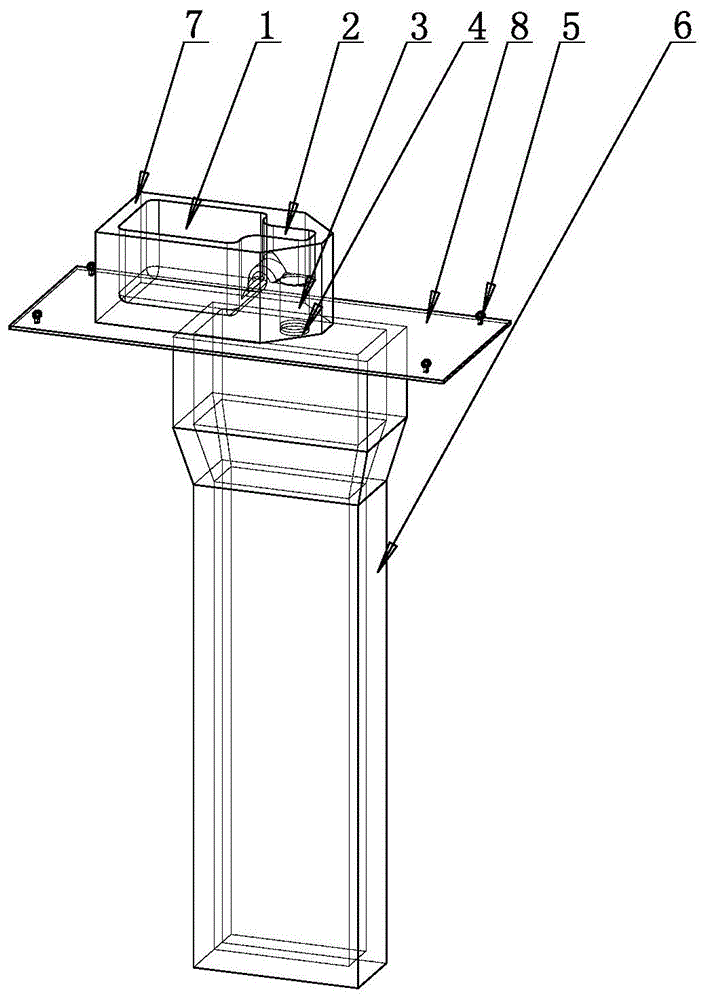
本发明涉及一种浇铸转移装置,属于耐火材料领域。
背景技术:
:低铁玻璃在高档建筑、家具及太阳能
技术领域:
具有广泛的应用,因此近年来得到极快的发展,生产该品种玻璃的窑炉结构与普通浮法玻璃窑炉基本相同,只是在成型部位略有不同。生产低铁玻璃的窑炉耐材也与通常浮法玻璃窑炉相同,熔化部同样采用电熔azs砖。在通常浮法玻璃窑炉中对池壁砖的侵蚀以液面线处最为严重,液面线下侵蚀逐渐减弱,但在低铁玻璃窑炉中因为玻璃的铁含量低,玻璃液透热性强,玻璃液上下温差小,所以对池壁砖的侵蚀呈现出整体性,对池壁砖上下两端侵蚀都极为严重;此外因为低铁玻璃粘度低,对池壁砖缝处的侵蚀也非常严重。作为玻璃窑炉耐材的电熔azs砖自身冷却遵循由外向内,由下向上的逐层冷却顺序,池壁砖上端液面线附件组织致密,耐侵蚀性强,而下端的致密性则较上端差。表层致密,内部因为属于最后凝固的部位因而组织疏松,尤其是下端中央部位。电熔砖的这种结构特点导致在玻璃窑炉运行中容易发生中下部的漏料问题,不得不进行热修,严重的会使的窑炉被迫停炉,导致严重的经济损失,并且可能产生严重的人身安全问题。所以对于低铁玻璃窑炉而言需要提高现有电熔azs砖的耐侵蚀性。做为业内所了解的常识,电熔砖的耐侵蚀性是通过在特定温度下一定时间内测定某种玻璃对样品的侵蚀量及测定电熔azs砖特定部位气孔比率来衡量的,在特定温度下一定时间内侵蚀量越小,气孔比率越低意味着耐侵蚀性越强,通过不同的技术手段可以达到减少侵蚀量,减少气孔率的效果。azs电熔砖的生产是将在电弧炉中熔化好的料液澄清后浇铸到事先成型好的砂型中,经过冷却退火保温后采用金刚石磨具加工成制品的过程。熔化完成后要吹入氧气,以便去除电极所含的碳元素带来的不利影响。但吹入的氧气会有部分残留在料液内部,虽然经过后续的澄清冷却后大部分吹入气体能够被排出,但仍有少量气体残留在料液中,这些气体在电熔砖的冷却退火中残留在电熔砖内部,造成内部气孔增加。因为这些内部气孔的存在,在电熔砖的侵蚀过程中会在有气孔的位置发生气液固三相界面的侵蚀,使得电熔砖的侵蚀速度被大大加快,对于低铁玻璃窑炉而言更加明显,导致窑炉寿命缩短,甚至被迫提前停炉,因此需要降低电熔砖的内部气孔率以提高电熔砖的使用性能。通常电熔砖浇铸是将准备好的砂型放于电炉炉嘴附近,然后对准砂型上的冲击部位,通过向前倾斜炉体使得料液从炉体中倒出,在此过程中为了避免高温下涂料的脱落及长时间对石英砂型的冲刷可能造成的漏料、气孔等问题,需要不断调整浇铸角度,尽量将料液浇铸在砂型中央位置,因为在持续的浇铸过程中需要不断调整冒口与炉嘴的相对位置,所以料液飞溅出的多,浇铸时间长,同时为了确保砖材的致密度浇铸后需要用钢棍插入进行搅拌、通气并进行再注入补浇,员工劳动强度很大。