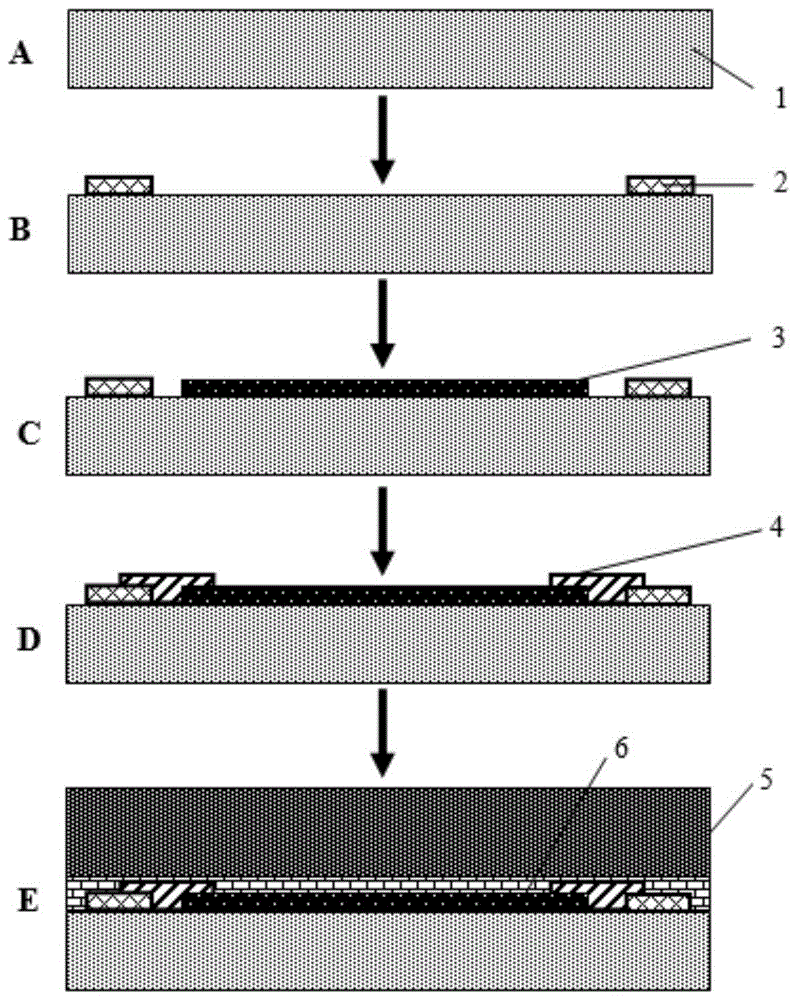
本发明属于电热取暖产品制造领域,涉及新型石墨烯材料在电热膜领域的应用,具体涉及采用新型石墨烯材料制造具有取暖和远红外保健双重功能的地暖电热膜及其制备方法。
背景技术:
:近年来,电采暖技术和市场发展迅速,特别是在国家北方煤改电政策支持下,越来越多的电采暖设备进入寻常百姓家庭,满足了北方家庭采暖季安全、高效的采暖需求,也为北方主要城市的空气质量持续改善提供了重要产品和技术支撑。在所有电采暖产品中,地暖电热膜是一种极具市场前景的产品,因其将采暖与家庭装修中地面工程紧密结合,且避免了水暖工程地面抬高较多,导致居住空间被压缩的问题。另外,地暖电热膜还可应用于发热地垫、发热地毯、发热墙裙等领域。石墨烯是近年来发展起来的重大战略新兴材料,具有导热、导电性好的显著优势,在诸多电子产品中逐步获得应用。在电采暖领域,石墨烯也逐步发挥了其材料优势,在电采暖发热体中逐步在取代传统碳晶发热体,形成石墨烯材料独特的技术优势。石墨烯地暖电热膜具有更好的稳定性和更高的远红外发射效率,越来越受到市场的认可和欢迎。当前石墨烯地暖电热膜制造过程中,采用银浆来连接载流条(铜箔)和石墨烯发热体,其制备工艺顺序是先通过涂布或印刷获得石墨烯导电发热体,随后再印刷银电极并连接(覆盖)于石墨烯发热体边缘,最后再压合铜箔载流条电极并与已经印刷的银电极相连。以此工艺制备的石墨烯电热膜,尚不能完全解决发热体使用过程中的打火问题,存在应用安全隐患。采用上述工艺方法制备的地暖用电热膜,由于是先完成发热体导电膜的制造,再完成桥接发热体与铜电极的银电极制造,最后再在银电极一端压合铜电极,而在上述制备工艺中,因为铜电极硬接触于银浆表面,银浆不能包覆于铜电极之上,导致铜电极与银电极存在接触不良问题,从而在实际使用过程中,存在发热体边缘打火的风险,容易导致失火等安全隐患。本发明提出了一种预植入粗化的载流条铜电极的工艺方案,能够彻底解决地暖电热膜使用过程中由于接触不良问题导致的发热体边缘打火问题,提高了电热膜使用安全性。技术实现要素:本发明的目的是针对现有地暖电热膜在使用过程中容易打火,存在易发生失火的安全隐患,及其制备过程中存在自动化衔接的技术问题,提供一种地暖用石墨烯电热膜及其制备方法,本发明的地暖用石墨烯电热膜的发热体与桥接电极、铜电极接触良好,桥接电极完全包覆铜电极,有效解决了发热体边缘打火所致失火的风险;另外,本发明更有利于实现全程自动化生产,杜绝了传统生产过程中,在铜电极复合工序容易出现异常而导致无法与前端工序自动化衔接的问题(传统生产,在石墨烯发热膜层印刷及银电极印刷阶段可以实现自动化生产,铜电极复合过程中,由于在与银电极贴合时容易产生异常,一般是独立生产,以防浪费物料,产生损失)。为实现本发明的目的,本发明一方面提供一种地暖用石墨烯电热膜的制备方法,包括在电热膜的绝缘基材表面涂覆石墨烯发热膜,并在石墨烯发热膜相对的两侧植入铜电极,而且石墨烯发热膜和铜电极之间间隔排列;然后在石墨烯发热膜和铜电极的表面印刷桥接电极。其中,所述石墨烯发热膜和铜电极之间的间隔距离为0.5-2cm。特别是,所述桥接电极选择银浆电极。在石墨烯发热膜和铜电极的表面印刷的桥接电极的两端分别包覆铜电极和石墨烯发热膜边缘的上表面,具有良好电连接性能、抗剥离性能,克服了现有石墨烯地暖电热膜制造过程中先制备石墨烯导电发热膜,接着再印刷银电极,且银电极的一端连接并覆盖于石墨烯发热体边缘,然后在银电极的另一端压合铜箔载流条电极,并与已经印刷的银电极相连的制备工艺而导致制备的石墨烯电热膜在使用过程中存在打火的不安全隐患的技术缺陷。其中,所述铜电极为表面粗糙度ra为0.5-5μm,优选为2-4μm,进一步优选为(3±0.5)μm的粗化处理的铜箔或铜条。特别是,所述粗化处理的铜箔或铜条按照如下方法处理:将铜箔或铜条浸入微蚀液中,微蚀液刻蚀铜箔或铜条的表面,进行粗化处理,即得。其中,所述微蚀液为双氧水与硫酸或盐酸的混合体系,其中双氧水与硫酸或盐酸的浓度之比为1:2.5-3.5。特别是,所述微蚀液优选为双氧水与硫酸的混合体系;微蚀液的(双氧水和硫酸)总浓度为20-150g/l,优选为105-135g/l,进一步优选为120g/l。