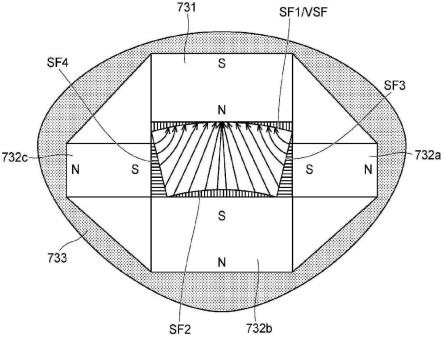
1.本发明涉及极性各向异性磁铁的制造方法、磁铁组件的制造方法、极性各向异性磁铁、磁铁组件及复合磁铁组件。
背景技术:2.众所周知,由所谓的哈尔巴赫阵列构成的磁铁组件能够以高磁通密度产生磁通。然而,想要实现哈尔巴赫阵】列的话,由于需要在产生较大引力和斥力的情况下将强力磁化的磁铁贴合在一起,因此困难重重,目前快来看量产化遥遥无期。
3.作为能够获得与哈尔巴赫阵列相同水平的磁通密度且具有量产化可能性的替代技术,已知有专利文献1的图3中记载的磁铁组件结构(以下简称为专利文献1中记载的磁铁组件)。
4.图30是用于说明专利文献1所记载的磁铁组件900的剖视图。在磁铁组件900内部画出的箭头表示磁化方向。如图30所示,磁铁组件900由呈圆筒形状的位于外周侧的磁铁组件900ex和位于内周侧的磁铁组件900in构成。外周侧的磁铁组件900ex的磁化方向为相对于磁铁组件900ex的法线nl以角度θhex倾斜的极性各向异性排列。角度θhex为超过45度且接近90度的角度,换言之该磁铁铸件的磁化方向是与外周面的切线(省略图示)所构成的角度较浅的“水平系的极性各向异性排列”。另一方面,内周侧的磁铁组件900in的磁化方向是相对于同法线nl以角度θhin倾斜的极性各向异性排列。角度θhin是大于等于0度且小于45度的角度,换言之,该磁铁组件的磁化方向是与内周面的切线(省略图示)所构成的角度较深的“垂直系的极性各向异性排列”。
5.该磁铁组件900是通过分别制造外周侧的磁铁组件900ex(也称为圆筒体900ex)和内周侧的磁铁组件900in(也称为圆筒体900in),并将这些圆筒体彼此嵌合并一体化后获得的。
6.由于外周侧磁铁组件900ex及内周侧的磁铁组件900in的制造方法基本相同,因此这里以制造外周侧的圆筒体900ex为代表进行说明。图31是用于说明磁铁组件900ex的以往制造方法的图。图31中的(1)表示磁场成型工序中使用的模框810及磁力源820s、820n;(2)表示磁铁母材m1;(3)表示磁化工序的情况;(4)表示在结束磁化工序后取出的磁铁组件900ex。
7.以往的磁铁组件的制造方法大致如下。
8.首先,准备磁铁用的粉末材料、模框810等。模框810的内侧为依照最终的磁铁组件900ex的形状的圆筒状。
9.接着,进行磁场成型工序。在向模框810的内侧810a投入粉末材料后,使用磁力源820s、820n从模框810的外侧施加规定的磁场,使粉末材料中的各分子在沿磁力线取向的同时进行成型(参照图31的(1))。通过这样获得磁铁母材m1(参照图31的(2))。之后,在经过必要的中间工序(烧结热处理工序、表面处理工序等)后,进行使用磁力源830s、830n(磁化磁
轭等)施加规定磁场的磁化工序(参照图31的(3))。通过这样,就可以获得磁铁组件900ex(参照图31的(4))。
10.【先行技术文献】
11.专利文献1:日本特开2010-142082号公报
12.然而,根据以往的磁铁组件的制造方法,如下所述,存在因成本高和量产率低(例如成品率低)而无法提高经济性的问题,以及在设计上制约多的问题。
13.举个例子,在磁场成型工序中使用的模框810,由于每当产品的规格改变时都必须重新准备依照最终的磁铁组件的形状的模框,因此模框费导致整体成本就不可避免地变高(即模框成本问题)。
14.在将外周侧的磁铁组件900ex的径向的壁厚以小尺寸设计得较薄的情况下,在进行了磁场成型工序之后进行烧结热处理工序时有时会产生破损,因而会降低成品率(即损耗问题)。
15.为了将上述损耗防范于未然,不得不将将外周侧的磁铁组件900ex的厚度尺寸设计成比能够发挥出规定性能的厚度尺寸更加厚的尺寸(不得不增加设计余量),相应地,内径侧的磁铁组件900in的径向的壁厚的设计余量就会被挤压,其就导致有时无法如预期那样获得水平系的极性各向异性排列的厚度与垂直系的径向各向异性排列的厚度之间的比例,从而无法获得预期的磁力特性。
16.在通过机型变更等要改变磁铁组件的径向厚度和外径等尺寸上的参数时,也会导致成品率降低、无法确保必要的磁特性等不良情况。
17.如图32(a)所示,在设计为能够充分确保磁铁组件径向厚度时(参照厚度t1),在磁力线被释放到外部的附近,可以相对于外周面以相应的角度确保进行磁场成型工序后的粉末的取向方向(可以设为比较接近法线nl的角度),粉末的取向方向在进行磁化工序后变为磁化方向,因此最终可以成型为具有目标磁性能的极各向异性的磁铁组件。但是,如图32(b)所示,在进行必须减薄径向厚度的设计时(参照厚度t2),只能以相对于外周面浅的角度确保粉末的取向方向(相对于法线nl呈大致接近90度的角度),其结果就导致无法以期望的强度向外部放射磁力线,最终无法确保产品所需的磁特性。
18.也就是说,如果优先使磁铁组件的厚度变薄,则会剥夺取向方向(磁化方向)的设计自由度,而如果优先取向方向(磁化方向),则会剥夺磁铁组件的厚度设计自由度。
19.而且,以往为了获得构成外周侧磁铁组件的一部分的极性各向异性磁铁(例如图30的虚线c包围的部分的极性各向异性磁铁),批量生产上的课题也很多。
20.当需要在磁化的状态下进行组装时,在大致水平的方向上磁化后的磁铁905及磁铁906彼此以相同的磁极的面对接,并在相互产生大的斥力的情况下接合,因此难以进行批量生产(虚线d内的磁铁907、908的极性各向异性也是一样)
21.顺便说一下,如果是成为磁铁905或磁铁906之前的磁化前的各次的母材“假设为母材905’、906’(省略图示)”,则母材905’和母材906’之间不会产生斥力,因此容易接合,但考虑到还未确立之后磁化工序中的磁化方法,因此会导致难以批量生产图30中虚线d、c所示的极各向异性磁铁。
22.因此,本发明是鉴于上述情况而完成的,目的在于提供一种设计自由度比以往高且经济性高的极性各向异性磁铁的制造方法及磁铁组件的制造方法。本发明的目的还在于
提供一种极性各向异性磁铁、磁铁组件及复合磁铁组件。
技术实现要素:23.【1】本发明涉及的极性各向异性磁铁的制造方法,用于制造剖视时具有分别面向四个方向的四个面,其特征在于,依次包含:粉末材料准备工序,用于准备磁铁用的粉末材料;磁场成型工序,在将所述四个面中应当集中产生磁通的面设为实效面时,从与该极性各向异性磁铁的所期望的形状相对应的模框的外侧,一边对假想的所述实效面施加第一方向的磁场,一边对其余的三个面分别施加第二方向的磁场,一边将所述粉末材料依次投入所述模框的内侧,成型为依照所述模框形状的磁铁母材;以及四方磁化工序,以包围基于所述磁铁母材获得的磁铁材料的方式,对该磁铁材料的所述实效面施加第一方向的磁场,以及对所述其余的三个面施加第二方向的磁场从而对所述磁铁材料进行磁化。
24.【6】本发明涉及的极性各向异性磁铁,具有剖视时分别面向四个方向的四个面,其特征在于:在将所述四个面中应当集中产生磁通的面设为实效面时,在所述实效面配置有一个磁极,在所述四个面中除所述实效面以外的其余三个面分别配置有另一个磁极,剖视时,所述极性各向异性磁铁的内部是在无接合痕的情况下连续形成的。
25.【8】本发明涉及的磁铁组件,其特征在于,包括:多个上述极性各向异性磁铁,通过以所述一个磁极以及所述另一个磁极交替出现的方式排列所述极性各向异性磁铁后将其相互接合来构成所述磁铁组件。
26.【13】本发明涉及的磁铁组件的制造方法,用于制造筒状的磁铁组件,其特征在于,依次包含:粉末材料准备工序,准备磁铁用的粉末材料;磁场成型工序,用于成型具有第一主面以及位于所述第一主面相反侧的第二主面的磁铁母材,在磁场成型工序中,向与所述磁铁母材的形状相对应的模框的内侧投入所述粉末材料,并从所述模框的外侧的与所述第一主面相对应的一侧向与所述第二主面相对应的一侧施加单一方向的平行磁场来成型所述磁铁母材;切割工序,在组装成磁铁组件时,在将应当成为该磁铁组件的外径面的面定义为“规定外径面”,并将应当成为内径面的面定义为“规定内径面”时,将所述规定外径面的切割线设定为相对于所述第一主面倾斜角度θ1后沿所述规定外径面的切割线切割所述磁铁母材,并且将所述规定内径面的切割线设定为相对于所述第一主面倾斜角度θ2后沿所述规定内径面的切割线切割所述磁铁母材,从而至少切割出以所述规定外径面和所述规定内径面为外表面的磁铁母材件;组装工序,将多个所述磁铁母材件相互组合后组装成磁铁母材组件;以及磁化工序,从所述磁铁母材组件的外部向规定位置施加规定的磁场来磁化所述磁铁母材组件。
