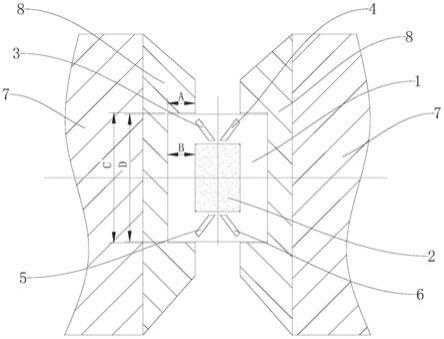
1.本发明涉及一种减小烧结钕铁硼磁体双面表磁差异技术,尤其是涉及一种减小烧结钕铁硼磁体双面表磁差异的方法。
背景技术:2.随着伺服电机、传感器、手机振动马达和无线充电器等产品应用的快速发展,降低成本、缩小体积、提高效率成为了当下这些工业产品的发展趋势,与此同时,这对应用在这些产品上的烧结钕铁硼磁体双面表磁一致性要求也随之提高。因生产技术受限,当前常用的生产双面表磁差异要求高(≤5%)的烧结钕铁硼磁体的方法,主要是通过加大毛坯磨削余量和成品全检的方法进行,但是该方法产品合格率低,材料利用率低,造成烧结钕铁硼磁体成本居高不下。
3.公开号为cn111489889a的中国发明专利申请中公开了一种高同质性高性能稀土永磁的制备方法,该方法在气流磨磨粉时采用脉冲喷雾方式均匀加入混合液体添加剂来提高粉料的流动性,以期改善坯体密度以及局域磁畴取向的均匀性,并在阴模内设聚磁板、压机的上压头和下压头都选用相对磁导率200~400的近磁导率材料来制作,以此优化成型模具的磁路结构,提高磁体的取向度,从而改善磁体的ns极差异,同时细粉采用装粉靴自动往复来回筛入附近设置有近磁导率聚磁板的阴模模腔内,然后使用振动器振动下压头,使初始布粉均匀化,此时粉料为松装状态,粉料松装尺寸为成型尺寸的1.5~2倍,然后采用3次磁化对向渐进预压工艺,脉冲磁场磁振取向使磁粉在磁场作用下自动均匀排列于阴模模腔中,每完成一次磁场取向,由压机的plc自动控制上压头、下压头分别进入阴模模腔中预先设置四五位移点,瞬时取向磁场峰值为2~3.5t,反复多次取向,上压头和下压头反复多次对向预压,多次预压后尺寸不小于最终压制成型尺寸的1.25倍,完成最后一次磁振取向后,上压头、下压头双向压制直至达到设定压制成型尺寸值,并完成退磁后制得生坯。
4.但是,上述方法中,气流磨磨粉时采用脉冲喷雾方式均匀加入混合液体添加剂,而混合液体添加剂中加入了氢化纳米重稀土金属,其核心目的是提高磁体的矫顽力,并不能直接起到改善两面表磁差异的作用,而阴模内设聚磁板、上压头和下压头都选用相对磁导率200~400的近磁导率材料来制作,虽然一定程度上能够改善两面表磁差异,但成型压制结束后聚磁板存在残磁,生坯在脱模过程中摩擦力增大,生坯容易产生缺角及裂纹等缺陷。生坯完成脱模后,因上压头和下压头存在残磁,生坯容易被上压头带起之后跌落而造成缺角,或生坯吸附在下压头上存在难以取料的问题,以致产品合格率低下。另外,采用装粉靴自动往复喂料,喂料结束才振动下压头并不能使初始布粉达到最佳均匀化的效果,且采用多次预压、多次取向的工艺方法,成型单模生产周期较常规工艺耗时长30%以上,成型生产效率低下,并不可取。
技术实现要素:5.本发明所要解决的技术问题是提供一种减小烧结钕铁硼磁体双面表磁差异的方
法,该方法在显著减小烧结钕铁硼磁体双面表磁差异的同时,能够提高产品合格率和生产效率。
6.本发明解决上述技术问题所采用的技术方案为:一种减小烧结钕铁硼磁体双面表磁差异的方法,包括以下步骤:
7.(1)、依配方完成烧结钕铁硼磁体的配料作业,采用熔炼炉制备获得铸片,将铸片破碎及除杂后送入氢碎炉氢破碎,得到氢碎粉料,对氢碎粉料进行分选,去除粒径尺寸在5μm之下的筛下物和100μm以上的筛上物,得到粒径范围在5μm~100μm的氢碎粉,向氢碎粉中添加润滑剂混合均匀后进入气流磨设备研磨制粉,得到粒径范围在2.5~5μm的细粉,其中氢碎粉和润滑剂混合时间控制到80分钟以上,润滑剂添加量为氢碎粉重量的0.5
