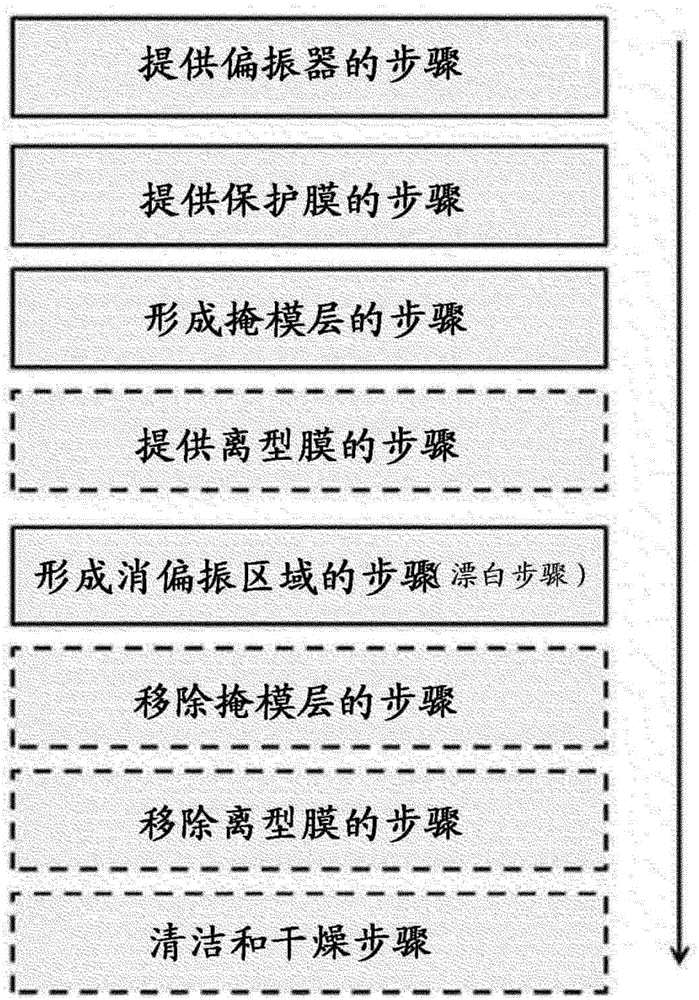
本申请要求于2014年10月6日在韩国知识产权局提交的韩国专利申请第10-2014-0134101号的优先权和权益,其全部内容通过引用并入本文。本发明涉及用于制造偏振片的方法及使用其制造的偏振片。
背景技术:
:液晶显示器是构造成使由液晶的转换效应所引起的偏振可视化的显示器,并已用于包含小型显示器和中型显示器的多种范畴,例如手表、电子计算器、移动电话和大屏幕TV。近来,强调便携性和移动性的小型和中型显示装置或笔记本计算机已变得普遍配置有多种功能,例如摄像机和视频通信,并且近来发布的实现上述功能的液晶显示器具有摄像机镜头暴露在外的结构。然而,液晶显示装置应包括附接在液晶元件外表面的偏振器或偏振片。当被附接时,偏振器或偏振片可能覆盖暴露在外的摄像机镜头,因此镜头的可视性可能因偏振片的固有透射率低于50%而降低。为了解决这一问题,当附接偏振片时,已经使用了通过冲孔或切割将覆盖摄像机镜头的偏振片的一部分穿孔并移除的物理移除法,和/或用碘离子化学物质将覆盖摄像机镜头的偏振片的一部分分离或漂白的化学移除法。然而,这样的方法具有损坏镜头、污染镜头、以及难以精确控制待移除区域的缺点。因此,需要研究用于制造应用于显示装置的偏振片的方法,所述显示装置具有摄像机镜头暴露在外的结构。技术实现要素:技术问题本说明书提供了用于制造偏振片的方法及使用其制造的偏振片。技术方案本说明书的一个方面提供了用于制造偏振片的方法,其包括:提供经碘和二色性染料中至少一者染色的基于聚乙烯醇的偏振器;在所述偏振器的一个表面上提供保护膜;在所述偏振器的另一个表面上提供包含至少一个穿孔部分的掩模层;以及通过使包含1重量%至30重量%漂白剂的漂白液与其上提供有掩模层的偏振器的另一个表面局部接触,形成在400nm至800nm的波长段内单透射率为80%或更高的消偏振区域,其中所述漂白液的表面张力为50mN/m或更小。此外,本说明书的另一个方面提供了通过上述制造方法制造的偏振片。此外,本说明书的又一个方面提供了图像显示装置,其包括:显示面板;和附接于所述显示面板的一个表面或两个表面的偏振片。此外,本说明书的再一个方面提供了表面张力为50mN/m或更小的漂白液。有益效果在根据本说明书的一个方面的用于制造偏振片的方法中,不进行冲孔或切割过程,通过化学漂白方法在期望位置形成经漂白区域。因此,对偏振片的损坏可最小化。此外,根据本说明书的一个方面的用于制造偏振片的方法包括连续工艺,并因此具有优异的工艺效率且需要低制造成本。此外,在根据本说明书的一个方面的用于制造偏振片的方法中,漂白过程期间微气泡的产生被抑制。因此,在进行连续工艺时,缺陷率可降低,致使稳定地进行连续工艺。此外,通过根据本说明书一个方面的用于制造偏振片的方法制造的偏振片在安装构件的部分或者显示颜色的区域包括几乎透明的消偏振区域。因此,可以抑制待安装构件的性能劣化,并且还可以实现多种颜色和/或设计。附图说明图1是为说明根据本说明书一个示例性实施方案的用于制造偏振片的方法而提供的流程图。图2是为说明在形成消偏振区域时产生微气泡的原因而提供的图,所述微气泡引起未漂白位点的产生。图3是示出由微气泡引起的未漂白位点的图。图4是为说明在实施例1至3中没有产生未漂白位点的原因而提供的图。具体实施方式下文中,将更详细地描述本说明书。就常规偏振片而论,由于偏振片的全部区域被碘和/或二色性染料染色,因此偏振片为深黑色。因此,难以给予显示装置各种颜色。特别地,如果偏振片位于构件例如摄像机上,则偏振片吸收50%或更大的光量,使得摄像机镜头的可视性降低。为了解决这一问题,已经使用了通过冲孔、切割等在偏振片的一个部分中冲出孔(穿孔)的方法,以物理移除覆盖摄像机镜头的偏振片部分。然而,物理方法降低图像显示装置的外观,并且可能因冲孔工艺的性质而损坏偏振片。同时,为了抑制偏振片的损坏例如撕裂,需要足够远离边缘来形成偏振片的穿孔部分。因此,如果将偏振片应用于图像显示装置,则图像显示装置的边框部件变得相对较宽,这导致这样的问题:脱离近来用以实现图像显示装置的大屏幕的窄边框设计趋势。此外,如果摄像机模块安装在如上所述的偏振片的穿孔部分上,则摄像机镜头暴露在外,当长时期使用时,这可能引起污染和损坏摄像机镜头的问题。因此,本公开内容提供了使得能够通过简单工艺移除偏振的化学方法,而不进行物理冲孔并且不降低外观。具体地,本说明书提供了这样的化学方法,其非常容易进行连续工艺并且在连续工艺中稳定。本说明书的一个示例性实施方案提供了用于制造偏振片的方法,其包括:提供经碘和二色性染料中至少一者染色的基于聚乙烯醇的偏振器;在所述偏振器的一个表面上提供保护膜;在所述偏振器的另一个表面上提供包含至少一个穿孔部分的掩模层;以及通过使包含1重量%至30重量%漂白剂的漂白液与其上提供有掩模层的偏振器的另一个表面局部接触,形成在400nm至800nm的波长段内单透射率为80%或更高的消偏振区域,其中所述漂白液的表面张力为50mN/m或更小。本文中,偏振器的另一个表面是指其上未提供保护膜的反面。图1示出根据本说明书的一个示例性实施方案的用于制造偏振片的方法的示意性流程图。如图1中所示,根据本说明书的一个示例性实施方案的用于制造偏振片的方法包括:提供经碘和二色性染料中至少一者染色的基于聚乙烯醇的偏振器;在所述偏振器的一个表面上提供保护膜;在所述偏振器的另一个表面上提供包含至少一个穿孔部分的掩模层;以及通过使漂白液与提供有掩模层的偏振器的另一个表面接触而形成消偏振区域。同时,根据本说明书的一个示例性实施方案的用于制造偏振片的方法还可根据需要包括提供离型膜的步骤、移除掩模层的步骤、移除离型膜的步骤、和/或清洁步骤。