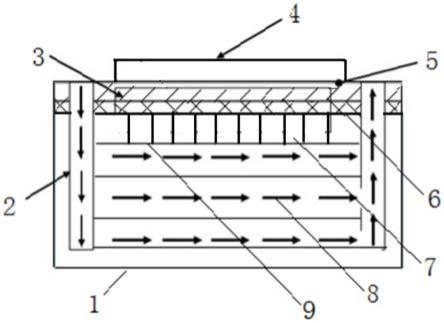
热管控微流道ltcc-m封装基板及其制造方法
技术领域
1.本发明涉及微波、毫米波应用领域,广泛应用在ltcc的系统级封装(sip)中实现高密度集成的微系统。具体涉及一种热管控微流道ltcc-m封装基板及其制造工艺方法。
背景技术:2.低温共烧陶瓷(ltcc)性能优良,是现代微电子封装中的重要组成部分,不仅在微波、毫米波应用领域具有广泛的应用。而且广泛应用于高速,高频系统中。ltcc多层基板技术可以制做多达几十层电路基板,ltcc基板可内植(埋)无源元件,能将部分无源元件集成到基板中,有利于系统的小型化,提高电路的组装密度和系统的可靠性。由于低温共烧陶瓷ltcc基板具有布线层数高、布线导体方阻小、介电常数低、烧结温度低等优点,可以将多个不同功能、不同功率、不同频率的芯片封装在一起,还可以实现无源元件的集成,并将多个电阻器、电容器和电感器等埋置在基板内部,使得基板表面腾出了大量空间用来组装其他元器件。在基于ltcc的系统级封装(sip)应用中可实现高密度集成的微系统,成为陶瓷单片集成系统的可行实现方案。因此ltcc被大量应用于电子装备中。然而,ltcc的热导率较差,导致了ltcc基板集成功率器件工作产生的热量不能快速及时散出,成为限制ltcc在高功率微波组件以及多功能微系统中应用的薄弱点。而且随着电子装备的快速发展,呈现出尺寸微型化、结构复杂化、组装密度高、功率大等特征,高密度三维集成功率模块热流密度的急剧增加,带来了新的更加严峻的热管控问题。
3.ltcc基板虽然能充分发挥大规模集成电路和高速集成电路的性能优势,使混合集成电路集成度更高,实现混合大规模集成电路(hlsi)。但ltcc为玻璃/陶瓷制品,其实际抗折强度一般<200mpa,抗机械冲击能力不是很大,在稍大的冲击下基板易出现裂纹或发生断裂,使电路失效。由于ltcc的导热率偏小,一般为2~3w/(m
·
k)。当电路中存在功率元器件时,基板导热慢,很容易引起模块内温度升高,引起或加快元器件的失效。若将ltcc与金属结合,做成ltcc/金属复合基板(简称ltcc-m),则可充分发挥ltcc的优势。目前实现ltcc与金属基片结合的方式是先在ltcc待结合面金属化,然后与金属基片进行焊接(一般采用ausn焊接)。这种方式的焊接可靠性不很稳定,另外成本较高,后道工作温度受限制。
4.随着现代通信的不断进步和微电子产业的迅速发展,电子产品逐渐趋向于小型化和高密度化,其封装密度也不断地提高,对于散热要求也日益增高,而传统的风冷技术对于高热密度芯片的散热不够理想,相比之下微流道散热器则具有更好的散热效果。用单配微流道的方式可以有效地将热量进行传递。但是传统的ltcc基板内置单层微流道并不能有效地将ltcc基板上热源产生的热量转移,这是因为ltcc基板的热导率很低,而热源一般存在于基板表面,热源产生的热量很难通过高热阻的ltcc基板传递到基板内部流体中。不仅对典型发热的功率器件工作温度的降低变得困难,而且由于传统的ltcc基板单层微流道结构存在自身的缺陷,会导致散热不均匀,因而很难达到sip封装组件温度均匀性要求。此外,使用传统ltcc基板,其抗折、抗机械冲击能力弱,在较大的载荷冲击下基板易出现裂纹或发生断裂失效。因而如何提高新型ltcc基板微流道的成型质量成为了难题。例如:如何对内嵌微
结构的陶瓷-金属梯度功能界面层进行优化调控、如何构建低热阻高可靠的热界面、如何解决ltcc基板内微流道层数多了之后,微流道管壁出现粗糙、塌陷、堵塞、基板翘曲、应力大等缺陷问题。成为了解决ltcc基板微流道在某sip组件上应用的技术难题。比如,某功率模块,由于存在大量的sip封装组件(发射部分有200个sip封装组件,接收部分有900个sip封装组件,总功率为900w。仅以发射部分200个sip封装组件进行计算,其总功率为500w,单个芯片面积为2
