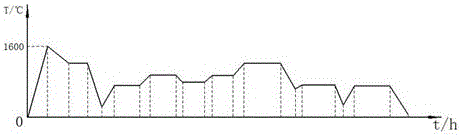
本实用新型涉及有色金属、黑色金属压延成型斜轧工艺,主要涉及到轧制变形孔腔辊型领域,尤其是一种八段式轧管辊型。
背景技术:
:为满足产品质量,适用市场发展的需求,不断的开发研制极限规格产品,开拓新的市场领域,适应有色金属的压延成型,设计了八段式轧辊辊型。该辊型的设计能够满足大尺寸薄壁规格产品的生产,产品D/S可达到40以上,产品规格范围Φ180~377mm,壁厚7~120mm,提高了本生产线的产品覆盖范围,使该工艺具备了生产更多规格、更多材质的系列产品的能力。该八段式轧管功能辊型的设计,使原有的产品外径系列由原来的28种增加到了96种规格,降低了综合成本,轧制材质由轧制黑色金属向有色金属领域迈进。技术实现要素:为提升生产线的综合效益,适应市场需求,提高本生产线的产品覆盖范围,使其生产工艺具备生产更过的规格系列产品,降低综合成本,本实用新型提供了一种八段式轧管辊型。一种八段式轧管辊型,轧管辊型的中心设有轴孔,轧管辊型外径1000-1200mm,辊身总长1000mm,辊身主要分为入口锥和出口锥,入口锥包括有四个辊面角度,出口锥包括有四个辊面角度,轧辊的辊面总共分为八个区间,依次为:入口锥I区,用于保障轧制过程毛管顺利咬入,倒角半径为40mm,轧辊入口端面辊面角为9°,长度为165mm;入口锥II区辊面角为7°,长度为165mm;入口锥Ⅲ区(辊面角为3.25°,长度为85mm;减壁区辊面角为4.5°,长度为45mm;精整区辊面角3.4°,长度为220mm;出口锥I区辊面角2°,的长度为150mm;出口锥II区辊面角2.25°,长度为100mm;出口锥Ⅲ区辊面角4°,长度为70mm,倒角半径为15mm。与现有技术相比,本实用新型的有益效果为:1.本实用新型的八段式轧管辊型,总的设计原理为两部分,入口段和出口段为主要轧制基础原理,八段式轧管用辊型设计在此基础上,将入口段和出口段的这两个工作段又细分为四个段,致使入口段出口段在整个辊身设计上分布了八个工作段。这样使荒管在同一轧制线速度的情况下与轧辊的接触切面更合理、更有效、更充分,提高了轧辊辊身的利用率,使轧辊辊型更适应金属变形的流动性。2.本实用新型的八段式轧管辊型,提高了辊面精度,增加了使用寿命,同时解决了原机构的故障率高的问题,轧制故障率由原来的百分之三降低到百分之一,确保生产作业的连续性,避免了一些轧卡现象,保障了在生产过程中的轧制稳定性,保证了产品的轧制精度,提高了生产作业效率。3.本实用新型的八段式轧管辊型,提高了生产组织的灵活性,使其具备了轧制有色金属、黑色金属色的能力;轧辊是压延成型过程中轧制孔腔的核心热工具,该八段式轧管辊型的设计应用使工艺可生产各种能源装备用高合金、海洋钻探合金、油套管、管线管、钛锆铪铌及其合金管等无缝管系列产品。4.本实用新型的八段式轧管辊型,提高了产品在加工制造过程中的质量,改进优化了在热塑性变形过程中金属的流动性,增强了轧制过程的稳定性;并保障在抛管过程中顺利抛出荒管,轧辊的辊型设计对荒管成型的几何尺寸和质量起到了至关重要的作用。附图说明图1为本实用新型的结构示意图;图2为本发明制作方法的温度-时间关系曲线图;图中,L1、出口锥Ⅲ区,L2、出口锥II区,L3、出口锥I区,L4、精整区,L5、减壁区,L6、入口锥Ⅲ区,L7、入口锥II区,L8、入口锥I区;1、出口锥,2、入口锥。具体实施方式以下结合附图对本申请的实施例进行详细说明,但是本申请可以由权利要求限定和覆盖的多种不同方式实施。构成本申请的一部分的附图用来提供对本申请的进一步理解,本申请的示意性实施例及其说明用于解释本申请,并不构成对本申请的不当限定。