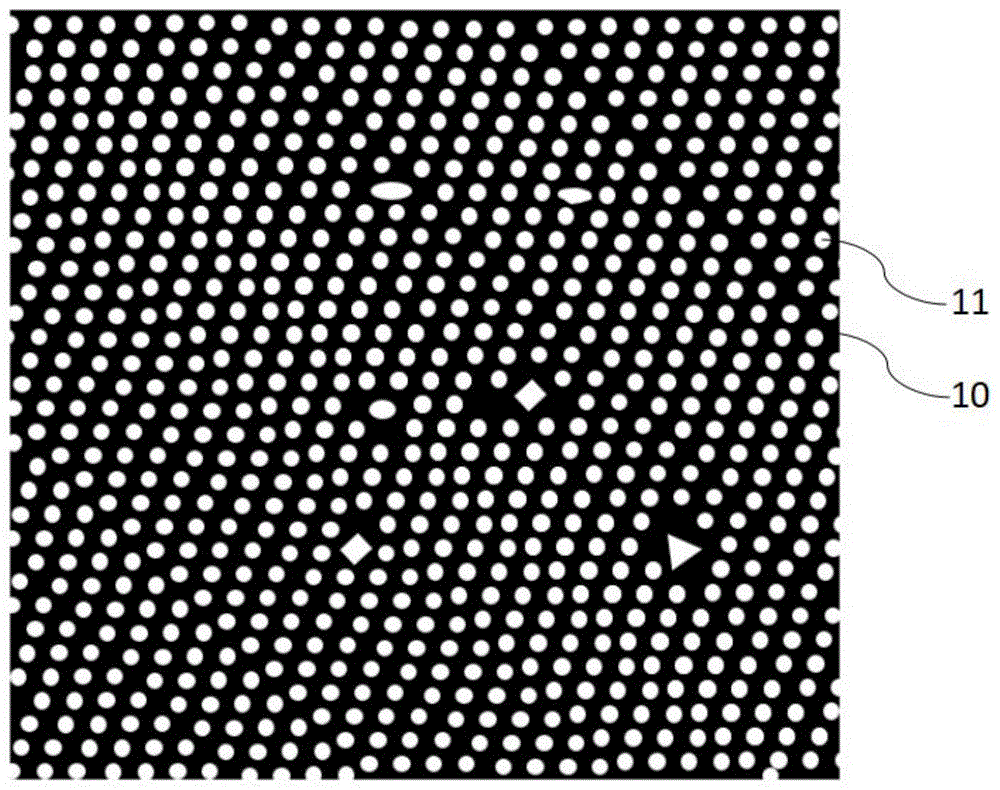
本发明涉及一种导热垫片及其制备方法,更具体而言,涉及一种导热膜增强的纵向高导热垫片,属于导热散热
技术领域:
。
背景技术:
:移动网络的迅猛发展,让越来越多的电子设备接入到移动网络中,并催生出一大批新的服务和应用。尤其是5g时代的来临,移动网络设备产品的功能更加强大,功耗也随之同步增长,同时设计空间尺寸却变得越来越小,电子元件在使用过程中产生的热能越来越多。这些热能如不能及时从内部散发出去,会导致电子元件运行速度减慢,寿命缩短。因此,如何有效地从产生更高温度的元件中移走大量的热,是5g电子设备热管理面临的严峻问题。导热界面材料(thermalinterfacematerials,tim)是决定电子产品散热效率高低的关键材料之一,其中导热垫片是导热界面材料领域最受关注,也是被研究最多的材料。普通的导热垫片产品,其导热系数难以达到10w/(m·k),在5g领域的应用已经远远不能满足。目前采用的碳纤维增强的导热垫片虽然具有较高的导热系数,但是碳纤维在基体中处于分散状态,而非连续状态,限制了碳纤维导热效果的发挥,从而难以进一步提升导热垫片的导热系数。同时,高导热碳纤维价格昂贵,且采购收到限制。另一方面,石墨导热膜和石墨烯导热膜均具有较高的导热系数,若能作为一个连续整体增强导热垫片,必能大幅提升其导热系数。对此,在文献internationaljournalofheatandmasstransfer118(2018)510-517中,采用石墨烯导热膜浸渍于环氧树脂中,取出后进行层压,固化后切割成石墨烯导热膜纵向排列的石墨烯导热膜/环氧树脂复合材料,其纵向导热系数高达384.9w/(m·k)。然而,该方法得到的石墨烯导热膜/环氧树脂复合材料为硬质材料,不能与界面充分接触导致热阻较大而不适合作为导热界面材料使用。另外,在文献acsnano2019,13,11561-11571中,记载了将石墨烯导热膜制成褶皱状,并控制褶皱的高度与聚集程度,从而得到纵向导热的纯石墨烯材料。该方法得到导热材料,虽然在纵向上可以获得较高的导热系数,但是由于表面粗糙,且褶皱之间存在大量空隙,以及石墨烯膜自身硬质等原因,导致不能与界面充分接触,热阻较大,不适宜作为导热垫片材料。此外,上述文献中虽然均设想直接将石墨烯导热膜应用于纵向导热,但由于热阻较大,散热效果受限等原因,不适宜用于导热界面。
背景技术:
部分的内容仅仅是发明人所知晓的技术,并不当然代表本领域的现有技术。技术实现要素:针对现有技术存在问题中的一个或多个,本发明提供一种导热垫片,其具有优异导热性能且能够与界面充分接触,接触热阻低,导热散热效果优异。此外,本发明还提供一种制备该导热垫片的方法。根据本发明的一个方面,提供一种导热垫片,其包含导热膜与粘结剂层;并且可选地包括其他导热填料,其中所述导热膜具有贯穿该导热膜上下表面的多个孔,所述多个孔中填充有粘结剂。因此不同层的粘结剂可以通过多个孔相连,形成连续结构,将导热膜在微观尺度上进行包裹,无需做表面涂层即可将粘结剂与导热膜强力地结合在一起,同时避免了导热膜自身分层的问题。