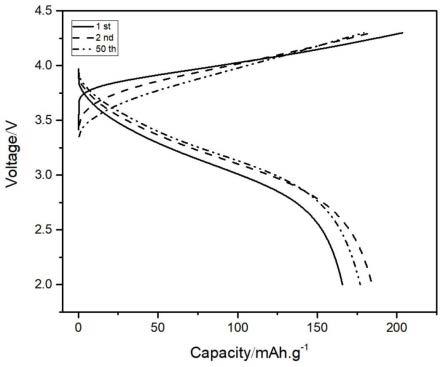
1.本发明属于全固态钠电技术领域,涉及一种复合电解质膜的制备方法及其应用,尤其涉及一种基于钠离子硫化物固态电解质的复合电解质膜的制备及应用。
背景技术:2.近来,锂离子电池被广泛应用于电子移动设备、电动汽车等领域。在锂离子电池中,使用金属锂电极虽然能提高电池的能量密度,但在液态锂电池中使用金属锂会导致锂枝晶的形成,最终造成电池短路,爆炸等危险。因此为了使金属锂电极在锂电池中能够被应用,全固态锂电池得到了广泛的关注以及研究,虽然全固态电解质的使用能抑制锂枝晶的生长,使安全性能显著提高,然而金属锂价格昂贵,使全固态锂电池工业化应用成本过高。为了解决成本过高问题,全固态钠二次电池被提出。金属钠资源丰富,这对于全固态钠二次电池的商业化应用是至关重要的
3.全固态电池使用不可燃的固体电解质代替传统的有机易燃电解液,从根本上避免了安全问题,固态电解质良好的机械性能可以有效地抑制负极枝晶的生长,降低了枝晶生长导致的电池短路问题,很好地提升了电池的寿命。其中,聚合物固态电解质由极性高分子和金属盐络合形成,具有良好的成膜性,可弯曲和高安全性能,但电导率较低,钠离子的迁移数较小,机械性能较差。硫化物固态电解质具有媲美于液态电解质溶液的离子电导率,电化学窗口宽,可适配高压正极材料,但由于硫化物固态电解质不稳定,且用于全固态电池与电极接触较差,导致界面阻抗过大限制了全固态电池大电流充放电。
4.有效的解决方法是通过将两种电解质材料复合,得到复合电解质膜用于全固态电池。传统的方法是将聚合物与无机固态电解质混合,得到复合的电解质,但由于聚合物常温下电导率低下,会在一定程度上降低电解质的电导率,无法形成均匀的钠离子通道,从而影响全固态电池的长循环性能。
5.cn111816910 a公开了一种复合电解质膜用于全固态锂电池。是通过静电纺丝将无机固态电解质与聚合物电解质和有机发泡剂进行静电纺丝,得到复合纤维,然后煅烧去除所述的有机聚合物。同时使所述的有机发泡剂分解发泡,得到无机电解质多孔纤维。该方法成本较高,工艺流程耗时较长,且复合电解质中聚合物含量在20%-99.8%,对复合电解质膜的电导率有一定的影响,且用于全固态电池,其能量密度的短板会限制其在商业上的应用。
技术实现要素:6.本发明的目的在于克服上述现有技术存在的不足,提供一种基于钠离子硫化物固态电解质的复合电解质膜的制备及应用。本发明的复合电解质部分主要成分还是钠离子型硫化物固态电解质,跟较少含量的聚合物电解质复合,聚合物的加入,一方面可以改善电解质的柔性,使其与电极部分接触更好,另一方面能够尽可能保证其用于全固电池时其能量密度不会受到较大影响。并且聚合物的加入可以去填补钠离子型硫化物固态电解质的孔
2min。
24.本发明还涉及一种全固态电池,包括正极部分、负极部分和电解质部分,所述电池的电解质采用所述的复合电解质膜。
25.作为本发明的一个实施方案,所述正极部分由正极活性物质和钠离子型硫化物固态电解质以及导电碳混合构建。正极活性物质为磷酸钒钠、磷酸钛钠、硫酸铁纳、钠离子氟磷酸盐、钠锰氧化物和钠钒氟磷酸盐中的一种。
26.本发明提供的全固态电池制备方法首先制备正极,将正极材料,导电炭黑以及钠离子型硫化物固态电解质按照一定的比例混合,并将其研磨混合均匀。电池组装步骤是将复合固态电解质放置在压片模具中,压制成固态电解质片,之后将正极片放在固态电解质的一侧,并加压力压制,最后在固态电解质的另一侧附上钠片,压制成三明治结构的全固态电池。
27.与现有技术相比本发明具有以下有益效果:
28.1)本发明通过将钠离子型硫化物固态电解质与聚合物电解质复合,改善了其与电极的接触;
29.2)本发明中少量的聚合物加入能够填充钠离子型硫化物固态电解质的孔隙,使电解质部分更加均匀,使钠离子的传输迁移更加顺利。
附图说明
30.通过阅读参照以下附图对非限制性实施例所作的详细描述,本发明的其它特征、目的和优点将会变得更明显:
31.图1为实施例1制备的复合电解质膜的xrd图;
32.图2为实施例1与对比例1循环50圈之后的全固态电池的阻抗图谱对比;
33.图3为实施例1的全电池循环性能图;
34.图4为对比例2的全电池循环性能图。
具体实施方式
35.下面结合实施例对本发明进行详细说明。以下实施例将有助于本领域的技术人员进一步理解本发明,但不以任何形式限制本发明。应当指出的是,对本领域的普通技术人员来说,在不脱离本发明构思的前提下,还可以做出若干调整和改进。这些都属于本发明的保护范围。
36.实施例1
