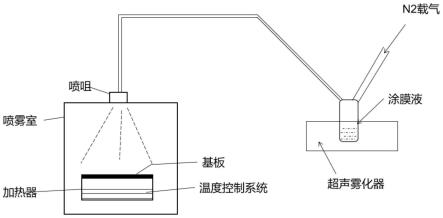
一种基于n掺杂zno人工电解质界面膜修饰硬碳负极及其制备方法
技术领域
1.本发明涉及锂离子电池负极材料领域,特别是涉及一种基于n掺杂zno人工电解质界面膜修饰硬碳负极及其制备方法。
背景技术:2.随着对于电池能量密度的要求越来越高,仅仅依靠石墨材料已无法满足人类当今社会对于电池应用的要求。而在非石墨碳材料中,具有类石墨结构与丰富空隙分布的硬碳因其低电压平台,容量大等特点被认为是理想材料。而硬碳材料由于其初始库伦效率(ice)较低,限制了其实际应用,因此提升硬碳材料的首圈库伦效率对于硬碳负极的开发拥有着巨大的意义,在此我们希望通过调整硬碳与电解质之间的界面结构来减少电解液的不可逆分解,从而提升硬碳负极材料的ice。而zno具有较高的理论容量(988mah/g),而在锂离子电池中氧化锌与锂结合、分离稳定,能够有效防止充放电过程中锂枝晶的形成,具有良好的安全性,能够有效提升负极材料的ice,同时提升初始比容量。
3.现有技术中的一种柿饼状核壳结构c/zno锂离子电池负极材料的制备方法,该方法以无水乙醇、二水合乙酸锌、乙醇胺、葡萄糖等为原料,通过控制水热反应的时间和温度,从而得到柿饼状核壳结构c/zno材料。此方法得到的柿饼状核壳结构c/zno材料具有较高的初始比容量,但是由于大部分容量提升都是通过调控zno来实现的,所以导致ice较低,并不具备实际应用要求。
技术实现要素:4.为解决上述技术问题,本发明提供一种性能优异的基于n掺杂zno人工电解质界面膜修饰硬碳负极。
5.本发明还提供一种基于n掺杂zno人工电解质界面膜修饰硬碳负极的制备方法,合成工艺简单、条件可控、成本低廉、易于扩大生产。
6.本发明采用如下技术方案:
7.一种基于n掺杂zno人工电解质界面膜修饰硬碳负极的制备方法,包括如下步骤:
8.s1、将4g植物纤维置于质量比为1:1的去离子水和乙醇的混合溶液中洗涤,除去表面灰尘和杂质,在80℃下干燥6h;取出干燥后的植物纤维,置于200ml 浓度为0.1~4mol/l的naoh溶液中,在80℃下搅拌4h,除去表面胶质等组分,搅拌结束后,用去离子水洗涤植物纤维至中性;将收集到的植物纤维置于100ml 浓度为0.1~1mol/l的氯的含氧盐溶液中,用乙酸调节溶液ph值至4.5,于80℃下搅拌1h,搅拌结束后将处理得到的植物纤维置于去离子和乙醇质量比为1:1 的溶液中洗涤三次,在80℃下干燥,得到预处理后的植物纤维;
9.s2、将预处理后的植物纤维进行烧结,得到硬碳材料;将硬碳材料进行粉碎后,按照比例将硬碳材料、cmc、sp、sbr制成水基浆料,将得到的浆料涂在铜箔上,于100℃的真空干燥箱中干燥12h,得到硬碳材料负极;
10.s3、将100ml一定浓度的zn(ch3coo)2·
2h2o水溶液与150ml一定浓度的ch3coonh4混合均匀,得到涂膜液;
11.s4、将得到的硬碳材料负极加热至300~500℃,然后通过超声雾化器将前驱体涂膜液雾化,通过n2载气送去薄膜生长室,在加热的硬碳材料负极表面发生热解反应生成n掺杂zno薄膜,喷咀到沉底表面距离为10cm,保温时间10min,在硬碳负极表面形成一定厚度的界面层,即得到n掺杂zno人工电解质界面膜修饰的硬碳负极。
12.对上述技术方案的进一步改进为,所述植物纤维为农作物秆茎、植物秆茎中的一种或两种组合;所述农作物秆茎包括但不限于秆稻壳、稻草、麦秸、玉米秸秆、棉花秆、木屑、竹屑。
13.对上述技术方案的进一步改进为,所述氯的含氧盐为高氯酸钠、次氯酸钠、亚氯酸钠中的一种。
