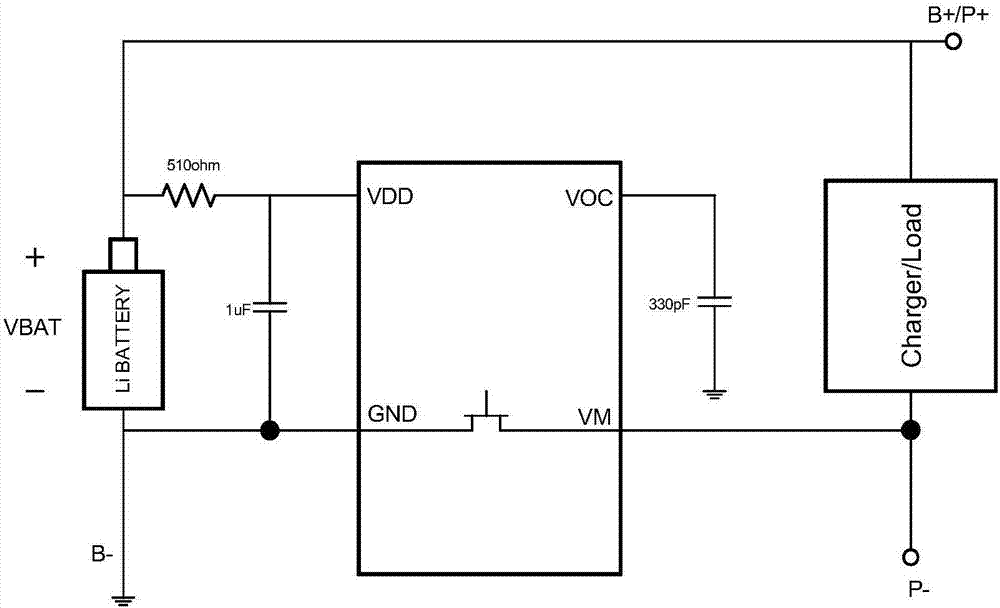
本实用新型涉及电子
技术领域:
,特别涉及电池充放电电路
技术领域:
,具体是指一种超低功耗锂电池充放电保护电路。
背景技术:
:近年来,PDA、手机、摄像机、便携式音乐设备、游戏机、助动车、电动车、蓝牙设备等越来越多的产品开始采用锂电池来当做它的主要电源。原因不外乎锂电池体积小、能量密度高、无记忆效应、循环寿命高、高电压、自放电率低等优点。由于锂电池与镍镉、镍氢电池不同,其必须考虑充电、放电时的安全,防止特性劣化的防止。但也因此,针对锂电池的过充、过放、过电流及短路电流的保护就显得更为重要。所以通常都会在电池包内设计保护线路用以保护锂电池,由此可见锂电池保护IC的重要性。锂离子电池因能量密度高,电池的安全性存在一定的风险。具体而言,在过度充电状态下,电池温度上升后能量将过剩,于是电解液分解而产生气体,电池内压上升,存在导致着火或破裂的危险。反之,在过度放电状态下,电解液因分解导致电池特性劣化及耐久性劣化(即充电次数降低)。锂离子电池的保护电路就是要确保电池处于过度充电及放电状态时的安全性,并防止特性的劣化。传统的锂离子电池保护电路如图1所示,其功能包括:(1)过度充电保护、(2)过度放电保护、(3)过电流/短路保护。以下就这三项功能的保护动作加以说明。1)过度充电:当锂电池发生过度充电时,电池内电解质会被分解,使得温度上升并产生气体,使得压力上升而可能引起自燃或爆裂的危机,锂电池保护IC用意就是要防止过充电的情形发生。过度充电保护IC原理:当外部充电器对锂电池充电时,为防止因温度上升所导致的内压上升,需终止充电状况,此时保护IC需检测电池电压,当到达4.25V时(假设电池过充点为4.25V)及启动过充电保护,将PowerMOS由ON转为OFF,进而截止充电。另外,过充电检测有可能被噪声干扰而产生误动作,为免将噪声判定为过充保护,需要设定延迟时间,而延迟时间也不能短于噪声的时间。2)过度放电:在过度放电的情形下,电解液因分解而导致电池特性劣化,并造成充电次数的降低,锂电池保护IC用以保护其过放电的状况发生,达成保护动作。过度放电保护IC原理:为了防止锂电池过度放电之状态,假设锂电池接上负载,当锂电池电压低于其过放电电压检测点(假设设定为2.3V),将启动过放电保护,将PowerMOS由ON转为OFF,进而截止放电,达成保护以避免电池过放电现象发生。并将电池保持在低静态电流的状态(standbymode)。当锂电池接上充电器,且此时锂电池电压高于过放电电压时,过放电保护功能方可解除。另外,为了对于脉冲放电之情形,过放侦测也设有延迟时间用以预防此种误动作。3)过电流及短路电流:因为不明原因(放电时或正负极遭金属物误触)造成过电流或短路电流发生,为确保安全,使其停止放电。电流保护IC原理:当放电电流过大或短路情况发生时,保护IC将启动过(短路)电流保护,此时过电流的检测是将PowerMOS的Rds(on)当成感应阻抗用以监测其电压的下降情形,若比所设定的过电流检测电压还高则停止放电。公式为:V-=I×Rds(on)×2其中,V-为过电流检测电压,假设V-=0.2V,Rds(on)=25mΩ,则保护电流的大小为I=4A同样的,过电流检出也必须要设有延迟时间以防有突然的电流流入时可能会发生的误动作。通常在过电流发生后,若能移除过电流的原因(例如:马上与负载脱离等),就会回复其正常状态,可以再实行正常的充放电动作。