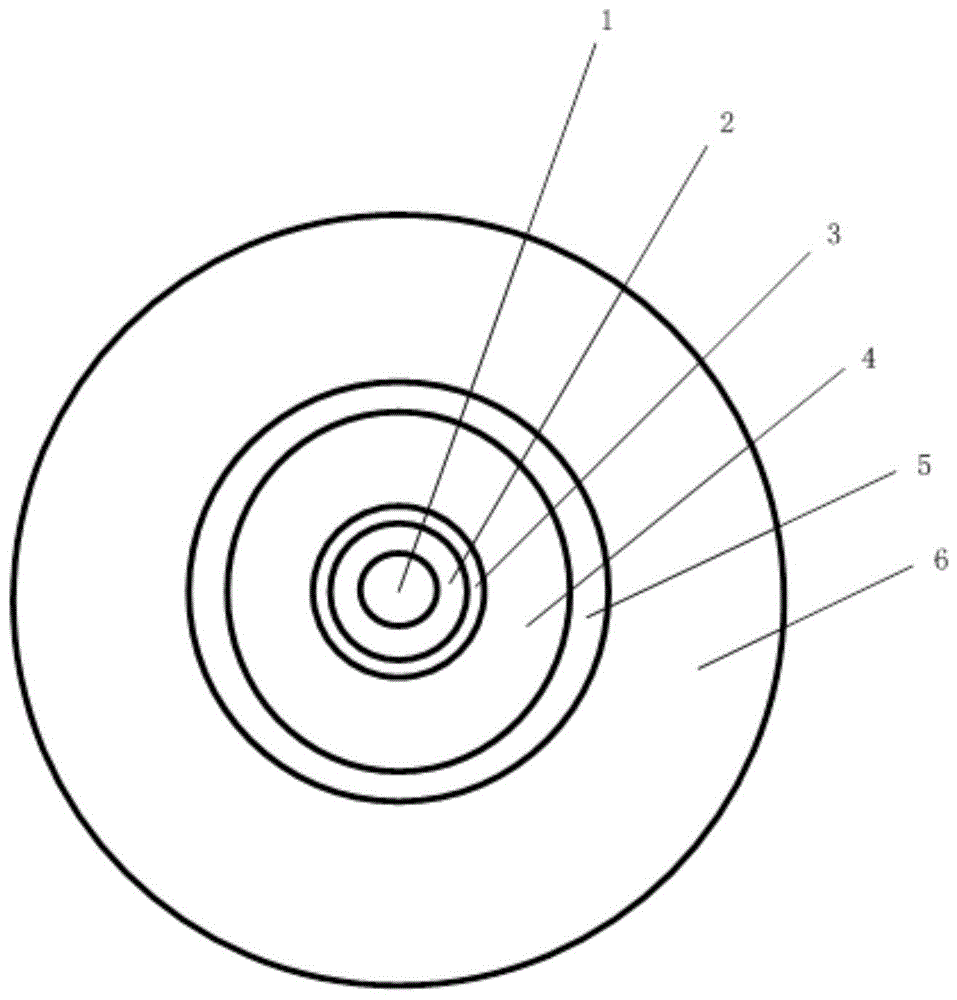
本实用新型涉及光通信
技术领域:
,尤其涉及一种光纤。
背景技术:
:本部分旨在为权利要求书中陈述的本实用新型的实施方式提供背景或上下文。此处的描述不因为包括在本部分中就承认是现有技术。G.657光纤由于其具有较为优异的耐弯曲特性,近年来被广泛应用,其主要结构包括由内向外设置的掺锗的单掺锗二氧化硅芯层、单掺氟二氧化硅光学包层及外包层。为了实现光纤本身弯曲损耗小的性能,主要是通过降低光纤的模场直径,增加凹陷包层的方式;而实现凹陷包层是通过在单掺氟二氧化硅光学包层内掺入折射率低的氟元素实现。由于氟元素的掺入,有一部分氟元素会与折射率高的锗元素混掺,在实现同样单掺锗二氧化硅芯层折射率的情况下会比普通G.652光纤多掺入10%~15%的锗元素。锗元素的增加掺入,会带来瑞利散射的增加,这种条件下生产出的光纤,1310nm波段的损耗一般会比G.652光纤高出0.010dB/km~0.015dB/km。因此需要一种光纤,来保证单掺锗二氧化硅芯层与单掺氟二氧化硅光学包层之间锗元素及氟元素之间的相互掺杂引起的光纤衰减增加的问题。技术实现要素:本实用新型的目的在于提供一种光纤,其具有保证低衰减的同时兼具有较低的弯曲损耗。本实用新型提供的技术方案为:一种光纤,内而外依次包括单掺锗二氧化硅芯层、隔断层、单掺氟二氧化硅光学包层及外包层,所述隔断层用于防止单掺锗二氧化硅芯层中锗和单掺氟二氧化硅光学包层中氟相互扩散;其中所述单掺氟二氧化硅光学包层分为三层,从内到外依次为浅掺氟层、主掺氟层及辅掺氟层,所述浅掺氟层及辅掺氟层的折射率均大于所述主掺氟层的折射率。优选的,所述隔断层、所述浅掺氟层、所述主掺氟层及所述辅掺氟层中相邻的每两层之间的折射率渐变变化,并控制每1μm内的折射率变化为0.03%~0.05%。优选的,所述单掺锗二氧化硅芯层的折射率为0.35%~0.45%,所述单掺锗二氧化硅芯层的厚度为4.0μm~4.5μm。优选的,所述隔断层的相对折射率为-0.01%~0.01%,其厚度为1.5μm~2μm。优选的,所述浅掺氟层的折射率为-0.04%~-0.07%,厚度为2.5μm~4.2μm。优选的,所述主掺氟层折射率为-0.08%~-0.15%,所述主掺氟层厚度为5μm~8.5μm。优选的,所述辅掺氟层的折射率为-0.01%~-0.07%,厚度为2.5~4.2μm。优选的,所述外包层为光纤的保护层,且所述外包层为纯SiO2层所述外包层的折射率为0~0.005%,其厚度为41.1μm~49.0μm。与现有技术相比,本实用新型提供的一种光纤包括由内而外依次包括单掺锗二氧化硅芯层、隔断层、单掺氟二氧化硅光学包层及外包层,所述隔断层用于防止单掺锗二氧化硅芯层中锗和单掺氟二氧化硅光学包层中氟相互扩散;其中所述单掺氟二氧化硅光学包层分为三层,从内到外依次为浅掺氟层、主掺氟层及辅掺氟层,所述浅掺氟层及辅掺氟层的折射率均大于所述主掺氟层的折射率。通过隔断层的设置减少了掺杂元素的迁移导致的折射率的抵消,且通过单掺氟二氧化硅光学包层的分层设置,使SiO2内掺氟的量在半径方向有一个浓度逐渐变化的过程,这种变化的过程可以使光纤截面粘度沿半径方向呈逐渐变化的趋势,这种结构可以在得到光纤低宏弯损耗的情况下降低光纤应力的产生,得到低损耗低弯曲损耗光纤。