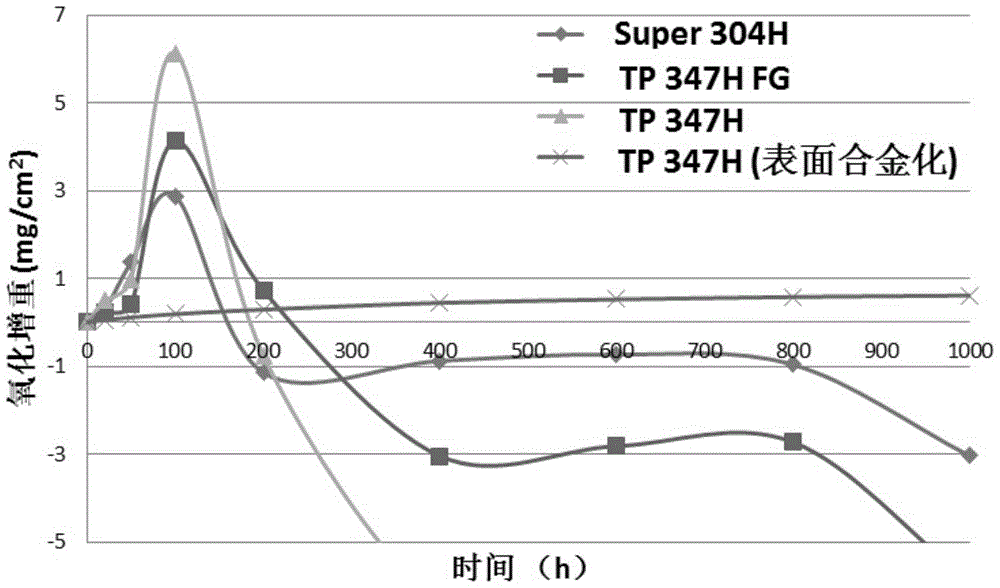
本发明属于表面合金化及涂层技术领域,涉及一种钢管表面合金化方法,具体涉及一种锅炉过/再热器用奥氏体不锈钢管表面合金化方法。
背景技术:过/再热器部件是锅炉中负责回收燃煤烟气能量、加热蒸汽、实现能量转化的关键部件,是锅炉中承受压力最大、温度最高、服役环境最苛刻的部分。奥氏体不锈钢因具有足够的高温强度、持久强度、塑性、较好的抗氧化性能、冲击性能、耐高温蒸汽腐蚀以及耐煤灰磨损性能等,正越来越多的被作为锅炉过/再热器材料使用。包括TP304H,TP347H,Super304H,HR3C,NF709等。尤其随着超超临界技术的发展,奥氏体钢是目前火电机组末级过/再热器的首选材料之一。不锈钢管的制作工艺决定了不锈钢管的性能。目前,国内外的钢管生产企业对于火电机组锅炉用奥氏体不锈钢管的生产工艺主要由两种制作工艺,分别为:1、热轧(挤压)的制作工艺。工艺流程包括圆管坯→加热→热挤压→热处理→冷拔→热处理→矫直→酸洗→检验→标记→入库。2、冷轧的制作工艺。工艺流程圆管坯→穿孔→冷轧→热处理→冷轧→热处理→矫直→酸洗→检验→标记→入库。对于火电机组用的奥氏体不锈钢管,两种工艺在冷拔(轧)与矫直工序之间都需要进行稳定化热处理工艺操作。研究表明,采用上述工艺制备的奥氏体不锈钢管可满足相关国标要求。但奥氏体钢作为锅炉管道在服役过程中蒸汽侧氧化膜具有双层结构,内层为Fe2Cr尖晶石层,外层为磁铁矿层。由于粗晶奥氏体钢与氧化皮热膨胀系数差异大,氧化皮受较大层间力作用,比较容易剥落。流通管道内剥落的氧化膜一方面会堵塞过、再热器管从而引发爆管事故,另一方面被高流速蒸汽携带出过/再热器(末级过热器管内流速19m/s,再热器37m/s)并经调门、喷嘴加速后损伤汽轮机高压级和中压级的前几级叶片。尤其是大容量锅炉受热面热负荷高、管径相对大,管圈长管内表面积大,新投产的高参数、大容量机组大量应用奥氏体不锈钢,这些机组在运行在一万小时后停机中高温受热面管内产生氧化皮的脱落,约四万小时左右频繁发生奥氏体不锈钢管内壁由于氧化物脱落堵塞造成超温爆管,大大降低了机组停运行后的可靠性。目前,表面合金化技术的热点研究议题之一,是寻求能克服现役超超临界电站锅炉奥氏体钢管服役过程中所面临的氧化/腐蚀问题的相关技术,并希望提供现役耐热钢材料在更高的蒸汽参数机组(600-650℃)上继续使用的途径。金属表面合金化技术是通过扩散工艺改变基体金属表面层的成分和组织以保护基体金属的防护技术。这种技术能够在不影响合金基体性能的前提下,改善和满足服役环境对合金表面功能的特殊要求。近年来,国外正在研发的技术主要包括高/低温粉末改性渗铝技术、腔道喷涂技术等。欧洲的“CoatingsforSupercriticalSteamCycles”(SUPERCOAT)研究项目主要采取了在耐热钢表面进行700℃传统热扩散渗铝的方法。然而传统热扩散渗铝方法存在制备效率低、能耗高等诸多问题,难以在锅炉管道等大型构件上经济性的实施。