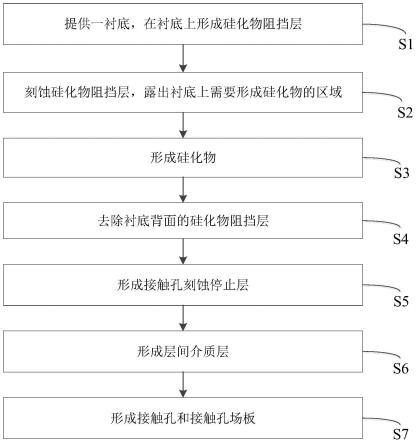
1.本技术涉及半导体技术领域,具体涉及一种改善层间介质层厚度均匀性的方法。
背景技术:2.随着半导体技术的不断发展,电源管理芯片技术也日新月异,作为电源管理芯片的核心,横向双扩散金属氧化物半导体(ldmos)的器件性能一直不断提升。为了减小器件导通电阻并降低尺寸,接触孔场板(ct plate)被广泛应用于ldmos器件中,低压化学气相沉积的四乙氧基硅烷(lpteos)作为接触孔场板的介质层的材料;为了改善负偏置温度不稳定性(nbti),高应力氮化硅(hsn)被引入作为接触孔刻蚀停止层(cesl)的材料。由于lpteos和hsn的存在,后续沉积的层间介质层的厚度均匀性变差,进而降低通过刻蚀在层间介质层中形成接触孔的工艺精度。
技术实现要素:3.鉴于以上所述现有技术的缺点,本技术的目的在于提供一种改善层间介质层厚度均匀性的方法,用于解决现有技术中采用lpteos和hsn分别作为接触孔场板的介质层的材料和接触孔刻蚀停止层的材料时沉积的层间介质层的厚度均匀性变差的问题。
4.为实现上述目的及其它相关目的,本技术提供一种改善层间介质层厚度均匀性的方法,包括:
5.步骤s1,提供一衬底,在衬底上形成硅化物阻挡层;
6.步骤s2,刻蚀硅化物阻挡层,露出衬底上需要形成硅化物的区域;
7.步骤s3,形成硅化物;
8.步骤s4,去除衬底背面的硅化物阻挡层
9.步骤s5,形成接触孔刻蚀停止层;
10.步骤s6,形成层间介质层;
11.步骤s7,形成接触孔和接触孔场板。
12.优选的,硅化物阻挡层的材料为低压化学气相沉积的四乙氧基硅烷。
13.优选的,硅化物阻挡层的厚度为900埃-1000埃。
14.优选的,衬底上需要形成硅化物的区域包括衬底上形成的栅极的顶部和栅极的两侧需要形成源极和漏极的区域。
15.优选的,通过背面硅化物阻挡层刻蚀工艺实施步骤s4。
16.优选的,背面硅化物阻挡层刻蚀工艺的腐蚀液为氢氟酸,持续时间3s~5s。
17.优选的,在步骤s3之后且步骤s4之前实施步骤s5。
18.优选的,接触孔刻蚀停止层的材料为高应力氮化硅。
19.优选的,层间介质层由自下而上层叠的harp膜层和等离子体增强四乙氧基硅烷层构成。
20.优选的,等离子体增强四乙氧基硅烷层的厚度为8000埃-9000埃。
21.如上所述,本技术提供的改善层间介质层厚度均匀性的方法,具有以下有益效果:沉积层间介质层之前通过背面硅化物阻挡层刻蚀(bse)工艺去除衬底背面的硅化物阻挡层,采用自下而上层叠的高深宽比工艺(harp)膜层和等离子体增强四乙氧基硅烷(peteos)层作为层间介质层,可以改善层间介质层的厚度均匀性,保证通过刻蚀在层间介质层中形成接触孔和接触孔场板的工艺精度。
附图说明
22.为了更清楚地说明本技术具体实施方式或现有技术中的技术方案,下面将对具体实施方式或现有技术描述中所需要使用的附图作简单地介绍,显而易见地,下面描述中的附图是本技术的一些实施方式,对于本领域普通技术人员来讲,在不付出创造性劳动的前提下,还可以根据这些附图获得其它附图。
23.图1显示为现有技术中采用lpteos和hsn分别作为接触孔场板的介质层的材料和接触孔刻蚀停止层的材料时沉积的层间介质层的厚度均匀性变差的数据分析图;
24.图2显示为本技术实施例提供的改善层间介质层厚度均匀性的方法的流程图;
25.图3显示为本技术实施例提供的改善层间介质层厚度均匀性的方法中,步骤s1完成后形成的器件剖面结构示意图;
26.图4显示为本技术实施例提供的改善层间介质层厚度均匀性的方法中,步骤s2完成后形成的器件剖面结构示意图;
27.图5显示为本技术实施例提供的改善层间介质层厚度均匀性的方法中,步骤s3完成后形成的器件剖面结构示意图;
28.图6显示为本技术实施例提供的改善层间介质层厚度均匀性的方法中,步骤s4完成后形成的器件剖面结构示意图;
