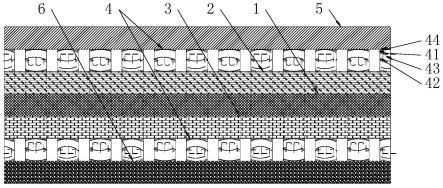
1.本发明属于羽绒服布料技术领域,具体涉及一种高弹性耐撕裂布料及其制备方法。
背景技术:2.在羽绒服产品向时装化、休闲化、运动化和个性化转变的进程中,也推动着相关面辅料产品的更新和换代,面料产品的档次和水平对羽绒服起着至关重要的作用。
3.现有技术中的羽绒服布料在具备高弹性的性能的同时便难以兼顾该布料的抗撕裂性能,但以高弹性耐撕裂的布料为基础可以创造出更多有亮点、有创意、有文化品位、符合消费者需求、对市场有强烈吸引力的羽绒服,因此发明一种高弹性耐撕裂布料及其制备方法是十分必要的。
技术实现要素:4.本发明的目的就在于为了解决上述问题而提供一种高弹性耐撕裂布料及其制备方法。
5.本发明通过以下技术方案来实现上述目的:
6.一种高弹性耐撕裂布料,包括基层、设于基层上表面的抗菌层、设于基层下表面的防绒层、位于抗菌层上表面以及防绒层下表面的耐撕裂层、设于耐撕裂层上表面的柔软层、设于耐撕裂层下表面的透气层;
7.所述耐撕裂层由抗撕裂件、纬纱、经纱以及布料粘合剂构成,所述抗撕裂件为一根首尾连接的高收缩纤维线,所述高收缩纤维线的中部位置相互粘合,所述高收缩纤维线的两端留有圈状的穿行通道,所述高收缩纤维线中部相互粘合的部分从防绒层、基层以及抗菌层穿行,多个抗撕裂件的圈状穿行通道充作网格端点分布在抗菌层上方以及防绒层下方,所述抗菌层上方以及防绒层下方均设置有多条纬纱和经纱,所述抗撕裂件的圈状穿行通道、纬纱以及经纱编织成网状结构,所述布料粘合剂填充在该网状结构的缝隙中。
8.作为本发明的进一步优化方案,所述基层由棉线纺织而成的基布,棉线中棉纤维、竹纤维以及羊毛纤维的质量比为6.4:1.3:2.3。
9.作为本发明的进一步优化方案,所述抗菌层由抗菌布料热压在基层上表面形成,所述抗菌布料由天竹纤维、罗布麻纤维以及纳米银离子纤维按照质量比4.6:4.2:1.2纺织而成。
10.作为本发明的进一步优化方案,所述防绒层由防绒布热压在基层下表面形成。
11.作为本发明的进一步优化方案,所述柔软层由柔软布料热压在耐撕裂层上表面形成,所述柔软布料由莱赛尔纤维、羊毛纤维以及蚕丝纤维按照质量比3.6:4.3:2.1纺织而成。
12.作为本发明的进一步优化方案,所述透气层由透气布料热压在耐撕裂层下表面形成,所述透气布料由涤纶纤维和聚酯纤维按照质量比5.7:4.3纺织而成。
13.一种高弹性耐撕裂布料的制备方法包括以下步骤:
14.步骤一、通过纺织设备将棉纤维、竹纤维以及羊毛纤维按照质量比6.4:1.3:2.3纺织成基布,以基布作为基层。
15.步骤二、通过纺织设备将天竹纤维、罗布麻纤维以及纳米银离子纤维按照质量比4.6:4.2:1.2纺织成抗菌布料,将抗菌布料热压在基层上表面形成抗菌层,将防绒布热压在基层下表面形成防绒层。
16.步骤三、通过捻搓设备将首尾连接的高收缩纤维线的中部位置捻搓呈螺旋状形态,然后通过热压辊将该高收缩纤维线的中部位置加热压合在一起,高收缩纤维线的两端留有圈状的穿行通道,通过纺织设备加工将多个高收缩纤维线中部相互粘合的部分依次从防绒层、基层以及抗菌层穿过,两端圈状的穿行通道充作网格端点分布在抗菌层上方以及防绒层下方,再通过纺织设备加工将高收缩纤维线的圈状穿行通道、纬纱以及经纱纺织成网状结构,并将布料粘合剂喷涂在网格结构的缝隙中,然后通过加热设备对布料进行加热处理,加热处理后的布料通过定型辊对布料热压定型,以此在抗菌层上表面以及防绒层下表面形成耐撕裂层。