特别是,所述微蚀液双氧水与硫酸的混合体系中双氧水的浓度为5-40g/l,优选为30g/l;硫酸的浓度为15-110g/l,优选为75-105g/l,进一步优选为90g/l。尤其是,所述双氧水-硫酸体系的浓度优选为120g/l,其中双氧水浓度为30g/l,硫酸浓度为90g/l。特别是,所述双氧水-盐酸体系的浓度为1-20g/l。尤其是,所述粗化处理的温度为20-35℃,优选为25-30℃;处理时间为10-500s,优选为100s;铜箔或铜条在微蚀液中的运动速度为2-4m/min,优选为2.5-3m/min。采用卷对卷式微蚀工艺对铜箔(条)进行微蚀处理,然后进行清洗、烘干后收卷,获得粗化铜箔(条)备用,微蚀后铜箔两侧都实现粗糙化,粗化铜箔(条)的表面粗糙度为ra为0.5-5μm。将卷式待处理铜箔(条)放入湿法刻蚀设备,采用卷对卷式微蚀工艺,用微蚀液对铜箔进行微蚀处理,铜箔(条)表面被微蚀液腐蚀,铜箔(条)在强氧化剂作用下,生成氧化铜,随后再与酸反应,产生刻蚀作用,总化学方程式为:h2o2+cu+h2so4→cuso4+2h2o。在铜箔(条)完成微蚀处理后,对铜箔(条)依次进行清洗、烘干处理;然后收卷,获得粗化铜箔,微蚀后铜箔两侧都实现粗糙化,微蚀处理后的粗化铜箔(条)的表面粗糙度ra为0.5-5μm。本发明另一方面提供一种地暖用石墨烯电热膜的制备方法,包括如下顺序进行的步骤:1)在第一绝缘基材的表面涂覆第一粘接剂;接着在第一绝缘基材表面的相对的两侧分别各放置1条铜箔或铜条,铜箔或铜条距离绝缘基材边缘0.5-2cm,相互平行,彼此对称分布;然后进行热压处理,在第一绝缘基材表面植入铜电极,制得铜电极-基材复合材;2)在铜电极-基材复合材的表面,在2个铜电极的相对的内侧,涂覆发热浆料石墨烯浆料,并将铜电极-基材复合材置于烘箱中进行发热浆料烘干处理,石墨烯浆料在铜电极-基材复合材的表面固化成石墨烯发热膜,制成石墨烯-铜电极-基材复合材;3)在石墨烯-铜电极-基材复合材的表面上涂覆桥接电极浆料,并进行桥接电极烘干处理,桥接电极浆料固化,形成桥接电极,连接石墨烯发热膜和铜电极,形成铜/桥接-石墨烯-基材复合体;4)在第二绝缘基材的表面涂覆第二粘接剂后,将制备的铜/桥接-石墨烯-基材复合体覆合在表面涂布第二粘接剂的第二绝缘基材上,并进行辊压、封装处理。其中,步骤1)中所述的铜箔或铜条为粗化处理后的粗化铜箔或铜条,粗化铜箔或铜条按照如下方法处理:将铜箔或铜条浸入微蚀液中,微蚀液刻蚀铜箔或铜条的表面,进行粗化处理,即得。特别是,所述粗化铜箔或铜条的表面粗糙度ra为0.5-5μm,优选为2-4μm。其中,所述微蚀液为双氧水与硫酸或盐酸的混合体系,其中双氧水与硫酸或盐酸的浓度之比为1:2.5-3.5。特别是,所述微蚀液优选为双氧水与硫酸的混合体系;微蚀液(双氧水和硫酸)的总浓度为20-150g/l,优选为105-135g/l。特别是,所述微蚀液双氧水与硫酸的混合体系中双氧水的浓度为5-40g/l,优选为30g/l;硫酸的浓度为15-110g/l,优选为75-105g/l。尤其是,所述粗化处理的温度为20-35℃,优选为25-30℃;处理时间为10-500s,优选为100s;铜箔或铜条在微蚀液中的运动速度为2-4m/min,优选为2.5-3m/min。其中,步骤1)中所述第一绝缘基材为pet膜、pi膜、pen膜或pp膜,优选为pet膜;所述第一粘接剂为热塑性聚酰亚胺(pi)预聚体、聚酰胺酸、丙烯酸胶粘剂或环氧胶粘剂。特别是,还包括对涂覆了第一粘接剂后的绝缘基材进行烘烤处理后,再放置所述的铜箔或铜条,其中,所述烘烤温度为50-200℃,优选为80-120℃;烘烤时间为1-20min,优选为5-10min。尤其是,所述第一粘接剂为热塑性聚酰亚胺(pi)预聚体或聚酰胺酸时,烘烤温度为120-200℃,优选为120℃;烘烤时间为1-20min,优选为10min;所述第一粘接剂为丙烯酸胶粘剂或环氧树脂胶粘剂时,烘烤温度为50-140℃,优选为80-100℃;烘烤时间为1-20min,优选为5-10min。其中,所述热压处理温度为140-350℃;热压压力为2-10mpa,优选为3-5mpa;热时间为30-60min,优选为30-45min。