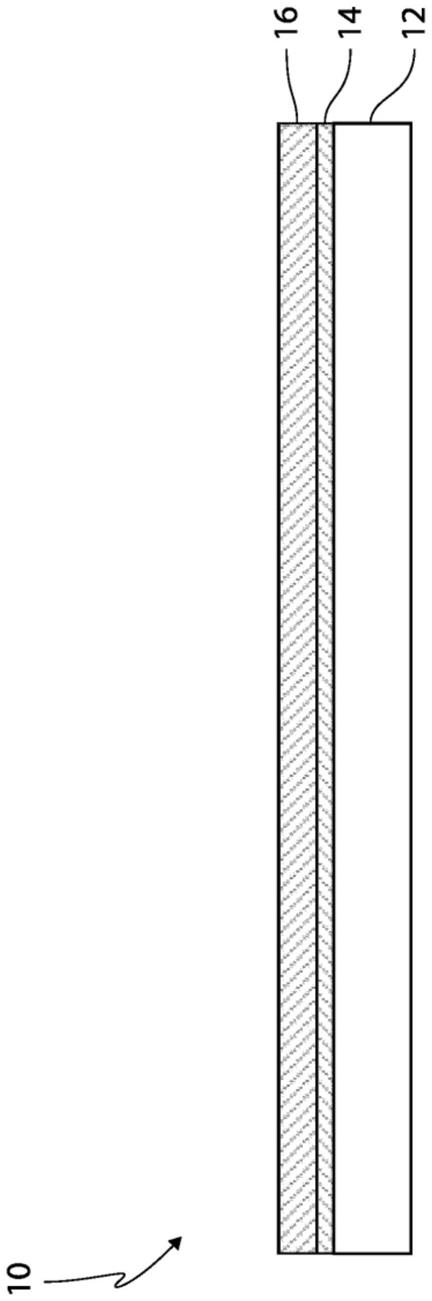
人造革产品及其生产方法
1.本发明涉及人造革(artificial leather),即在结构和外观上类似于天然革或合成革的革替代物。本发明还涉及一种用于生产人造革的方法,一种包括所述人造革的制品如服装,以及所述人造革在制造制品如服装以及例如还有家具、鞋、钱包、包、行李和衬里中的用途。特别地,所述人造革包括由韧皮纤维(bast fibre)形成的非织造毡(non-woven matt),更特别地由从大麻植物获得的纤维形成的非织造毡。所述非织造毡中的纤维浸渍有聚合物,例如聚酯或聚氨酯(pu)。所述人造革包括作为离散底层,即作为层压结构中的不同或单独的底层的所述非织造毡,该层压结构还包括粘合剂材料(例如pu)的离散中间层和涂层材料(例如pu涂层材料)的离散顶层。所述底层的厚度大于第一中间层或所述顶层中的任一个的厚度。所述顶层的厚度优选高于所述中间层的厚度。
2.常规的合成革由于其质地、外观、延展性、耐水性等而成为非常有吸引力的客户产品。这导致了广泛的用途或应用,例如在鞋、手提包、钱包等的生产中,然而,常规革的生产是化学密集型的,通常需要在鞣制过程中使用特别重的化学品。合成革的生产需要使用通常基于石油的人造纤维,因此产生显著的负面环境影响。
3.因此,已经存在合成革或人造革形式的不同解决方案,所述合成革部分地包括使用天然纤维,所述人造革是通过使用天然纤维(即基于植物的纤维,例如大麻纤维)作为原料生产的。
4.ep2893068a公开了由个体化韧皮纤维组成的非织造织物。通过在所述非织造织物的表面上涂覆聚合物材料的膜来将所述非织造织物形成为层压材料。
5.wo2010/044761a1公开了一种用于生产人造革的方法,所述人造革通过使用中间产品获得,所述中间产品是通过在泡沫机械中在空气的帮助下搅拌水基聚氨酯和/或丙烯酸、乳胶、染料和其他辅助化学品,以使其具有多孔结构而获得的。
6.cn206109852u公开了一种合成革,其中使用大麻纤维。所述合成革显示出不同的层,其形式为由可生物降解的大麻纤维和化学合成革纤维制成的第一非织造大麻纤维层,在其顶部涂覆第二亲水性pu层。该pu层涂覆有第三亲水性pu层,并且最后涂覆第四疏水性pu层。此外,在大麻纤维非织造织物中需要使用化学合成革纤维。还需要pu的发泡,以通过直接涂覆在大麻纤维非织造织物上来实现高厚度(0.35-0.4mm)的pu层(2),得到低厚度(0.95-1.05mm)的底层(1)。
7.ep25766881a公开了一种包括不同层的人造革,其中每个层包括茎材纤维和固化聚合物,并且其中这些层通过例如针刺机械地接合在一起。因此,该人造革是多层非织造叠层。
8.jph02145877a公开了一种制造合成革的方法,其包括使用tetron/人造丝作为底基织物,并解决了如何处理用于粘合和着色海绵层(对应于合成革的底层)的聚合物的问题。
9.现有技术至少没有提及提供具有层压结构的人造革,其中基材是非织造毡的韧皮纤维,特别是非织造毡的大麻纤维,而不使用化学合成革纤维,并且其中形成中间层的粘合材料层比形成顶层的pu涂层薄,即其中顶层比中间层厚。
10.因此,本发明的一个目的是提供人造革,其层状结构比现有技术的人造革产品更简单。
11.本发明的另一个目的是提供一种使用韧皮纤维作为原料生产人造革的方法,该方法比现有技术方法更简单。
12.本发明解决了这些和其它目的。
13.因此,在本发明的第一方面,提供了人造革,具有多个离散层形式的层压结构,
[0014]-所述多个层包括底层、中间层和顶层,