27.【22】本发明的磁铁组件,其特征在于,包括:磁铁块,具有大致平面的外径面和内径面,并相对于该外径面和内径面以规定的角度且沿单一方向平行地被磁化,多个所述磁铁块经由所述外径面和所述内径面以外的面相互接合而成。
28.【23】本发明涉及的复合磁铁组件,其特征在于,包括:根据权利要求8所述的第一形态的磁铁组件,各所述磁铁块的相对于所述外径面和所述内径面的磁化方向的角度为第一角度;以及根据权利要求8所述的第二形态的磁铁组件,各所述磁铁块的相对于所述外径面和所述内径面的磁化方向的角度为第二角度,其中,所述第一形态的磁铁组件配置在应当成为该复合磁铁组件的有效h磁通面的一侧,所述第二形态的磁铁组件配置在应当成为
该复合磁铁组件的有效v磁通面的一侧,所述第一形态的磁铁组件与所述第二形态的磁铁组件相互接合后构成所述复合磁铁组件。
29.【21】本发明涉及的另一形态的极性各向异性磁铁的制造方法,用于制造剖面视时具有四个面的极性各向异性磁铁,其特征在于,依次包含:粉末材料准备工序,用于准备磁铁用的粉末材料;磁场成型工序,用于成型具有第一主面和位于所述第一主面相反侧的第二主面的磁铁母材,向与所述磁铁母材的形状相对应的模框的内侧投入所述粉末材料,并从所述模框的外侧的与所述第一主面相对应的一侧向与所述第二主面相对应的一侧施加单一方向的平行磁场来成型所述磁铁母材;切割工序,在将该极性各向异性磁铁组装成磁铁组件时,在将应当成为该磁铁组件的外径面的面定义为“规定外径面”,并将应当成为内径面的面定义为“规定内径面”时,将所述规定外径面的切割线设定为相对于所述第一主面倾斜角度θ1后沿所述规定外径面的切割线切割所述磁铁母材,并且将所述规定内径面的切割线设定为相对于所述第一主面倾斜角度θ2后沿所述规定内径面的切割线切割所述磁铁母材,从而至少切割出以所述规定外径面和所述规定内径面为外表面的磁铁母材件;子组装工序,通过组合至少四个所述磁铁母材件来组装具有四个面的磁铁母材子组件,在将所述四个面中应当集中产生磁通的面设为实效面时,在成为所述磁铁母材子组件的所述实效面的一侧,配置在所述切割工序中以所述角度θ1及所述角度θ2分别在超过45度且小于90度的范围内的设定进行切割后的水平系的所述磁铁母材件,并在成为所述实效面的一侧的相反侧,配置在所述切割工序中以所述角度θ1及所述角度θ2分别在大于等于0度且小于45度的范围内的设定进行切割后的垂直系的所述磁铁母材件来组装所述磁铁母材子组件;以及四方磁化工序,以包围所述磁铁母材子组件的方式,对该磁铁母材子组件的所述实效面施加第一方向的磁场;以及对其余的三个面施加第二方向的磁场来磁化所述磁铁母材子组件。
30.发明效果
31.本发明的上述结构是一种设计自由度比以往高且经济性高的极性各向异性磁铁的制造方法及磁铁组件的制造方法。
附图说明
32.图1是用于说明磁铁组件100的一例剖视图。
33.图2是展示在磁化并成为极性各向异性磁铁1n、1s之前的预磁化材料5的情况的剖视图。
34.图3是用于说明极性各向异性磁铁1n、1s的一例示例图。
35.图4是用于说明极性各向异性磁铁1n、1s另一例示例图。
36.图5是用于说明实施方式一涉及的磁极性各向异性磁铁的制造方法的流程图。
37.图6是展示实施磁场成型工序s20时情况的示意性剖视图。
38.图7是在实施了磁场成型工序s20后取出的磁铁母材m1的示意图。
39.图8是实施了加工工序s32后取出的磁铁材料m2的示意图。
40.图9是实施了表面处理工序s33后取出的磁铁材料m2’的示意图。
41.图10是展示实施四方磁化工序s40时的情况的示意性剖视图。
42.图11是用于说明实施方式一涉及磁铁组件100的图。
43.图12是用于说明应用例涉及的电机510、发电机520及致动器530的图。
44.图13是用于说明四方磁化工序s40的实施方法的变形例的图。
45.图14是用于说明变形例涉及的磁铁组件110、120的图。
46.图15是展示变形例涉及的圆筒状的双层结构的磁铁单元400的图。
47.图16是变形例涉及的直线状的双层结构的磁铁单元420的图。
48.图17是用于说明实施方式二涉及的磁铁组件的制造方法的流程图。
49.图18是用于说明磁场成型工序ss20的图。
50.图19是用于说明切割工序ss40的图。
51.图20是用于说明组装工序ss60的图。
52.图21是用于说明磁化工序ss70的图。
53.图22是用于说明实施方式三涉及的切割工序ss40的剖视图。
54.图23是用于说明实施方式三涉及的组装工序ss60的剖视图。
55.图24是实施了实施方式三涉及的磁化工序ss70后的磁铁组件100in的剖视图。
56.图25是用于说明实施方式五涉及的磁铁组件的制造方法及极性各向异性磁铁的制造方法的流程图。
57.图26是用于说明子组装工序ss80的图。
58.图27是用于说明四方磁化工序ss85的图。
59.图28是用于说明应用例的变形例涉及的直线电机结构体550的示意图。
60.图29的是用于说明直线电机结构体550详细情况的图。
61.图30是用于说明专利文献1所记载的磁铁组件900的剖视图。
62.图31是用于说明磁铁组件900ex的以往的制造方法的图。
63.图32是展示基于以往的制造方法的磁场成型工序中粉末材料的取向方向的示意图。
具体实施方式
64.以下,参照附图说明本发明涉及的极性各向异性磁铁的制造方法、磁铁组件的制造方法、极性各向异性磁铁、磁铁组件及复合磁铁组件的各实施方式。各附图仅为示例,并不一定严格反映实际的尺寸、比例等。在图17~图32中,在磁铁母材10、磁铁母材件20、30等的内部描绘的虚线或实线表示分子的取向方向(易磁化轴),在磁铁组件或极性各向异性磁铁的内部描绘的带箭头的实线表示磁化方向。
65.a.基于四方磁化的极性各向异性磁铁的制造方法
66.首先,公开构成磁铁组件的要素即极性各向异性磁铁的基于四方磁化的制造方法。
67.【实施方式一】
68.1.极性各向异性磁铁1n、1s及磁铁组件100
69.在说明极性各向异性磁铁的制造方法之前,先说明需要制造的极性各向异性磁铁1n、1s及磁铁组件100(有时称为复合磁铁组件)的一例。
70.(1)磁铁组件100
71.图1是用于说明磁铁组件100的示例剖视图。在图1中,极性各向异性磁铁1n、1s内
部的箭头b表示磁化方向。图1所示的磁铁组件100能够发挥与专利文献1的图3中记载的磁铁组件900大致相同的磁性能。在实施方式一涉及的极性各向异性磁铁的制造方法中,被图1中的虚线包围的单位来制造极性各向异性磁铁1n、1s。
72.(2)基于直线分子取向(易磁化轴)的预磁化材料5
73.图2是与图1中的虚线包围的1个单位相对应的部分的图,其是展示磁化并极性各向异性磁铁1n、1s之前的预磁化材料5的情况的剖视图。在预磁化材料5的内侧描绘的粗实线表示分子取向(易磁化轴)。
74.如图2所示,将预磁化材料5的内部分为四个区域时,在各区域内为直线且相互平行的分子取向(易磁化轴)。此处,设外径侧区域的分子取向(易磁化轴)与预磁化材料5的外周面的中央部分的切线tl之间的角为θout,设内径侧的区域的分子取向(易磁化轴)与预磁化材料5的外周面的中央部分的法线nl之间的角为θin。
75.作为实施例之一,也可以在预磁化材料5的内径侧配置分割环形状的软磁性体6。此时,通过将θin设定为超过0度的值,可以使软磁铁6的厚度变薄。通过适当改变θout的值,可以改变从表示为法线nl的位置即外周面的中央部分输出的磁力线的磁通密度形状。
76.通过以适当的方法磁化与图2所示的方法对应的预磁化材料5,可以构成如图3所示的磁极性各向异性磁铁1n和1s。
77.(3)直线磁化方向的极性各向异性磁铁1n、1s
78.图3是用于说明极性各向异性磁铁1n、1s示例图。其中,图3(a)及图3(b)分别展示时了极性各向异性磁铁1n及1s。在图3中,在极性各向异性磁铁1n、1s内部的箭头b表示磁化方向。
79.如图3(a)所示,极性各向异性磁铁1n在剖视时具有四个面sf1、sf2、sf3、sf4。这四个面sf1、sf2、sf3、sf4分别面向4个方向(粗箭头)。