其中,所述导热膜与所述粘结剂逐层交错堆叠。其中,所述导热膜选自石墨或石墨烯导热膜、氮化硼导热膜中的一种,优选石墨或石墨烯导热膜。其中,所述导热膜的厚度为4-60μm,优选10-50μm,更优选15-40μm。其中,所述导热膜的多个孔的尺寸为0.5-200μm,优选5-100μm,更优选10-50μm,孔间距为5-200μm,优选10-150μm,更优选20-100μm。其中,所述粘结剂包含选自有机硅胶、聚氨酯、聚丙烯酸酯、聚烯烃弹性体中的至少一种成分,其中优选有机硅胶,所述有机硅胶选自硅油、硅凝胶、聚二甲基环硅氧烷、聚二甲基硅氧烷、α,ω-二羟基聚二甲基硅氧烷、聚二苯基硅氧烷、α,ω-二羟基聚甲基(3,3,3-三氟丙基)硅氧烷、氰基硅氧基硅烷、α,ω-二乙基聚二甲基硅氧烷中的至少一种。其中,所述其他导热填料选自氧化铝、氮化硼、石墨、二氧化硅、氧化锌、氧化铍、氮化铝或其混合物中的一种,其中优选氧化铝、氮化铝、氮化硼或其混合物。其中,该导热垫片的厚度为0.25-3mm,优选0.5-2mm。根据本发明的另一方面,提供一种制备导热垫片的方法,其包括如下步骤:(1)在导热膜上形成贯穿该导热膜上下表面的多个孔;(2)在步骤(1)形成的导热膜上层叠粘结剂层,然后在该粘结剂层上继续层叠步骤(1)形成的导热膜,重复该逐层交替层叠工序,形成堆叠体;(3)将步骤(2)所得堆叠体进行压制成型,并进行硫化处理;(4)将步骤(3)所得成型体沿着垂直于所述导热膜平面的方向进行切片;(5)将步骤(4)所得切片进行二次硫化处理,并可选地进行表面打磨处理,得到导热垫片。其中所述粘结剂层还含有其他导热填料,该导热填料选自氧化铝、氮化硼、石墨、二氧化硅、氧化锌、氧化铍、氮化铝或其混合物中的一种,其中优选氧化铝、氮化铝、氮化硼或其混合物。其中,优选通过激光技术在所述导热膜上形成多个孔。可以通过其他方法进行打孔。其中,步骤(2)中,通过涂布或喷涂的方式将粘结剂层叠在步骤(1)中形成的导热膜上。其中,步骤(3)中的硫化处理的温度为100-150℃。二次硫化温度为120-200℃。优选地,所述导热膜经过表面处理,所述表面处理为表面金属化处理、等离子体处理中的至少一种;优选地,所述金属化处理选自镀铜、镀镍、镀铁、镀银中的至少一种;优选地,金属镀层的厚度为0.1-2μm,优选为0.5-1μm;优选地,所述等离子处理在空气气氛、氮气气氛或氧气气氛下进行;优选的,所述等离子处理的等离子功率为1-10kw,优选3-8kw根据本发明的又一方面,提供一种将膜结构与高分子材料结合的方法,其包括如下步骤:(1)在膜结构上形成贯穿该膜结构上下表面的多个孔;(2)在步骤(1)形成的膜结构上层叠高分子材料,其中高分子材料至少覆盖所述多个孔;以及(3)可选地继续层叠所述膜结构或者其他材料。其中,所述膜结构选自石墨或石墨烯导热膜、氮化硼导热膜中的一种,优选石墨或石墨烯导热膜;所述高分子材料为粘结剂。根据该方法,可以容易地将膜结构与其他界面或者其他材料结合。根据本发明的又一方面,提供一种电子设备,其特征在于,该电子设备具备热源、散热部件、以及夹持于该热源与该散热部件之间的本发明的导热垫片。