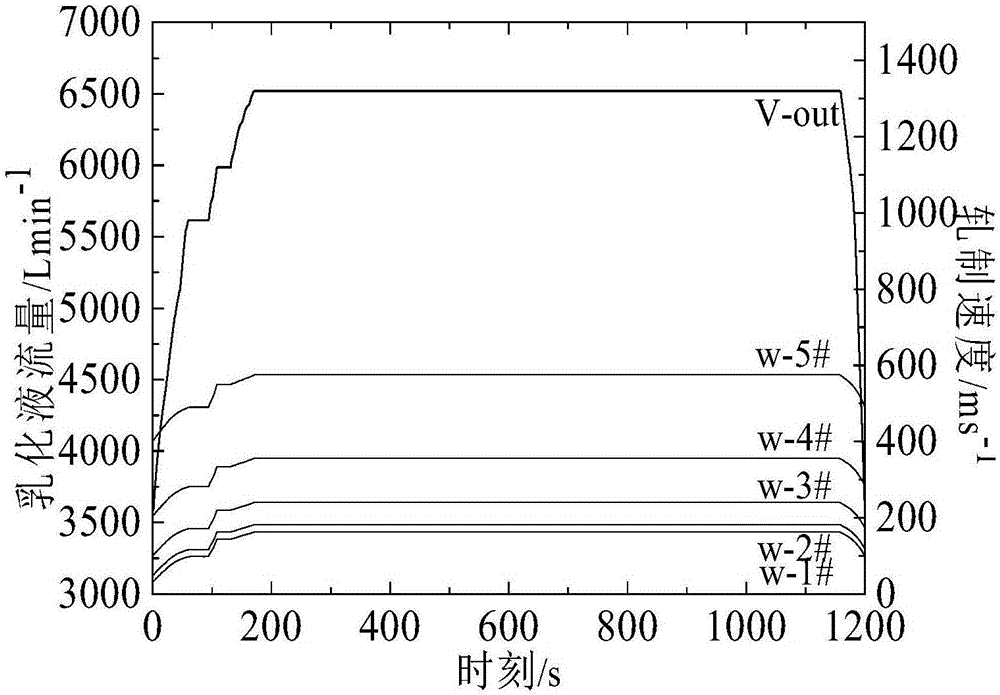
本发明属于冷轧
技术领域:
,特别涉及一种冷连轧机组的乳化液流量设定方法。
背景技术:
:在冷连轧生产过程中,为了降低轧辊与带材的表面温度、减小变形区接触弧表面上摩擦系数和摩擦力、防止金属粘在轧辊表面的同时减少轧辊磨损,需要向轧辊与带材表面喷洒的乳化液。现阶段对于冷连轧机组而言,在总流量与单机架流量不超过最大值的前提下机架之间乳化液流量是根据生产经验按照固定流量比例分配的。考虑到冷连轧机组各个机架带材的强度、压下率、前后张力等轧制工艺以及轧辊直径、表面粗糙度等设备工艺参数是不一样的,因此不同机架保证润滑与冷却所需要的乳化液供给量是不同的,不合理的乳化液流量的分配容易导致各机架冷却能力不均匀,容易造成轧制压力异常增大以及轧制压力“倒挂”等问题。特别的,由于冷连轧过程中轧制速度与摩擦系数、轧制压力、轧制功率、摩擦热、变形热、打滑因子、滑伤指数等关键轧制特征参数之间的关系是非线性的,因此维持冷却与润滑平衡所需要的乳化液的流量与轧制速度之间的关系也是非线性的。而正是由于这种非线性的存在,使得在不同轧制速度下各个机架之间所需要乳化液流量的比例应该是不断变化的。这就是说,冷连轧过程中机架间乳化液流量的分配系数不应该是一个固定值,而应该随着轧制速度的变化动态调整。现阶段,在冷连轧机组乳化液流量分配的过程中,均是单机架乳化液流量固定分配,这样的乳化液流量分配结果,不能很好的保证各机架冷却能力均匀[1-8]。(参考文献:[1]王康健,郑涛,陈杰.一种冷连轧机组极薄带钢轧制的乳化液流量综合优化方法:中国,CN201410058091.4[P].2015-08-26.[2]白振华,邢雨,李伯阳等.冷连轧过程以成本综合控制为目标的乳化液流量设定方法:中国,CN201510859447.9[P].2016-04-20.[3]王康健,郑涛,陈杰.一种冷连轧机组的工艺润滑制度优化方法:中国,CN201410371135.9[P].2016-02-10.[4]白振华,孙立壮,郭乾勇.冷连轧机组以拉毛防治为目标的工艺润滑制度优化方法:中国,CN201310562473.6[P].2014-03-05.[5]徐俊,邱格君,白振华.高速冷连轧时工艺润滑的优化技术[J].轧钢,2005,22(5):12-14.[6]刘凯,胡滨,李连胜,等.邯钢新冷轧乳化液系统的优化[J].轧钢,2011,28(6):54-56.[7]顾正秋.轧制工艺润滑理论分析[J].辽宁科技大学学报,1981,(3):97-107.[8]李红翠,张虎.济钢冷轧生产中热划伤现象的研究[J].山东冶金,2007,29(6):52-54.)技术实现要素:针对冷连轧机组机架之间乳化液流量分配固定,不能随着轧制速度的变化动态调整等问题,本发明提供一种能够充分发挥各机架乳化液的冷却能力、避免乳化液流量供给不足产生的轧制压力异常增大以及轧制压力“倒挂”等问题、提高机组生产稳定性的适用于冷连轧机组的乳化液流量动态综合优化设定方法。本发明包括以下由计算机执行的步骤:(a)参数收集;(a1)收集带材参数,主要包括带材宽度b,各机架入、出口带材厚度Hi、hi,(i=1,2,...,n),各机架带材入、出口速度v0,i、v1,i,(i=1,2,...,n),各机架带材入、出口温度ts0,i、ts1,i,(i=1,2,...,n);(a2)收集轧制工艺参数,主要包括各机架轧制压力pi,(i=1,2,...,n),各机架压下率εi,(i=1,2,...,n),各机架前张力σ1,i,(i=1,2,...,n),各机架后张力σ0,i,(i=1,2,...,n),轧制速度vi,(i=1,2,...,n);(a3)收集工艺润滑参数,主要包括乳化液浓度C,乳化液初始温度t0;(a4)收集轧辊参数,主要包括各机架工作辊直径Di,(i=1,2,...,n);(b)设定目标函数初始值F0,定义1#机架乳化液流量并初始化w1,min,w1,max