‰
~1.5
‰
,然后细粉中添加润滑剂混合均匀后在温度15~22℃的环境下静置8h以上,其中细粉和润滑剂混合时间控制到200分钟以上,润滑剂添加量为细粉重量的0.5
‰
~2.0
‰
,最后采用100目~200目筛网过筛并装瓶,得到预混合粉;
8.(2)、准备成型模具和压机,并将所述的成型模具安装在所述的压机上,具体为:
9.所述的成型模具包括上压头、下压头、阴模、阴模模腔和4个镶件,所述的阴模为长方体结构,所述的阴模模腔通过在所述的阴模中部开设上下贯通的长方体形状内腔实现,所述的阴模的材质为非导磁合金或非导磁模具钢,4个镶件的材质为导磁材料,所述的上压头和所述的下压头材质为非导磁合金或非导磁模具钢,所述的阴模模腔的宽度尺寸为烧结宽度收缩率乘以1~2倍的黑片宽度尺寸减去生坯回弹量,所述的阴模模腔的取向尺寸为烧结取向收缩率乘以1~15倍的黑片取向尺寸减去生坯回弹量,且所述的阴模模腔的取向尺寸控制在20~45mm之间,以保证所述的阴模模腔内磁场均匀度及兼顾生产效率,其中烧结钕铁硼磁体毛坯经切割后的半成品称之为黑片,含机械加工余量,4个镶件嵌入所述的阴模内,将4个镶件分别称为第一镶件、第二镶件、第三镶件和第四镶件,所述的第一镶件和所述的第二镶件左右对称设置在所述的阴模模腔的前侧且相对于所述的阴模模腔沿前后方向的对称平面左右对称,所述的第三镶件和所述的第四镶件左右对称设置在所述的阴模模腔的后侧且相对于所述的阴模模腔沿前后方向的对称平面左右对称,所述的第一镶件和所述的第三镶件相对于所述的阴模模腔沿左右方向的对称平面前后对称,所述的第二镶件和所述的第四镶件相对于所述的阴模模腔沿左右方向的对称平面前后对称,所述的第一镶件、所述的第二镶件、所述的第三镶件和所述的第四镶件与所述的阴模模腔沿前后方向的对称平面之间的夹角均为45度,每个所述的镶件的宽度尺寸为4~10mm,每个所述的镶件距离所述的阴模模腔宽度工作面的距离为3~5mm;
10.所述的压机包括plc控制系统、压机工作台、模架、上油缸、下油缸、上模冲、下模冲、喂料系统、充磁系统和振动器,所述的模架安装在所述的压机工作台上,所述的上模冲安装在所述的上油缸上,所述的下模冲安装在所述的下油缸上,所述的振动器分别与所述的模架和所述的下模冲连接,所述的充磁系统包含两个线圈、两个极柱以及两个充磁极头,两个线圈一一对应绕制在两个极柱上,两个极柱左右间隔设置,两个充磁极头一一对应固定在两个极柱内侧上,两个充磁极头均为收敛锥体,且左右对称设置,两个充磁极头上沿其中线对称开槽,开槽深度与所述的阴模取向方向壁厚相等,开槽长度比所述的阴模的长度尺寸大0.02~0.05μm;
11.所述的成型模具的上压头安装在所述的压机的上模冲上,所述的成型模具的下压
头安装在所述的压机的下模冲上,所述的阴模安装在所述的模架上,所述的阴模卡紧在两个充磁极头的开槽内,所述的第一镶件和所述的第三镶件的外边延长线与位于左侧的充磁极头上的开槽顶点相交,所述的第二镶件和所述的第四镶件的外边延长线与位于右侧的充磁极头上的开槽顶点相交;
12.(3)、调整所述的压机,使其上油缸和下油缸位于初始位置,此时上压头和下压头位于预设的初始位置,采用喂料系统自动往复来回多次将步骤(1)获得的预混合粉喂料到所述的阴模模腔内,同时使用振动器振动所述的阴模和所述的下压头,具体为:所述的喂料系统每喂料一次所述的振动器振动一次,激振频率为50~100hz,振动时长为0.2s以上;plc自动控制上压头向下以及下压头向上位移至其预先设定的预压制前位置,预压制密度为2.3~2.6g/cm3,距离预压制位置5~10