[0015]-所述底层为包括韧皮纤维的非织造毡,所述韧皮纤维浸渍有用于粘合和着色所述韧皮纤维的聚合物,并且所述底层限定底层厚度,
[0016]-所述中间层为粘合剂材料层,其中所述中间层与所述底层直接连接(即相邻)并且与所述顶层直接连接,以与所述顶层胶合,并且所述中间层限定中间层厚度,
[0017]-所述顶层为聚合物涂层并且限定顶层厚度,并且
[0018]-其中所述底层厚度大于所述第一中间层厚度或所述顶层厚度中的任一个,并且所述第一中间层厚度不同于所述顶层厚度。
[0019]
优选地,所述多个层仅包括底层、中间层和顶层。也就是说,所述人造革具有三个离散层。
[0020]
只有底层(其为基材)为非织造毡。
[0021]
在根据第一方面的实施例中,所述顶层的所述聚合物涂层选自丙烯酸涂料或乳胶漆、pvc、聚乙烯(pe)、聚丙烯(pp)或聚氨酯(pu)。优选地,所述聚合物涂层为pu。如本文所用,术语聚合物涵盖聚合物和共聚物两者。如本文所用,术语胶乳是指聚合物微粒在水中的悬浮液。
[0022]
通过提供不同厚度的涂层(中间层和顶层),得到人造革,其包含韧皮纤维的天然功能和性能,同时保持合成革的外观和性质。韧皮纤维是二氧化碳中性的,这意味着在这种韧皮纤维的生产中二氧化碳的净产量为零或负值。通过使用韧皮纤维代替在合成革的生产中已知的微纤维、聚酯、pvc或其他化学合成纤维,现在还可以以更环保的方式回收产品,例如通过生物降解产品并通过将其作为新的材料重新使用。因此能够通过尽可能长时间地使用韧皮纤维来维持生命周期。因此提供了合成革的环境友好替代品。此外,与诸如cn206109852u的现有技术相反,其中合成层的底层由包括使用化学合成革纤维的大麻非织造织物制成,并且由于pu的发泡,这种底层比相邻的中间层更薄,在本发明中,非织造毡由100%的韧皮纤维(例如大麻)制成,并且非织造毡浸渍有用于粘合和着色的聚合物,从而还提供了均匀的强度,这在cn206109852u中通过在大麻非织造织物的生产中使用化学合成革纤维而另外实现。
[0023]
在根据第一方面的实施例中,所述底层的所述韧皮纤维为大麻纤维并且浸渍有选自聚酯或pu的聚合物。因此,非织造毡包含浸渍有例如pu的纤维,pu用于提供纤维的颜色和粘合力。
[0024]
在根据第一方面的实施例中,所述中间层的所述粘合剂材料选自生物树脂、聚乙烯(pe)、聚丙烯(pp)或pu。优选地,粘合剂材料是pu。粘合剂材料用于涂覆和增强非织造毡以及粘合到顶层的pu涂层。
[0025]
在根据第一方面的实施例中,底层厚度为1-5mm,例如2-5mm,优选3mm,并且比所述
第一中间层厚度或所述顶层厚度中的任一个大5-30倍;并且所述顶层厚度比所述第一中间层厚度大1.5-4倍。通过使用比顶层更薄的中间层,已经发现保持了大麻的自然凉爽性能,同时可以获得人造革的柔软质地。顶层的厚度优选为0.1-0.3mm,中间层的厚度优选为0.1-0.2mm。尽管每层的较低范围被规定为0.1mm,但两层的厚度不同的条件仍然适用。中间层不是可喷涂胶乳、聚α-烯烃或乙烯乙酸乙烯酯形式的粘合剂,对于该粘合剂,在人造革中不形成可见的离散或不同的层。
[0026]
在根据第一方面的实施例中,所述底层在干燥条件下具有150-350g/m2的纤维密度、优选180-300g/m2,或在干燥条件下具有300-600g/m2的纤维密度、优选400-500g/m2;所述中间层在干燥条件下具有20-200g/m2的粘合剂材料密度、优选30-100g/m2;并且所述顶层在干燥条件下具有密度,优选30-200g/m2的pu密度,优选40-150g/m2。这使得能够实现均匀的顶层,同时保持中间层的足够的物理和粘合强度,而不损害大麻的自然冷却性质。
