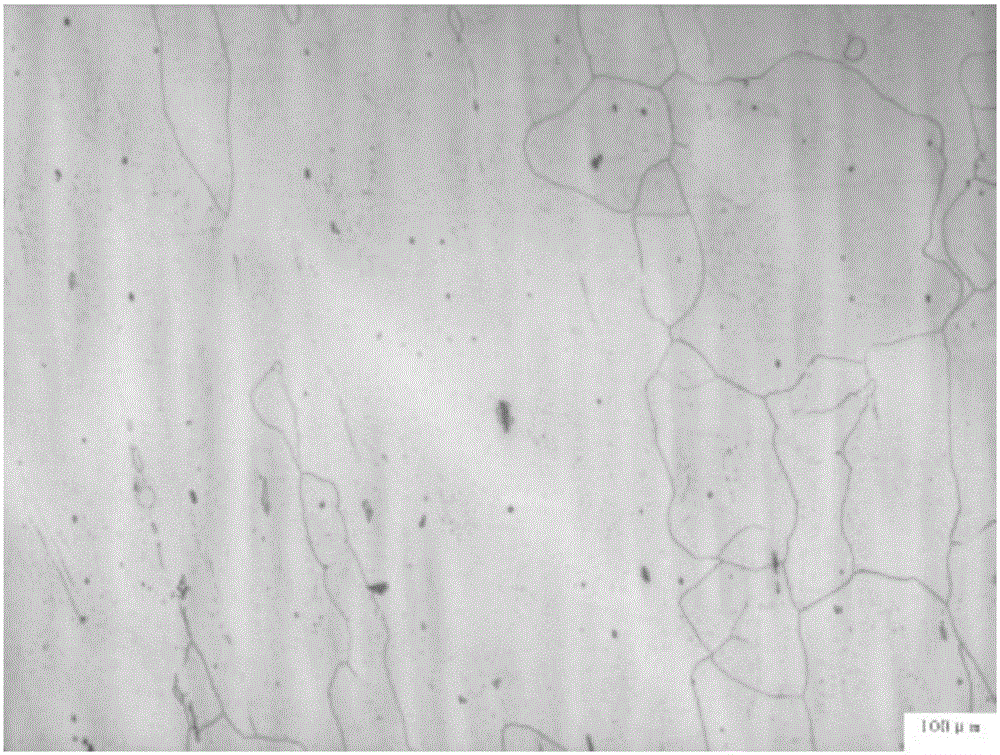
本发明属于不锈钢管材制造
技术领域:
,特别涉及一种奥氏体不锈钢大口径厚壁管的制造。
背景技术:
:奥氏体不锈钢由于具有良好的力学性能、耐腐蚀性能和冷热加工性能,得到了广泛的应用。对于直径在300mm以上,壁厚在30mm以上的奥氏体不锈钢大口径厚壁管材,目前一般采用锻造实心(空心)棒坯+机加工的方法加工制造,由于其机加工量大,导致其成材率低、生产周期长、成本高。采用离心铸坯+热轧工艺生产奥氏体不锈钢大口径管,由于具有生产工序简单,成材率高的特点而得到了广泛的应用。但是由于目前皮尔格热轧机组的变形特点决定了其管壁减薄量在60mm以下,超过60mm后,容易在外表面产生折叠和开裂缺陷,为了获得良好的晶粒组织和力学性能,其热轧变形比应不小于3:1,因此离心铸坯+热轧工艺仅适用于生产壁厚不超过20mm的大口径薄壁管材。在生产30mm以上的大口径厚壁管时,很难获得3.0以上的晶粒组织,特别是在管壁芯部容易出现粗大的晶粒组织。采用大口径冷轧机组生产奥氏体不锈钢大口径管,由于具有表面质量和尺寸精度高的特点,近年来开始得到的应用,但是由于奥氏体不锈钢冷变形抗力大,因此大口径管冷轧管材的冷轧变形量一般不超过30%,成品管材的晶粒度一般很难超过4.0级,特别是对于厚壁管来说,由于变形量不够,在管壁芯部容易产生粗大晶粒。技术实现要素:本发明的目的在于提供一种奥氏体不锈钢大口径厚壁管的制造方法,既避免了采用锻造实心(空心)棒坯+机加工方法的成材率低、生产周期长、成本高等缺陷,又解决了单纯采用皮尔格热轧机组或单纯采用大口径冷轧机组生产的奥氏体不锈钢大口径厚壁管的晶粒尺寸粗大的问题。采用本发明的制造方法生产加工的大口径厚壁管(直径300mm~500mm,壁厚30~60mm)的晶粒度可以达到4.0级以上,进一步可以达到5.0级以上。本发明的奥氏体不锈钢大口径不锈钢的制造方法,包括以下工艺步骤:(1)采用电炉+AOD炉或其他方法熔炼钢水;(2)采用离心铸造浇铸空心管坯,空心管坯的壁厚控制在100~150mm之间;(3)空心管坯经修磨后采用皮尔格热轧机组进行热轧,壁厚减薄量控制在50-60mm之间,热轧管坯的壁厚控制在45~80mm之间;(4)热轧管坯在1150-1250℃之间进行均匀化热处理;(5)均匀化热处理后热轧管材采用大口径冷轧机组进行冷轧,其冷轧变形量控制在20~30%之间;(6)冷轧管坯在870-1000℃进行组织调控退火热处理;(7)退火后冷轧管坯采用大口径冷轧机组进行二次冷轧,其冷轧变形量控制在20~30%之间;(8)冷轧大口径厚壁管材在1000-1150℃之间进行成品固溶热处理;(9)去除固溶态冷轧大口径厚壁管的氧化皮。在上述技术方案的基础上,本发明还可以做如下改进:进一步,步骤(7)中的轧辊直径控制在700~1200mm之间。