本发明具有以下有益效果:(1)由于在导热膜上形成了多个微米级别的孔,在确保导热膜的整体连续性和完整性的同时,提供了导热膜与诸如硅油或硅凝胶等粘结剂的良好结合,并提升了导热垫片的导热系数,降低热阻。(2)粘结剂与导热膜逐层交错层叠的方式互相结合,解决了诸如石墨或石墨烯导热膜的硬质的问题,使得整体材料具有良好的机械弹性,能够与界面接触良好,降低了接触热阻。(3)本发明的构思也为其他膜结构材料与高分子材料的结合提供了新思路与新方法。附图说明附图用来提供对本发明的进一步理解,并且构成说明书的一部分,与本发明的实施例一起用于解释本发明,并不构成对本发明的限制。在附图中:图1是本发明的导热膜表面打上贯穿孔后的示意图;图2是层层堆叠、模压成型后的堆叠体示意图,其中多个孔的内部填充了粘结剂,与周边粘结剂形成一个整体;图3是切片后形成的本发明的导热垫片示意图,其中,导热膜沿着垫片的纵向进行排列。附图标记说明:1:导热垫片;2:堆叠体;10:导热膜;11:孔;12:粘结剂层;12a:填充于孔中的粘结剂。具体实施方式在下文中,仅简单地描述了某些示例性实施例。正如本领域技术人员可认识到的那样,在不脱离本发明的精神或范围的情况下,可通过各种不同方式修改所描述的实施例。因此,附图和描述被认为本质上是示例性的而非限制性的。以下结合附图对本发明的优选实施例进行说明,应当理解,此处所描述的优选实施例仅用于说明和解释本发明,并不用于限定本发明。首先对本发明的导热垫片进行说明。如图3所示,本发明的导热垫片1包含导热膜10与粘结剂层12,其中导热膜10上形成有贯穿该导热膜10上下表面的多个孔11,所述多个孔11中填充有粘结剂12a。该导热垫片1的厚度为0.25-3mm,优选0.5-2mm。作为本发明的导热膜,可以采用本领域常用的导热膜,例如选择石墨或石墨烯导热膜、氮化硼导热膜中的任一种,优选石墨或石墨烯导热膜。导热膜的长宽尺寸无特殊限制,可以根据需要进行选择。导热膜的厚度可以根据需要进行选择,一般厚度在4-60μm范围内为佳,例如10-50μm或者5-40μm。在导热膜上形成多个孔的方式无特殊要求,从精度与效果方面考虑,优先使用激光进行打孔,孔之尺寸为0.5-200μm,优选5-100μm,更优选10-50μm,孔间距为5-200μm,优选10-150μm,更优选20-100μm,此处所述的孔间距是指相邻的两孔的相邻边缘的距离。这样形成的微米级别的孔,能够确保导热膜的整体完整性,提供了连续的导热通道,极大地提升了导热垫片的导热系数。另外,可以根据需要对导热膜施加表面处理,所述表面处理为表面金属化处理、等离子体处理中的至少一种。金属化处理可以是诸如镀铜、镀镍、镀铁、镀银。金属镀层的厚度可以为0.1-2μm,优选为0.5-1μm。关于等离子处理,优选在空气气氛、氮气气氛或者氧气气氛下进行,等离子功率可以为1-10kw,优选3-8kw。另外,本发明使用的粘结剂可以选自有机硅胶、聚氨酯、聚丙烯酸酯、聚烯烃弹性体中的至少一种成分,其中优选有机硅胶。有机硅胶可以选自硅油、硅凝胶、聚二甲基环硅氧烷、聚二甲基硅氧烷、α,ω-二羟基聚二甲基硅氧烷、聚二苯基硅氧烷、α,ω-二羟基聚甲基(3,3,3-三氟丙基)硅氧烷、氰基硅氧基硅烷、α,ω-二乙基聚二甲基硅氧烷中的至少一种。