通过起过渡作用的浅掺氟层及辅掺氟层,减少了光纤预制棒制备及光纤拉丝过程中粘度不匹配带来的应力产生,方便了光纤本身的制备;且通过折射率相对较低的主掺氟层的设置,将主掺氟层作为下陷包层来对实现降低光纤的弯曲衰减;且本实用新型中,光纤折射率剖面结构,没有采用深掺氟的单掺氟二氧化硅光学包层结构,给光纤的制备工艺降低了难度,有利于采用VAD、OVD工艺大批量生产。附图说明下面结合附图和具体实施方式对本实用新型作进一步详细的说明。图1为本实用新型中一实施方式中光纤的剖面示意图。图2为本实用新型中所述的光纤折射率剖面示意图。图3为隔断层在疏松体状态下不同密度下采用VAD工艺制备的光纤衰减参数特性。附图标记说明:单掺锗二氧化硅1隔断层2浅掺氟层3主掺氟层4辅掺氟层5外包层6如下具体实施方式将结合上述附图进一步说明本实用新型实施例。具体实施方式为了能够更清楚地理解本实用新型实施例的上述目的、特征和优点,下面结合附图和具体实施方式对本实用新型进行详细描述。需要说明的是,在不冲突的情况下,本申请的实施方式中的特征可以相互组合。在下面的描述中阐述了很多具体细节以便于充分理解本实用新型实施例,所描述的实施方式仅是本实用新型一部分实施方式,而不是全部的实施方式。基于本实用新型中的实施方式,本领域普通技术人员在没有做出创造性劳动前提下所获得的所有其他实施方式,都属于本实用新型实施例保护的范围。本文中″瑞利散射″属于散射的一种情况,又称″分子散射″,是指散射粒子线度比波长小得多的粒子对光波的散射。除非另有定义,本文所使用的所有的技术和科学术语与属于本实用新型实施例的
技术领域:
的技术人员通常理解的含义相同。本文中在本实用新型的说明书中所使用的术语只是为了描述具体的实施方式的目的,不是旨在于限制本实用新型实施例。光纤,如图1所示,包括单掺锗二氧化硅芯层1、单掺氟二氧化硅光学包层及外包层6,在单掺锗二氧化硅芯层1与单掺氟二氧化硅光学包层之间设有防止锗和氟扩散的隔断层2。通过隔断层2的设置,使得在光纤预制棒制备和光纤拉丝过程中,可以减少单掺锗二氧化硅芯层1中的锗与单掺氟二氧化硅光学包层中的氟混掺,通过隔断层2阻隔单掺氟二氧化硅光学包层中的氟进入到单掺锗二氧化硅芯层1中,可以有效地降低了光纤中的瑞利散射,从而实现了光纤本身的低衰减;且同时,通过隔断层2的设置,对单掺氟二氧化硅光学包层中的氟进行阻隔,保证了单掺氟二氧化硅光学包层中氟的含量始终保持一定,避免氟含量的降低导致弯曲损耗增高的现象产生。在一些实施方式中,所述隔断层2、所述浅掺氟层3、所述主掺氟层4及所述辅掺氟层5中相邻的每两层之间的折射率渐变变化,并控制每1μm内的折射率变化为0.03%~0.05%。在一些实施方式中,单掺锗二氧化硅芯层1的折射率为0.35%~0.45%,单掺锗二氧化硅芯层1的半径为4.0μm~4.5μm。通过对单掺锗二氧化硅芯层1折射率及半径的限定,使得单掺锗二氧化硅芯层1与现有技术中相比能够有较为良好的折射率,保证了使用过程中,能够有较小的传输衰减。