×
1mm2,功率为2.5w,热流密度为125w/cm2),导致了组装密度增大,散热问题突出,这将不可避免地导致其功率密度和热流密度大幅度提高,从而引起芯片结温升高,导致功率mmic可靠性降低,严重的会造成失效、烧毁等严重后果。同时,高功率负载带了工作温度的大幅度增加,热管控成为了不能忽视的重要问题,一方面需要将芯片温度控制在正常工作范围,以提高sip封装组件的增益;另一方面需要保证成百上千个sip封装组件(包含发射、接收部分)在相同的温度条件下,保证相位一致。
5.ltcc材料自身的导热系数较低,仅为3w/(m
·
k)。因此,在ltcc微流道平台下散热需面临一个功率芯片热量如何传导至微流结构中的问题。ltcc基板制造及性能控制,影响因素很多,较为复杂。主要体现为叠片层压和烧结过程中,特别是层压阶段微流道结构需要充分保护,以避免其被压裂而导致结构破坏或整个基板的断裂。大面积、多层ltcc基板,烧结收缩率一致性对其成品率、产品性能影响很大。制造ltcc基板关键技术之一是烧结收缩率控制。基板的烧结收缩率主要是通过控制影响烧结收缩率的各个因素来控制,影响烧结收缩率的主要因素有粉料的颗粒度、流延黏合剂的比例、热压叠片的压力和烧结曲线等。
6.ltcc基板平整性遭遇破坏对整个基板其他性能(如传感器、rf信号收发)造成不利影响,也影响整个单片系统的可靠性。尽管ltcc具有诸多优点,但是任何事物都不是完美的,ltcc也具有一些缺点:一是控制收缩率问题。收缩率控制是影响ltcc埋置器件可靠性的最主要因素之一,大面积、多层ltcc基板,烧结收缩率一致性对其成品率、产品性能影响很大。基板的烧结收缩率主要是通过控制影响烧结收缩率的各个因素来控制,影响烧结收缩率的主要因素有粉料的颗粒度、流延黏合剂的比例、热压叠片的压力和烧结曲线等。在多层ltcc烧结的时候,生瓷带在水平x、y方向上的收缩率一般为12.2%到16%,误差大约为0.2%左右。在厚度z方向上收缩率通常大约为15.3%到25%,收缩率误差0.5%左右。金属布线的宽度和间距非常细小,可以小到几十微米,在烧结时层与层之间不能有过大的错位和变形,否则可能使导电金线不能对准、不能连结,造成电路的断路或短路,严重影响模块的性能,甚至使模块丧失该有的功能。为了控制收缩率问题,目前主要有几种工艺方法:自约束烧结法(scs)、压力辅助烧结法(pas)、无压力辅助烧结法(plas)、复合板共同压烧法。二是腔室塌陷问题。ltcc基板表面和内部有很多用来埋置元器件的腔室,在叠片、层压、烧结过程中,腔室可能塌陷,使元器件收到损伤。ltcc基板的平整度也会遭到破坏,影响模块的其他性能,比如传感器的精度、rf收发的性能。对于ltcc基板微流道散热来说,内部槽道尺寸相对较大,更容易发生塌陷,甚至基板局部断裂,气密性不够将可能引起渗液,整个ltcc模块遭到破坏,整个系统的可靠性也降低了。四是在基板绝对面积较大的同时因i/o数量多、组装效率高而造成单位面积基板上的外引线数很多,使其封装面临着减小外形尺寸、提高封装效率、保证i/o数量的难题。验调整排胶阶段开益速、时间,院结阶段开益速、时间,合所段至气重守里安工乙参数。ltcc基板的结构也是决定ltcc基板烧结翘曲度的关键因素,当ltcc基板上存在
多种规格的空腔结构时,其结构难以均衡对称,同时由于ltcc基板上含有大量通孔及密集金属导线,这些都难以均匀分布,这样就容易导致其翘曲度超差。