80.这里的“四个面”是指大致四个面。各个面在剖视时的轮廓可以是直线状也可以是曲线状。多条直线或曲线也可以部分弯折。例如在90度以内弯折且连续的直线或曲线也作为这里所说的大致一个面来处理。
81.图2及图3所示的形状是应当制造的“极性各向异性磁铁的期望形状”。“极性各向异性磁铁的期望形状”是所谓的圆弧形,其示例呈在剖视时将圆环n等分的分割环形状(n为大于等于2的自然数)。在极性各向异性磁铁1n、1s例如为圆筒形转子来应用的情况下,第一面sf1为外周面,第二面sf2为内周面。
82.在此,将四个面中应当集中产生磁通的面定义为“实效面vsf”。在实施方式一涉及的极性各向异性磁铁1n、1s中,从实效面vsf(第一面sf1)的中央附近向外侧集中产生磁通。
83.当该极性各向异性磁铁例如用作电机等电力机械的转子时,该实效面vsf位于与定子相向配置的一侧。在实效面vsf设定在外周面侧(第一面sf1)的情况下,该极性各向异性磁铁可以适合用作内转子。在实效面vsf被设定在内周面侧(第二面sf2)的情况下,该极性各向异性磁铁适合作为外转子使用。
84.在图3(a)所示的极性各向异性磁铁1n中,第一面sf1成为实效面vsf。在实效面vsf(第一面sf1)配置有n极(一个磁极),在实效面vsf以外的其余的第二面sf2、第三面sf3及第四面sf4配置有s极(另一个磁极)。图3(b)所示的极性各向异性磁铁1s被磁化为与极性各向异性磁铁1n相反的方向,在实效面vsf(第一面sf1)配置有s极(一个磁极),在实效面vsf以
外的其余的第二面sf2、第三面sf3及第四面sf4配置有n极(另一个磁极)。
85.图3所示极性各向异性磁铁1n、1s为本实施方式一的对象。
86.(4)基于曲线磁化方向的其他极性各向异性磁铁1n、1s
87.图4是用于说明极性各向异性磁铁1n、1s另一例图。图3中显示的是基于直线磁化方向的极性各向异性磁铁1n,1s。作为构成与图3所示的极性各向异性磁铁1n、1s类似且能够发挥与其大致同等的磁特性的磁铁,也可以考虑图4所示的在追踪内部的磁化方向时为曲线的其他极性各向异性磁铁1n、1s。其他极性各向异性磁铁1n、1s也为本实施方式一的对象。图4所示其他极性各向异性磁铁1n、1s涉及的四个面(sf1、sf2、sf3、sf4)、实效面vsf等的说明引用了上述图3所示的极性各向异性磁铁1n、1s的说明。
88.关于极性各向异性磁铁1n、1s及磁铁组件100的详细说明将在后面叙述。
89.2.实施方式一涉及的极性各向异性磁铁的制造方法
90.图5是用于说明实施方式一涉及的磁极性各向异性磁铁的制造方法的流程图。图6是展示实施磁场成型工序s20情况的示意性剖视图。图7是在实施了磁场成型工序s20后取出的磁铁母材m1的示意图。图8是实施了加工工序s32后取出的磁铁材料m2的示意图。图8中的双点划线表示的是磁铁母材m1的外形形状的轮廓。图9是实施了表面处理工序s33后取出的磁铁材料m2’的示意图。图10是展示实施四方磁化工序s40时的情况的示意性剖视图。
91.如图5所示,实施方式一涉及的极性各向异性磁铁的制造方法至少依次包含:粉末材料准备工序s10、磁场成型工序s20、以及四方磁化工序s40。在实施方式一中,在磁场成型工序s20与四方磁化工序s40之间还进一步包含中间工序s30(例如烧结热处理工序s31)。
92.(1)粉末材料准备工序s10
93.粉末材料准备工序s10是用于准备磁铁用粉末材料pd的工序。磁铁用粉末材料的准备可以采用以往的一般方法。例如,如假设采用钕磁铁,可以在溶解钕、铁、硼等原料后进行固体化,并使用粉碎机、研磨机等对固体材料进行粗粉碎和微粉碎后准备磁铁用的粉末材料pd。
94.(2)磁场成型工序s20
95.在磁场成型工序s20中,一边从与极性各向异性磁铁的期望形状对应的模框710的外侧,向假想的实效面vsf’(因为还没有形成极性各向异性磁铁的原型,因此使用假想一词)施加第一方向的磁场,一边对其余的三个面分别施加第二方向的磁场,同时将粉末材料pd依次投入模框710的内侧,成形依照模框710形状的磁铁母材m1(参照图5及图6)。
96.作为具体的结构,如图6所示,准备与“极性各向异性磁铁的期望的形状”对应的模框710,在该模框710的外侧,以第一磁极与假想的实效面vsf’相向的方式配置第一磁力源721,并且,以第二磁极与四个面中除假想的实效面以外的其余三个面(在图中为下表面、右侧面、左侧面)的各自相向的方式分别配置第二磁力源722b、722a、722c。在图6中,展示了第一磁极为n极,第二磁极为s极的例子。
97.在这样的配置下,一边通过第一磁力源721对假想的实效面vsf’施加第一方向的磁场,一边通过第二磁力源722对其余的三个面分别施加第二方向的磁场,同时将粉末材料pd依次投入模框710的内侧,成型依照模框710形状的磁铁母材m1。
98.在将粉末材料pd投入模框710之前预先混合粘合剂(粘合剂)。当向施加有规定磁场的模框710的内侧投入粉末材料pd时,粉末材料pd的各分子的方向与磁场的方向一致,并
且该粉末被层叠。此时从模框710外部进行加压。
99.通过这样实施磁场成型工序s20,可以获得如图7所示的磁铁母材m1。图7所示的磁铁母材m1中的实线表示分子的排列方向(分子的取向)。
100.第一磁力源721及第二磁力源722的宽度、第一磁力源721的第一磁极(峰值部分)及第二磁力源722的第二磁极(峰值部分)相对于模框框710的配置位置可以根据设计意图适当变更。关于各面的第一磁力源721、第二磁力源722的输出(施加的磁场的强度),也可以根据设计意图设为适当的大小(磁场的强度)。此时,分子的排列方向(分子取向/易磁化轴/磁铁排列)可以通过调整第二磁力源722b、722a、722c的各磁力线强度而轻易地进行适当改变。并且,从极性各向异性磁铁1n、1s的实效面vsf输出的磁力线的磁通密度形式也可以适当地进行设计变更。
101.这里,“第一方向”、“第二方向”是指朝向模框710内侧或外侧的方向,第一方向及第二方向相反。在图6的例子中,“第一方向”是磁力线从第一磁力源721的第一磁极朝向模框710的内侧的方向,“第二方向”是磁力线从模框710的内侧朝向第二磁力源722的第二磁极的方向。“第一方向”、“第二方向”不限于上述那样相相对于模框710的方向,也可以被定义为相对于磁铁材料m2、m2’的方向。
102.通过使内周面sf2与第一磁力源721相向,并使外周面sf1与第二磁力源722b相向配置,也能够制作在内周面sf2具有实效面vsf的极性各向异性磁铁。这样的变形也应用于后述的四方磁化工序s40(图10等)。
103.(3)中间工序s30
104.中间工序s30是用于将在磁场成型工序s20中获得的磁铁母材m1投入到后述的四方磁化工序s40中而进行的中间处理工序(参照图5)。
105.在实施方式一中,进行对通过磁场成型工序s20获得的磁铁母材m1(参照图7)进行烧结热处理的烧结热处理工序s31。当进行烧结热处理工序s31时,磁铁母材m1中所含的粘合剂(粘合剂)因热量而气化并飞溅,磁性体的材料的纯度提高。在进行了磁场成型后,虽然也有在磁铁母材m1的内部稍微磁化的情况,但可以通过进行烧结热处理工序s31来消磁。
106.在实施方式一中,紧接着烧结热处理工序s31进行将经过烧结热处理后的磁铁母材m1加工成“极性各向异性磁铁的期望的形状”并形成磁铁材料m2的加工工序s32(参照图8)。然后,进行对磁铁材料m2实施用于防锈的表面处理(例如镀镍、光泽铬酸盐处理、电泳涂装等)从而形成磁铁材料m2’的表面处理工序s33(参照图9,图中的符号7表示表面处理层),最后进行检查磁铁材料m2’的成品状态的检查工序s34。
107.在模框710的内侧形状为“极性各向异性磁铁的期望的形状”的情况下,有时可以不进行加工工序s32或不进行表面处理工序s33。
108.(4)四方磁化工序s40
109.四方磁化工序s40以包围基于磁铁母材获得的磁铁材料m2、m2’的方式,对该磁铁材料m2、m2’的实效面vsf(sf1)施加第一方向的磁场,以及对其余的三个面(sf2、sf3、sf4)施加第二方向的磁场来磁化磁铁材料m2、m2’(参照图5及图10)。