29.图7显示为本技术实施例提供的改善层间介质层厚度均匀性的方法中,步骤s5完成后形成的器件剖面结构示意图;
30.图8显示为本技术实施例提供的改善层间介质层厚度均匀性的方法中,步骤s6完成后形成的器件剖面结构示意图;
31.图9显示为本技术实施例提供的改善层间介质层厚度均匀性的方法中,步骤s7完成后形成的器件剖面结构示意图;
32.图10显示为采用本技术实施例提供的改善层间介质层厚度均匀性的方法相比现有技术沉积的层间介质层的厚度均匀性得到改善的数据分析图。
具体实施方式
33.以下通过特定的具体实例说明本技术的实施方式,本领域技术人员可由本说明书所揭露的内容轻易地了解本技术的其它优点与功效。本技术还可以通过另外不同的具体实施方式加以实施或应用,本说明书中的各项细节也可以基于不同观点与应用,在没有背离本发明的精神下进行各种修饰或改变。
34.下面将结合附图,对本技术中的技术方案进行清楚、完整的描述,显然,所描述的实施例是本技术的一部分实施例,而不是全部的实施例。基于本技术中的实施例,本领域普通技术人员在不做出创造性劳动的前提下所获得的所有其它实施例,都属于本技术保护的
范围。
35.在本技术的描述中,需要说明的是,术语“中心”、“上”、“下”、“左”、“右”、“竖直”、“水平”、“内”、“外”等指示的方位或位置关系,仅是为了便于描述本技术和简化描述,而不是指示或暗示所指的装置或元件必须具有特定的方位、以特定的方位构造和操作,因此不能理解为对本技术的限制。此外,术语“第一”、“第二”、“第三”仅用于描述目的,而不能理解为指示或暗示相对重要性。
36.在本技术的描述中,需要说明的是,除非另有明确的规定和限定,术语“安装”、“相连”、“连接”应做广义理解,例如,可以是固定连接,也可以是可拆卸连接,或一体地连接;可以是机械连接,也可以是电气连接;可以是直接相连,也可以通过中间媒介间接相连,还可以是两个元件内部的连通,可以是无线连接,也可以是有线连接。对于本领域的普通技术人员而言,可以具体情况理解上述术语在本技术中的具体含义。
37.此外,下面所描述的本技术不同实施方式中所涉及的技术特征只要彼此之间未构成冲突就可以相互结合。
38.请参阅图1,其示出了现有技术中采用lpteos和hsn分别作为接触孔场板的介质层的材料和接触孔刻蚀停止层的材料时沉积的层间介质层的厚度均匀性变差的数据分析图。
39.在图1中,横坐标代表以硅片圆心为原点,沿半径方向到圆心的距离,纵坐标代表在硅片上沉积的层间介质层的厚度。
40.对于现有技术1,采用臭氧-四乙氧基硅烷(ots)作为接触孔场板的介质层的材料,采用hsn作为接触孔刻蚀停止层的材料,沉积的层间介质层的厚度均匀性较好。
41.为了提升器件性能,现有技术2采用lpteos和hsn分别作为接触孔场板的介质层的材料和接触孔刻蚀停止层的材料,沉积的层间介质层的厚度均匀性变差,越靠近硅片边缘,层间介质层的厚度越厚。
42.现有技术2采用lpteos作为接触孔场板的介质层的材料,由于是将硅片置于炉管中生长lpteos,所以硅片背面也会形成lpteos。沉积层间介质层时,硅片放置于加热托盘上,硅片受热具有一定的翘曲度,边缘温度低翘曲度大。由于硅片背面存在lpteos,导致热传导慢,会进一步增大硅片边缘的翘曲度,造成层间介质层的厚度均匀性变差。
43.因此,需要提出一种改善层间介质层厚度均匀性的方法,以解决现有技术采用lpteos和hsn分别作为接触孔场板的介质层的材料和接触孔刻蚀停止层的材料时沉积的层间介质层的厚度均匀性变差的技术问题。
44.请参阅图2,其示出了本技术实施例提供的改善层间介质层厚度均匀性的方法的流程图,该方法包括如下步骤:
45.步骤s1,提供一衬底,在衬底上形成硅化物阻挡层。
46.如图3所示,提供衬底100,衬底100上形成有器件结构,例如栅极101,栅极101两侧形成有侧墙102。
47.可选的,衬底100为硅衬底、锗衬底或者绝缘体上硅衬底等;或者衬底100的材料还可以包括其它的材料,例如砷化镓等iii-v族化合物。本领域的技术人员可以根据衬底100上形成的器件结构类型选择衬底100的构成材料,因此衬底100的类型不应限制本发明的保护范围。