一种八段式轧管辊型,轧辊辊型的中心设有轴孔,轧辊外径1000-1200mm,辊身总长1000mm,辊身主要分为入口锥2和出口锥1两个锥角,其中,入口锥2长540mm,出口锥1长460mm。入口锥2又细分为四个辊面角度,出口锥1也细分了四个辊面角度,轧辊的辊面总共分为八个区间,依次设有入口锥I区L8、入口锥II区L7、入口锥Ⅲ区L6、减壁区L5,精整区L4,出口锥I区L3,出口锥II区L2,出口锥Ⅲ区L1。其中,入口锥I区L8设计了倒角,倒角半径为40mm,保障轧制过程毛管顺利咬入,入口锥I区L8辊面角为9°、L8长度尺寸为165mm。入口锥II区L7辊面角为7°,L7长度为165mm;入口锥Ⅲ区L6辊面角为3.25°,L6长度为85mm;减壁区L5辊面角为4.5°,减壁区L5长度为45mm;精整区L4辊面角3.4°,精整区L4长度为220mm;出口锥I区L3辊面角2°,出口锥I区L3的长度为150mm;出口锥II区L2辊面角2.25°,出口锥II区L2长度为100mm;出口锥Ⅲ区L1辊面角4°,出口锥Ⅲ区L1圆角区长度尺寸为70mm,同时出口锥Ⅲ区L1设计的倒角半径为15mm。轧管机的轧辊在轧制过程中的基本工作原理:咬入、稳定轧制、抛出三个阶段,首先是保障毛管在入口端的顺利咬入,轧辊使管体咬入并旋转前进,在稳定轧制过程中致使管体减壁同时横向纵向延伸。实施例1本轧管辊型总共分为八个工作段,由出口方向起每个工作段的角度分别为:第一段L1为4°、第二段L2为2°30`、第三段L3为2°、第四段L4为3°45`、第五段L5为4.5°、第六段L6为3°30`、第七段L7为7°第八段L8为9°,每个角度在轧制过程中对轧制的荒管起到了不同的轧制作用。自入口方向起每段的作用实现了对毛管的正常咬入、管体压缩变形、管体旋转、横向延伸、纵向延伸对管体起到了减壁、均壁、扩径、均外表面归圆、最后抛出荒管完成轧制。经过一系列的轧制变形更合理的使得金属在孔腔区间完成轧制成型,本实用新型的轧管辊型具有轧制精度高,轧制平稳的实用特性,是轧制变形保证产品质量必不可少的核心部分。一种八段式轧管辊型的制作方法,包括如下工艺步骤:a.将混合的钢坯料放入电炉中加热熔化;混合的钢坯料百分比组分为:C:2.9-3.2、W:0.9-1.3、Mo:4.3-6.8、V:4.6-5.7、Cr:11.41-12.9、Al:0.3-0.8、Ni:1.4-1.5、Co:8.8-10.5、Nb:0.1-0.35、Ti:0.3-0.8、Ce:0.5-0.7、Zr:0.08-0.23、Si<0.7、Mn<1.4、S<0.07、P<0.03、其余为Fe;b.3-5h内,将电炉温度均匀升至1500-1595℃,加入REB复合变质剂,并充分搅拌均匀,1-2h内,将电炉温度均匀降至1400-1495℃,再次加入REB复合变质剂,并充分搅拌均匀;REB复合变质剂为RE和B的混合物,其中,RE≤2.0wt%,B≤0.05wt%;c.调整钢水温度为1430-1480℃,启动离心机,使其转速为800rpm-l000rpm;将钢水浇注到铸型中,钢水浇注完毕40-55min后,关闭离心机,从铸型中取出铸坯直接入炉退火处理;d.退火处理工艺为:铸坯随温度不低于250℃的热处理炉加热至670-720℃保温2h-3h,然后继续加热至980-1010℃保温5-7h,1-3h炉冷至750-815℃,然后继续加热至920-970℃保温3-5h,1-3h炉冷至室温;e.粗加工后进行淬火处理,淬火处理工艺是随炉加热至1260-1280℃,保温3-5h,然后油淬,淬火后进行回火处理,回火处理工艺是随炉加热至620-650℃,保温5-7h,炉冷,然后再加热至610-630℃,保温5-7h,空冷,回火处理后进行精加工,得到尺寸精度和表面光洁度符合要求的轧辊。