110.作为具体的结构,如图10所示,首先,以包围基于磁铁母材m1获得的磁铁材料m2、m2’的方式,以第一磁极与实效面vsf(第一面sf1)相向的方式配置磁化用第一磁力源731,并且以第二磁极与其余三个面(第二面sf2、第三面sf3、第四面sf4)分别相向的方式分别配
置磁化用第二磁力源732b、732a、732c。作为磁化用第一磁力源731以及磁化用第二磁力源732b、732a、732c可以采用所被称为磁化磁轭的部件。
111.然后,使磁化用第一磁力源731及磁化用第二磁力源732a、732b、732c工作,对实效面vsf(第一面sf1)施加第一方向的磁场,以及对其余的三个面(第二面sf2、第三面sf3、第四面sf3)施加第二方向的磁场来磁化磁铁材料m2。
112.关于电场的施加方法,可以适当采用以往的方法。关于第一磁极、第二磁极、第一方向及第二方向的说明引用磁场成型工序s20中的说明。
113.通过这样实施四方磁化工序s40,就能够获得图2或图3所示的极性各向异性磁铁1n或2n。
114.此外,磁化用第一磁力源731和磁化用第二磁力源732的宽度、磁化用第一磁力源731的第一磁极(峰值部分)和磁化用第二磁力源732的第二磁极(峰值部分)的配置位置可以根据设计意图适当变更。关于各面的磁化用第一磁力源731、磁化用第二磁力源732的输出(施加的磁场的强度),也能够根据设计意图设为适当的大小(磁场的强度)。
115.通过适当地进行这样的调整,能够任意地设定完成极性各向异性磁铁1n、1s时成为水平系的极性各向异性排列的部分的厚度以及成为垂直系的径向各向异性排列的部分的厚度,还能够适当地变更表示磁化方向的假想线的密度。
116.在以上的说明以及与说明对应的附图中,作为一例,例举了制造极性各向异性磁铁1n的例子,当制造极性各向异性磁铁1s的情况下,在将第一磁极作为s极,将第二磁极作为n极调换极性的基础上,通过使第一方向和第二方向的方向相互转换,也能够实施与上述同样的工序。
117.3.实施方式一涉及的极性各向异性磁铁1n、1s
118.接着,返回图4,对通过上述极性各向异性磁铁的制造方法获得的极性各向异性磁铁1n、1s的结构进行补充说明。
119.极性各向异性磁铁1n、1s具有在剖视时分别面向四个方向(粗箭头)的四个面(第一面sf1、第二面sf2、第三面sf3、第四面sf4)。在将极性各向异性磁铁1n、1s的四个面sf1、sf2、sf3、sf4中的应当集中产生磁通的面设为实效面vsf(sf1)时,在实效面vsf(sf1)配置一个磁极,在四个面中除实效面vsf以外的其余三个面分别配置另一个磁极。当一个磁极为n极时,另一个磁极为s极。相反,当一个磁极为s极时,另一个磁极为n极。
120.实施方式一中例举的极性各向异性磁铁1n、1s在剖视时呈将圆环n等分的分割环形状(n为大于等于2的自然数)。此时,在磁极性各向异性磁铁1n、1s例如作为圆筒形转子应用的情况下,第一面sf1为外周面,第二面sf2为内周面。
121.如图2和图3所示,例如从第三面sf3的上侧附近到第一面sf1的靠中央附近的部分为比较接近水平的磁化方向,因此可以说是水平系的极性各向异性排列。例如第三面sf3下侧附近和接近第二面sf2的附近的部分为比较接近垂直的磁化方向,因此可以说为垂直系的径向各向异性排列。
122.对极性各向异性磁铁1n、1s进行剖面观察时,其内部没有粘接痕迹,并且其内部是连续形成的,因此极性各向异性磁铁1n、1s为连续的个体构件。
123.4.实施方式一涉及的极性各向异性磁铁的制造方法、极性各向异性磁铁及磁铁组件的效果
124.在实施方式一涉及的极性各向异性磁铁的制造方法中,以第一磁极与实效面vsf(也包含假想的实效面vsf’)(sf1)相向的方式配置磁力源(第一磁力源721或磁化用第一磁力源731),并且,以第二磁极与除有效面vsf(sf1)以外的其余三面sf2、sf3、sf4相向的方式配置磁力源(第二磁力源722或磁化用第二磁力源732),并在此基础上对实效面vsf施加第一方向的磁场,以及对其余三个面施加第二方向的磁场。
125.因此,实施方式一涉及的极性各向异性磁铁的制造方法能够一并制造在内部同时具有水平系的极性各向异性排列的部分和垂直系的径向各向异性排列的部分的极性各向异性磁铁1n、1s,其与哈尔巴赫排列的磁铁组件以及与其类似的磁铁组件等的以往的制造方法相比,能够大幅提升量产效率。
126.通过适当变更对各自四个面sf1、sf2、sf3、sf4配置的磁力源(第一磁力源721、第二磁力源722、磁化用第一磁力源731、磁化用第二磁力源732)的位置、各磁力源的输出(施加的磁场的强度),就能够适当变更水平系的极性各向异性排列的部分的厚度及垂直系的极性各向异性排列的部分的厚度。即,不会受到如专利文献1所记载的磁铁组件900的制造方法那样需要在外周侧的圆筒体900ex的径向壁厚与内周侧的圆筒体900in的壁厚之间进行权衡的设计制约。
127.根据实施方式一涉及的极性各向异性磁铁的制造方法,能够提高批量生产性,还能够提高水平系的极性各向异性排列的厚度以及垂直系的径向各向异性排列的厚度的设计自由度。也就是说,是一种设计自由度比以往高且经济性高的极性各向异性磁铁的制造方法。
128.尽管为了获得实施方式一涉及的磁铁组件100需要接合了磁化方向相互不同的极性各向异性磁铁1n、1s,但在这种情况下,例如出现在极性各向异性磁铁1n的第一面sf1上的s极和出现在极性各向异性磁铁1s的第四面sf4上的n极相互吸引,因此能够很容易地将多个极性各向异性磁铁进行排列、接合。这也有助于提升量产效率。
129.5.实施方式一涉及的磁铁组件100
130.图11是用于说明实施方式一涉及的磁铁组件100的图。其中,图11(a)是磁铁组件100的剖视图,图11(b)是磁铁组件100的立体图。
131.如图11所示,磁铁组件100以一个磁极及另一个磁极交替出现在外部的方式排列极性各向异性磁铁并相互接合的结构。具体而言,磁铁组件100的结构为:磁极性各向异性磁铁1n和磁极性各向异性磁铁1s沿着规定的方向交替地依次排列,且相互邻接的两个磁极性各向异性磁铁被磁化为相互相反的方向。
132.换言之,磁铁组件100通过磁极性各向异性磁铁1n、1s沿着以轴ax为中心周方向排列而成,其外形为大致圆筒状。
133.这里,将圆环8等分(n=8)后呈分割环形状的极性各向异性磁铁1n和极性各向异性磁铁1s以在彼此的第三面sf3和第四面sf4相接的方式相互接合粘接,彼此的第一面sf1(实效面vsf)处于同一平面上(即接合部处不存在落差)。
134.【应用例】
135.图12是用于说明作为各实施方式涉及的极性各向异性磁铁及磁铁组件的应用例的电机510、发电机520及致动器530的图。实施方式一中获得的极性各向异性磁铁1n、1s以及使用它们构成的磁铁组件100能够应用于各种产品领域。例如,能够构成:具有包含磁铁
组件100的转子的电机(参照图12(a));具有包含磁铁组件100的转子的发电机(参照图12(b))、具有包含磁铁组件100的转子的致动器(图12(c))等。
136.以上,基于上述实施方式一对本发明进行了说明,但本发明并不限定于上述实施方式一中的形态。在不脱离构思的范围内能够以多种方式实施,例如还能够进行以下变形。
137.(1)在实施方式一的磁场成型工序s20和/或四方磁化工序s40中,第一磁力源721或磁化用第一磁力源731中配置有第一磁极的一侧的宽度与实效面vsf(包括假想的实效面)的宽度大致相等,但本发明不限于此。
138.图13是用于说明四方磁化工序s40的实施方法的变形例的图。例如图13所示,在四方磁化工序s40中,磁化用第一磁力源731的配置有第一磁极的一侧的宽度w1也可以设定为小于实效面vsf的宽度w2。换言之,与实效面vsf相对的磁化用第一磁力源731的磁场施加面可以设定为仅与实效面vsf的一部分重叠(overlap)。
139.通过这样,就能够调整在实效面vsf外部产生的磁通密度分布的疏密程度及磁力线的强弱。
140.虽然在图13及上述说明中提到了四方磁化工序s40的实施方法的变形例,但在磁场成型工序s20中也可以进行同样的处理。即,在磁场成型工序s20中,第一磁力源721的配置有第一磁极的一侧的宽度可以设定为比假想的实效面vsf’的宽度小。
