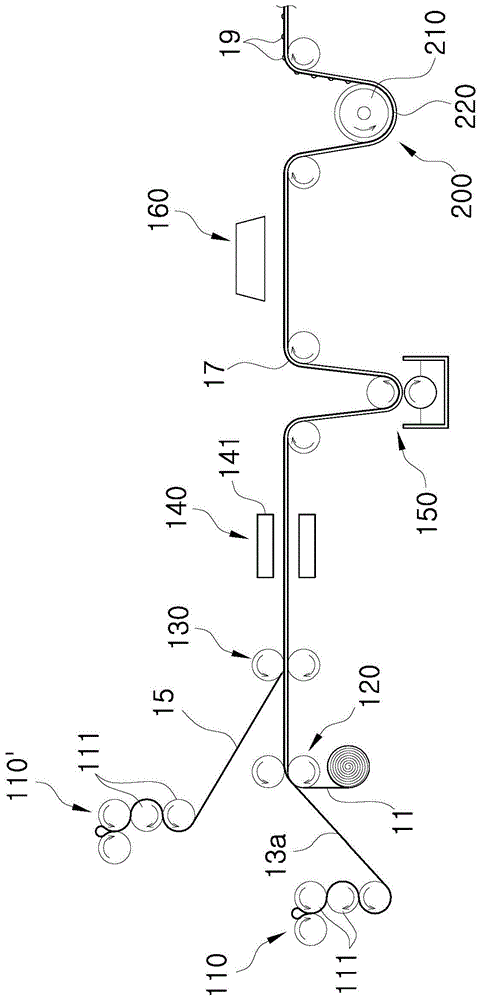
本发明涉及一种人造革制造装置及制造方法,更详细涉及能够通过利用真空的压纹成型装置在人造革的表面有效地吸附成型出压纹的人造革制造装置及利用该装置的人造革制造方法。
背景技术:
:通常,汽车内部被视为第二个居住空间。最近,为了在这种汽车内部空间舒适并愉快地驾驶,功能性座椅受人瞩目。这种汽车座椅材料多用天然皮革或pv、pu人造革。人造革具有比天然皮革价格低廉的优点,但在豪华感和在驾驶时保持愉快的状态的功能性方面,比天然皮革差。因此,一直开发价格比较低廉并同时能够满足天然皮革的触感和功能性方面的人造革。即,天然皮革的功能性方面的优点在于诸如高透湿度和夏季座椅的表面温度降低等。这是因为湿度和热通过形成于天然皮革的表面和内部的无数个气孔进行传递。现有的韩国授权专利第10-0328301号(公告日:2002年03月16日)等申请了用于实现与这种天然皮革相似的特征的具有发泡层的人造革。具体而言,现有的人造革由从下至上地包括背衬层、发泡层、表层、表面处理层的层叠结构构成。此时,所述发泡层和表层主要由pvc(polyvinylchloride,聚氯乙烯)、tpu(thermoplasticpolyurethane,热塑性聚氨酯)材料形成,通过压延(calendar)成型方式以规定的厚度层叠形成。之后,经过发泡工序,所述发泡层以规定倍率发泡成型。另外,使其在表层的上表面压纹成型,以赋予天然皮革的质感和缓冲感。现在,为了使压纹成型,主要使用使层叠有发泡层和表层的半成品通过旋转的辊之间以转印压纹的轧辊式。然而,在利用所述轧辊式的压纹成型方式中,发泡层内的发泡单元不规则且数量少。尤其是,因压纹辊的压力,存在发泡单元的形状以扭曲形状的封闭单元(closecell)形成而非圆形结构的问题。另一方面,在所述压纹成型工序中,压纹辊与经发泡工序之后被加热的人造革的表层的上表面持续地进行面接触,以使压纹成型,因此,压纹辊自身的温度会上升。然而,所述压纹辊应当保持适当的温度,以适用于压纹成型,因此,现有的压纹辊内会使用空冷式(aircoolingtype)冷却装置,以保持适当的温度。此时,所述空冷式的压纹辊需要规定的冷却时间。像这样,现有的压纹成型的工艺速度与之前的制造人造革所需的工艺速度彼此不匹配,因此,只能通过单独的装备分开进行相应工序,因此,存在人造革的生产效率降低的问题。技术实现要素:技术问题本发明为了解决上述问题而被提出,其目的在于提供一种人造革制造装置及制造方法,其能够对在人造革的表层上成型出压纹的压纹辊应用利用真空的吸附方式,从而防止构成发泡层的发泡单元扭曲或破损,并且能够通过将压纹成型装置的压纹辊冷却方式从现有的空冷式变更为水冷式,提高压纹辊的冷却速度,由此能够将压纹成型装置与现有的人造革制造装置以在线(in-line)方式一同使用。技术方案为了实现上述目的,本发明提供一种压纹成型装置,其包括:辊主体部210,呈圆筒状,接受电机203的动力而进行旋转;压纹辊部220,呈管状,以便结合于所述辊主体部210的外周表面,且在表面具备压纹成型用真空孔221和规定的压纹图案223;真空发生部230,其通过所述辊主体部210与所述真空孔221相连接,并通过产生真空,在被供给移送的人造革表面吸附成型出压纹19;以及水冷式冷却部240,位于所述辊主体部210内,将所述压纹辊部220冷却至规定温度。另外,本发明提供一种人造革制造装置,其包括压纹成型部200,所述压纹成型部200通过利用真空的所述压纹成型装置,在发泡成型的半成品的表层15的上表面吸附成型出压纹19。