此外,粘结剂根据需要还可以含有其他添加剂,例如可以添加其他导热填料,诸如氧化铝、氮化硼、石墨、二氧化硅、氧化锌、氧化铍、氮化铝或其混合物等,优选氧化铝、氮化铝、氮化硼或其混合物。作为将粘结剂施加(层叠)在导热膜上的方式,可以采用涂布或喷涂等工艺,也可以采用本领域的公知的其他方式,只要能够大致均匀地将粘结剂层叠)在导热膜上。在施加粘结剂的过程中,粘结剂进入到导热膜的多个孔之内,并与位于导热膜上(下)表面及周边的粘结剂形成一体,有效解决了导热膜不能与诸如硅油或硅凝胶这样的粘结剂相结合的难题,并提供了导热垫片与散热界面的良好接触,降低了接触热阻。另外,将导热膜与粘结剂层逐层交错堆叠若干层的方式,解决了石墨或石墨烯导热硬质的问题,使导热垫片具有良好的机械弹性,改善了压缩性,提供了纵向高导热垫片。示例性的制备本发明的导热垫片的方法包括如下步骤:(1)在导热膜上形成贯穿该导热膜10上下表面的多个孔11,如图1所示;(2)在步骤(1)形成的导热膜10上层叠粘结剂层12,然后在该粘结剂层上继续层叠步骤(1)形成的导热膜10。该步骤可以使粘结剂12a进入多个孔11中。重复该逐层交替层叠工序,形成堆叠体2,如图2所示;(3)将步骤(2)所得堆叠体2进行压制成型,并进行硫化处理;(4)将步骤(3)所得成型体沿着垂直于所述导热膜平面的方向(如图2中箭头所示方向)进行切片,如图2;(5)将步骤(4)所得切片进行二次硫化处理,并可选地进行表面打磨处理,得到导热垫片1(如图3所示)。其中,步骤(3)中压制成型可以但不限于采用模压成型的方式,也可以采用本领域公知的其他方法。其中,步骤(3)中硫化处理的温度为100-150℃,例如110-140℃、120-130℃等。其中,步骤(5)中二次硫化处理的温度为120-200℃,例如140-180℃或150-170℃等。其中,步骤(4)中的切片工艺无特殊要求,从切割精度与连续化程度等角度考虑,优先采用超声波切割工艺。切片的厚度为本领域的常规厚度诸如0.5-5mm即可,也可以根据需要切成合适的厚度,例如1-2mm。另外,优选地,可以对切片进行打磨处理,得到表面更平整的导热垫片,有助于进一步降低接触热阻。根据本发明的又一方面,提供一种将膜结构与其他高分子材料结合的方法,其包括如下步骤:(1)在膜结构上形成贯穿该膜结构上下表面的多个孔;(2)在步骤(1)形成的膜结构上层叠高分子材料,其中高分子材料至少覆盖所述多个孔;以及(3)可选地继续层叠所述膜结构或者其他材料。其中,所述膜结构可以选自石墨或石墨烯导热膜、氮化硼导热膜中的一种,优选石墨或石墨烯导热膜;所述高分子材料为粘结剂。本发明将诸如石墨或石墨烯的导热膜以连续的状态应用于导热垫片中,形成了内部导热通道网络,从而大幅提升垫片纵向导热系数;在导热膜上形成多个微米级的孔,可以实现硅油或硅凝胶与导热膜的紧密粘接,形成稳定的整体结构;另外,由于沿着导热膜排列的垂直方向进行切片,因此能够获得具有纵向高导热的垫片材料。