在本说明书中,术语“提供”可意指“层合”。本发明的发明人发现,如果通过选择性地使漂白液与经碘和/或二色性染料染色的基于聚乙烯醇的偏振器的一部分接触来局部形成消偏振区域,则不像物理方法例如冲孔和切割那样产生穿孔,并且在将保护膜层合于偏振器的一个表面上之后进行漂白过程,因而偏振器的溶胀被抑制,并且消偏振区域中的微褶皱可最小化。通常,如果使漂白液与其上未层合保护膜的基于聚乙烯醇的偏振器直接接触,则偏振器因水分而溶胀,因而可能在消偏振区域和消偏振区域周围形成褶皱。在这种情况下,消偏振区域的表面粗糙度增加且雾度增加。因此,难以充分获得偏振片的外观和位于消偏振区域中的摄像机的可视性。就此而言,如果根据本说明书的用于制造偏振片的方法在与漂白液接触之前将保护膜层合于偏振器的一个表面上,则保护膜与偏振器彼此结合,因而可抑制溶胀和褶皱。此外,本发明的发明人发现,可以通过如下步骤有效地提高连续工艺的容易度和对缺陷的抑制:使用表面张力低,特别地为50mN/m或更小的漂白液,并且在使偏振器与漂白液接触之前提供包含一个或更多个穿孔部分的掩模层,然后形成消偏振区域。下文中,将更详细地描述根据本说明书的一个示例性实施方案的用于制造偏振片的方法的各个步骤。基于聚乙烯醇的偏振器可通过本领域已知用于制造PVA偏振器的方法来制造,或者可通过购买市售的基于聚乙烯醇的偏振器来使用。提供基于聚乙烯醇的偏振器的步骤可如下进行,例如,但不限于:用碘和/或二色性染料对基于聚乙烯醇的聚合物膜进行染色,对基于聚乙烯醇的膜和染料进行交联,以及拉伸所述基于聚乙烯醇的膜。首先,进行染色步骤以用碘分子和/或二色性染料对基于聚乙烯醇的膜进行染色。碘分子和/或二色性染料分子吸收在偏振器的拉伸方向上振动的光,并且透射在垂直方向上振动的光,因而使得可以获得在特定振动方向上的偏振。此处,例如,染色步骤可通过将基于聚乙烯醇的膜浸没在填充有碘溶液和/或含二色性染料的溶液的处理浴中来进行。本文中,通常使用水作为用于染色步骤的溶液中的溶剂,并且可添加适量与水相容的有机溶剂。同时,相对于100重量份溶剂,可使用0.06重量份至0.25重量份的量的碘和/或二色性染料。如果二色性物质例如碘在上述范围内,则拉伸后制造的偏振器的透射率可满足40.0%至47.0%的范围。同时,如果使用碘作为二色性物质,则优选地,还可包含辅剂例如碘化物以提高染色效率。相对于100重量份溶剂,可使用0.3重量份至2.5重量份的量的辅剂。使用辅剂例如碘化物的原因是为了提高碘在水中的溶解度,因为碘在水中具有低溶解度。同时,优选地,碘和碘化物的重量混合比可为1:5至1:10。可添加的碘化物的具体实例可包括碘化钾、碘化锂、碘化锌、碘化铝、碘化铅、碘化铜、碘化钡、碘化钙、碘化锡、碘化钛或其混合物,但不限于此。同时,可将处理浴的温度保持在25℃至40℃。如果处理浴的温度低于25℃,则染色效率可能降低;而如果处理浴的温度高于40℃,则发生大量碘的升华,并且使用的碘的量可能增加。本文中,优选地,将基于聚乙烯醇的膜浸没在处理浴中的时间可为30秒至120秒。如果浸没时间小于30秒,则可能无法实现基于聚乙烯醇的膜的均匀染色;而如果浸没时间大于120秒,则染色可能饱和,并因此所述膜不再需要浸没。同时,进行交联步骤以使碘和/或二色性染料吸附至聚乙烯醇聚合物基体。交联步骤通常使用浸没法进行,其中将基于聚乙烯醇的膜浸没在填充有硼酸水溶液等的交联浴中,但不限于此。其还可通过涂敷或喷洒法来进行,其中将包含交联剂的溶液涂敷或喷洒在基于聚乙烯醇的膜上。本文中,通常使用水作为交联浴中溶液的溶剂,并且可添加适量与水相容的有机溶剂。相对于100重量份溶剂,可添加0.5重量份至5.0重量份的量的交联剂。如果添加小于0.5重量份的量的交联剂,则基于聚乙烯醇的膜中的交联度可能不足,并因此,所述基于聚乙烯醇的膜在水中的强度可能减小。如果添加大于5.0重量份的量的交联剂,则可能发生过度交联,导致基于聚乙烯醇的膜的可拉伸性降低。此外,交联剂的具体实例可包括硼化合物例如硼酸或硼砂、乙二醛、戊二醛等,其可单独使用或组合使用。然而,本发明不限于此。同时,交联浴的温度根据交联剂的量和膜的拉伸比而变化,并且优选为45℃至60℃,但不限于此。通常,随着交联剂的量增加,将交联浴的温度控制于高温,以提高基于聚乙烯醇的膜中链的移动性;而随着交联剂的量减少,将交联浴的温度控制于相对低的温度。然而,按照根据本说明书的一个示例性实施方案的用于制造偏振片的方法,将膜拉伸至少5倍。因此,需要将交联浴的温度保持在45℃或更高以提高基于聚乙烯醇的膜的可拉伸性。同时,基于聚乙烯醇的膜在交联浴中浸没的时间可优选地为30秒至120秒。如果浸没时间小于30秒,则可能无法实现基于聚乙烯醇的膜的均匀交联;而如果浸没时间大于120秒,则交联可能饱和,并因此所述膜不再需要浸没。同时,进行拉伸步骤以使基于聚乙烯醇的膜中的聚合物链以预定方向排列。拉伸方法可分为湿拉伸法和干拉伸法。干拉伸法进一步分为辊间拉伸法、热辊拉伸法、压机拉伸法、拉幅机拉伸法等;而湿拉伸法可进一步分为拉幅机拉伸法、辊间拉伸法等。本文中,可进行拉伸步骤以在优选4倍至10倍的拉伸比下拉伸基于聚乙烯醇的膜。为了赋予基于聚乙烯醇的膜偏振性能,需要排列基于聚乙烯醇的膜中的聚合物链。在小于4倍的拉伸比下,基于聚乙烯醇的膜中的链不能充分排列;而在大于10倍的拉伸比下,基于聚乙烯醇的膜中的链可能断裂。本文中,拉伸步骤可在优选45℃至60℃的拉伸温度下进行。拉伸温度可根据交联剂的量变化。在低于45℃的温度下,基于聚乙烯醇的膜中的链的移动性可能降低,并且拉伸效率可能降低;而在高于60℃的温度下,基于聚乙烯醇的膜可能变软,并因此强度可能降低。