特别是,所述第一粘接剂为热塑性聚酰亚胺(pi)预聚体或聚酰胺酸时,热压处理温度为250-350℃,优选为250℃;热压压力为2-10mpa,优选为3-5mpa;热时间为30-60min,优选为30-45min;所述第一粘接剂为丙烯酸胶粘剂或环氧树脂胶粘剂时,热压处理温度为140-200℃,优选为150-180℃;热压压力为2-10mpa,优选3-5mpa;热压时间为30-60min,优选为30-40min。其中,步骤2)中石墨烯发热膜的边缘与铜电极相互平行,且与铜电极之间的距离为0.5-2cm。石墨烯发热干膜与铜电极相平行的边缘与铜电极之间的区域为预留的桥接电极区域,用于印刷桥接电极,形成的2个预留的桥接电极区域相互平行、彼此相对,桥接电极区域的宽度为0.5-2cm。特别是,所述发热浆料烘干处理温度为50-180℃,优选为120-150℃;烘干处理时间为1-60min,优选为20-40min;石墨烯发热干膜的厚度为10-100μm,优选为15-25μm。尤其是,所述发热浆料石墨烯浆料按照如下方法制备而成:将发热材料、树脂胶粘剂、溶剂混合,并分散均匀,其中发热材料的质量百分比浓度5-60wt%,树脂胶粘剂的质量百分比浓度为5-30wt%,余量为溶剂。特别是,所述发热材料的质量百分比浓度为15-30wt%;树脂胶粘剂的质量百分比浓度为8-15wt%;余量为溶剂。尤其是,所述发热材料为石墨烯或石墨烯与碳纳米管、石墨炔、炭黑、石墨、金属颗粒或金属纳米线中的一种或多种的组合;树脂胶粘剂为丙烯酸树脂、环氧树脂、饱和聚酯树脂或聚氨酯树脂;溶剂为水、氮甲基吡咯烷酮(nmp)、乙醇、异丙醇、甘油、松油醇、乙二醇乙醚醋酸酯或邻苯二甲酸二丁酯。特别是,所述发热材料为石墨烯与碳纳米管、炭黑,其中石墨烯、碳纳米管、炭黑的质量之比为100:(5-80):(60-100),优选为100:40:90。特别是,所述发热材料为石墨烯与碳纳米管,其中石墨烯与碳纳米管的质量之比为100:(5-80),优选为100:60。步骤3)中固化后的桥接电极的两端分别包覆铜电极和石墨烯发热干膜边缘的上表面,形成具有良好电连接性能、抗剥离性能的铜/桥接-石墨烯-基材复合体。其中,步骤3)中所述桥接电极烘干处理的温度为50-180℃,优选为130-150℃;烘干时间为1-60min,优选为20-40min。特别是,所述桥接电极浆料为银导电浆料(即银浆)、铜导电浆料等高导电浆料,优选为银浆。桥接电极浆料为银浆,则形成的桥接电极为银浆桥接电极,制得的铜/桥接-石墨烯-基材复合体为铜/银浆-石墨烯-基材复合体。银浆电极包覆铜电极和石墨烯发热层边缘的上表面,形成具有良好电连接性能和抗剥离性能的铜/银浆复合体。尤其是,所述银浆中银粉颗粒度为1~3μm,银粉固含量大于50%,优选为60-75%;烘干固化的银浆桥接电极厚度5-50μm,优选为25μm;方阻为5-50mohm/sq,优选为10mohm/sq。其中,步骤4)中所述第二绝缘基材为pet膜、pi膜、pen膜或pp膜,优选为pet膜;所述第二粘接剂为eva热熔胶、丙烯酸胶粘剂、环氧胶粘剂或tpu热熔胶。特别是,还包括对涂覆了第二粘接剂后的绝缘基材进行烘烤处理后,再进行所述的辊压、封装处理,其中所述烘烤温度为50-140℃,优选为80-100℃;烘烤时间为1-20min,优选为5-10min。其中,所述辊压、封装处理过程中温度为100-180℃,优选为120-150℃;时间为0.5-5min,优选为0.5-2min,进一步优选为1min;辊压、封装处理过程中控制辊压压力为0.2-10mpa,优选为0.6-0.7mpa。特别是,所述第二粘接剂为eva热熔胶时,辊压封装处理的温度为100-180℃,优选为120-150℃;时间为0.5-5min,优选为0.5-2min,进一步优选为1min;辊压、封装处理过程中控制辊压压力为0.2-10mpa,优选为0.6-0.7mpa。第二粘接剂采用eva热熔胶时,进行辊压封装处理后,不需要进行固化处理;而第二粘接剂为丙烯酸胶粘剂、环氧胶粘剂或tpu热熔胶时,辊压、封装处理后,还包括进行烘烤固化处理。