7.保护基板表面盲腔通常用嵌件的方法,在叠片阶段把嵌件填放在腔室内,待烧结后取出;但是对于基板内部的腔室和微流道来说,烧结后嵌件是无法取出的,这种情况一般用牺牲层法,填充的牺牲层在烧结过程中会分解为气体排出。三是机械强度问题。ltcc是脆性材料,拉伸强度和弯曲强度都较低,受力易断裂,机械强度较差,抗挠强度为117-180mpa,远低于al2o3的抗挠强度75~345mpa。当局部温度过高时,产生的热变形时基板挠曲度增大,影响基板整度,使模块性能变差。所以在热设计阶段有必要考虑ltcc基板的热变形。金属具有强度高,韧性好、导热导电性能好等优点,但高温耐腐蚀性差。陶瓷材料具有耐高温,抗腐蚀等特点,却脆性大因由于两者界面的膨胀系数不同,在粘合时往往会产生很大的热应力,引起剥离、脱落和耐热性能的降低,造成材料的破坏。
8.随着电子产品小型化、高性能化和多功能化的发展,封装密度不断提高,单位面积的功耗持续增加,导致封装体的温度越来越高。温度过高不仅使得芯片的工作性能降低、器件烧毁、连线断裂,而且会因温差过大而导致封装体结构断裂和芯片脱落等问题。实际研究中发现,基于ltcc基板的微流道并没有达到金属或者合金微流道的散热效果,这是因为ltcc的导热率很低,只有2~5w/m
·
k,这导致芯片外壳与流固耦合面之间的传导热阻较大,热量无法被液体带走。传统的ltcc陶瓷-金属复合材料在两相界面上存在物理性能的失配问题,由于复合材料中陶瓷和金属间热膨胀系数的差异,在服役环境下,特别是极高温下,由于两者界面的膨胀系数不同,在粘合时往往会大的热应力,引起刺离、脱落和耐执性能的降低,造成材料的破坏。因此在温度载荷作用下层间易产生应力集中而出现脱层现象,或者在界面上萌生裂纹而削弱材料的性能,会有残余应力产生。造成材料的破坏,所以散热已成为制约芯片封装的核心问题。而对各种严峻、苛刻的使用环境,一种新型的功能材料-梯度功能材料fgm应运而生。fgm要求构成材料的要素(组成、结构等)在集合空间内连续变化,从而得到性能在几何空间上连续变化的非匀质材料。梯度功能材料(fgm)是组成、结构及孔隙率等要素在材料的某个方向上和结构呈连续梯度变化或阶梯变化,从而使材料的性质和功能也呈连续变化或阶梯变化的一种非均质复合材料。这种非均匀的复合材料可以把各组原材料的不同性能融于一体,具有耐执和执应力缓释功能。
9.ltcc基板多层微流道腔体在工艺制造过程中经过高压等静压层压和共烧两道工序后,产生变形无可避免。这主要是由于新型ltcc多层基板的等静压层压工艺一般是在约21mpa、70℃水温下加压9min,使新型ltcc多层基板热压形成叠层基板,导致新型ltcc基板材料特性温度曲线不匹配共烧产生腔体变形和容腔错位形貌结,容腔错位主要是由共烧过程产生的残余热应力和后烧过程产生的热应力应变导致。由于采用印刷机丝网印刷,要求碳黑的颗粒度达微米级,因此实际加工过程中需要对大颗粒的碳黑需进行球磨,但是依然存着印刷过程中的扩散,因为每个芯片下方布置的流道,流道中冷液在靠近主流道位置支流道是进口,到中间位置时,流体已经吸收大量热量而被加热,流体温度升高会增大对流换热热阻,降低对流换热系数。
技术实现要素:10.本发明的目的是针对现有技术存在的不足之处,为了尽快满足某sip高密度三维
集成功率模块热流密度急剧增加对快速高效热管控的需求,提供一种散热均匀,对流热换效率高,能有效提升散热能力,降低散热通道热阻且可显著提升ltcc基板微流道抵抗弯折、机械冲击能力的热管控微流道ltcc-m封装基板微流道结构及其制造工艺方法。