另外,本发明包括如下步骤:预制发泡层或发泡层及表层成型步骤s1,分别成型预制发泡层13a或发泡层13b和表层15;背衬层层叠步骤s3,将机织物或无纺布层叠在所述预制发泡层13a或发泡层13b的底表面,以形成背衬层11;表层层叠步骤s5,将所述表层15层叠在形成有所述背衬层11的预制发泡层13a或发泡层13b的上表面;表面处理层形成步骤s7,在所述表层15的上表面形成表面处理层17;红外线照射步骤s9,向所述表面处理层17的表面照射红外线;以及压纹成型步骤s11,通过所述压纹成型装置,在通过所述红外线照射而被加热的半成品的表层15及表面处理层17的上部吸附成型出压纹19。有益效果上述的本发明能够将压纹成型装置的压纹辊冷却方式从现有的空冷式变更为水冷式,从而提高压纹辊的冷却速度,由此,能够使人造革的制造工艺中的表面处理部与压纹成型部以在线(in-line)方式构成,从而提高生产效率。另外,在本发明的人造革中,能够防止构成发泡层的发泡单元扭曲或破损,从而实现缓冲感优秀的效果。附图说明图1是示出本发明的人造革制造装置的一实施例的概略的整体构成图。图2是示出本发明一实施例的利用真空的压纹成型装置的整体结构的主视图。图3是示出本发明一实施例的辊主体部与压纹辊部的结合状态的分解立体图。图4是示出本发明一实施例的压纹辊部的照片。图5是沿图3的i-i线的剖面图。图6是示出本发明一实施例的真空棒组装件的组装结构的图。图7是图6的‘a’部分的详细图。图8是图6的‘b’部分的详细图。图9是示出本发明一实施例的人造革的层叠结构的侧剖面图。图10是示出利用本发明一实施例的人造革制造装置的人造革制造过程的流程图。附图标记10:人造革11:背衬层13a:预制发泡层13b:发泡层15:表层17:表面处理层19:压纹110:第一成型部110’:第二成型部111:压延辊120:背衬层层叠部130:表层层叠部140:发泡成型部141:加热炉150:表面处理部160:红外线加热部200:压纹成型部210:辊主体部211:主辊211a:喷射孔213:橡胶层215:真空棒组装件215a:真空棒215b:吸入孔215c:固定板215d:结合槽220:压纹辊部221:真空孔223:压纹图案230:真空发生部240:水冷式冷却部241:第一冷却水管243:第二冷却水管具体实施方式以下,参照附图,对本发明的具体实施例的构成及作用进行详细说明。其中,应当注意的是,在对各附图的多个构成要素添加附图标记时,即便示于不同的附图,也尽可能使用相同的附图标记表示了相同的构成要素。图1是示出本发明的一实施例的人造革制造装置的概略的整体构成图。参照图1,本发明的一优选实施例的人造革制造装置包括压纹成型部200,所述压纹成型部200通过利用真空的压纹成型装置,在发泡成型的半成品的表层15的上表面吸附成型出压纹19。此时,在所述压纹成型部200之前可以包括表面处理部150,所述表面处理部150用于在表层15的上表面形成表面处理层17,其中,所述表面处理层17与压纹成型部200可以以在线(in-line)方式配置。另外,可以在所述表面处理部150之前包括:第一成型部100,用于形成预制发泡层13a或发泡层13b;第二成型部100’,用于形成表层15;背衬层层叠部120,将机织物或无纺布层叠在所述预制发泡层13a或发泡层13b的底表面,以形成背衬层11;以及表层层叠部130,用于将所述表层15层叠在所述预制发泡层13a或发泡层13b的上表面。此时,作为一实施例,所述第一成型部100和第二成型部100’可以以压延成型方式构成。所述压延成型可以是使所述预制发泡层13a或发泡层13b及表层15制造用组合物分别在搅拌器中捏合之后,通过160~170℃的压延辊111的压延工艺。作为另一实施例,所述第一成型部100和第二成型部100’可以以通过挤压成型分别形成的方式构成。所述挤压成型可以是使预制发泡层13a或发泡层13b及表层15制造用组合物分别在挤压机中熔融之后利用t-die(t型模头)挤压机的t-die挤压工艺。以下,在本发明中,以形成所述预制发泡层13a或发泡层13b以及表层15的第一成型部100和第二成型部100’采用压延成型方式的情况为例进行说明,但不限于此。