14.对上述技术方案的进一步改进为,在所述步骤s2中,所述烧结的条件为在惰性气体条件下烧结,所述烧结的温度为400℃~1500℃,烧结时间为0.5~10h,所述惰性气体为氮气、氩气中的一种或组合。
15.对上述技术方案的进一步改进为,在所述步骤s2中,所述粉碎的方式为机械磨粉碎、流化床磨粉碎、球磨粉碎或气流磨粉碎中的一种,所述粉碎终点条件为d50=3~20μm。
16.对上述技术方案的进一步改进为,在所述步骤s2中,所述硬碳材料、cmc、 sp、sbr的质量比为94.5:1.5:1.5:2.5。
17.对上述技术方案的进一步改进为,在所述步骤s3中,所述 zn(ch3coo)2·
2h2o水溶液的浓度为0.1~2mol/l,所述ch3coonh4的浓度为 1~4mol/l。
18.对上述技术方案的进一步改进为,在所述步骤s4中,所述n2载气的流速为10~80l/h,沉积时间为10~60s。
19.对上述技术方案的进一步改进为,在所述步骤s4中,所述界面层为 1~100nm。
20.一种基于n掺杂zno人工电解质界面膜修饰硬碳负极,使用上述的制备方法制得所述基于n掺杂zno人工电解质界面膜修饰硬碳负极。
21.本发明的有益效果为:
22.(1)本发明采用生物质前驱体植物纤维,来源广泛,成本低廉易得。
23.(2)通过提纯改性得到的纤维素具有独特的三维网状结构,有利于在碳化热解过程中构建良好的离子导电通路。
24.(3)基于超声喷雾热解法制备的n掺杂zno涂层合成工艺简单、条件可控、成本低廉、易于扩大生产,利用该工艺制备的n掺杂zno涂层导电性能优异,与硬碳负极材料结合力强,在硬碳负极材料表面形成的一层人工sei膜能够有效的提高ice,且容量损失小,是一种能够兼顾容量与首效的负极材料制备方法,具有较高的应用前景。
附图说明
25.图1为本发明的基于n掺杂zno人工电解质界面膜修饰硬碳负极的制备方法的设备示意图。
具体实施方式
26.下面结合实例来进一步说明本发明,但本发明要求保护的范围并不局限于实施例所表述的范围。
27.一种基于n掺杂zno人工电解质界面膜修饰硬碳负极的制备方法,包括如下步骤:
28.s1、将4g植物纤维置于质量比为1:1的去离子水和乙醇的混合溶液中洗涤,除去表面灰尘和杂质,在80℃下干燥6h;取出干燥后的植物纤维,置于200ml 浓度为0.1~4mol/l的naoh溶液中,在80℃下搅拌4h,除去表面胶质等组分,搅拌结束后,用去离子水洗涤植物纤维至中性;将收集到的植物纤维置于100ml 浓度为0.1~1mol/l的氯的含氧盐溶液中,用乙酸调节溶液ph值至4.5,于80℃下搅拌1h,搅拌结束后将处理得到的植物纤维置于去离子和乙醇质量比为1:1 的溶液中洗涤三次,在80℃下干燥,得到预处理后的植物纤维;
29.s2、将预处理后的植物纤维进行烧结,得到硬碳材料;将硬碳材料进行粉碎后,按照比例将硬碳材料、cmc、sp、sbr制成水基浆料,将得到的浆料涂在铜箔上,于100℃的真空干燥箱中干燥12h,得到硬碳材料负极;
30.s3、将100ml一定浓度的zn(ch3coo)2·
2h2o水溶液与150ml一定浓度的ch3coonh4混合均匀,得到涂膜液;
31.s4、如图1所示,在温度控制系统调节下,将得到的硬碳材料负极通过加热器加热至300~500℃,然后通过超声雾化器将前驱体涂膜液雾化,通过n2载气送去薄膜生长室(喷雾室),在加热的硬碳材料负极表面发生热解反应生成n 掺杂zno薄膜,喷咀到沉底表面距离为10cm,保温时间10min,在硬碳负极表面形成一定厚度的界面层,即得到n掺杂zno人工电解质界面膜修饰的硬碳负极。
