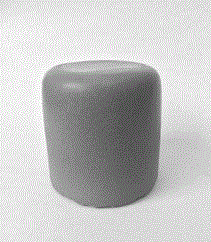
本发明涉及核工业领域,尤其是放射性污染废机油水泥固化技术领域,该方法能够用于核电行业放射性污染废机油水泥固化。
背景技术:在核工业领域,包括核设施和核电站运行过程中,会产生一定量的被放射性核素污染的废机油。该类机油主要包括压缩机油和真空泵油,这些有机介质会与放射性核素会形成相对稳定的络合物,而络合物的生成则增加了废机油的处理难度。目前,国际上处理放射性有机废液的方法主要包括焚烧法、高温高压处理方法、各种高级氧化方法等,然而前述方法工艺复杂、能耗高,对于设备要求苛刻,因此,难以实施。而我国国内缺少放射性废机油简单易行的有效处理方法,核工业领域仍存放有一定量的放射性污染废机油亟待处理。水泥固化法是将放射性污染废机油水泥固化成固化体后,放入中低放固体废物处置场的方法,其具有工艺简单、能耗低、投资少、安全可靠,且水泥固化体具有耐辐照和自屏蔽效应好等优点。然而,放射性废机油与水泥混合不能形成均匀的体系。如果将机油直接加入水泥中进行固化,机油将影响水泥水化反应过程,并最终导致制成的水泥固化体性能达不到国家标准GB14569.1-2011要求。因此,目前迫切需要一种新的方法,以解决上述问题。
技术实现要素:本发明的发明目的在于:针对目前采用水泥固化法处理废机油时,机油与水泥相容性差,难以获得满足国家标准GB14569.1-2011要求的包容废机油水泥固化体的问题,提供一种放射性废机油高强度水泥固化体的制备方法。本发明采用将机油与水乳化后进行水泥固化,同时在固化水泥配方中加入了粉煤灰、吸油树脂、木质纤维作为添加剂,加大水泥固化体的强度和降低放射性核素的浸出率。本发明能有效解决机油与水泥相容性问题,所制备的含有机物的水泥固化体性能优于国家标准GB14569.1-2011要求。本发明设计合理,操作方便,工艺简单,投资少,安全可靠,能够满足放射性废机油的处理要求,对于处理放射性废机油具有重要意义。为了实现上述目的,本发明采用如下技术方案:一种放射性废机油高强度水泥固化体的制备方法,包括如下步骤:(1)制备均质水包油乳液将乳化剂、机油、水混合后,高速搅拌,形成均质水包油乳液;(2)制备水泥浆料将水泥、粉煤灰混匀后,向其中加水湿润,形成水泥浆料;(3)制备水泥固化体将步骤1制备的均质水包油乳液、步骤2制备的水泥浆料、吸油剂、水泥体增强剂混合,搅拌均匀,经固化养护后,即得水泥固化体;所述步骤1中,机油、水、乳化剂的体积比为1~1.5:1~2:0.1~0.2;所述步骤2中,水泥、粉煤灰、水按质量比是1:0.05~0.1:0.1~0.2;所述步骤3中,步骤1制备的均质水包油乳液、步骤2中的水泥、吸油剂、水泥体增强剂的质量比为0.35~0.50:1:0.01~0.15:0.01~0.1。所述步骤1中,乳化剂为司苯、吐温、十二烷基苯磺酸钠、十二烷基硫酸钠、辛基酚聚氧乙烯醚中的两种或两种以上。所述步骤2中,水泥为普通硅酸盐水泥、铝酸盐水泥、火山灰水泥中的一种或多种。作为优选,所述步骤1中,机油、水、乳化剂的体积比为1~1.5:1:0.1。作为优选,所述步骤2中,水泥、粉煤灰、水按质量比是1:0.05~0.1:0.1。所述吸油剂为吸油树脂,所述水泥体增强剂为木质纤维。一种放射性废机油高强度水泥固化体的制备方法,包括如下步骤:(a)制备均质水包油乳液将乳化剂、机油、水混合后,高速搅拌,形成均质水包油乳液;(b)制备水泥浆料将水泥、粉煤灰、吸油剂、水泥体增强剂混匀后,向其中加水湿润,形成水泥浆料;(c)制备水泥固化体将步骤a制备的均质水包油乳液、步骤b制备的水泥浆料混合,搅拌均匀,经固化养护后,即得水泥固化体;所述步骤a中,机油、水、乳化剂的体积比为1~1.5:1~2:0.1~0.2;所述步骤c中,水泥固化体中各组分的质量比为均质水包油乳液:水泥:粉煤灰:吸油剂:水泥体增强剂=0.30~0.50:1:0.05~0.1:0.01~0.15:0.01~0.1。