3段烘干区,下降段有3段烘干区,起点烘干区温度高,中间烘干区的温度高低交替,从上升至下降每个温区的温度是:130
±
2℃、120
±
2℃、125
±
2℃、110
±
2℃、115
±
2℃、100
±
2℃,出来后滚压,滚压压力为80t;
50.(5)按照设置参数进行横向裁切,裁切出来的极板:宽度50mm,长度107mm,厚度0.2mm;所对应制备出来的极片:宽度50mm,长度107mm,厚度0.2mm;裁切出来的极板通过视觉装置扫描,合格极板经机器手进入激光切割工位,再经极耳成型切割后,制备出极片。
51.通过此实施例制造的极片,胶带利用率由现有技术48%提升到98%,直接取消了现有工艺中的极耳单独焊接工序——原先一条极片生产线含极耳单独焊接工序需要24台焊接设备对应两台基板涂布生产线,每一台焊接设备需要两个人工,1个负责操作焊接设备和周转,1个负责极耳整理、基板清粉和极片配重,加上基板涂布生产线6个人(含两台基板涂布生产线的两名撕胶带人员),共需要54个人。本实施例取消撕胶带工位,相应人工数为0,不需要单独的极耳焊接机,基板生产出来经检测合格后直接通过机器手进入激光切割极耳成型极片工位,整体自动化联通,自动化监控人员增加1人,也省略基板到极耳焊接的人
工周转,一条极片生产线的工人用数减少至6人,极片人工周转次数减少50%,本实施例成品率达到98%。
52.将制备得到的极片进入后续清粉工序,正负极极片与隔膜交替叠片成电芯,经入壳、注液、封口、化成,制造出成品电池。
53.实施例3
54.一种稀土新电源极片的制备方法,包括以下步骤:
55.(1)选取孔数为120ppi、厚度为2.4mm、宽度为300mm的泡沫镍作为集流体,将集流体泡沫镍进行预压滚,将集流体泡沫镍其中一个预压宽度至10mm作为白边,白边预压厚度至0.5mm,非白边预压厚度至0.9mm,经牵引进入焊接平台;
56.(2)选取厚度为1.5mm、宽度为35mm的镀镍钢带,将此镀镍钢带裁切成若干段,每一段镀镍钢带的长度为720mm,长度是极板宽度的6倍,分别采用点焊成焊缝的方式激光焊接在步骤(1)得到的集流体泡沫镍的白边上,焊接两条焊缝,两条焊缝之间的距离为3mm,预压后进行双面贴胶带;
57.(3)经牵引进入喷涂浆料工位双面喷涂浆料;
58.(4)经牵引进入烘干室进行烘干,烘干室为双向垂直烘干室,所述双向垂直烘干室是由上升段烘干区和下降段烘干区组成,共分为6段温度烘干区,上升段有3段烘干区,下降段有3段烘干区,起点烘干区温度高,中间烘干区的温度高低交替,从上升至下降每个温区的温度是:140
±
2℃、125
±
2℃、130
±
2℃、115
±
2℃、120
±
2℃、105
±
2℃,出来后滚压,滚压压力为100t;
59.(5)按照设置参数进行横向裁切,裁切出来的极板:宽度120mm,长度325mm,厚度0.4mm;所对应制备出来的极片:宽度120mm,长度325mm,厚度0.4mm;裁切出来的极板通过视觉装置扫描,合格极板经机器手进入激光切割工位,再经极耳成型切割后,制备出极片。
60.通过此实施例制造的极片,胶带利用率由现有技术47%提升到99%,直接取消了现有工艺中的极耳单独焊接工序——原先一条极片生产线含极耳单独焊接工序需要12台焊接设备对应两台基板涂布生产线,每一台焊接设备需要两个人工,1个负责操作焊接设备和周转,1个负责极耳整理、基板清粉和极片配重,加上基板涂布生产线6个人(含两台基板涂布生产线的两名撕胶带人员),共需要30个人。本实施例取消撕胶带工位,相应人工数为0,不需要单独的极耳焊接机,基板生产出来经检测合格后直接通过机器手进入激光切割极耳成型极片工位,整体自动化联通,自动化监控人员增加1人,也省略基板到极耳焊接的人工周转,一条极片生产线的工人用数减少至6人,极片人工周转次数减少50%,成品率达到99%。
61.将制备得到的极片进入后续清粉工序,正负极极片与隔膜交替叠片成电芯,经入壳、注液、封口、化成,制造出成品电池。
62.实施例4
63.一种稀土新电源极片的制备方法,与实施例1基本一致,唯一不同在于:步骤(4)为:经牵引进入烘干室进行烘干,烘干室为普通烘干设备,烘干温度是:100℃,出来后滚压,滚压压力为200t。
64.通过此实施例制造的极片,胶带利用率由现有技术46%提升到91.2%,人工数下降至7人,极片周转次数减少50%,成品率达到91.2%。
65.通过实施例1-4可以看出,步骤(4)烘干室采用双向垂直烘干室,与采用普通烘干设备相比,成品率更高。
66.对比例1
67.一种稀土新电源极片的制备方法,与实施例1基本一致,唯一不同在于:每一段镀镍钢带的长度为320mm,长度是极板宽度的3.2倍。
68.通过对比例1制造的极片,成品率为72.1%。
69.由于对比例1中每一段镀镍钢带的长度是极板宽度的3.2倍,并不是整数倍,步骤(5)在裁切时,裁切后有的极板上有两段镀镍钢带的交接处,是不合品。
70.由实施例1和对比例1可以看出,步骤(2)将镀镍钢带裁切成若干段,每一段镀镍钢带的长度是极板宽度的整数倍,与非整数倍相比,成品率更高。
71.对比例2
72.一种稀土新电源极片的制备方法,与实施例1基本一致,唯一不同在于:步骤(1)中将集流体泡沫镍的两侧的两个边均预压宽度至9mm作为白边,步骤(2)中分别采用点焊成焊缝的方式激光焊接在步骤(1)得到的集流体泡沫镍的每个白边上,每个白边均焊接两条焊缝。
73.通过此实施例制造的极片,胶带利用率由现有技术46%提升到75%,自动化监控人员需要增加4人,人工数下降至9人,极片周转次数减少50%,但成品率仅为75%。
74.通过实施例1和对比例2可以看出,集流体泡沫镍只有一侧有白边,进行点焊成焊缝的方式激光焊接在集流体泡沫镍的白边上,与两侧均有白边进行焊接相比,成品率更高。
75.对于本领域技术人员而言,以上所述,仅是本发明的较佳实施例而已,并非是对本发明作其它形式的限制,任何熟悉本专业的技术人员可能利用上述揭示的技术内容加以变更或改型为等同变化的等效实施例,如正负极与凝胶隔膜采用卷绕方式。但是凡是未脱离本发明技术方案内容,依据本发明的技术实质对以上实施例所作的任何简单修改、等同变化与改型,仍属于本发明技术方案的保护范围。
76.此外,应当理解,虽然本说明书按照实施方式加以描述,但并非每个实施方式仅包含一个独立的技术方案,说明书的这种叙述方式仅仅是为清楚所见,本领域技术人员应当将说明书作为一个整体,各实施例中的技术方案也可以经适当组合,形成本领域技术人员可以理解的其他实施方式。