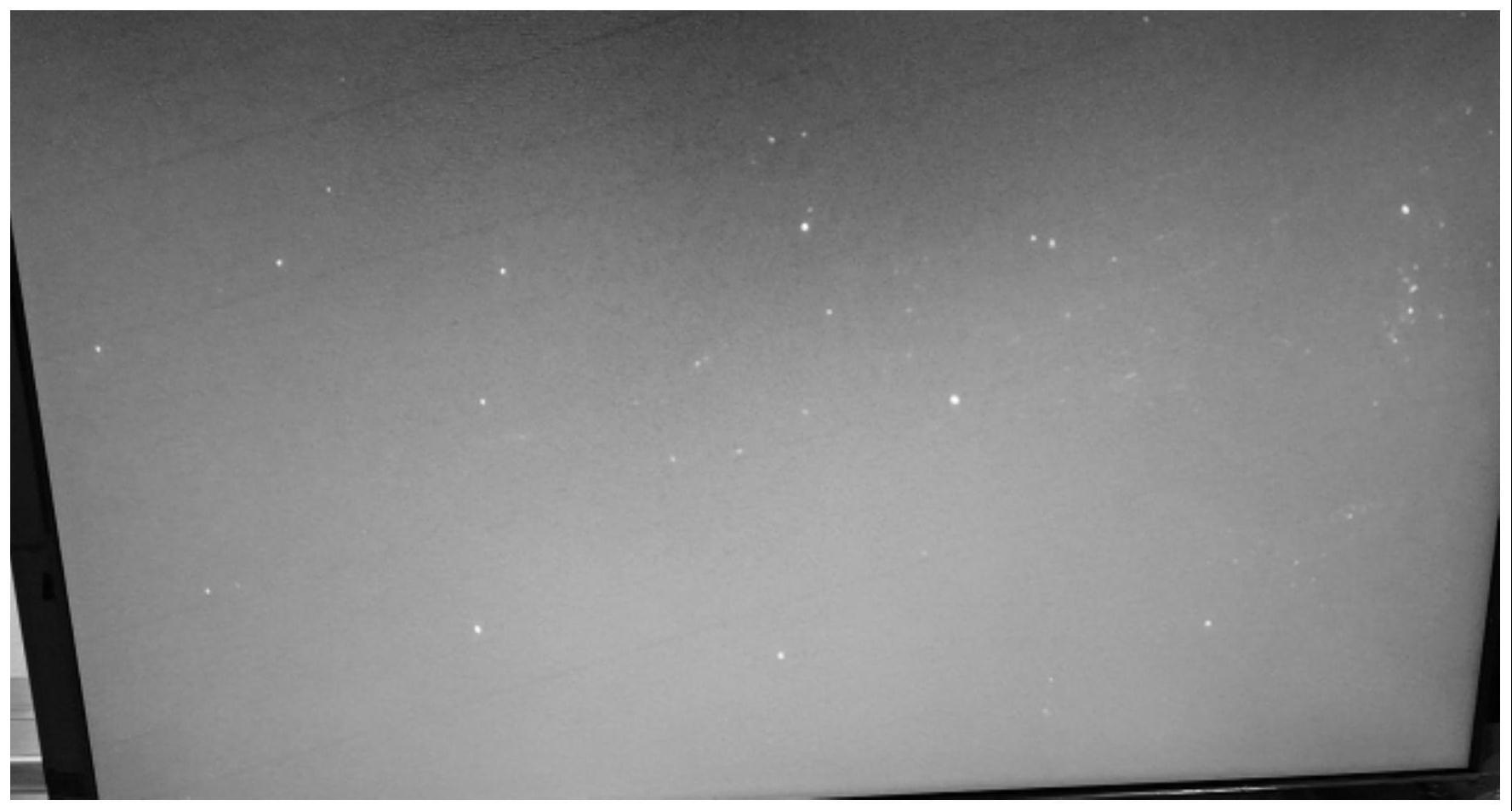
1.本发明涉及电池技术领域,特别是涉及一种硅片清洗方法及电池。
背景技术:2.hjt电池简称异质结电池,相比于当前使用的perc电池,hjt电池具有更高的提升潜力,具有较低的温度系数和低光致衰减,稳定性高,且hjt工艺制备流程相对简化,它以n型单晶硅片作衬底,经制绒、非晶硅薄膜沉积、金属氧化物导电层tco制备、丝网印刷制作正负电极导出电流等4个步骤,工艺简单。
3.传统的异质结电池的制备技术中,一般采用pvd工艺制备金属氧化物导电层tco。pvd是指在真空条件下采用物理方法将固体或液体的原料源气化成气态原子或分子、或部分电离成离子,并通过低压气体或等离子体过程,在基体表面沉积具有某种特殊功能的薄膜的技术,采用pvd工艺镀膜的过程中不可避免的会产生原料粉尘和颗粒。
4.因此,现有技术仍有待改进。
技术实现要素:5.基于此,本发明提供一种硅片清洗方法及电池,该硅片清洗方法能高效去除镀膜硅片表面附着的粉尘或颗粒的同时,不损伤镀膜硅片。
6.本发明的一个方面,提供了一种硅片清洗方法,包括如下步骤:
7.将硅片依次进行第一水洗、化学清洗和第二水洗,得到清洗后的硅片;
8.所述化学清洗采用的试剂为碱液或酸液,所述酸液的质量浓度为0.4%~5%,所述酸液的组分包含hf;所述碱液的质量浓度为0.3%~0.9%;
9.所述化学清洗的步骤的温度为20℃~30℃,时间为100s~300s;
10.所述硅片包括硅基材及包覆于所述硅基材表面的透明导电薄膜。
11.在其中一些实施例中,所述第一水洗的步骤在超声条件下进行,所述超声的频率为1khz~2.4khz。
12.在其中一些实施例中,所述提拉清洗的步骤中,控制提拉速度为3mm/s~5mm/s。
13.在其中一些实施例中,所述提拉清洗的温度为55℃~80℃。
14.在其中一些实施例中,所述第一水洗的步骤的温度为20℃~30℃,时间为100s~300s。
15.在其中一些实施例中,所述第二水洗的步骤的温度为20℃~30℃,时间为100s~300s。
16.在其中一些实施例中,所述酸液的组分还包含hcl。
17.在其中一些实施例中,所述碱液中的碱选自碱金属的氢氧化物。
18.在其中一些实施例中,所述透明导电薄膜经物理气相沉积法制得。
19.本发明的另一方面,提供一种电池,该电池包含如上所述的硅片的清洗方法制得的硅片。
20.上述硅片清洗方法中,将硅片依次进行第一水洗、化学清洗、第二水洗和提拉清洗,通过第一水洗将硅片表面大部分粘附较松的粉尘及颗粒,进一步采用酸液或碱液进行化学清洗,酸液或碱液与粉尘及颗粒反应,从而腐蚀掉硅片表面粘附紧密的粉尘或颗粒,同时通过控制酸液或碱液的组分及其浓度,并控制化学清洗的步骤的温度及时间,使酸液或碱液腐蚀掉硅片表面粘附紧密的粉尘或颗粒的同时,不损伤硅基材及其表面的透明导电薄膜;然后进行第二水洗和提拉清洗,清洗掉残留的酸液或碱液以及残留的粉尘颗粒。如此,在高效去除硅片表面附着的粉尘或颗粒的同时,不损伤镀膜硅片,使其保持原有的导电性能。