32.进一步地,所述植物纤维为秆稻壳、稻草、麦秸、玉米秸秆、棉花秆、木屑、竹屑等农作物秸秆或其它植物的秆茎中的一种或几种组合。
33.进一步地,所述氯的含氧盐为高氯酸钠、次氯酸钠、亚氯酸钠中的一种。
34.进一步地,在所述步骤s2中,所述烧结的条件为在惰性气体条件下烧结,所述烧结的温度为400℃~1500℃,烧结时间为0.5~10h,所述惰性气体为氮气、氩气中的一种或组合。
35.进一步地,在所述步骤s2中,所述粉碎的方式为机械磨粉碎、流化床磨粉碎、球磨粉碎或气流磨粉碎中的一种,所述粉碎终点条件为d50=3~20μm。
36.进一步地,在所述步骤s2中,所述硬碳材料、cmc、sp、sbr的质量比为94.5:1.5:1.5:2.5。
37.进一步地,在所述步骤s3中,所述zn(ch3coo)2·
2h2o水溶液的浓度为 0.1~2mol/l,所述ch3coonh4的浓度为1~4mol/l。
38.进一步地,在所述步骤s4中,所述n2载气的流速为10~80l/h,沉积时间为10~60s。
39.进一步地,在所述步骤s4中,所述界面层为1~100nm。
40.一种基于n掺杂zno人工电解质界面膜修饰硬碳负极,使用上述的制备方法制得所述基于n掺杂zno人工电解质界面膜修饰硬碳负极。
41.所述基于n掺杂zno人工电解质界面膜修饰硬碳负极的平均体积粒径d50 一般为3~20μm,比表面积为2~30m2/g,放电容量为550mah/g以上,首次充放电效率为72%以上。
42.实施例1
43.s1、将4g稻壳纤维置于质量比为1:1的去离子水和乙醇的混合溶液中洗涤,除去表面灰尘和杂质,在80℃下干燥6h;取出干燥后的稻壳纤维,置于200ml 浓度为1mol/l的naoh溶液中,在80℃下搅拌4h,除去表面胶质等组分,搅拌结束后,用去离子水洗涤稻壳纤维至中性;将收集到的稻壳纤维置于100ml 浓度为0.1mol/l的次氯酸钠溶液中,用乙酸调节溶液ph值至4.5,于80℃下搅拌1h,搅拌结束后将处理得到的稻壳纤维置于去离子和乙醇质量比为1:1的溶液中洗涤三次,在80℃下干燥,得到预处理后的稻壳纤维;
44.s2、将预处理后的稻壳纤维在400℃氮气氛围下烧结10h,得到硬碳材料;将硬碳材料通过球磨粉碎至d50=3,按照质量比,硬碳材料:cmc:sp: sbr=94.5:1.5:1.5:2.5制成水基浆料,将得到的浆料涂在铜箔上,于100℃的真空干燥箱中干燥12h,得到硬碳材料负极;
45.s3、将100ml 0.46mol/l的zn(ch3coo)2·
2h2o水溶液与150ml 1.5mol/l 的ch3coonh4混合均匀,得到涂膜液;
46.s4、将得到的硬碳材料负极加热至300℃,然后通过超声雾化器将前驱体涂膜液雾化,通过n2载气送去薄膜生长室,n2流速为10l/h,沉积时间为60s,在加热的硬碳材料负极表面发生热解反应生成n掺杂zno薄膜,喷咀到沉底表面距离为10cm,保温时间10min,在硬碳负极表面形成8nm的界面层,即得到 n掺杂zno人工电解质界面膜修饰的硬碳负极。
47.s5、将得到的人工电解质界面膜修饰的硬碳负极作为扣式电池负极,正极采用金属锂片,电解液为1mol/l lipf6/ec+dec(1:1),装配成cr2032扣式电池。电池测试采用蓝电电池测试系统,测试方法采用恒流充放电,在c/10电流密度下进行充放电测试。在放电截止电压为0v,充电截止电压为2.5v的条件下,测试结果如表1所示。
48.实施例2
