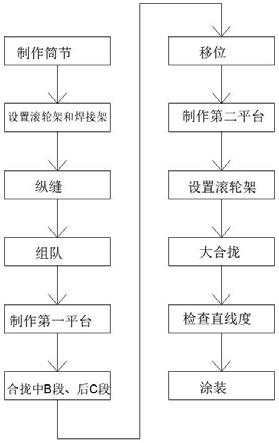
1.本发明属于风电设备制作技术领域,具体涉及一种用于漂浮型风电基座的超大直径单桩复合筒的建造方法。
背景技术:2.传统的大直径分段,直径小于φ10000mm,大直径的复合筒,普遍的建造方法为需要将大直径的复合筒立着进行拼装,焊接,然后再将分段翻身,合拢,这种方法虽然可以将复合筒分段建造出来,但是效率比较低,不能有效的利用埋弧自动焊接。该方法,效率低的主要原因为竖直拼装筒节效率比较低,且焊接环缝效率更低,因竖直拼装无法使用埋弧焊接,只能使用二氧化碳气体保护焊,装配和焊接效率很低,加工工期较长。
技术实现要素:3.本发明的目的在于提供一种超大直径单桩复合筒的建造方法,以解决上述背景技术中提出的问题。
4.为实现上述目的,本发明提供如下技术方案:一种超大直径单桩复合筒的建造方法,包括以下步骤:s1,制作筒节:将复合筒划分为前a段、中b段和后c段,根据每段的尺寸下料并裁切钢板,并将每块钢板卷圆,钢板卷圆后焊接成筒节;s2,设置滚轮架和焊接架:由于目前组队机和焊接架的最大直径可使用范围为10m,直径超过10m后,滚轮的夹角小于安全角度45度,因此为了适用大于10m的直径,首先需要对将滚轮架和焊接架进行加高加宽处理,(如图1所示),在滚轮架的两个侧面焊接支撑结构,在支撑结构上进行钻孔,滚轮结构根据筒节的大小,向外侧移动1个及以上的孔位;s3,纵缝:将卷圆后的筒节进行全熔透焊接,焊接后进行回圆;s4,组队:分别组对前a段、中b段和后c段,所述前a段、中b段和后c段分段组对时,从直径大的一侧,向着直径小的一侧组对,调节各段筒节下端的滚轮架的间距,使筒节在左右两侧滚轮架上的支点与筒节的圆心呈49度夹角由于变径范围较大,因此需在复合筒直径较小一侧的滚轮架进行垫高处理,在滚轮结构与滚轮架的横梁结构之间固定安装垫块结构,将分段的轴线保持到水平状态,然后使用埋弧自动焊接,对各组分别进行环缝焊接;s5,制作第一平台:采用h型钢制作滚轮架平台,在滚轮架平台上铺设轨道,使滚轮架能够在轨道上移动;s6,合拢中b段和后c段:将后c段置于两组滚轮架上,将另外两组滚轮架设置在轨道上,然后使用两台行车双机将中b段抬吊至轨道上的滚轮架上,所述轨道上的滚轮架一组为主动滚轮架,另一组为从动滚轮架,由主动滚轮架带动从动滚轮架和中b段向后c段靠近合拢,合拢后通过埋弧自动焊进行焊接;s7,移位:首先将位于bc段中间的两个滚轮架分别移位至bc段的首尾两端,然后四个滚轮架同时向bc段尾部方向移动,当首部的两个滚轮架移动至滚轮架平台的边缘处,停
止移动,此时将20轴线的模块车移动至bc段的底部,将bc段固定在其搁架上,将四个滚轮架全部移出bc段的底部,最后通过模块车将合拢后的bc段移位到大合拢工位;s8,制作第二平台:制作用于垫高的第二平台,并在第二平台上铺设轨道,通过卡马将轨道与第二平台相连接;s9,设置滚轮架:在第二平台的轨道上设置三个滚轮架,在地面的轨道上设置一个主动滚轮架,其中靠近第二平台轨道尾部的两个滚轮架为有油缸的组队滚轮架,另一个靠近第二平台轨道首部的为从动滚轮架;s10,大合拢:通过模块车将合拢后的bc段的尾端置于地面轨道的主动滚轮架上,首端置于第二平台尾部外侧的有油缸滚轮架上,将a前段的首部置于第二平台上的主动滚轮架上,尾部置于第二平台尾部内侧的有油缸滚轮架上;通过移动内侧的有油缸滚轮架将a前段向bc段靠拢,采用埋弧自动焊接,将a前段与bc段合拢为管桩;s11,检查直线度:直线度在筒体0
