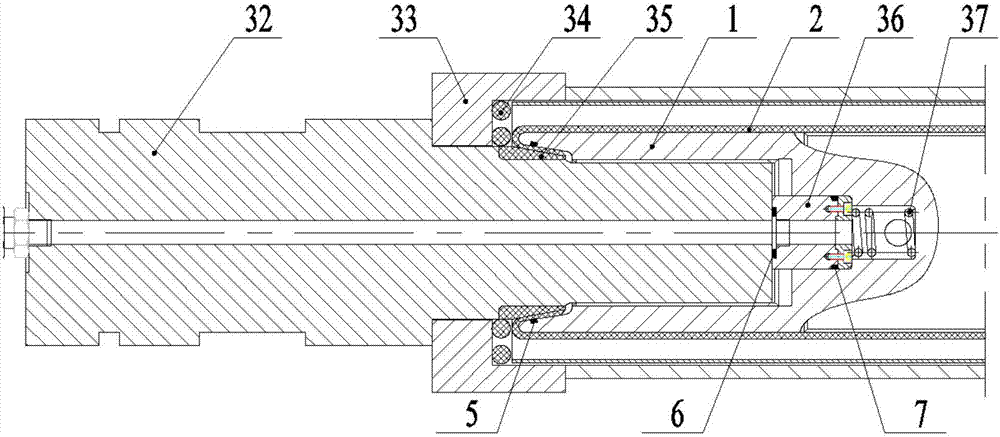
本发明属于双金属复合管制造技术领域,特别涉及一种弹性材料液胀成形双金属复合管的装置及方法。
背景技术:管道输送作为一种经济、环保、安全、不间断的长距离输送工具得到了迅速发展,已成为与铁路、公路、水路和航空并列的五大运输行业之一,但近年来,管道输送安全问题也日渐突出,因管道腐蚀引发的安全事故频发。因此,研发高性价比的耐腐蚀输送管道及对已有管道的修复一直是国内外学者主要研究课题之一。不锈钢、钛合金等管道因其具有优良的耐蚀性和加工工艺性,在石油、天然气、化工、市政、建筑等行业具有很好的应用前景,但采用纯不锈钢或钛合金管道成本较高,限制了其在工业实际生产领域内的广泛应用。而如果使用不锈钢-碳钢双金属复合管,既可有效解决管道腐蚀问题,也可大大降低成本,充分发挥了碳钢与不锈钢各自的优点,双金属复合管就是在这样的背景下应运而生。双金属复合管的制造方法有多种,典型的方法包括:液胀法、热挤压法、爆炸焊接法、粉末冶金法、离心铸造法等。根据基管与衬管间的成形界面,又分为具有冶金结合面的双金属复合管和具有机械结合面的双金属复合管。多年的应用实践证明,机械式双金属复合管耐腐蚀性能优良,成本低,是高腐蚀性油气输送管道的最佳选择,特别是通过高压液胀成形方式生产的双金属复合管,具有生产效率高,结合力大,管内表面无擦伤和破坏现象,且无加工硬化现象,复合精度高等显著优点,占据了世界范围内大部分双金属复合管市场。传统液胀成形工艺因为压力传递介质是水,胀形过程中,内外管均会与水接触,一次复合过程进行一次充水、排水过程。为保证双金属复合管的复合质量,在内外管复合前,需将内外管两端缝隙进行封焊、抽真空等工序或者在内外管两端加装防水密封圈,使内外管之间没有水分进入,保证复合要求。传统液胀成形装置,胀形过程中的轴向力通过两根或四根机架大梁承受,复合管两端的密封通过液压缸顶紧密封,液压缸同样需要克服轴向力,使得装置体积庞大,造价较高。同时,装置维护成本和运行成本较高。
技术实现要素:为了克服上述现有技术的缺陷,本发明的目的在于提供一种弹性材料液胀成形双金属复合管的装置及方法,保证胀形复合过程中双金属复合管的内外均没有水的接触,完全杜绝双金属复合管内外管夹层进水问题;高压液体在密闭的弹性材料容腔内反复使用,无充排水过程,简化胀形复合工艺,节约生产制造成本,零排放无污染。为达到上述目的,本发明采用的技术方案为:一种弹性材料液胀成形双金属复合管的装置,包括胀杆1,包覆在胀杆1外表面的高弹性胶管材料2,与胀杆1一端采用螺纹连接的高压液体输送装置3,与胀杆1另一端采用螺纹连接的双金属复合管穿套导向装置4。所述的高压液体输送装置3包括尾部连接体32,尾部连接体32一端与高压液体输送管31相连,尾部连接体32另一端与活塞体36在轴向力调节弹簧37的作用下紧密贴合,尾部连接体32的螺纹根部轴肩处安装有用自润滑材料制成的支撑环35,尾部连接体32的第二轴肩处安装有尾环33,尾环33凸台底面处安装有调整垫片34。