48.栅极101可以为多晶硅栅极,侧墙102可以为氧化硅、氮化硅、氮氧化硅中一种或者
由他们的组合构成。
49.衬底100中形成有多个隔离部件,隔离部件将衬底分成多个区域,为了简化,图例中未予示出。隔离部件可由诸如二氧化硅(sio2)等任何绝缘材料、或具有高介电常数的“高k”介电质所组成,该高介电常数举例而言,可高于3.9。在一些情况中,隔离部件可由氧化物物质所组成。适用于组成隔离部件的材料举例而言,可包括二氧化硅(sio2)、氧化铪(hfo2)、矾土(al2o3)、氧化钇(y2o3)、氧化钽(ta2o5)、二氧化钛(tio2)、氧化镨(pr2o3)、氧化锆(zro2)、氧化铒(erox)、以及其它目前已知或以后才开发的具有类似特性的材料。
50.在本实施例中,本技术通过浅沟槽隔离工艺(sti,shallow trench isolation)形成隔离部件,浅沟槽隔离工艺包括但不限于浅沟槽刻蚀、氧化物填充和氧化物平坦化。
51.其中浅沟槽刻蚀包括但不限于隔离氧化层、氮化物沉淀、采用掩膜版进行浅槽隔离以及进行sti浅槽刻蚀。其中sti氧化物填充包括但不限于沟槽衬垫氧化硅、沟槽cvd(化学气相沉积)氧化物填充或pvd(物理气相沉积)氧化物填充。其中硅片表面的平坦化可以通过多种方法实现。可以通过使用sog(spin-on-glass)填充间隙实现硅片的平坦化,sog可以由80%的溶剂与20%的二氧化硅构成,淀积之后烘焙sog,蒸发掉溶剂,将二氧化硅留在间隙当中,也可以进行全部表面的反刻,以减少整个硅片的厚度。亦可以通过cmp工艺(也称为化学机械抛光工艺)有效地进行平坦化处理,包括但不限于对沟槽氧化物进行抛光(可以采用化学机械抛光)以及氮化物去除。
52.接下来,在衬底100上形成硅化物阻挡层103。作为示例,采用沉积工艺形成硅化物阻挡层103。为了提升器件性能,采用低压气相沉积工艺在衬底100上沉积lpteos层作为硅化物阻挡层103。作为示例,硅化物阻挡层103的厚度为900埃-1000埃。
53.由于低压气相沉积工艺是在炉管中实施的,所以衬底100的背面也会形成硅化物阻挡层103。
54.步骤s2,刻蚀硅化物阻挡层,露出衬底上需要形成硅化物的区域。
55.如图4所示,通过刻蚀工艺去除部分硅化物阻挡层103,露出衬底100上需要形成硅化物的区域,例如,栅极101的顶部,栅极101两侧需要形成源极和漏极的区域。
56.先在衬底100上形成光刻胶,利用具有需要形成硅化物的区域的图案的掩模版对光刻胶进行曝光、显影,将该图案转移到光刻胶中。再以具有该图案的光刻胶为掩模,刻蚀硅化物阻挡层103,露出衬底100上需要形成硅化物的区域。然后,通过灰化工艺去除光刻胶。
57.步骤s3,形成硅化物。
58.如图5所示,在衬底100上需要形成硅化物的区域形成硅化物105。
59.作为示例,形成硅化物105的步骤如下:
60.优选地,在进行金属层沉积之前,先对衬底100进行预清洗,以使得衬底100上需要形成硅化物的区域的表面没有杂质或者氧化膜,避免影响后续形成金属层和金属硅化物层的质量。预清洗可采用稀释的氢氟酸等湿法清洗工艺或者siconi预清洗工艺。
61.接着,在衬底100上需要形成硅化物的区域的表面上形成粘附层,以增强后续沉积的金属层与该区域表面的粘附性,并用于限制后续金属层中的金属向该区域以外的地方扩散。该粘附层可以为钛(ti)层、氮化钛(tin)层、钽(ta)层或氮化钽(tan)层中的任意一种单层结构,也可以是钛(ti)层、氮化钛(tin)层、钽(ta)层、氮化钽(tan)层中的多层堆叠而成
的复合层结构。
62.然后,通过物理气相沉积(pvd)工艺、化学气相沉积(cvd)工艺或原子层沉积(ald)工艺等在衬底100上需要形成硅化物的区域上形成金属层。金属层中含有的金属可以包括锰(mn)、钛(ti)、锆(zr)、钽(ta)、钨(w)、钯(pd)、铂(pt)、钴(co)、镍(ni)、钇(yb)中的至少一种,金属层优选为两种金属以上形成的合金。