[0027]
在根据第一方面的实施例中,所述底层包括:
[0028]-65-90wt%的韧皮纤维,其平均纤维长度为4-80mm,优选10-30mm,
[0029]-0-5wt%的碎屑(shives),
[0030]-10-30wt%的固化树脂,优选纤维形式的树脂,例如纤维形式的生物树脂,
[0031]
其中所有上述的总和为100wt%,
[0032]
或者在可选的实施例中:
[0033]
所述底层(12)包括:
[0034]-95-100wt%的韧皮纤维,其平均纤维长度为4-80mm,优选10-30mm,
[0035]-0-5wt%的碎屑,
[0036]
其中上述总和为100wt%。
[0037]
因此,底层中的纤维仅是韧皮纤维,即底层特别不含合成纤维。
[0038]
在可选的实施例中,不使用树脂,例如纤维形式的生物树脂,从而进一步减少或完全消除在形成非织造毡时对合成化合物的需要。
[0039]
如本文所用,平均纤维长度表示按重量计的平均纤维长度。
[0040]
由于韧皮纤维浸渍有聚合物例如pu,因此韧皮纤维的上述重量百分比包括这种聚合物的重量。在非织造毡中使用的全部原料纤维是韧皮纤维,例如大麻纤维,因此能够产生更仿生人造革。如果使用固化树脂,则包括10-30wt%的固化树脂优选来自以纤维形式提供的树脂,更优选来自以纤维形式(即以熔融纤维的形式)提供的生物树脂。也可以使用具有双组分纤维的其他树脂,例如聚乙烯/聚丙烯纤维或聚酯/聚丙烯纤维。当与大麻纤维混合并固化时,生物树脂纤维和大麻纤维部分地熔融在一起,从而彼此粘附,如在非织造织物中那样。
[0041]
在第二方面,本发明提供了用于生产具有多个离散层形式的层压结构的人造革的方法,
[0042]-所述多个层包括底层、中间层和顶层,
[0043]-所述底层为包括韧皮纤维的非织造毡,所述韧皮纤维浸渍有用于粘合和着色所述韧皮纤维的聚合物,并且所述底层限定底层厚度,
[0044]-所述中间层为粘合剂材料层,其中所述中间层与所述底层直接连接并且与所述顶层直接连接,以与所述顶层胶合,并且所述中间层限定中间层厚度,
[0045]-所述顶层为聚合物涂层并且限定顶层厚度,并且
[0046]-其中所述底层厚度大于所述第一中间层厚度或所述顶层厚度中的任一个,并且所述第一中间层厚度不同于所述顶层厚度,
[0047]
所述方法包括以下步骤:
[0048]
(a)通过研磨一批原料韧皮纤维(raw bast fibre)直到达到平均纤维长度为2-100mm,优选4-80mm,形成纤维层,并从所述一批原料韧皮纤维中分离碎屑直到达到纤维层含量为0-3wt%,
[0049]
(b-1)在气流成网阶段中向所述纤维层中添加量为所述纤维层的10-30wt%的树脂,固化所述树脂,并通过压制形成未加工的非织造毡,或
[0050]
(b-2)梳理多个所述纤维层并交叉铺网以形成交叉铺网的多层布置,针刺所述交叉铺网的多层布置,并通过辊压形成未加工的非织造毡,(c)通过使所述未加工的非织造毡通过用于浸渍所述韧皮纤维的所述聚合物的轧染浴,形成包括浸渍有聚合物的韧皮纤维的所述非织造毡,
[0051]
(d)单独提供可剥离纸,在其上涂覆聚合物涂层以形成组合的可剥离纸-聚合物涂层,然后对其进行干燥步骤,
[0052]
(e)在步骤(d)的所述组合的可剥离纸-聚合物涂层的干燥聚合物涂层上涂覆粘合剂材料层,随后将包括浸渍有聚合物的韧皮纤维的所述非织造毡铺设在所述粘合剂材料层上,并对由此组合的可剥离纸-聚合物涂层-粘合剂材料层进行干燥步骤,并随后对所得干燥产品进行压延步骤,和
[0053]
(f)从步骤(e)中获得的所述产品移除所述可剥离纸。
[0054]