141.(2)在实施方式一涉及的极性各向异性磁铁的制造方法中,说明了作为圆筒状的磁铁组件100的一部分的分割环形状的极性各向异性磁铁,并说明了在将它们组合而制成磁铁组件100时,能够在圆筒外周的外侧产生高密度磁通的极性各向异性磁铁的制造方法。但是,本发明不限于此。例如,在磁场成型工序s20及四方磁化工序s40中,也可以将第二面sf2设定为实效面vsf,并将作为除该实效面vsf以外的其余的三个面设为为第一面sf1、第三面sf3、第四面sf4,同时通过变更各磁力源磁化用磁力源极性及应施加的磁场的设定以使分子的排列方向的线或磁化方向的线集中在圆弧状的极各向异性磁铁的内周侧,从而在圆筒内周的内侧制造可产生高磁通的极各向异性磁铁。这种极性各向异性磁铁例如可以适合用作外转子。
142.(3)虽然实施方式一涉及的磁铁组件100呈大致圆筒状,但本发明并不限定于此。例如,如图14(a)所示,也可以设为直线型磁铁组件110、圆弧型的磁铁组件120。图14是用于说明变形例磁铁组件110、120的图。
143.(4)虽然实施方式一涉及的极性各向异性磁铁的制造方法、极性各向异性磁铁1n、1s以及磁铁组件100与专利文献1的图3所记载的磁铁组件900相对应,但是本发明并不限定于此。例如,实施方式一的极性各向异性磁铁的制造方法也能够应用于基于哈尔巴赫排列的磁铁组件、或应用于基于哈尔巴赫排列的磁铁组件的极性各向异性磁铁。
144.(5)本发明所涉及的极性各向异性磁铁的制造方法及极性各向异性磁铁1n、1s也可以应用于基于对面磁场的双层结构的磁铁单元。
145.图15是呈圆筒状双层结构的磁铁单元400的图。圆筒状的双重结构的磁铁单元400具备外周侧的磁铁组件400ex和内周侧的磁铁组件400in。构成磁铁组件400ex,400in的极性各向异性磁铁1n、1n’、1s、1s’也可以通过本发明的极性各向异性磁铁的制造方法获得,可以将本发明的极性各向异性磁铁1n、1n’、1s、1s’适用于磁铁组件400ex,400i。
146.图16是表示呈线性的双层结构的磁铁单元420的图。线性双层结构的磁铁单元420
包括:上侧(为了便于说明,使用“上”、“下”来区别)的磁铁组件420u、下侧的磁铁组件420l、以及配置在它们之间的磁铁组件430。构成磁铁组件420u、420l的极性各向异性磁铁2n、2n’、2s、2s’也可以通过本发明的极性各向异性磁铁的制造方法获得,也可以将本发明的极性各向异性磁铁2n、2n’、2s、2s’应用于磁铁组件420u、420l。
147.(6)在实施方式一和变形例中,说明了剖面视图中具有四个边(四个面)的极性各向异性磁铁,但本发明并不限定于此。例如实施方式一不限于四个面,也可以应用于具有三个面或五个及以上个面的形状的极性各向异性磁铁。例如,在剖面视图中具有三角形三个面的磁铁母材m1磁铁材料m2、剖面视图中具有六边形的六个面的磁铁母材m1磁铁材料m2中,也可以对一个面施加第一方向的磁场,并对其余的面分别施加第二方向的磁场。通过这样,可以获得在一面具有一个磁极(例如n极)而在其余面分别具有另一个磁极(例如s极)的极性各向异性磁铁。
148.b.利用平行磁场及切割技术制造磁铁组件的制造方法
149.接下来,公开一种基于平行磁场和切割技术的磁铁组件的制造方法。
150.【实施方式二】
151.1.实施方式二涉及的磁铁组件的制造方法
152.图17是用于说明实施方式二涉及磁铁组件的制造方法的流程图。作为实施方式二,以下对制造外周侧的磁铁组件100ex的方法进行说明。
153.实施方式二涉及的磁铁组件的制造方法是制造筒状的磁铁组件的方法。
154.如图17所示,实施方式二涉及的磁铁组件的制造方法至少依次包含:粉末材料准备工序ss10、磁场成型工序ss20、切割工序ss40、组装工序ss60、以及磁化工序ss70。在实施方式二中,在磁场成型工序ss20与切割工序ss40之间还包含烧结热处理工序ss30。在切割工序ss40与组装工序ss60之间还包含表面处理工序ss50。注意,在图17的右侧,作为参考显示了在规定工序中输入输出的材料构件。
155.(1)粉末材料准备工序ss10
156.粉末材料准备工序ss10是准备磁铁用粉末材料pd的工序。磁铁用粉末材料的准备可以采用以往的一般方法。例如钕磁铁,可以在溶解钕、铁、硼等原料后进行固体化,并使用粉碎机、研磨机等对固体材料进行粗粉碎和微粉碎,准备磁铁用的粉末材料pd。
157.(2)磁场成型工序ss20
158.图18是用于说明磁场成型工序ss20的图。其中,图18(a)是磁场成型情况的立体图,图18(b)是磁铁母材10的立体图,图18(c)是用假想平面pl1剖切图18(b)中的磁铁母材10时的剖视图,图18(d)是将图18(b)中的磁铁母材10用假想平面pl2剖切后的剖视图。
159.磁场成型工序ss20是成型具有第一主面11及与第一主面11相反侧的第二主面12的“磁铁母材10”的工序(参照图18(b))。在图中,符号13a指的是a侧面,13b指的是b侧面,13c指的是c侧面,13d指的是d侧面。在磁场成型工序ss20中,向与磁铁母材10的形状对应的模框890的内侧投入在粉末材料准备工序ss10中准备的粉末材料pd(省略图示),并从模框890的外侧的与第一主面11对应的一侧(图中上侧)向与第二主面12对应的一侧(图中下侧)施加单一方向的平行磁场。
160.作为具体的结构,例如在模框890的外侧,以该磁力源的n极与在成型后成为磁铁母材10时成为第一主面11的一侧(在图中为模框890的上侧)相向的方式配置第一磁力源
(省略图示),并以该磁力源的s极与在成型后成为磁铁母材10时成为第二主面12的一侧(在图中为模框890的下侧)相向的方式配置第二磁力源(省略图示)。在此基础上,使第一磁力源及第二磁力源工作,以相对于第一主面11及第二主面12垂直且磁力线相互平行、且为相同的磁通密度的方式跨越整个第一主面11及第二主面12施加磁场(参照图18(a))。虽然图中示例了从上侧到下侧的磁场,但是磁场的方向也可以是相反的方向。
161.当在模框890的内部加压如上所述的磁场时,粉末材料pd的各分子以与磁场的方向一致的方式沿着磁场的方向取向,整体上成型具有与模框890的形状对应的形状的磁铁母材10(参照图18(b))。第一主面11为大致平面。第二主面12也是大致平面且与第一主面大致平行。但并不限定于此。在磁铁母材10内部,如图18(c)及图18(d)的虚线所示,分子的方向在与第一主面11及第二主面12垂直的方向上均匀地取向。一旦分子的方向被调整好,通过执行后述的磁化工序ss70,就会沿此排列方向强烈磁化。在本说明书中,有时将这样通过实施磁场成型工序ss20而对齐的粉末材料pd中的各粉末的方向(分子的取向方向)称为“易磁化轴”。
162.(3)烧结热处理工序ss30
163.烧结热处理工序ss30对通过磁场成型工序ss20获得的磁铁母材10进行烧结热处理。当进行烧结热处理工序ss30时,磁铁母材10中所含的粘合剂(粘合剂)因热量而气化并飞溅,磁性体材料的纯度提高。进行磁场成型后,虽然也有在磁铁母材m1的内部稍微磁化的情况,但可以通过进行烧结热处理来消磁。
164.(4)切割工序ss40
165.(4-1)切割出磁铁母材件20
166.图19是用于说明切割工序ss40的图。其中,图19(a)是从与c侧面13c垂直的方向观察切割前的磁铁母材10时的右侧视图。切入磁铁母材10剖面的实线(假想线)是在进行切割时沿着该实线进行切割的切割线,即标示线。当沿着切割线切割时,后述的磁铁母材件20的轮廓(外表面)出现在外部。图19(b)是切割工序s40后获得的磁铁母材件20的立体图。
167.切割工序ss40是通过沿着上述切割线切割磁铁母材10而切割出后述的磁铁母材20的工序。
168.切割工序ss40通过线切割加工来实施。在进行线切割的时候,优选一边冷却一边切割。在切割工序ss40中导入的加工方式不限定于线切割加工,例如既可以是水射流切割加工,也可以是切削加工。通过这样,无需如以往磁铁组件的制造方法那样在每次变更规格时重新开发模框就能够仅用以往的一般的磁铁制造用设备进行规格变更。
169.(4-2)设置切割线