21.其中,当采用酸液进行化学清洗时,hf可以去除硅片表面的sio2,sio2具有极性键,有亲水特性,hf可以去除镀膜硅片表面的sio2后,硅片表面转为疏水性,使镀膜硅片在后续的第二水洗步骤中,表面表现出脱水性,减少了清洗后的镀膜硅片上的水印。
22.进一步地,第一水洗的步骤在超声条件下进行,并控制超声的频率为1khz~2.4khz,在特定频率的超声作用下,促进镀膜硅片表面的粉尘及颗粒与镀膜硅片分离,在进一步促进对粉尘及颗粒的清除的同时,不损伤硅基材及其表面的透明导电薄膜,使其保持原有的导电性能。
23.进一步地,提拉清洗的步骤中,控制提拉速度为3mm/s~5mm/s,缓慢提拉清洗硅片,使硅片表面附着的水洗液体逐渐脱离,从而减少水洗后的镀膜硅片的表明附着的水洗液体,在减少了清洗后的镀膜硅片上的水印的同时,进一步避免了水洗液中的携裹的粉尘或颗粒又重新附着在镀膜硅片上,进一步提高了清洗效果。
24.上述电池包含如上所述的硅片的清洗方法制得的硅片,上述硅片的清洗方法能高效去除镀膜硅片表面附着的粉尘或颗粒的同时,不损伤镀膜硅片。如此,避免了粉尘和颗粒对电池性能的不利影响,提高了电池性能,并能提高丝网印刷时网版的使用寿命,进而提高电池的制备效率,降低损耗成本。
附图说明
25.图1为实施例1未清洗的镀膜硅片的照片;
26.图2为实施例1清洗后的镀膜硅片的照片;
27.图3为实施例1实验组的光电转化效率趋势图;
28.图4为实施例1对照组的光电转化效率趋势图。
具体实施方式
29.为了便于理解本发明,下面将对本发明进行更全面的描述,给出了本发明的较佳实施例。但是,本发明可以以许多不同的形式来实现,并不限于本文所描述的实施例。相反地,提供这些实施例的目的是使对本发明的公开内容的理解更加透彻全面。
30.除非另有定义,本文所使用的所有的技术和科学术语与属于本发明的技术领域的技术人员通常理解的含义相同。本文中在本发明的说明书中所使用的术语只是为了描述具体的实施例的目的,不是旨在于限制本发明。本文所使用的术语“和/或”包括一个或多个相关的所列项目的任意的和所有的组合。
31.本发明中的词语“优选地”、“更优选地”等是指,在某些情况下可提供某些有益效
果的本发明实施方案。然而,在相同的情况下或其他情况下,其他实施方案也可能是优选的。此外,对一个或多个优选实施方案的表述并不暗示其他实施方案不可用,也并非旨在将其他实施方案排除在本发明的范围之外。
32.当本文中公开一个数值范围时,上述范围视为连续,且包括该范围的最小值及最大值,以及这种最小值与最大值之间的每一个值。进一步地,当范围是指整数时,包括该范围的最小值与最大值之间的每一个整数。此外,当提供多个范围描述特征或特性时,可以合并该范围。换言之,除非另有指明,否则本文中所公开之所有范围应理解为包括其中所归入的任何及所有的子范围。