另外,传统热扩散渗铝通常需保温数个小时才能实现,增加了热加工步骤和成本。纳米技术的发展带动了表面合金化的进展。美国科学家以纯铁氮化为对象的研究表明:金属表面纳米化能够加速其表面合金化进程。进一步研究发现低碳钢表面纳米化后,600℃时渗铝层η-Fe2Al5的生长速率是原来的3倍,这一结果为解决耐热钢低温渗铝效率低下的问题提供了方案。但必须注意的是,渗层仍为η-Fe2Al5相,因而其存在的力学性能问题仍未能由表面纳米化的方法解决。同时,锅炉管道的表面纳米化处理在技术可行性与成本方面还有待商榷。此外,对于内径较小的锅炉管道来说,要对其内壁作喷丸纳米化处理,技术上也是一种挑战。在国内,研究人员对锅炉过/再热器管道表面合金化技术也有一定程度的研究。西安热工院早期采用了热浸渗铝技术,在锅炉管道表面形成了以FeAl为主相的合金化层,显著提高了管道抗烟气腐蚀能力,并在马头电厂得到了示范应用。但是,受热浸渗铝工艺所限,能处理的管子比较短(2~3米),大大增加了施工中的焊接量,因而未能得到推广。中国科学院金属研究所发明了一种大气条件下无保护气氛或保护层的料浆高速渗铝方法。该法将工件表面沉积渗铝料浆,在无保护气氛和保护层下直接对工件加热,可以在工件表层获得一定厚度的富铝层。但对锅炉使用的超长管内壁实施此工艺,工艺性和可行性尚待确认。
技术实现要素:本发明的目的在于克服上述现有技术的缺点,提供了一种锅炉过/再热器用奥氏体不锈钢管表面合金化方法,该方法可以实现锅炉过/再热器用奥氏体不锈钢管表面的合金化。为达到上述目的,本发明所述的锅炉过/再热器用奥氏体不锈钢管表面合金化方法的具体操作为:对需要合金化的锅炉过/再热器用奥氏体不锈钢管表面依次进行料浆涂覆、烘干硬化及高温烧结,其中,料浆由渗剂及粘结剂混合而成,渗剂与粘结剂的比例为80-120g∶100mL;所述烘干硬化的具体操作为:将料浆涂覆处理后的锅炉过/再热器用奥氏体不锈钢管在室温下放置1-5小时,然后再100-300℃的温度下烘干硬化1-5小时;所述高温烧结的具体操作为:将经过烘干硬化后的锅炉过/再热器用奥氏体不锈钢管在850-920℃的温度下热处理30min-5h。所述渗剂由铝粉、硅粉及铬粉组成,其中,铝粉、硅粉及铬粉的质量占渗剂的总质量的比例分别为30-60%、15-45%及25-55%。所述粘结剂由浓度为10%-30%的磷酸盐水溶液与铬酐混合而成,其中,粘结剂中铬酐所占质量为1%-10%。所述锅炉过/再热器用奥氏体不锈钢管表面涂覆的料浆的厚度为30-500微米。本发明具有以下有益效果:本发明所述的锅炉过/再热器用奥氏体不锈钢管表面合金化方法在对锅炉过/再热器用奥氏体不锈钢管表面合金化过程中,先分别依次对需要合金化的锅炉过/再热器用奥氏体不锈钢管表面依次进行料浆涂覆、烘干硬化及高温烧结,所述浆料由渗剂及粘结剂混合而成,渗剂与粘结剂的比例为80-120g∶100mL,从而实现锅炉过/再热器用奥氏体不锈钢管表面的合金化,可以使经合金化的锅炉过/再热器用奥氏体不锈钢管表面达到完成抗氧化级,操作简单、方便。