作为优选,所述步骤c中,水泥固化体中各组分的质量比为均质水包油乳液:水泥:粉煤灰:吸油剂:水泥体增强剂=0.42:1:0.05:0.03:0.01。针对前述问题,本申请提供一种放射性废机油高强度水泥固化体的制备方法。本发明中,首先利用乳化剂将机油与水乳化形成水包油型乳液(即均质水包油乳液),然后制备水泥浆料、固化,得到水泥固化体。经过实际测定,本发明中所获得水泥固化体的机油包容量大于15%,固化体抗压强度大,最大达12.6MPa,显著优于现有技术,其它各方面指标均满足国家标准GB14569.1-2011要求。本发明可用于核工业中低水平放射性污染废机油的固化处理,有效降低放射性废物管理的安全隐患,具有重要的意义。附图说明本发明将通过例子并参照附图的方式说明,其中:图1为实施例8所制备的样品图。图2为实施例9所制备的样品图。图3为采用现有方法制备的废油乳液图。图4为采用现有方法制备的固化体图。具体实施方式本说明书中公开的所有特征,或公开的所有方法或过程中的步骤,除了互相排斥的特征和/或步骤以外,均可以以任何方式组合。本说明书中公开的任一特征,除非特别叙述,均可被其他等效或具有类似目的的替代特征加以替换。即,除非特别叙述,每个特征只是一系列等效或类似特征中的一个例子而已。实施例1将废机油、乳化剂和水按体积比1:0.1:1.0的比例充分搅拌后,形成机油乳化液。将普通硅酸盐水泥、粉煤灰、吸油树脂、木质纤维按质量比1:0.05:0.03:0.01搅拌均匀后,形成水泥浆料。将上述水泥浆料与废机油乳化液按质量比1:0.5搅拌均匀,经固化养护后,得到的水泥固化体强度为8.9MPa。实施例2将废机油、乳化剂和水按体积比1:0.1:1的比例充分搅拌后,形成机油乳化液。将普通硅酸盐水泥、粉煤灰、水、吸油树脂、木质纤维按质量比1:0.05:0.1:0.03:0.01搅拌均匀后,形成水泥浆料。将上述水泥浆料与废机油乳化液按质量比1:0.5搅拌均匀,经固化养护后,得到的水泥固化体强度为11.3MPa。与实施例1相比,实施例2在制备水泥浆料的过程中,加入部分水,使水泥浆料湿润,其能够有效减少水泥浆料与废机油乳化液接触时,破乳现象的产生,最终显著提高水泥固化体的强度。实施例3将废机油、乳化剂和水按体积比1.0:0.1:1的比例充分搅拌后,形成机油乳化液。将普通硅酸盐水泥、粉煤灰、水按质量比1:0.05:0.1搅拌均匀后,形成水泥浆料。将上述水泥浆料与机油乳化液、吸油树脂、木质纤维按质量比1:0.5:0.025:0.008搅拌均匀,经固化养护后,得到的水泥固化体强度为11.2MPa。实施例3与实施例2相比,吸油树脂与木质纤维的添加顺序不同,但两者的实验结果无明显差异。这表明:吸油树脂与木质纤维先添加于水泥浆料中或最后添加,不会对水泥固化体本身产生影响。实施例4将废机油、乳化剂和水按体积比1.0:0.1:1.5的比例充分搅拌后,形成机油乳化液。将普通硅酸盐水泥、粉煤灰、水、吸油树脂、木质纤维按质量比1:0.05:0.1:0.03:0.01搅拌均匀后,形成水泥浆料。将上述水泥浆料与机油乳化液按质量比1:0.45搅拌均匀,经固化养护后,得到的水泥固化体强度为12.5MPa。实施例5将废机油、乳化剂和水按体积比1.3:0.1:1的比例充分搅拌后,形成机油乳化液。将普通硅酸盐水泥、粉煤灰、水、吸油树脂、木质纤维按质量比1:0.05:0.1:0.03:0.01搅拌均匀后,形成水泥浆料。将上述水泥浆料与废机油乳化液按质量比1:0.5搅拌均匀,得到的水泥固化体强度为9.3MPa。对比实施例1将废机油、乳化剂和水按体积比2:0.1:1的比例充分搅拌后,形成机油乳化液。将普通硅酸盐水泥、粉煤灰、水、吸油树脂、木质纤维按质量比1:0.05:0.1:0.03:0.01搅拌均匀后,形成水泥浆料。将上述水泥浆料与废机油乳化液按质量比1:0.5搅拌均匀,得到的水泥固化体强度为6.8MPa,该过程搅拌相对困难,上层少许浮油。通过实施例4、5与对比实施例1的比较,能够看出:采用本申请技术方案之外的方案,其固化强度难以满足相关的要求,不能用于放射性废机油的水泥固化处理。