170.在此,将组装为磁铁组件时应当成为该磁铁组件的外径面的面定义为“规定外径面20ex”,将应当成为内径面的面定义为“规定内径面20in”。关于与切割前的这些对应的切割线,使用相同的符号【’】进行标注。
171.在实施方式二中,以在切割工序中切割的规定外径面20ex和/或规定内径面20in为平面的方式进行切割。通过使规定外径面20ex和规定内径面20in为平面,与形成为曲面的情况相比,切割作业变得简便,既能够确保高精度又能够提高生产率。
172.在实施方式二中,规定外径面20ex及规定内径面20in相互平行。
173.如图19(a)所示,规定外径面的切割线20ex’设定为相对于第一主面11倾斜角度θ
1。规定内径面的切割线20in
′
设定为相对于第一主面11倾斜角度θ2。在实施方式二中,由于例举了规定外径面及规定内径面平行情况,因此满足θ1=θ2。
174.这里虽然以第一主面11作为基准进行了切割线的设定,但实际上也可以以第一主面11和第二主面12中任意一方作为基准设定切割线。在本说明书中,也能够实施将“第一主面11”替换为“第二主面12”的实施方式,这样的情况也包含于本发明的技术范围内。
175.(4-3)切割线参数
176.在实施方式二的切割工序ss40中,相对于第一主面11的角度θ1及角度θ2分别被设定在超过45度且小于90度的范围内,在该设定下,沿着规定外径面的切割线20ex’及规定内径面的切割线20in’对磁铁母材10进行切割。
177.换言之,在实施方式二的切割工序ss40中,规定外径面的切割线20ex’设定在相对于易磁化轴(虚线的方向)超过0度且小于45度的范围内(θ3),并且,规定内径面的切割线20in’设定在相对于易磁化轴超过0度小于45度的范围内(θ4),在该设定下,沿着规定外径面切割线20ex’及规定内径面的切割线20in’切割磁铁母材10(参照图19(a))。
178.通过这样设定θ1、θ2、θ3、θ4,就能够制造水平系的极性各向异性排列的磁铁组件(外周侧的磁铁组件)。
179.(4-4)切割出磁铁母材件20
180.接下来,在如上所述地确定切割线之后,沿着规定外径面的切割线20ex’切割磁铁母材10,并且沿着规定内径面的切割线20in’切割磁铁母材10,从而切割出至少以规定外径面20ex及规定内径面20in为外表面的磁铁母材件20(参照图19(b))。
181.如图19(b)所示,通过切割工序ss40切割出的磁铁母材20在外表面除了规定外径面20ex和规定内径面20in之外,还具有在之后的组装工序ss60时相互接合的接合侧面21、24。在实施方式二例子中,接合侧面21是在进行切割工序ss40之前与磁铁母材10的第一主面11为同一面的部位。接合侧面24是通过设定另外的切割线进行切割而新出现的面。磁铁母材20具有长度方向一端侧的面22和另一端侧的面23。在图19中,展示了切出多个磁铁母材件20-1、20-2、20-3、20-4的例子,但切割出单数的情况也包含在此的切割工序ss40的实施方式中。
182.(5)表面处理工序ss50
183.表面处理工序是对磁铁块20实施用于防锈的表面处理(例如镀镍、光泽铬酸盐处理、电泳涂装、静电涂装等)的工序。
184.(6)组装工序ss60
185.图20是用于说明组装工序ss60的图。其中,图20(a)是将四块磁铁母材件20组合时的图。图20(b)是表示磁铁母材组件40ex的立体图。作为参考,图20(b)的虚线sa所示的范围如图20(a)所示。
186.组装工序ss60是将多个磁铁母材件20相互组合从而组装成磁铁母材组件40ex的工序。具体而言,准备多个通过切割工序ss40获得的磁铁母材件20(参照图19(b)),将磁铁母材件20的接合侧面21、24彼此相互接合粘接。此时,相邻的规定外径面20ex、相邻的规定内径面20in在彼此接合部没有间隙的状态(也可以是角)下被接合。通过这样,就能够组合多个磁铁块20来构成连续的外周面和内周面。
187.作为一例,图19(b)是将四块的磁铁母材件20进行组合的情况(参照图20(a))。
188.从左侧开始,首先将一端侧的面22置于近处,配置磁铁母材20-1。在其右侧相邻配置磁铁母材20-2,使长度方向的一端侧和另一端侧互换,使另一端侧的23位于近处。此时磁铁母材20-1的接合侧面24与磁铁母材20-2的接合侧面24接合。接着,在其右侧相邻,以一端侧的面22为近处配置磁铁母材20-3。此时磁铁母材20-2的接合侧面21与磁铁母材20-3的接合侧面21接合。接着,在其右侧相邻位置,将长度方向的一端侧和另一端侧调换,使另一端侧的23位于近处,配置磁铁母材20-4。此时磁铁母材20-3的接合侧面24与磁铁母材20-4的接合侧面24接合。
189.可以如上所述地组合四块磁铁母材件20-1~20-4进行组装。通过重复这样的组装,可以获得图20(b)所示的磁铁母材组件40ex。
190.(7)磁化工序ss70
191.图21是用于说明磁化工序ss70的图。图21(a)是展示进行磁化时的磁力源840n、840s的配置的剖视图,图21(b)是实施了磁化工序后的磁铁组件100ex的剖视图。
192.磁化工序ss70是从磁铁母材组件40ex的外部在规定位置施加规定的磁场而对磁铁母材组件40ex进行磁化的工序。
193.例如,如图21(a)所示,沿着磁铁母材组件40ex的外径面(更严格地说,是以中心轴为中心的周面),一边交替极性一边以等角度配置四个由磁轭构成的磁力源840n、840s。磁力源840n、840s的极配置在随着从中心轴向径向的外侧推进而逐渐接近接合侧面21、24的接合部的位置(图23(a)中用p1、p2表示的位置)。
194.并且,在规定的时间点以规定的输出使磁力源840n、840s工作来对磁铁母材组件40ex施加磁场。通过这样,在磁铁母材组件40ex的内部,可以按照在磁场成型工序ss20中形成的分子的取向方向(易磁化轴)进行磁化。最终成为如图21(b)所示的方向(磁化方向)的被磁化的磁铁组件100ex。
195.通过至少实施以上磁场成型工序ss20、切割工序ss40、组装工序ss60及磁化工序ss70,就能够获得磁铁组件100ex。
196.2.磁铁组件100ex
197.接着,对由实施方式二涉及的磁铁组件的制造方法获得的磁铁组件100ex进行说明。
198.磁铁组件100ex如图21(b)所示,具备:具有大致平面的外径面和内径面,且相对于外径面和内径面以规定的角度(θ3、θ4)且在单一方向平行地磁化的多个(n个)磁铁块50,磁铁块50经由除外径面和内径面以外的面(图20(a)中为接合侧面21、24)相互接合。
199.具体而言,磁铁组件100ex由n个磁铁块50相互接合而成,其外径侧及内径侧因该磁铁组件100ex呈n边形的筒状。图21(b)所示的磁铁组件100ex当nps(同极数)=2、npns(异极数)=2、ns(设定值且为1以上的自然数)时,ns=4,且n=2
·2·
4=16的例子。
200.也可以在组装工序ss60与磁化工序ss70之间实施圆筒化工序(省略图示),该圆筒化工序通过切削大致n边形的筒状的磁铁母材组件40ex的外径面的角,或者使保护膜等附着于外表面,来将整体圆筒化。在这种情况下,磁铁组件100ex也与此相对应地成为圆筒状。
201.在上述中,磁铁组件100ex描述为具有大致平面的外径面且呈大致n边形的筒状,但经过圆筒化工序后,最终形状的外径面为曲面或整体成为大致圆筒状时的磁铁组件也称为大致平面大致n边形并包含在本实施方式的一个形态中。
202.3.实施方式二磁铁组件的制造方法的效果
203.实施方式二涉及的磁铁组件的制造方法是:从与第一主面11对应的一侧向与第二主面12对应的一侧施加单一方向的平行磁场而成型磁铁母材10,然后,将规定外径面的切割线20ex’设定为相对于第一主面11倾斜角度θ1,从而切割磁铁母材10,并且将规定内径面的切割线20in’设定为相对于第一主面11倾斜角度θ2,从而切割磁铁母材10,从而切割出磁铁母材件20,在此基础上,将磁铁母材块20相互组合组成装磁铁母材组件40ex并进行磁化,获得磁铁组件100ex。