11.本发明的上述目的可以通过下述技术方案予以实现:一种热管控微流道ltcc-m封装基板,包括:设置在ltcc/金属复合基板1面上的热源4、金属层3和位于热源4两边的入口及出口,连通所述入口及出口的水泵流道2,向下垂直连通入口及出口并与水泵管路形成双向垂直平行循环微流道的微流道拓扑结构,其特征在于:在热源4的下方金属层3的ltcc衬底中设有内嵌芯片的芯片传热通道5,并且在所述芯片传热通道5的下方设有与双向平行多层微流道8之间的热通道方向上,设有道金属层3热换流道复合为一体的水平对流热换且直线平行并列在金属结构盲腔中的多层微流道单元8,固联在梯度功能fgm材料界面隔离层6且内嵌于ltcc陶瓷层9腔体中的阵列导热金属微柱7,从而形成金属层3通过热换流道fgm材料界面隔离层6梯度热换功能界面-阵列金属微柱7-多层微流道单元8-ltcc陶瓷层9陶瓷界面-层层互联,液冷流道、传热通道热界面对流热换的热管控单元,液冷流道、传热通道热界面对流热换的热管控单元。
12.一种制造热管控微流道ltcc-m封装基板的工艺方法,所述工艺方法在生瓷流延、打孔、叠片层压之后,从热膨胀系数、弹性模量、热导率匹配方面进行材料选择,从厚度、尺寸、布局参数进行界面匹配结构设计,从印刷fgm的压力、速度、金属层喷涂温度、速度工艺参数进行fgm功能层的设计,然后根据材料的物性参数和梯度成分的分布函数进行温度分布和热应力计算,求出应力强度比达到最小值的成分组合体系和梯度分布,通过对ltcc基板表层的fgm的材料印刷,固化工艺后,完成fgm功能层的固化,之后在fgm表面涂敷金属金属材料,涂敷之后,将ltcc基板一起进行烧结,形成金属-fgm-陶瓷界面;采用ferro a6m体系的ltcc材料作为射频功能层多层基板介质,通过ltcc多层制作工艺、内嵌金属微结构陶瓷-金属界面集成工艺以及微流道成型工艺,实现ltcc基板内嵌金属微结构的多层微流道集成制造;ltcc基板层间的高精度对位依靠无膜工艺实现,构建陶瓷-金属界面,选取热膨胀系数与ltcc陶瓷想接近的cumocu作为ltcc基板金属层,通过中间层-梯度功能界面层与金属层、ltcc相近的热膨胀系数的ltcc陶瓷层实现界面结合,采用烧结温度大于850℃,与金属层、ltcc基板和ltcc陶瓷层共烧的梯度功能界面层材料,使ltccltcc陶瓷层与金属层通过梯度功能界面层的作用下紧密结合,ltcc基板多层微流道腔体在工艺制造过程中经过高压、等静压层压和共烧两道工序后,在大于21mpa、70℃水温下加压至少10min,使ltcc多层基板热压形成叠层基板;在600~850℃时对腔体的三维结构支撑作用下,采用碳黑膏这种颗粒度达微米级的牺牲材料,制作满足印刷机丝网印刷方案要求的图形掩膜板,填充材料填入空腔,多次印刷烘干到所需填充高度后烧结,对大颗粒的碳黑进行球磨,控制碳基牺牲材料埋置腔的缺陷,将共烧后的基板在后烧前增加退火处理的步骤,将基板退火处理后,再进行后烧过程。
13.本发明相比于现有技术,具有如下有益效果:本发明在低温共烧多层陶瓷(ltcc)基板在芯片与双向平行循环微流道之间的热通道方向上,设置对流热换流道的金属层3、水平对流热换且直线平行并列在金属结构盲腔中的多层微流道单元8和内嵌金属微柱阵列的金属-梯度功能界面材料fgm-对比材料之间的扩散到陶瓷界面ltcc陶瓷层4,确保了层间的连续性,利用功能梯度材料(fgm)实现材料