同时,拉伸步骤可与染色步骤或交联步骤同时进行或者分开进行。同时,拉伸步骤可只对基于聚乙烯醇的膜进行,或者可在将基底膜层合于基于聚乙烯醇的膜上之后,对基于聚乙烯醇的膜和基底膜一起进行。如果拉伸厚度小的基于聚乙烯醇的膜(例如,60μm或更小的PVA膜),则基底膜用于抑制拉伸步骤期间基于聚乙烯醇的膜的断裂,并因此可用于制造10μm或更小的薄PVA偏振器。在这种情况下,可使用在20℃至85℃的温度下的最大拉伸倍率为5倍或更大的聚合物膜作为基底膜。例如,基底膜可包括高密度聚乙烯膜、聚氨酯膜、聚丙烯膜、聚烯烃膜、基于酯的膜、低密度聚乙烯膜、高密度聚乙烯和低密度聚乙烯的共挤出膜,具有包含在高密度聚乙烯中的乙烯乙酸乙烯酯的共聚物树脂膜、丙烯酸膜、聚对苯二甲酸乙二醇酯膜、基于聚乙烯醇的膜、和基于纤维素的膜。同时,最大拉伸倍率表示恰好在断裂发生之前的拉伸倍率。此外,将基底膜和基于聚乙烯醇的膜层合的方法没有特别限制。例如,可使用粘合剂将基底膜和基于聚乙烯醇的膜层合,或者可不用任何介质将基于聚乙烯醇的膜置于基底膜上。另外,将基底膜和基于聚乙烯醇的膜层合的方法可通过将构成基底膜的树脂与构成基于聚乙烯醇的膜的树脂共挤出来进行,或者可通过将基于聚乙烯醇的树脂涂覆在基底膜上来进行。同时,在完成拉伸步骤后,可将基底膜与偏振器分离并移除,或者可不将其移除并可进行后续步骤。在这种情况下,基底膜可用作用于偏振器的保护膜。然后,如果基于聚乙烯醇的偏振器通过上述方法来制备,则可进行在基于聚乙烯醇的偏振器的一个表面上提供保护膜的步骤。术语“保护膜”是指附接至偏振器的一个表面以保护厚度非常小的偏振器的透明膜。可使用具有优异的机械强度、热稳定性、防潮特性并且各向同性的膜作为保护膜。保护膜可为基于乙酸酯的树脂膜例如三乙酰纤维素(TAC)膜、基于聚酯的树脂膜、基于聚醚砜的树脂膜、基于聚碳酸酯的树脂膜、基于聚酰胺的树脂膜、基于聚酰亚胺的树脂膜、基于聚烯烃的树脂膜、基于环烯烃的树脂膜、基于聚氨酯的树脂膜、和基于丙烯酸的树脂膜,但不限于此。此外,保护膜可为各向同性膜或者可为向其提供补偿功能例如延迟的各向异性膜,并且保护膜可构造成一层膜或者可通过将两层膜或更多附接来构造。此外,保护膜可为未拉伸膜或者单轴或双轴拉伸膜,并且保护膜的厚度通常可为1μm至500μm,并且优选1μm至300μm。在这种情况下,保护膜对基于聚乙烯醇的偏振器的粘合力可优选地为1N/2cm或更大,并且更优选地为2N/2cm或更大。特别地,粘合力意指在将保护膜附接在经碘和二色性染料中至少一者染色的基于聚乙烯醇的偏振器上之后,通过使用质构分析仪通过90°剥离力测量的粘合力。如果粘合力满足上述范围,则可抑制保护膜和基于聚乙烯醇的偏振器的溶胀,并且在制造过程中,卷曲和缺陷的出现可最小化。同时,进行将保护膜层合于基于聚乙烯醇的偏振器的一个表面上的步骤以将保护膜附接在偏振器上,并且可使用粘合剂附接保护膜。在这种情况下,附接可通过本领域已知的膜的层合法进行,并且例如,附接可使用本领域已知的粘合剂进行,例如水基粘合剂,如基于聚乙烯醇的粘合剂;热固性粘合剂,如基于聚氨酯的粘合剂;可光阳离子固化的粘合剂,如基于环氧化合物的粘合剂;和可光自由基固化的粘合剂,如基于丙烯酸化合物的粘合剂。然后,可进行在提供有保护膜的偏振器的另一个表面上提供包含至少一个穿孔部分的掩模层的步骤。根据本说明书的一个示例性实施方案,所述方法还可包括在形成消偏振区域的步骤之前,在偏振器的另一个表面上形成包含至少一个穿孔部分的掩模层的步骤。在这种情况下,掩模层可由掩模膜或涂层形成。如果在形成消偏振区域的步骤之前进行形成掩模层的步骤,则优点在于辊对辊加工中的缺陷率可降低,原因是不需消偏振的部分,即,不需漂白的部分被掩模层覆盖,并且由于基于聚乙烯醇的偏振器和掩模层是层合的,因此加工速率没有限制。根据本说明书的一个示例性实施方案,可在提供保护膜的步骤之前进行形成掩模层的步骤。如果将其上形成有包含穿孔部分的掩模层的偏振器浸没在漂白液中,则漂白液通过穿孔部分与基于聚乙烯醇的偏振器接触,并因此,仅在对应于穿孔部分区域的部分中发生部分漂白。根据另一个示例性实施方案,如果使用掩模膜作为掩模层,则形成掩模层的步骤可包括:在掩模膜中形成穿孔部分;以及将所述掩模膜附接在偏振器的另一个表面上。在这种情况下,掩模膜可为基于烯烃的膜,例如聚乙烯(PE)、聚丙烯(PP)、和聚对苯二甲酸乙二醇酯(PET);或者基于乙酸乙烯酯的膜,例如乙烯-乙酸乙烯酯(EVA)和聚乙酸乙烯酯,但不限于此。此外,掩模膜的厚度可为约10μm至约100μm,并且优选约10μm至约70μm,但不限于此。在掩模膜中形成穿孔部分的步骤没有特别限制,并且可通过本领域熟知的膜穿孔法进行,例如,模具加工、刀具加工、激光加工等。根据本说明书的一个示例性实施方案,形成穿孔部分的步骤可通过激光加工来进行。激光加工可使用本领域公知的激光加工装置进行,但没有特别限制。激光加工条件例如激光装置的种类、功率和激光脉冲重复率可根据膜的材料或厚度、穿孔部分的形状等改变,并且本领域普通技术人员可考虑到上述因素而适当选择激光加工条件。例如,在使用厚度为30μm至100μm的聚烯烃膜作为掩模膜的情况下,可使用中心波长为约9μm至约11μm的二氧化碳(CO2)激光装置、中心波长为约300nm至约400nm的UV装置等形成穿孔部分。在这种情况下,激光装置的最大平均功率可为约0.1W至约30W,并且其脉冲重复率可为约0kHz至约50kHz,但激光装置不限于此。可在将掩模膜附接在偏振器的另一个表面上的步骤之前或之后进行形成穿孔部分的步骤。