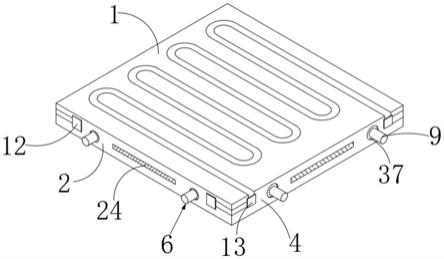
t型孔树脂塞孔板及其制备方法
技术领域
1.本发明属于pcb板技术领域,具体涉及t型孔树脂塞孔板;本发明还涉及t型孔树脂塞孔板的制备方法。
背景技术:2.pcb行业内,树脂塞孔板是最为常见的pcb板之一,树脂塞孔的方法成为缩小pcb设计尺寸,配合装备元器件的重要方法之一,其设计构思和可规模化的生产在pcb的制作领域发挥了极大的推动力,有效的提高hdi、厚铜、背板等产品的可靠性和制作工艺能力;
3.但是现有的树脂塞孔板大多是是有一定的规格尺寸的,但是在实际的使用过程中,无法根据实际的情况进行拼接使用,为此我们提出t型孔树脂塞孔板及其制备方法来解决现有技术中存在的问题。
技术实现要素:4.本发明的目的在于提供t型孔树脂塞孔板及其制备方法,以解决上述背景技术中提出现有技术中在实际的使用过程中,无法根据实际的情况进行拼接使用的问题。
5.为实现上述目的,本发明采用了如下技术方案:
6.t型孔树脂塞孔板,包括塞孔板本体,所述塞孔板本体分别包括第一侧壁、第二侧壁、第三侧壁以及第四侧壁,所述第一侧壁与第三侧壁相对应设置,所述第二侧壁与第四侧壁相对应设置,两组所述塞孔板本体之间通过固定结构连接固定,所述固定组件包括插接固定组件和套装定位组件,所述插接固定组件安装于第一侧壁和第三侧壁上,所述套装定位组件安装于第二侧壁和第四侧壁上;
7.所述插接固定组件包括溢出槽和插接柱,所述插接柱固定于溢出槽的内底部,且所述插接柱与溢出槽呈同心设置;
8.所述套装定位组件包括开设在第二侧壁和第四侧壁上的插接盲孔和粘合胶层,所述粘合胶层设置位于插接盲孔的内壁上;
9.所述第一侧壁上设置有第一凸片导电组件,所述第三侧壁上设置有第二凸片导电组件,所述第二侧壁上设置有与第一凸片导电组件相配合的第一凹片导电组件,所述第四侧壁上设置有与第二凸片导电组件相配合的第二凹片导电组件。
10.优选的,所述第一凸片导电组件包括第一凸片和第二凸片,所述第二凸片导电组件包括第三凸片和第四凸片,所述第三凸片与塞孔板本体上的沉铜线路的输入端电性连接,且所述第一凸片与第三凸片通过设置在第一侧壁和第三侧壁上的沉铜线路电性连接。
11.优选的,所述第一凹片导电组件包括第一凹片和第二凹片,所述第二凹片导电组件包括第三凹片和第四凹片,所述第三凹片和第四凹片分别与塞孔板本体上的沉铜线路的输入端和输出端电性连接,所述第一凹片与第三凹片电性连接,且所述第二凹片与第四凹片电性连接。
12.优选的,所述第一侧壁和第三侧壁上均设置有双面粘合胶带,所述第二侧壁和第
四侧壁与双面粘合胶带相对应位置设置有粘合毛面。
13.优选的,所述塞孔板本体包括基板、第一铝板和第二铝板,所述第一铝板和第二铝板分别贴合于基板上下表面,所述基板上等距阵列开设有t形塞孔,所述第一铝板上开设有与t形塞孔位置相对应的过孔。
14.优选的,所述第一铝板包括两种规格,具体为:
15.1)当孔径≤0.35mm,铝片孔比t形塞孔孔径>0.05mm;
16.2)当孔径>0.40mm,铝片孔与t形塞孔孔径等大。
17.优选的,所述固定结构包括两组对称设置的固定板,所述塞孔板本体的第一侧壁和第三侧壁上均设置有第一凸台,所述第二侧壁和第四侧壁上均设置有第二凸台,所述第一凸台与第二凸台的长度之和与固定板的长度相同,所述固定板通过螺钉分别与第一凸台和第二凸台连接固定。