特别是,所述第二粘接剂为丙烯酸胶粘剂或环氧胶粘剂时,辊压、封装处理后,还包括进行烘烤固化处理,其中固化处理温度为120-200℃,优选为140-160℃;固化时间为5-60min,优选为20-30min。辊压、封装处理是将石墨烯发热干膜、铜电极、银浆桥接电极覆合封装在第一、第二绝缘基材内部,制得完备的地暖用石墨烯电热膜。采用覆合机将上述的铜/桥接-石墨烯-基材复合体覆合、表面涂布第二粘接剂的第二绝缘基材覆合在一起。其中,步骤1)中所述涂覆第一粘接剂的方法为喷涂、丝网印刷或凹版印刷;步骤2)中所述涂覆发热浆料石墨烯浆料的方法为丝网印刷、凹版印刷、喷涂、悬涂或狭缝式涂布等;步骤3)中所述涂覆桥接电极浆料的方法为丝网印刷或凹版印刷;步骤4)中所述涂覆第二粘接剂的方法为涂布、印刷或覆膜(胶粘剂膜)。特别是,还包括将辊压、封装处理后的石墨烯电热膜的铜电极与电热膜温度控制器、外接电源线通过导线相连接,制成成品地暖用石墨烯电热膜。封装处理后的石墨烯电热膜收成卷,然后根据地暖生产的需求,截取一定的长度,随后通过在铜电极上焊接/或铆接的方法,将电热膜温控器与电热膜相连接,并通过温控器连接至外接电源,即可实现电热膜工作状态通断电及温度控制。本发明再一方面提供一种按照上述方法制备而成的地暖用石墨烯电热膜。针对现有地暖电热膜存在发热体边缘打火的问题,本发明通过先粗化铜电极,随后预植入铜电极于绝缘基材(pet,聚对苯二甲酸乙二醇酯)表面,最后再印刷银浆电极,以桥接铜电极粗化面和发热体表面,从而使得银浆能够充分包覆于铜电极的粗化面,获得了极佳的接触电阻,从而有效解决发热体边缘打火的安全风险。本发明的地暖用石墨烯电热膜,其核心要点是在pet基材上预先植入铜电极,随后再分别制备石墨烯发热层和银浆电极,银浆电极能够充分包裹覆盖铜电极和石墨烯发热层边缘的上表面,从而获得在电连接和抗剥离性能方面极佳的铜/银浆复合体,能够有效避免石墨烯地暖电热膜使用过程中打火问题,提升产品使用安全性。与现有技术相比,本发明采用一种预植入粗化的载流条铜电极的工艺方案,解决了现有石墨烯地暖电热膜出现的发热体边缘打火问题,具有如下优点和好处:1、本发明方法制备的地暖用石墨烯电热膜中石墨烯发热体边缘的桥接银浆电极与铜载流电极的表面充分包覆,降低了银浆电极与铜电极表面接触电阻,本发明的铜电极与银电极的接触电阻在0.01ω以下,铜电极与银电极之间的接触电阻仅为0.007-0.008ω,显著低于现有地暖用石墨烯电热膜的铜电极与银电极的接触电阻0.05-0.2ω;2、本发明的地暖电热膜,铜电极与银电极之间接触电阻较低,有利于降低无效的热损耗(接触电阻造成),提高能源利用率;3、本发明方法制备的地暖电热膜中石墨烯发热体边缘的桥接银浆电极与铜载流电极的表面充分包覆,提高了银浆电极与铜电极之间的附着力,提高了两者之间的附着力等级,银浆电极与铜电极之间的附着力强,附着力等级达到1级,显著提高了银浆电极与铜电极之间的抗剥离性能,解决了发热体边缘在通电使用过程中打火的问题。而现有的地暖电热膜的铜箔与银浆电极为硬接触,存在打火现象,本发明的地暖电热膜中的银浆电极完全包覆在铜电极的表面,其附着力等级显著高于现有石墨烯地暖膜中银电极与铜电极之间的附着力等级,明显减少打火现象的发生。4、本发明的地暖用石墨烯电热膜的制备方法,有利于实现石墨烯地暖电热膜全程自动化生产,杜绝了传统生产过程中,在铜电极与银电极复合过程中,复合工序出现的异常,如铜箔产生移位、褶皱等,导致无法与前端工序(石墨烯发热层制备和银浆电极制备)自动化衔接的问题(不良品比例高,物料损耗会较大。)附图说明图1为本发明石墨烯地暖电热膜制备流程图,其中:a、电热膜pet基材准备;b、在pet基材上植入铜电极;c、在pet基材上制备石墨烯发热层;d、制备银浆电极,连接铜电极和石墨烯发热层;e、在封装pet表面涂布胶水粘结剂,并对电热膜完成封装;图2为本发明石墨烯地暖电热膜的结构示意图(不包含第二绝缘基材);图3为本发明石墨烯地暖电热膜的剖视示意图。附图标记说明1、第一绝缘基材;2铜电极;3、石墨烯发热膜;4、桥接电极;5、第二绝缘基材;6、第二粘接剂。具体实施方式下面结合具体实施例来进一步描述本发明,本发明的优点和特点将会随着描述而更为清楚。但这些实施例仅是范例性的,并不对本发明的范围构成任何限制。