保护电路的要求:A)过度充电保护的高精化:当锂离子电池有过度充电状态时,为防止因温度上升所导致的内压上升,须截止充电状态。此保护IC即检测电池电压,当侦测到过度充电时,则使过度充电侦测的Power-MOSFET设置为OFF,截止充电。此时应当注意过度充电的检测电压的高精度化。在电池充电时,使电池充电到饱满的状态是使用者很在意的问题,同时,兼顾到安全性的问题,就得在达到容许电压时截止充电状态。要同时符合这两个条件,就要有非常高精度的侦测器,目前精度为25mV,但将来势需有更精度的要求。B)减低保护IC的耗电流达到过度放电保护目的:已充过电的锂离子电池电随着使用时间,电池电压会渐减,最后低到规格标准值以下。此时就需要再度充电。若未充电而继续使用的话,恐就无法再充电了(过放电状态)。而为防止过放电状态,保护IC即要侦测电池电压的状态,一旦到达过放电侦测电压以下,就得使放电一方的Power-MOSFETOFF而截止放电。但此时电池本身仍有自然放电及保护IC的消费电流存在,因此需要使保护IC的耗电流降到最低的程度。C)过电流/短路保护需有低侦测电压及高精度的要求:因不明原因导致短路而有大电流耗损时,为确保安全而使之停止放电。在过电流的侦测是以PowerMOS的Rds(on)为感应阻抗,以监视其电压的下降,此时的电压若比过电流侦测电压还高时即停止放电。为了使PowerMOS的Rds(on)在充电电流与放电电流时有效的应用,需使该阻抗值尽量低,(目前约20mΩ~30mΩ)。如此,过电流侦测电压就可较低。D)实现耐压值:电池包与充电器连接时瞬间会有高压产生,因此保护IC因具备有”耐高压的要求(Ricoh的保护IC即可承受到28V)。E)低耗电:当到达保护时,其静态耗电流必须要小(0.1uA)。F)零伏可充电:有些电池在存放的过程中可能因为放太久或不正常的原因导致电压低到0V,故保护IC需要在0V也可以充电的动作。综上所述,现有技术的主要缺点在于:传统锂电池保护芯片的静态电流皆为几uA,使得待机时间不够久就必须对锂电池做充电,且频繁的对锂电池做充放电,电池的使用寿命将大大的缩短。技术实现要素:本实用新型的目的是克服了上述现有技术中的缺点,提供一种具有更长的待机时间,能够延长锂电池使用寿命的超低功耗锂电池充放电保护电路。为了实现上述的目的,本实用新型的具有如下构成:该超低功耗锂电池充放电保护电路,包括电压检测子电路,连接于锂电池的正负极之间,充放电控制子电路,连接于所述锂电池的负极,所述的电压检测子电路还连接所述的充放电控制子电路并控制该充放电控制子电路的导通及导通方向。该超低功耗锂电池充放电保护电路中,该锂电池充放电保护电路的工作功耗为260nA~300nA,休眠功耗为160nA~200nA。该超低功耗锂电池充放电保护电路中,充放电控制子电路包括两个分别连接于所述的锂电池负极且导通方向相反的MOSFET,所述的电压检测子电路连接所述的两个MOSFET的栅极。该超低功耗锂电池充放电保护电路中,所述的电压检测子电路和所述的充放电控制子电路封装于一个芯片中。该超低功耗锂电池充放电保护电路中,所述的芯片包括连接所述锂电池正极的VDD引脚、连接所述锂电池负极的GND引脚、VREF引脚和VOC引脚,还包括VM引脚,所述的电压检测子电路连接于所述的VDD引脚和VREF引脚之间,以及所述的VDD引脚和VOC引脚之间,所述的充放电控制子电路连接于所述的GND引脚和所述的VM引脚之间,外部充电器或负载连接于所述的锂电池的正极和所述的VM引脚之间。