另一方面,可包括发泡成型部140,当由所述第一成型部100在预制发泡层13a与发泡层13b中形成预制发泡层13a时,所述发泡成型部140使层叠有所述表层15的半成品通过加热炉141,以使包含发泡剂的预制发泡层13a以规定倍率发泡,从而形成发泡层13b。另外,可以在所述表面处理部150与压纹成型部200之间包括红外线加热部160,所述红外线加热部160能够向层叠有所述表面处理层17的半成品表面照射红外线以进行加热。具体而言,所述红外线加热部160能够将以规定速度移送的人造革半成品在150~180℃(优选160~170℃)的温度下顺利地加热软化,红外线照射时间优选为5~15秒或10~15秒。作为一例,半成品的工艺速度可以是13~17m/min,当为15m/min时,沿移送方向的长度优选为3~4m。即,当缩短所述红外线加热部160的长度而红外线照射不充分时,难以预热成适合压纹成型的状态,例如,当红外线加热部160的长度较短且将热温度设置为较高的190℃以上时,半成品的表层15会熔融而破损。还有加长所述红外线加热部160的长度并降低热温度的方法,但此时会增加设备费用。另外,当降低工艺速度时,在3m以下也能够照射所需的红外线,并且其下限没有限制。本发明的基准工艺速度为12~15m/min,此时,最适当的长度可以是3~4m。作为一例,当工艺速度为15m/min时,红外线照射区(zone)的长度优选为3.5m。另一方面,作为另一实施例,所述表面处理部150能够以在线(in-line)或线外(out-line)方式构成于压纹成型部200之后。优选地,通过使所述表面处理部150以在线方式构成于发泡成型部140与压纹成型部200之间,能够使表面处理层17的厚度均匀,从而能够具有没有斑痕的优秀的外观。作为另一实施例,所述发泡成型部140、表面处理部150、红外线加热部160以及压纹成型部200能够以在线方式构成。作为另一实施例,预制发泡层13a与表层15的第一成型部110、第二成型部110’、背衬层层叠部120、表层层叠部130、发泡成型部140、表面处理部150、红外线加热部160以及压纹成型部200以在线方式构成。图2是示出本发明的一实施例的利用真空的压纹成型装置的整体结构的主视图。参照图2,构成本发明的压纹成型部200的压纹成型装置包括辊主体部210、压纹辊部220、真空发生部230以及水冷式冷却部240。以下,对这种本发明的构成进行具体说明。首先,辊主体部210呈圆筒状,并可旋转地位于放置台201上。这种辊主体部210接受电机203的动力而以规定的速度进行旋转。压纹辊部220在以半成品状态被移送供给的人造革10的表层15的表面形成压纹19。压纹辊部220呈管状,以便结合于辊主体部210的外周表面。参照图3及图4,在压纹辊部220的外周表面具备压纹成型用真空孔221和规定的压纹图案223(参照图4)。此时,真空孔221能够通过单独的工艺来贯通形成,但所述压纹辊部220本身为多孔结构,因此,能够起到真空孔221的功能。本发明以压纹辊部220为多孔结构并起到真空孔221的作用为例进行了说明。但不限于此。具备多个这种所述压纹辊部220,以使用户能够有选择地使用所需规定的压纹图案223并制造人造革10。换言之,以能够将多个压纹辊部220中任一个替换到辊主体部210的外周表面的方式结合。为此,所述辊主体部210具备能够更换压纹辊部220并固定为一体的结构。参照图5,进行详细说明。所述辊主体部210包括:主辊211,当通过空气供给部(未示出)供给空气时,通过位于外周表面的多个喷射孔211a向外部喷射空气;橡胶层213,呈管状,以套入方式结合于主辊211的外周表面,基于通过喷射孔211a所喷射的空气压力向外侧扩张;真空棒组装件215,多个真空棒215a以主辊211的中心轴为旋转中心,以放射状结合在橡胶层213的外周表面,并且在所述真空棒215a的外周表面具备与所述真空孔221相连通的多个吸入孔215b。参照图6,所述主辊211的两侧结合有一对固定板215c,所述一对固定板215c的对置表面具备结合槽215d,以固定真空棒215a的两端。