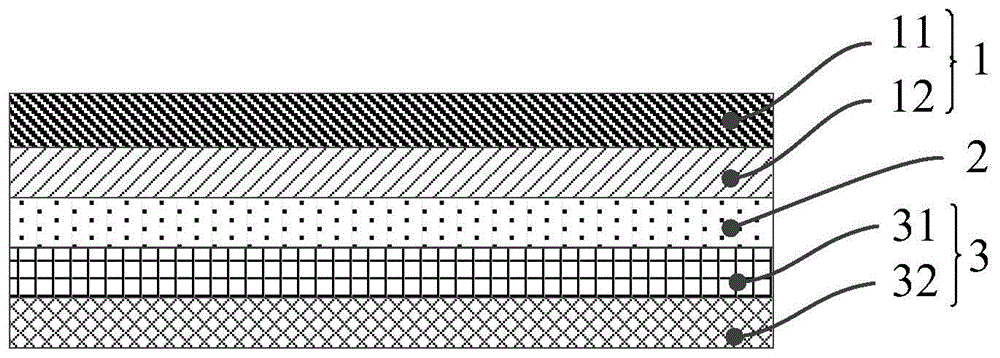
本实用新型属于锂离子电池包装
技术领域:
,具体涉及一种耐腐蚀聚酯复合薄膜和耐腐蚀铝塑复合膜。
背景技术:
:锂离子电池是目前常用的二次电池,已经广泛的应用于3c领域,随着电动汽车的发展,对大型锂离子电池的能量密度等提出了更高的要求,软包锂离子电池愈发得到电动汽车行业的青睐,对软包锂离子电池的外包装材料性能的要求也越来越高。电动汽车的电池组通常由多个电池包组成,电池组在汽车上使用时,路况、行驶环境等因素影响,可能会因碰撞等引起某个电池包或某几个电池包发生电解液泄漏。如果软包锂离子电池的外包装材料的耐腐蚀性或防潮性不高,单个电池包发生电解液泄漏则会损坏整个电池组的使用,从而使电动汽车无法正常行驶。目前所使用的锂离子电池外包装材料为复合材料,其结构组成依次为:外层基材层、第一粘结层、金属阻隔层、第二粘结层、热封层。外层基材层多选用聚酯,金属阻隔层一般采用铝箔,热封层多选用聚丙烯。由于铝箔需要分别与外层基材层和热封层进行粘结,选用同一种粘合剂时,因外层基材层和热封层的材料性能不同,通常会在电池包装过程中引起用于铝塑膜的复合薄膜分层。为了提高电池包的耐腐蚀性,采用聚酯材料制作的外层基材层,具有较好的防潮性和耐腐蚀性,若单个电池发生电解液泄漏,可以有效防止其他电池铝塑膜的污染,特别适合于新能源汽车电池的应用。公告号为cn104205407b的中国实用新型专利公开了一种锂离子电池用封装材料,其具有由树脂膜构成的基材层以及在所述基材层的一个面上依次层叠的第一粘接层、金属箔层、防腐蚀处理层、第二粘接层及密封层,其中第一粘接层采用聚氨酯系粘接剂,第二粘结层采用马来酸酐接枝改性的聚丙烯系树脂。由于铝箔两面分别涂覆不同性能的粘合剂,为了保证用于铝塑膜的复合薄膜冷冲压成型的成型效果,使铝箔和外层基材层、铝箔和热封层在冲压后不分层,通常对于粘合剂的性能要求很高,且导致用于铝塑膜的复合薄膜的复合工艺很繁琐。为了优化用于铝塑膜的复合薄膜的生产工艺、实现同一粘合剂即可满足用于铝塑膜的复合薄膜生产的需求,需要提出一种能替代原有的外层基材层、且与热封层使用同一种粘合剂的用于铝塑膜的聚酯复合薄膜。技术实现要素:针对现有技术中锂离子电池的复合薄膜的不足,本实用新型的第一个目的在于提供一种耐腐蚀聚酯复合薄膜,第二个目的在于提供一种耐腐蚀铝塑复合膜。所述的一种耐腐蚀聚酯复合薄膜,与聚丙烯膜采用同种粘合剂复合于铝箔上,采用该聚酯复合薄膜作为外基材层制备铝塑复合膜,对粘合剂的要求较低,可以简化铝塑膜的生产工艺,且使铝塑膜具有较好的耐腐蚀性,满足动力汽车电池的对包装材料的应用要求。为实现上述目的,本实用新型的第一方面提供一种耐腐蚀聚酯复合薄膜,厚度为15-50μm,从上到下依次为表层、中间层和内层,其特征在于,所述一种耐腐蚀聚酯复合薄膜通过三泡法共挤成型得到;所述表层为聚酯层,所述表层的厚度为8-30μm,所述表层由第一聚酯层和第二聚酰胺层构成,所述第二聚酰胺层与所述中间层相连;所述中间层为胶黏剂层,所述中间层的厚度2-5μm;所述内层为树脂层,所述内层的厚度为5-15μm。优选的,所述第一聚酯层和第二聚酰胺层的厚度相同,所述第一聚酯层的厚度为4-15μm。