33.镀膜的过程中不可避免的会产生原料粉尘和颗粒,一方面,原料粉尘或颗粒会掉落到硅片表面,导致制得的电池片的外观不良,另一方面,原料粉尘或颗粒带到后续丝网印刷制备电极的步骤中,会划伤丝网或使丝网网板堵孔,从而影响丝网印刷性,最终影响到电池片的效率。
34.本技术发明人在从事本领域技术工作过程中发现:本领域中一般采用压缩空气或者吹n2或吸的方式去除镀膜硅片表面的原料粉尘或颗粒,本技术发明人经过大量实际工艺技术操作后进一步发现:采用压缩空气或者吹n2的工艺无法准确控制,如风量小了颗粒无法吹掉,风量大了会损伤硅片,甚至将粉尘吹到没有粉尘的硅片上,反而导致二次污染,负面影响更大,采用吸的方式时,pvd产生的部分较小的颗粒紧密粘附在膜的表面,无法完全吸除,且吸力太大又会将损伤硅片,反而导致电池的生产制造成本增加。基于此,本技术的技术人员另辟蹊径,在经过大量创造性实验探究后,获得本技术中能高效去除镀膜硅片表面附着的粉尘或颗粒的同时,不损伤镀膜硅片的清洗方法。
35.本发明一实施方式提供了一种硅片清洗方法,包括如下步骤s10。
36.步骤s10、将硅片依次进行第一水洗、化学清洗、第二水洗和提拉清洗,得到清洗后的硅片。
37.化学清洗采用的试剂为碱液或酸液,酸液的质量浓度为0.4%~5%,酸液的组分包含hf;碱液的质量浓度为0.3%~0.9%;
38.镀膜硅片包括硅基材及包覆于所述硅基材表面的透明导电薄膜。
39.上述硅片的清洗方法中,将硅片依次进行第一水洗、化学清洗、第二水洗和提拉清洗,通过第一水洗将镀膜硅片表面大部分粘附较松的粉尘及颗粒,进一步采用酸液或碱液进行化学清洗,酸液或碱液与粉尘及颗粒反应,从而腐蚀掉镀膜硅片表面粘附紧密的粉尘或颗粒,同时通过控制酸液或碱液的组分及其浓度,并控制化学清洗的步骤的温度及时间,使酸液或碱液腐蚀掉镀膜硅片表面粘附紧密的粉尘或颗粒的同时,不损伤硅基材及其表面的透明导电薄膜;然后进行第二水洗和提拉清洗,清洗掉残留的酸液或碱液以及残留的粉尘颗粒。如此,在高效去除镀膜硅片表面附着的粉尘或颗粒的同时,不损伤镀膜硅片,使其保持原有的导电性能。
40.其中,当采用酸液进行化学清洗时,hf可以去除镀膜硅片表面的sio2,sio2具有极性键,有亲水特性,hf可以去除镀膜硅片表面的sio2后,镀膜硅片表面转为疏水性,使镀膜硅片在后续的第二水洗步骤中,表面表现出脱水性,减少了清洗后的镀膜硅片上的水印。
41.可理解,由于现有镀膜工艺的工艺特性,镀膜硅片表面不可避免的会存在粉尘或颗粒,这些粉尘或颗粒中小部分来自于空气中的携带的粉尘,绝大部分为镀膜原料源在镀
膜过程中产生的原料颗粒或粉尘,如镀膜表面的膜层为透明导电薄膜,则粉尘绝大部分为形成透明导电薄膜的原料在镀膜过程中产生的粒子。
42.在其中一些实施例中,透明导电薄膜经物理气相沉积法制得。