换言之,可在掩模膜中预先形成穿孔部分,然后可将形成有穿孔部分的掩模膜附接在偏振器上;或者可将掩模膜附接在偏振器上,然后可形成穿孔部分。将掩模膜附接在偏振器的另一个表面上的步骤可通过本领域熟知的膜层合法,例如用于通过粘合层附接掩模膜和偏振元件的方法进行。在这种情况下,粘合层可通过将粘合剂(例如,基于丙烯酸化合物的粘合剂、基于硅酮的粘合剂、基于环氧化合物的粘合剂、和基于橡胶的粘合剂)施用于掩模膜或偏振元件上来形成,但本发明不限于此。例如,在使用具有自粘合力的膜(例如,EVA膜、PVAC膜、PP膜等)作为掩模膜的情况下,可不形成粘合层将掩模膜直接附接在偏振器的另一个表面上。根据本说明书的一个示例性实施方案,如果掩模层由涂层形成,则形成掩模层的步骤包括:在偏振器的另一个表面上形成涂层;以及通过选择性移除涂层的部分区域而形成穿孔部分。形成涂层的步骤可如下进行:在偏振器的另一个表面上施用并干燥用于形成涂层的组合物,或者照射热或活性能量束例如UV束或电子束以使涂层固化。用于形成涂层的组合物的种类没有特别限制,只要组合物可被激光蚀刻并且不溶于碱溶液即可。例如,作为用于形成涂层的组合物,可使用包含可分散性聚合物树脂,例如水分散性聚氨酯、水分散性聚酯、和水分散性丙烯酸共聚物的组合物,或者光敏性树脂组合物。同时,作为光敏性树脂组合物,可不受特别限制地使用可在市场上购得的光敏性树脂组合物,例如,正型光刻胶、负型光刻胶等。根据本说明书的一个示例性实施方案,涂层可使用聚合物树脂组合物或光敏性树脂组合物来形成。用于涂敷用于形成涂层的组合物的方法没有特别限制,并且涂敷可通过本领域常用的涂敷方法进行,例如,棒涂、旋涂、辊涂、刮涂、喷涂等,并且固化可通过以下方法进行:在所涂敷的树脂组合物上施加热或者照射活性能量束,例如UV束或电子束。根据本说明书的一个示例性实施方案,涂层的厚度可为100nm至500nm。如果涂层的厚度满足上述数值范围,则存在这样的优点:当形成穿孔部分时,可以抑制对基于聚乙烯醇的偏振器的损坏,并且不必在漂白过程之后额外进行移除涂层的过程。通过选择性移除涂层的部分区域形成穿孔部分的步骤可通过以下方法进行:将能量束照射在涂层的部分区域上,接着进行蒸发、光刻法等。用于使涂层的一部分蒸发的方法可使用本领域公知的装置进行,例如,中心波长为约300nm至约400nm的UV激光装置、中心波长为约1,000nm至约1,100nm的IR激光装置、中心波长为约500nm至约550nm的绿色激光装置等。同时,激光加工条件例如激光装置的种类、激光器功率和脉冲重复率可根据涂层的种类和厚度、待形成的穿孔部分的形成等改变,并且本领域普通技术人员可考虑到上述因素而适当选择激光加工条件。根据本说明书的一个示例性实施方案,通过选择性移除涂层的部分区域而形成穿孔部分的步骤可通过激光加工来进行。同时,如果涂层由光敏性树脂组合物形成,则穿孔部分可通过光刻法形成。例如,穿孔部分可通过如下方法形成:将光敏性树脂组合物涂敷在偏振片的另一个表面上,并且将能量束选择性暴露于对应于穿孔部分的区域,然后用显影液使所述区域显影。在这种情况下,曝光可使用光源(例如,UV束)或能量束(例如,激光)进行。如果曝光使用激光进行,则存在这样的优点:可不使用单独的掩模用于曝光,并且穿孔部分的形状可相对自由地形成。更特别地,在本说明书的一个示例性实施方案中,如果涂层由光敏性树脂组合物形成至200nm的厚度,则曝光可使用最大平均功率为约0.1W至约10W的芯和300nm至400nm的UV激光器进行。在这种情况下,激光的动作脉冲重复率可为约30kHz至约100kHz。同时,在显影中,可根据本文中所使用的光敏性树脂的种类选择合适的显影液来使用。在一些情况下,可使用上述漂白液作为显影液。在这种情况下,可以不进行单独的显影步骤。同时,穿孔部分可形成为对应于待漂白区域的形状,并且其形状或形成位置没有特别限制。例如,穿孔部分可在安装构件(例如,摄像机)的位置形成,以便对应所述构件的形状,或者可在印刷产品标识的区域中以产品标识的形状形成。如果对偏振器的边缘部分提供颜色,则穿孔部分可在偏振器的边缘部分形成以具有框架形状。根据本说明书的一个示例性实施方案,所述方法还可包括在形成消偏振区域的步骤之前,在面对偏振器的保护膜的反面上提供离型膜的步骤。如果在进一步提供离型膜之后进行漂白过程,则可以使由偏振器溶胀时发生的MD收缩所引起的下陷现象最小化。根据本说明书的一个示例性实施方案,离型膜的力可为6,000N或更大。所述力意指通过以下方程式1获得的值。[方程式1]力(N)=模量(N/mm2)×膜的厚度(mm)×膜的宽度(mm)在本说明书中,模量(杨氏模量)是指如下获得的值:将根据JIS-K6251-1标准制备的样品的两端固定,然后在垂直于膜的厚度方向的方向上施加力,以根据应变测量每单位面积的应力。在这种情况下,作为测量装置,可使用例如拉伸强度测试仪(Zwick/RoellZ010UTM)等。离型膜的力可通过改变离型膜的厚度来调节。所述力随离型膜的厚度而变化的程度可根据离型膜的材料而变化。然而,用于调节离型膜的力的方法不限于此。然后,进行如上所述通过使包含1重量%至30重量%漂白剂的漂白液与其上提供有保护膜的偏振器的另一个表面局部接触,形成在400nm至800nm的波长段内单透射率为80%或更高的消偏振区域的步骤。在这种情况下,漂白液的表面张力为50mN/m或更小。为了降低漂白液的表面张力,并且更具体地,为了将表面张力降低至50mN/m或更小,可使用添加相对于漂白液的总重量1重量%至50重量%的量的醇类溶剂(例如甲醇、乙醇和异丙醇)的方法,和/或添加少量表面活性剂的方法。