优选的,所述第一聚酯层为聚对苯二甲酸乙二酯或聚萘二甲酸丁二醇酯。优选的,所述第二聚酰胺层为尼龙6、尼龙66或聚己二酰间苯二甲胺中的任一种。优选的,所述胶黏剂层为酸酐改性的共聚聚丙烯树脂或酸酐改性的乙烯丙烯酸酯树脂。优选的,所述树脂层为不饱和羧酸接枝聚丙烯树脂或聚丙烯树脂。优选的,所述树脂层由第一树脂层和第二树脂层构成,所述第一树脂层与中间层相连,其中,所述第二树脂层的厚度大于所述第一树脂层的厚度。进一步的,所述第二树脂层的厚度为3-9μm。本实用新型所述一种耐腐蚀聚酯复合薄膜的三泡法共挤成型生产工艺,其特征在于,包括如下步骤:a)、第一泡:多层共挤出膜管将第一聚酯层、第二聚酰胺层、胶黏剂层、树脂层对应的原料分别通过挤出机在高温下融化,并按照第一聚酯层、第二聚酰胺层、胶黏剂层、树脂层的顺序排布分层供给熔融料流,在模头内汇合,通过环状口模制成一个端部封闭的多层薄壁管坯,再通入压缩空气,使之吹胀到所需厚度的膜管,膜管的厚度为135-600μm;共挤出后进行快速冷却至室温,让膜管处于高度无规、无定形态,以利于双向拉伸;b)、第二泡:吹胀,双向拉伸冷却后的膜管加温至80-100℃后双向拉伸,拉伸比为:纵向3.0-4.0;横向:3.0-4.0;c)、第三泡:热定型处理拉伸后的膜管经牵引辊压平后在保持纵向和横向张力的情况下,进行退火热处理,热处理温度为100-180℃;d)、收卷:将热处理后的薄膜冷却,并进行裁剪、收卷得到聚酯复合薄膜成品。本实用新型的第二方面提供一种耐腐蚀铝塑复合膜,从上至下依次为外基材层、第一粘结层、金属阻隔层、第二粘结层和热封层,其特征在于,所述外基材层为上述任一所述的一种耐腐蚀聚酯复合薄膜,金属阻隔层为铝箔,热封层为聚丙烯薄膜,所述外基材层和所述热封层采用干法复合。优选的,所述第一粘结层和第二粘结层均为马来酸酐接枝改性的聚丙烯系树脂。本实用新型所述的一种耐腐蚀铝塑复合膜制备方法,其特征在于,包括以下步骤:(1)钝化:铝箔经碱洗和酸洗除去表面油污,再经铬酸盐溶液钝化处理后,作为金属阻隔层;(2)涂胶:在金属阻隔层的正反两面分别涂覆马来酸酐接枝改性的聚丙烯系树脂后得到第一粘结层和第二粘结层;(3)干复:将外基材层、热封层分别与第一粘结层和第二粘结层贴合后,在干式复合机上复合,并在60℃的烘箱内烘干,即得到铝塑复合膜半成品;(4)熟化:将步骤(3)制得的铝塑复合膜半成品放入熟化室于55℃熟化6小时,即得到一种耐腐蚀铝塑复合膜。与现有技术相比,本实用新型的优点在于:本实用新型的一种耐腐蚀聚酯复合薄膜和耐腐蚀铝塑复合膜,所述一种耐腐蚀聚酯复合薄膜从上到下依次为表层、中间层和内层,所述内层为树脂层;采用该聚酯复合薄膜作为外基材层制备的耐腐蚀铝塑复合膜,对粘合剂的要求较低,生产工艺简单、易于冷冲压成型,且具有一定的耐腐蚀性能,可适用于动力汽车电池的对包装材料的应用要求。附图说明图1为本实用新型的聚酯复合膜的结构示意图;图2为本实用新型中对比例1的结构示意图;图3为本实用新型中一种耐腐蚀铝塑复合膜的结构示意图。具体实施方式以下结合附图和具体实施例,对本实用新型做进一步说明。本实施例中所用的生产设备均为常规生产设备。本实施例中所用的马来酸酐接枝改性的聚丙烯系树脂为三井化学公司制造的商品名为“アドマー”。