18.优选的,所述第一凸台和第二凸台上均开设有螺纹孔,所述固定板上开设有与螺纹孔相对应的沉头孔,且所述螺钉的一端穿过沉头孔螺纹连接于螺纹孔内部。
19.优选的,所述第一凸台与第二凸台的连接端面上设置有电性连接块,所述电性连接块设置有两组,且两组所述电性连接块分别与塞孔板本体上的沉铜线路的输入端和输出端电性连接,所述第二凸台上开设有电性连接插孔,所述电性连接插孔内设凹字形导电块,且所述导电块设置有两组,且两组所述导电块分别与塞孔板本体上的沉铜线路的输入端和输出端电性连接。
20.t型孔树脂塞孔板的制备方法,包括如下步骤:
21.s1、t型孔pcb的制备:开料、图形转移、层压、钻孔、孔金属化、控深钻或背钻;树脂塞孔板塞孔前过前处理其中:酸洗,浓度5
‑
10%烘干板面,再立式炉烤板:150℃x30分钟,抽检板面及孔内是否有污染物及水渍残留;
22.s2、装冶具准备两种塞孔铝片:
23.1)当孔径≤0.35mm,铝片孔比塞孔孔径>0.05mm;
24.2)当孔径>0.40mm,铝片孔与塞孔孔径等大;
25.3)当板有大小孔径相差0.2mm时铝片需分开钻,网版铝片无打折,无堵塞及脏物;
26.s3、第一次塞孔从背钻面塞孔,把做好之铝片塞孔网架装在丝印机上锁紧,具体步骤为:
27.1)塞孔垫板与网版对准后装管位钉;
28.2)架机装网:将网版图形区置于台面中心区,调整网框夹将网版固定,并锁紧固定夹;
29.3)导气板安装:将工作板件与导气板对应好,生产板所塞孔与导气板钻孔必须对应重合以达到导气效果,并用定位钉固定;
30.4)对位调节:将操作控制设定为手动模式,把已装好的网版由对位孔用笔画圈定位于机台,拿塞孔垫板对位孔对准机台位定位圈固定好垫板,用片钉对准导气垫板对位孔后固定片钉,然后把工作板件贴上保护膜进行塞孔试塞,通过机台移位进行调整,确保下油点与工作板件的孔重合,完成精硧对位。
31.本发明的技术效果和优点:本发明提出的t型孔树脂塞孔板,与现有技术相比,具有以下优点:
32.1、本发明通过固定结构的设计,并将固定组件设置包括插接固定组件和套装定位组件,在使用时,能通过固定结构将多组塞孔板本体拼接使用,并且能将拼接后的塞孔板本体之间电性连接,使用方便;
33.2、本发明通过将固定结构设置包括两组对称设置的固定板,并通过螺钉将固定板固定于第一凸台和第二凸台上,连接牢固,并且通过电性连接块和电性连接插孔实现了多组塞孔板本体之间的电性连接关系。
附图说明
34.图1为本发明的t型孔树脂塞孔板结构示意图;
35.图2为本发明实施例1中两组塞孔板本体拼接时状态图;
36.图3为本发明实施例1中塞孔板本体的俯视结构剖视图;
37.图4为本发明塞孔板本体的结构示意图;
38.图5为本发明实施例2中两组塞孔板本体拼接时状态图。
39.图中:1、塞孔板本体;2、第一侧壁;3、第二侧壁;4、第三侧壁;5、第四侧壁;6、固定结构;7、插接固定组件;8、套装定位组件;9、插接柱;10、插接盲孔;11、粘合胶层;12、第一凸片导电组件;13、第二凸片导电组件;14、第一凹片导电组件;15、第二凹片导电组件;16、第一凸片;17、第二凸片;18、第三凸片;19第四凸片;20、第一凹片;21、第二凹片;22、第三凹片;23、第四凹片;24、双面粘合胶带;25、基板;26、第一铝板;27、第二铝板;28、t形塞孔;29、过孔;30、第一凸台;31、固定板;32、第二凸台;33、螺纹孔;34、电性连接块;35、电性连接插孔;36、导电块;37、溢出槽。