㎜
时,plc自动控制上压头微降和下压头微升到达设定的预压制位置,完成预压制,其中上压头微降速度和下压头微升速度控制在2~5mm/s;
13.(4)、采用所述的充磁系统在所述的阴模处产生脉冲磁场进行充磁取向,与此同时上压头和下压头继续双向压制,直至达到设定的压制成型尺寸值,双向压制的成型位需控制在充磁极头中心线向下的0~20
㎜
内,然后退磁,退磁完成后脱模制得密度在3.9~4.2g/cm3的生坯,所述的压制成型尺寸值为烧结压制收缩率乘以1~3倍的黑片高度尺寸;
14.(5)、将步骤(4)获得的生坯经烧结炉高温液相烧结获得烧结钕铁硼磁体毛坯,烧结钕铁硼磁体毛坯经过机加工方法获得黑片,黑片经酸洗及电镀获得最终的低双面表磁差异的烧结钕铁硼磁体成品。
15.与现有技术相比,本发明的优点在于先依配方完成烧结钕铁硼磁体的配料作业,采用熔炼炉制备获得铸片,将铸片破碎及除杂后送入氢碎炉氢破碎,得到氢碎粉料,对氢碎粉料进行分选,去除粒径尺寸在5μm之下的筛下物和100μm以上的筛上物,得到粒径范围在在5μm~100μm的氢碎粉,向氢碎粉中添加润滑剂混合均匀后进入气流磨设备研磨制粉,得到粒径范围在2.5~5μm的细粉,其中氢碎粉和润滑剂混合时间控制到80分钟以上,润滑剂添加量为氢碎粉重量的0.5
‰
~1.5
‰
,然后细粉中添加润滑剂混合均匀后在温度15~22℃的环境下静置8h以上,其中细粉和润滑剂混合时间控制到200分钟以上,润滑剂添加量为细粉重量的0.5
‰
~2.0
‰
,最后采用100目~200目筛网过筛并装瓶,由此得到粒度一致性较好的预混合粉,且在制备粉料的过程中,分两次添加润滑剂,润滑剂能够均匀包裹和浸润粉料颗粒,且将细粉的内应力充分去除,故细粉流动性有显著改善,为后续生坯成型的喂料均匀性提供充分保障,另外通过对成型模具和压机充磁极头的结构进行改进,通过上压头、下压头、阴模、阴模模腔和4个镶件来构建成型模具,阴模为长方体结构,阴模模腔通过在阴模中部开设上下贯通的长方体形状内腔实现,阴模的材质为非导磁合金或非导磁模具钢,4个镶件的材质为导磁材料纯铁,上压头和下压头材质为非导磁合金或非导磁模具钢,阴模模腔的宽度尺寸为烧结宽度收缩率乘以1~2倍的黑片宽度尺寸减去生坯回弹量,阴模模腔的取向尺寸为烧结取向收缩率乘以1~15倍的黑片取向尺寸减去生坯回弹量,且阴模模腔的取向尺寸控制在20~45mm之间,以保证阴模模腔内磁场均匀度及兼顾生产效率,其中烧结钕铁硼磁体毛坯经切割后的半成品称之为黑片,含机械加工余量,4个镶件嵌入阴模内,将4个镶件分别称为第一镶件、第二镶件、第三镶件和第四镶件,第一镶件和第二镶件左右对称设置在阴模模腔的前侧且相对于阴模模腔沿前后方向的对称平面左右对称,第三镶件和第四镶件左右对称设置在阴模模腔的后侧且相对于阴模模腔沿前后方向的对称平面左右对