所述的活塞体36左端安装有平面密封6,右侧安装有径向组合密封7,初始状态时,活塞体36通过轴向力调节弹簧37左端紧密贴合在尾部连接体32右端面上。所述双金属复合管导向装置4包括头部连接体44,头部连接体44的螺纹根部轴肩处安装有用自润滑材料制成的支撑环41,头部连接体44的第二轴肩处安装有导向环43,导向环43端面安装有调整垫片42,套筒46由导向环43定位并与试压帽45端面紧密贴合。所述的弹性材料胶管2与胀杆1之间采用O形密封圈5密封,尾部连接体32与活塞体36之间采用平面密封6,活塞体36与胀杆1之间采用径向组合密封7。基于上述装置的一种弹性材料液胀成形双金属复合管的方法,包括以下步骤:(1)将弹性材料胶管2套入胀杆1上,两端露出等长距离,将高压液体输送装置3与双金属复合管导向装置4分别安装在胀杆1的两端,弹性材料胶管两端通过带有斜度的支撑环压紧密封;(2)将双金属复合管8的内管82在双金属复合管穿套导向装置4的支撑下安装到位,将双金属复合管8的外管81在双金属复合管穿套导向装置4的支撑下安装到位,将套筒46由导向环43定位,将试压帽45通过螺钉拧紧固定在头部连接体44,使外管端面分别与尾环33、套筒46的端面紧密贴合;(3)将高压液体由高压液体输送管31输入,经尾部连接体32、活塞体36及胀杆1,将高压传递至弹性材料胶管2内,在高压液体压力作用下,弹性材料胶管2发生膨胀变形,并随着压力的增大经历三个阶段:第一阶段紧密贴合住双金属复合管8的内管82,第二阶段使内管82发生塑性变形紧密贴合住双金属复合管8的外管81,第三阶段使外管81发生弹性变形,直至高压液体压力达到设定的能够使材料形变的压力值;(4)高压液体在比例控制下卸压,弹性材料胶管2回复到原位,将试压帽45、导向环43、套筒46依次取出,将成形好的双金属复合管8进行退管出料。与现有技术相比,本发明具有的有益效果:1、使用了弹性材料胶管作为高压液体压力传递的介质,保证胀形复合过程中双金属复合管的内外均没有水的接触,完全杜绝双金属复合管内外管夹层进水问题,提高了双金属复合管的成形质量。2、在高压液体输送通道中采用了“平面密封+径向组合密封”的轴向自密封活塞体,且在弹性材料胶管与胀杆之间采用了O形密封圈密封,保证了高压液体在输送过程中具有良好的密封性,不发生泄漏,使实际成形压力与设定压力值相等,保证了双金属复合管成型质量。3、高压胀形液体在密闭环形容腔内反复使用,零排放无污染。不需要大量充水、排水时间,节约用水用电。4、胀形中产生的轴向力由胀杆承受,无机架大梁和平衡液压缸,简化了装置承力结构,降低装置投资成本,减少装置维护和运行成本。5、因胀形复合过程中双金属复合管的内外均没有水的接触,复合前后的准备工序大大简化,节约生产制造周期和成本。附图说明图1为本发明发明整体结构示意图。图2为高压液体输送装置3结构示意图。图3为双金属复合管穿套导向装置4结构示意图。图4为弹性材料胶管安装示意图。图5为双金属复合管内管及外管安装示意图。图6为双金属复合管液胀成形示意图。图7为最终成形的双金属复合管示意图。