49.s1、将4g麦秸纤维置于质量比为1:1的去离子水和乙醇的混合溶液中洗涤,除去表面灰尘和杂质,在80℃下干燥6h;取出干燥后的麦秸纤维,置于200ml 浓度为0.1mol/l的naoh溶液中,在80℃下搅拌4h,除去表面胶质等组分,搅拌结束后,用去离子水洗涤麦秸纤维至中性;将收集到的麦秸纤维置于100ml 浓度为1mol/l的高氯酸钠溶液中,用乙酸调节溶液ph值至4.5,于80℃下搅拌1h,搅拌结束后将处理得到的麦秸纤维置于去离子和乙醇质量比为1:1的溶液中洗涤三次,在80℃下干燥,得到预处理后的麦秸纤维;
50.s2、将预处理后的麦秸纤维在1500℃氦气氛围下烧结0.5h,得到硬碳材料;将硬碳材料通过机械磨粉碎至d50=20,按照质量比,硬碳材料:cmc:sp: sbr=94.5:1.5:1.5:2.5制成水基浆料,将得到的浆料涂在铜箔上,于100℃的真空干燥箱中干燥12h,得到硬碳材料负极;
51.s3、将100ml 0.61mol/l的zn(ch3coo)2·
2h2o水溶液与150ml 2mol/l的 ch3coonh4混合均匀,得到涂膜液;
52.s4、将得到的硬碳材料负极加热至500℃,然后通过超声雾化器将前驱体涂膜液雾化,通过n2载气送去薄膜生长室,n2流速为80l/h,沉积时间为10s,在加热的硬碳材料负极表面发生热解反应生成n掺杂zno薄膜,喷咀到沉底表面距离为10cm,保温时间10min,在硬碳负极表面形成15nm的界面层,即得到n掺杂zno人工电解质界面膜修饰的硬碳负极。
53.s5、将得到的人工电解质界面膜修饰的硬碳负极作为扣式电池负极,正极采用金
属锂片,电解液为1mol/l lipf6/ec+dec(1:1),装配成cr2032扣式电池。电池测试采用蓝电电池测试系统,测试方法采用恒流充放电,在c/10电流密度下进行充放电测试。在放电截止电压为0v,充电截止电压为2.5v的条件下,测试结果如表1所示。
54.实施例3
55.s1、将4g玉米秸秆纤维置于质量比为1:1的去离子水和乙醇的混合溶液中洗涤,除去表面灰尘和杂质,在80℃下干燥6h;取出干燥后的玉米秸秆纤维,置于200ml浓度为0.5mol/l的naoh溶液中,在80℃下搅拌4h,除去表面胶质等组分,搅拌结束后,用去离子水洗涤玉米秸秆纤维至中性;将收集到的玉米秸秆纤维置于100ml浓度为0.5mol/l的亚氯酸钠溶液中,用乙酸调节溶液ph 值至4.5,于80℃下搅拌1h,搅拌结束后将处理得到的玉米秸秆纤维置于去离子和乙醇质量比为1:1的溶液中洗涤三次,在80℃下干燥,得到预处理后的玉米秸秆纤维;
56.s2、将预处理后的玉米秸秆纤维在1000℃氩气氛围下烧结10h,得到硬碳材料;将硬碳材料通过机械磨粉碎至d50=20,按照质量比,硬碳材料:cmc: sp:sbr=94.5:1.5:1.5:2.5制成水基浆料,将得到的浆料涂在铜箔上,于100℃的真空干燥箱中干燥12h,得到硬碳材料负极;
57.s3、将100ml 0.3mol/l的zn(ch3coo)2·
2h2o水溶液与150ml 1mol/l的 ch3coonh4混合均匀,得到涂膜液;
58.s4、将得到的硬碳材料负极加热至400℃,然后通过超声雾化器将前驱体涂膜液雾化,通过n2载气送去薄膜生长室,n2流速为80l/h,沉积时间为60s,在加热的硬碳材料负极表面发生热解反应生成n掺杂zno薄膜,喷咀到沉底表面距离为10cm,保温时间10min,在硬碳负极表面形成100nm的界面层,即得到n掺杂zno人工电解质界面膜修饰的硬碳负极。