17.步骤四、通过纺织设备将莱赛尔纤维、羊毛纤维以及蚕丝纤维按照质量比3.6:4.3:2.1纺织成柔软布料,利用热压辊将柔软布料热压在耐撕裂层上表面形成柔软层。
18.步骤五、通过纺织设备将涤纶纤维和聚酯纤维按照质量比5.7:4.3纺织成透气布料,利用热压辊将透气布料热压在耐撕裂层上表面形成透气层,以此制备得到高弹性耐撕裂布料。
19.作为本发明的进一步优化方案,耐撕裂层的制备步骤如下:在步骤三中,热压辊加热温度保持在180℃
±
5℃。
20.作为本发明的进一步优化方案,耐撕裂层的制备步骤如下:在步骤三中,相邻网格端点之间的距离为100μm~500μm。
21.作为本发明的进一步优化方案,耐撕裂层的制备步骤如下:在步骤三中,每平方米布料在加热设备中停留的时间为55s~125s,加热设备的加热温度保持在180℃~196℃,定型辊热压温度保持在180℃
±
5℃。
22.本发明的有益效果在于:
23.1)本发明通过设置耐撕裂层使得布料在具备高弹性性能的同时依旧可以保持较好的耐撕裂的性能,布料坚韧有弹性,使用寿命较长,构成耐撕裂层的抗撕裂件的中部位置相互粘合,并令抗撕裂件上相互粘合的中部位置从防绒层、基层以及抗菌层穿行,然后令抗撕裂件上位于两端的圈状穿行通道、纬纱以及经纱编织成网状结构,进一步地增加布料的耐撕裂性能和弹性性能;
24.2)本发明将高收缩纤维线中部位置捻搓成螺旋状后再通过热压辊将该高收缩纤维线的中部位置加热压合在一起,可以进一步的增加高收缩纤维线的耐撕裂性能,从而提升布料的耐撕裂性能,而高收缩纤维线两端圈状的穿行通道充作网格端点分布在抗菌层上方以及防绒层下方,相邻网格端点之间的距离为300μm时,布料的弹性性能和耐撕裂性能都较好。
25.3)本发明将布料粘合剂喷涂在网格结构的缝隙中,然后令布料通过加热设备,每平方米布料在加热设备中停留的时间为95s时,可以进一步的加强布料的弹性性能和耐撕
裂性能。
附图说明
26.图1是本发明的整体结构示意图;
27.图2是本发明的耐撕裂层的俯视图;
28.图3是本发明的抗撕裂件的侧视图;
29.图中:1、基层;2、抗菌层;3、防绒层;4、耐撕裂层;41、抗撕裂件;42、纬纱;43、经纱;44、布料粘合剂;5、柔软层;6、透气层。
具体实施方式
30.下面结合附图对本技术作进一步详细描述,有必要在此指出的是,以下具体实施方式只用于对本技术进行进一步的说明,不能理解为对本技术保护范围的限制,该领域的技术人员可以根据上述申请内容对本技术作出一些非本质的改进和调整。
31.实施例1
32.如图1-3所示,一种高弹性耐撕裂布料,包括基层1、设于基层1上表面的抗菌层2、设于基层1下表面的防绒层3、位于抗菌层2上表面以及防绒层3下表面的耐撕裂层4、设于耐撕裂层4上表面的柔软层5、设于耐撕裂层4下表面的透气层6;
33.所述耐撕裂层4由抗撕裂件41、纬纱42、经纱43以及布料粘合剂44构成,所述抗撕裂件41为一根首尾连接的高收缩纤维线,所述高收缩纤维线的中部位置相互粘合,所述高收缩纤维线的两端留有圈状的穿行通道,所述高收缩纤维线中部相互粘合的部分从防绒层3、基层1以及抗菌层2穿行,多个抗撕裂件41的圈状穿行通道充作网格端点分布在抗菌层2上方以及防绒层3下方,所述抗菌层2上方以及防绒层3下方均设置有多条纬纱42和经纱43,所述抗撕裂件41的圈状穿行通道、纬纱42以及经纱43编织成网状结构,所述布料粘合剂44填充在该网状结构的缝隙中;