本发明的有益效果是:采用大壁厚的离心铸造空心管坯作为荒管,减少了荒管的制造工序,提高了成材率;热轧管坯经高温均匀化热处理后,提高了管材壁厚方向的组织和性能的均匀性,改善了在后续冷轧变形过程中壁厚方向的变形均匀性;冷轧管坯经组织调控退火热处理后,利用第二相的钉扎作用,获得了均匀细小的晶粒组织;特别是在成品管材的冷轧工序中采用超大直径轧辊,沿管材壁厚方向获得更好的均匀变形,从而可以获得具有更加均匀细小晶粒组织的大口径厚壁成品管材。1)热轧管壁减薄量控制热轧变形量越大,热轧管坯的变形能贮存越多,高温均匀化热处理后再结晶形核位置越多,再结晶晶粒越细;同时要有足够大的变形量,壁厚芯部才有足够大的变形量,破碎铸态组织,经高温均匀化热处理后形成完全再结晶组织。但是由于离心铸坯为铸态组织,热塑性低,若变形量过高,内外表面容易出现轧制裂纹缺陷,同时变形抗力提高,会超出轧机的轧制能力。因此采用皮尔格热轧机热轧时,其管壁减薄量控制在50~60mm范围内。2)热轧管坯的均匀化热处理为了保证管材轧制变形时的变形量,大口径厚壁离心管坯壁厚超过100mm,热轧时其管壁减薄量在50~60mm之间,因此其变形比仅约为2:1,不仅总变形比低,而且由于管壁厚度大,沿壁厚方向变形不均匀,内外层变形量大,芯部变形量小。采用常规退火热处理工艺(约1050~1150℃)后,管材会形成内外表层细小、芯部粗大的“三明治型”晶粒组织,此类组织经后续的冷轧和固溶热处理等加工后也不能完全消除。热轧管坯经高温均匀化热处理(1150~1250℃)后,沿壁厚方向可以获得较为均匀的晶粒组织,消除了壁厚方向的组织和成分不均匀性;均匀热处理温度超过1250℃后,表面氧化严重,恶化了管坯的表面质量。因此热轧管坯的高温均匀化热处理温度控制在1150~1250℃之间。3)冷轧变形量冷轧变形量越大,冷轧管坯的变形能贮存越多,在随后的热处理过程中再结晶形核位置越多,再结晶晶粒越细;但是由于奥氏体不锈钢的冷变形抗力大,变形量过大,变形抗力会超出冷轧设备的轧制能力。因此,冷轧变形量控制在20~30%之间。4)冷轧管坯的组织调控退火热处理在常规的冷轧管中间道次的退火热处理过程中,为了提高生产效率,热处理温度在1050~1150℃之间,控制较高的热处理温度可以获得具有良好变形能力的冷轧管坯,在随后的冷轧变形过程中获得单道次大变形量(超过50%),从而细化晶粒。但是对于大口径厚壁管而言,由于其单道次变形量很难超过30%,因此不能通过单道次大变形量来改善晶粒组织。对于大口径厚壁管,冷轧管的组织调控退火热处理温度控制在870~1000℃之间。冷轧奥氏体不锈钢在此温度范围内加热,首先析出碳氮化物和金属间相(比如σ相),随后形成的再结晶晶粒在先析出的碳氮化物和金属间相的钉扎作用下很难发生长大,因此可以获得比常规退火热处理细小的再结晶组织。