本领域技术人员应该理解的是,在不偏离本发明的精神和范围下可以对本发明技术方案的细节和形式进行修改或替换,但这些修改和替换均落入本发明的保护范围内。本发明石墨烯地暖用电热膜的制备流程按照如图1进行制备。实施例11、粗化处理将卷式待处理铜箔(条)放入湿法刻蚀设备采用卷对卷式微蚀工艺,用微蚀液对铜箔进行微蚀,即将铜箔(条)浸入微蚀液中,对铜箔(条)进行微蚀处理,铜箔(条)匀速通过微蚀液,铜箔(条)表面被微蚀液腐蚀,铜箔(条)在强氧化剂作用下,生成氧化铜,随后再与酸反应,产生刻蚀作用,总化学方程式为:h2o2+cu+h2so4→cuso4+2h2o,其中:微蚀液为双氧水-硫酸体系(即双氧水与硫酸的混合液),双氧水浓度为30g/l,硫酸浓度为90g/l,双氧水与硫酸浓度比为:1:3;双氧水-硫酸体系中双氧水的浓度和硫酸的浓度之和为120g/l;微蚀处理过程中控制温度为30℃(通常为20-35℃);微蚀处理时间为100s(通常为10-500s);铜箔运动速度为3m/min(通常为2-4m/min);本发明中微蚀液以浓度为120g/l的双氧水-硫酸体系为例进行说明,其他浓度是双氧水-硫酸体系均适用于本发明,例如双氧水-硫酸体系的浓度为20-150g/l;微蚀液中双氧水的浓度以30g/l为例进行说明,其他浓度如5-40g/l;双氧水与硫酸浓度比为:1:(2.5-3.5)均适用于本发明。微蚀液除了双氧水-硫酸体系之外,还可以是双氧水-盐酸体系,双氧水-盐酸体系的浓度为1-20g/l。铜箔(条)微蚀处理100s,完成刻蚀后,对铜箔(条)依次进行清洗、烘干处理;然后收卷,获得粗化铜箔(条),微蚀后铜箔(条)两侧都实现粗糙化,粗化处理后的粗化铜箔表面粗糙度ra为(3±0.5)μm(通常为0.5-5μm)。2、铜电极的植入处理在第一绝缘基材1(pet膜)的表面涂布第一粘接剂(即热塑性聚酰亚胺(pi)预聚体(聚酰胺酸))后,将pet膜置于烘箱中进行烘烤处理,其中,控制烘烤温度为120℃(通常为50-200℃,优选为120-200℃),烘烤10min(通常为1-20min);接着在pet膜表面(即涂覆了第一粘接剂的一侧)的相对的两边且分别距离pet膜边缘1cm(通常为0.5-2cm)的位置,采用自动复合机,对称放置2条平行的粗化铜箔(条),即对称的两侧边各1条粗化铜箔(条),如图2,并同时进行热压(亚胺化)处理,粗化铜箔最终固化贴合在绝缘基材pet膜的表面,形成铜电极,即在绝缘基材的表面植入铜电极2,制得铜电极-基材复合材;其中,植入的铜电极距离pet膜边缘的距离为1cm(通常为0.5-2cm);热压处理温度为250℃(通常为250-350℃);热压压力为5mpa(通常为2-10mpa);热压固化(亚胺化)时间为45min(通常为30-60min)。第一绝缘基材表面涂覆粘接剂后进行烘烤处理,在高温条件下,第一粘接剂热塑性聚酰亚胺(pi)预聚体(聚酰胺酸)形成半固化的聚酰胺酸膜;所述热压处理是粘接剂热塑性聚酰亚胺(pi)预聚体(聚酰胺酸)在高温条件下压合,交联反应,亚胺化,并固化。第一绝缘基材除了选择pet膜之外,其余如pi膜、pen膜、pp膜等均适用于本发明,优选为pet膜。第一粘接剂除了热塑性聚酰亚胺(pi)预聚体之外,本领域中其他现有已知的用于柔性线路板的衬底与铜箔粘接固定的胶粘剂均适用于本发明,例如丙烯酸胶粘剂或环氧胶粘剂。第一胶粘剂主要作用为粘接固定铜电极在pet等衬底表面,要求具有较佳的抗剥离特性(胶粘剂与pet等衬底,以及胶粘剂与铜电极之间),以及具有较好的耐温特性(耐120℃(优选为140℃)以上高温,满足银浆和石墨烯发热层烘烤条件)因此,常用的胶粘剂应优选环氧和丙烯酸胶粘剂。第一粘接剂通常耐120℃(优选为140℃)以上高温。