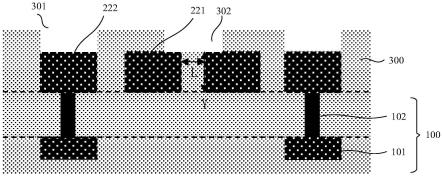
1.本发明属于半导体领域,特别是涉及一种用于焊盘过刻蚀的检测结构、制备及检测方法。
背景技术:2.在晶圆制程中,往往需要将各个膜层中形成的构件连接在一起以构成一个完整的半导体器件,或需要将半导体器件与其他电子元件连接起来以构成所需的电子电路,要完成这些连接就需要形成许多的焊盘(pad),可以说焊盘是晶圆制程中重要的连接构件。为此,在半导体领域中,对焊盘在导电性与可靠性上具有较高的要求。
3.为了保证焊盘的显露以便进行后续的电连接,现有的制备工艺中会存在过蚀的过程,该刻蚀过程,业界通常的做法是抓取焊盘上层的ti/tin信号,然后刻蚀一定时间吃开ti/tin,或者直接刻蚀一定时间后默认焊盘已经打开,该刻蚀过程存在一定风险,比如等离子体(plasma)积累,或形成晶格缺陷(crystaldefect)等,从而需要对焊盘的过刻蚀情况进行检测,目前检测焊盘过刻蚀过程只能通过失效分析(fa)切片来观察,测试的便捷性极低。
技术实现要素:4.鉴于以上所述现有技术的缺点,本发明的目的在于提供一种用于焊盘过刻蚀的检测结构、制备及检测方法,用于解决现有技术中难以对焊盘过刻蚀检测进行便捷操作的问题。
5.为实现上述目的及其他相关目的,本发明提供一种用于焊盘过刻蚀的检测结构,所述检测结构包括:
6.基底,所述基底包括晶圆有源区及晶圆切割区;
7.参比单元,所述参比单元位于所述晶圆切割区,与位于所述晶圆有源区的所述焊盘同步构成,所述参比单元包括2个间隔设置的参比焊盘及与所述参比焊盘一一对应连接的第一探测焊盘;
8.检测单元,所述检测单元位于所述晶圆切割区,与位于所述晶圆有源区的所述焊盘同步构成,且所述检测单元与所述参比单元具有相同形貌,所述检测单元包括2个间隔设置的检测焊盘及与所述检测焊盘一一对应连接的第二探测焊盘;
9.介电层,所述介电层位于所述基底上覆盖所述基底、所述参比单元及所述检测单元,且具有显露所述第一探测焊盘及所述第二探测焊盘的介电层探测窗口,以及至少显露位于所述检测焊盘之间的所述介电层的介电层检测窗口,其中,对应设置的2个所述参比焊盘结合所述介电层构成参比电容,对应设置的2个所述检测焊盘结合所述介电层构成检测电容。
10.可选地,所述参比单元及所述检测单元同时位于晶圆边缘切割区、同时位于晶圆中心切割区,或同时分布于整片晶圆切割区。
11.可选地,所述参比单元及所述检测单元位于相邻芯片的晶圆切割区中。
12.可选地,所述介电层包括氧化硅介电层;焊盘包括铝焊盘或铝合金焊盘。
13.可选地,所述介电层检测窗口显露所述检测焊盘。
14.本发明还提供一种用于焊盘过刻蚀检测结构的制备方法,包括以下步骤:
15.提供基底,所述基底包括晶圆有源区及晶圆切割区;
16.于所述基底的晶圆切割区上形成具有相同形貌的参比单元与检测单元,且所述参比单元及所述检测单元与位于所述晶圆有源区的所述焊盘同步形成,其中,所述参比单元包括2个间隔设置的参比焊盘及与所述参比焊盘一一对应连接的第一探测焊盘,所述检测单元包括2个间隔设置的检测焊盘及与所述检测焊盘一一对应连接的第二探测焊盘;
17.于所述基底上形成介电层,所述介电层覆盖所述基底、所述参比单元及所述检测单元;
18.于所述介电层上形成掩膜层,并对所述掩膜层进行图形化;