附图说明图1为本发明的实施例一中处理后的锅炉过/再热器用奥氏体不锈钢管表面的截面图;图2为本发明的实施例一中处理后的锅炉过/再热器用奥氏体不锈钢管表面在750℃纯蒸汽环境中的氧化动力学曲线。具体实施方式下面结合附图及实施例对本发明做进一步详细描述:实施例一对TP347H钢管表面进行合金化,本发明所述的锅炉过/再热器用奥氏体不锈钢管表面合金化方法的具体操作为:对需要合金化的锅炉过/再热器用奥氏体不锈钢管表面依次进行料浆涂覆、烘干硬化及高温烧结,其中,料浆由渗剂及粘结剂混合而成,渗剂与粘结剂的比例为100g∶100mL;所述烘干硬化的具体操作为:将料浆涂覆处理后的锅炉过/再热器用奥氏体不锈钢管在室温下放置3小时,然后再200℃的温度下烘干硬化2小时;所述高温烧结的具体操作为:将经过烘干硬化后的锅炉过/再热器用奥氏体不锈钢管在890℃的温度下热处理1h。所述渗剂由铝粉、硅粉及铬粉组成,其中,铝粉、硅粉及铬粉的质量占渗剂的总质量的比例分别为60%、15%及25%。所述粘结剂由浓度为30%的磷酸盐水溶液与铬酐混合而成,其中,粘结剂中铬酐所占质量为10%。所述锅炉过/再热器用奥氏体不锈钢管表面涂覆的料浆的厚度为150微米。实施例二本发明所述的锅炉过/再热器用奥氏体不锈钢管表面合金化方法的具体操作为:对需要合金化的锅炉过/再热器用奥氏体不锈钢管表面依次进行料浆涂覆、烘干硬化及高温烧结,其中,料浆由渗剂及粘结剂混合而成,渗剂与粘结剂的比例为80g∶100mL;所述烘干硬化的具体操作为:将料浆涂覆处理后的锅炉过/再热器用奥氏体不锈钢管在室温下放置1小时,然后再300℃的温度下烘干硬化1小时;所述高温烧结的具体操作为:将经过烘干硬化后的锅炉过/再热器用奥氏体不锈钢管在920℃的温度下热处理30min。所述渗剂由铝粉、硅粉及铬粉组成,其中,铝粉、硅粉及铬粉的质量占渗剂的总质量的比例分别为30%、45%及25%。所述粘结剂由浓度为10%的磷酸盐水溶液与铬酐混合而成,其中,粘结剂中铬酐所占质量为1%。所述锅炉过/再热器用奥氏体不锈钢管表面涂覆的料浆的厚度为30微米。实施例三本发明所述的锅炉过/再热器用奥氏体不锈钢管表面合金化方法的具体操作为:对需要合金化的锅炉过/再热器用奥氏体不锈钢管表面依次进行料浆涂覆、烘干硬化及高温烧结,其中,料浆由渗剂及粘结剂混合而成,渗剂与粘结剂的比例为120g∶100mL;所述烘干硬化的具体操作为:将料浆涂覆处理后的锅炉过/再热器用奥氏体不锈钢管在室温下放置5小时,然后再100℃的温度下烘干硬化5小时;所述高温烧结的具体操作为:将经过烘干硬化后的锅炉过/再热器用奥氏体不锈钢管在850℃的温度下热处理30min。所述渗剂由铝粉、硅粉及铬粉组成,其中,铝粉、硅粉及铬粉的质量占渗剂的总质量的比例分别为30%、15%及55%。所述粘结剂由浓度为15%的磷酸盐水溶液与铬酐混合而成,其中,粘结剂中铬酐所占质量为5%。所述锅炉过/再热器用奥氏体不锈钢管表面涂覆的料浆的厚度为500微米。