具体实施方式
40.下面将结合本发明实施例中的附图,对本发明实施例中的技术方案进行清楚、完整地描述,显然,所描述的实施例仅仅是本发明一部分实施例,而不是全部的实施例。此处所描述的具体实施例仅仅用以解释本发明,并不用于限定本发明。基于本发明中的实施例,本领域普通技术人员在没有做出创造性劳动前提下所获得的所有其他实施例,都属于本发明保护的范围。
41.本发明提供了如图1
‑
4所示的t型孔树脂塞孔板,包括塞孔板本体1,塞孔板本体1分别包括第一侧壁2、第二侧壁3、第三侧壁4以及第四侧壁5,第一侧壁2和第三侧壁4上均设置有双面粘合胶带24,第二侧壁3和第四侧壁5与双面粘合胶带24相对应位置设置有粘合毛面,第一侧壁2与第三侧壁4相对应设置,第二侧壁3与第四侧壁5相对应设置,其特征在于:两组塞孔板本体1之间通过固定结构6连接固定,固定结构6包括插接固定组件7和套装定位组件8,插接固定组件7安装于第一侧壁2和第三侧壁4上,套装定位组件8安装于第二侧壁3和第四侧壁5上;
42.插接固定组件7包括溢出槽37和插接柱9,插接柱9固定于溢出槽37的内底部,且插接柱9与溢出槽37呈同心设置;
43.套装定位组件8包括开设在第二侧壁3和第四侧壁5上的插接盲孔10和粘合胶层11,粘合胶层11设置位于插接盲孔10的内壁上;
44.第一侧壁2上设置有第一凸片导电组件12,第三侧壁4上设置有第二凸片导电组件
13,第二侧壁3上设置有与第一凸片导电组件12相配合的第一凹片导电组件14,第四侧壁5上设置有与第二凸片导电组件13相配合的第二凹片导电组件15;第一凸片导电组件12包括第一凸片16和第二凸片17,第二凸片导电组件13包括第三凸片18和第四凸片19,第三凸片18与塞孔板本体1上的沉铜线路的输入端电性连接,且第一凸片16与第三凸片18通过设置在第一侧壁2和第三侧壁4上的沉铜线路电性连接,第一凹片导电组件14包括第一凹片20和第二凹片21,第二凹片导电组件15包括第三凹片22和第四凹片23,第三凹片22和第四凹片23分别与塞孔板本体1上的沉铜线路的输入端和输出端电性连接,第一凹片20与第三凹片22电性连接,且第二凹片21与第四凸片19电性连接;通过固定结构6的设计,并将固定组件6设置包括插接固定组件7和套装定位组件8,在使用时,能通过固定结构6将多组塞孔板本体1拼接使用,并且能将拼接后的塞孔板本体1之间电性连接,使用方便;
45.塞孔板本体1包括基板25、第一铝板26和第二铝板27,第一铝板26和第二铝板27分别贴合于基板25上下表面,基板25上等距阵列开设有t形塞孔28,第一铝板26上开设有与t形塞孔28位置相对应的过孔29,第一铝板26包括两种规格,具体为:
46.1当孔径≤0.35mm,铝片孔比t形塞孔28孔径>0.05mm;
47.2当孔径>0.40mm,铝片孔与t形塞孔28孔径等大。
48.其中,塞孔板本体1的制备方法为:
49.s1、t型孔pcb的制备:开料、图形转移、层压、钻孔、孔金属化、控深钻或背钻;树脂塞孔板塞孔前过前处理其中:酸洗,浓度5
‑
10%烘干板面,再立式炉烤板:150℃x30分钟,抽检板面及孔内是否有污染物及水渍残留;