在一些实施方式中,为了实现隔断层2对单掺锗二氧化硅芯层1与单掺氟二氧化硅光学包层之间的分隔,隔断层2的相对折射率为-0.01%~0.01%,其厚度为1.5μm~2μm,且在一些实施方式中,隔断层的疏松体密度为0.32g/cm3~0.35g/cm3。本实用新型中,隔断层2发挥隔断的作用,一方面是通过隔断层的设置对其进行物理阻隔,另外一方面是通过控制该层在疏松体状态下的密度实现的。在一些实施方式中,如图1所示,单掺氟二氧化硅光学包层分为三层,所述单掺氟二氧化硅光学包层从内到外,依次为浅掺氟层3、主掺氟层4及辅掺氟层5;且浅掺氟层3及辅掺氟层5的折射率均大于主掺氟层4的折射率;这里,各层的折射率及厚度如下所示:主掺氟层4折射率为-0.08%~-0.15%,主掺氟层4厚度为5μm~8.5μm;浅掺氟层3的折射率为-0.04%~-0.07%,厚度为2.5μm~4.2μm;辅掺氟层5的折射率为-0.01%~-0.07%,厚度为2.5~4.2μm。通过采用层间跃变的方式,使得通过单掺氟二氧化硅光学包层内掺氟量的逐渐变化,使光纤截面的粘度沿半径方向呈逐渐变化的趋势,从而实现了光纤中长波长的衰减有明显的降低作用,采用这种结构的G.657光纤比没有这种结构的G.657光纤1550nm波段的衰减低0.008dB/km~0.013dB/km,一般衰减值可达到0.178dB/km以下;且本实施例中,通过限定主掺氟层4作为光纤截面方向折射率最低的部分,对单掺锗二氧化硅芯层1的光起到主要的束缚作用,而位于主掺氟层4内外两侧的浅掺氟层3及辅掺氟层5,主要起到辅助束缚的作用。在一些实施方式中,如图1所示,还包括位于最外侧的外包层6,使用过程中,外包层6作为光纤的机械保护层,所述外包层6为纯SiO2层,外包层6的折射率为0~0.005%,其厚度为41.1μm~49.0μm。这样,通过外包层6的设置对内部的单掺锗二氧化硅芯层1及单掺氟二氧化硅光学包层形成保护。实施例1-实施例10提供的一种低衰减低弯曲损耗光纤的结构与上述具体实施方式基本相同,其不同之处在于各层之间的折射率及比厚度的不同,其具体表现为:上述实施例中所提供的一种低衰减低弯曲损耗的光纤,可以采用VAD、OVD、MCVD和PCVD等工艺实现,且其具体效果表现如下:本实用新型所提供的光纤通过隔断层2的设置,使得在光纤预制棒制备和光纤拉丝过程中,可以减少单掺锗二氧化硅芯层1中的锗与单掺氟二氧化硅光学包层中的氟混掺,通过隔断层2阻隔单掺氟二氧化硅光学包层中的氟进入到单掺锗二氧化硅芯层1中,可以有效地降低了光纤中的瑞利散射,从而实现了光纤本身的低衰减;通过隔断层2的设置,对单掺氟二氧化硅光学包层中的氟进行阻隔,保证了单掺氟二氧化硅光学包层中氟的含量始终保持一定,避免氟含量的降低导致弯曲损耗增高的现象产生。且通过表格可以得出,采用本实用新型中的折射率剖面结构的G.657光纤,在1310nm的模场直径(MFD)为8.58μm情况下,1310nm衰减典型值为0.318dB/km,1550nm衰减典型值为0.177dB/km,1550nm/R7.5弯曲损耗典型值为0.048dB,1625nm/R7.5弯曲损耗典型值为0.128dB,即在保证低衰减的同时也保证了低的弯曲损耗。