34.优选的,所述基层1由棉线纺织而成的基布,棉线中棉纤维、竹纤维以及羊毛纤维的质量比为6.4:1.3:2.3。
35.优选的,所述抗菌层2由抗菌布料热压在基层1上表面形成,所述抗菌布料由天竹纤维、罗布麻纤维以及纳米银离子纤维按照质量比4.6:4.2:1.2纺织而成。
36.在本实施例中,所述防绒层3由防绒布热压在基层1下表面形成。
37.优选的,所述柔软层5由柔软布料热压在耐撕裂层4上表面形成,所述柔软布料由莱赛尔纤维、羊毛纤维以及蚕丝纤维按照质量比3.6:4.3:2.1纺织而成。
38.优选的,所述透气层6由透气布料热压在耐撕裂层4下表面形成,所述透气布料由涤纶纤维和聚酯纤维按照质量比5.7:4.3纺织而成。
39.上述高弹性耐撕裂布料的制备方法,包括以下步骤:
40.步骤一、
[0041]ⅰ、将棉纤维、竹纤维以及羊毛纤维按照质量比6.4:1.3:2.3配比好之后进行充分混合形成混合纤维;
[0042]ⅱ、然后将混合纤维放入捻搓设备中捻搓形成棉线,再将棉线作为径向棉线及纬向棉线分别放入纺织机中纺织成基布,以基布作为基层。
[0043]
步骤二、
[0044]ⅰ、将天竹纤维、罗布麻纤维以及纳米银离子纤维按照质量比4.6:4.2:1.2配比好之后进行充分混合形成抗菌纤维;
[0045]ⅱ、然后将抗菌纤维放入捻搓设备中捻搓形成抗菌纤维线,再将抗菌纤维线作为径向抗菌纤维线及纬向抗菌纤维线分别放入纺织机中纺织成抗菌布料;
[0046]ⅲ、将抗菌布料热压在基层上表面形成抗菌层,热压温度保持在166℃~175℃,将防绒布热压在基层下表面形成防绒层,热压温度保持在168℃~178℃。
[0047]
步骤三、
[0048]ⅰ、首先通过捻搓设备将首尾连接的高收缩纤维线的中部位置捻搓呈螺旋状形态,通过热压辊将该高收缩纤维线的中部位置加热压合在一起,加热温度保持在180℃
±
5℃,同时该高收缩纤维线的两端留有圈状的穿行通道;
[0049]ⅱ、通过纺织设备加工将多个高收缩纤维线的中部相互粘合的部分依次从防绒层、基层以及抗菌层穿过,该高收缩纤维线两端圈状的穿行通道充作网格端点分布在抗菌层上方以及防绒层下方,相邻网格端点之间的距离为100μm;
[0050]ⅲ、通过纺织设备加工将高收缩纤维线的圈状穿行通道、纬纱以及经纱纺织成网状结构,并将布料粘合剂喷涂在网格结构的缝隙中,然后令布料通过加热设备,每平方米布料在加热设备中停留的时间为55s,加热温度保持在180℃~196℃,布料从加热设备内传输出来后通过定型辊对布料热压定型,热压温度保持在180℃
±
5℃。
[0051]
步骤四、
[0052]ⅰ、将莱赛尔纤维、羊毛纤维以及蚕丝纤维按照质量比3.6:4.3:2.1配比好之后进行充分混合形成柔软纤维;
[0053]ⅱ、然后将柔软纤维放入捻搓设备中捻搓形成柔软纤维线,再将柔软纤维线作为径向柔软纤维线及纬向柔软纤维线分别放入纺织机中纺织成柔软布料,并将柔软布料平铺在耐撕裂层上表面,利用热压辊将柔软布料热压在耐撕裂层上表面形成柔软层,热压温度保持在158℃~165℃。
[0054]
步骤五、