实施例6将废机油、乳化剂和水按体积比1.3:0.1:1的比例充分搅拌后,形成机油乳化液。将普通硅酸盐水泥、粉煤灰、水、吸油树脂、木质纤维按质量比1:0.05:0.1:0.03:0.01搅拌均匀后,形成水泥浆料。将上述水泥浆料与废机油乳化液按质量比1:0.4搅拌均匀,得到的水泥固化体强度为8.0MPa。本实施例中,乳化剂采用十二烷基苯磺酸钠与辛基酚聚氧乙烯醚复配而成。实施例7将废机油、乳化剂和水按体积比1.3:0.1:1的比例充分搅拌后,形成机油乳化液。将普通硅酸盐水泥、粉煤灰、水、吸油树脂、木质纤维按质量比1:0.05:0.1:0.03:0.01搅拌均匀后,形成水泥浆料。将上述水泥浆料与废机油乳化液按质量比1:0.55搅拌均匀,得到的水泥固化体强度为7.3MPa。养护后,该固化体上层有少许乳化液干燥的迹象。实施例8将废机油、乳化剂和水按体积比1.3:0.1:1的比例充分搅拌后,形成机油乳化液。将普通硅酸盐水泥、粉煤灰、水、吸油树脂、木质纤维按质量比1:0.1:0.1:0.07:0.05搅拌均匀后,形成水泥浆料。将上述水泥浆料与废机油乳化液按质量比1:0.5搅拌均匀,得到的水泥固化体强度为8.3MPa。对比实施例2将废机油、乳化剂和水按体积比2:0.1:1的比例充分搅拌后,形成机油乳化液。将普通硅酸盐水泥、粉煤灰、水、吸油树脂、木质纤维按质量比1:0.1:0.1:0.15:0.1搅拌均匀后,形成水泥浆料。将上述水泥浆料与废机油乳化液按质量比1:0.5搅拌均匀,得到的水泥固化体强度为7.8MPa,该过程浆料搅拌相对困难。实施例9将废机油、乳化剂和水按体积比1.3:0.1:1的比例充分搅拌后,形成机油乳化液。将火山灰水泥、粉煤灰、水、吸油树脂、木质纤维按质量比1:0.05:0.1:0.03:0.01搅拌均匀后,形成水泥浆料。将上述水泥浆料与废机油乳化液按质量比1:0.5搅拌均匀,得到的水泥固化体强度为12.6MPa。实施例10将废机油、乳化剂和水按体积比1.3:0.1:1的比例充分搅拌后,形成机油乳化液。将铝酸盐水泥、粉煤灰、水、吸油树脂、木质纤维按质量比1:0.05:0.1:0.03:0.01搅拌均匀后,形成水泥浆料。将上述水泥浆料与废机油乳化液按质量比1:0.5搅拌均匀得到的水泥固化体强度为8.6MPa。同时,申请人对上述实施例所得到的水泥固化体进行了测定,测定结构如表1所示。表1获得水泥固化体性能指标从表1的结果抗压看出,本发明中制备的废机油水泥固化体,抗压强度较高,浸出率较低,满足国家标准要求,具有较好的应用前景。对比实验一经过检索,申请人发现中国专利ZL201010534138.1(简称在先申请)公开了一种放射性有机废液水泥固化的方法,该专利与本发明的方法较为类似。为此,申请人依照中国专利ZL201010534138.1中提供的方法及配方,进行了废机油固化的验证实验。实验过程及结果如下:①乳化实验过程:将机油、常见复配乳化剂、水以体积比为1:(0.8~1):(0.15~0.3)混合,该比例条件下机油较难以形成均一的油水乳液,乳化后机油与水分层明显。②固化实验过程:将上述机油水混合液与水泥、沸石、石灰与常用水泥促凝剂CaCl2按专利(专利申请号:201010534138.1)公布配方比例进行固化。其中,图3为采用在先申请制备的废油乳液图,图4为采用该方法制备的固化体图,通过图3、4可以看出:油水不能均一乳液,固化体强度及28天后强度都不能满足国标要求。实验表明,该固化过程中,机油水混合液与水泥仍然难以相容,搅拌困难,最后形成的固化体强度及其它性能不能满足国家标准GB14569.1-2011要求,因此,该专利方法不适用于放射性废机油的水泥固化。通过对比可以看出,本发明能够有效实现放射性废机油的水泥固化,所制备的固化体具有较高的机械强度,且机油包容量大于15%,其他各项指标均满足国家标准GB14569.1-2011的要求。本发明并不局限于前述的具体实施方式。本发明扩展到任何在本说明书中披露的新特征或任何新的组合,以及披露的任一新的方法或过程的步骤或任何新的组合。