204.也就是说,一旦获得单一方向的分子取向方向(易磁化轴)的磁铁母材10之后,在切割工序ss40中通过变更切割的角度、切割的形状等就可以进行磁铁组件的设计变更、机型变更。即,只要适当改变切割线的设定方法,就可以适当改变磁化方向、厚度、形状等。因此,本发明磁铁组件的制造方法的设计自由度高。
205.从其他观点来说,将粉末材料准备工序ss10、磁场成型工序ss20、烧结热处理工序ss30的工序通用化、标准化,并且只要适当改变切割工序ss40的切割线的设定方法,就能够分别制作外周侧的磁铁组件100ex及内周侧的磁铁组件100in。因此,不需要对每个产品种类进行大规模的工序变更。
206.而且,不需要像以往那样针对每种产品变化准备专用的模框,而且切割工序ss40本身也能够在以往的一般的磁铁制造用设备中进行。特别是,实施方式二的制造方法在活用构成基于所谓单极制造的烧结磁铁的设备时也有用,由于设计变更容易且自由度高,因此有助于抑制开发成本、缩短开发时间,在开发试制阶段也有用。因此本发明磁铁组件的制造方法比以往经济性更高。
207.此外,即使在要组装的磁铁组件100ex的径向厚度较薄的情况下,也能够适当变更切口的角度、切口的形状等,即使是较薄的磁铁组件,也能够自由地控制磁化方向。例如,用以往的制造方法难以实现的、厚度t2为1mm~2mm左右的磁铁组件也可以根据实施方式的制造方法来实现(参照图32)。因此,在这一点上也比以往设计自由度更高。
208.由于不像以往那样在薄部件的状态下进行烧结热处理,所以在烧结热处理工序中也不会产生破损。因此成品率也比以往高,具备非常高的经济性。
209.由于在组装工序ss60中处理的构件是未磁化的磁铁母材件20,因此在没有引力、斥力的状态下相互组装,这样一来,也不存在以往哈尔巴赫排列组装时因相邻磁铁间的引力、斥力的问题无法顺利接合的问题,使接合作业非常容易进行,极具批量生产性。
210.因此,根据实施方式二是一种能够提供设计自由度比以往高且经济性高的磁铁组件的制造方法。
211.此外,以往如图32所示,一般认为分子的取向方向(易磁化轴)受到磁力源的配置、磁力源的输出大小和输出方法等的变动的影响。由于这些变动,在磁化方向上也容易产生每个产品的个体差异,导致品质参差不齐。不过根据实施方式二的磁铁组件的制造方法,由于单纯地施加单一方向的平行磁场,因此在内部形成的是相同的分子的取向方向(易磁化轴),因此能够能够抑制偏差,有助于维持高品质。
212.【实施方式三】
213.图22是展示实施方式三的切割工序ss40的情况的剖视图。其中,图22(a)是从与c侧面13c垂直的方向观察切割前的磁铁母材10时的右侧视图。图19(b)是实施了切割工序
ss40后获得的磁铁母材30的剖视图。图23是用于说明实施方式三组装工序ss60的剖视图。图23(a)是将四块磁铁母材件30组合时的图。图23(b)是展示磁铁母材组件40in立体图。图24是实施了实施方式三的磁化工序ss70后的磁铁组件100in的剖视图。图中符号30ex指规定外径面,30in指规定内径面。
214.对于基本结构和特征与实施方式二相同的结构要素,引用实施方式二中的符号并在此省略其说明。
215.实施方式三磁铁组件100in的制造方法基本上具有与实施方式二的磁铁组件100ex的制造方法相同的结构,但在切割工序ss40中的切割的角度、形状等的设定上与实施方式二的磁铁组件100ex的制造方法有所不同。
216.即,如图22(a)所示,在切割工序ss40中,规定外径面的切割线30ex’相对于第一主面11的角度θ1、及规定内径面的切割线30in’相对于第一主面11的角度θ2分别设定在0度以上且小于45度的范围内,在该设定下,并沿预定外径面的切割线30ex’及预定内径面的切割线30in’切割磁铁母材10。
217.换言之,规定外径面的切割线30ex’及规定内径面的切割线30in’分别相对于易磁化轴(虚线的方向)设定在超过45度且90度以下的范围内,在这样的设定下,沿规定外径面的切割线30ex’及规定内径面的切割线30in’来切割磁铁母材10。
218.在实施了切割工序ss40后获得的磁铁母材30如图22(b)所示。之后,与实施方式二同样地实施组装工序ss60后,可以获得如图23(b)所示磁铁母材组件40in。图23(a)对应于图20(a),而图23(b)对应于图20(b)。然后,在实施磁化工序ss70后,可以获得如图24所示磁铁组件100in。
219.在实施方式三涉及的磁铁组件100in的制造方法中,由于如上所述设定了切割线的角度,因此能够制造磁化方向更接近与外径面垂直的方向的垂直系的极性各向异性排列的磁铁组件(内周侧的磁铁组件100in)。根据实施方式三的磁铁组件100in的制造方法,也可以构成为磁化方向相对于外径面成90度(磁化方向与径向一致)。
220.由于实施方式三磁铁组件100in的制造方法除了在切割工序ss40中的切割的角度、形状等的设定以外,具有与实施方式二的磁铁组件100ex的制造方法基本相同的结构,因此具有实施方式二磁铁组件100ex的制造方法所具有的相应效果。
221.【实施方式四】
222.通过将根据实施方式二获得的磁铁组件100ex和根据实施方式三获得的磁铁组件100in组合,可以获得与专利文献1中记载的磁铁组件900类似的复合磁铁组件100(参照图30)。
223.复合磁铁组件100如图30所示,由n个磁铁块50、60(参照图21(b)和图24)相互接合而成,其外周侧和内周侧通过该磁铁组件呈n边形的筒状。
224.当nps=2:nps为同极数,npns=2:npns为异极数,ns为设定数(1以上的自然数)时,n为满足n=nps
·
npns
·
ns关系的自然数。
225.(1)复合磁铁组件100具有:第一形态的磁铁组件100ex,其通过各磁铁块50中磁化方向相对于外径面及内径面的角度为第一角度(接近0度)的实施方式二获得;以及第二形态的磁铁组件100in,其通过磁化方向相对于各磁铁块60的外径面及内径面的角度为与第一角度不同的角度即第二角度(接近90度)的实施方式三获得。并且,复合磁铁组件100的第
一形态的磁铁组件100ex配置在该复合磁铁组件100的应成为有效h磁通面100h的一侧,第二形态的磁铁组件100in配置在该复合磁铁组件的应成为有效v磁通面100v的一侧,并相互接合(参照图30)。
226.这里的“有效h磁通面”是指复合磁铁组件100的外表面,即该面的正下方内部的磁化方向相对于外表面为接近水平(h)方向的面。“有效v磁通面”是指复合磁铁组件100的外表面,且是该面的正下方内部的磁化方向接近与外表面垂直(v)的方向的面。
227.在图30的例子中,展示了将外周侧面设定为有效h磁通面100h、将内周侧面设定为有效v磁通面100v的筒状的复合磁铁组件100。该复合磁铁组件100适合作为内转子使用。
228.这里的“第一角度(θ10)”是指在磁铁组件100ex外周面(外径面)出现的磁极的位置处的切线与该磁极的位置的正下方的位置相邻的磁铁块的磁化方向之间构成的角θ10。
229.在图21(b)中,例如磁极n出现在磁铁块50-4和磁铁块50-5接合部的外周面侧,但在该磁极n的位置图示的θ10相当于第一角度。
230.同样地,“第二角度(θ20)”是指在磁铁组件100in外周面(外径面)出现的磁极位置处的切线与该磁极位置正下方的位置相邻的磁铁块的磁化方向之间构成的角θ20。在图24中,例如磁极n出现在磁铁块60-5及磁铁块60-6接合部的外周面侧,在该磁极n的位置图示的θ20相当于第二角度。
231.以上以外周面(外径面)为基准进行了说明,但以内周面(外径面)为基准也为同样的定义。
232.(2)上述例子说明的复合磁铁组件100是将外周侧的面设定为有效h磁通面100h的类型件,但实施方式四并不限定于此。例如,也可以通过将第一角度θ10设为接近90度的角度并将第二角度θ20设为接近0度的角度,将内周侧的面设定为有效h磁通面而构成另一形态的复合磁铁组件(省略图示)。所述复合磁铁组件适合作为外转子使用。
233.【实施方式五】
234.图25是用于说明实施方式五涉及的磁铁组件的制造方法及极性各向异性磁铁的制造方法的流程图。图26是用于说明子组装工序ss80的图。图27是用于说明四方磁化工序ss85的图。图27中的符号45、3所示的构件为被磁化后的状态。对于基本结构和特征与实施方式一至四相同的结构要素,标注实施方式一至四中的符号,并引用其说明而省略实施方式五中的说明。