,及寻优步长Δw1,设定1#机架乳化液流量寻优中间过程参数k1,并令k1=0;(c)令w1=w1,min+k1Δw1;(d)定义2#机架乳化液流量并初始化w2,min,w2,max,及寻优步长Δw2,设定2#机架乳化液流量寻优中间过程参数k2,并令k2=0;(e)令w2=w2,min+k2Δw2;(f)定义3#机架乳化液流量并初始化w3,min,w3,max,及寻优步长Δw3,设定3#机架乳化液流量寻优中间过程参数k3,并令k3=0;(g)令w3=w3,min+k3Δw3;(h)定义4#机架乳化液流量并初始化w4,min,w4,max,及寻优步长Δw4,设定4#机架乳化液流量寻优中间过程参数k4,并令k4=0;(i)令w4=w4,min+k4Δw4;(j)定义5#机架乳化液流量并初始化w5,min,w5,max,及寻优步长Δw5,设定5#机架乳化液流量寻优中间过程参数k5,并令k5=0;(k)令w5=w5,min+k5Δw5;(l)计算轧制速度为vj时各机架乳化液冷却能力系数ηi,j,其表达式为(l1)计算带材轧制过程中的摩擦热Qf,其表达式为Qf=2blμpmnf(SH(l-xn)+Shxn);式中,b为带钢宽度,mm;l为变形区长度,mm;μ为摩擦系数;pm为轧制区平均单位压力,kN;ηf为摩擦功转化为热的分配系数,一般取2/3;SH为变形区后滑率,Sh为变形区前滑率,v0、v1分别为轧件入出口速度,ms-1;vr为轧辊圆周速度,ms-1;α为变形区咬入角,rad;xn为中性面到出口的距离,mm。(l2)计算带材轧制过程中的变形热Qb,其表达式为Qb=pmηmVln(H/h);式中,ηm为塑性变形功转化为热的分配系数,一般取0.9;V为变形区带材的体积,mm3;H、h分别为带材入、出口厚度,mm。(l3)计算带材轧制过程中上游机架残留的热量Qc,其表达式为式中:Qc,i为第i机架所在的上游机架残留的热量;Qf,i-1为第i-1机架带材轧制过程中的摩擦热;Qb,i-1为第i-1机架带材轧制过程中的变形热;Qr,i-1为第i-1机架带材轧制过程中乳化液带走的热量;Qd,i-1为第i-1机架与第i机架之间带钢表面热量的散失量。(l4)计算两个机架之间带钢表面热量的散失量Qd,其表达式为Qd=ρcmV(ts1-ts0);式中:ρ为带材密度,对于钢材ρ=7800Kg/m3;cm为带材的比热,对于钢材可以取cm=470J/(Kg.℃);ts1为前部机架带材的出口温度,℃;ts0为后部机架带材的入口温度,℃。(l5)计算带材轧制过程中乳化液带走的热量Qr,其表达式为Qr=αBA(tm-t0);式中:αB为换热系数,αB=αB0w0.264T-0.213exp(9.45-0.1918C)×1.163;αB0为喷嘴形状、喷射角度影响系数;C为乳化液浓度,%;w为乳化液流量,L/min;T为带材温度,℃;A为变形区接触面积,mm2;tm为带钢与轧辊的平均温度,℃;t0为乳化液初始温度,℃。(m)计算冷连轧机组第i机架稳态轧制速度下保证Qri=Qfi+Qbi+Qci时的理论最佳流量wli,(i=1,2,...,n);(n)判断不等式wi≤wli是否成立?如果成立,转入步骤(o),否则直接转入步骤(s);(o)计算轧制速度为vj时机架乳化液总流量W,其表达式为(p)判断不等式W≤Wmax是否成立?如果成立,转入步骤(q),否则直接转入步骤(s);(q)计算轧制速度为vj时乳化液流量动态综合优化设定的目标函数F(X),其表达式为式中,α为加权系数;为冷连轧机组轧制速度为vj时整体平均乳化液冷却能力系数,(r)判断不等式F<F0是否成立?如果成立,则令F0=F,1#机架乳化液流量w1y=w1,2#机架乳化液流量w2y=w2,3#机架乳化液流量w3y=w3,4#机架乳化液流量w4y=w4,5#机架乳化液流量w5y=w5,转入步骤(s),否则,直接转入步骤(s);(s)判断不等式是否成立?如果不等式成立,则令k5=k5+1,转入步骤(k),否则转入步骤(t);(t)判断不等式是否成立?