表面活性剂的种类没有特别限制。即,表面活性剂可为阳离子类表面活性剂、阴离子类表面活性剂、两性表面活性剂、或非离子表面活性剂。根据本说明书的一个示例性实施方案,漂白液还可包含表面活性剂。特别地,相对于漂白液的总重量,可添加0.01重量%至0.5重量%的量的表面活性剂。在这种情况下,如上所述,偏振器的另一个表面是指未提供保护膜和/或离型膜的反面。即,由于漂白液需要与基于聚乙烯醇的偏振器而不是保护膜和/或离型膜直接接触,因此该步骤应在偏振器的另一个表面上进行。提供掩模层然后进行漂白过程(形成消偏振区域的过程)的方法具有非常容易进行连续工艺的优点,但存在的问题是:漂白液由于掩模层的端部而不能完全充满穿孔部分,并且微气泡在边界处产生,这引起未漂白位点的产生。未漂白位点的产生意指经漂白位点形成为不期望的形状。掩模层的端部是指对应于掩模层厚度的高度。参见图2,引起产生未漂白位点的微气泡的形成原因是空气通过掩模层边界处的端部渗透。这是由于,因漂白液的高表面张力,掩模层与漂白液之间的接触角高。因此,根据本说明书的一个示例性实施方案的用于制造偏振片的方法使用具有低表面张力的漂白液抑制未漂白位点的产生。根据本说明书的一个示例性实施方案,漂白液的表面张力可为30mN/m或更小。在这种情况下,上述抑制未漂白位点的作用可最大化。即,缺陷率可最小化。图3是示出由微气泡引起的未漂白位点的图。可以看出,不能实现完全漂白,而是产生呈小滴形式的未漂白位点。根据本说明书的一个示例性实施方案,漂白液与偏振器之间的接触角可为30度或更小。如果接触角为30度或更小,则空气的渗透可最小化,因而可以抑制由微气泡引起的未漂白位点的产生。根据本说明书的一个示例性实施方案,漂白液与偏振器之间的接触角可为20度或更小,并且更优选地10度或更小。在这种情况下,上述使空气渗透最小化并因此抑制未漂白位点产生的作用可最大化。根据本说明书的一个示例性实施方案,相对于整个偏振片,消偏振区域可以以0.005%至40%的比例形成。同时,漂白液基本上包括可漂白碘和/或二色性染料的漂白剂和溶剂。漂白剂没有特别限制,只要漂白剂可漂白染在偏振器上的碘和/或二色性染料即可。根据本说明书的一个示例性实施方案,漂白剂可包括选自以下的一种或更多种漂白剂:氢氧化钠(NaOH)、硫氢化钠(NaSH)、叠氮化钠(NaN3)、氢氧化钾(KOH)、硫氢化钾(KSH)、和硫代硫酸钾(KS2O3)。作为溶剂,可优选地使用水,例如蒸馏水。此外,溶剂可另外与醇类溶剂混合使用。溶剂可与例如但不限于甲醇、乙醇、丁醇、异丙醇等混合使用。如上所述,相对于漂白液的总重量,可添加1重量%至50重量%的量的醇类溶剂以降低漂白液的表面张力。更具体地,漂白液的表面张力可降低至50mN/m或更小。在上述范围内,随着醇类溶剂的含量增加,漂白液的表面张力减小。同时,漂白液中漂白剂的含量可根据漂白过程中的接触时间改变,但相对于漂白液的总重量,漂白剂可以以优选地约1重量%至约30重量%,并且更优选地约5重量%至约15重量%的量包含在内。如果漂白剂的含量小于1重量%,则漂白可能无法进行,或者漂白可能花费几十分钟或更久,并因此难以实际应用漂白剂。如果漂白剂的含量大于30重量%,则漂白液不易扩散进偏振器,因而漂白效率的增加不明显,并因此经济可行性降低。此外,根据本说明书的一个示例性实施方案,漂白液的pH可为11至14。优选地,pH可为13至14。漂白剂为强碱性化合物,并应具有足以破坏与聚乙烯醇形成交联键的硼酸的强碱性。如果pH满足上述范围,则漂白可充分进行。例如,硫代硫酸钠(pH7)作为分解(漂白)碘以确保透明性(碘钟反应)的溶液可引起一般碘化合物水溶液的漂白,但即使进行长时间段(10小时)的接触也不会引起实际偏振器(PVA)的漂白。即,这意味着需要在碘被分解之前通过强碱破坏硼酸的交联键。根据本说明书的一个示例性实施方案,漂白液的粘度可为1cP至2,000cP。更特别地,根据本说明书的一个示例性实施方案,漂白液的粘度可为5cP至2,000cP。这是因为,如果漂白液的粘度满足上述数值范围,则印刷过程可容易地进行,并且可抑制印刷漂白液根据连续加工线中偏振元件的移动而扩散或向下流,并因此漂白区域可在期望区域内形成为期望形状。同时,漂白液的粘度可根据本文中所使用的印刷装置和偏振器的表面性质来适当改变。例如,在使用凹版印刷法的情况下,漂白液的粘度可为约1cP至约2,000cP,并且优选约5cP至约200cP;而在使用喷墨印刷法的情况下,漂白液的粘度可为约1cP至约55cP,并且优选约5cP至约20cP。同时,优选地,形成消偏振区域的步骤可在10℃至70℃的漂白液中进行1秒至60秒。如果漂白液的温度和浸没时间在上述数值范围外,则可能存在这样的问题:由漂白液引起偏振器的溶胀和脱水收缩,因而发生偏振器的弯曲,或者即使在不期望区域内也发生漂白。根据本说明书的一个示例性实施方案,漂白液还可包含粘度剂。为了使漂白液的粘度满足上述范围,优选使用进一步添加粘度剂的方法。因此,粘度剂提高漂白液的粘度以帮助抑制溶液的扩散,以及在期望位置形成具有期望尺寸的消偏振区域。如果将具有高粘度的溶液施用于快速移动的偏振器上,则由于液体与偏振器之间的相对速度差(在施用期间产生)减小,因此溶液向不期望部分的扩散被抑制,并且溶液(在进行漂白时直至施用后进行洗涤的时间段内施加)的流动减慢,因此可形成具有期望位置或尺寸的消偏振区域。粘度剂没有特别限制,只要粘度剂具有低反应性并且可增加溶液的粘度即可。根据本说明书的一个示例性实施方案,粘度剂包括选自以下的一种或更多种粘度剂:基于聚乙烯醇的树脂、基于聚乙酰乙酸乙烯酯的树脂、经乙酰乙酰基改性的基于聚乙烯醇的树脂、基于丁烯二醇乙烯醇的树脂、基于聚乙二醇的树脂、和基于聚丙烯酰胺的树脂。