实施例2轧管辊型结构同时实施例1,制作方法,包括如下工艺步骤:a.将混合的钢坯料放入电炉中加热熔化;混合的钢坯料百分比组分为:C:2.9,W:0.9,Mo:4.3,V:4.6,Cr:11.41,Al:0.3,Ni:1.4,Co:8.8,Nb:0.1,Ti:0.3,Ce:0.5,Zr:0.08,Si:0.7,Mn:1.4,S:0.07,P:0.03,其余为Fe;b.3h内,将电炉温度均匀升至1500℃,加入REB复合变质剂,并充分搅拌均匀,1h内,将电炉温度均匀降至1400℃,再次加入REB复合变质剂,并充分搅拌均匀;REB复合变质剂为RE和B的混合物,其中,RE为1.0wt%,B为0.01wt%;c.调整钢水温度为1430℃℃,启动离心机,使其转速为800rpm;将钢水浇注到铸型中,钢水浇注完毕40min后,关闭离心机,从铸型中取出铸坯直接入炉退火处理;d.退火处理工艺为:铸坯随温度250℃的热处理炉加热至670℃保温2h,然后继续加热至980℃保温5h,1h炉冷至750℃,然后继续加热至920℃保温3h,1h炉冷至室温;e.粗加工后进行淬火处理,淬火处理工艺是随炉加热至1260℃,保温3h,然后油淬,淬火后进行回火处理,回火处理工艺是随炉加热至620℃,保温5h,炉冷,然后再加热至610℃,保温5h,空冷,回火处理后进行精加工,得到尺寸精度和表面光洁度符合要求的轧辊。实施例3轧管辊型结构同时实施例1,制作方法,包括如下工艺步骤:a.将混合的钢坯料放入电炉中加热熔化;混合的钢坯料百分比组分为:C:3.2,W:1.3,Mo:6.8,V:5.7,Cr:12.9,Al:0.8,Ni:1.5,Co:10.5,Nb:0.35,Ti:0.8,Ce:0.7,Zr:0.23,Si:0.7,Mn:1.4,S:0.07,P:0.03,其余为Fe;b.5h内,将电炉温度均匀升至1595℃,加入REB复合变质剂,并充分搅拌均匀,2h内,将电炉温度均匀降至1495℃,再次加入REB复合变质剂,并充分搅拌均匀;REB复合变质剂为RE和B的混合物,其中,RE:2.0wt%,B:0.05wt%;c.调整钢水温度为1480℃,启动离心机,使其转速为l000rpm;将钢水浇注到铸型中,钢水浇注完毕55min后,关闭离心机,从铸型中取出铸坯直接入炉退火处理;d.退火处理工艺为:铸坯随温度不低于250℃的热处理炉加热至720℃保温3h,然后继续加热至1010℃保温7h,3h炉冷至815℃,然后继续加热至970℃保温5h,3h炉冷至室温;e.粗加工后进行淬火处理,淬火处理工艺是随炉加热至1280℃,保温5h,然后油淬,淬火后进行回火处理,回火处理工艺是随炉加热至650℃,保温7h,炉冷,然后再加热至630℃,保温7h,空冷,回火处理后进行精加工,得到尺寸精度和表面光洁度符合要求的轧辊。试验效果:将实施例1-3中的轧辊以及所购买的普通轧辊分别取三根,分别加热至300℃,500℃,700℃,对实施例1-3中的轧辊以及所购买的普通轧辊进行硬度测试,测试所得的数值如表所示,硬度测试HRC普通轧辊实施例1轧辊实施例2轧辊实施例3轧辊300℃47595860500℃41515253700℃36464748通过上表所示,我们可以明显的看出,通过本实用新型方法制作加工出的轧辊,不同的温度范围内,在强度方面,均具有明显的优势。最后所应说明的是,以上具体实施方式仅用以说明本实用新型的技术方案而非限制,尽管参照较佳实施例对本实用新型进行了详细说明,本领域的普通技术人员应当理解,可以对本实用新型的技术方案进行修改或者等同替换,而不脱离本实用新型技术方案的精神和范围,其均应涵盖在本实用新型的权利要求范围当中。当前第1页1 2 3