19.刻蚀所述介电层,形成显露所述第一探测焊盘及所述第二探测焊盘的介电层探测窗口,以及至少显露位于所述检测焊盘之间的所述介电层的介电层检测窗口,其中,对应设置的2个所述参比焊盘结合所述介电层构成参比电容,对应设置的2个所述检测焊盘结合所述介电层构成检测电容。
20.可选地,所述基底中还形成有底部金属层及与所述底部金属层相连接的金属柱。
21.本发明还提供一种用于焊盘过刻蚀的检测方法,包括以下步骤:
22.提供任一上述检测结构;
23.结合所述介电层探测窗口,通过所述第一探测焊盘获取所述参比电容的参比容值,以及通过所述第二探测焊盘获取所述检测电容的检测容值;
24.比对获取的所述参比容值与所述检测容值,以对所述焊盘的过刻蚀进行检测。
25.可选地,改变所述检测电容的方法包括改变对应设置的2个所述检测焊盘的厚度、长度、间距及所述介电层检测窗口的大小中的一种或组合。
26.可选地,还包括对位于不同晶圆切割区中的所述检测电容的检测容值进行比对的步骤,以反映晶圆制程在不同区域的差异。
27.如上所述,本发明的用于焊盘过刻蚀的检测结构、制备及检测方法,在晶圆切割区中形成参比单元及检测单元,并结合介电层构成参比电容及检测电容,由于检测电容中的介电层上方具有介电层检测窗口,且检测焊盘与介电层具有较大的选择蚀刻比,从而在刻蚀的过程中,检测电容中的介电层被刻蚀,使得检测电容的容值发生变化,通过对检测电容及参比电容的电性能数据即电容值的变化的监控,即可反应出焊盘过刻蚀的情况,免于切片确认。
附图说明
28.图1显示为本发明实施例一中的晶圆结构示意图。
29.图2显示为本发明实施例一中的参比电容的放大结构示意图。
30.图3显示为图2中的沿a-a的截面结构示意图。
31.图4显示为本发明实施例一中的检测电容的放大结构示意图。
32.图5显示为图4中的沿b-b的截面结构示意图。
33.图6显示为本发明实施例二中的用于焊盘过刻蚀检测结构的制备工艺流程图。
34.图7显示为本发明实施例三中的用于焊盘过刻蚀检测的流程图。
35.元件标号说明
36.10
ꢀꢀꢀꢀꢀꢀꢀꢀꢀꢀꢀꢀꢀꢀꢀꢀꢀꢀꢀꢀꢀ
晶圆
37.20
ꢀꢀꢀꢀꢀꢀꢀꢀꢀꢀꢀꢀꢀꢀꢀꢀꢀꢀꢀꢀꢀ
晶圆有源区
38.30
ꢀꢀꢀꢀꢀꢀꢀꢀꢀꢀꢀꢀꢀꢀꢀꢀꢀꢀꢀꢀꢀ
晶圆切割区
39.100
ꢀꢀꢀꢀꢀꢀꢀꢀꢀꢀꢀꢀꢀꢀꢀꢀꢀꢀꢀꢀ
基底
40.101
ꢀꢀꢀꢀꢀꢀꢀꢀꢀꢀꢀꢀꢀꢀꢀꢀꢀꢀꢀꢀ
底部金属层
41.102
ꢀꢀꢀꢀꢀꢀꢀꢀꢀꢀꢀꢀꢀꢀꢀꢀꢀꢀꢀꢀ
金属柱
42.211
ꢀꢀꢀꢀꢀꢀꢀꢀꢀꢀꢀꢀꢀꢀꢀꢀꢀꢀꢀꢀ
参比焊盘
43.212
ꢀꢀꢀꢀꢀꢀꢀꢀꢀꢀꢀꢀꢀꢀꢀꢀꢀꢀꢀꢀ
第一探测焊盘
44.221
ꢀꢀꢀꢀꢀꢀꢀꢀꢀꢀꢀꢀꢀꢀꢀꢀꢀꢀꢀꢀ
检测焊盘
45.222
ꢀꢀꢀꢀꢀꢀꢀꢀꢀꢀꢀꢀꢀꢀꢀꢀꢀꢀꢀꢀ
第二探测焊盘
46.300
ꢀꢀꢀꢀꢀꢀꢀꢀꢀꢀꢀꢀꢀꢀꢀꢀꢀꢀꢀꢀ
介电层
47.301
ꢀꢀꢀꢀꢀꢀꢀꢀꢀꢀꢀꢀꢀꢀꢀꢀꢀꢀꢀꢀ
介电层探测窗口
48.302
ꢀꢀꢀꢀꢀꢀꢀꢀꢀꢀꢀꢀꢀꢀꢀꢀꢀꢀꢀꢀ
介电层检测窗口
49.x
ꢀꢀꢀꢀꢀꢀꢀꢀꢀꢀꢀꢀꢀꢀꢀꢀꢀꢀꢀꢀꢀꢀ
长度
50.y
ꢀꢀꢀꢀꢀꢀꢀꢀꢀꢀꢀꢀꢀꢀꢀꢀꢀꢀꢀꢀꢀꢀ
厚度
51.l
ꢀꢀꢀꢀꢀꢀꢀꢀꢀꢀꢀꢀꢀꢀꢀꢀꢀꢀꢀꢀꢀꢀ
间距
52.s1~s5、sa~sc
ꢀꢀꢀꢀꢀꢀꢀꢀꢀꢀ
步骤
具体实施方式