在根据第二方面的实施例中,在进行步骤(e)之前重复步骤(d)。
[0055]
在根据第二方面的实施例中,所述顶层的所述聚合物涂层选自丙烯酸涂料或乳胶漆、pvc、聚乙烯(pe)、聚丙烯(pp)或聚氨酯(pu)。优选地,所述聚合物涂层为pu。如上所述,术语聚合物涵盖聚合物和共聚物两者,并且术语胶乳是指聚合物微粒在水中的悬浮液。
[0056]
在根据第二方面的实施例中,在步骤(e)中,所述铺设包括浸渍有聚合物的韧皮纤维的所述非织造毡的步骤包括对所述毡进行压延步骤,优选在130-180℃,更优选在140-160℃下进行压延。当所述非织造毡被辊压到优选湿的粘合剂材料层上时,其在干燥步骤之前经过压延步骤,从而进一步确保与所述粘合剂材料层的直接接触以及产品的均匀性。此外,在步骤(e)中,所述对所得干燥产品进行压延步骤的最终步骤在130-180℃下进行,优选在140-160℃下进行。因此,在干燥步骤之后,进行最终压延步骤以提供非织造毡、粘合剂材料层和聚合物(例如pu)涂层的最终附接。在最终的人造革中,非织造毡成为底层,粘合剂材料层成为中间层,pu涂层成为顶层。
[0057]
在根据第二方面的另一个实施例中,步骤(e)中的所述压延步骤的任一个在3-6巴的压力下进行,优选在4巴的压力下进行。
[0058]
在根据第二方面的实施例中,在步骤(a)之前或结合步骤(a),所述方法包括对所述原料韧皮纤维进行去皮。去皮是指压碎和敲击所述一批韧皮纤维中包含的原料韧皮纤维。该批料优选以一捆原料韧皮纤维的形式提供。通常,还对原料纤维进行脱胶步骤,其中通过除去导致原料纤维粘在一起的“胶”来尽可能地分离纤维。这通常是通过在koh或naoh的水溶液中清洁原料纤维来完成的。通过本发明,已经发现可以省略这种脱胶步骤。
[0059]
在根据第二方面的实施例中,步骤(b-1)包括在130-200℃,优选170-180℃,更优选175℃的固化烘箱中固化所述树脂,并且步骤(b-1)还包括在固化所述树脂之后,压制所述未加工的非织造毡直至达到在干燥条件下纤维密度为150-400g/m2,优选180-300g/m2。如上所述,树脂优选是生物树脂,例如纤维形式的生物树脂,即熔融纤维形式的生物树脂。树脂包括双组分纤维,例如聚乙烯/聚丙烯纤维或聚酯/聚丙烯纤维;参见例如:https://www.fibervisions.com/products/bicomponent-products。当与大麻纤维混合并固化时,生物树脂纤维和大麻纤维部分地熔融在一起,从而彼此粘附,如在非织造织物中那样。
[0060]
固化后的压制使得能够将材料压实到上述纤维密度,而气流成网赋予非织造毡均匀性和细度。非织造毡的厚度为1-5mm,然后优选卷绕成1-2m的卷。适用于后续处理步骤。
[0061]
代替步骤(b-1),进行梳理、交叉铺网和针刺的组合,即步骤(b-2)。梳理和交叉铺网使得能够控制纤维层中纤维的方向,而针刺将纤维缠绕在一起,使得实现非织造毡的适当强度,而不需要如步骤(b-1)中那样使用例如生物树脂。
[0062]
在特定实施例中,在针刺步骤(28”')之前,涂覆覆盖材料,例如天然纤维层或植物基塑料材料,例如pla(聚乳酸)。在另一个特定实施例中,在交叉铺网之后和针刺之前,交叉铺网的纤维层可以通过纤维层重新排列步骤,例如粘着步骤,由此纤维层在垂直方向上移动,使得纤维层在进行所述针刺之前和/或在涂覆所述覆盖材料之前适当地对齐。
[0063]