37.将peo与natfsi按照重量比2:8称取,加入15ml超干乙腈中,搅拌8h,最开始先用200rpm缓慢搅拌使其缓慢分散开,再用500rpm的转速搅拌使其混合均匀。然后将钠离子型硫化物固态电解质(na3ps4,5-10μm)加入分散,搅拌均匀,搅拌速率为800rpm,时间为10h。将混合均匀的电解质溶液(其中,natfsi 8%、peo 2%、na3ps
4 90%)加热使其溶剂挥发均匀,温度为60℃,时间为2h。
38.将正极材料(该正极材料可以是na
x
tmo2(x≤1,tm为ni、mn、fe、co、cu等3d过渡金属的一种或几种,本实施例中选用nacoo2)、na3ps4和导电炭黑以及粘结剂sbr以20:75:1:4的比例混合,将其研磨均匀后得到正极粉末。将正极粉末100mg溶解于20mg dme中,磁力搅拌
均匀后涂覆在铝箔上。将复合固态电解质材料放置在压片模具中,压制(压制参数为200-370mpa,30s-2min;本实施例中是在370mpa下压制2min)成固态电解质片,之后将正极片放在固态电解质的一侧,并加压力压制(压制参数为200-370mpa,30s-2min;本实施例中是在200mpa下压制1min),最后在固态电解质的另一侧附上裁好的平整的金属钠片,在50mpa下压制0.5min,压制成全固态电池。
39.图1为实施例1制备的复合电解质膜的xrd图,2θ=30-40之前的宽峰为电介质的特征峰;图3为实施例1的全电池循环性能图。
40.实施例2
41.将paa与natfsi按照重量比2:8称取,加入15ml超干二甲苯中,搅拌8h,最开始先用200rpm缓慢搅拌使其缓慢分散开,再用500rpm的转速搅拌使其混合均匀。然后将钠离子型硫化物固态电解质(na3ps4,5-10μm)加入分散,搅拌均匀,搅拌速率为800rpm,时间为10h。将混合均匀的电解质溶液(其中,natfsi 4%、paa 1%、na3ps495%)加热使其溶剂挥发均匀,温度为60℃,时间为2h。
42.将正极材料(nacoo2)、na3ps4和导电炭黑以及粘结剂sbr以20:75:1:4的比例混合,将其研磨均匀后得到正极粉末。将正极粉末100mg溶解于20mg dme中,磁力搅拌均匀后涂覆在铝箔上。将复合固态电解质材料放置在压片模具中,在370mpa下压制2min,压制成固态电解质片,之后将正极片放在固态电解质的一侧,并加压力在200mpa下压制1min,最后在固态电解质的另一侧附上裁好的平整的钠金属片,在50mpa下压制0.5min,压制成全固态电池。
43.实施例3
44.将pvdf与natfsi按照重量比2:8称取,加入15ml超干乙腈中,搅拌8h,最开始先用200rpm缓慢搅拌使其缓慢分散开,再用500rpm的转速搅拌使其混合均匀。然后将钠离子型硫化物固态电解质(na3ps4,5-10μm)加入分散,搅拌均匀,搅拌速率为800rpm,时间为10h。将混合均匀的电解质溶液(其中,natfsi 2%、pvdf 0.5%、na3ps497.5%)加热使其溶剂挥发均匀,温度为60℃,时间为2h。
45.将正极材料(nacoo2)、钠离子型硫化物固态电解质和导电炭黑以及粘结剂sbr以20:75:1:4的比例混合,将其研磨均匀后得到正极粉末。将正极粉末100mg溶解于20mg dme中,磁力搅拌均匀后涂覆在铝箔上。将复合固态电解质材料放置在压片模具中,在370mpa下压制2min,压制成固态电解质片,之后将正极片放在固态电解质的一侧,并加压力在200mpa下压制1min,最后在固态电解质的另一侧附上裁好的纳金属片,在50mpa下压制0.5min,压制成全固态电池。
46.对比例1
47.不添加peo与钠盐,直接将钠离子型硫化物固态电解质用于全固态电池,其他同实施例1。
48.图2为实施例1与对比例1循环50圈之后的全固态电池的阻抗图谱对比;由图可见,添加peo的界面阻抗更小。
49.对比例2
50.对比例2基本同实施例1,所不同之处在于:电解质溶液中na3ps4的含量是87%,peo的含量5%、natfsi含量8%。对应的电池循环性能如图4所示。
51.综上所述,本发明制得的电解质膜用于全固态钠电池,由于无机电解质具有一定
的孔隙,采用无机电解质与聚合物电解质复合,可以填入无机电解质的孔隙中,能够有效地减小固态电池的界面阻抗,提高复合电解质钠离子导电率,改善电池循环性能。
52.以上对本发明的具体实施例进行了描述。需要理解的是,本发明并不局限于上述特定实施方式,本领域技术人员可以在权利要求的范围内做出各种变形或修改,这并不影响本发明的实质内容。