[0055]ⅰ、将涤纶纤维和聚酯纤维按照质量比5.7:4.3配比好之后进行充分混合形成透气纤维;
[0056]ⅱ、然后将透气纤维放入捻搓设备中捻搓形成透气纤维线,再将透气纤维线作为径向透气纤维线及纬向透气纤维线分别放入纺织机中纺织成透气布料,并将透气布料平铺在耐撕裂层下表面,利用热压辊将透气布料热压在耐撕裂层下表面形成透气层,热压温度保持在162℃~176℃,以此制备得到高弹性耐撕裂布料。
[0057]
实施例2
[0058]
本实施例中的高弹性耐撕裂布料,制备方法包括以下步骤:
[0059]
除步骤三中,相邻网格端点之间的距离为300μm,其余步骤同实施例1。
[0060]
实施例3
[0061]
本实施例中的高弹性耐撕裂布料,制备方法包括以下步骤:
[0062]
除步骤三中,相邻网格端点之间的距离为500μm,其余步骤同实施例1。
[0063]
实施例1-3,每组布料数量30个,单个布料的规格为2cm
×
2cm的正方形,在室温环境
为25℃
±
1℃下进行布料的抗撕裂性能和弹性性能测试,测试结果如表1:
[0064]
表1
[0065][0066]
实验结论:将高收缩纤维线中部位置加热压合在一起,中部相互粘合的部分依次从防绒层、基层以及抗菌层穿过,并令高收缩纤维线两端圈状的穿行通道充作网格端点分布在抗菌层上方以及防绒层下方,相邻网格端点之间的距离为300μm时,再通过纺织设备加工将高收缩纤维线的圈状穿行通道、纬纱以及经纱纺织成网状结构,以此方法制备出的布料相对比于实施例1以及实施例3的所制备出的布料,布料的抗撕裂性能依次为实施例1》实施例2》实施例3,布料的弹性性能依次为实施例3》实施例2》实施例1,因此依据实施例2所制备出的布料的弹性较好抗撕裂性能也较好,因此实施例2为最优实施例。
[0067]
实施例4
[0068]
本实施例中的高弹性耐撕裂布料,制备方法包括以下步骤:
[0069]
除步骤三中,每平方米布料在加热设备中停留的时间为75s,其余步骤同实施例2。
[0070]
实施例5
[0071]
本实施例中的高弹性耐撕裂布料,制备方法包括以下步骤:
[0072]
除步骤三中,每平方米布料在加热设备中停留的时间为95s,其余步骤同实施例2。
[0073]
实施例6
[0074]
本实施例中的高弹性耐撕裂布料,制备方法包括以下步骤:
[0075]
除步骤三中,每平方米布料在加热设备中停留的时间为105s,其余步骤同实施例2。
[0076]
实施例7
[0077]
本实施例中的高弹性耐撕裂布料,制备方法包括以下步骤:
[0078]
除步骤三中,每平方米布料在加热设备中停留的时间为125s,其余步骤同实施例2。
[0079]
实施例4-7,每组布料数量30个,单个布料的规格为2cm
×
2cm的正方形,在室温环
境为25℃
±
1℃下进行布料的抗撕裂性能和弹性性能测试,测试结果如表2:
[0080]
表2
[0081][0082][0083]
实验结论:根据表2可以得出,将布料粘合剂喷涂在网格结构的缝隙中,当每平方米布料在加热设备中停留的时间在95s时,所制备出的布料弹性较好抗撕裂性能也较好,因此实施例5为最优实施例。
[0084]
对比例1
[0085]
本实施例中的高弹性耐撕裂布料,制备方法包括以下步骤:
[0086]
将步骤三替换为:
[0087]ⅰ、首先通过捻搓设备将首尾连接的高收缩纤维线的中部位置捻搓呈螺旋状形态,通过热压辊将该高收缩纤维线的中部位置加热压合在一起,加热温度保持在180℃
±
5℃,同时该高收缩纤维线的两端留有圈状的穿行通道;
[0088]ⅱ、通过纺织设备加工将多个高收缩纤维线的中部相互粘合的部分依次从防绒层、基层以及抗菌层穿过,该高收缩纤维线两端圈状的穿行通道充作网格端点分布在抗菌层上方以及防绒层下方,相邻网格端点之间的距离为100μm;
[0089]ⅲ、通过纺织设备加工将纬纱以及经纱纺织成网状结构,并将布料粘合剂喷涂在网格结构的缝隙中,然后令布料通过加热设备,每平方米布料在加热设备中停留的时间为95s,加热温度保持在180℃~196℃,布料从加热设备内传输出来后通过定型辊对布料热压定型,热压温度保持在180℃
±
5℃。
[0090]
其余步骤同实施例5。
[0091]
对比例2
[0092]
本实施例中的高弹性耐撕裂布料,制备方法包括以下步骤:
[0093]
将步骤三替换为:
[0094]ⅰ、通过热压辊将首尾连接的高收缩纤维线的中部位置加热压合在一起,加热温度
保持在180℃
±
5℃,同时该高收缩纤维线的两端留有圈状的穿行通道;
[0095]ⅱ、通过纺织设备加工将多个高收缩纤维线的中部相互粘合的部分依次从防绒层、基层以及抗菌层穿过,该高收缩纤维线两端圈状的穿行通道充作网格端点分布在抗菌层上方以及防绒层下方,相邻网格端点之间的距离为300μm;
[0096]ⅲ、通过纺织设备加工将高收缩纤维线的圈状穿行通道、纬纱以及经纱纺织成网状结构,并将布料粘合剂喷涂在网格结构的缝隙中,然后令布料通过加热设备,每平方米布料在加热设备中停留的时间为95s,加热温度保持在180℃~196℃,布料从加热设备内传输出来后通过定型辊对布料热压定型,热压温度保持在180℃
±
5℃;
[0097]
其余步骤同实施例5。
[0098]
对比例1、对比例2以及实施例5,每组布料数量30个,单个布料的规格为2cm
×
2cm的正方形,在室温环境为25℃
±
1℃下进行布料的抗撕裂性能和弹性性能测试,测试结果如表3:
[0099]
表3
[0100][0101]
实验结论:实施例5中,先通过捻搓设备将首尾连接的高收缩纤维线的中部位置捻搓呈螺旋状形态,再通过热压辊将该高收缩纤维线的中部位置加热压合在一起,通过纺织设备加工将多个高收缩纤维线的中部相互粘合的部分依次从防绒层、基层以及抗菌层穿过,该高收缩纤维线两端圈状的穿行通道充作网格端点分布在抗菌层上方以及防绒层下方,通过纺织设备加工将高收缩纤维线的圈状穿行通道、纬纱以及经纱纺织成网状结构,而对比例1中,是通过纺织设备加工直接将纬纱以及经纱纺织成网状结构,根据表3可以可得出,依据对比例1的方法所制备出的布料的弹性性能以及抗撕裂性能均较差;
[0102]
而对比例2中,是直接通过热压辊将首尾连接的高收缩纤维线的中部位置加热压合在一起,根据表3可以可得出,依据实施例5的方法所制备出的布料的弹性性能以及抗撕裂性能均优于依据实施例8的方法所制备出的布料的弹性性能以及抗撕裂性能,因此实施例5为最优的实施例。
[0103]
以上所述实施例仅表达了本发明的几种实施方式,其描述较为具体和详细,但并不能因此而理解为对本发明专利范围的限制。应当指出的是,对于本领域的普通技术人员来说,在不脱离本发明构思的前提下,还可以做出若干变形和改进,这些都属于本发明的保护范围。