的两侧具有不同的功能,同时克服了不同材料结合部位的性能不匹配的缺陷。由于fgm组成和性能与传统材料具有很大的差异,热学性能和力学性能沿某一方向连续变化以及功能的多样性,与传统ltcc基板微流道对比,证明了可以增加向流体换热的面积,可以有效提升散热能力和散热均匀性,提高对流热换效率。利用fgm具有极好的金属基体界面相容性和高的柔韧性、可靠性和梯度功能性,可防止微裂纹的产生,消除剥落现象,避免其被压裂而导致结构破坏或整个基板的断裂。水平对流热换且直线平行并列在金属结构盲腔中的多层微流道单元8和内嵌金属微柱阵列的金属-梯度功能界面材料fgm-陶瓷界面ltcc陶瓷层,可避免微流道管壁出现粗糙、塌陷、堵塞、基板翘曲、应力大等缺陷问题。通过ltcc下层基板在微流道中制造高密度的导热通孔通道,所设计的散热结构可以有效地改进ltcc微流道平台下热源区域散热面临功率芯片热量如何传导至微流结构中的这一问题,温度值会随着加载散热流量的增加而逐渐降低。同时解决了ltcc基板内微流道层数多了之后,微流道管壁出现粗糙、塌陷、堵塞、基板翘曲、应力大等缺陷问题。同时保证了成百上千个sip封装组件在相同的温度条件下相位的一致。通过流过内嵌在ltcc基板内、发热芯片下方的导热微柱来进行热传导,通过外界的热交换系统进行散热,提高了对流换热系数,内嵌金属微柱的热传导散热明显高于传统新型ltcc的热扩散散热。
14.本发明为足某sip高密度三维集成功率模块热流密度急剧增加对快速高效热管控的需求,采用ltcc基板内嵌金属微结构多层微流道结构及ltcc基板金属微柱阵列及梯度功能界面层层互联,形成芯片-金属层-梯度功能界面层-内嵌阵列微柱-液冷流道的传热通道和芯片-的新型热界面,可以增加与流体换热的面积,该阵列与腔体及梯度功能界面层互联,形成芯片-金属层-梯度功能界面层-内嵌阵列微柱-液冷流道的传热通道,达到有效热管控的目的。而且金属层、梯度功能界面层的应用,可以显著提升ltcc基板微流道抵抗弯折、机械冲击能力。由于ltcc基板在芯片传热路径上嵌入了金属层、梯度功能界面层,显著提升了ltcc基板微流道抵抗弯折、机械冲击能力。内嵌金属微结构和具备高效传热的多层微流道,可以确保900多个sip封装组件稳定的热管控能力。
15.本发明通过在ltcc基板芯片与微流道之间的热通道方向上设计金属层、梯度功能界面层和内嵌金属微柱阵列的ltcc陶瓷层。其中,梯度功能界面材料(fgm)既解决了复合材料的界面应力问题,同时又保持了材料的复合特性。而fgm通过逐渐地改变材料成分的体积分数而使其在界面上不产生突变。fgm能在极高温度梯度下工作,且能保持其构件的结构完整性,减小了热应力、残余应力以及应力集中系数,从而消除了界面问题并使应力分布平缓。因此,金属/陶瓷fgm既能够充分发挥陶瓷良好的耐高温、抗腐蚀和金属的强度高、韧性好的特点,又能很好地解决金属和陶瓷之间热膨胀系数不匹配的问题。芯片产生的热量可以通过金属层等快速、高效传递至液冷通道内。降低了散热通道热阻,达到有效热管控的目的。而且金属层、梯度功能界面层的应用,可以显著提升ltcc基板微流道抵抗弯折、机械冲击能力。
16.本发明针对ltcc基板微流道关键工艺难度,根据微流道散热交换系统结构,结合ltcc工艺水平的限制从热源到多层微流道金属通孔的排列分布、多层微流道结构及其流道腔体结构、流体流速和流道压强以及形状变形等方面,对热源到热通道流道的结构进行仿真,得出其导热微柱和流道腔体结构尺寸分布。通过内嵌金属微结构的多层微流道ltcc集成制造技术途径,主要解决多层ltcc基板层间对位、内嵌金属微结构陶瓷-金属界面集成制
造以及ltcc基板多层微流道成型等技术难题。通过在ltcc基板内嵌芯片-金属层对流热换-fgm-ltcc陶瓷层梯度功能界面层-内嵌微柱阵列-液冷流道的传热通道和芯片的热界面工艺设计、ltcc基板内嵌金属微结构多层微流道集成制造工艺以及ltcc基板内嵌金属微结构多层微流道缺陷控制等关键技术上的突破,避免了传统的ltcc陶瓷-金属复合材料在两相界面上存在物理性能的失配问题。通过将微流散热通道集成于ltcc基板内部,特别是在ltcc基板组装的高功率器件下方,可有效改善ltcc基板的散热特性。结合高密度导热通孔技术以及微流道制造技术,实现了局部孔比例高达50%的高密度导热孔制造。测试结果证实,该ltcc微流体系具备不低于50w/c