在根据第二方面的实施例中,在步骤(c)中,用于浸渍所述韧皮纤维的所述聚合物优选为聚氨酯(pu),并且步骤(c)在所述轧染浴之后包括用于除去过量pu的压延步骤,以及任选地还包括干燥步骤。因此,可以压实所述非织造毡以除去过量的pu,同时实现均匀的表面,使得随后的涂层可以适当地结合到所述非织造毡的表面。在压延步骤之后,通过例如使所述非织造毡通过在例如130-160℃下操作的烘箱来施加干燥步骤。然后将干燥的非织造毡辊压,从而形成适合于随后涂覆的有色或浸渍的非织造毡卷。
[0064]
浸渍步骤(c)还能够避免在形成非织造毡时使用化学合成纤维。因此,其中的所有纤维都是韧皮纤维,并且实现了聚合物(例如pu)的最佳可能分布,从而确保所得人造革的均匀强度。
[0065]
在根据第二方面的实施例中,在步骤(d)中,首先用pu涂层涂覆可剥离纸至0.1-0.3mm的厚度;而在步骤(e)中,粘合剂材料层被涂覆至厚度为0.1-0.3mm,诸如0.1-0.2mm。尽管较低范围可以是相同的(0.1mm),但是两个层的厚度不同的条件仍然适用。
[0066]
在根据第二方面的实施例中,在步骤(d)中,所涂覆的聚合物涂层是湿聚合物涂层,并且在步骤(e)中,所涂覆的粘合剂材料层是粘合剂材料的湿层,并且将包括浸渍有聚合物的韧皮纤维的所述非织造毡铺设在所述粘合剂材料的湿层上。粘合剂材料优选为pu。
[0067]
通常,将需要额外的整理步骤,包括压制和压花步骤(f)的产品。压制和压花使得能够进一步软化大麻纤维,同时还使人造革纹理化以甚至更类似于天然或合成革的纹理和外观。然而,通过本发明,不再需要这样的压制和压花步骤,因为压花的效果已经由上述纸上的涂层提供。
[0068]
在本发明的第三方面,还提供了一种服装、家具、鞋、钱包、包、行李和衬里形式的制品,其包括根据上述或下述实施例中任一项所述的人造革。
[0069]
在本发明的第四方面,本发明还包括根据上述或下述实施例中任一项所述的人造革在制造服装、家具、鞋、钱包、包、行李和衬里中的用途。
[0070]
第一方面的实施例的任何特征可以与第二或第三或第四方面的实施例的任何特征组合。
[0071]
现在将通过附图进一步描述本发明,其中图1示出了根据本发明的第一方面的人造革,图2是用于生产图1的所述人造革的总体工艺方案,图3a和图3b详细地示出了非织造毡的涂覆步骤。特别地,图3a更详细地示出了非织造毡的浸渍轧染和压延,并且图3b更详细地示出了非织造毡的中间层和顶层的后续涂覆。
[0072]
图1示出了根据本发明的第一方面的人造革10的示意图,该人造革10通过具有三个离散层(即三个不同或单独的层)而具有层压结构。底层12为浸渍有聚合物并具有1-5mm厚度的韧皮纤维(例如大麻纤维)的非织造毡。中间层14为粘合剂材料的形式,例如厚度为0.2mm的pu,并且其与底层(即基材层)直接连接,并且还与聚合物涂层(优选pu)的顶层16直接连接,所述聚合物涂层具有0.3mm的厚度,并且其提供人造革的结构和外观,因此其类似于合成革。
[0073]
图2a示出了用于制造人造革的整个过程20,其中原料韧皮纤维,特别是原料大麻纤维,由纤维供应商分批输送,例如捆包。对原料大麻纤维进行去皮22和任选地脱胶,随后进行用于将碎屑与纤维分离的细化步骤24。碎屑为原料大麻纤维的碎片簇,其通常不希望通过整个过程。这导致具有4-80mm的平均纤维长度和0-3wt%的碎屑的纤维。纤维沉积在传送带上,从而形成纤维层。然后,在混合步骤26中将树脂,优选纤维形式(即熔融纤维形式)的生物树脂与纤维层混合。这是通过以树脂与纤维重量比为15/85或20/85将树脂添加到传送带上的纤维层的顶部来完成的。传统的气流成网阶段28能够使树脂与纤维完全物理混合,并使所得混合物轻轻地落在带上,然后在130-200℃,例如175℃,的固化炉(未示出)中固化树脂。在烘箱中的停留时间很容易适应环境,但通常停留时间为0.5-1.5分钟就足够了。