63.接着,采用化学气相沉积工艺或物理气相沉积工艺在金属层上还可沉积形成一层保护层,如ti或tin,以保护金属层在后续工艺过程中表面不被氧化,保护层在后续退火工艺中不参与反应,并可在去除多余的金属层时一并被去除。
64.接着,采用低温快速退火工艺对衬底100和金属层进行第一次退火处理,使得金属层和与之相接触的衬底100上需要形成硅化物的区域的硅结合形成电阻率较高的第一相金属硅化物。退火温度需要根据沉积的金属来确定,当沉积的金属为ti时,第一次退火优选的退火温度为600℃~700℃,主要得到高阻的c49相-tisi2;当沉积的金属为co时,第一次退火优选的退火温度为400℃~600℃,主要得到高阻的cosi;当沉积的金属为ni时,第一次退火优选的退火温度为200℃~400℃,主要得到高阻的ni2si。
65.然后,通过选择性刻蚀,去除未反应的金属层,防止其中的金属在后续的第二次退火处理中继续与衬底100上需要形成硅化物的区域的硅发生反应。
66.接下来,采用高于第一次退火处理的温度进行第二次退火处理,使得高阻的第一相金属硅化物转化为低阻的第二相金属硅化物。退火温度需要根据沉积的金属来确定,当沉积的金属为ti时,第二次退火优选的退火温度为800℃~900℃,主要得到低阻的c54相-tisi2;当沉积的金属为co时,第二次退火优选的退火温度为700℃以上,主要得到低阻的cosi2;当沉积的金属为ni时,第二次退火优选的退火温度为400℃~700℃,主要得到低阻的nisi。优选的,第二次退火处理在含有氢气的气氛下进行,可以防止生成的金属硅化物被氧化,并进一步改善界面态。
67.两次退火处理可以均采用恒温退火工艺、尖峰退火工艺、闪光退火工艺或激光退火工艺中的一种。
68.接着,可以选用强酸和强氧化剂组合的腐蚀剂在较高的温度下(以便加快腐蚀速度)对衬底100表面进行第一次后清洗,以去除残留的未反应金属以及粘附层和第一相金属硅化物。具体地,第一次后清洗的清洗剂可以是硫酸与过氧化氢的混合溶液(spm),清洗时间为30s~100min。
69.然后,对衬底100表面进行第二次后清洗处理,以去除到硫酸基晶体及颗粒等污染物,并对第二次后清洗处理后的衬底100表面进行干燥,以去除表面附着的空心气泡等缺陷,获得形貌平整、均匀性良好的第二相金属硅化物。具体地,第二次后清洗处理的清洗剂可以是氨水和过氧化氢溶液的混合液,清洗时间为30s~100min,并伴随超声振动,可以将衬底100表面残留的硫酸基晶体溶解,同时将不可溶解于水溶液的金属颗粒转化成可溶于水溶液的金属络合物,并将第二相金属硅化物表面粘附的颗粒通过超声振动从第二相金属硅化物表面脱离出去。
70.步骤s4,去除衬底背面的硅化物阻挡层。
71.如图6所示,通过背面硅化物阻挡层刻蚀工艺去除衬底100背面的硅化物阻挡层103。作为示例,背面硅化物阻挡层刻蚀工艺的腐蚀液为氢氟酸,持续时间3s~5s。
72.步骤s5,形成接触孔刻蚀停止层。
73.如图7所示,通过沉积工艺在衬底100上形成接触孔刻蚀停止层106。作为示例,接触孔刻蚀停止层106的厚度为450埃~550埃。为了改善负偏置温度不稳定性(nbti),沉积高应力氮化硅层作为接触孔刻蚀停止层106,该沉积为化学气相沉积。示例性的,高应力氮化硅层的应力大于等于1.5gpa。
74.可选的,步骤s5可以在步骤s4之前实施。
75.步骤s6,形成层间介质层。
76.如图8所示,通过沉积工艺在衬底100上形成层间介质层107。为了进一步改善层间介质层107的厚度均匀性,使得层间介质层107的表面具有良好的平整度,本技术采用自下而上层叠的harp膜层和peteos层作为层间介质层107。