53.以下通过特定的具体实例说明本发明的实施方式,本领域技术人员可由本说明书所揭露的内容轻易地了解本发明的其他优点与功效。本发明还可以通过另外不同的具体实施方式加以实施或应用,本说明书中的各项细节也可以基于不同观点与应用,在没有背离本发明的精神下进行各种修饰或改变。
54.如在详述本发明实施例时,为便于说明,表示器件结构的剖面图会不依一般比例作局部放大,而且所述示意图只是示例,其在此不应限制本发明保护的范围。此外,在实际制作中应包含长度、宽度及深度的三维空间尺寸。
55.为了方便描述,此处可能使用诸如“之下”、“下方”、“低于”、“下面”、“上方”、“上”等的空间关系词语来描述附图中所示的一个元件或特征与其他元件或特征的关系。将理解到,这些空间关系词语意图包含使用中或操作中的器件的、除了附图中描绘的方向之外的其他方向。此外,当一层被称为在两层“之间”时,它可以是所述两层之间仅有的层,或者也可以存在一个或多个介于其间的层。其中,当元件被称为“固定于”或“设置于”另一个元件,它可以直接在另一个元件上或者间接在该另一个元件上。当一个元件被称为是“连接于”另一个元件,它可以是直接连接到另一个元件或间接连接至该另一个元件上。
56.此处可能使用诸如“介于
……
之间”,该表达表示包括两端点值,以及可能使用诸如“多个”,该表达表示两个或两个以上,除非另有明确具体的限定。此外,术语“第一”、“第二”仅用于描述目的,而不能理解为指示或暗示相对重要性或者隐含指明所指示的技术特征的数量。由此,限定有“第一”、“第二”的特征可以明示或者隐含地包括一个或者更多个该
特征。
57.需要说明的是,本实施例中所提供的图示仅以示意方式说明本发明的基本构想,遂图示中仅显示与本发明中有关的组件而非按照实际实施时的组件数目、形状及尺寸绘制,其实际实施时各组件的型态、数量及比例可为一种随意的改变,其组件布局型态也可能更为复杂。
58.实施例一
59.如图1~图5,本实施例提供一种用于焊盘过刻蚀的检测结构,所述检测结构包括:
60.基底100,所述基底100包括晶圆有源区20及晶圆切割区30;
61.参比单元,所述参比单元位于所述晶圆切割区30,与位于所述晶圆有源区20的所述焊盘同步构成,所述参比单元包括2个间隔设置的参比焊盘211及与所述参比焊盘211一一对应连接的第一探测焊盘212;
62.检测单元,所述检测单元位于所述晶圆切割区30,与位于所述晶圆有源区20的所述焊盘同步构成,且所述检测单元与所述参比单元具有相同形貌,所述检测单元包括2个间隔设置的检测焊盘221及与所述检测焊盘221一一对应连接的第二探测焊盘222;
63.介电层300,所述介电层300位于所述基底100上覆盖所述基底100、所述参比单元及所述检测单元,且具有显露所述第一探测焊盘212及所述第二探测焊盘222的介电层探测窗口301,以及至少显露位于所述检测焊盘221之间的所述介电层300的介电层检测窗口302,其中,对应设置的2个所述参比焊盘211结合所述介电层300构成参比电容,对应设置的2个所述检测焊盘221结合所述介电层300构成检测电容。
64.具体的,参阅图1,在晶圆10的制备过程中,通常一片所述晶圆10上会含有几个~几千乃至上万个芯片,相邻的所述芯片之间会设置切割道,以便于后续芯片的分割,本实施例中,将所述晶圆10中的芯片所占用的区域称为所述晶圆有源区20,将切割道所占用的区域称为所述晶圆切割区30,且本技术所涉及的所述检测结构优选位于所述晶圆切割区30中,以降低对晶圆有效区域的占用。