现有技术方案是在熔化后期降低电力量,采用拉弧方式将电极贴近料液面进行低电力熔化,该方式可以维持料液表面的液态状体,防止料液表面结壳导致内部气体不能排出(也称为“澄清”过程),但因料液内外温差很小,所以气体排出效果有限。另外近年来v法铸造方式在电熔砖行业有所推广,如专利cn201010541884.3,cn200710055073.0等,但该方式只是通过对砂型抽真空以便铸造生产,对电熔砖内部气孔降低没有实质性作用。技术实现要素:本发明的目的是提供一种浇铸转移装置,通过设置空腔,使料液从较大的空腔流入较小的空腔,然后进入砂型中,可以有效地减少残留在azs电熔砖内部的气孔,提高电熔砖的耐侵蚀性,有效延长玻璃窑炉的使用寿命、确保窑炉安全。本发明所述的浇铸转移装置,包括浇铸转移载体,浇铸转移载体内设有第一空腔,所述第一空腔通过第二空腔连接下料口,第二空腔设置在浇铸转移载体内,下料口贯穿于浇铸转移载体。料液从第一空腔经第二空腔流入下料口,料液转移过程中,可以释放残留在azs电熔砖内的大量气泡,可以有效减少产品成型后的气孔率,提高电熔砖的耐侵蚀性。所述的第一空腔的宽度为200-500mm,长度为300-800mm,深度为120-500mm。所述的第二空腔的宽度为50-150mm,长度为100-300mm,深度为50-100mm。第一空腔的深度不小于第二空腔的深度,第一空腔的容积不小于第二空腔的容积,更利于料液在转移过程中气孔的挥发。所述的下料口的直径为50-100mm,浇铸转移载体的厚度最小为15mm。所述的第二空腔底部为弧形。使得料液转移过程更加顺畅,同时料液在第一空腔内的流动更加均匀,避免产生清洗死角。所述的浇筑转移装置底部设有支撑隔板,支撑隔板上设有出料口,所述的下料口和出料口对应放置,出料口的直径和下料口的直径相适应。所述的支撑隔板上设有吊钩。通过设置支撑隔板,并且在支撑隔板上设置吊钩,可以工行车对浇铸转移装置进行搬运,避免搬运过程中高温状态下的浇铸转移装置对操作人员带来不必要的损伤。所述的浇筑转移载体和支撑隔板为一体成型结构。所述的浇筑转移载体的材质为钢材、白刚玉或者石墨。与现有技术相比,本发明的有益效果是:1、本使用新型所述的浇铸转移装置,通过设置不同容积的空腔,料液从第一空腔上升经第二空腔流入下料口,在料液转移过程中,可以释放残留在azs电熔砖内的大量气泡,而而后续料液陆续倒入起到了搅拌作用,加速料液内残留气体的排出,可以有效减少产品成型后的气孔率,提高电熔砖的耐侵蚀性。2、避免原来浇铸过程中因为位置调整造成的料液浪费,浇铸过程中洒出料液量减少80%。3、使用浇铸转移装置后,可以有效减少浇铸成型过程中缩孔现象的出现,可以通过浇铸转移装置完成补浇,减少员工的工作强度,并且减少补浇次数,可以使料液使用量减少8%以上。4、使用浇铸转移装置后,azs电熔砖内部各处的气孔率在常规方式的20%以下。5、使用浇铸转移装置后,产品的致密度较常规方式提高35%,气孔率降低的azs电熔砖的耐侵蚀性较常规方式提高20%以上。