实施例1如图1所示,本实施例所述的一种耐腐蚀聚酯复合薄膜厚度为15μm,从上到下依次为表层1、中间层2和内层3,表层1由第一聚酯层11和第二聚酰胺层12组成,所述第一聚酯层11厚度为4μm,所述第二聚酰胺层12为4μm;中间层2为胶黏剂层,厚度为2μm;内层3由第一树脂层31和第二树脂层32组成,所述第一树脂层31厚度为2μm,所述第二树脂层32厚度为3μm;其中,所述第一聚酯层11为聚对苯二甲酸乙二酯,所述第二聚酰胺层12为尼龙6;所述胶黏剂层为酸酐改性的乙烯丙烯酸酯树脂;所述第一树脂层31为不饱和羧酸接枝聚丙烯树脂,所述第二树脂层32为聚丙烯树脂。本实用新型所述的用于铝塑膜的聚酯复合薄膜采用三泡法共挤成型,具体生产工艺如下:a)、第一泡:多层共挤出膜管将聚对苯二甲酸乙二酯、尼龙6、酸酐改性的乙烯丙烯酸酯树脂、不饱和羧酸接枝聚丙烯树脂和聚丙烯树脂分别通过对应的挤出机在高温下融化,按照第一聚酯层11/第二聚酰胺层12/中间层2/第一树脂层31/第二树脂层32的顺序排布分层供给熔融料流,在模头内汇合,通过环状口模制成一个端部封闭的多层薄壁管坯,再通入压缩空气,使之吹胀到所需厚度的膜管,膜管的厚度为135μm;共挤出后进行快速冷却至室温,让膜管处于高度无规、无定形态,以利于双向拉伸;b)、第二泡:吹胀,双向拉伸冷却后的膜管加温至80℃后双向拉伸,拉伸比为:纵向3.0;横向:3.0;c)、第三泡:热定型处理拉伸后的膜管经牵引辊压平后在保持纵向和横向张力的情况下,进行退火热处理,热处理温度为100℃;d)、收卷:将热处理后的薄膜冷却,并进行裁剪、收卷得到成品。如图3所示,将本实施例制得的一种耐腐蚀聚酯复合薄膜作为外基材层100制备成一种耐腐蚀铝塑复合膜,具体方法如下:(1)钝化:选用40μm厚铝箔经碱洗和酸洗除去表面油污,再经铬酸盐溶液钝化处理后,作为金属阻隔层200;(2)涂胶:在金属阻隔层200的正反两面分别涂覆马来酸酐接枝改性的聚丙烯系树脂后得到第一粘结层400和第二粘结层500;(3)干复:将外基材层100、热封层300分别与第一粘结层400和第二粘结层500贴合后,在干式复合机上复合,并在60℃的烘箱内烘干,即得到铝塑复合膜半成品;(4)熟化:将上述pet-铝箔膜放入熟化室于55℃熟化6小时,即得到易于冲压成型的铝塑复合膜。实施例2如图1所示,本实施例所述的一种耐腐蚀聚酯复合薄膜厚度为25μm,从上到下依次为表层1、中间层2和内层3,表层1由第一聚酯层11和第二聚酰胺层12组成,所述第一聚酯层11厚度为7μm,所述第二聚酰胺层12为7μm;中间层2为胶黏剂层,厚度为4μm;内层3由第一树脂层31和第二树脂层32组成,所述第一树脂层31厚度为3μm,所述第二树脂层32厚度为4μm;其中,所述第一聚酯层11为聚萘二甲酸丁二醇酯,所述第二聚酰胺层12为尼龙66;所述胶黏剂层为酸酐改性的乙烯丙烯酸酯树脂;所述第一树脂层31为聚丙烯树脂,所述第二树脂层32为不饱和羧酸接枝聚丙烯树脂。