另外,由于微米级或亚微米级孔的存在,解决了当导热膜在导热垫片中竖直排列时,因厚度较小(0.25-3mm)而硬质化的难题,并且由于完全由固化后的硅油或硅凝胶表现出的柔韧性及弹性等机械性能,能够进一步降低接触热阻。同时,本发明的制备方法还优化了现有导热垫片制作工艺上定向及表面处理的工艺步骤。以下结合更具体的实施例详细描述本发明。实施例1:本实施例中,石墨烯导热膜增强的纵向高导热垫片的制备过程包括如下步骤:1)将厚度为4μm的石墨烯导热膜通过激光技术进行打孔,贯穿上下两表面,孔尺寸为200μm,孔间距为200μm;2)将硅凝胶与导热氧化铝粉均匀混合,并进行脱泡处理,得到混合硅凝胶,其中氧化铝含量70%;3)将步骤2)中得到的混合硅凝胶采用刮涂的的方式均匀涂敷于步骤1)中打孔后的石墨烯导热膜的表面,并交错堆叠该石墨烯导热膜,形成堆叠体;4)将步骤3)中的堆叠体置于模具内,真空脱泡后,在60℃下进行热压成型;5)在步骤4)的基础上直接进行硫化处理,硫化温度为125℃;6)待冷却后,将硫化后的样品取出,采用超声波切割的方式,沿着垂直于石墨烯导热膜平面的方向进行切片,得到厚度为0.25-3mm的片状材料;7)将上述片状材料进行二次硫化,硫化温度为200℃;8)将二次硫化后的片状材料的表面进行打磨处理,得到本发明的石墨烯导热膜增强的纵向高导热垫片。实施例2:本实施例中,石墨烯导热膜增强的纵向高导热垫片的制备过程包括如下步骤:1)将厚度为60μm的石墨烯导热膜通过激光技术进行打孔,贯穿上下两表面,孔尺寸为0.5μm,孔间距为5μm;2)采用硅凝胶与导热氮化铝均匀混合,并进行脱泡处理,得到混合硅凝胶,其中氮化铝含量60%;3)将步骤2)中得到的混合硅凝胶采用刮涂的的方式均匀涂敷于步骤1)中打孔后的石墨烯导热膜表面,并交错堆叠该石墨烯导热膜,形成堆叠体;4)将步骤3)中的堆叠体置于模具内,真空脱泡后,在80℃下进行热压成型;5)在步骤4)的基础上直接进行硫化处理,硫化温度为100℃;6)待冷却后,将硫化后的样品取出,采用超声波切割的方式,沿着垂直于石墨烯导热膜平面的方向进行切片,得到厚度为0.25-3mm的片状材料;7)将上述片状材料进行二次硫化,硫化温度为200℃;8)将二次硫化后的片状材料的表面进行打磨处理,得到本发明的石墨烯导热膜增强的纵向高导热垫片。实施例3:本实施例中,石墨烯导热膜增强的纵向高导热垫片的制备过程包括如下步骤:1)将厚度为30μm的石墨烯导热膜通过激光技术进行打孔,贯穿上下两表面,孔尺寸为25μm,孔间距为20μm;2)采用硅凝胶与氮化硼粉末、氧化铝粉末均匀混合,并进行脱泡处理,得到混合硅凝胶,其中氮化硼含量20%,氧化铝含量50%;3)将步骤2)中得到的混合硅凝胶采用刮涂的的方式均匀涂敷于步骤1)中打孔后的石墨烯导热膜的表面,并交错堆叠该石墨烯导热膜,形成堆叠体;4)将步骤3)中的堆叠体置于模具内,真空脱泡后,在70℃下进行热压成型;5)在步骤4)的基础上直接进行硫化处理,硫化温度为140℃;6)待冷却后,将硫化后的样品取出,采用超声波切割的方式,沿着垂直于石墨烯导热膜平面的方向进行切片,得到0.25-3mm的片状材料;7)将上述片状材料进行二次硫化,硫化温度为180℃;8)将二次硫化后的片状材料的表面进行打磨处理,得到本发明的石墨烯导热膜增强的纵向高导热垫片。