根据另一个示例性实施方案,相对于漂白液的总重量,粘度剂可以以0.5重量%至30重量%的含量包含在内。特别地,根据本说明书的一个示例性实施方案,相对于漂白液的总重量,粘度剂可以以2.5重量%至15重量%的含量包含在内。如果粘度剂的含量大于上述范围,则粘度过度增加,并因此,洗涤无法有效地进行。如果粘度剂的含量过低,则粘度低,并因此,难以通过液体的扩散和流动实现具有期望形状和期望尺寸的漂白区域。根据本说明书的一个示例性实施方案,漂白液可包含:相对于总重量,1重量%至30重量%的漂白剂;0.5重量%至30重量%的粘度剂;和40重量%至70重量%的水。此外,消偏振区域可具有各种形状但不限于此,并且消偏振区域可在整个偏振片的任何位置形成。然而,例如,如果消偏振区域在摄像机模块上形成,则消偏振区域的尺寸可优选地为约0.01cm2至约5cm2。同时,以下将具体描述通过本说明书的消偏振步骤的消偏振机理。已知经碘和/或二色性染料染色的聚乙烯醇络合物可吸收可见光范围内,例如400nm至800nm的波长段的光。在这种情况下,如果使漂白液与偏振器接触,则吸收具有可见光波长段的光并存在于偏振器中的碘和/或二色性染料被分解以漂白偏振器,并因而增加透射率并降低偏振程度。例如,消偏振区域在400nm至800nm的波长段内单透射率可为80%或更高,并且偏振程度可为20%或更小。在本说明书中,术语“单透射率”由偏振片的吸收轴透射率和透射轴透射率的平均值表示。此外,本说明书的术语“单透射率”和术语“偏振程度”是使用由JASCO公司制造的V-7100型测量的值。例如,如果使包含氢氧化钾(KOH)(漂白剂)的水溶液与经碘染色的基于聚乙烯醇的偏振器的部分区域接触,则碘通过由以下化学式1和2表示的一系列过程分解。同时,如果在制造经碘染色的基于聚乙烯醇的偏振器时进行硼酸交联过程,则氢氧化钾直接分解硼酸以消除由聚乙烯醇与硼酸的氢键所引起的交联作用,如以下化学式3中所述。[化学式1]12KOH+6I2→2KIO3+10KI+6H2O[化学式2]I5-+IO3-+6H+→3I2+3H2OI3-→I-+I2[化学式3]B(OH)3+3KOH→K3BO3+3H2O即,偏振器吸收可见光区域内的光以分解碘和/或碘离子络合物,例如I5-(620nm)、I3-(340nm)和I2-(460nm),并因而产生I-(300nm或更小)或其盐,从而透射可见光区域内的大部分光。因此,由于偏振器在约400nm至800nm的区域(可见光区域)内消偏振,因此透射率整体增加而使偏振器透明。换言之,为了在偏振器中进行偏振,可将排列的吸收可见光的碘络合物分解为不吸收可见光的单体,从而进行消偏振。根据本说明书的一个示例性实施方案,如有必要,则所述方法还可包括在形成消偏振区域的步骤之后移除掩模层的步骤。移除掩模层的步骤可通过从偏振器剥离掩模层的方法来进行。如果使用掩模膜作为掩模层,则优选进行该步骤,但如果使用涂层作为掩模层,则该步骤可不进行。更具体地,移除掩模层的步骤可通过使用剥离辊等从偏振器剥离掩模层的方法来进行。根据本说明书的一个示例性实施方案,如有必要,则所述方法还可包括在形成消偏振区域的步骤之后使偏振器交联的步骤(未举例说明)。在通过与漂白液接触而形成消偏振区域的步骤中,漂白区域可因漂白液而溶胀,因而偏振器可变形。因此,进行交联步骤以恢复变形的偏振器,并且交联步骤可通过将偏振器浸没在交联溶液中的方法来进行。本文中,交联溶液可包含选自以下的一种或更多种交联剂:硼化合物,例如硼酸和硼砂;以及酸,例如琥珀酸、戊二酸和柠檬酸。交联剂的含量可根据交联剂的种类变化,并且可为例如约0.001重量%至约20重量%,优选地约0.003重量%至约15重量%,并且更优选地约0.005重量%至约10重量%。如果使用硼化合物作为交联剂,则交联剂的含量可为约0.001重量%至约5重量%;而如果使用酸作为交联剂,则交联剂的含量可为约0.001重量%至约1重量%。如果交联剂的含量满足上述数值范围,则可实现偏振片的优异工艺产率和外观品质、光学特性和/或耐久性。同时,可使用水(纯水)作为交联溶液的溶剂。根据本说明书的一个示例性实施方案,为了调整偏振片的特性和颜色,交联溶液还可包含碘化物,例如碘化钾、碘化锂、碘化钠、碘化锌、碘化铝、碘化铅、碘化铜、碘化钡、碘化钙、碘化锡、碘化钛或其混合物。在这种情况下,碘化物的含量可优选地为约3重量%至约5重量%。如果碘化物的含量在上述数值范围外,则可不利地影响偏振器的耐久性或颜色特性。同时,在交联过程期间交联溶液的温度可为例如,但不限于约10℃至约70℃,优选地约15℃至约65℃,并且更优选地约20℃至约60℃。如果交联溶液的温度满足上述数值范围,则可有效地矫正由漂白过程所引起的偏振元件的变形。如果交联溶液的温度在上述数值范围外,则偏振元件的光学特性或外观品质可能劣化,并且在严重情况下,偏振元件的变形可能更严重。此外,进行交联过程的时间可为例如,但不限于约1秒至约120秒,优选地约1秒至约90秒,并且更优选地约1秒至约60秒。如果交联时间满足上述数值范围,则可有效地矫正由漂白所引起的偏振元件的变形。如果交联时间在上述数值范围外,则偏振元件的光学特性或品质可能劣化,并且在严重情况下,偏振元件的变形可能更严重。如上所述,如果将偏振元件浸没在包含交联剂的交联溶液中,则PVA膜中的聚乙烯醇链通过包含在交联溶液中的硼化合物或酸彼此结合,因此可实现矫正偏振元件的变形的效果。根据本发明的发明人的研究,如果交联过程在形成消偏振区域的步骤之后进行,则与不进行交联过程的情况相比,漂白区域的尺寸变形率降低至10%至70%,并且通常为约20%至约60%。