3、制备石墨烯-铜电极-基材复合材如图2,在铜电极-基材复合材的表面,在对称的2个铜电极的相对的内侧,采用丝网印刷的方法,涂覆发热浆料石墨烯浆料,并将铜电极-基材复合材置于烘箱中进行发热浆料烘干处理,石墨烯浆料在铜电极-基材复合材的表面固化成石墨烯发热干膜3,制成石墨烯-铜电极-基材复合材,如图2,其中,石墨烯发热干膜与铜电极相平行的边缘与铜电极之间的距离为1cm(通常为0.5-2cm);石墨烯发热干膜与铜电极相平行的边缘与铜电极之间的区域为预留的桥接电极区域,用于印刷桥接电极,形成的2个预留的桥接电极区域相互平行、彼此相对,桥接电极区域的宽度为1cm(通常为0.5-2cm);发热浆料烘干处理温度为150℃(通常为50-180℃),烘干处理时间为20min(通常为1-60min);石墨烯发热干膜的厚度为20μm(通常为10-100μm);其中,石墨烯浆料按照如下方法制备而成:将发热材料石墨烯、树脂胶粘剂、溶剂混合,并分散均匀,其中:发热材料的质量百分比浓度为20wt%(通常为5-60wt%),树脂胶粘剂的质量百分比浓度为10wt%(通常为5-30wt%);树脂胶粘剂为丙烯酸树脂;溶剂为水;发热材料以石墨烯为例,除了石墨烯之外,发热材料还可以为石墨烯与碳纳米管、石墨炔、炭黑、石墨、金属颗粒或金属纳米线中的一种或多种的组合,例如石墨烯与碳纳米管;石墨烯与石墨炔、炭黑;石墨烯与碳纳米管、石墨、金属颗粒等;树脂胶粘剂除了丙烯酸树脂之外,其他本领域中现有已知的胶粘剂均适用于本发明,例如环氧树脂、饱和聚酯树脂、聚氨酯树脂;溶剂除了水之外,其他本领域中现有已知的溶剂均适用于本发明,例如氮甲基吡咯烷酮(nmp)、乙醇、异丙醇、甘油、松油醇、乙二醇乙醚醋酸酯或邻苯二甲酸二丁酯。制备的石墨烯浆料中发热材料的质量百分比浓度为5-60wt%均适用于本发明。4、印刷桥接电极采用凹版印刷的方法,在石墨烯-铜电极-基材复合材表面的预留的2个桥接电极区域内部(即石墨烯发热干膜和铜电极之间的位置内部)涂覆银浆,连接石墨烯发热干膜和铜电极,如图2;接着在温度为150℃(通常为50-180℃)下进行银浆电极烘干处理,银浆电极烘干时间为20min(通常为1-60min),银浆固化,形成银浆电极(即桥接电极)4,固化后的银浆电极的两端分别包覆铜电极和石墨烯发热干膜边缘的上表面,形成具有良好电连接性能、抗剥离性能的铜/银浆-石墨烯-基材复合体。其中银浆为银粉颗粒度为1~3μm,银粉固含量达70%(通常为50%以上,优选为60-75%)的高导电银浆;固化后厚度为25μm(通常为5-50μm),方阻达10mohm/sq(通常为5-50mohm/sq);本领域中现有已知的银导电浆料、铜导电浆料等高导电浆料均适用于制备本发明的桥接电极。5、封装处理在第二绝缘基材5(pet膜)的表面预涂布第二粘接剂6(eva热熔胶),并于温度100℃(通常为50-140℃)下烘烤5min(通常为1-20min),形成半固化膜;接着采用自动覆合机将铜/银浆-石墨烯-基材复合体与表面涂布第二粘接剂的第二绝缘基材覆合,进行封装处理,覆合封装通过热辊覆合,即在温度为120℃(通常为100-180℃),压力为0.7mpa(通常为0.2-10mpa)下直接辊压覆合1min(通常为0.5-5min);将石墨烯发热干膜、铜电极、银浆电极覆合封装在第一、第二绝缘基材内部,制得完备的地暖用石墨烯电热膜,如图3。第二粘接剂以eva热熔胶为例,其他本领域中现有已知的粘接剂均适用于本发明,例如丙烯酸胶粘剂或环氧胶粘剂等。本发明封装步骤的第二粘接剂与植入铜电极步骤的第一粘接剂可以相同,也可以不同。第二粘接剂通常采用eva胶粘剂膜作为主要胶粘剂,因为eva胶粘剂膜使用方便,性价比高,工艺简单,直接采用自动化设备,采用一步工艺,覆膜粘接的方法可以实现第二衬底和待封装结构的自动化封装。且地暖电热膜使用温度一般为50℃以下,因此第二粘接剂无需耐高温。封装处理后的石墨烯电热膜收成卷,然后根据地暖生产的需求,截取一定的长度,随后通过在铜电极上焊接/或铆接的方法,将电热膜温控器与电热膜互相连接,并通过温控器连接至外接电源,即可实现电热膜工作状态通断电及温度控制。实施例21、粗化处理除了微蚀液选用双氧水-硫酸体系,其中双氧水和硫酸总浓度为105g/l,双氧水与硫酸的浓度比为:1:2.5,双氧水浓度为30g/l,硫酸浓度为75g/l,反应温度为25℃,铜箔运动速度为3m/min,刻蚀时间为100s,粗化铜箔表面的粗糙度ra为2.5±0.5μm除此之外,其余与实施例1相同。