65.其中,在所述晶圆10的制备过程中,所述晶圆有源区20内,会设置焊盘,如所述芯片的表面,以便于后续进行电性连接,该焊盘的材质优选为铝焊盘或铝合金焊盘,但并非局限于此,在制备工艺过程中,所述焊盘的表面会覆盖有钝化层等材料层,为避免对电性能的影响,需要对位于所述焊盘表面的材质层进行刻蚀,以完全显露所述焊盘的导电层,为确保所述焊盘表面的完全打开,通常会进行过刻蚀。
66.参阅图2~图5,本实施例中,为提高对所述焊盘的过刻蚀情况的检测,在制备所述焊盘的同时,在所述晶圆切割区30中制备所述参比单元中的所述参比焊盘211、所述第一探测焊盘212,以及所述检测单元中的所述检测焊盘221、所述第二探测焊盘222。其中,所述检测单元与所述参比单元具有相同形貌,所述第一探测焊盘212及所述第二探测焊盘222为扎针测试焊盘,所述参比焊盘211及所述检测焊盘221结合所述介电层300构成平板电容结构,即所述参比焊盘211及所述检测焊盘221可视为平板电容的极板。
67.在进行刻蚀以显露所述焊盘的过程中,由于所述介电层300与焊盘材质具有不同的刻蚀选择比,所述介电层300被去除的速率大于焊盘,如所述介电层300可包括氧化硅介电层,但并非局限于此,从而通过所述介电层300中的所述介电层检测窗口302,位于所述检测电容中的所述介电层300会有更大的损失量,从而根据电容原理,所述检测电容的电容值
会发生变化,而由于所述参比电容上方的所述介电层300不具有所述介电层检测窗口302,即所述参比电容上方被所述介电层300覆盖,且刻蚀过程中所述参比电容中的所述介电层300未被刻蚀,从而所述参比电容的电容值不会发生变化,因此,通过比对所述第一探测焊盘212及所述第二探测焊盘222所获取的分别对应于所述参比电容及所述检测电容的电容值,即可获知所述焊盘过刻蚀的情况,从而可通过电性能数据即电容值的变化来监控所述焊盘的过刻蚀,可避免进行切片操作。
68.本实施例中,关于所述基底100的结构,其可包括如图2及图3所示的位于钝化层如氧化硅层中的底部金属层101及金属柱102,但并非局限于此,可根据需要在所述基底100中设置有源或无源器件,此处不作过分限制。
69.作为示例,所述参比单元及所述检测单元可同时位于晶圆边缘切割区、同时位于晶圆中心切割区,或同时分布于整片晶圆切割区。
70.具体的,针对所述晶圆10上对位于不同区域的所述焊盘过刻蚀检测的需求,可将所述参比单元及所述检测单元同时设置于晶圆边缘切割区、或同时设置于晶圆中心切割区,或同时分布于整片晶圆切割区,此处不作过分限制。
71.进一步的,为提高所述检测结构对所述焊盘过刻蚀的检测准确度,优选所述参比单元、所述检测单元及待检测的所述焊盘临近设置,如所述参比单元及所述检测单元位于相邻待测芯片的晶圆切割区(切割道)中,具体间距可根据需要进行设置,此处不作过分限制。
72.进一步的,当对位于不同所述晶圆切割区30中的所述检测电容的检测容值进行比对操作时,还可反映晶圆制程在不同区域的差异,如加工差异等,以便于优化晶圆制程工艺。
73.作为示例,所述介电层检测窗口302可显露所述检测焊盘221。
74.具体的,根据需要,当想要更多考量焊盘金属的刻蚀情况时,可增大所述介电层检测窗口302的开窗(决定包含焊盘金属的多与少),当想要通过所述介电层300的变化来反映所述焊盘的刻蚀情况时,可减小所述介电层检测窗口302的开窗,关于所述介电层检测窗口302的具体尺寸此处不作过分限制,可通过改变所述介电层检测窗口302改变所述检测电容的检测容值。