根据本说明书的一个示例性实施方案,所述方法还可包括在形成消偏振区域的步骤之后清洁并干燥偏振器的步骤。更具体地,如果包括交联步骤,则清洁和干燥步骤可在交联步骤之后另外进行。进行清洁和干燥步骤以洗涤残留在偏振器上的交联溶液,以及进一步矫正由漂白液所引起的偏振元件的外观变形,并且清洁和干燥步骤可通过本领域已知的清洁和干燥偏振器的方法来进行。根据本说明书的一个示例性实施方案,清洁和干燥步骤可通过使偏振器通过清洁辊和加热辊来进行。在这种情况下,加热辊的直径可为约100Φ至约500Φ,并且优选地约150Φ至约300Φ。加热辊的温度可为约30℃至约150℃,并且优选约60℃至约150℃。根据本发明的发明人的研究,矫正偏振元件的外观变形的效果根据清洁和干燥步骤中加热辊的直径和温度而变化,并且如果加热辊的直径和温度满足上述数值范围,则可最有效地矫正偏振元件的外观变形。根据本说明书的一个示例性实施方案,为了进一步改善偏振器的表面粗糙度,所述方法还可包括在交联步骤之后在偏振器的一个表面上形成平整化层的步骤。优选地,平整化层可在与漂白液接触的表面(即,其上形成掩模层的表面)上形成,并且厚度可为约1μm至约10μm,并且更优选地约2μm至约5μm。根据本说明书的一个示例性实施方案,所述方法还可包括在形成消偏振区域的步骤之后,在偏振器的至少一个表面上形成光学层的步骤。在这种情况下,光学层可为聚合物膜层,例如保护膜或延迟膜;功能膜层,例如增亮膜;或者功能层,例如硬涂层、抗反射层和粘合层。更具体地,根据本说明书的一个示例性实施方案,在偏振器的另一个表面上形成光学层。换言之,在其上未提供保护膜和/或离型膜的偏振器表面上形成光学层。如果包括交联步骤,则形成光学层的步骤可优选地在交联步骤之后进行。同时,光学层可直接附接至或形成于基于聚乙烯醇的偏振器表面上,或者可附接在保护膜或其他涂层上,所述保护膜或其他涂层附接于基于聚乙烯醇的偏振器的一个表面上。光学层可根据待形成的光学层的种类通过不同方法形成,并且例如,光学层可使用本领域中熟知的用于形成光学层的方法来形成,并且其方法没有特别限制。根据本说明书的一个示例性实施方案,所述方法还可包括在形成消偏振区域的步骤之后移除离型膜的步骤。移除离型膜的步骤可通过从保护膜剥离离型膜的方法来进行。更具体地,移除离型膜的步骤可通过使用剥离辊等从保护膜剥离离型膜的方法来进行。由于离型膜用于在形成消偏振区域的步骤中抑制下陷(在保护膜方向上的延伸)的发生,因此优选在形成消偏振区域后移除离型膜。本说明书的另一个示例性实施方案提供了通过根据上述示例性实施方案的用于制造偏振片的方法制造的偏振片。在偏振片中,消偏振区域的算术平均粗糙度Ra可为200nm或更小。在偏振片中,消偏振区域的均方根粗糙度Rq可为200nm或更小。算术平均粗糙度Ra是JISB0601-1994中规定的值,并且表示通过以下步骤获得的值:从粗糙度曲线沿其平均线方向采样参考长度,并且累计采样部分从平均线到测量曲线的偏差绝对值,接着进行平均;而均方根粗糙度Rq是JISB0601-2001中规定的。算术平均粗糙度Ra和均方根粗糙度Rq使用光学轮廓仪(NanoviewE1000,NanoSystemInc.)来测量。通常,如果偏振器表面的粗糙度增加,则雾度通过光的折射和反射而增加。如果消偏振区域的粗糙度满足上述范围,则雾度足够低并可确保鲜明的可视性。此外,偏振片的偏振程度可为10%或更低。在偏振片中,消偏振区域的雾度可为3%或更低。偏振片的下陷深度可为10μm或更小。在本说明书中,下陷意指当基于聚乙烯醇(PVA)的偏振器与漂白液接触时发生的在保护膜方向上的下陷现象。浅深度下陷意指低程度的下陷现象,并且浅深度下陷可使偏振片的外观变形最小化,并因此,存在这样的优点:当将保护膜等层合在另一个表面上时可均匀地施加粘合剂。因此,当制造具有保护膜存在于偏振器两个表面上的结构的偏振片时,可减少缺陷的出现。此外,浅深度下陷的优点在于可提供具有改善的外观的偏振片。下陷的深度可使用白光三维测量仪(光学轮廓仪)或激光显微镜(CLSM,共聚焦激光扫描显微镜)来测量。消偏振区域在400nm至800nm并且更优选450nm至750nm的波长带(可见光区域)中的单透射率可为80%或更高,优选地90%或更高,并且更优选地92%或更高。此外,消偏振区域的偏振程度可为10%或更低,更优选地5%或更低。当消偏振区域具有较高的单透射率和较低的偏振程度时,可视性提高,因而位于消偏振区域中的摄像机镜头的性能和图像品质可进一步提高。根据本说明书的一个示例性实施方案,偏振片除消偏振区域以外的其他区域的单透射率可优选地为40%至47%,并且更优选地42%至47%。此外,偏振片除消偏振区域以外的其他区域的偏振程度可优选地为99%或更高。这是因为,偏振片除消偏振区域以外的其他区域需要通过发挥偏振片的作用而表现出上述范围内的优异光学特性。在根据本说明书的一个示例性实施方案的偏振片中,消偏振区域与偏振区域之间边界的宽度可为5μm或更大至200μm或更小,或者5μm或更大至100μm或更小,或者5μm或更大至50μm或更小。消偏振区域与偏振区域之间的边界可指位于消偏振区域与偏振区域之间的偏振器区域。消偏振区域与偏振区域之间的边界可指与消偏振区域和偏振区域中的每一个接触的区域。此外,消偏振区域与偏振区域之间的边界可指具有介于消偏振区域的单透射率与偏振区域的单透射率之间的值的区域。消偏振区域与偏振区域之间的边界的宽度可指从具有消偏振区域的单透射率的值的区域到具有偏振区域的单透射率的值的区域的最短距离。