2、铜电极的植入处理除了第一粘接剂为环氧树脂胶粘剂,烘烤温度为100℃(通常为50-200℃,优选为50-140℃);烘烤5min(通常为1-20min);对称放置的2条粗化铜箔(条)距离第一绝缘基材pet膜的边缘1.5cm;植入的铜电极距离pet膜边缘的距离为1.5cm(通常为0.5-2cm);热压处理温度为180℃(通常为140-350℃,优选为140-200℃);热压压力为5mpa(通常为2-10mpa);热压固化时间为30min(通常为30-60min)之外,其余与实施例1相同。本实施例中第一粘接剂还可以选择本领域常用的丙烯酸胶粘剂。3、制备石墨烯-铜电极-基材复合材除了采用高精度涂布机在铜电极-基材复合材上涂布发热浆料石墨烯浆料;桥接电极区域的宽度为0.5cm(通常为0.5-2cm);发热浆料烘干处理温度为120℃(通常为50-180℃)下烘烤40min(通常为1-60min);石墨烯发热干膜的厚度为15μm(通常为10-100μm);石墨烯浆料中发热材料石墨烯浓度为15wt%(通常为5-60%),树脂胶粘剂为的质量百分比浓度为8wt%(通常为5-30wt%);发热材料选择石墨烯与碳纳米管、炭黑,其中石墨烯、碳纳米管、炭黑的质量之比为100:40:90(通常为100:(5-80):(60-100));树脂胶粘剂为聚氨酯胶粘剂之外,其余与实施例1相同。4、印刷桥接电极除了采用丝网印刷法印刷银浆电极(即桥接电极);桥接电极烘干处理温度为130℃(通常为50-180℃);烘干40min(通常为1-60min);除此之外,其余与实施例1相同。5、封装处理除了在第二绝缘基材pet膜的表面涂布第二粘接剂丙烯酸胶粘剂;于温度90℃(通常为50-140℃)下烘烤5min(通常为1-20min);覆合封装处理过程中热辊覆合温度为150℃(通常为100-180℃),压力为0.7mpa(通常为0.2-10mpa);热辊覆合时间为1min(通常为0.5-5min);在热辊覆合处理之后,再采用高温烘烤进行固化,固化温度为150℃(通常为120-200℃),固化时间为30min(通常为5-60min)之外,其余与实施例1相同。实施例31、粗化处理除了微蚀液选用双氧水-硫酸体系,其中双氧水和硫酸总浓度为135g/l,双氧水与硫酸浓度比为:1:3.5,双氧水浓度为30g/l,硫酸浓度为105g/l,反应温度为30℃,铜箔(条)运动速度为2.5m/min,刻蚀时间为100s,粗化铜箔表面的粗糙度ra为3.5±0.5μm之外,其余与实施例1相同。2、铜电极的植入处理除了第一粘接剂为丙烯酸树脂粘接剂;烘箱中的烘烤温度为80℃(通常为50-200℃,优选为50-140℃);烘烤10min(通常为1-20min);对称放置的2条粗化铜铜箔(条)距离第一绝缘基材pet膜的边缘0.5cm;植入的铜电极距离pet膜边缘的距离为0.5cm(通常为0.5-2cm);热压处理温度为150℃(通常为140-350,优选为140-200℃);热压压力为3mpa(通常为2-10mpa);热压固化时间为40min(通常为30-60min)之外,其余与实施例2相同。3、制备石墨烯-铜电极-基材复合材除了采用凹版印刷机在铜电极-基材复合材上涂布发热浆料石墨烯浆料;桥接电极区域的宽度为1.5cm(通常为0.5-2cm);发热浆料烘干处理温度为140℃(通常为50-180℃)下烘烤20min(通常为1-60min);石墨烯发热干膜的厚度为20μm(通常为10-100μm);石墨烯浆料中发热材料浓度为25wt%(通常为5-60wt%),树脂胶粘剂的质量百分比浓度为15wt%(通常为5-30wt%)之外,其余与实施例1相同。4、印刷桥接电极除了采用丝网印刷法印刷银浆电极(即桥接电极);桥接电极烘干处理温度为140℃(通常为50-180℃);烘干30min(通常为1-60min)之外,其余与实施例1相同。5、封装处理除了在第二绝缘基材pet膜的表面涂布第二粘接剂环氧树脂胶粘剂;于温度90℃(通常为50-140℃)下烘烤10min(通常为1-20min);在覆合过程中控制热辊覆合温度为150℃(通常为100-180℃),压力为0.7mpa(通常为0.2-10mpa);热辊覆合时间为1min(通常为0.5-5min);随后采用高温烘烤进行固化,固化条件为温度为150℃(通常为120-200℃),时间为30min(通常为5-60min)之外,其余与实施例1相同。