如果不等式成立,则令k4=k4+1,转入步骤(i),否则转入步骤(u);(u)判断不等式是否成立?如果不等式成立,则令k3=k3+1,转入步骤(g),否则转入步骤(v);(v)判断不等式是否成立?如果不等式成立,则令k2=k2+1,转入步骤(e),否则转入步骤(w);(w)判断不等式是否成立?如果不等式成立,则令k1=k1+1,转入步骤(c),否则转入步骤(x);(x)输出轧制速度为vj时最优1#机架乳化液流量w1y,j,最优2#机架乳化液流量w2y,j,最优3#机架乳化液流量w3y,j,最优4#机架乳化液流量w4y,j,最优5#机架乳化液流量w5y,j。(y)令vj=vj+1,转入步骤(b),完成新的轧制速度vj+1情况下各机架乳化液流量的分配,直至最终完成全部轧制速度情况下各机架乳化液流量的分配。本发明与现有技术相比具有如下优点:实现了冷连轧机组乳化液流量随着轧制速度进行动态综合优化设定,避免了机架间乳化液流量固定分配造成的轧制压力异常增大以及轧制压力“倒挂”等问题,充分发挥了乳化液冷却能力,同时使得各机架乳化液冷却能力更加均匀,提高了生产的稳定性,为生产企业带来了效益。附图说明图1是本发明总计算流程图;图2是本发明实施例1优化后各机架乳化液流量随着轧制速度的变化曲线图;图3是本发明实施例2优化后各机架乳化液流量随着轧制速度的变化曲线图。图中:v-out—轧制速度曲线、w-1#—1#机架流量曲线、w-2#—2#机架流量曲线、w-3#—3#机架流量曲线、w-4#—4#机架流量曲线、w-5#—5#机架流量曲线。具体实施方式实施例1一种适用于冷连轧机组的乳化液流量动态综合优化设定方法,其计算流程如图1所示:首先,在步骤(a)中,参数收集:(a1)收集带材参数,主要包括带材宽度b=850mm,各机架入、出口带材厚度Hi={2.1,1.17,0.65,0.40,0.27}(mm)、hi={1.17,0.65,0.40,0.27,0.22}(mm),各机架带材典型入、出口速度(m/s)v0,i=1#44.1,93.4,147.5,330,219;2#79.4,203.3,285.4,483.2,375.3;3#112.6,317.3,448.1,642,622.8;4#163.2,437.8,615.5,813.2,741.1;5#213.3,583.3,821.4,1015.3,1126.2,]]>v1,i=1#79.4,203.3,285.4,483.2,375.3;2#112.6,317.3,448.1,642,622.8;3#163.2,437.8,615.5,813.2,741.1;4#213.3,583.3,821.4,1015.3,1126.2;5#260,751.4,1038.9,1371,1156,]]>各机架带材典型入、出口温度(℃)ts0,i=1#20,20,20,20,20;2#47.1,48.3,51.4,52.3,51.7;3#49.6,50.7,52.6,54.2,53.6;4#55.2,56.9,61.0,63.2,63.2;5#64.6,66.2,69.0,71.1,69.2,]]>ts1,i=1#49.5,51.2,54.6,55.0,55.2;2#52.4,53.7,56.3,58.1,57.0;3#58.9,60.3,63.1,66.8,65.7;4#67.2,69.3,69.2,73.1,72.9;5#69.2,71.2,74.0,74.1,74.3;]]>(a2)收集轧制工艺参数,主要包括各机架典型轧制压力(kN)pi=1#7598,7584,7460,7476,7435;2#6705,6641,6554,6508,6568;3#6024,5987,5922,5895,5932;4#5589,5554,5498,5466,5538;5#5228,5218,5161,5147,5175,]]>各机架压下率εi={1#44.3%;2#44