称,第一镶件和第三镶件相对于阴模模腔沿左右方向的对称平面前后对称,第二镶件和第四镶件相对于阴模模腔沿左右方向的对称平面前后对称,第一镶件、第二镶件、第三镶件和第四镶件与阴模模腔沿前后方向的对称平面之间的夹角均为45度,每个镶件的宽度尺寸为4~10mm,每个镶件距离阴模模腔宽度工作面的距离为3~5mm;压机包括plc控制系统、压机工作台、模架、上油缸、下油缸、上模冲、下模冲、喂料系统、充磁系统和振动器,模架安装在压机工作台上,上模冲安装在上油缸上,下模冲安装在下油缸上,振动器分别与模架和下模冲连接,充磁系统包含两个线圈、两个极柱以及两个充磁极头,两个线圈一一对应绕制在两个极柱上,两个极柱左右间隔设置,两个充磁极头一一对应固定在两个极柱内侧上,两个充磁极头均为收敛锥体,且左右对称设置,两个充磁极头上沿其中线对称开槽,开槽深度与阴模取向方向壁厚相等,开槽长度比阴模的长度尺寸大0.02~0.05μm;成型模具的上压头安装在压机的上模冲上,成型模具的下压头安装在压机的下模冲上,阴模安装在模架上,阴模卡紧在两个充磁极头的开槽内,第一镶件和第三镶件的外边延长线与位于左侧的充磁极头上的开槽顶点相交,第二镶件和第四镶件的外边延长线与位于右侧的充磁极头上的开槽顶点相交;在成型时,喂料系统每喂料一次振动器振动一次,激振频率为50~100hz,振动时长为0.2s以上;plc自动控制上压头向下以及下压头向上位移至其预先设定的预压制前位置,预压制密度为2.3~2.6g/cm3,距离预压制位置5~10
㎜
时,plc自动控制上压头微降和下压头微升到达设定的预压制位置,完成预压制,其中上压头微降速度和下压头微升速度控制在2~5mm/s;在采用充磁系统在阴模处产生脉冲磁场进行充磁取向时,上压头和下压头继续双向压制,直至达到设定的压制成型尺寸值,双向压制的成型位需控制在充磁极头中心线向下的0~20
㎜
内,然后退磁,退磁完成后脱模制得密度在3.9~4.2g/cm3的生坯,压制成型尺寸值为烧结压制收缩率乘以1~3倍的黑片高度尺寸;其中,喂料系统每喂料一次,振动器工作一次,喂入阴模腔体内的粉料松装密度均匀,上压头微降和下压头微升的特殊预压制工艺控制方法,为后续充磁取向保证生坯密度均匀提供了保障,阴模卡紧在两个充磁极头的开槽内,成型模具和压机之间的装夹配合,使得充磁取向时阴模模腔内磁力线平行分布,解决阴模模腔的边缘磁力线发散的问题,同时阴模模腔特定尺寸的设置,可改善阴模模腔磁场均匀性和减小成型脱模时生坯四周与阴模模腔侧壁的摩擦力,从而达到减小磁体毛坯中边角黑片和中间黑片的表磁差异;通过成型模具结构、压机充磁极头结构、喂料方法及成型方法的改进,使得获得的生坯的各个颗粒的细粉经过充磁取向和压制后,各个颗粒未发生明显位移,生坯密度极其均匀,从而减少后续机械加工黑片工序带来的累积误差,即减小磁体双面表磁差异,由此本发明在显著减小烧结钕铁硼磁体双面表磁差异的同时,能够提高产品合格率和生产效率。
附图说明
16.图1为烧结钕铁硼磁体毛坯尺寸及黑片出片示意图;
17.图2为本发明的减小烧结钕铁硼磁体双面表磁差异的方法中成型模具和压机安装结构示意图;
18.图3为本发明的减小烧结钕铁硼磁体双面表磁差异的方法中成型模具中镶件的示意图。
具体实施方式
19.以下结合附图实施例对本发明作进一步详细描述。
20.实施例:如图1~图3所示,一种减小烧结钕铁硼磁体双面表磁差异的方法,包括以下步骤:
21.(1)、依配方完成烧结钕铁硼磁体的配料作业,采用熔炼炉制备获得铸片,将铸片破碎及除杂后送入氢碎炉氢破碎,得到氢碎粉料,对氢碎粉料进行分选,去除粒径尺寸在5μm之下的筛下物和100μm以上的筛上物,得到粒径范围在5μm~100μm的氢碎粉,向氢碎粉中添加润滑剂混合均匀后进入气流磨设备研磨制粉,得到粒径4
±
0.1μm的细粉,其中氢碎粉和润滑剂混合时间控制到90分钟,润滑剂添加量为氢碎粉重量的0.7
‰