75.如图4及图5,还可通过改变对应设置的2个所述检测焊盘221的厚度y、长度x、间距l的大小中的一种或组合改变所述检测电容的检测容值,或同时通过改变所述检测焊盘221及所述介电层检测窗口302的形貌以改变所述检测电容的检测容值,具体可根据需要设置。
76.实施例二
77.如图6,本实施例提供一种用于焊盘过刻蚀检测结构的制备方法,该方法可用以制备实施例一中的所述检测结构,但所述检测结构的制备工艺并非局限于此。本实施中采用以下制备工艺制备上述检测结构,从而关于所述检测结构的陈述均可参阅实施例一,此处不作赘述。
78.具体的,制备方法可包括以下步骤:
79.s1:提供基底,所述基底包括晶圆有源区及晶圆切割区;
80.s2:于所述基底的晶圆切割区上形成具有相同形貌的参比单元与检测单元,且所述参比单元及所述检测单元与位于所述晶圆有源区的所述焊盘同步形成,其中,所述参比
单元包括2个间隔设置的参比焊盘及与所述参比焊盘一一对应连接的第一探测焊盘,所述检测单元包括2个间隔设置的检测焊盘及与所述检测焊盘一一对应连接的第二探测焊盘;
81.s3:于所述基底上形成介电层,所述介电层覆盖所述基底、所述参比单元及所述检测单元;
82.s4:于所述介电层上形成掩膜层,并对所述掩膜层进行图形化;
83.s5:刻蚀所述介电层,形成显露所述第一探测焊盘及所述第二探测焊盘的介电层探测窗口,以及至少显露位于所述检测焊盘之间的所述介电层的介电层检测窗口,其中,对应设置的2个所述参比焊盘结合所述介电层构成参比电容,对应设置的2个所述检测焊盘结合所述介电层构成检测电容。
84.其中,所述基底中可形成有底部金属层及与所述底部金属层相连接的金属柱,但并非局限于此,还可根据需要在所述基底中设置其他有源或无源器件,此处不作过分限制。
85.实施例三
86.如图7,本实施例提供一种用于焊盘过刻蚀的检测方法,具体包括以下步骤:
87.sa:提供实施例一中的所述检测结构;
88.sb:结合所述介电层探测窗口,通过所述第一探测焊盘获取所述参比电容的参比容值,以及通过所述第二探测焊盘获取所述检测电容的检测容值;
89.sc:比对获取的所述参比容值与所述检测容值,以对所述焊盘的过刻蚀进行检测。
90.作为示例,改变所述检测电容的方法可包括改变对应设置的2个所述检测焊盘的厚度、长度、间距及所述检测窗口的大小中的一种或组合,具体可参阅实施例一,此处不作赘述。
91.作为示例,还可包括对位于不同晶圆切割区中的所述检测电容的检测容值进行比对的步骤,以反映晶圆制程在不同区域的差异,如加工差异等。
92.如上所述,本发明的用于焊盘过刻蚀的检测结构、制备及检测方法,在晶圆切割区中形成参比单元及检测单元,并结合介电层构成参比电容及检测电容,由于检测电容中的介电层上方具有介电层检测窗口,且检测焊盘与介电层具有较大的选择蚀刻比,从而在刻蚀的过程中,检测电容中的介电层被刻蚀,使得检测电容的容值发生变化,通过对检测电容及参比电容的电性能数据即电容值的变化的监控,即可反应出焊盘过刻蚀的情况,免于切片确认。
93.上述实施例仅例示性说明本发明的原理及其功效,而非用于限制本发明。任何熟悉此技术的人士皆可在不违背本发明的精神及范畴下,对上述实施例进行修饰或改变。因此,举凡所属技术领域中具有通常知识者在未脱离本发明所揭示的精神与技术思想下所完成的一切等效修饰或改变,仍应由本发明的权利要求所涵盖。