消偏振区域与偏振区域之间的边界的较小宽度可意味着消偏振区域有效地形成于期望的局部位点。在本说明书中,偏振区域可指偏振器除消偏振区域以外的区域。本说明书的一个示例性实施方案还可提供图像显示装置,其包括:显示面板;和附接于所述显示面板的一个表面或两个表面的根据上述示例性实施方案的偏振片。显示面板可为液晶面板、等离子面板和有机发光面板。因此,图像显示装置可为液晶显示器(LCD)、等离子显示面板(PDP)、和有机发光二极管(OLED)。更具体地,图像显示装置可为液晶显示器,其包括:液晶面板;和分别提供在液晶面板两侧的偏振片。在这种情况下,偏振片中至少一者可为根据本说明书一个示例性实施方案的包含偏振器的偏振片。本文中,包含在液晶显示器中的液晶面板的种类没有特别限制。液晶面板的实例可包括,但不限于所有已知面板,包括:无源矩阵面板,例如扭曲向列(TN)面板、超扭曲向列(STN)面板、铁电(F)面板或聚合物分散(PD)面板;有源矩阵面板,例如两终端型面板或三终端型面板;面内转换(IPS)面板;和垂直排列(VA)面板等。此外,液晶显示器其他构件例如上基板和下基板(如,滤色器基板或阵列基板)的种类没有特别限制,并且可使用本领域中已知的那些而没有限制。根据本说明书的一个示例性实施方案,图像显示装置还可包括提供在偏振片的消偏振区域内的摄像机模块。通过将摄像机模块置于消偏振区域(其中可见光区域的透射率提高并且偏振程度降低)内,可确保提高摄像机镜头部分的可视性的效果。此外,如果形成消偏振区域的步骤在提供离型膜之后进行,则可通过包括抑制消偏振区域的下陷现象的偏振片来确保外观改善效果。本说明书的一个示例性实施方案还提供了表面张力为50mN/m或更小的漂白液。特别地,漂白液可用于制造偏振片时形成偏振器的消偏振区域的步骤中。根据本说明书的一个示例性实施方案,相对于漂白液的总重量,漂白液可包含1重量%至50重量%的量的醇类溶剂。根据本说明书的一个示例性实施方案,相对于漂白液的总重量,漂白液可包含0.01重量%至0.5重量%的量的表面活性剂。如果醇类溶剂和/或表面活性剂的含量在上述范围内,则可获得表面张力为50mN/m或更小的漂白液。醇类溶剂和表面活性剂的详情与上述相同。实施例下文中,将参照实施例更详细地描述本说明书。然而,提出以下实施例以举例说明本说明书,但本说明书的范围不限于此。<制备例>使基于聚乙烯醇的膜(NipponGohseiCo.,Ltd.M3000级30μm)在25℃的纯溶液中经历溶胀过程15秒,然后在25℃下在浓度为0.2重量%的碘溶液中经历染色过程60秒。其后,使基于聚乙烯醇的膜在45℃下在包含1重量%硼酸的溶液中经历清洁过程30秒,然后在52℃下在包含2.5重量%硼酸的溶液中拉伸6倍。在拉伸后,使基于聚乙烯醇的膜在包含5重量%碘化钾(KI)的溶液中经历补色过程,然后在烘箱中于60℃下干燥5秒,由此制造厚度为12μm的基于聚乙烯醇的偏振器。然后,将基于丙烯酸化合物的保护膜层合在基于聚乙烯醇的偏振器的一个表面上,并将包含直径为约4mm的孔的掩模膜层合在偏振器的另一个表面上。然后,使用粘合剂将聚对苯二甲酸乙二醇酯(PET)层合在基于丙烯酸化合物的保护膜的另一个表面(面对偏振器的保护膜的反面)上。<实施例1>将一个表面上层合有包含孔的掩模膜并且另一个表面上层合有保护膜和聚对苯二甲酸乙二醇酯(PET)的偏振器在添加有0.2重量%表面活性剂(BYK-348,BYKChemie)的60KOH10重量%水溶液中浸没并漂白3秒,然后在硼酸4重量%水溶液中浸没并中和5秒,并且在烘箱中于60℃下干燥30秒。然后,移除掩模膜并层合基于丙烯酸化合物的保护膜。然后,移除聚对苯二甲酸乙二醇酯(PET)膜,从而制造出具有包含基于丙烯酸化合物的保护膜/基于聚乙烯醇的偏振器/基于丙烯酸化合物的保护膜的结构的偏振片。<实施例2>在与实施例1相同的条件下制造偏振片,不同之处在于:使用添加有0.1重量%表面活性剂(BYK-348,BYKChemie)的漂白液。<实施例3>在与实施例1相同的条件下制造偏振片,不同之处在于:使用添加有20重量%异丙醇的漂白液。<实施例4>在与实施例1相同的条件下制造偏振片,不同之处在于:使用添加有10重量%异丙醇的漂白液。<实施例5>在与实施例1相同的条件下制造偏振片,不同之处在于:使用添加有5重量%异丙醇的漂白液。<比较例1>在与实施例1相同的条件下制造偏振片,不同之处在于:使用添加有2重量%异丙醇的漂白液。<比较例2>在与实施例1相同的条件下制造偏振片,不同之处在于:使用添加有1重量%异丙醇的漂白液。<比较例3>在与实施例1相同的条件下制造偏振片,不同之处在于:使用不含添加剂的漂白液。对根据实施例1至5和比较例1至3制造的偏振片中的未漂白位点产生率(即,缺陷率)进行比较,其结果在表1中示出。[表1]漂白液的表面张力(mN/m)漂白液与偏振器的接触角(°)缺陷率(%)实施例120<100实施例220.3<100实施例328.2<100实施例436.8153实施例544.9305比较例154.24215比较例256.74520比较例3705540如表1中所列,可以看出,与使用具有高表面张力的漂白液形成消偏振区域的偏振片相比,通过根据本说明书的示例性实施方案的制造方法制造的偏振片,即,使用具有低表面张力的漂白液和/或与偏振器具有小接触角的漂白液形成消偏振区域的偏振片的未漂白位点产生率(缺陷率)显著降低。更具体地,参见图4,如果漂白液的表面张力为30mN/m或更小,则漂白液与偏振器之间的接触角减小。因此,微气泡产生的可能性降低。因此,如实施例1至5中所示,未漂白位点产生率(缺陷率)降低。当前第1页1 2 3