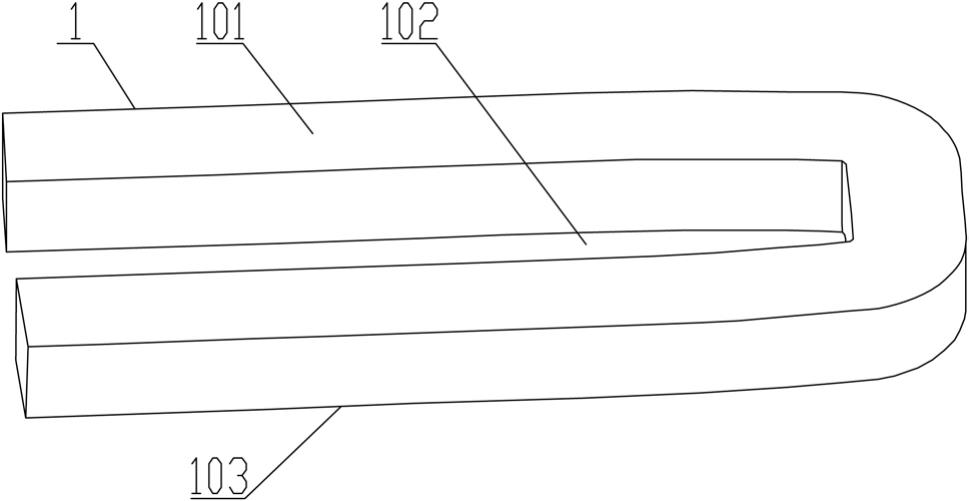
[0001]
本发明涉及薄壁件加工技术领域,特别是涉及异形不锈钢薄壁件的三维模拟加工工装及方法。
背景技术:[0002]
接管类零件是ge公司的长线产品,其组成零件“插入块”是典型的薄壁零件代表,带有“不规则曲面结构”,且材料为不锈钢,有很高的尺寸精度和几何形状要求,加工难度高,附加值更高。
[0003]
目前,公司对该类零件是成品采购,花费大量的资金,大大增加了成本,不符合公司提出的精益生产的要求,也违背了公司的利益。因零件为特殊的异形不锈钢件,而且很薄、形状怪异,直接无法装夹;所以必须要借用工装进行辅助装夹加工。由于该零件外型都是不规则的曲面,无法人工编制程序,所以必须借助ug软件辅助生成三维模拟图设计加工工装。因此,需要针对此薄壁零设计相应的加工工装和方法来实现其加工。
技术实现要素:[0004]
本发明目的是提供了异形不锈钢薄壁件的三维模拟加工工装及方法,此工装能够用于接管类薄壁零件的辅助加工,能够完成曲面加工,提高了其加工质量和效率。
[0005]
为了实现上述的技术特征,本发明的目的是这样实现的:异形不锈钢薄壁件的三维模拟加工工装,它包括用于对毛坯件的大端面和u型内腔进行加工装夹时的大面内腔加工工装;包括用于对毛坯件的小端面进行加工装夹时的小面外型加工工装;所述小面外型加工工装与用于对毛坯件进行压紧的压紧盖板相配合。
[0006]
所述大面内腔加工工装包括矩形装夹底座,所述矩形装夹底座的中心部位加工有让刀凹槽,所述让刀凹槽的轮廓线与毛坯件的u型内腔的轮廓相匹配;所述让刀凹槽的外围加工有多个第一通孔。
[0007]
所述第一通孔与加工在毛坯件的小端面上的装夹螺纹孔相配合,并对整个毛坯件进行固定。
[0008]
所述小面外型加工工装包括底座,所述底座的顶部加工有定位凸台,所述定位凸台的中间部位加工有用于和压紧盖板相配合的多个第一螺纹孔,所述定位凸台的外围加工有用于和已加工好的大面内腔体相配合的弧形过渡外轮廓,所述弧形过渡外轮廓的末端设置有用于和大端面边缘相配合的定位边板,所述底座上加工有第二螺纹孔。
[0009]
所述压紧盖板通过顶部螺栓将毛坯件固定在定位凸台的顶部,所述底座的顶部通过压紧螺杆固定安装有压板,并将整个小面外型加工工装压紧在机床上。
[0010]
采用所述的三维模拟加工工装对异形不锈钢薄壁件进行加工的方法,它包括以下步骤:步骤1:工装制作;根据所加工的异形不锈钢薄壁件结构尺寸制作相应的大面内腔加工
工装、小面外型加工工装和压紧盖板;步骤2:毛坯件的下料;选取一定厚度和相应尺寸的板材,采用水刀切割的方式,将板材切割成带有u型内腔的毛坯件;步骤3:毛坯件和大面内腔加工工装的初步装夹固定;步骤4:对毛坯件的大端面和u型内腔进行加工;步骤5:对已经加工好大面内腔体的毛坯件与小面外型加工工装进行再次装夹固定;步骤6:对毛坯件的小端面及外型进行加工。
[0011]
所述步骤3的具体操作过程为:步骤3.1:在待加工的毛坯件的小端面加工多个用于和大面内腔加工工装的第一通孔相配合的装夹螺纹孔;步骤3.2:将毛坯件放置于大面内腔加工工装的顶部,并通过螺栓将毛坯件和大面内腔加工工装固定;步骤3.3:将大面内腔加工工装置于等高垫上,采用打压板压紧之后将整个大面内腔加工工装放置于立式加工中心平台上。
[0012]
所述步骤4的具体加工过程为:步骤4.1:根据产品的大端面以及大面内腔体的外形尺寸,采用ug模拟加工生成程序,启动立式加工中心根据所生成的程度用第一铣刀对u型内腔部分进行粗加工;步骤4.2:采用ug模拟加工生成程序,用第二铣刀对u型内腔部分进行半精加工;步骤4.3:采用ug模拟加工生成程序,用第三铣刀对u型内腔部分进行精加工,最终形成高精度的大面内腔体。