实施例四本发明所述的锅炉过/再热器用奥氏体不锈钢管表面合金化方法的具体操作为:对需要合金化的锅炉过/再热器用奥氏体不锈钢管表面依次进行料浆涂覆、烘干硬化及高温烧结,其中,料浆由渗剂及粘结剂混合而成,渗剂与粘结剂的比例为90g∶100mL;所述烘干硬化的具体操作为:将料浆涂覆处理后的锅炉过/再热器用奥氏体不锈钢管在室温下放置3小时,然后再150℃的温度下烘干硬化2小时;所述高温烧结的具体操作为:将经过烘干硬化后的锅炉过/再热器用奥氏体不锈钢管在880℃的温度下热处理1h。所述渗剂由铝粉、硅粉及铬粉组成,其中,铝粉、硅粉及铬粉的质量占渗剂的总质量的比例分别为40%、25%及35%。所述粘结剂由浓度为12%的磷酸盐水溶液与铬酐混合而成,其中,粘结剂中铬酐所占质量为4%。所述锅炉过/再热器用奥氏体不锈钢管表面涂覆的料浆的厚度为100微米。实施例五本发明所述的锅炉过/再热器用奥氏体不锈钢管表面合金化方法的具体操作为:对需要合金化的锅炉过/再热器用奥氏体不锈钢管表面依次进行料浆涂覆、烘干硬化及高温烧结,其中,料浆由渗剂及粘结剂混合而成,渗剂与粘结剂的比例为110g∶100mL;所述烘干硬化的具体操作为:将料浆涂覆处理后的锅炉过/再热器用奥氏体不锈钢管在室温下放置4小时,然后再250℃的温度下烘干硬化4小时;所述高温烧结的具体操作为:将经过烘干硬化后的锅炉过/再热器用奥氏体不锈钢管在910℃的温度下热处理3h。所述渗剂由铝粉、硅粉及铬粉组成,其中,铝粉、硅粉及铬粉的质量占渗剂的总质量的比例分别为50%、20%及30%。所述粘结剂由浓度为22%磷酸盐水溶液与铬酐混合而成,其中,粘结剂中铬酐所占质量为6%。所述锅炉过/再热器用奥氏体不锈钢管表面涂覆的料浆的厚度为180微米。实施例六本发明所述的锅炉过/再热器用奥氏体不锈钢管表面合金化方法的具体操作为:对需要合金化的锅炉过/再热器用奥氏体不锈钢管表面依次进行料浆涂覆、烘干硬化及高温烧结,其中,料浆由渗剂及粘结剂混合而成,渗剂与粘结剂的比例为95g∶100mL;所述烘干硬化的具体操作为:将料浆涂覆处理后的锅炉过/再热器用奥氏体不锈钢管在室温下放置3.5小时,然后再220℃的温度下烘干硬化3.5小时;所述高温烧结的具体操作为:将经过烘干硬化后的锅炉过/再热器用奥氏体不锈钢管在910℃的温度下热处理2.5h。所述渗剂由铝粉、硅粉及铬粉组成,其中,铝粉、硅粉及铬粉的质量占渗剂的总质量的比例分别为30%、30%及40%。所述粘结剂由浓度为25%的磷酸盐水溶液与铬酐混合而成,其中,粘结剂中铬酐所占质量为9%。所述锅炉过/再热器用奥氏体不锈钢管表面涂覆的料浆的厚度为250微米。图1为合金化层的截面形貌,由图可知,合金化层厚度为90微米,主要由内外两层组成,外层含少量孔洞及氧化物夹杂,涂层中平均Al含量33%,Si含量8%,Cr含量12%,其余为Fe,图2为几种合金在750℃下纯蒸汽环境中的氧化动力学曲线,可以发现,TP347H,TP347HFG,Super304H合金均出现了氧化失重,表明氧化膜发生了剥落现象,而表面合金化的TP347H具有最低的氧化速率,氧化增重趋势符合抛物线规律,在此条件下,达到了完全抗氧化级。