°
、120
°
、240
°
三个径向的点上沿管桩筒体长度拉一钢丝线的方法作重复检查,保证直线度满足技术规范要求,直线度检查合格后,根据焊接工艺规程,用埋弧焊烧焊筒体环焊缝;焊完后根据图纸要求做探伤检测;焊接完成后重新复查直线度,直到合格为止;s12,涂装:焊接完成后,将复合筒整体转运到涂装车间进行涂装。
5.本发明的进一步改进在于:所述步骤s1中的中b段由b1段和b2段组成。
6.本发明的技术效果和优点:采用卧造的方法,能够有效的节约管节的装配时间,并可以使用埋弧自动,提高了生产的效率,节约了生产的时间,只焊接时间就从15天减少到10天左右。
附图说明
7.图1为滚轮架的结构示意图;图2.1-2.3为前a段小组示意图;图3.1-3.4为中b段小组对示意图;图4.1-4.4为小节段组对示意图;图5.1为b段和c段组对示意图;图5.2-5.3为bc段位移示意图;图5.4位abc段合拢组队示意图;图6为本发明的流程图。
具体实施方式
8.下面将结合本发明实施例中的附图,对本发明实施例中的技术方案进行清楚、完整地描述,显然,所描述的实施例仅仅是本发明一部分实施例,而不是全部的实施例。基于本发明中的实施例,本领域普通技术人员在没有做出创造性劳动前提下所获得的所有其他实施例,都属于本发明保护的范围。
9.如图1-图5.4示出了本发明一种超大直径单桩复合筒的建造方法的一种具体实施方式:包括以下步骤:s1,制作筒节:将复合筒划分为前a段、中b段和后c段,根据每段的尺寸下料并裁切
钢板,并将每块钢板卷圆,钢板卷圆后焊接成筒节,其中中b段由b1段和b2段组成;s2,设置滚轮架和焊接架:由于目前组队机和焊接架的最大直径可使用范围为10m,直径超过10m后,滚轮的夹角小于安全角度45度,因此为了适用大于10m的直径,首先需要对将滚轮架和焊接架进行加高加宽处理,(如图1所示),在滚轮架的两个侧面焊接支撑结构,在支撑结构上进行钻孔,滚轮结构根据筒节的大小,向外侧移动1个及以上的孔位;当直径为φ12000mm的筒节在滚轮架上面进行组对时,筒节的夹角为49度,符合滚轮架45度-110度的安全角度范围要求。
10.s3,纵缝:将卷圆后的筒节进行全熔透焊接,焊接后进行回圆;s4,组队:分别组对前a段、中b段和后c段,分段组对时,从直径大的一侧,向着直径小的一侧组对(组队顺序详见图2.1-图4.4),所述前a段、中b段和后c段分段组对时,从直径大的一侧,向着直径小的一侧组对,调节各段筒节下端的滚轮架的间距,使筒节在左右两侧滚轮架上的支点与筒节的圆心呈49度夹角,由于变径范围较大,因复合筒的变径段较大,导致整个复合筒的外表面高差较大,组对时,需要保持分段的轴线为水平状态,因此需要对滚轮架的高度进行调节,因此需在复合桶直径较小一侧的滚轮架进行垫高处理,在滚轮结构与滚轮架的横梁结构之间固定安装垫块结构,将分段的轴线保持到水平状态,然后使用埋弧自动焊接,对各组分别进行环缝焊接;当组对到b中段时,前三个滚轮架要求使用300mm高度的垫高块,组对到c后段的时候,需要将前两个滚轮架使用垫梁垫高200mm,用这种方法有效解决变径差较大引起的高度差较大的问题,分段焊接的方法采用埋弧焊接,内侧使用埋弧自动焊接,筒节的外侧焊接,同样使用埋弧自动焊接,需要在焊接架上面焊接,由于目前所采用的焊接架,只能满足直径小于10m的管节,因此,需要对原焊接架进行加高、加宽处理,用以适应大变径的管节组对,同时,在焊接的环缝的时候,将环缝焊接架进行改造(如图5.1所示),高度和宽度,要求改造到12000mm。