光纤的制备方法,其用于对上述技术方案中的光纤进行制备,具体步骤如下所示:S1:制备掺锗纤芯层:所述掺锗纤芯层是通过通入3~10g/min的SiCl4和200~400mg/min的GeCl4,初始沉积在靶棒上形成的。S2:通过气相沉积法在掺锗纤芯层外周形成疏松体状态的预制隔断层,并在预制隔断层外周形成掺氟的预制单掺氟二氧化硅光学包层得到光纤预制棒,本实施例中,预制隔断层的粘度接近掺锗纤芯的粘度,且预制隔断层能够有效地防止纤芯层中的锗的扩散和预制单掺氟二氧化硅光学包层中氟的扩散。通过使用气相沉积法形成的隔断层2,制备过程中,作为一层物理隔断,可以有效地阻止光纤及其原材料在高温状态下,单掺锗二氧化硅芯层1中的锗与单掺氟二氧化硅光学包层中的氟相互掺杂导致的折射率抵消的情况出现,从而降低了单掺锗二氧化硅芯层1或者单掺氟二氧化硅光学包层中的掺杂物的浓度。这种浓度的降低,一方面可以减少材料散射,另一方面可以降低材料应力,有利于降低光纤传输的衰减系数。在一些实施方式中,预制隔断层疏松体密度为0.32g/cm3~0.35g/cm3,如图3所示,图3中展示了隔断层2在疏松体状态下不同密度下采用VAD工艺制备的光纤衰减参数特性。这里,通过图3可以得出,而当疏松体密度在0.3g/cm3以上时,1310nm及1550nm的衰减都达到了较低的值,且在疏松体状态下的密度介于0.32g/cm3~0.35g/cm3时,衰减值达到了最低。本实施方式中,预制单掺氟二氧化硅光学包层分为三层进行堆积形成,其由内而外依次为预制浅掺氟层、预制主掺氟层及预制辅掺氟层,最终得到浅掺氟层3及辅掺氟层5的折射率均大于主掺氟层4的折射率的单掺氟二氧化硅光学包层结构。这样,通过单掺氟二氧化硅光学包层的浓度变化的设置,没有采用深掺氟的单掺氟二氧化硅光学包层结构,给光纤的制造工艺降低了难度,有利于采用VAD、OVD工艺大规模生产。S3:将光纤预制棒通过光纤熔融退火工艺及光纤涂覆固化工艺得到光纤:此过程中,光纤熔融退火工艺:预制棒从拉丝炉炉顶进入拉丝炉,拉丝炉炉体内部的温度设定为2000~2200℃,预制棒在拉丝炉炉体内熔融拉丝,牵引速度大于2000m/min;牵引完成后,光纤进入保温退火炉,保温退火炉中加热元件的温度控制在900~1300℃,并在在退火保温炉内形成800~1200℃的梯度温场,光纤在保温退火炉内逐渐降温,基本释放内应力。光纤涂覆固化工艺:光纤进入涂覆机进行涂层后,随即进入紫外光固化炉,环境温度20~28℃,环境湿度40~60%,紫外光固化炉功率控制在70~95%,紫外光固化炉内使用抽风系统,将光纤表面涂层固化挥发物抽出,并抽走有害气体,形成最终的光纤。本实用新型所提供的光纤的制备方法,其通过疏松体状态下的隔断层对纤芯层中的锗及单掺氟二氧化硅光学包层中的氟进行隔断,从而有效地避免了两种元素相互混掺,导致光纤的衰减系数增加或弯曲损耗增加的情况出现。上述实施例为本实用新型较佳的实施方式,但本实用新型的实施方式并不受上述实施例的限制,以上实施方式仅是用于解释权利要求书。然本实用新型的保护范围并不局限于说明书。任何熟悉本
技术领域:
的技术人员在本实用新型披露的技术范围内,可轻易想到的变化或者替换,都包含在本实用新型的保护范围之内。当前第1页1 2 3