[0013]
所述步骤5的具体操作过程为:步骤5.1:将前工序加工好的大面内腔体倒扣在小面外型加工工装的定位凸台上,并保证大面内腔体与弧形过渡外轮廓相匹配;步骤5.2:将小面外型加工工装底面置于工作台上,将压紧盖板盖好,并通过顶部螺栓将压紧盖板固定在工装上同时将毛坯压紧;步骤5.3:在底座的第二螺纹孔上通过压紧螺杆装压板,进而将整个小面外型加工工装固定在工作台上。
[0014]
所述步骤6的具体加工过程为:步骤6.1:根据产品的小端顶面及外轮廓的外形尺寸,采用ug模拟加工生成程序,启动立式加工中心根据所生成的程度用第四铣刀对小端顶面及外轮廓部分进行粗加工;步骤6.2:采用ug模拟加工生成程序,用第五铣刀对小端顶面及外轮廓部分进行半精加工;步骤6.3:采用ug模拟加工生成程序,用第六铣刀对小端顶面及外轮廓部分进行精加工;步骤6.4:对精加工之后的产品进行抛光处理。
[0015]
本发明有如下有益效果:1、本发明通过对插入块的实际加工验证:工装制作简单,装夹便捷,加工过程稳定,尺寸得到精确控制,完工产品通过质量认证。
[0016]
2、通过本发明的工装及加工方法,克服了不锈钢薄壁异形件难以装夹和加工的难
题,能够达到精确装夹加工,保证尺寸的稳定性。
[0017]
3、通过上述的大面内腔加工工装能够用于对毛坯件进行装夹,进而便于对其另一端的大面内腔体进行加工。
[0018]
4、通过上述的小面外型加工工装能够用于和已经加工好的大面内腔体相配合,进而实现对毛坯件的小端面进行加工。
附图说明
[0019]
下面结合附图和实施例对本发明作进一步说明。
[0020]
图1为本发明毛坯件三维结构图。
[0021]
图2为本发明毛坯件俯视图图3为本发明产品三维结构图。
[0022]
图4为本发明大面内腔加工工装三维结构图。
[0023]
图5为本发明毛坯件上加工装夹螺纹孔之后的三维图。
[0024]
图6为本发明毛坯件与大面内腔加工工装装夹之后的附图视图。
[0025]
图7为本发明毛坯件与大面内腔加工工装装夹之后的三维图。
[0026]
图8为本发明小面外型加工工装三维结构图。
[0027]
图9为本发明小面外型加工工装俯视图。
[0028]
图10为本发明小面外型加工工装右视图。
[0029]
图11为本发明压紧盖板俯视图。
[0030]
图12为本发明毛坯件与小面外型加工工装装夹之后的三维图。
[0031]
图13为本发明毛坯件进行u型内腔加工时的粗加工示意图。
[0032]
图14为本发明毛坯件进行u型内腔加工时的半精加工示意图。
[0033]
图15为本发明毛坯件进行u型内腔加工时的精加工示意图。
[0034]
图16为本发明毛坯件加工好大面内腔体之后的结构图。
[0035]
图17为本发明毛坯件进行外轮廓加工时的粗加工示意图。
[0036]
图18为本发明毛坯件进行外轮廓加工时的半精加工示意图。
[0037]
图19为本发明毛坯件进行外轮廓加工时的精加工示意图。
[0038]
图中:毛坯件1、产品2、大面内腔加工工装3、小面外型加工工装4、压紧盖板5、顶部螺栓6、压紧螺杆7、压板8、第一铣刀9、第二铣刀10、第三铣刀11、第四铣刀12、第五铣刀13、第六铣刀14;小端面101、u型内腔102、大端面103、装夹螺纹孔104;小端顶面201、大面内腔体202、外轮廓203;第一通孔301、让刀凹槽302、矩形装夹底座303;第二螺纹孔401、定位边板402、弧形过渡外轮廓403、第一螺纹孔404、定位凸台405、底座406。