,然后细粉中添加润滑剂混合均匀后在温度20℃的环境下静置9h,其中细粉和润滑剂混合时间控制到240分钟,润滑剂添加量为细粉重量的1.2
‰
,最后采用150目筛网过筛并装瓶,得到预混合粉;
22.(2)、准备成型模具和压机,并将成型模具安装在压机上,具体为:
23.成型模具包括上压头、下压头、阴模1、阴模模腔2和4个镶件,阴模1为长方体结构,阴模模腔2通过在阴模1中部开设上下贯通的长方体形状内腔实现,阴模1的材质为非导磁模具钢,4个镶件的材质为纯铁,上压头和下压头材质为非导磁模具钢,阴模模腔2的宽度尺寸为烧结宽度收缩率乘以1倍的黑片宽度尺寸w减去0.2mm的生坯回弹量,阴模模腔2的取向尺寸为烧结取向收缩率乘以7倍的黑片取向尺寸l减去0.4mm的生坯回弹量,4个镶件嵌入阴模1内,将4个镶件分别称为第一镶件3、第二镶件4、第三镶件5和第四镶件6,第一镶件3和第二镶件4左右对称设置在阴模模腔2的前侧且相对于阴模模腔2沿前后方向的对称平面左右对称,第三镶件5和第四镶件6左右对称设置在阴模模腔2的后侧且相对于阴模模腔2沿前后方向的对称平面左右对称,第一镶件3和第三镶件5相对于阴模模腔2沿左右方向的对称平面前后对称,第二镶件4和第四镶件6相对于阴模模腔2沿左右方向的对称平面前后对称,第一镶件3、第二镶件4、第三镶件5和第四镶件6与阴模模腔2沿前后方向的对称平面之间的夹角e均为45度,每个镶件的宽度尺寸f为6mm,每个镶件距离阴模模腔2宽度工作面的距离g为4mm;
24.压机包括plc控制系统、压机工作台、模架、上油缸、下油缸、上模冲、下模冲、喂料系统、充磁系统、振动器,模架安装在压机工作台上,上模冲安装在上油缸上,下模冲安装在下油缸上,振动器分别与模架、下模冲连接,充磁系统包含两个线圈、两个极柱7以及两个充磁极头8,两个线圈一一对应绕制在两个极柱7上,两个极柱7左右间隔设置,两个充磁极头8一一对应固定在两个极柱内侧上,两个充磁极头8均为收敛锥体,且左右对称设置,两个充磁极头8上沿其中线对称开槽,开槽深度a与阴模1取向方向壁厚b相等,开槽长度c比阴模1的长度尺寸d大0.04μm;
25.成型模具的上压头安装在压机的上模冲上,成型模具的下压头安装在压机的下模冲上,阴模1安装在模架上,阴模1并卡紧在两个充磁极头8的开槽内,第一镶件3和第三镶件5的外边延长线a与位于左侧的充磁极头上的开槽顶点相交,第二镶件4和第四镶件6的外边延长线与位于右侧的充磁极头上的开槽顶点相交;
26.(3)、调整压机,使其上油缸和下油缸位于初始位置,此时上压头和下压头位于预设的初始位置,采用喂料系统自动往复来回多次将步骤(1)获得的预混合粉喂料到阴模模腔2内,同时使用振动器振动阴模1和下压头,具体为:喂料系统每喂料一次振动器振动一
次,激振频率为80hz,振动时长为0.3s;plc自动控制上压头向下以及下压头向上位移至其预先设定的预压制前位置,预压制密度为2.3g/cm3,距离预压制位置5
㎜
时,plc自动控制上压头微降和下压头微升到达设定的预压制位置,完成预压制,其中上压头微降速度和下压头微升速度控制在3mm/s;
27.(4)、采用充磁系统在阴模1处产生脉冲磁场进行充磁取向,与此同时上压头和下压头继续双向压制,直至达到设定的压制成型尺寸值,双向压制的成型位需控制在充磁极头中心线向下的5
㎜
内,然后退磁,退磁完成后脱模制得密度在3.95g/cm3的生坯,压制成型尺寸值为烧结压制收缩率乘以2倍的黑片高度尺寸h;