㎡
的散热能力。可提升ltcc基板在微波功率组件以及ltcc-sip技术领域的应用范围。ltcc基板微流道结构,内嵌金属微结构和具备高效传热的多层微流道,可以确保900多个sip封装组件稳定的热管控能力。并与传统的散热方式进行对比,取得了良好的散热效果。
17.本发明从ltcc/金属复合基板整体考虑,针对ltcc基板微流道结构,分别从内嵌金属微结构陶瓷-金属关键工艺、集成制造关键工艺以及缺陷控制关键工艺,利用金属层有较高的导热率、较好的机械强度和与ltcc相近的热膨胀系数,起到了散热和加固的作用。虽然关于陶瓷-金属界面构建,ltcc陶瓷与金属层很难直接结合,但本发明通过中间层-梯度功能界面层来实现。梯度功能界面层与金属层、ltcc陶瓷层能够实现良好的界面结合。梯度功能界面材料(fgm)与金属层、ltcc陶瓷层共烧(烧结温度约850℃)的梯度功能界面层材料,以连续,逐步的方式逐渐改变成分或结构,改变复合材料的性能,创建连续的梯度,实现内嵌金属微结构陶瓷-金属界面梯度集成制造。fgm与金属层、ltcc基板有相近的热膨胀系数导热,烧结后,具备较高的化学稳定性、热稳定性、机械强度等,能够使ltcc陶瓷层与金属层通过梯度功能界面层的作用下紧密结合,降低陶瓷-金属传热热阻,提高可靠性。层压和烧结时的三维结构支撑;牺牲材料与ltcc基板tce匹配,在烧结时牺牲材料不对腔体造成受压;烧结后易于去除(通过分解或其他方式)。一是降低共烧过程产生的残余应力,二是降低后烧过程出现的热应力。
18.本发明ltcc基板层间的高精度对位依靠无膜工艺实现,因为无膜工艺可以释放较多的应力,从而提高层间对位精度。制作工艺一次烧结成型,印制精度高,可适应大电流及耐高温特性要求,比普通pcb电路基板具有优良的热传导性。较好的温度特性,如较小的热膨胀系数(cte),较小的共振频率温度系数。
19.本发明将微电路或组件的基板作为封装的载体,在基板上直接引出封装的1/0端子并装连封装体的其他部分,使基板与外壳成为一个封装整体,可以较好地解决高密度集成复杂mcm-c的封装难题。
附图说明
20.为了更清楚地说明本实施例中的技术方案,下面将对实施例描述中所需要使用的附图作简要介绍,显而易见地,下面描述中的附图仅仅是本实施例的一些实施例,对于本领域的普通技术人员来讲,在不付出创造性劳动性的前提下,还可以根据这些附图获得其他的附图。
21.图1为本发明热管控微流道ltcc封装基板的示意图。
22.图2是图1内嵌阵列导热金属微柱结构尺寸及其分布的可选实施例示意图;
图3是制造热管控微流道ltcc-m封装基板的工艺流程图;图中:1.ltcc-m封装基板,2.水泵流道,3、金属层,4.热源,5芯片传热通道,6、fgm材料界面隔离层,7.阵列导热金属微柱,8.多层微流道单元,9.ltcc陶瓷层。
23.下面通过附图以及具体实施例对本实施例技术方案做详细的说明。
具体实施方式
24.参阅图1。在以下描述的优选实施例中,一种热管控微流道ltcc-m封装基板,包括:设置在ltcc/金属复合基板1面上的热源4、金属层3和位于热源4两边的入口及出口,连通所述入口及出口的水泵流道2,向下垂直连通入口及出口并与水泵管路形成双向垂直平行循环微流道的微流道拓扑结构,其特征在于:在热源4的下方金属层3的ltcc衬底中设有内嵌芯片的芯片传热通道5,并且在所述芯片传热通道5的下方设有与双向平行多层微流道8之间的热通道方向上,设有道金属层3热换流道复合为一体的水平对流热换且直线平行并列在金属结构盲腔中的多层微流道单元8,固联在梯度功能fgm材料界面隔离层6且内嵌于ltcc陶瓷层9腔体中的阵列导热金属微柱7,从而形成金属层3热换流道通过热换流道fgm材料界面隔离层6梯度热换功能界面-阵列金属微柱7-多层微流道单元8-ltcc陶瓷层9陶瓷界面-层层互联,液冷流道、传热通道热界面对流热换的热管控单元,液冷流道、传热通道热界面对流热换的热管控单元。