6、本装置使得原来的变大,使得作业方式灵活方便,简单易行,降低了作业强度。7、使用浇铸转移装置后,由原来的直接浇铸变为通过料液自身的重力作用流向砂型,避免了常规方式通过炉嘴直接倾倒过程中卷入的空气,又进一步减少电熔砖内部气孔,使得浇铸过程更加稳定,产品致密性更好。附图说明图1是本发明所述浇铸转移装置使用状态下的结构示意图;图2是本发明所述浇铸转移装置的俯视图;图3是本发明所述浇铸转移装置的结构示意图;图中:1、第一空腔2、第二空腔3、下料口4、出料口5、吊钩6、砂型7、浇铸转移载体8、支撑隔板。具体实施方式实施例1如图1-3所示,本发明所述的浇铸转移装置的实施例,包括浇铸转移载体7,浇铸转移载体7内设有第一空腔1,所述第一空腔1通过第二空腔2连接下料口3,第二空腔2设置在浇铸转移载体7内,下料口3贯穿于浇铸转移载体7。所述的第一空腔1的宽度为200-500mm,长度为300-800mm,深度为120-500mm。所述的第二空腔2的宽度为50-150mm,长度为100-300mm,深度为50-100mm。第一空腔的深度不小于第二空腔的深度,第一空腔的容积不小于第二空腔的容积。所述的下料口3的直径为50-100mm,浇铸转移载体7的厚度最小为15mm。所述的第二空腔2底部为弧形。所述的浇筑转移装置底部设有支撑隔板8,支撑隔板8上设有出料口4,所述的下料口3和出料口4对应放置,出料口4的直径和下料口3的直径相适应。所述的支撑隔板8上设有吊钩5。所述的浇筑转移装置和支撑隔板8为一体成型结构。所述的浇筑转移载体7的材质为钢材、白刚玉或者石墨。工作过程或工作原理:本发明的实施方式时,只需要用行车将浇铸转移装置放到带吊钩5的支撑隔板8上,然后再用行车通过吊钩5将该装置放到普通砂型6冒口上便可进行浇铸。下面结合具体实验对本装置加以验证:对玻璃窑炉常用的250mm厚度池壁砖,采用本方案与常规技术方案进行对比分析,以确认本方案的改善效果,对比内容包括裂纹率、显气孔率、抗玻璃侵蚀速度。按照jc/t493-2015规定的裂纹规格进行统计确认裂纹情况。为确认产品内部气孔的改善情况随机选取同材质同尺寸产品测定不同位置的显气孔率,分析方式遵循jc/t493-2015的要求。为确认气孔率改善与azs电熔砖耐侵蚀性之间的关系,按照jc/t493-2015规定的方式进行静态下抗玻璃液侵蚀速度测定。为确保azs电熔砖内部组织致密性采用电磁波无损探伤进行砖材内部组织确认,按照组织致密度的差异将砖材内部组织分为a、b、c、d四个等级,其中d级属于不合格品,c级以上属于合格品,b级以上属于组织致密度较好的产品。通过对比b级以上组织的产品的比例确认本方案的改善效果。同时为了全面评价本方案的效果,对常规浇铸方式与本方案浇铸过程中料液量的重量差别(以kg计算),浇铸过程中洒出的料液重量(以kg计算)的差别进行对比统计。