.2%;3#38.1%;4#32.5%;5#19.3%},各机架典型前张力(MPa)σ1,i=1#72,58.8,54.9,53.9,76.3;2#98,79.2,71.2,73.2,101.2;3#121.1,92.7,90.1,89.5,127.9;4#181.2,152.7,141,132.7,194.7;5#62,45,49.2,48.2,67.2,]]>各机架典型后张力(MPa)σ0,i=1#49,37,38.4,37.4,52.9;2#72,58.8,54.9,53.9,76.3;3#98,79.2,71.2,73.2,101.2;4#121.1,92.7,90.1,89.5,127.9;5#181.2,152.7,141,132.7,194.7;,]]>典型轧制速度vi={260,751.4,1038.9,1371,1156}(m/s);(a3)收集工艺润滑参数,主要包括乳化液浓度C=5.6%,乳化液初始温度t0=20℃;(a4)收集轧辊参数,主要包括各机架工作辊直径Di={1#435;2#435;3#435;4#435;5#435}(mm);随后,在步骤(b)中,设定目标函数初始值F0=1.0×1020,定义1#机架乳化液流量并初始化w1,min=3000L/min,w1,max=4000L/min,及寻优步长Δw1=50L/min,设定1#机架乳化液流量寻优中间过程参数k1,并令k1=0;随后,在步骤(c)中,令w1=w1,min+k1Δw1=3000L/min;随后,在步骤(d)中,定义2#机架乳化液流量并初始化w2,min=3000L/min,w2,max=4000L/min,及寻优步长Δw2=50L/min,设定2#机架乳化液流量寻优中间过程参数k2,并令k2=0;随后,在步骤(e)中,令w2=w2,min+k2Δw2=3000L/min;随后,在步骤(f)中,定义3#机架乳化液流量并初始化w3,min=3000L/min,w3,max=4000L/min,及寻优步长Δw3=50L/min,设定3#机架乳化液流量寻优中间过程参数k3,并令k3=0;随后,在步骤(g)中,令w3=w3,min+k3Δw3=3000L/min;随后,在步骤(h)中,定义4#机架乳化液流量并初始化w4,min=3500L/min,w4,max=5000L/min,及寻优步长Δw4=50L/min,设定4#机架乳化液流量寻优中间过程参数k4,并令k4=0;随后,在步骤(i)中,令w4=w4,min+k4Δw4=3500L/min;随后,在步骤(j)中,定义5#机架乳化液流量并初始化w5,min=3500L/min,w5,max=5000L/min,及寻优步长Δw5=50L/min,设定5#机架乳化液流量寻优中间过程参数k5,并令k5=0;随后,在步骤(k)中,令w5=w5,min+k5Δw5=3500L/min;随后,在步骤(l)中,计算轧制速度vj=260m/s时各机架乳化液冷却能力系数ηi,j={0.32,0.38,0.45,0.42,0.47};其中,在步骤(l1)中,计算轧制速度vj=260m/s时各机架带材在轧制过程中的摩擦热Qfi,j={59726,52707,47353,43934,41096}(KJ);其中,在步骤(l2)中,计算轧制速度vj=260m/s时各机架带材在轧制过程中的变形热Qbi,j={2100,1036,444,213,76}(KJ);其中,在步骤(l3)中,计算轧制速度vj=260m/s时各机架带材在轧制过程中的上游机架残留的热量Qci,j={0,15627,2095,17356,263}(KJ);其中,在步骤(l4)中,计算轧制速度vj=260m/s时两个机架之间带钢表面热量的散失量Qdi,j={1#-2#:4157,2#-3#:2700,3#-4#:2058,4#-5#:923}(KJ);其中,在步骤(l5)中,计算轧制速度vj=260m/s时带材轧制过程中乳化液带走的热量Qri,j={42042,48948,28383,42961,22084}(KJ);随后,在步骤(m)中,计算冷连轧机组第i机架稳态轧制速度下保证Qri=Qfi+Qbi+Qci时的理论最佳流量wli={3615L/min,3897L/min,4212L/min,4751L/min,5208L/min};随后,在步骤(n)中,判断不等式wi≤wli是否成立?