本实用新型所述的用于铝塑膜的聚酯复合薄膜采用三泡法共挤成型,具体生产工艺如下:a)、第一泡:多层共挤出膜管将聚萘二甲酸丁二醇酯、尼龙66、酸酐改性的乙烯丙烯酸酯树脂、聚丙烯树脂和不饱和羧酸接枝聚丙烯树脂分别通过对应的挤出机在高温下融化,按照第一聚酯层11/第二聚酰胺层12/中间层2/第一树脂层31/第二树脂层32的顺序排布分层供给熔融料流,在模头内汇合,通过环状口模制成一个端部封闭的多层薄壁管坯,再通入压缩空气,使之吹胀到所需厚度的膜管,膜管的厚度为300μm;共挤出后进行快速冷却至室温,让膜管处于高度无规、无定形态,以利于双向拉伸;b)、第二泡:吹胀,双向拉伸冷却后的膜管加温至100℃后双向拉伸,拉伸比为:纵向3.5;横向:3.4;c)、第三泡:热定型处理拉伸后的膜管经牵引辊压平后在保持纵向和横向张力的情况下,进行退火热处理,热处理温度为150℃;d)、收卷:将热处理后的薄膜冷却,并进行裁剪、收卷得到成品。如图3所示,将本实施例制得的一种耐腐蚀聚酯复合薄膜作为外基材层100制备成一种耐腐蚀铝塑复合膜,具体方法如下:(1)钝化:选用40μm厚铝箔经碱洗和酸洗除去表面油污,再经铬酸盐溶液钝化处理后,作为金属阻隔层200;(2)涂胶:在金属阻隔层200的正反两面分别涂覆马来酸酐接枝改性的聚丙烯系树脂后得到第一粘结层400和第二粘结层500;(3)干复:将外基材层100、热封层300分别与第一粘结层400和第二粘结层500贴合后,在干式复合机上复合,并在60℃的烘箱内烘干,即得到铝塑复合膜半成品;(4)熟化:将上述pet-铝箔膜放入熟化室于55℃熟化6小时,即得到易于冲压成型的铝塑复合膜。实施例3如图1所示,本实施例所述的一种耐腐蚀聚酯复合薄膜厚度为50μm,从上到下依次为表层1、中间层2、次内层和内层3,表层1由第一聚酯层11和第二聚酰胺层12组成,所述第一聚酯层11厚度为15μm,所述第二聚酰胺层12为15μm;中间层2为胶黏剂层,厚度为5μm;内层3由第一树脂层31和第二树脂层32组成,所述第一树脂层31厚度为6μm,所述第二树脂层32厚度为9μm;其中,所述第一聚酯层11为聚萘二甲酸丁二醇酯,所述第二聚酰胺层12为聚己二酰间苯二甲胺;所述胶黏剂层为酸酐改性的乙烯丙烯酸酯树脂;所述第一树脂层31为不饱和羧酸接枝聚丙烯树脂,所述第二树脂层32为不饱和羧酸接枝聚丙烯树脂。本实用新型所述的用于铝塑膜的聚酯复合薄膜采用三泡法共挤成型,具体生产工艺如下:a)、第一泡:多层共挤出膜管将聚萘二甲酸丁二醇酯、聚己二酰间苯二甲胺、酸酐改性的乙烯丙烯酸酯树脂、不饱和羧酸接枝聚丙烯树脂和不饱和羧酸接枝聚丙烯树脂分别通过对应的挤出机在高温下融化,按照第一聚酯层11/第二聚酰胺层12/中间层2/第一树脂层31/第二树脂层32的顺序排布分层供给熔融料流,在模头内汇合,通过环状口模制成一个端部封闭的多层薄壁管坯,再通入压缩空气,使之吹胀到所需厚度的膜管,膜管的厚度为600μm;共挤出后进行快速冷却至室温,让膜管处于高度无规、无定形态,以利于双向拉伸;b)、第二泡:吹胀,双向拉伸冷却后的膜管加温至85℃后双向拉伸,拉伸比为:纵向4.0;横向:4.0;c)、第三泡:热定型处理拉伸后的膜管经牵引辊压平后在保持纵向和横向张力的情况下,进行退火热处理,热处理温度为180℃;d)、收卷:将热处理后的薄膜冷却,并进行裁剪、收卷得到成品。