25.热源4产生的热量转移,部分集成在金属层3腔体中的无源元件及金属化布线和通孔金属化芯片、叠片借助ltcc盲腔制造中填入的“fgm嵌件”,将ltcc基板上表面热芯片热载荷用来模拟需要散热的热源,通过分子尺度上的扩散相互融合,形成无缝的物体和连续渐变纤维素基材料在界面处分配应力的流变特性,利用高对比度和多维刚度梯度得到多层微流道单元8的热流密度梯度信息;冷却流体从入口流入,沿路经并行支流道分流出口处的主流道,从出口流出。
26.液冷流道冷流在对流热换中,发热芯片及ltcc的热扩散散热通过流过内嵌在fgm材料界面隔离层6下方的阵列导热金属微柱7来进行热传导,芯片产生的热量通过金属层3对流热换流急速冷却及阵列导热金属微柱7下方盲腔中的多层微流道单元8并列流道快速、高效传递至液冷通道内,通过外界的热交换系统进行散热。
27.在可选的实施例中,金属层3的宽边方向制有金属微结构的热换流道,热换流道沿金属层3的宽边方向平行阵列。如图2所示,ltcc陶瓷层9的阵列导热金属微柱7可以采用金浆料制作,参数以及分布可以设计等距间隔节距排列的矩阵排列,或以b为第边,c为腰的等腰三角形,并按45度交叉排列的点状阵列排列矩阵,以及点状线阵间隔形成点状等腰三角形交错混合排列分布的点状阵列排列矩阵。
28.在温度分布和热应力计算中,首先给出随机变量矩母函数m(s)与分布函数一一对应可逆性的条件,然后利用重期望法则,给出相互独立的离散型、连续型随机变量的线性运算、除法、乘积的分布,将系数值带入离散分布函数中,转换为离散累积函数和连续累积函数,再进行微分获得密度函数,推导出它们的分布函数、概率密度函数,得到随机数个相互独立的随机变量之和的矩母函数,对矩母函数求逆即可得到对应的分布函数f(x)=p{x≤x}。其中x是一个随机变量,x是任意实数。
29.随机变量x取0与1两个值,分布律为p{x=k}=p*(1-p)1-k,k=0,1,0《p《1,则称x
服从以p为参数的0-1分布。设随机变量x的所有可能取值为0,1,2,3,
…
,而取各个值的概率为2e-2,则p{x=k}=λke-λ
/k,k=0,1,2,3,...,其中,λ》0是常数,则称x服从参数为λ的泊松分布,记做x~π(λ)。
30.根据目前加工技术和微空腔对于基板性能的影响,为了避免造成基板表层塌陷的设计加工多层微流道结构,按照新型ltcc基板开孔工艺和温度梯度分布设计ltcc基板,热源芯片放置于基板上表面,在基板表面保留四层生瓷片,采用25层生瓷片烧结而成,其中1-4层生瓷片是实心层,主要是埋置一些无源器件和有源器件,5-17是流道层,18-25是出入口调整层,ltcc基板烧结后,ltcc尺寸:长宽(wl)≥60mm,厚度(h)≥8mm,其流道层的每层厚度≥200um。
31.微流道结构采用ansys软件对直插型微流道、阿基米德矩形的螺旋型微流道、蛇型曲线微流道、h型和树型微流道六种常见结构的单层微流道进行建模和仿真,根据不同芯片功率下的不同结构微流道的基板温度分布、流道内流体的速度分布和压强分布进行仿真,预制出ltcc多层微通道截面结构;螺旋型单层微流道结构;蛇型曲线单层微流道结构;根据上述热源热流密度的三维分布,采用有限元仿真方法针对直插型微流道、螺旋型、蛇曲线型3种常见结构,采用顺序耦合法进行模拟计算微流道结构在热疲劳状态下结构受到流热耦合和应力应变状态,根据不同单层微通道多层次互联组合,得出多层微流道腔体的液体流速和芯片功率变化规律,选择直插型微流道、螺旋型、蛇曲线型其中的一种作为微流道结构。