43.换言之,上述硅片为经物理气相沉积法镀膜后的硅片。以ito膜为例,通常采用ito(in2o3掺锡)靶材通过pvd的方式沉积到硅片表面形成透明导电薄膜,沉积的过程中,在硅片表面沉积的同时,也会沉积到设备的腔体部分,不断的积累沉积,加上温度湿度的变化形成粉尘,在批量化生产过程中,粉尘又会落到硅片表面,然后带入丝网生产段,对丝网印刷造成影响,从而会影响到电池的整体效率。
44.在其中一些实施例中,上述透明导电薄膜包括金属薄膜、半导体薄膜中的至少一种。
45.进一步地,上述透明导电薄膜为透明导电氧化物薄膜。具体地,包括但不限于:ito膜、iwo膜
46.在其中一些实施例中,上述第一水洗的步骤在超声条件下进行,超声的频率为1khz~2.4khz。
47.在特定频率的超声作用下,促进镀膜硅片表面的粉尘及颗粒与镀膜硅片分离,在进一步促进对粉尘及颗粒的清除的同时,不损伤硅基材及其表面的透明导电薄膜,使其保持原有的导电性能。
48.在其中一些实施例中,化学清洗的步骤的温度为20℃~30℃,时间为100s~300s。
49.在其中一些实施例中,上述提拉清洗的温度为55℃~80℃。
50.控制提拉清洗的温度在较高的范围,为后续烘干做准备。
51.在其中一些实施例中,第一水洗和/或化学清洗和/或第二水洗可采用槽式设备进行,也可采用链式设备进行。
52.具体地,第一水洗和/或化学清洗和/或第二水洗的清洗方式可采用循环清洗,也可采用溢流清洗方式。
53.在其中一些实施例中,第一水洗的步骤的温度为20℃~30℃,时间为100s~300s。
54.在其中一些实施例中,第二水洗的步骤的温度为20℃~30℃,时间为100s~300s。
55.在其中一些实施例中,上述提拉清洗的步骤中控制提拉速度为3mm/s~5mm/s。
56.可理解,硅片在镀膜过程中,其表面的部分硅不可避免地会被氧化成亲水性的二氧化硅,通过控制镀膜硅片时的提拉速度,缓慢提拉清洗后的镀膜硅片,使镀膜硅片表面附着的水洗液体逐渐脱离,从而减少水洗后的镀膜硅片的表明附着的水洗液体,在减少了清洗后的镀膜硅片上的水印的同时,进一步避免了水洗液中的携裹的粉尘或颗粒又重新附着在镀膜硅片上,进一步提高了清洗效果。
57.具体地,上述提拉清洗的清洗液采用水,具体采用溢流清洗方式进行。
58.在其中一些实施例中,上述酸液的组分还包含hcl。
59.需要说明的是,当上述酸液的组分还包含hcl时,酸液的质量浓度为是指hcl和hf的总质量浓度。
60.在其中一些实施例中,上述碱液中的碱选自碱金属的氢氧化物。
61.具体地,上述碱液中的碱选自氢氧化钾和氢氧化钠中的至少一种。
62.在其中一些实施例中,上述酸液或碱液为酸的水溶液或碱液的水溶液。
63.在其中一些实施例中,在第二水洗的步骤之后,还包括将水洗后的镀膜硅片进行干燥的步骤。
64.本发明以实施方式还提供一种电池,该电池包含如上所述的硅片的清洗方法制得的硅片。
65.上述硅片的清洗方法能高效去除镀膜硅片表面附着的粉尘或颗粒的同时,不损伤镀膜硅片。如此,避免了粉尘和颗粒对电池性能的不利影响,提高了电池性能,并能提高丝网印刷时网版的使用寿命,进而提高电池的制备效率,降低损耗成本。