235.实施方式五的磁铁组件的制造方法相对于实施方式三涉及的磁铁组件的制造方法所述的方法,在切割工序之后进行的组装工序及磁化工序的实施范围和实施方法上有所不同。
236.如图25所示,实施方式五涉及的磁铁组件的制造方法至少依次包括:粉末材料准备工序ss10、磁场成型工序ss20、切割工序ss40、子组装工序ss80、以及四方磁化工序ss85。在实施方式五中,在四方磁化工序ss85之后还包含磁铁组装工序ss90。另外,也可以在切割工序ss40与子组装工序ss80之间、或者子组装工序ss80与四方磁化工序ss85之间进行表面处理工序ss50。
237.粉末材料准备工序ss10、磁场成型工序ss20及切割工序ss40与实施方式三中那些工序为同样的内容。
238.子组装工序ss80是通过组合至少四个磁铁母材件20、30来组装具有四个面的磁铁
母材子组件45的工序。在实施方式五中,实施方式三中叙述的组装工序ss60由该子组装工序ss80构成。
239.如图26所示,在子组装工序ss80中,在成为磁铁母材子组件45实效面vsf“构成磁铁母材子组件45的四个面(剖面视时)中的应当集中产生磁通的面”的一侧,配置以切割工序ss40中的角度θ1及角度θ2分别为超过45度且小于90度的设定范围进行切割的水平系的磁铁母材20,并在与实效面vsf相反的一侧,配置在切割工序ss40中以角θ1及角度θ2分别在0度以上且小于45度的设定范围进行切割的垂直系的磁铁母材件30,在此基础上,将它们相互组合进行接合粘接等,从而获得磁铁母材子组件45。
240.在该阶段,由于磁铁母材件20、30还未磁化,相互不产生斥力引力,因此可以容易地进行磁铁母材件20、30彼此的组合和接合粘接等作业。
241.如图27所示,在四方磁化工序ss85中,以包围磁铁母材子组件45的方式,对磁铁母材子组件45的实效面vsf施加第一方向的磁场,以及对其余三个面施加第二方向的磁场来对磁铁母材子组件45进行磁化。在图27例子中,对作为磁铁母材子组件45的实效面vsf的第一面sf1施加由磁化用第一磁力源731产生的正磁场,对其余的第二面sf2、第三面sf3、第四面sf4,分别施加由磁化用第二磁力源732b、732a、732a产生的负磁场,从而获得从实效面vsf发出正极性磁力线的极性各向异性磁铁3n。
242.通过适当更换作为磁场施加方向的第一方向、第二方向的极性,能够获得与从极性各向异性磁铁的实效面vsf发出的磁力线的极性相反的极性各向异性磁铁3s。
243.关于上述以外的四方磁化工序ss85的详细说明,由于与实施方式一的四方磁化工序s40相同,因此引用实施方式一的四方磁化工序s40的说明并在此省略说明。作为参考,实施方式三中叙述的磁化工序在实施方式五中由该四方磁化工序ss85构成。
244.经过以上工序可以获得极性各向异性磁铁3(以上是实施方式五的极性各向异性磁铁的制造方法)。
245.磁铁组装工序ss90是组合在四方磁化工序ss85中获得的极性各向异性磁铁3n、3s来组装磁铁组件的工序。例如,将从实效面vsf发出磁力线的极性相互不同的极性各向异性磁铁3n、3s相互在侧面进行接合粘接。在这种情况下,由于相邻的极性各向异性磁铁3n、3s的侧面彼此的磁极为相反的极(n极和s极),因此在接合粘接等时相互吸引,因此组装非常容易。经过以上工序,就可以获得图25下方所示的圆筒状(圆环状)的磁铁组件100’(实施方式五的磁铁组件的制造方法)。
246.根据实施方式五涉及的磁铁组件的制造方法及极性各向异性磁铁的制造方法是将实施方式二至四的基于平行磁场及切割技术获取磁铁母材件20、30与实施方式一的基于四方磁化技术进行磁化相组合的制造方法。因此,能够同时获得实施方式二至四的平行磁场和切割技术的优点(不需要模框、设计自由度高等)、以及实施方式一的四方磁化的优点(摆脱厚度的设计制约的同时,在批量生产的基础上获得分别具有水平系和垂直系的极性各向异性排列的极性各向异性磁铁等)。
247.【应用例】
248.实施方式二中获得的磁铁组件100ex、实施方式三中获得的磁铁组件100in及使用它们构成的实施方式四的复合磁铁组件100可以应用于各种产品领域。例如,可以构成:具有包含复合磁铁组件100的转子的电机(参照图12(a))、具有包含复合磁铁组件100的转子
的发电机)参照图12(b))、具有包含复合磁铁组件100的转子的致动器(图12(c))等。
249.复合磁铁组件100优选作为旋转侧转子使用,但也可以作为固定侧的定子使用。在这种情况下,本说明书中“转子”可以替换为“定子”来应用,该情况下的结构也包含在本发明的技术范围内。
250.以上,基于上述实施方式说明了本发明,但本发明并不限定于上述实施方式。在不脱离构思的范围内能够以多种方式实施,例如还能够进行以下变形。
251.(1)上述对实施实施方式二和实施方式三而获得的磁铁组件100ex、100in呈筒状进行了说明,但本发明并不限定于此。也可以应用于直线状的磁铁组件(省略图示)。
252.例如,也可以将实施方式二、三中将规定外径面的切割线20ex’和规定内径面的切割线20in’的长度设定为相等的基础上,通过将构成磁铁块的面中应当成为该复合磁铁组件的有效h磁通面的面在相互邻接磁铁块间排列成大致同一平面的方式来构成直线形的磁铁组件。
253.在这种情况下,除了不是筒状这一点与实施方式二至四不同外,其他结构能够同样地实施。通过组合该直线形的第一形态的磁铁组件和第二形态的磁铁组件,例如能够获得图29(a)所示的直线形的复合磁铁组件130。
254.(2)通过使用线性复合磁铁组件130,也可以构成包含复合磁铁组件130的线性电机结构体550(参照图28、图29(b)及图29(c))。此时,本说明书中的转子(转子)可以替换为移动器(动子)来应用。
255.图28是用于说明应用例变形例的直线电机结构体550的示意图。图29是用于说明直线电机结构体550详细情况的图。其中,图29(b)为沿与长度方向轴平行的平面切割图28所示的直线电机结构体550时的剖视图,图29(c)为沿图29(b)的a-a线切割时的剖视图。在图中,符号552为轨道,553为移动体,553a为移动体的线圈部,70、80为磁铁块,130ex为外径侧的磁铁组件,130in为内径侧的磁铁组件,130为复合磁铁组件。
256.【符号说明】
257.1n、1n’、1s、1s’、2n、2n’、2s、2s’、3、3n、3s
…
极性各向异性磁铁;5
…
预磁化材料;6
…
软磁铁;10
…
磁铁母材;11
…
第一主面;12
…
第二主面;13a
…
a侧面;13b
…
b侧面;13c
…
c侧面;13d
…
d侧面;20、30
…
磁铁母材件;20ex、30ex
…
规定外径面;20ex'、30ex
’…
规定外径面的切割线;20in、30in
…
规定内径面;20in'、30in
’…
规定内径面的切割线;21、24
…
接合侧面;22
…
一端侧的面;23
…
另一端侧的面;40ex,40in
…
磁铁母材组件;45
…
磁铁母材子组件;50、60、70、80
…
磁铁块;100、100'、100ex、100in、110、120、130ex、130in、400ex、400in、420l、420u、430、900、900ex、900in
…
磁铁组件;100h
…
有效h磁通面;100v
…
有效v磁通面;130
…
复合磁铁组件;400
…
圆筒状的双层结构的磁铁单元;420
…
直线状的双层结构的磁铁单元;510
…
电机;520
…
发电机;530
…
致动器;550
…
直线电机结构体;552
…
导轨;553
…
移动体;553a
…
移动体的线圈部;710
…
模框;721
…
第一磁力源;722、722a、722b、722c
…
第二磁力源;731
…
磁化用第一磁力源;732、732a、732b、732c
…
磁化用第二磁力源;890、810
…
模框;810a
…
模框的内侧;820n、820s、830n、830s、840n、840s
…
磁力源;905、906、907、908
…
磁铁;905'、906'
…
母材。