59.s5、将得到的人工电解质界面膜修饰的硬碳负极作为扣式电池负极,正极采用金属锂片,电解液为1mol/l lipf6/ec+dec(1:1),装配成cr2032扣式电池。电池测试采用蓝电电池测试系统,测试方法采用恒流充放电,在c/10电流密度下进行充放电测试。在放电截止电压为0v,充电截止电压为2.5v的条件下,测试结果如表1所示。
60.实施例4
61.s1、将4g玉米秸秆纤维置于质量比为1:1的去离子水和乙醇的混合溶液中洗涤,除去表面灰尘和杂质,在80℃下干燥6h;取出干燥后的玉米秸秆纤维,置于200ml浓度为1mol/l的naoh溶液中,在80℃下搅拌4h,除去表面胶质等组分,搅拌结束后,用去离子水洗涤玉米秸秆纤维至中性;将收集到的玉米秸秆纤维置于100ml浓度为0.5mol/l的次氯酸钠溶液中,用乙酸调节溶液ph 值至4.5,于80℃下搅拌1h,搅拌结束后将处理得到的玉米秸秆纤维置于去离子和乙醇质量比为1:1的溶液中洗涤三次,在80℃下干燥,得到预处理后的玉米秸秆纤维;
62.s2、将预处理后的玉米秸秆纤维在1300℃氩气氛围下烧结8h,得到硬碳材料;将硬碳材料通过气流磨粉碎至d50=10,按照质量比,硬碳材料:cmc:sp: sbr=94.5:1.5:1.5:2.5制成水基浆料,将得到的浆料涂在铜箔上,于100℃的真空干燥箱中干燥12h,得到硬碳材料负极;
63.s3、将100ml 0.325mol/l的zn(ch3coo)2·
2h2o水溶液与150ml 0.5mol/l 的ch3coonh4混合均匀,得到涂膜液;
64.s4、将得到的硬碳材料负极加热至400℃,然后通过超声雾化器将前驱体涂膜液雾化,通过n2载气送去薄膜生长室,n2流速为10l/h,沉积时间为10s,在加热的硬碳材料负极表面发生热解反应生成n掺杂zno薄膜,喷咀到沉底表面距离为10cm,保温时间10min,在硬碳负极表面形成1nm的界面层,即得到 n掺杂zno人工电解质界面膜修饰的硬碳负极。
65.s5、将得到的人工电解质界面膜修饰的硬碳负极作为扣式电池负极,正极采用金属锂片,电解液为1mol/l lipf6/ec+dec(1:1),装配成cr2032扣式电池。电池测试采用蓝电电池测试系统,测试方法采用恒流充放电,在c/10电流密度下进行充放电测试。在放电截止电压为0v,充电截止电压为2.5v的条件下,测试结果如表1所示。
66.实施例5
67.s1、将4g玉米秸秆纤维置于质量比为1:1的去离子水和乙醇的混合溶液中洗涤,除去表面灰尘和杂质,在80℃下干燥6h;取出干燥后的玉米秸秆纤维,置于200ml浓度为1mol/l的naoh溶液中,在80℃下搅拌4h,除去表面胶质等组分,搅拌结束后,用去离子水洗涤玉米秸秆纤维至中性;将收集到的玉米秸秆纤维置于100ml浓度为0.5mol/l的次氯酸钠溶液中,用乙酸调节溶液ph 值至4.5,于80℃下搅拌1h,搅拌结束后将处理得到的玉米秸秆纤维置于去离子和乙醇质量比为1:1的溶液中洗涤三次,在80℃下干燥,得到预处理后的玉米秸秆纤维;
68.s2、将预处理后的玉米秸秆纤维在1300℃氩气氛围下烧结8h,得到硬碳材料;将硬碳材料通过气流磨粉碎至d50=10,按照质量比,硬碳材料:cmc:sp: sbr=94.5:1.5:1.5:2.5制成水基浆料,将得到的浆料涂在铜箔上,于100℃的真空干燥箱中干燥12h,得到硬碳材料负极;
69.s3、将100ml 1.95mol/l的zn(ch3coo)2·
2h2o水溶液与150ml 3mol/l的 ch3coonh4混合均匀,得到涂膜液;