其中,1—胀杆,2—高弹性胶管材料,3—高压液体输送装置,31—高压液体输送管,32—尾部连接体,33—尾环,34—调整垫片,35—支撑环,36—活塞体,37—轴向力调节弹簧,4—双金属复合管导向装置,41—支撑环,42—调整垫片,43—导向环,44—头部连接体,45—试压帽,46—套筒,5—O形密封圈,6—平面密封,7—径向组合密封,8—双金属复合管,81—外管,82—内管。具体实施方式以下结合附图对本发明发明作进一步详细的说明。参照图1,一种弹性材料液胀成形双金属复合管的装置,包括胀杆1,包覆在胀杆1外表面的弹性材料胶管2,与胀杆1一端采用螺纹连接的高压液体输送装置3,与胀杆1另一端采用螺纹连接的双金属复合管穿套导向装置4。参照图2,所述高压液体输送装置3包括尾部连接体32,尾部连接体32一端与高压液体输送管31相连,另一端与活塞体36在轴向力调节弹簧37的作用下紧密贴合,尾部连接体32的螺纹根部轴肩处安装有用自润滑材料制成的支撑环35,尾部连接体32的第二轴肩处安装有尾环33,尾环33凸台底面处安装有调整垫片34。参照图2,所述的活塞体36左端安装有平面密封6,右侧安装有径向组合密封7,初始状态时,在轴向力调节弹簧37的作用下左端紧密贴合在尾部连接体32右端面上,压力升高轴向力增加时,胀杆1轴向会伸长,活塞体36右端受压面积大于左端受压面积,在液体压力下作用下,自动紧密贴合尾部连接体32右端面,轴向自动补偿。参照图3,所述双金属复合管导向装置4包括头部连接体44,头部连接体44的螺纹根部轴肩处安装有用自润滑材料制成的支撑环41,头部连接体44的第二轴肩处安装有导向环43,导向环43端面安装有调整垫片42。参照图2及图3,所述弹性材料胶管2与胀杆1之间采用O形密封圈5密封,尾部连接体32与活塞体36之间采用平面密封6,活塞体36与胀杆1之间采用径向组合密封7。基于上述装置的一种弹性材料液胀成形双金属复合管的方法,包括以下步骤:(1)参照图4,将弹性材料胶管2套入胀杆1上,两端露出等长距离约50mm,将高压液体输送装置3与双金属复合管导向装置4分别安装在胀杆1的两端,弹性材料胶管两端通过带有斜度的支撑环压紧密封;(2)参照图5,将双金属复合管8的内管82在双金属复合管穿套导向装置4的支撑下安装到位,再将双金属复合管8的外管81在双金属复合管穿套导向装置4的支撑下安装到位,再将套筒46由导向环43定位,再将试压帽45通过螺钉拧紧固定在头部连接体44,使外管端面分别与尾环33、套筒46的端面紧密贴合;(3)参照图6,将高压液体由高压液体输送管31输入,经尾部连接体32、活塞体36及胀杆1,将高压传递至弹性材料胶管2内,在高压液体压力作用下,弹性材料胶管2发生膨胀变形,并随着压力的增大经历三个阶段:第一阶段紧密贴合住双金属复合管8的内管82,第二阶段使内管82发生塑性变形紧密贴合住双金属复合管8的外管81,第三阶段使外管81发生弹性变形,直至高压液体压力达到设定压力值具体压力值与双金属复合管的内管与外管材料有关;(4)参照图5及图7,高压液体在比例控制下卸压,弹性材料胶管2回复到原位,将试压帽45、导向环43、套筒46依次取出,将成形好的双金属复合管8进行退管出料。