28.(5)、将步骤(4)获得的生坯经烧结炉高温液相烧结获得烧结钕铁硼磁体毛坯,烧结钕铁硼磁体毛坯经过机加工方法获得黑片,黑片经酸洗及电镀获得最终的低双面表磁差异的烧结钕铁硼磁体成品。
29.采用本实施例的方法制备牌号42m的烧结钕铁硼磁体,其中,黑片宽度尺寸w为54.8mm,黑片高度尺寸h为9mm,黑片取向尺寸l为4mm,生坯尺寸设计为:56.3mm(宽度,对应于宽度方向)
×
20.2mm(高度,对应于压制方向)
×
32.14mm(长度,对应于取向方向),出片方式:1(宽度方向)
×
2(高度方向,对应于压制方向)
×
7(长度方向,对应于取向方向)=14。其中,得到的烧结钕铁硼磁体成品双面中心表磁差异数据见下表1:
30.表1
[0031][0032]
对比例:为验证本发明的减小烧结钕铁硼磁体双面表磁差异的方法的性能,先采用常规工艺制备牌号42m的烧结钕铁硼磁体作为对比例,包括以下步骤:
[0033]
(1)、采用与实施例相同的配方配料,采用与实施例相同的熔炼炉制备获得铸片,送入与实施例相同的氢碎炉氢破碎,得到氢碎粉料,粒径范围在1μm~300μm的氢碎粉,向氢碎粉中添加润滑剂混合均匀后进入气流磨设备研磨制粉,得到粒径4
±
0.1μm的细粉,其中
氢碎粉和润滑剂混合时间控制到40分钟,润滑剂添加量为氢碎粉重量的0.7
‰
,然后细粉中添加润滑剂混合均匀,其中细粉和润滑剂混合时间控制到80分钟,润滑剂添加量为细粉重量的1.2
‰
,最后采用80目筛网过筛并装瓶,得到预混合粉;
[0034]
(2)、准备成型模具和压机,并将成型模具安装在压机上,具体为:对比例成型模具与实例模具相比除少了4个镶件外,其余结构及模具材质均相同;阴模模腔的宽度尺寸为烧结宽度收缩率乘以1倍的黑片宽度尺寸w减去0.2mm的生坯回弹量,阴模模腔的取向尺寸为烧结取向收缩率乘以10倍的黑片取向尺寸l减去0.4mm的生坯回弹量;成型模具的上压头安装在压机的上模冲上,成型模具的下压头安装在压机的下模冲上,阴模安装在压机的模架上,阴模夹紧在两个充磁极头之间并未嵌入极头;
[0035]
(3)、常规工艺方法制备预压密度2.3g/cm3、成型密度3.95g/cm3的生坯,压制成型尺寸值为烧结压制收缩率乘以4倍的黑片高度尺寸h;
[0036]
(4)、将步骤(3)获得的生坯经烧结炉高温液相烧结获得烧结钕铁硼磁体毛坯,烧结钕铁硼磁体毛坯经过机加工方法获得黑片,黑片经酸洗及电镀获得最终的低双面表磁差异的烧结钕铁硼磁体成品,步骤(4)与实施例步骤(5)完全相同。
[0037]
对比例采用与实施例尺寸完全相同的黑片,即宽度尺寸w为54.8mm,黑片高度尺寸h为9mm,黑片取向尺寸l为4mm,生坯尺寸设计为:56.3mm(宽度,对应于宽度方向)
×
39mm(高度,对应于压制方向)
×
45.2mm(长度,对应于取向方向),出片方式:1(宽度方向)
×
4(高度方向)
×
10(长度方向)=40。其中,得到的烧结钕铁硼磁体成品双面中心表磁差异数据见下表2:
[0038]
表2
[0039]
[0040][0041]
分析表1数据可知,本发明的方法制备的磁体成品双面表磁差异的最大值为2.14%,检测黑片100%满足≤5%双面表磁差异的技术要求;分析表2数据可知,现有的方法(对比例)磁体成品双面表磁差异的最大值为6.36%,其中40片黑片中15%的黑片未能满足≤5%双面表磁差异的技术要求,本发明的方法相对于现有的方法(对比例)磁体成品双面表磁差异的最大值6.36%下降了4.22%,改善明显。