具体实施方式
[0039]
下面结合附图对本发明的实施方式做进一步的说明。
[0040]
实施例1:
参见图1-19,异形不锈钢薄壁件的三维模拟加工工装,它包括用于对毛坯件1的大端面103和u型内腔102进行加工装夹时的大面内腔加工工装3;包括用于对毛坯件1的小端面101进行加工装夹时的小面外型加工工装4;所述小面外型加工工装4与用于对毛坯件1进行压紧的压紧盖板5相配合。通过上述的加工工装,能够用于对毛坯件1进行加工,最终实现异形不锈钢薄壁件的加工成型。
[0041]
进一步的,所述大面内腔加工工装3包括矩形装夹底座303,所述矩形装夹底座303的中心部位加工有让刀凹槽302,所述让刀凹槽302的轮廓线与毛坯件1的u型内腔102的轮廓相匹配;所述让刀凹槽302的外围加工有多个第一通孔301。通过上述的大面内腔加工工装3能够用于对毛坯件1进行初步装夹固定,通过让刀凹槽302保证了加工过程中实现对u型内腔102的加工,进而使其形成大面内腔体202。
[0042]
进一步的,所述第一通孔301与加工在毛坯件1的小端面101上的装夹螺纹孔104相配合,并对整个毛坯件1进行固定。其中装夹螺纹孔104加工在后续需要铣削去掉的区域。
[0043]
进一步的,所述小面外型加工工装4包括底座406,所述底座406的顶部加工有定位凸台405,所述定位凸台405的中间部位加工有用于和压紧盖板5相配合的多个第一螺纹孔404,所述定位凸台405的外围加工有用于和已加工好的大面内腔体202相配合的弧形过渡外轮廓403,所述弧形过渡外轮廓403的末端设置有用于和大端面103边缘相配合的定位边板402,所述底座406上加工有第二螺纹孔401。通过上述的小面外型加工工装4能够用于对初步加工之后的工件进行再次装夹,以便于对外轮廓203进行加工。
[0044]
进一步的,所述压紧盖板5通过顶部螺栓6将毛坯件1固定在定位凸台405的顶部,所述底座406的顶部通过压紧螺杆7固定安装有压板8,并将整个小面外型加工工装4压紧在机床上。通过上述的固定方式,能够将毛坯件1与小面外型加工工装4进行可靠固定。
[0045]
实施例2:采用所述的三维模拟加工工装对异形不锈钢薄壁件进行加工的方法,它包括以下步骤:步骤1:工装制作;根据所加工的异形不锈钢薄壁件结构尺寸制作相应的大面内腔加工工装3、小面外型加工工装4和压紧盖板5;步骤2:毛坯件1的下料;选取一定厚度和相应尺寸的板材,采用水刀切割的方式,将板材切割成带有u型内腔102的毛坯件1;步骤3:毛坯件1和大面内腔加工工装3的初步装夹固定;步骤3.1:在待加工的毛坯件1的小端面101加工多个用于和大面内腔加工工装3的第一通孔301相配合的装夹螺纹孔104;步骤3.2:将毛坯件1放置于大面内腔加工工装3的顶部,并通过螺栓将毛坯件1和大面内腔加工工装3固定;步骤3.3:将大面内腔加工工装3置于等高垫上,采用打压板压紧之后将整个大面内腔加工工装3放置于立式加工中心平台上。
[0046]
步骤4:对毛坯件1的大端面103和u型内腔102进行加工;步骤4.1:根据产品2的大端面以及大面内腔体202的外形尺寸,采用ug模拟加工生成程序,启动立式加工中心根据所生成的程度用第一铣刀9对u型内腔102部分进行粗加工;步骤4.2:采用ug模拟加工生成程序,用第二铣刀10对u型内腔102部分进行半精加工;
步骤4.3:采用ug模拟加工生成程序,用第三铣刀11对u型内腔102部分进行精加工,最终形成高精度的大面内腔体202。
[0047]