66.具体地,上述电池的制备包括如下步骤:
67.将硅片基材进行制绒、然后经物理气相沉积法镀膜、再采用如上所述的硅片的清洗方法清洗、最后制作电极,得到电池。
68.在其中一些实施例中,在经物理气相沉积法镀膜的步骤之前,将制绒后的硅片采用pecvd沉积非晶硅薄膜。此时,制得的电池为异质结电池。具体地,通过丝网印刷技术在硅片上印刷银栅线,制作正负电极导出。
69.下面将结合具体的实施例对本发明进行了说明,但本发明并不局限于下述实施例,应当理解,所附权利要求概括了本发明的范围,在本发明构思的引导下本领域的技术人员应意识到,对本发明的各实施例所进行的一定的改变,都将被本发明的权利要求书的精神和范围所覆盖。
70.以下为具体实施例。
71.实施例1
72.(1)配置hf溶液:将浓度为49wt%的氢氟酸和水按照1:60的体积比混合,得到hf溶液。hf溶液的浓度为质量浓度为0.8%。
73.准备镀膜硅片:采用pvd在硅片上沉积ito膜,形成镀膜硅片,镀膜硅片的照片如图1所述,镀膜硅片表面有细小粉尘及颗粒。
74.(2)将pvd处理下料后的镀膜硅片置于水槽中,于2.4khz的超声波作用下,于23+/-3℃水洗300s;
75.将水洗后的镀膜硅片置于hf溶液中进行循环式清洗,于23+/-3℃清洗150s;然后于23+/-3℃下、水槽中进行溢流清洗150s,然后于溢流清洗模式、60℃下,将镀膜硅片以3mm/s~5mm/s的提拉速度提拉清洗,60s将镀膜硅片提拉出水槽,然后于90℃下干燥900s,得到清洗后的镀膜硅片。
76.清洗后的镀膜硅片的照片如图2所示,清洗后的镀膜硅片表面未存在粉尘及颗粒,且膜面完整无损伤。
77.(3)重复步骤(1)~(2)100次,清洗镀膜硅片100片,清洗后的镀膜硅片表面未存在粉尘及颗粒,视为清洗合格硅片;清洗后的镀膜硅片表面未存在粉尘及颗粒,且膜面完整无损伤为良品,视为合格产品,并进一步按照如下公式计算清洗合格率及良品率:
78.清洗合格率=清洗合格硅片数量
÷
硅片总数
×
100%
79.良品率=合格产品
÷
硅片总数
×
100%
80.具体结果请见表1。
81.(4)分别将未清洗和清洗后的镀膜硅片设为实验组合対照组,分别制成电池片,并分别进行电性能测试,测试过程以常规太阳电池标准为准:3a标准,25℃,am1.5,1000w/m2。
实验组和対照组的光电转换效率图分别如图3和图4所示,图3和图4中横纵坐标为硅片数,纵坐标为光电转换效率。
82.进一步地,计算电性能测试中各参数的平均值,具体结果请见表2。
83.表2
[0084] 数量etauociscff实验组843224.0410.744610.48184.45対照组634323.9850.743610.50684.17
[0085]
其中,数量是指进行实验的镀膜硅片的数量;eta为光电转换效率,单位为%;uoc为开路电压,单位为v;isc为短路电流,单位为a;ff为填充因子,单位为%。
[0086]