;s5,制作第一平台:采用h型钢制作滚轮架平台,组对平台的高度为700mm,使用700mm的h型钢制作,在滚轮架平台上铺设轨道,使滚轮架能够在轨道上移动;s6,合拢中b段和后c段:将后c段置于两组滚轮架上,将另外两组滚轮架设置在轨道上,然后使用两台行车双机将中b段抬吊至轨道上的滚轮架上,所述轨道上的滚轮架一组为主动滚轮架,另一组为从动滚轮架,由主动滚轮架带动从动滚轮架和中b段向后c段靠近合拢,合拢后通过埋弧自动焊进行焊接;所述第一平台轨道上的滚轮架为350t,地面轨道上的滚轮架为650 t;s7,移位:bc段合拢后,重量达到了485吨,无法使用两台行车进行移位,因此,需要使用模块车将合拢段移位,首先将位于bc段中间的两个滚轮架分别移位至bc段的首尾两端,然后四个滚轮架同时向bc段尾部方向移动,当首部的两个滚轮架移动至滚轮架平台的边缘700mm处,停止移动,此时将20轴线的模块车移动至bc段的底部,将bc段固定在其搁架上,将四个滚轮架全部移出bc段的底部,最后通过模块车将合拢后的bc段移位到大合拢工位(如图5.2、图5.3所示);s8,制作第二平台:制作用于垫高的第二平台,并在第二平台上铺设轨道,通过卡马将轨道与第二平台相连接,第二平台的高度为1600mm;s9,设置滚轮架:在第二平台的轨道上设置三个滚轮架,在地面的轨道上设置一个
主动滚轮架,其中靠近第二平台轨道尾部的两个滚轮架为有油缸的组队滚轮架,另一个靠近第二平台轨道首部的为从动滚轮架(如图5.4所示),可以有效的解决半径差较大的问题;s10,大合拢:通过模块车将合拢后的bc段的尾端置于地面轨道的主动滚轮架上,首端置于第二平台尾部外侧的有油缸滚轮架上,将a前段的首部置于第二平台上的主动滚轮架上,尾部置于第二平台尾部内侧的有油缸滚轮架上;通过移动内侧的有油缸滚轮架将a前段向bc段靠拢,采用埋弧自动焊接,将a前段与bc段合拢为复合筒;s11,检查直线度:直线度在筒体0
°
、120
°
、240
°
三个径向的点上沿管桩筒体长度拉一钢丝线的方法作重复检查,保证直线度满足技术规范要求,直线度检查合格后,根据焊接工艺规程,用埋弧焊烧焊筒体环焊缝;焊完后根据图纸要求做探伤检测;焊接完成后重新复查直线度,直到合格为止;s12,涂装:焊接完成后,将复合筒整体转运到涂装车间,首先将中间的两个滚轮架,移动到头部一侧,然后再使用24轴线模块车进入到复合筒底部位置,要求模块车的中心位置与复合筒的重心位置对齐,滚轮架撤出复合筒底部,然后使用模块车将复合筒转运到涂装车间,转运过程要求平稳。
11.本发明采用卧造的方法,能够有效的节约管节的装配时间,并可以使用埋弧自动,提高了生产的效率,节约了生产的时间,仅焊接时间就从15天减少到10天左右。
12.申请人又一声明,本发明通过上述实施例来说明本发明的实现方法及装置结构,但本发明并不局限于上述实施方式,即不意味着本发明必须依赖上述方法及结构才能实施。所属技术领域的技术人员应该明了,对本发明的任何改进,对本发明所选用实现方法等效替换及步骤的添加、具体方式的选择等,均落在本发明的保护范围和公开的范围之内。
13.本发明并不限于上述实施方式,凡采用和本发明相似结构及其方法来实现本发明目的的所有方式,均在本发明的保护范围之内。