热处理温度低于870℃,很难发生完全再结晶;高于1000℃,先析出的碳氮化物和金属间相发生溶解,无钉扎晶界的作用,再结晶晶粒长大粗化。因此冷轧管坯的组织调控退火热处理控制在870~1000℃之间。5)成品管材的固溶热处理冷轧成品管材经固溶热处理后形成完全再结晶奥氏体组织,获得良好的力学性能和耐腐蚀性能。若固溶热处理温度低于1000℃,在加热过程中形成的碳氮化物和金属间相溶解不充分,会恶化管材的力学性能和耐腐蚀性能;若固溶热处理温度高于1150℃,此时完全再结晶结晶晶粒发生异常长大,形成粗晶和混晶,也会恶化管材的力学性能。因此,成品管材的固溶热处理温度区间控制在1000-1150℃之间。6)轧辊直径在变形量一定的情况下,冷轧辊直径的增大可以减少管材外表面的剪切变形,让轧制变形可以渗透到管壁芯部,从而提高管壁芯部的变形量,细化退火热处理后的再结晶组织。轧辊直径过大,轧机的轧制能力不够。因此成品管材的冷轧辊直径控制在700-1200mm之间。附图说明图1为热轧管坯经1080℃退火热处理后内壁晶粒组织图。图2为热轧管坯经1080℃退火热处理后芯部晶粒组织图。图3为热轧管坯经1080℃退火热处理后外壁晶粒组织图。图4为热轧管坯经1180℃退火热处理后内壁晶粒组织图。图5为热轧管坯经1180℃退火热处理后芯部晶粒组织图。图6为热轧管坯经1180℃退火热处理后外壁晶粒组织图。图7为高温均匀化退火温度和热轧管材内壁、芯部和外壁晶粒尺寸的关系图。图8为组织调控热处理温度和冷轧管坯芯部晶粒尺寸的关系图。图9为冷轧管坯经830℃组织调控热处理后的晶粒组织图。图10为冷轧管坯经950℃组织调控热处理后的晶粒组织图。图11为冷轧管坯经1050℃组织调控热处理后的晶粒组织图。图12为采用常规退火热处理工艺生产的成品管材内壁晶粒组织图。图13为采用常规退火热处理工艺生产的成品管材芯部晶粒组织图。图14为采用常规退火热处理工艺生产的成品管材外壁晶粒组织图。图15为采用高温均匀化退火和组织调控退火工艺生产的成品管材内壁晶粒组织图。图16为采用高温均匀化退火和组织调控退火工艺生产的成品管材芯部晶粒组织图。图17为采用高温均匀化退火和组织调控退火工艺生产的成品管材外壁晶粒组织图。图18为采用大直径轧辊生产的成品管材的内壁晶粒组织图。图19为采用大直径轧辊生产的成品管材的芯部晶粒组织图。图20为采用大直径轧辊生产的成品管材的外壁晶粒组织图。具体实施方式以下结合附图对本发明的原理和特征进行描述,所举实例只用于解释本发明,并非用于限定本发明的范围。实施例采用电炉+AOD炉+离心铸造熔炼浇,化学成分如表1所示,管材的加工工艺参数如表2所示。按GB/T6394-2002“金属平均晶粒度测定法”进行晶粒度评级。