77.harp膜层可以达到较好的间隙填充效果,该间隙例如栅极之间的间隙。在本实施例中,可以采用常规的harp工艺沉积harp膜层。harp工艺使用的含硅前驱物包括但不限于硅烷或四乙氧基硅烷(teos)中的一种,含氧前驱物包括但不限于o2或o3中的一种。
78.为了确保最终形成的层间介质层107的平整度较高,沉积harp膜层之后,在harp膜层上覆盖peteos层。示例性地,peteos层的厚度为8000埃~9000埃。
79.peteos层采用等离子体增强化学气相沉积(pecvd)工艺形成。示例性地,peteos层可以由teos和o2通过pecvd工艺形成等离子体增强型氧化硅层,由于该pecvd工艺己经为本领域所熟知,在此不再进行详细描述。
80.步骤s7,形成接触孔和接触孔场板。
81.如图9所示,通过刻蚀工艺在层间介质层107和接触孔刻蚀停止层106中形成接触孔108和接触孔场板109。接触孔108的底部接触硅化物105,接触孔场板109的底部位于硅化物阻挡层103中,接触孔场板109可以用于屏蔽衬底100表面的电场。
82.先在层间介质层107上依次形成apf(advanced patterning film)薄膜、底部抗反射涂层(barc)和光刻胶,利用具有接触孔108和接触孔场板109顶部开口图案的掩模版对光刻胶进行曝光、显影,将该图案转移到光刻胶中。再以具有该图案的光刻胶为掩模,依次刻蚀底部抗反射涂层、apf薄膜、层间介质层107和接触孔刻蚀停止层106。然后,通过灰化工艺去除光刻胶,采用干法刻蚀工艺去除底部抗反射涂层和apf薄膜。
83.由于自下而上层叠的harp膜层和peteos层作为层间介质层107,层间介质层107的材料为氧化物,接触孔刻蚀停止层106的材料为氮化物,所以,通过刻蚀工艺在层间介质层107和接触孔刻蚀停止层106中形成接触孔108和接触孔场板109时,该刻蚀工艺对层间介质层107和接触孔刻蚀停止层106具有高选择比。
84.需要说明的是,本实施例中所提供的图示仅以示意方式说明本技术的基本构想,遂图式中仅显示与本发明中有关的组件而非按照实际实施时的组件数目、形状及尺寸绘制,其实际实施时各组件的型态、数量及比例可为一种随意的改变,且其组件布局型态也可能更为复杂。
85.请参阅图10,其示出了采用本技术实施例提供的改善层间介质层厚度均匀性的方法相比现有技术沉积的层间介质层的厚度均匀性得到改善的数据分析图。
86.现有技术采用ots作为接触孔场板的介质层的材料,采用hsn作为接触孔刻蚀停止层的材料,沉积的层间介质层的厚度均匀性较好。
87.本技术采用采用lpteos和hsn分别作为接触孔场板的介质层的材料和接触孔刻蚀停止层的材料,沉积的层间介质层的厚度均匀性相比现有技术没有区别,同时器件性能得到进一步提升。
88.由于沉积层间介质层107时衬底100背面的硅化物阻挡层103已被去除,加之自下而上层叠的harp膜层和peteos层作为层间介质层107使得层间介质层107的表面具有良好的平整度,所以即使衬底100在受热的情况下具有较大的翘曲度,沉积的层间介质层107在衬底100不同区域的厚度也不会出现明显的差异。
89.综上所述,本技术提供的改善层间介质层厚度均匀性的方法,具有以下有益效果:沉积层间介质层107之前通过背面硅化物阻挡层刻蚀工艺去除衬底背面的硅化物阻挡层103,采用自下而上层叠的harp膜层和peteos层作为层间介质层107,可以改善层间介质层107的厚度均匀性,保证通过刻蚀在层间介质层中形成接触孔108和接触孔场板109的工艺精度。所以,本技术有效克服了现有技术中的种种缺点而具高度产业利用价值。
90.接下来,在接触孔108和接触孔场板109中填充金属,示例性地,填充的金属为钨。
91.上述实施例仅例示性说明本技术的原理及其功效,而非用于限制本技术。任何熟悉此技术的人士皆可在不违背本技术的精神及范畴下,对上述实施例进行修饰或改变。因此,举凡所属技术领域中具有通常知识者在未脱离本发明所揭示的精神与技术思想下所完成的一切等效修饰或改变,仍应由本技术的权利要求所涵盖。