采用本实用新型所述结构的超低功耗锂电池充放电保护电路,其功耗在正常操作下为280nA,休眠状态仅180nA,传统锂电池保护IC的功耗为uA等级,因此与传统产品相比,本实用新型明显有着更长待机时间的优势,解决了对锂电池频繁充放电的问题,且在低功耗的表现下仍然能够精确的侦测出各种保护的触发点。且本实用新型的超低功耗锂电池充放电保护电路,其结构相对简单,生产及使用成本低廉,应用范围也相对广泛。附图说明图1为现有技术中的锂电池保护芯片外部零件接线图。图2为本实用新型的超低功耗锂电池充放电保护电路的外部零件接线图。图3为本实用新型的超低功耗锂电池充放电保护电路的充电器对锂电池的充电电流路径示意图。图4为本实用新型的超低功耗锂电池充放电保护电路的锂电池对负载的放电电流路径示意图。图5为本实用新型的超低功耗锂电池充放电保护电路的及其电路板与电池组装示意图。具体实施方式为了能够更清楚地理解本实用新型的技术内容,特举以下实施例详细说明。请参阅图2所示,为本实用新型的超低功耗锂电池充放电保护电路的外部零件接线图。在一种实施方式中,如图2所示,该超低功耗锂电池充放电保护电路包括电压检测子电路,连接于锂电池的正负极之间,充放电控制子电路,连接于所述锂电池的负极,所述的电压检测子电路还连接所述的充放电控制子电路并控制该充放电控制子电路的导通及导通方向。所述的电压检测子电路和所述的充放电控制子电路封装于一个芯片中。该锂电池充放电保护电路的工作功耗为260nA~300nA,休眠功耗为160nA~200nA。在优选的实施方式中,充放电控制子电路包括两个分别连接于所述的锂电池负极且导通方向相反的MOSFET,所述的电压检测子电路连接所述的两个MOSFET的栅极。所述的芯片包括连接所述锂电池正极的VDD引脚、连接所述锂电池负极的GND引脚、VREF引脚和VOC引脚,还包括VM引脚,所述的电压检测子电路连接于所述的VDD引脚和VREF引脚之间,以及所述的VDD引脚和VOC引脚之间,所述的充放电控制子电路连接于所述的GND引脚和所述的VM引脚之间,外部充电器或负载连接于所述的锂电池的正极和所述的VM引脚之间。集成电路(根据其规模,现在常称之为“超大规模集成电路”)被发明以来的几十年时间里,它的集成度和速度都以指数的速率不断增长,摩尔定律对此现象有着粗略地估计。尽管多数专家承认这种增长最终会到达一个尽头,然而那时集成电路能够达到的性能尚不能清楚地预测。使用传统材料金属氧化物半导体场效应管(MOSFET)制成的器件可以达到6.3纳米的沟道宽度,而使用新型的碳纳米管作为栅极材料则可以获得几乎1纳米的沟道宽度。集成电路中器件高度密集,因此,其性能在很大程度上受到功耗问题的限制。得益于优化的器件设计,单个互补式金属氧化物半导体(CMOS)的功耗不断在降低,但是由于芯片的特征尺寸不断收缩,单位面积上的晶体管数量越来越多,因此个人电脑的功率耗散仍然以每年大约22%的比例增长。集成电路芯片中包含了大量的电容性负载,它们有的是设计人员有意加入的(如CMOS的栅极-沟道电容),有的则是不希望得到的(如相邻但是未连接的导线之间产生的电容)。对于不希望得到的寄生电容,电路状态的改变,会给它带来一个通过相连的电阻器负载来充电、放电的过程,这一过程将会耗费电能。这一部分是电路状态切换造成的动态功耗。随着电路尺寸的缩小,亚阈值电流的影响也会变得更加显著。对于最理想的晶体管,当栅极电压低于阈值电压(开启电压),晶体管处于截止区(亚阈值区),即表现为未导通状态,因此理论上电路逻辑状态稳定时不会有静态功耗。