因此,能够将多个真空棒215a以放射状套入结合到主辊211的外周表面。此时,优选地,所述真空棒215a由铝材料形成。另一方面,所述压纹辊部220以松动配合方式结合于真空棒组装件215的外周表面,以便能够在空气供给部未动作时进行更换。这种压纹辊部220由与金属相比具有更高的耐热性和硬度的陶瓷材料形成。具体而言,所述压纹辊部220可以由包含二氧化硅(sio2)、固化剂、玻璃纤维(glassfiber)的材料形成。参照图7,在这种结构的辊主体部210中,当通过空气供给部供给空气时,在橡胶层213膨胀的同时,真空棒组装件215联动并以放射状扩张。因此,扩张的真空棒组装件215对压纹辊部220的内周表面220a进行加压,从而牢牢固定被更换的压纹辊部220。参照图8,真空发生部230通过用于构成辊主体部210的真空棒215a的吸入孔215b与压纹辊部220的真空孔221相连接,并通过产生的真空,在被供给移送的半成品状态的人造革10表面吸附成型出压纹19。即,真空发生部230在使外周表面形成有压纹图案223的压纹辊部220与人造革10的表面接触的状态下,利用真空吸附,从而在人造革10的表面成型出压纹19。此时,示于附图的真空孔221和压纹19的形状比实际更加夸张,以方便说明利用真空的吸附成型原理,因此,实际形状可能与此不同。水冷式冷却部240位于辊主体部210内,并将压纹辊部220冷却至规定温度。即,在压纹成型工序中,压纹辊部220与经发泡工序之后被加热的人造革10表面持续地进行面接触,以成型出压纹19,因此,辊主体部210和压纹辊部220的温度会上升至适当值以上。因此,需要通过水冷式冷却部240将压纹辊部220的温度冷却至规定数值以下。具体而言,所述水冷式冷却部240沿真空棒215a的内部长度方向设置有第一冷却水管241,从而使通过冷却水供给部240a供给的冷却水进行循环。另外,所述第一冷却水管241与位于主辊211内部的第二冷却水管243(参照图5)相连接,以使冷却水进行循环,从而提高冷却效率。通过这种水冷式冷却部240的结构,能够将压纹辊部220的温度冷却至适当值60~80℃。对利用上述的本发明的一优选实施例的人造革制造装置所制造的人造革10的层叠结构进行说明。参照图9,人造革10从下至上地包括背衬层11、发泡层13b、表层15以及表面处理层17,并可以包括形成于所述表层15及表面处理层17的上部的压纹19。更具体而言,背衬层11能够辅助机械物性,并起到保持人造革的形态及抗皱等作用,可以是基于棉、人造丝、丝绸、聚烯烃(例如,聚乙烯、聚丙烯等)、尼龙、聚酯、聚氨酯等多种合成物的机织物、无纺布、编织织物、平织织物、纺粘织物等柔性聚合物,并可以有选择地进一步包括天然纤维及/或合成纤维。发泡层13b用于对人造革赋予柔和的特性及缓冲感,可以由包含热塑性树脂、增塑剂以及发泡剂的发泡层制造用组合物形成。此时,所述热塑性树脂可以是能够同时确保优秀的缓冲感和高延伸率以及优秀的耐久性的pvc树脂。表层15用于确保表面平滑度并体现颜色,可以由包含热塑性树脂、增塑剂以及颜料的表层制造用组合物形成。另外,所述表层15制造用组合物可以进一步包括热稳定剂、难燃剂以及填充剂,以调节熔融强度及物性。表面处理层17可在所述表层15涂布双液型水性表面处理剂后,经干燥及熟化而形成。具体而言,通过在所述表层15的上部涂布所述双液型水性表面处理剂,能够形成厚度为4~30μm的表面处理层17,通过将所述表面处理层17的厚度保持在上述范围内,能够在保持人造革的柔软性的状态的同时,确保耐污染性。当小于上述范围时,厚度过薄,导致耐久性降低,当大于上述范围时,水性表面处理剂的需要增加,导致需要较多的材料费用,因此,优选具有上述范围内的厚度。压纹19形成于通过照射红外线而被加热的半成品的表层15及表面处理层17的表面,能够利用本发明的压纹成型装置形成规定的压纹图案。