在步骤30中,通过压制来压实所得的非织造毡,得到厚度为1-5mm的非织造毡,将其卷绕成在干燥条件下具有150-350g/m2的纤维密度的卷,例如180g/m2。这种大麻纤维的非织造毡为其顶部涂覆有离散的中间层和顶层的基材。涂覆步骤32包括浸渍大麻纤维和随后涂覆(流延涂覆)浸渍纤维的非织造毡;参见下面的图3a和3b的描述。在将中间层和顶层涂覆在非织造毡上之后,还对人造革进行压制和压花的任选步骤34,以便进一步促进常规合成革结构,并且其可以进一步通过任选的整理步骤或工艺36来实现,其中人造革用常规革涂饰制剂处理,例如用于防水。然后在步骤38中将人造革卷成大麻(生物)革或仅仅人造革的成品卷。
[0074]
图2b示出了代替图2a的步骤26、28和30的用于生产非织造毡的替代方法。因此,不需要添加生物树脂(步骤26,图2a),省略了气流成网(步骤28,图2a),因此也省略了随后的通过压制的压实(步骤30,图2a)。因此,在图2b中,在步骤26'中,纤维沉积在传送带上,并通过经梳理机28'进行的梳理步骤、交叉铺网部分28”和针刺部分28”',如图所示。因此,更好地控制纤维的取向,并且在不需要添加诸如生物树脂的树脂的情况下实现基材(即非织造毡)的强度。可选地,在针刺步骤(28”')之前,可以涂覆覆盖材料,例如天然纤维层或植物基塑料材料,例如pla(聚乳酸),也如图所示。在交叉铺网之后和针刺之前,并且也在涂覆覆盖材料之前,交叉铺网的纤维层可以通过纤维层重新排列步骤,例如粘着步骤,由此纤维层在垂直方向上移动(上下,如图中的箭头所示),使得纤维层在涂覆覆盖材料的可选步骤和针刺之前适当地对齐。
[0075]
图3a表示图2的步骤32的第一步骤。图3a示出了在步骤30中所生产的大麻纤维的基材或未加工的非织造毡40。未加工的非织造毡40在轧染浴42中着色。为了着色,用聚合物(这里是pu)浸渍纤维,从而随后提供人造革10的所得底层12(图1)。在浸渍之后,非织造毡经历压延步骤44,其将浸渍的过量聚合物从非织造毡压出,同时在着色或浸渍的非织造毡46卷上提供均匀的表面,使得随后的涂覆是可能的。在辊压非织造毡之前,也可以在例如130-160℃的烘箱(未示出)中进行干燥步骤。
[0076]
图3b表示图2的步骤32的第二步骤。图3b示出了从卷48单独提供可剥离纸的膜。例如通过刮涂52将湿pu涂层50涂覆至0.3mm的厚度,从而形成组合的可剥离纸-pu涂层54,然后在烘箱56中在160℃下将其干燥。代替在160℃下干燥,干燥优选在较低温度,如约110℃下进行。任选地重复提供可剥离纸的第一步骤、刮涂和随后的干燥。此后,例如通过在上述组合的可剥离纸-pu涂层54的干燥pu涂层上刮涂60来涂覆湿粘合剂材料层58(例如pu)至0.2mm的厚度。随后,通过在130-180℃,优选160℃下进行的压延步骤62,在其上铺设如结合图3a所述的包括浸渍有聚合物的韧皮纤维的非织造毡46。然后在烘箱66中对组合的可剥离纸-pu涂层-粘合剂材料层64进行另外的干燥步骤,并且最后在130-180℃,优选160℃下进行另外的压延步骤68。因此,显而易见的是,中间产品64在底部包含可剥离纸70,随后是厚度达0.3mm的pu层,其对应于图1的所述顶层16,然后是厚度达0.2mm的粘合剂材料层,其对应于图1的中间层14,以及包括浸渍有聚合物的韧皮纤维的非织造毡,其对应于图1中的底层12。最后,将可剥离纸70移除并卷绕成单独的卷72,同时将分离的人造革74卷绕成人造革10的卷76(图1)。当可剥离纸被移除时,在顶层上留下革状结构,以及任何其他期望的结构或外观,诸如自然结构或定制的。