为降低现场员工工作强度,尝试取消浇铸完成后不再用钢棍搅拌进行再注入补浇的作业。验证过程:将azs砖原料按照一定比例加入到电炉中进行熔化,熔化完成后进行吹氧澄清,用行车将转移装置放到池壁冒口上方,进行浇铸,浇铸过程中通过辅助系统确认浇铸料液量,浇铸完成后通过机械装置收集洒出凝固的料液结块冷却后测定重量。浇铸不同尺寸规格的池壁砖,并选择相同尺寸的砖进行通常浇铸方式与本方案进行比较,比较内容为裂纹率、内部探伤,尺寸分别为250*400*1550,250*450*1500,250*400*1500,单位mm,其中250*400*1550和250*400*1500的产品采用的冒口空腔1的宽度为400mm,长度为600mm,深度为500mm,空腔2的宽度为100mm,长度为200mm,深度为80mm,下料孔的直径为60mm;250*450*1500的产品采用的冒口空腔1的宽度为450mm,长度为550mm,深度为450mm,空腔2的宽度为100mm,长度为300mm,深度为100mm,下料孔的直径为80mm。具体如表1所示。随机选取加工后同材质同尺寸的不同浇铸方式铸造产品,取底部及距底500mm处中心及表皮样品进行显气孔率的测试,具体如表2所示。选取底部以上100mm进行抗玻璃液侵蚀测试,结果见表3。表1池壁砖浇铸评价表表2:不同部位气孔率对比表3:不同浇铸方式抗玻璃液侵蚀速度对比项目常规本实例33zws1.541.236ws1.471.1641ws1.31.03从表1中可以看到,对于通常方式与本方案的对比方式,通常方式取消再注入操作时出现不合格的情况,且b组织以上比例为60%,a组织比例为20%。本方案中b组织以上比例为95%,a组织以上比例达到45%,改善效果显著,需要特别注意的是本方案中b组织以下比例仅为5%,即使取消再注入操作产品组织也没有出现没有不合格的情况,这对于改善现场员工的作业意义巨大,使得现场员工不必在高温下从事用钢棍通冒口这样繁重的体力劳动,极大减轻了作业强度。从表1可以看到采用本方案后,浇铸过程中洒出浪费的料液量大为减少,绝大部分在5kg以下,较之通常方式动辄在30kg左右的浪费量相比效果明显。另一方面由于可以取消再注入作业,平均减少料液重量约在210kg,二者累计对降低企业成本有着积极的作用。从表2可以看到,采用本方案后,产品内部气孔率,尤其是中间部位气孔率有了极大的降低,本方案产品内部气孔率仅为通常方式的20%以下,产品的均一性得到极大提高。从表3可以看出,电熔砖内部气孔率的降低,有效降低了抗玻璃液的侵蚀速度,不同品种的电熔azs砖的抗侵蚀速度较原来提高20%以上,效果显著。综合以上数据,本方案对于改善产品内部气孔,提高产品的耐用性有着明显的效果,可以有效地减少残留在azs电熔砖内部的气孔,提高电熔砖的耐侵蚀性,有效延长玻璃窑炉的使用寿命、确保窑炉安全。当前第1页12