表1实施例奥氏体不锈钢的化学成分炉号CSiMnPSCrNiMoNFe10.0220.470.90.0220.00418.410.70.110.04余20.0630.581.20.0120.00517.712.42.70.15余30.0320.398.10.0280.00620.36.60.090.28余实施例1热轧管坯的均匀化热处理图1、图2和图3分别示出了炉号为1#的热轧管坯经1080℃热处理后内壁、芯部和外壁的晶粒组织;图4、图5和图6分别示出了炉号为1#的热轧管坯经1180℃高温均匀化热处理后内壁、芯部和外壁的晶粒组织。热轧管坯经过1080℃热处理后,内壁和外壁均发生了完全再结晶,再结晶晶粒尺寸细小,芯部再结晶不完全,还有未完全再结晶的铸态组织;经过1180℃高温均匀化热处理后,内壁、外壁和芯部均发生了完全的再结晶组织,晶粒尺寸比较均匀。可见,提高热轧管坯均匀化热处理温度对于改善壁厚方向的组织均匀性有非常大的有益作用。图7示出了高温均匀化退火温度和热轧管材内壁、芯部和外壁的晶粒尺寸的关系。可见应将热轧管坯的均匀化退火温度控制在1150~1250℃之间。实施例2冷轧管坯的组织调控退火热处理图9、图10和图11分别示出了炉号为2#的冷轧管坯在分别经830℃、930℃和1050℃组织调控热处理后管壁芯部的晶粒组织。经过930℃和1050℃热处理后,冷轧管坯发生了完全再结晶,1050℃热处理后,管壁芯部再结晶晶粒尺寸大,其晶粒度为3.5级,930℃热处理后,管壁芯部再结晶晶粒尺寸小,晶粒度为4.5级;经过830℃热处理后,冷轧管坯未完全再结晶,晶粒粗大,为2.0级。图8示出了组织调控退火热处理温度和冷轧管坯芯部晶粒尺寸的关系。可见应将冷轧轧管坯的组织调控热处理温度控制在870℃~1000℃之间。图12、图13和图14分别示出了采用常规退火热处理工艺生产的成品管材内壁、芯部和外壁的晶粒组织(11#),其内壁壁、芯部和外壁的晶粒度分别为3.5、2.0和3.5级;图15、图16和图17分别示出了采用高温均匀化退火和组织调控退火工艺生产的成品管材内壁、芯部和外壁的晶粒组织(13#),其内壁、芯部和外壁的晶粒度分别为5.0、4.5和5.0级。可见采用高温均匀化退火和组织调控退火工艺对细化成品管材的晶粒有良好作用。表2实施例加工工艺参数和晶粒度评级结果实施例3轧辊直径采用直径为600mm、800mm和1000mm的冷轧辊轧制的冷轧成品管材的管壁芯部的晶粒度分别为4.5、5.0和5.5级,图18、图19和图20分别示出了1000mm冷轧辊轧制的成品管材的内壁、芯部和外壁的晶粒组织。可见,提高成品管材的冷轧辊直径对于细化管壁芯部的晶粒有良好的有益作用。进一步将轧辊直径控制在700-1200mm之间,成品管材的晶粒度可以控制在5.0及其以上级别。以上所述仅为本发明的所有实施例的一部分,并不用以限制本发明,凡在本发明的精神和原则之内,所作的任何修改、等同替换、改进等,均应包含在本发明的保护范围之内。当前第1页1 2 3