70.s4、将得到的硬碳材料负极加热至400℃,然后通过超声雾化器将前驱体涂膜液雾化,通过n2载气送去薄膜生长室,n2流速为45l/h,沉积时间为30s,在加热的硬碳材料负极表面发生热解反应生成n掺杂zno薄膜,喷咀到沉底表面距离为10cm,保温时间10min,在硬碳负极表面形成30nm的界面层,即得到n掺杂zno人工电解质界面膜修饰的硬碳负极。
71.s5、将得到的人工电解质界面膜修饰的硬碳负极作为扣式电池负极,正极采用金属锂片,电解液为1mol/l lipf6/ec+dec(1:1),装配成cr2032扣式电池。电池测试采用蓝电电池测试系统,测试方法采用恒流充放电,在c/10电流密度下进行充放电测试。在放电截止电压为0v,充电截止电压为2.5v的条件下,测试结果如表1所示。
72.实施例6
73.s1、将4g玉米秸秆纤维置于质量比为1:1的去离子水和乙醇的混合溶液中洗涤,除去表面灰尘和杂质,在80℃下干燥6h;取出干燥后的玉米秸秆纤维,置于200ml浓度为1mol/l的naoh溶液中,在80℃下搅拌4h,除去表面胶质等组分,搅拌结束后,用去离子水洗涤玉米秸秆纤维至中性;将收集到的玉米秸秆纤维置于100ml浓度为0.5mol/l的次氯酸钠溶液中,用乙酸调节溶液ph 值至4.5,于80℃下搅拌1h,搅拌结束后将处理得到的玉米秸秆纤维置于去离子和乙醇质量比为1:1的溶液中洗涤三次,在80℃下干燥,得到预处理后的玉米秸秆纤维;
74.s2、将预处理后的玉米秸秆纤维在1300℃氩气氛围下烧结8h,得到硬碳材料;将硬
碳材料通过气流磨粉碎至d50=10,按照质量比,硬碳材料:cmc:sp:sbr=94.5:1.5:1.5:2.5制成水基浆料,将得到的浆料涂在铜箔上,于100℃的真空干燥箱中干燥12h,得到硬碳材料负极;
75.s3、将100ml 1.625mol/l的zn(ch3coo)2·
2h2o水溶液与150ml 2.5mol/l 的ch3coonh4混合均匀,得到涂膜液;
76.s4、将得到的硬碳材料负极加热至450℃,然后通过超声雾化器将前驱体涂膜液雾化,通过n2载气送去薄膜生长室,n2流速为45l/h,沉积时间为30s,在加热的硬碳材料负极表面发生热解反应生成n掺杂zno薄膜,喷咀到沉底表面距离为10cm,保温时间10min,在硬碳负极表面形成1nm的界面层,即得到 n掺杂zno人工电解质界面膜修饰的硬碳负极。
77.s5、将得到的人工电解质界面膜修饰的硬碳负极作为扣式电池负极,正极采用金属锂片,电解液为1mol/l lipf6/ec+dec(1:1),装配成cr2032扣式电池。电池测试采用蓝电电池测试系统,测试方法采用恒流充放电,在c/10电流密度下进行充放电测试。在放电截止电压为0v,充电截止电压为2.5v的条件下,测试结果如表1所示。
78.实施例7
79.s1、将4g玉米秸秆纤维置于质量比为1:1的去离子水和乙醇的混合溶液中洗涤,除去表面灰尘和杂质,在80℃下干燥6h;取出干燥后的玉米秸秆纤维,置于200ml浓度为1mol/l的naoh溶液中,在80℃下搅拌4h,除去表面胶质等组分,搅拌结束后,用去离子水洗涤玉米秸秆纤维至中性;将收集到的玉米秸秆纤维置于100ml浓度为0.5mol/l的次氯酸钠溶液中,用乙酸调节溶液ph 值至4.5,于80℃下搅拌1h,搅拌结束后将处理得到的玉米秸秆纤维置于去离子和乙醇质量比为1:1的溶液中洗涤三次,在80℃下干燥,得到预处理后的玉米秸秆纤维;