32.为了降低制作成本,提高产品质量和效率,本发明针对ltcc工艺中关键工艺问题,在制造热管控微流道ltcc-m封装基板的工艺中,采用波长为964nm的红外激光在金属层3和fgm材料界面隔离层6打孔,在金属层3切割出沿宽边平行阵列的沟槽,采用激光和机械组合加工方式,先用激光切割机打孔出ltcc/金属复合基板1两侧的水泵流道2,在生瓷带上粗切出多层微通道,再用cnc铣刀将通道精加工出满足流体流动通畅要求的多层微通道结构,并采用自蔓延高温合成法,将构成fgm化合物的元素粉末和金属粉末按梯度组成填充,静成型,放入反应容器,在一端点火燃烧,通过反向前传播,在基体表面形成熔池,合成出沿截面具有成份渐变或晶粒度梯度的层状结构,生成金属间化合物梯度功能材料,制备出强化相呈梯度分布,由反应产物与金属功能材料的fgm。
33.参阅图3。根据本发明,通过流延生成生瓷带共烧等工艺,在ltcc生瓷流延、打孔、叠片层压形成三维结构之后,从热膨胀系数、弹性模量、热导率匹配方面进行材料选择,从厚度、尺寸、布局参数进行界面匹配结构设计,从印刷fgm的压力、速度、金属层喷涂温度、速度工艺参数进行fgm功能层的设计,通过对ltcc基板表层的fgm的材料印刷,基于聚合物的制造材料相结合,促进分子在细丝边界上的扩散并产生连续的梯度,创建多维和连续的刚度梯度,固化工艺后使用热压叠片机在不同的压力及温度下,制成多层生瓷层,经烧结后测出烧结收缩率与热压温度及压力的关系;完成fgm功能层的固化之后在fgm表面涂敷金属金属材料,涂敷之后,将ltcc基板一起进行烧结,形成金属-fgm-陶瓷界面;采用ferro a6m体系的ltcc材料作为射频功能层多层基板介质,通过ltcc多层制作工艺、内嵌金属微结构金属-陶瓷界面集成工艺以及微流道成型工艺,实现ltcc基板内嵌金属微结构的多层微流道集成制造;ltcc基板层间的高精度对位依靠无膜工艺实现,构建金属-陶瓷界面,选取热膨胀系数与ltcc陶瓷接近的cumocu作为金属层复合ltcc基板,通过中间层-fgm梯度功能界面
层与金属层、ltcc相近的热膨胀系数的ltcc陶瓷层实现界面结合,烧结阶段采用烧结温度750℃-850℃、20-25mpa压力,与金属层、ltcc金属层复合基板和ltcc陶瓷层共烧发生结晶和析晶反应,通过优化烧结曲线,优化各阶段气流量,缓解不同材料热膨胀系数不匹配的应力,调整阶段升温速率、时间,烧结阶段升温速率、时间,各阶段空气流量等重要工艺参数,使ltcc陶瓷层与金属层通过梯度功能界面层材料fgm的梯度功能界面层的作用下紧密结合,ltcc金属层复合基板多层微流道腔体在工艺制造过程中经过高压、等静压层压和共烧两道工序后,在大于21mpa、70℃水温下加压至少9min,使ltcc多层基板热压形成叠层基板。
34.在600~800℃时对ltcc金属层复合基板腔体的三维结构支撑作用下,采用碳黑膏这种颗粒度达微米级的牺牲材料,制作满足印刷机丝网印刷方案要求的图形掩膜板,填充材料填入空腔,多次印刷烘干到所需填充高度后烧结,对大颗粒的碳黑进行球磨,控制碳基牺牲材料埋置腔的缺陷,将共烧后的基板在后烧前增加退火处理的步骤,将基板退火处理后,再进行后烧过程和层压。
35.应当理解本实施例以及实施例中的具体特征是对本实施例技术方案的详细的说明,而不是对本实施例技术方案的限定,在不冲突的情况下,本实施例以及实施例中的技术特征可以相互组合。