将两者的效率趋势图对比分析可以看出,将硅片表面的粉层去除之后,清洗后的镀膜硅片的效率稳定性明显更高,而未清洗的部分因为粉层对丝网影响,效率持续成下滑趋势;最终体现在平均效率上时,从表2中的数据eta可看出,实验组的平均效率高0.05%。
[0087]
而在shj电池的规模化生产中,效率的提升意味着成本的降低。例如,按照0.05%的效率提升进行测算,以每瓦1.2元,shj电池的原效率按照24%进行粗略测算,则每gw产能每年可增加收益为:1.2
×
1000000000
×
0.05%
÷
24%=500万元。
[0088]
实施例2
[0089]
(1)配置hf溶液:将浓度为49wt%的氢氟酸和水按照1:10的体积比混合,得到hf溶液。hf溶液的浓度为质量浓度为4.9%。
[0090]
准备镀膜硅片:采用pvd在硅片上沉积ito膜,形成镀膜硅片,镀膜硅片的照片如图1所述,镀膜硅片表面有细小粉尘及颗粒。
[0091]
步骤(2)~(3):同实施例1步骤(2)~(3)。具体结果请见表1。
[0092]
实施例3
[0093]
(1)配置hf溶液:将浓度为49wt%的氢氟酸和水按照1:120的体积比混合,得到hf溶液。hf溶液的浓度为质量浓度为0.4%。
[0094]
准备镀膜硅片:采用pvd在硅片上沉积ito膜,形成镀膜硅片,镀膜硅片的照片如图1所述,镀膜硅片表面有细小粉尘及颗粒。
[0095]
步骤(2)~(3):同实施例1步骤(2)~(3)。具体结果请见表1。
[0096]
实施例4
[0097]
(1)同实施例1步骤(1)。
[0098]
(2)将pvd处理下料后的镀膜硅片置于水槽中,于1khz的超声波作用下,于23+/-3℃水洗300s;
[0099]
其余步骤同实施例步骤(2)。
[0100]
清洗后的镀膜硅片表面未存在粉尘及颗粒,且膜面完整无损伤。
[0101]
步骤(3):同实施例1步骤(3)。具体结果请见表1。
[0102]
实施例5
[0103]
(1)配置koh溶液:将浓度为46wt%的koh水溶液和水按照1:100的体积比混合,得到koh溶液。koh溶液的浓度为质量浓度为0.45%。
[0104]
准备镀膜硅片:采用pvd在硅片上沉积ito膜,形成镀膜硅片,镀膜硅片表面有细小粉尘及颗粒。
[0105]
(2)将pvd处理下料后的镀膜硅片置于水槽中,于2.4khz的超声波作用下,于23+/-3℃水洗300s;
[0106]
将水洗后的镀膜硅片置于koh溶液中进行循环式清洗,于23+/-3℃清洗150s;然后于23+/-3℃下、水槽中进行溢流清洗150s,然后于溢流清洗模式、60℃下,将镀膜硅片以3mm/s~5mm/s的提拉速度提拉,60s将镀膜硅片提拉出水槽,然后于90℃下干燥900s,得到清洗后的镀膜硅片,清洗后的镀膜硅片表面未存在粉尘及颗粒,且膜面完整无损伤。
[0107]
(3)重复步骤(1)~(2)100次,清洗镀膜硅片100片,清洗后的镀膜硅片表面未存在粉尘及颗粒,且膜面完整无损伤为良品,并计算良品率:
[0108]
良品率=合格硅片数量
÷
硅片总数
×
100%
[0109]
具体结果请见表1。
[0110]
实施例6
[0111]
实施例6与实施例1基本相同,不同之处仅在于:步骤(2)中提拉清洗时以100mm/s的提拉速度提拉清洗,60s将镀膜硅片提拉出水槽,然后于90℃下干燥900s,得到清洗后的镀膜硅片。其他步骤与条件同实施例1相同。具体结果请见表1。
[0112]
对比例1
[0113]
对比例1与实施例1基本相同,不同之处仅在于采样点hf溶液的浓度不同,配置hf溶液:将浓度为49wt%的氢氟酸和水按照1:5的体积比混合,得到hf溶液。hf溶液的浓度为质量浓度为10%。
[0114]
其他步骤与条件同实施例1相同。具体结果请见表1。
[0115]
对比例2
[0116]
对比例2与实施例1基本相同,不同之处仅在于:步骤(2)中将pvd处理下料后的镀膜硅片置于水槽中,于5khz的超声波作用下,于23+/-3℃水洗300s。其他步骤与条件同实施例1相同。
[0117]
具体结果请见表1。
[0118]
对比例3
[0119]
对比例3与实施例5基本相同,不同之处仅在于采用的碱液的浓度不同:配置koh溶液:将浓度为46wt%的koh水溶液和水按照1:10的体积比混合,得到koh溶液。koh溶液的浓度为质量浓度为4.6%。其他步骤与条件同实施例5相同。
[0120]
具体结果请见表1。
[0121]
对比例4
[0122]
对比例4与实施例1基本相同,不同之处仅在于:步骤(2)中将水洗后的镀膜硅片置于hf溶液中清洗时,控制温度为60+/-3℃,其他步骤与条件同实施例1相同。
[0123]
具体结果请见表1。
[0124]
对比例5
[0125]
对比例5与实施例1基本相同,不同之处仅在于:步骤(2)中将水洗后的镀膜硅片置于hf溶液中清洗时,控制清洗时间为600s,其他步骤与条件同实施例1相同。
[0126]
具体结果请见表1。
[0127]
表1
[0128] 清洗合格率良品率
实施例199%98.2%实施例298.5%98.1%实施例398.6%98.1%实施例498.9%98.2%实施例598.3%98%实施例698.5%95%对比例150%49.2%对比例295%94.3%对比例310%9.8%对比例460%59.2%对比例590.1%85.5%
[0129]
以上所述实施例的各技术特征可以进行任意的组合,为使描述简洁,未对上述实施例中的各个技术特征所有可能的组合都进行描述,然而,只要这些技术特征的组合不存在矛盾,都应当认为是本说明书记载的范围。
[0130]
以上所述实施例仅表达了本发明的几种实施方式,其描述较为具体和详细,但并不能因此而理解为对发明专利范围的限制。应当指出的是,对于本领域的普通技术人员来说,在不脱离本发明构思的前提下,还可以做出若干变形和改进,这些都属于本发明的保护范围。因此,本发明专利的保护范围应以所附权利要求为准。