由步骤(m)计算结果可知,不等式结果显然成立,转入步骤(o);随后,在步骤(o)中,计算轧制速度vj=260m/s时机架乳化液总流量W=16000L/min;随后,在步骤(p)中,判断不等式W≤Wmax=34000L/min是否成立?由步骤(o)计算结果可知,不等式显然成立,转入步骤(q);随后,在步骤(q)中,计算轧制速度vj=260m/s时乳化液流量动态综合优化设定的目标函数F(X)=0.218;随后,在步骤(r)中,判断不等式F<F0=1.0×1020是否成立?由步骤(q)计算结果可知,不等式显然成立,则令F0=0.218,1#机架乳化液流量w1y=3000L/min,2#机架乳化液流量w2y=3000L/min,3#机架乳化液流量w3y=3000L/min,4#机架乳化液流量w4y=3500L/min,5#机架乳化液流量w5y=3500L/min,转入步骤(s);随后,在步骤(s)中,判断不等式是否成立?由于此时k5=1,不等式显然成立,则令k5=2,转入步骤(k)继续循环计算,直到k5=30时转入步骤(t);随后,在步骤(t)中,判断不等式是否成立?由于此时k4=1,不等式显然成立,则令k4=2,转入步骤(i)继续循环计算,直到k4=30时转入步骤(u);随后,在步骤(u)中,判断不等式是否成立?由于此时k3=1,不等式显然成立,则令k3=2,转入步骤(g)继续循环计算,直到k3=20时转入步骤(v);随后,在步骤(v)中,判断不等式是否成立?由于此时k2=1,不等式显然成立,则令k2=2,转入步骤(e)继续循环计算,直到k2=20时转入步骤(w);随后,在步骤(w)中,判断不等式是否成立?由于此时k1=1,不等式显然成立,则令k1=2,转入步骤(c)继续循环计算,直到k1=20时转入步骤(x);随后,在步骤(x)中,输出轧制速度vj=260m/s时最优1#机架乳化液流量w1y=3100L/min,最优2#机架乳化液流量w2y=3200L/min,最优3#机架乳化液流量w3y=3350L/min,最优4#机架乳化液流量w4y=3600L/min,最优5#机架乳化液流量w5y=4400L/min。随后,在步骤(y)中,令vj=vj+1,转入步骤(b),完成新的轧制速度vj+1情况下各机架乳化液流量的分配,直至最终完成全部轧制速度情况下各机架乳化液流量的分配。优化后各机架乳化液流量随着轧制速度的变化曲线如图2所示。实施例2首先,在步骤(a)中,参数收集:(a1)收集带材参数,主要包括带材宽度b=975mm,各机架入、出口带材厚度Hi={2.1,1.17,0.65,0.40,0.27}(mm)、hi={1.17,0.65,0.40,0.27,0.22}(mm),各机架带材典型入、出口速度(m/s)v0,i=1#32.4,82.4,135.7,320,208;2#56.9,182.6,264.5,462.3,359.3;3#88.6,285.3,412.8,611,592.8;4#124.3,398.7,576.5,774.3,730.1;5#166.3,533.3,771.4,968.5,974.1,]]>v1,i=1#56.9,182.6,264.5,462.3,359.3;2#88.6,285.3,412.8,611,592.8;3#124.3,398.7,576.5,774.3,730.1;4#166.3,533.3,771.4,968.5,974.1;5#210,700.4,987.9,1320,1102,]]>各机架带材典型入、出口温度(℃)ts0,i