但是实际的MOSFET在截止区时,沟道中仍然有微量亚阈值电流通过,因此真实的电路存在静态功耗。虽然单个晶体管的亚阈值电流很小,但是由于超大规模集成电路含有大量的晶体管,因此总电流造成的功耗相当可观。由于亚阈值电流造成的功耗可以通过提高阈值电压和降低电源电压来降低。不过,这些方法会使电路的速度降低,因此一些现代的低功耗电路采用了双电源电压,在需要保证速度的关键路径上采用有利于运算速度的设计,而在非关键路径上使用低功耗电路。有的电路会使用不同阈值电压的晶体管来搭建,从而在尽可能保证性能不受太大损失的前提下降低整体功耗。本实用新型的超低功耗锂电池保护芯片内部所含电路皆是利用亚阈值区的特性来做设计。因此可以达到超低电流的要求。在实际应用中,本实用新型的超低功耗锂电池充放电保护电路的工作原理如下:a.电池充电:如图3为本实用新型的超低功耗锂电池充放电保护电路的充电器对锂电池的充电电流路径,充电电流由充电器正端对锂电池充电再经由导通的MOSFET回到充电器负端。b.电池放电:如图4为本实用新型的超低功耗锂电池充放电保护电路的锂电池对负载的放电电流路径,放电电流由锂电池正端对负载放电再经由导通的MOSFET回到锂电池负端。c.当充电过程或放电过程芯片侦测到过充电压/过放电压/过充电流/过放电流的情况,芯片会关断内部MOSFET阻止对锂电池的充放电行为。d.待电池电压恢复到保护电压之外,再次导通内部MOSFET,等待Charger或Load对电池进行充放电。本实用新型的超低功耗锂电池充放电保护电路的及其电路板与电池组装的示意图5所示,电池与充电器的正极及地相接,而系统负载的的则是透过芯片的VM脚,如此一来锂电池所有充放电行为皆会受到芯片的监控,达到可穿戴式产品在确保用户安全的前提下,享受低功耗带来的超长时间待机优势。下表1为本实用新型的超低功耗锂电池充放电保护电路的静态消耗电流在室温下所量得。表1本实用新型的超低功耗锂电池充放电保护电路的静态消耗电流下表2为本实用新型的超低功耗锂电池充放电保护电路的以PTS-2008进行连续5次精准测试的结果。次数过电压(V)过电压释放(V)过放电压(V)过放电压释放(V)14.4264.2382.5372.924.4264.2382.5382.90134.4274.22.532.944.4274.2392.5372.954.4264.2382.5352.898表2本实用新型的超低功耗锂电池充放电保护电路的以PTS-2008进行连续5次精准测试的结果下表3为本实用新型的超低功耗锂电池充放电保护电路的参数。表3本实用新型的超低功耗锂电池充放电保护电路的参数可以从量测结果看出均接近规格之中心值,可以说明本实用新型做了省电上的技术突破,同时仍然保有精准与稳定的电压侦测保护功能。采用本实用新型所述结构的超低功耗锂电池充放电保护电路,其功耗在正常操作下为280nA,休眠状态仅180nA,传统锂电池保护IC的功耗为uA等级,因此与传统产品相比,本实用新型明显有着更长待机时间的优势,解决了对锂电池频繁充放电的问题,且在低功耗的表现下仍然能够精确的侦测出各种保护的触发点。且本实用新型的超低功耗锂电池充放电保护电路,其结构相对简单,生产及使用成本低廉,应用范围也相对广泛。在此说明书中,本实用新型已参照其特定的实施例作了描述。但是,很显然仍可以作出各种修改和变换而不背离本实用新型的精神和范围。因此,说明书和附图应被认为是说明性的而非限制性的。当前第1页1 2 3