50.s2、装冶具准备两种塞孔铝片:1.当孔径≤0.35mm,铝片孔比塞孔孔径>0.05mm;2.当孔径>0.40mm,铝片孔与塞孔孔径等大,3.当板有大小孔径相差0.2mm时铝片需分开钻,网版铝片无打折,无堵塞及脏物;若发现有铝片网打折需报废重新做网,有堵塞需用钻咀捅穿,网版上机前需做清洁,真空塞孔机使用全新网版其中:新网框或旧网框均可以,但必须是新网纱拉的网版;也可使用0.3mm不含铜芯板蚀铜厚钻塞孔代替铝片塞孔,塞孔铝片及芯板开料比板子开料尺寸单边大15
‑
25mm;
51.刮胶选择:丝印塞树脂刮胶要求无缺口,无变形,长度比作业板件图型宽2~4cm,目前刮胶只能更换,不能研磨真空塞孔采用35mm厚度75
°
刮胶,根据实际刮胶使用情况选择研磨或者更换,每生产300
‑
400块改成每天检查一次刮刀是否有缺损;
52.导气板选择:所有塞孔板必须使用导气板,使用与铝片同一钻带钻孔,钻咀选用3.0mm,板厚3.0mm;需将板料底铜蚀成光板除去底板毛刺披锋;如出现孔密度过大可先采用3.0mm钻嘴钻,再用大钻嘴控深钻方式控深钻垫板,控深深度2.0mm,控深垫板需要加导气槽;
53.s3、第一次塞孔从背钻面塞孔,把做好之铝片塞孔网架装在丝印机上锁紧;塞孔垫板与网版对准后装管位钉;架机装网:将网版图形区置于台面中心区,调整网框夹将网版固定,并锁紧固定夹;导气板安装:将工作板件与导气板对应好,生产板所塞孔与导气板钻孔必须对应重合以达到导气效果,并用定位钉固定;对位调节:将操作控制设定为手动模式,把已装好的网版由对位孔用笔画圈定位于机台,拿塞孔垫板对位孔对准机台位定位圈固定好垫板,用片钉对准导气垫板对位孔后固定片钉,然后把工作板件贴上保护膜进行塞孔试塞,通过机台移位进行调整,确保下油点与工作板件的孔重合,完成精硧对位。
54.实施例2
55.与实施例1不同的地方在于,如图5所示,固定结构6包括两组对称设置的固定板31,塞孔板本体1的第一侧壁2和第三侧壁4上均设置有第一凸台30,第二侧壁3和第四侧壁5上均设置有第二凸台32,第一凸台30与第二凸台32的长度之和与固定板31的长度相同,固定板31通过螺钉分别与第一凸台30和第二凸台32连接固定;
56.第一凸台30和第二凸台32上均开设有螺纹孔33,固定板31上开设有与螺纹孔33相对应的沉头孔,且螺钉的一端穿过沉头孔螺纹连接于螺纹孔33内部,第一凸台30与第二凸台32的连接端面上设置有电性连接块34,电性连接块34设置有两组,且两组电性连接块34分别与塞孔板本体1上的沉铜线路的输入端和输出端电性连接,第二凸台32上开设有电性连接插孔35,电性连接插孔35内设凹字形导电块36,且导电块36设置有两组,且两组导电块36分别与塞孔板本体1上的沉铜线路的输入端和输出端电性连接,通过将固定结构6设置包括两组对称设置的固定板31,并通过螺钉将固定板31固定于第一凸台30和第二凸台32上,连接牢固,并且通过电性连接块34和电性连接插孔35实现了多组塞孔板本体1之间的电性连接关系。
57.最后应说明的是:以上所述仅为本发明的优选实施例而已,并不用于限制本发明,尽管参照前述实施例对本发明进行了详细的说明,对于本领域的技术人员来说,其依然可以对前述各实施例所记载的技术方案进行修改,或者对其中部分技术特征进行等同替换,凡在本发明的精神和原则之内,所作的任何修改、等同替换、改进等,均应包含在本发明的保护范围之内。