=1#20,20,20,20,20;2#45.2,47.7,50.2,51.3,51.7;3#48.4,49.7,52.3,54.8,53,6;4#54.6,56.4,59.0,62.3,62.1;5#63.5,65.4,68.0,70.1,68.4,]]>ts1,i=1#48.5,50.4,53.6,54.0,54.7;2#51.4,52.7,55.2,57.7,56.1;3#57.8,59.3,62.3,65.8,64.6;4#66.3,68.3,69.0,72.3,72.1;5#68.2,70.1,73.0,73.6,73.4;]]>(a2)收集轧制工艺参数,主要包括各机架典型轧制压力(kN)pi=1#8715,8699,8557,8575,8528;2#7691,7617,7517,7465,7534;3#6910,6867,6792,6762,6804;4#6411,6370,6306,6270,6352;5#5996,5985,5920,5904,5936,]]>各机架压下率εi={1#44.3%;2#44.2%;3#38.1%;4#32.5%;5#19.3%},各机架典型前张力(MPa)σ1,i=1#87,67.8,63.9,63.9,89.9;2#105,88.2,79.8,80.4,111.3;3#130.3,102.7,100.5,98.5,139.7;4#198.2,161.5,151,147.5,205.7;5#71,54,57.8,57.2,73.8,]]>各机架典型后张力(MPa)σ0,i=1#58,46,45.2,44.6,61.2;2#87,69.8,63.9,63.9,89.9;3#105,88.2,79.8,80.4,111.3;4#130.3,102.7,100.5,98.5,139.7;5#198.2,161.5,151,147.5,205.7;]]>典型轧制速度vi={210,700.4,987.9,1320,1102}(m/s);(a3)收集工艺润滑参数,主要包括乳化液浓度C=5.6%,乳化液初始温度t0=20℃;(a4)收集轧辊参数,主要包括各机架工作辊直径Di={1#435;2#435;3#435;4#435;5#435}(mm);随后,在步骤(b)中,设定目标函数初始值F0=1.0×1020,定义1#机架乳化液流量并初始化w1,min=3000L/min,w1,max=4000L/min,及寻优步长Δw1=50L/min,设定1#机架乳化液流量寻优中间过程参数k1,并令k1=0;随后,在步骤(c)中,令w1=w1,min+k1Δw1=3000L/min;随后,在步骤(d)中,定义2#机架乳化液流量并初始化w2,min=3000L/min,w2,max=4000L/min,及寻优步长Δw2=50L/min,设定2#机架乳化液流量寻优中间过程参数k2,并令k2=0;随后,在步骤(e)中,令w2=w2,min+k2Δw2=3000L/min;随后,在步骤(f)中,定义3#机架乳化液流量并初始化w3,min=3000L/min,w3,max=4000L/min,及寻优步长Δw3=50L/min,设定3#机架乳化液流量寻优中间过程参数k3,并令k3=0;随后,在步骤(g)中,令w3=w3,min+k3Δw3=3000L/min;随后,在步骤(h)中,定义4#机架乳化液流量并初始化w4,min=3500L/min,w4,max=5000L/min,及寻优步长Δw4=50L/min,设定4#机架乳化液流量寻优中间过程参数k4,并令k4=0;随后,在步骤(i)中,令w4=w4,min+k4Δw4=3500L/min;随后,在步骤(j)中,定义5#机架乳化液流量并初始化w5,min=3500L/min,w5,max=5000L/min,及寻优步长Δw5=50L/min,设定5#机架乳化液流量寻优中间过程参数k5,并令k5=0;随后,在步骤(k)中,令w5=w5,min+k5Δw5=3