实施例4:本实施例中,石墨烯导热膜增强的纵向高导热垫片的制备过程包括如下步骤:1)将厚度为15μm的石墨烯导热膜通过激光技术进行打孔,贯穿上下两表面,孔尺寸为10μm,孔间距为25μm;2)采用硅凝胶与氧化铝粉末均匀混合,并进行脱泡处理,得到混合硅凝胶,其中氧化铝含量80%;3)将步骤2)中得到的混合硅凝胶采用刮涂的的方式均匀涂敷于步骤1)中打孔后的石墨烯导热膜的表面,并交错堆叠该石墨烯导热膜,形成堆叠体;4)将步骤3)中的堆叠体置于模具内,真空脱泡后,在75℃下进行热压成型;5)在步骤4)的基础上直接进行硫化处理,硫化温度为150℃;6)待冷却后,将硫化后的样品取出,采用超声波切割的方式,沿着垂直于石墨烯导热膜平面的方向进行切片,得到0.25-3mm的片状材料;7)将上述片状材料进行二次硫化,硫化温度为200℃;8)将二次硫化后的片状材料的表面进行打磨处理,得到石墨烯导热膜增强的纵向高导热垫片。将上述各实施例中获得的高导热垫片,进行以下性能测试。导热系数测试:测试方法采用astmd5470-17,在不同厚度下测试得到表观导热系数。热阻测试:测试方法采用astmd5470-17,测试2mm厚度样品在应变50%时的总体热阻。压缩性能测试:参照astmd575-1991,压缩率0.5mm/s对样品压缩至应变50%,并保持10min后观测其压缩性能。粘附力测试:参照astmd575-1991,完成压缩性能测试后,向上移动压头,测此拉伸应力,从而评价其粘附力。回弹率测试:参照astmd395,将样品压缩至50%应变后保持30min后释放压力,观测其恢复后的厚度情况。热阻可靠性测试:高温老化:125℃,1000h高温高湿:85℃/85%rh,1000h温度循环:-40℃至125℃,10至15℃/min温变率,1000个循环通过以上老化实验后,考察本发明的导热垫片的热阻的变化率。测试结果汇总于下表中。性能参数实施例1实施例2实施例3实施例4导热系数(w·m-1·k-1)88.61104.5293.52110.37热阻(k·in2·w-1)0.0830.0610.0690.056压缩应力(psi)15.3426.6921.0319.46粘附力(psi)12.1111.9413.2410.94回弹率(%)91.3995.7296.3292.18老化后热阻增加率(%)8.947.459.138.87根据上表可知,与现有技术的导热垫片(导热系数一般不超过10w·m-1·k-1)相比,本发明的导热垫片具备优异的导热系数(高达88.61w·m-1·k-1以上),极低的热阻和优异的机械性能,是一种导热散热性能优异的导热垫片,非常适用于需要高导热垫片的各种电子设备。最后应说明的是:以上所述仅为本发明的优选实施例而已,并不用于限制本发明,对于本领域的技术人员来说,其依然可以对前述各实施例所记载的技术方案进行修改,或者对其中部分技术特征进行等同替换。凡在本发明的精神和原则之内,所作的任何修改、等同替换、改进等,均应包含在本发明的保护范围之内。当前第1页12