如图3所示,将本实施例制得的一种耐腐蚀聚酯复合薄膜作为外基材层100制备成一种耐腐蚀铝塑复合膜,具体方法如下:(1)钝化:选用40μm厚铝箔经碱洗和酸洗除去表面油污,再经铬酸盐溶液钝化处理后,作为金属阻隔层200;(2)涂胶:在金属阻隔层200的正反两面分别涂覆马来酸酐接枝改性的聚丙烯系树脂后得到第一粘结层400和第二粘结层500;(3)干复:将外基材层100、热封层300分别与第一粘结层400和第二粘结层500贴合后,在干式复合机上复合,并在60℃的烘箱内烘干,即得到铝塑复合膜半成品;(4)熟化:将上述pet-铝箔膜放入熟化室于55℃熟化6小时,即得到易于冲压成型的铝塑复合膜。对比例1采用实施例1的方法制备一种铝塑膜,其不同之处在于:外基材层100选用15μm自制双向拉伸聚酯膜。对比例2采用对比例1的方法制备一种铝塑膜,其不同之处在于:第一粘结层400选用聚氨酯系粘结剂作为胶黏剂;第二粘结层500选用马来酸酐接枝改性的聚丙烯系树脂。对比例3采用对比例1的方法制备一种铝塑膜,其不同之处在于:外基材层100选用15μm自制双向拉伸聚酰胺膜。测试实验:(1)第一剥离强度测试:根据gb/t8808-1988《软质复合塑料材料剥离试验方法》,对实施例1-3和对比例1-3所制得的铝塑膜进行外基材层100和金属阻隔层200的层间剥离强度测试。(2)第二剥离强度测试:根据gb/t8808-1988《软质复合塑料材料剥离试验方法》,将实施例1-3和对比例1-3所制得的铝塑膜进行剥离强度测试金属阻隔层200和热封层300的层间剥离强度测试。(3)铝塑膜冷冲压成型测试:将实施例1-3和对比例1-3所制得的铝塑膜切成10mm*20mm大小的样品;将样品置于冲压机上进行测试,冲压机的参数设置:压力0.15-0.3mpa,速度20-40mm/s,保压时间2-3s。(4)表面耐腐蚀性测试:将实施例1-3和对比例1-3所制得的铝塑膜切成100cm*100cm,在表层的表面刷一层电解液,控制电解液的用量为4ml,置于40℃、80%rh的环境,放置24小时。擦去铝塑膜表面的电解液后,确认表层表面的腐蚀情况,并按如下的基准进行评价:“优”:未观察到表层表面的腐蚀情况;“合格”:基材层表面上的腐蚀面积小于等于总面积的15%;“不合格”:基材层表面上的腐蚀面积大于总面积的15%。表1性能测试实施例1实施例2实施例3对比例1对比例2对比例3第一剥离力/n555292第二剥离力/n666666冷冲压成型深度/mm677557表面耐腐蚀性测试优优优优优不合格由表1的性能测试结果可知,采用本实用新型的一种耐腐蚀聚酯复合薄膜作为外基材层时,制得的铝塑膜具有较高的剥离强度,且表面耐腐蚀性能优良,但冷冲压成型性较外基材层为聚酰胺薄膜时,略有下降。而采用自制双向拉伸尼龙膜作为铝塑膜的外基材层时,第一粘结层和第二粘结层采用同种粘合剂时,粘合效果不好,当冷冲压成型深度超过5mm时,会发生较为严重的层间剥离现象;第一粘结层和第二粘结层采用不同种粘合剂时,加工工艺较为复杂,且当冷冲压成型深度超过5mm时,也会一定程度发生层间剥离现象。以上已对本实用新型创造的较佳实施例进行了具体说明,但本实用新型创造并不限于所述实施例,熟悉本领域的技术人员在不违背本实用新型创造精神的前提下还可做出种种的等同的变型或替换,这些等同的变型或替换均包含在本申请权利要求所限定的范围内。当前第1页12