500L/min;随后,在步骤(l)中,计算轧制速度vj=210m/s时各机架乳化液冷却能力系数ηi,j={0.41,0.48,0.51,0.49,0.56};其中,在步骤(l1)中,计算轧制速度vj=210m/s时各机架带材在轧制过程中的摩擦热Qfi,j={78581,69348,62306,57807,54065}(KJ);其中,在步骤(l2)中,计算轧制速度vj=210m/s时各机架带材在轧制过程中的变形热Qbi,j={2763,1364,584,280,100}(KJ);其中,在步骤(l3)中,计算轧制速度vj=210m/s时各机架带材在轧制过程中的上游机架残留的热量Qci,j={0,26794,3830,26202,1120}(KJ);其中,在步骤(l4)中,计算轧制速度vj=210m/s时两个机架之间带钢表面热量的散失量Qdi,j={1#-2#:6557,2#-3#:3318,3#-4#:2042,4#-5#:1140}(KJ);其中,在步骤(l5)中,计算轧制速度vj=210m/s时带材轧制过程中乳化液带走的热量Qri,j={47993,63564,34646,55827,24953}(KJ);随后,在步骤(m)中,计算冷连轧机组第i机架稳态轧制速度下保证Qri=Qfi+Qbi+Qci时的理论最佳流量wli={3782L/min,3991L/min,4365L/min,4923L/min,5518L/min};随后,在步骤(n)中,判断不等式wi≤wli是否成立?由步骤(m)计算结果可知,不等式结果显然成立,转入步骤(o);随后,在步骤(o)中,计算轧制速度vj=210m/s时机架乳化液总流量W=16000L/min;随后,在步骤(p)中,判断不等式W≤Wmax=34000L/min是否成立?由步骤(o)计算结果可知,不等式显然成立,转入步骤(q);随后,在步骤(q)中,计算轧制速度vj=210m/s时乳化液流量动态综合优化设定的目标函数F(X)=0.365;随后,在步骤(r)中,判断不等式F<F0=1.0×1020是否成立?由步骤(q)计算结果可知,不等式显然成立,则令F0=0.365,1#机架乳化液流量w1y=3000L/min,2#机架乳化液流量w2y=3000L/min,3#机架乳化液流量w3y=3000L/min,4#机架乳化液流量w4y=3500L/min,5#机架乳化液流量w5y=3500L/min,转入步骤(s);随后,在步骤(s)中,判断不等式是否成立?由于此时k5=1,不等式显然成立,则令k5=2,转入步骤(k)继续循环计算,直到k5=30时转入步骤(t);随后,在步骤(t)中,判断不等式是否成立?由于此时k4=1,不等式显然成立,则令k4=2,转入步骤(i)继续循环计算,直到k4=30时转入步骤(u);随后,在步骤(u)中,判断不等式是否成立?由于此时k3=1,不等式显然成立,则令k3=2,转入步骤(g)继续循环计算,直到k3=20时转入步骤(v);随后,在步骤(v)中,判断不等式是否成立?由于此时k2=1,不等式显然成立,则令k2=2,转入步骤(e)继续循环计算,直到k2=20时转入步骤(w);随后,在步骤(w)中,判断不等式是否成立?由于此时k1=1,不等式显然成立,则令k1=2,转入步骤(c)继续循环计算,直到k1=20时转入步骤(x);随后,在步骤(x)中,输出轧制速度vj=210m/s时最优1#机架乳化液流量w1y=3150L/min,最优2#机架乳化液流量w2y=3200L/min,最优3#机架乳化液流量w3y=3400L/min,最优4#机架乳化液流量w4y=3650L/min,最优5#机架乳化液流量w5y=4400L/min。随后,在步骤(y)中,令vj=vj+1,转入步骤(b),完成新的轧制速度vj+1情况下各机架乳化液流量的分配,直至最终完成全部轧制速度情况下各机架乳化液流量的分配。优化后各机架乳化液流量随着轧制速度的变化曲线如图3所示。当前第1页1 2 3