实施例41、粗化处理除了微蚀液选用双氧水-硫酸体系,其中双氧水和硫酸总浓度为135g/l,双氧水与硫酸浓度比为:1:3.5,其中双氧水浓度为30g/l,硫酸浓度为105g/l,反应温度为30℃,铜箔运动速度为2.5m/min,刻蚀时间为100s,粗化铜箔表面的粗糙度ra为3.5±0.5μm之外之外,其余与实施例1相同。2、铜电极的植入处理除了第一绝缘基材pet膜表面涂覆的第一粘接剂为丙烯酸胶粘剂;烘箱中的烘烤温度为100℃(通常为50-200℃,优选为50-140℃)下烘烤10min(通常为1-20min);对称放置的2条粗化铜铜箔(条)距离第一绝缘基材pet膜的边缘0.5cm;植入的铜电极距离pet膜边缘的距离为2cm(通常为0.5-2cm);热压处理温度为150℃(通常为140-350℃,优选为140-200℃);热压压力为3mpa(通常为2-10mpa);热压固化时间为40min(通常为30-60min)之外,其余与实施例2相同。3、制备石墨烯-铜电极-基材复合材除了采用凹版印刷机在铜电极-基材复合材上涂布发热浆料石墨烯浆料;桥接电极区域的宽度为2cm(通常为0.5-2cm);发热浆料烘干处理温度为135℃(通常为50-180℃)下烘干30min(通常为1-60min);石墨烯发热干膜的厚度为25μm(通常为10-100μm);石墨烯浆料中发热材料浓度为30wt%(通常为通常为5-60wt%),树脂胶粘剂的质量百分比浓度为12wt%(通常为5-30wt%);发热材料选择石墨烯与碳纳米管,其中石墨烯与碳纳米管的质量之比:100:60(通常为100:(5-80));树脂胶粘剂为丙烯酸胶粘剂之外,其余与实施例1相同。4、印刷桥接电极除了采用凹版印刷机印刷银浆(即桥接电极);烘干处理温度为135℃(通常为50-180℃);烘干30min(通常为1-60min)之外,其余与实施例1相同。5、封装处理除了在第二绝缘基材pet膜的表面涂布第二粘接剂eva胶粘剂;于温度80℃(通常为50-140℃)下烘烤10min(通常为1-20min);在覆合过程中热辊覆合温度为135℃(通常为100-180℃),压力为0.6mpa(通常为0.2-10mpa)下直接辊压覆合0.5min(通常为0.5-5min)之外,其余与实施例1相同。对照例1对照例1为传统石墨烯地暖电热膜制造方法,其主要方法步骤为:1)在pet表面印刷石墨烯发热层,并制备成干膜;发热材料石墨烯浆料与实施例1步骤3)中使用的石墨烯浆料相同;2)在石墨烯发热层边缘印刷制备银浆电极,形成pet-石墨烯-银电极复合结构;银浆与实施例1步骤4)中使用的银浆相同;3)采用覆合机,将pet-石墨烯-银电极与铜电极、eva胶膜和pet封装基材进行复合,并确保铜电极一部分与银浆电极进行接触,铜电极直接压合并硬接触在银电极之上。实验例1地暖用石墨烯电热膜铜电极与银电极之间的接触电阻测试实验采用中华人民共和国国家军用标准(简称国军标)gjb360b-2009《电子及电气元件试验方法》中方法307接触电阻测试方法,对实施例1-4制备的石墨烯地暖电热膜、对照例1制备的传统石墨烯地暖电热膜,测定电热膜中铜电极与银电极接触电阻,测定结果如表1所示。表1地暖用电热膜中铜电极与银电极之间的接触电阻测定结果接触电阻(ω)接触电阻(ω)实施例10.007实施例40.008实施例20.008对照例10.12实施例30.007实验例2地暖用石墨烯电热膜的抗剥离性能测试采用中华人民共和国国家标准gbt9286-1998《色漆和清漆-划格试验》对实施例1-4制备的石墨烯地暖电热膜、对照例1制备的传统石墨烯地暖电热膜,测定电热膜中银电极在铜电极表面的附着力,测定结果如表2所示。表2地暖用电热膜中铜电极与银电极之间的附着力测定结果附着力等级附着力等级实施例11实施例41实施例21对照例15实施例31对照例1由于银浆与铜电极为硬接触,故银浆在铜电极表面没有附着力,附着力等级最差。本发明上述实施例仅是范例性的,并不对本发明的范围构成任何限制。本领域技术人员应该理解的是,在不偏离本发明的精神和范围下可以对本发明技术方案的细节和形式进行修改或替换,但这些修改和替换均落入本发明的保护范围内。当前第1页12