步骤5:对已经加工好大面内腔体202的毛坯件1与小面外型加工工装4进行再次装夹固定;步骤5.1:将前工序加工好的大面内腔体202倒扣在小面外型加工工装4的定位凸台405上,并保证大面内腔体202与弧形过渡外轮廓403相匹配;步骤5.2:将小面外型加工工装4底面置于工作台上,将压紧盖板5盖好,并通过顶部螺栓6将压紧盖板5固定在工装上同时将毛坯压紧;步骤5.3:在底座406的第二螺纹孔401上通过压紧螺杆7装压板8,进而将整个小面外型加工工装4固定在工作台上。
[0048]
步骤6:对毛坯件1的小端面101及外型进行加工;步骤6.1:根据产品2的小端顶面201及外轮廓203的外形尺寸,采用ug模拟加工生成程序,启动立式加工中心根据所生成的程度用第四铣刀12对小端顶面201及外轮廓203部分进行粗加工;步骤6.2:采用ug模拟加工生成程序,用第五铣刀13对小端顶面201及外轮廓203部分进行半精加工;步骤6.3:采用ug模拟加工生成程序,用第六铣刀14对小端顶面201及外轮廓203部分进行精加工;步骤6.4:对精加工之后的产品2进行抛光处理。
[0049]
实施例3:采用所述的三维模拟加工工装对异形不锈钢薄壁件进行加工的方法,它包括以下步骤:步骤1:工装制作;根据所加工的异形不锈钢薄壁件结构尺寸制作相应的大面内腔加工工装3、小面外型加工工装4和压紧盖板5;步骤2:毛坯件1的下料;选取一定厚度65mm和相应尺寸的板材,采用水刀切割的方式,将板材切割成带有u型内腔102的毛坯件1;步骤3:毛坯件1和大面内腔加工工装3的初步装夹固定;步骤3.1:在待加工的毛坯件1的小端面101加工多个用于和大面内腔加工工装3的第一通孔301相配合的10-m12装夹螺纹孔104;步骤3.2:将毛坯件1放置于大面内腔加工工装3的顶部,并通过m12螺栓将毛坯件1和大面内腔加工工装3固定;步骤3.3:将大面内腔加工工装3置于等高垫上,采用打压板压紧之后将整个大面内腔加工工装3放置于立式加工中心平台上。
[0050]
步骤4:对毛坯件1的大端面103和u型内腔102进行加工;步骤4.1:根据产品2的大端面以及大面内腔体202的外形尺寸,采用ug模拟加工生成程序,启动立式加工中心根据所生成的程度用φ50的第一铣刀9对u型内腔102部分进行粗加工;步骤4.2:采用ug模拟加工生成程序,用φ25r4的第二铣刀10对u型内腔102部分进行半精加工;
步骤4.3:采用ug模拟加工生成程序,用r8球头的第三铣刀11对u型内腔102部分进行精加工,最终形成高精度的大面内腔体202。
[0051]
步骤5:对已经加工好大面内腔体202的毛坯件1与小面外型加工工装4进行再次装夹固定;步骤5.1:将前工序加工好的大面内腔体202倒扣在小面外型加工工装4的定位凸台405上,并保证大面内腔体202与弧形过渡外轮廓403相匹配;步骤5.2:将小面外型加工工装4底面置于工作台上,将10mm的板材压紧盖板5盖好,并通过顶部螺栓6将压紧盖板5固定在工装上同时将毛坯压紧;步骤5.3:在底座406的第二螺纹孔401上通过压紧螺杆7装压板8,进而将整个小面外型加工工装4固定在工作台上。
[0052]
步骤6:对毛坯件1的小端面101及外型进行加工;步骤6.1:根据产品2的小端顶面201及外轮廓203的外形尺寸,采用ug模拟加工生成程序,启动立式加工中心根据所生成的程度用φ63的第四铣刀12对小端顶面201及外轮廓203部分进行粗加工;步骤6.2:采用ug模拟加工生成程序,用φ32r5的第五铣刀13对小端顶面201及外轮廓203部分进行半精加工;步骤6.3:采用ug模拟加工生成程序,用r8球头的第六铣刀14对小端顶面201及外轮廓203部分进行精加工;步骤6.4:对精加工之后的产品2进行抛光处理。