80.s2、将预处理后的玉米秸秆纤维在1300℃氩气氛围下烧结8h,得到硬碳材料;将硬碳材料通过气流磨粉碎至d50=10,按照质量比,硬碳材料:cmc:sp: sbr=94.5:1.5:1.5:2.5制成水基浆料,将得到的浆料涂在铜箔上,于100℃的真空干燥箱中干燥12h,得到硬碳材料负极;
81.s3、将100ml 1.3mol/l的zn(ch3coo)2·
2h2o水溶液与150ml 2mol/l的ch3coonh4混合均匀,得到涂膜液;
82.s4、将得到的硬碳材料负极加热至450℃,然后通过超声雾化器将前驱体涂膜液雾化,通过n2载气送去薄膜生长室,n2流速为45l/h,沉积时间为30s,在加热的硬碳材料负极表面发生热解反应生成n掺杂zno薄膜,喷咀到沉底表面距离为10cm,保温时间10min,在硬碳负极表面形成20nm的界面层,即得到n掺杂zno人工电解质界面膜修饰的硬碳负极。
83.s5、将得到的人工电解质界面膜修饰的硬碳负极作为扣式电池负极,正极采用金属锂片,电解液为1mol/l lipf6/ec+dec(1:1),装配成cr2032扣式电池。电池测试采用蓝电电池测试系统,测试方法采用恒流充放电,在c/10电流密度下进行充放电测试。在放电截止电压为0v,充电截止电压为2.5v的条件下,测试结果如表1所示。
84.对比例1
85.s1、将4g玉米秸秆纤维置于质量比为1:1的去离子水和乙醇的混合溶液中洗涤,除去表面灰尘和杂质,在80℃下干燥6h;取出干燥后的玉米秸秆纤维,置于200ml浓度为1mol/l的naoh溶液中,在80℃下搅拌4h,除去表面胶质等组分,搅拌结束后,用去离子水洗涤玉米
秸秆纤维至中性;将收集到的玉米秸秆纤维置于100ml浓度为0.5mol/l的次氯酸钠溶液中,用乙酸调节溶液ph 值至4.5,于80℃下搅拌1h,搅拌结束后将处理得到的玉米秸秆纤维置于去离子和乙醇质量比为1:1的溶液中洗涤三次,在80℃下干燥,得到预处理后的玉米秸秆纤维;
86.s2、将预处理后的玉米秸秆纤维在1300℃氩气氛围下烧结8h,得到硬碳材料;将硬碳材料通过气流磨粉碎至d50=10,按照质量比,硬碳材料:cmc:sp:sbr=94.5:1.5:1.5:2.5制成水基浆料,将得到的浆料涂在铜箔上,于100℃的真空干燥箱中干燥12h,得到硬碳材料负极;
87.s3、将得到的硬碳负极作为扣式电池负极,正极采用金属锂片,电解液为 1mol/l lipf6/ec+dec(1:1),装配成cr2032扣式电池。电池测试采用蓝电电池测试系统,测试方法采用恒流充放电,在c/10电流密度下进行充放电测试。在放电截止电压为0v,充电截止电压为2.5v的条件下,测试结果如表1所示。
88.表1包含采用实施例1~7的方法制备的材料和对比例1制备的材料的扣式电池的电性能测试结果
89.样品可逆比容量(mah/g)首效(%)实施例155877实施例253180实施例357071实施例447062实施例557585实施例658382实施例759881对比例143248
90.对于本领域技术人员而言,显然本发明不限于上述示范性实施例的细节,而且在不背离本发明的精神或基本特征的情况下,能够以其他的具体形式实现本发明。因此,无论从哪一点来看,均应将实施例看作是示范性的,而且是非限制性的,本发明的范围由所附权利要求而不是上述说明限定,因此旨在将落在权利要求的等同要件的含义和范围内的所有变化囊括在本发明内。
91.此外,应当理解,虽然本说明书按照实施方式加以描述,但并非每个实施方式仅包含一个独立的技术方案,说明书的这种叙述方式仅仅是为清楚起见,本领域技术人员应当将说明书作为一个整体,各实施例中的技术方案也可以经适当组合,形成本领域技术人员可以理解的其他实施方式。