以下,对具有所述层叠结构的人造革10的制造过程进行说明。图10是示出利用本发明的一实施例的人造革制造装置的人造革制造过程的流程图。参照图10,首先,通过第一成型部100和第二成型部100’分别形成预制发泡层13a或发泡层13b和表层15(s1)。然后,将机织物或无纺布层叠在所述预制发泡层13a或发泡层13b的底表面,以形成背衬层11(s3)。然后,将所述表层15层叠在形成有背衬层11的预制发泡层13a或发泡层13b的上部(s5)。此时,当通过所述第一成型部100形成预制发泡层13a时,在所述表层15层叠步骤之后,使半成品通过加热炉141,以使包含发泡剂的所述预制发泡层13a以规定倍率发泡,从而形成发泡层13b(s6)。然后,在所述表层15的上表面涂布表面处理剂,以形成表面处理层17(s7)。向形成有所述表面处理层17的半成品表面照射红外线以进行加热(s9)。然后,利用真空,在通过所述红外线照射而被加热的半成品的表层15及表面处理层17的上部吸附成型出压纹19,从而完成本发明的人造革的制造(s13)。此时,本发明的一实施例的人造革制造方法可以由所述发泡成型步骤s6、表面处理层形成步骤s7、红外线照射步骤s9以及压纹成型步骤s11以在线方式构成。或者,可以由所述预制发泡层或发泡层及表层成型步骤s1、背衬层层叠步骤s3、表层层叠步骤s5、发泡成型步骤s6、表面处理层形成步骤s7、红外线照射步骤s9以及压纹成型步骤s11以在线方式构成。此时,所述利用真空吸附成型出压纹19的压纹成型步骤s11可以在0.02~0.08mpa,优选在0.04~0.07mpa的压力下进行。当所述压纹成型步骤s11在小于上述压力范围下进行时,难以形成压纹19,从而导致缓冲感降低,当在大于上述范围下进行时,会损伤表面处理层17,或表面物性降低,因此,优选在上述压力范围内进行。另外,所述压纹成型步骤s11可以在150~190℃,优选在160~180℃的温度下进行。当所述工序在小于上述温度范围下进行时,难以充分形成压纹19,当在大于上述范围下进行时,因高温,人造革的表面物性会变得粗糙或撕裂,因此,优选在上述温度范围内进行。能够利用真空在通过向有选择地经所述发泡过程的半成品的表层15的上部照射红外线而被加热的半成品的表层15表面吸附成型出压纹19之后,涂布表面处理剂,以形成表面处理层17,从而完成人造革的制造。上述的本发明能够将压纹成型装置的压纹辊冷却方式从现有的空冷式变更为水冷式,从而提高压纹辊的冷却速度,由此,能够使人造革的制造工艺中表面处理部150与压纹成型部200以在线(in-line)方式构成,从而提高生产效率。更具体而言,对根据所述压纹辊部200的冷却方式的压纹19成型速度进行说明。利用本发明的包括水冷式冷却部240的压纹成型装置所制造的实施例和利用包括空冷式冷却部的现有的压纹成型装置所制造的比较例的人造革压纹成型速度示于下表1。表1实施例比较例生产速度[m/min]~30~9如上表1所示,具备本发明的水冷式冷却部240的实施例的压纹成型装置与具备空冷式冷却部的比较例的压纹成型装置相比,压纹成型速度约为3.3倍,显著地更快。另一方面,所述比较例的具备空冷式冷却部的现有的压纹成型装置在冷却压纹辊时需要相当长的时间。即,所述现有的压纹成型装置与构成人造革制造装置的其他装置生产速度不同,因此无法以在线方式构成。相反地,本发明的具备水冷式冷却部240的压纹成型装置的压纹辊的冷却速度比现有的压纹成型装置更快,即,本发明的压纹成型装置能够与构成人造革制造装置其他装置生产速度相匹配,从而能够以在线方式构成。因此,能够提高人造革的生产效率。另一方面,现有的压辊方式的压纹成型装置的压纹转印效率为80~90%,但本发明的利用真空的压纹成型装置的压纹转印效率可以是100%。以上,通过特定的具体实施例对本发明进行了示例并进行了说明,但本发明不限于上述实施例,并且,在不超出本发明的技术思想的范围内,能够进行多种变形及修改。当前第1页12